
3 minute read
5-axis opportunities
presenting opportunities – and Mazak had certainly seen growth in those areas.
“Our customers are still telling us they are very busy … I think most companies remain fairly confident.”
And companies are confident that investing in manufacturing technology will help them to grow.
“I think that the more technologically advanced you are in your machining operations the more positive the outlook. Anecdotally there is a shortage of 5-axis capability in the marketplace. OEMs and Tier One suppliers are struggling to find subcontract capability for 5-axis machining.”
“It is key that subcontractors are forward thinking in their investment plans to take the opportunity and really grasp the benefits that will accrue to them.”
He stressed that Mazak has made a real effort to focus on bringing 5-axis machines to a wider market.
“The CV5-500 that we developed here in the UK – and we are very proud of that fact –has really enabled us to target and achieve penetration in the marketplace and that has enabled smaller companies to invest in the transition away from 3-axis or to supplement their 3axis with 5-axis machining.”
Presentations to the press at the event also set out Mazak’s Go Green initiative that aims to significantly reduce the environmental impact of the manufacture and use of its machines.
The goal is to halve its carbon footprint by 2030 compared to 2010 and to achieve four times higher environmental efficiency in the same time frame. For example, using a range of approaches such as replacing pneumatic and hydraulic systems with electrical ones, the carbon footprint of the latest VARIAXIS NEO has been reduced by 22%.
The presentations also looked at approaches to addressing the skills crisis. These included the greater use of automation –freeing up operators to carry out more value added tasks – and the use of Artificial Intelligence to refine some of the processes that previously required a high degree of skill. Examples include Solid MAZATROL, which can create a machining programme from a 3D file in a matter of minutes on the machine, and SMOOTH AI spindle, which uses machine learning to set the optimum parameters to minimise vibration and tool chatter.
Machines on display at Discovery Week included Mazak’s latest vertical machining centre, the VCN-700, which is designed and manufactured in the UK specifically for machine users requiring highperformance machining. The VCN range has been developed to significantly improve productivity rates for manufacturers undertaking everything from heavy-duty cutting through to high-speed machining.
The event featured live demonstrations with the VCN700, along with the VARIAXIS i300 AWC that offers an expandable high-capacity tool magazine for high-mix, lowvolume applications. In addition, the UK-designed and built CV5500 was displayed with an MA robot for increased productivity, including lights-out and unmanned machining.
Laser users were able to see in live cutting action the OPTIPLEX
3015 FIBER III 10. kW laser processing machine, equipped with a TEKMAG automated sheet metal loading system. Specifically, the ultra-high-speed cutting of medium thickness material and the ability to cut the finest widths and most difficult reflective materials. The 10.0 kW 3015 FIBER III model that was displayed at Discovery Week can also process workpieces up to 1525 mm x 3000 mm.
Discovery Week also served as a showcase for Mazak iCONNECT, the latest remote servicing solution that allows users to monitor their machine operations, perform remote diagnoses, access part order history and more through the company’s secure cloud service –ultimately delivering improved productivity and machine performance.
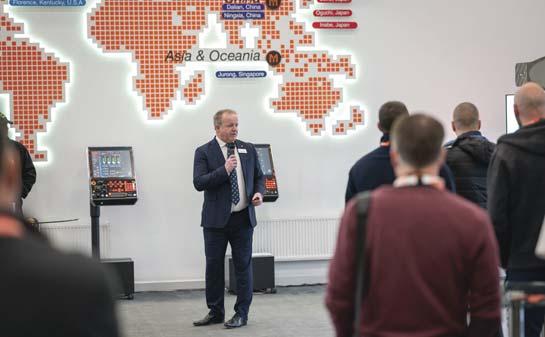
Mazak’s European Manufacturing Plant in Worcester is responsible for the production of an extensive range of UKdesigned and built machines, including the highly popular entrylevel CV5-500 5-axis machining centre as well as the VCN-700 and VCE-600 next generation vertical machining centres.
8 mazakeu.co.uk
ES Precision has helped an Oxfordshire dental practice to keep track of dental tools without the need for label application or hard-to-read serial numbers. The laser marks are permanent, clear and withstand repeated autoclaving.
Deddington Dental is a 4-surgery dental practice with around 40 fast and slow dental handpieces that are used by 7 dentists and looked after by 8 nurses. Each dental handpiece costs £400-700 so it is important to keep track and account for each one. Each surgery has its own allocation of handpieces, and they are taken to a different decontamination room and processed several times each day.
Akhil Gupta, Principal Dentist, explained: “Previously, we relied on using the tiny serial numbers marked on the handpieces or using a coloured tape on each one to identify which surgery