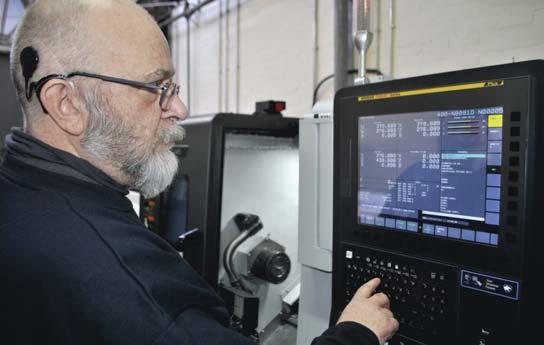
1 minute read
Turning on new service
manufactured every week by JTB: a majority being dispatched immediately to the customer’s production line and the remainder, including the assembly’s individual components, retained for spares and stock.
Explains Ivan Evans, JTB’s managing director, said: “We are always looking to improve, diversify and grow.
“As such, we regularly invest in advanced manufacturing technologies to increase our productivity, manufacturing flexibilities and overall competitiveness.”
A recent example of JTB’s investment strategy in action saw the company, in 2018, acquire a state-of-the-art, large-capacity Nukon Eco 315 (2kW) laser cutting machine.
“This machine has added another string to our bow”, says Ivan Evans. “It has helped us grow the business enabling us to acquire a number of new customers looking for highquality laser cut parts.”
To protect and strengthen its supply chain position with customers, help it increase productivity, improve process efficiencies, and control operational costs, JTB made the decision, back in 2021, to further expand the range of services it offered to customers, by developing its machine shop at its Willenhall facility.
Steve Lounds, JTB’s general manager said: “We knew from experience, and from talking to customers and prospects, that there was a demand we could meet for machining high-quality, competitively priced turned parts.
“We made the decision to meet this demand by creating a world-class, in-house subcontract machining resource, focused on producing complex, high-precision small turned parts for customers.”
8 jtb-pressings.co.uk