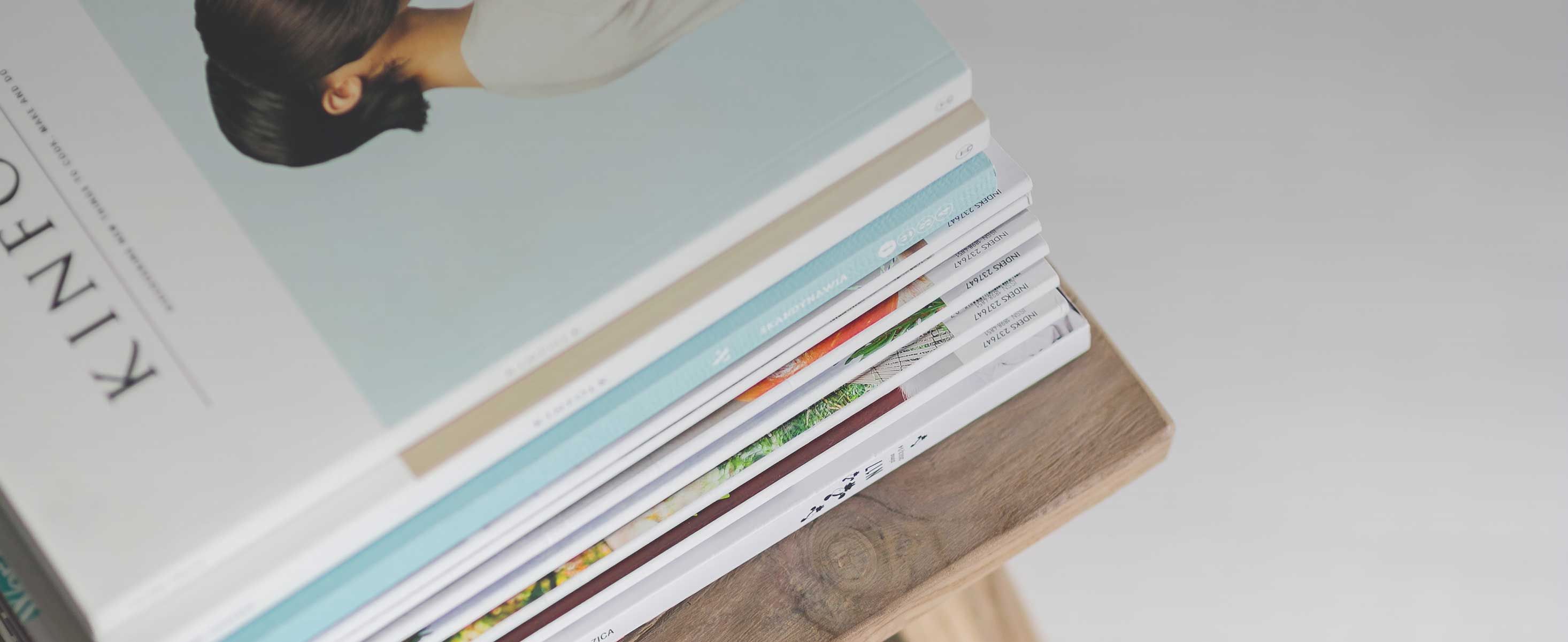
2 minute read
Mill and turn for repeatability
Irish subcontract machining company Shannon Precision Engineering Ltd has recently invested in new mill-turn centres for aerospace and automotive contracts.
The two Nakamura-Tome machines, a WT150II and an SC100X2 , were supplied by the Engineering Technology Group (ETG).
Located in Shannon, the 80 employee manufacturer is AS: 9100 and ISO: 9001 certified, and it frequently works on highprofile projects for Airbus, Lear, Bombardier, Collins Aerospace, Liebherr, Safran, Spirit and many other leading names in the aerospace, automotive, offshore, rail and power generation sectors.
Machining everything from inconel, titanium, Hastelloy, duplex and Nitronic 40 and 60 as well as hardened steels, the stability and performance of its machine tools are of paramount importance. With the company winning a significant automotive order as well as major opportunities in the aerospace sector, SPE needed a new strategy in its mill/turn department.
Managing director Dominic Murphy said: “On some projects, we have been struggling with repeatability when machining particularly difficult materials. We won a contract to machine electro-mechanical connections for the aerospace industry from Nitronic 40 and titanium, and we needed to be very responsive with our changeovers and lead times. With regular batches from 200 to 500 and up to 20 different part families in the series, the project has some very ambitious cycle time targets. With tolerances of +/-5 and +/-10μm on many features, we didn’t want to be chasing repeatability – we needed a more robust process than we had.”
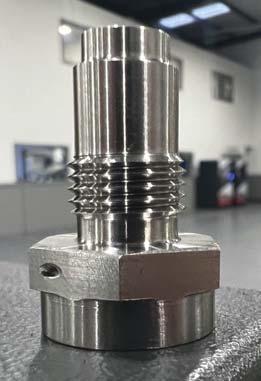
The County Clare company investigated the mill/turn market and it was the Nakamura WT150II that won the day with cycle times more than 20% faster than its rivals. “We gave ETG and other vendors a series of components as a prove-out. ETG built a machine set up around the family of components and they delivered a turnkey solution to our facility that was best suited to our requirements. We already have a lot of mill/turn centres onsite, so the Nakamura-Tome WT150II wasn’t just about cycle times. We needed a turnkey solution that could meet our ambitious cycle times and tight tolerances with relentless repeatability for long batch production – the NakamuraTome WT150II certainly delivered on that.”
The SC1002 was able to produce an extremely complex automotive part in one hit. It previously required a 4-axis horizontal machining centre and two lathes.
8 spe.ie
Visit our website or contact us for a quote or advice
Yamazaki Mazak’s Discovery Week in December featured live cutting demonstrations on 20 machines, presentations by senior managers on the state of the market and the business’ goal of cutting its carbon footprint by 50%, and the use of AI to bridge the skills gap.
From the point of view of the subcontract manufacturing market, Alan Mucklow, Managing Director UK, Eire and National Distributors at Yamazaki Mazak, said that the UK market is remarkably resilient and there are big opportunities for subcontractors that invest in 5-axis machining.
“There have been many challenges over the last few years – the pandemic, an economic crisis and a skills crisis that we are living through now. But the impact of recessions is neither universal nor uniform. Some sectors will do better than others and some companies will thrive.”
He added that the key way to use these challenges to grow a business is to focus on taking those challenges on board and maximising the opportunities they present.
He noted that aerospace was really starting to get on track and growing, the effects of the war in Ukraine were creating opportunities in the energy market, the medical sector continues to be strong and has grown significantly. Automotive has struggled with shortages of microprocessors, but the transition away from traditional combustion engines was