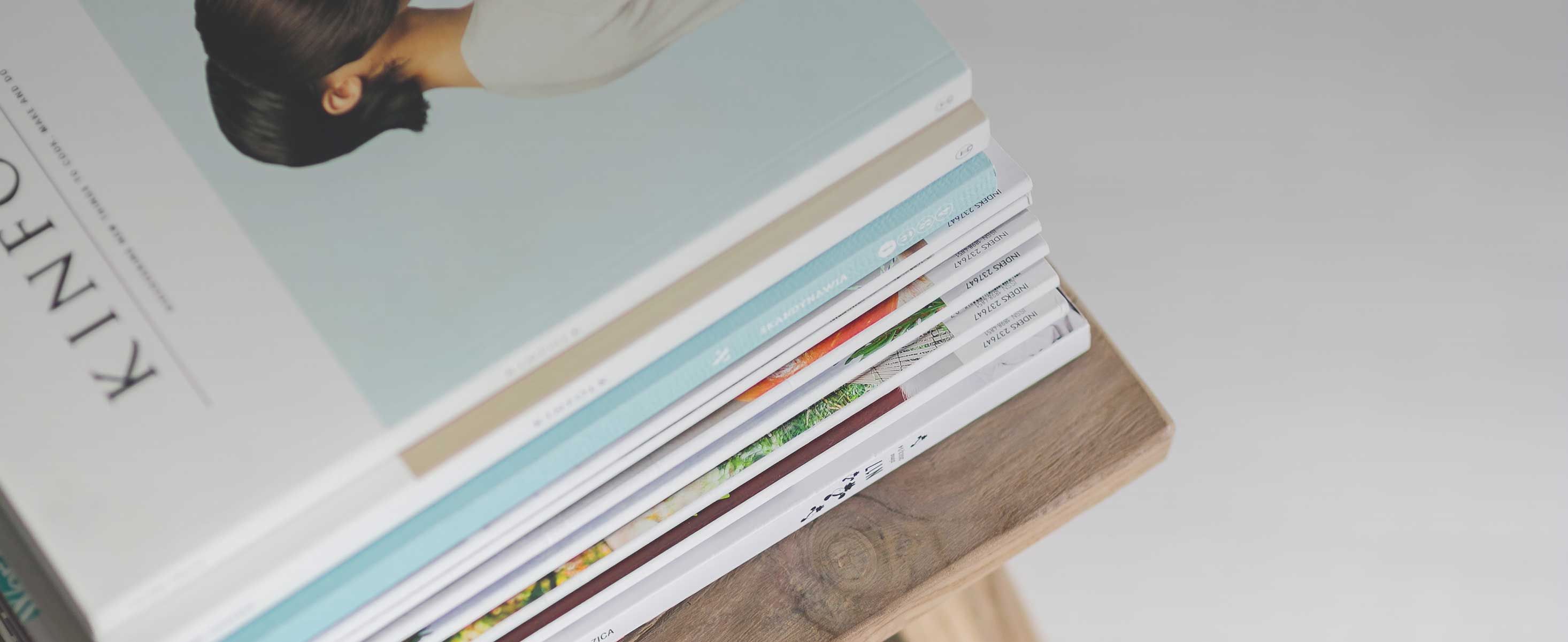
6 minute read
Plans of Work
Troubleshooting Plans of Work
‘Planning’ is a subject causing considerable challenges for many licensed contractors and attracting frequent criticism from the Health and Safety Executive (HSE). This brief article is intended to help contractors critically review their own approach, but it may also be of interest to clients and others with an interest in assessing plans, and health and safety management.
Regulation 7 of the Control of Asbestos Regulations requires employers to prepare a written plan before any asbestos work is carried out. Standard licence conditions require the production of a “suitable and sufficient” plan, prior to notification of work, and state that the plan must be followed on site.
Licence conditions mean that written plans must be at the heart of licence holders’ safety management systems: plans should clearly show what senior management expects a site team to do. The quality of planning is likely to be a major focus of licence assessments and inspections.
There is a problem when gaps open between actual practice and “paperwork”: asbestos removal is a practical job and it is a challenge to ensure that Plans of Work (PoW) are seen to help and guide the removal process. The key to closing this gap often lies in engaging relevant staff (particularly contract managers, supervisors and auditors) in the on-going development of the planning process.
Format and Quality
Guidance “Asbestos Regulation 7 Plans of Work – Purpose and Core Principles”, which can be read alongside ALG memo 04/12, aids format and content for a suitable Plan of Work (this guidance is referenced at end of article). Templates may be useful for those preparing the plan but are not necessarily helpful for those being asked to use the finished plan. Following one format cannot guarantee that a plan will be “suitable and sufficient”: for example, the required section on air management might have been completed, but the contents might be incorrect or difficult to follow; a sketch may be included but it does not reflect site reality etc. In addition, any one particular format is likely to suit some types of jobs more than others. Regardless of format, any reader should be able to quickly identify what the particular challenges are for this job and how management have decided these will be tackled. Where jobs are straightforward and simple, the plan should be. The main emphasis should always be on the quality of the information being given, not the format.
Do reviews / audits focus on format or quality? Has the company format(s) been developed with input from those who need to use it?
Can a list of quality criteria be developed (with input from users) to help determine good / bad plans?
Content Current guidance (Asbestos Regulation 7 Plans of Work – Purpose and Core Principles) lists what should be considered as part of a plan. The immediate purpose of the plan is to clearly address significant risks associated with a particular project. Standard procedures, industry guidance, ‘standard’ training courses, generic assessments etc. deal with the common situations associated with removal work. For example they address: w Size of timber / grade of polythene to use for enclosures w Keeping areas tidy, to avoid slips and trips w Choosing ‘appropriate’ equipment for work at height and ‘appropriate lifting aids’ for manual handling etc. A site-specific plan would refer to general procedures, but it would provide a very clear focus on, for example: w The particular access equipment for
THIS job w What lifting aids are needed for THIS job w Details of specific welfare provision for
THIS job w Given the size / fixings of THESE panels, how many operatives will be working together on THAT platform in order to lift, shadow vac, spray and bag etc? To improve clarity and usefulness, it makes sense to be careful about how generic / standard issues are presented in the plan. Non-specific, generic material will tend to make plans less user-friendly and less likely to be read. Generic information increases the chance of missing important, site-specific items.
Are the particular challenges for this job obvious? Is the scope and sequence/phasing of work clear?
Could visitors measure site conditions/progress against the plan? Repeats Templates often encourage repetition. For example, a “Method of Work” section describes what will be done, where and how and then later sections in the plan on “Controls” and “Equipment” repeat much of the same information. Often the location and layout of transit routes, enclosures and airlocks are described in writing and then also shown in a sketch.
Repetitions increase the chance of ‘cut and paste’ errors, increase length and complexity and therefore make plans less likely to be read.
Could the format encourage repetition? Do POW reviews/audits check for consistency between sections?
What language? The choice of language is a good indicator of WHO the plan has been written for. The following examples are common: w w
w ‘Access and egress will be via …’ ‘H-Class vacs will be situated in the enclosure…’ ‘Work will commence…’
Most people do not usually talk this way and this choice of language does not help to make a user-friendly document. More significantly, the choice of language encourages a perception that the plan is not really for the site team. Perception matters: if we want site teams to use plans, they must be produced in a style that is accessible for them.
Are plans written in plain English?
Why use words? Following on from the above, why use words at all when good sketches, flow charts and photographs would provide the same information more accurately and in a more user-friendly format? Well-constructed sketches and photographs (marked with labels, arrows etc.), supported by flow charts showing the sequence of work and the precise methods expected.
Could some written information be replaced by diagrams etc.? Do reviews/audits identify good and bad examples of sketches, photographs etc.? Who is the plan for? During licence assessments, HSE examines a contractor’s general approach to planning: licences are not granted unless the ALU is confident licence conditions can be complied with. Between licence assessments, contractors may often encounter individual HSE inspectors demanding particular changes to plans. Inspectors provide invaluable input into particular controls for particular circumstances. However, if inspectors (or others) are insisting on changes to a contractor’s general approach to assessment and planning, then it would be advisable to discuss the issue with the ALPI (members can contact ARCA for advice in such situations). First and foremost, plans must work for the managers and supervisors etc. being asked to use them: they are central to an organisation’s management system and undue external influence may undermine this.
Are plans primarily produced for supervisors and contract managers, rather than clients / others?
How is it used? The real test of whether or not a plan is ‘suitable and sufficient’ lies with site teams and their managers. Do they find it useful? Could it be improved?
If plans are criticised, the response should not be limited to re-writing that particular plan and / or sending staff on a training course; it is much more positive to involve all relevant staff in reconsidering the general approach to producing and using plans.
ARCA offers members support and advice with planning and management systems. For more information, call ARCA on 01283 566467 or visit www.arca.org.uk
References
“Asbestos Regulation 7 Plans of Work – Purpose and Core Principles” https://webcommunities.hse.gov.uk/ connect.ti/asbestos.licensing/view?objectId=684325 ALG memo “04/12 Suitable and Sufficient Plans of Work” - http://webcommunities.hse.gov.uk/connect. ti/asbestosliaison/view?objectId=250672 “Managing and Working with Asbestos: Approved Code of Practice and Guidance to the Control of Asbestos Regulations 2012 - http://www.hse.gov.uk/pubns/ priced/l143.pdf