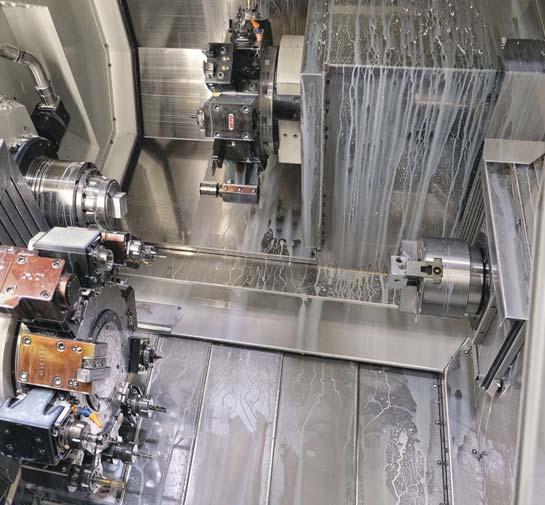
3 minute read
Turn-milling cuts lead time
Subcontracting firm Mintdale Engineering, Chesterfield, is run by four members of the Toyne family, managing director Chris, his wife and company secretary Christine and two other directors - their son Jason and his wife Julie.
The company specialises in CNC turning of bar, tube and billet as well as CNC milling on five vertical machining centres (VMCs). It operates twice as many machines for rotational parts production as for prismatic, although the borderline between the two is increasingly blurred these days.
Take for example an aluminium gas regulator base produced on the company's latest turning centre, an Italian-built Biglia B465 T2 Y2 twin-spindle, twin Yaxis turret model supplied in spring 2022 by UK and Ireland sales and service agent Whitehouse Machine Tools. The 1.25 inch high cuboid part is machined from 2 inch square bar fed by an LNS Quick Load Servo 80 S2 short bar magazine.
The component, which Mintdale Engineering has been producing for 22 years, was latterly machined 20 at a time on a twin-pallet-change VMC. Op 1 involved machining three sides, milling a circular pocket, drilling various holes and then tapping them, while Op 2 after pallet change completed similar features. Floor-to-floor time per base was two minutes.
On the Biglia, the part is produced in one hit and requires only a small amount of face turning and parting off, the remainder of the cycle being prismatic machining. Both live turrets are deployed at the main spindle for some of the time, followed by simultaneous machining at both spindles using the two tool carriers. Although cycle time is three minutes, i.e. 50% longer per part than before, the big advantage is that production is unattended, unlike on the VMC. The finish-machined components pass through the counter spindle onto a conveyor feeding a Hydrafeed Rota-Rack parts accumulator.
The lathe continues producing throughout the day shift, after which 100 parts can be added by running the machine lights-out until the bar is used up. The only special items needed to realise this application, which represents a good balance between main and counter spindle operations, were a spindle liner and a bar feed attachment for the square stock.
Another component produced more efficiently on the B465 T2 Y2, this time from 3 inch diameter round brass bar, is a conversion body for legacy gas delivery systems used in hospitals. The so-called Mark III component formerly required four operations: milling on a VMC and turning on a single-turret lathe, followed by two further separate visits to different VMCs for more prismatic operations and engraving.
The part is now turned, milled and drilled complete in the Biglia in a five-minute cycle. That is quicker than just one of the previous VMC operations.
Moreover no special workholding is needed, which would add expense and cause unnecessary delay to the delivery of the first batch of parts.
A third part that has been transferred to the Italian lathe is a Mark IV version of the gas delivery conversion body, turnmilled from the same brass bar. It used to be produced in two operations on a chucking lathe on which a special jig was made for holding the irregularly shaped Op1-machined billet to enable Op 2 to be carried out.
The extended floor-to-floor time for producing batches of the components is eliminated by the Biglia's ability to machine the component in one hit from bar in a five-minute cycle. Again, the cost of making a fixture and of work-in-progress is avoided.
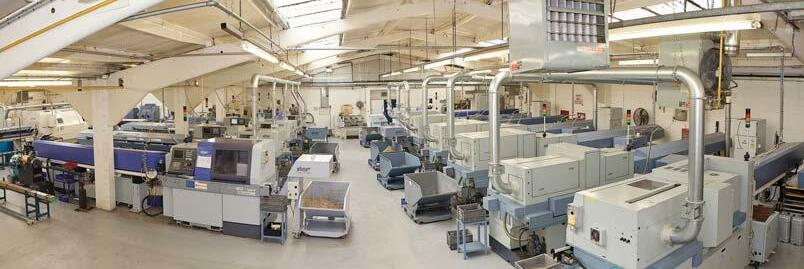
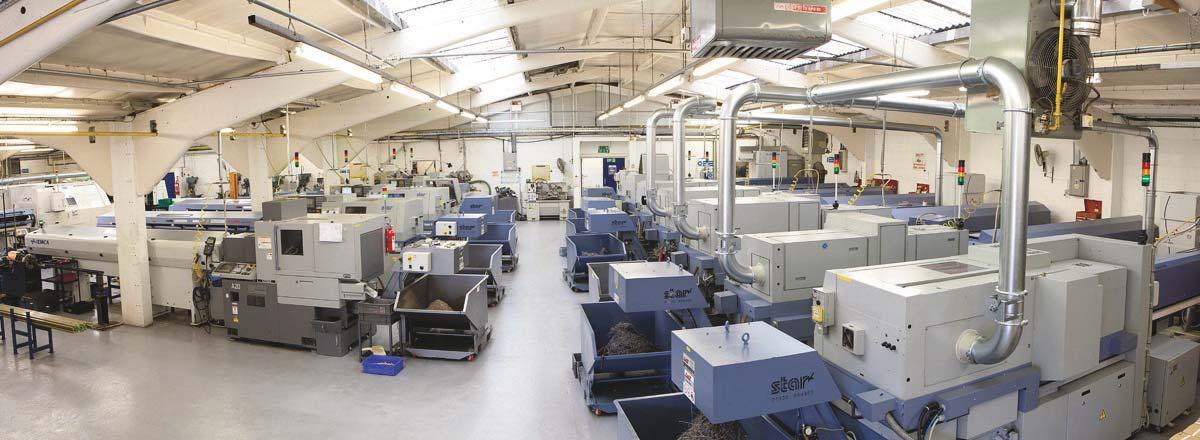
8 mintdale.com
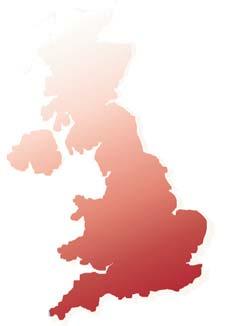
Two new 51mm capacity lathes are being put through their paces on parts for JCB at JTB Pressings in Wolverhampton.
The company had formerly subcontracted out turning and this move was made to help the company increase the range of manufacturing services it provides to existing customers, as well as spearheading a drive to secure new business from different sectors. It now offers a one-stop-shop, vertically integrated, manufacturing service that also includes laser cutting, welding and fabrication, powder coating and assembly services.
The DN Solutions (formerly Doosan) machines, a 6” chuck/ 51mm bar capacity Lynx 2100LYSA and, a similarly sized Lynx 2100, were installed at one of the company’s (three) production facilities in Willenhall, Wolverhampton.
Since their arrival both lathes have been machining, almost exclusively, a range of small, precision turned parts for the construction and agricultural equipment manufacturer JCB.
These parts, with their short cycle times and machined in high volumes, include six individual components (i.e., washers, bolts, bushes etc.), made from a range of materials that include steel, bronze, Nylon 6 etc., for a specific JCB Telehandler model’s door catch system which, after being machined, are then finished, powder-coated and assembled in-house by JTB.
Over 600 of these fullyassembled door catches are