
18 minute read
Automation
High-mix, low-volume automation
A compact modular machine tending system can automate the loading and unloading of parts, or material, to a wide range of machines. Easy to set up and with an intuitive interface, machine tending solutions can be easily integrated into new and existing production processes.
Automated tending is the operation of machine tools within a manufacturing environment, incorporating robot automation systems. Historically machinetending applications were undertaken by operators (humans) and featured within machine shops whose primary processes included lathes and milling machines, as examples. Raw materials would be placed into the machine by the operator and removed once the machine had completed its cycle. The skills gap however has meant that qualified operators are becoming difficult to find and as a result, businesses are adopting robotic processes within their supply chains to ensure operational continuity.
A robotic machine-tending process can be repeated continually, as raw parts are constantly delivered to the robot, minimizing cycle times and optimising operational processes by removing parts from the machine’s working area. Compact and easy to install, machine tending cells can be moved from one machine to another and, are easily reconfigured. Their ability to run autonomously for many hours means that they provide a very quick return on investment.
The flexibility of a machine tending system means they can be easily adapted to satisfy an array of production demands and, key processes can be supported that will deliver increases in productivity and reduced operational costs. Not only can the loading and unloading of machines be supplemented, but the robot can also perform additional tasks, such as inspection. The mobile nature of the system means that several different tasks and applications can be supported across the operational footprint and, much like the mobile cobot solution that is available, the machine tending solution is a viable choice for SME’s as an all-encompassing tool with interchangeable applications across several tasks.
There are several health and safety considerations that also
8 The MultiTend (MT-4) modular
system has been designed and developed by DesignPro Automation, KUKA Ireland Platinum System Partner
support the adoption of automated machine tending. It can be dangerous work and a robotic solution can provide a level of consistency consummate with both throughput and, quality output demands. Robots replace the manual (human) element and assume the management of product movement. By design, robots have a higher level of accuracy and repeatability throughout the loading and unloading cycle. They do not tire nor suffer lapses in concentration. Repetitive and mind-numbing tasks will be attended by a dedicated robot.
One additional benefit in the adoption of machine tending robots is their suitability of use in a ‘lights-out’ operation, or ‘dark factory manufacturing’
environments. Fully autonomous and, with no human presence required, robots can continue in production, delivering additional cost savings as no heat, light or air conditioning is required, also known as ‘total automation’.
In many production facilities, space is already at a premium. Automated robotic machine tending systems tend to have a small footprint meaning they can be incorporated within an established operation. Standardised hardware also means that installation is both fast and efficient. Flexible machine tending solutions are also less expensive and easier to integrate than you might imagine and, will provide considerable benefits even on small production runs.
Automated machine tending cells can also add value where the monotonous, dirty and dangerous nature of tending machines manually, makes finding and retaining trained personnel difficult. Once they have been created, machine-tending programs can be alternated to coincide with the receipt of new orders. And if we consider the monotonous nature of machine tending, from a manual perspective, the adoption of automated robot cells enables a business owner to upskill his staff. Operators become robot programmers, which in turn presents the opportunity for upscaling automated processes. With the necessary skilled personnel in employ, businesses can position themselves strategically against their competitors, by future-proofing operations. Recent events have highlighted just how delicate the manual element of our operations can be when external factors impact health and wellbeing. Automated robotic processes however can continue to operate, delivering minimal impact within a manufacturing supply chain, in the event of another global event that presents productivity challenges.
Robotics have proven to be ideal for companies who strive to keep their machines running at full capacity whilst mitigating cost and remaining competitive and, as a result many SME’s are turning to automated machine tending, embracing the speed and flexibility that these cells can deliver that are critical to operational success. 8 designproautomation
Kuka.com
5DLVLQJWKHSURƩOHRI engineering, composites DQGVFLHQWLƩFFRPSDQLHV

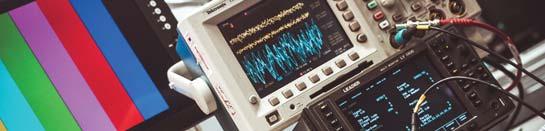

PR | Marketing | 6RFLDO0HGLD | Copywriting | Events Awards | Design | 0HGLD5HODWLRQV | Web & SEO
01752 894786 www.aroprandmarketing.co.uk
A bespoke sheet metal enclosure or structure offers a welcome solution when nothing standard or ‘off-theshelf’ can be found. It promises freedom and flexibility to overcome problems and get exactly what you want without compromise. Chris Arnoldof manufacturing contractor ICEE Managed Services offers some tips on achieving best value for money from this option
Typically there are four situations where a bespoke solution becomes essential: first, where a standard enclosure cannot adequately accommodate special and important features of the equipment specification and compromises are undesirable; second, where a customer wants changes to a standard equipment enclosure to gain competitive edge in the market; third, where equipment to be enclosed or a service to be delivered is completely new or novel and no standard enclosure or structure exists to meet its special demands; fourth, where an unmistakable branding or unique form is essential to make the structure enclosing equipment or delivering a service stand out in the marketplace.
Chris Arnold, ICEE Managed Services Ltd.

No compromises with bespoke enclosures
CAD 3D solid modelling speeds design for manufacture and rapid prototyping at ICEE
Bespoke is a real option Compared to compromising with a standard enclosure, a bespoke approach will generally deliver important benefits far outweighing any time and cost required for its design and development. Modern technologies plus lean methods have transformed the economics of bespoke design and manufacture, making it a viable and affordable option. This includes rapid prototyping methods such as sophisticated CAD 3D solid modelling; the latest CNC fibre laser, waterjet cutting and brake press bending machines; web-enabled collaboration and smarter supply chains. At ICEE we find it no more expensive to manufacture and assemble bespoke enclosures than standard ones.
We also use advanced software to support best practice design for manufacture. When quoting, for the customer’s sake and ours, we ensure a sheet metal panel can be made in least time, at least cost, without any production issues. A customer’s bespoke design may include a hundred or more different types of sheet metal component. We ask for STEP files and run each design through our software. Any issues found are discussed with the customer and solutions offered. This not only makes evaluation and quoting fast and efficient, it also means subsequent production is fully optimised and hitch-free.
Tips to get a specification right Above all, with bespoke, ensure the requirements specification is right. An obvious point (especially with long projects), first doublecheck if the end-product will be completely fit for purpose and meet all commercial demands. Think about possible changes during its working lifetime and with today’s trend towards a circular economy, consider decommissioning and recycling. This means you don’t reach the prototype stage – virtual or physical - and find the design doesn’t meet functional or market requirements and requires a drastic rethink (and find nothing left in the R&D budget). Get the fundamental requirements specification fully worked out and planned first, before moving to the design and
prototyping stage. It can save a lot of time and money.
Standard equipment enclosures come with a number of approval and type-testing compliances in place. With a bespoke solution those requirements have to be built into the design. First check certification and compliance. For example, what mandatory regulations and industry standards must the bespoke design meet? Risk assessment has to be considered. This can range from electrical safety to electro-magnetic compatibility (EMC). Check ingress protection (IP) rating on water penetration and sealing requirements. If applicable, look at standards and regulations applying in all countries the enclosure or structure will be used in. CE marking is a case in point.
In short, make compliance checking a top priority. If an obscure regulation is overlooked and emerges after completing design and prototyping stages, correcting the oversight can have damaging effects on marketing and roll-out programmes (and project budgets). A new regulation may appear during a long project, so it pays to be vigilant.
Rapid prototyping - virtual vs actual Today, screen-based, 3D solid modelling speeds up the prototyping process and saves a lot of money. Virtual iterations cost far less to do on-screen. Across a network, collaboration and consultation is easier and faster. Several more variations than would normally be possible
Brompton folding bicycles: ICEE manufacture, fit-out, install and maintain a range of high quality bespoke docking stations across the UK for Brompton Bike Hire
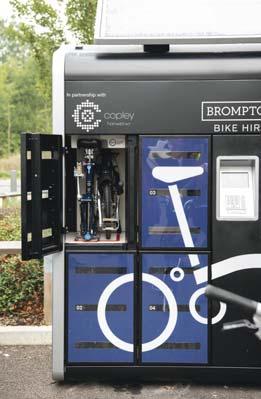
Picture courtesy of Brompton Bike Hire
may be explored, before selecting one that best meets the brief or specification.
Above all, do as much as you can virtually on-screen, before moving to a physical prototype. With today’s CAD software, many simulations, tests and prove-outs may be performed to ensure everything works in practice, including all-important design for manufacture. Taking this circumspect approach means less risk of discovering an anomaly or flaw when a physical prototype is built, or worse, production is about to start.
Summing up Compared to a standard enclosure or structure, a bespoke solution means you can get exactly what you want without compromise. It provides freedom and flexibility to overcome problems. Time and cost necessary for design, development and manufacture may be more than offset by greater benefits gained. Thanks to lean methodology plus advanced design and production technologies time and cost may now be brought down substantially, so the difference between a standard or bespoke choice is often very little.
ICEE specialises in delivering bespoke solutions. We can simply make parts, but that’s not our main business. Working closely with the customer, we have considerable experience in prototyping and manufacturing completely bespoke products, from the enclosure or structure itself, to assembly and internal fitout, cabling and testing of equipment and systems, all done in our factory, ready for deployment. We offer to install across the UK, commission and then maintain an equipment enclosure throughout its working life, including upgrading internals if and when required. We can make bespoke one-offs, or produce batches and variants. In short, we deliver a total, managed service.
8 For more information please contact: ICEE Managed Services Ltd. 20 Arnside Road, Waterlooville Hampshire PO7 7UP Tel: 02392 230 604. Email: sales@icee.co.uk Web: www.icee.co.uk

Lock gates link the lochs
ECS Engineering Services has completed the installation of 2 sets of lock gates at Kytra Lock, on the Caledonian Canal in Scotland.
The operation, part of a refurbishment investment by Scottish Canals, was vital to maintain the navigation of the historic waterway.
The Caledonian Canal opened in 1822 and runs for 60 miles across the Scottish Highlands. The watercourse offers a unique scenic setting, as it passes through famous lochs, such as Loch Ness, and runs next to Urquhart Castle and the mountain scenery at Fort William. The canal's fascinating environment and heritage attracts over 1,400 boats every year. Therefore, ensuring their safe and secure navigation whilst preserving the natural and historical features of the waterway is of the utmost importance.
In its ongoing commitment to improve reliability and safety of the waterway, Scottish Canals regularly inspects the conditions of the many lock complexes along the canal, including examining the upstream and downstream lock gates at Kytra, a particularly popular location between Fort Augustus and Loch Oich.
The investigation revealed the need to replace all the upstream and downstream steel lock gates. The new systems would have to retain the traditional design and materials of the original gates. In this way, they would seamlessly integrate with their surroundings, keep their technical and historical significance, and maintain the individual character of the Caledonian Canal.
To complete this complex and specialised project, Scottish Canals appointed ECS to survey, design, manufacture and install the new lock gates.
After conducting an exhaustive survey, ECS developed an upgraded design of lock gates, suitable for the structure, in its Sutton-in-Ashfield factory in Nottinghamshire. The structure would not only match the historical design, but also feature an extended service life. The two pairs of lock gates combining steel and traditional Douglas fir timber elements, are 6.5 metres wide. The downstream gates are 8.27m high and weigh 18.65 tonnes, whereas the two upstream lock gates have a height of 5.89m and weigh 13.3 tonnes.
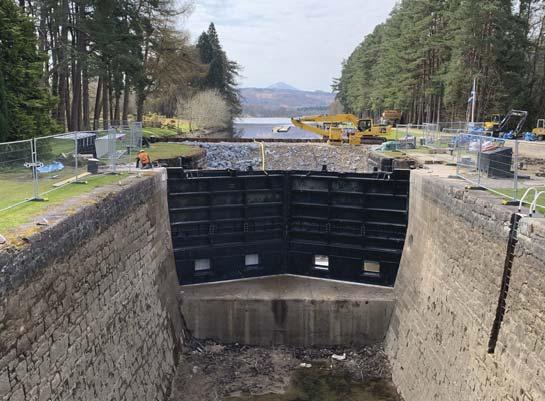
The anatomy of a lock gate replacement
The installation of such large structures, restricted to the winter months to reduce any disruption to boaters and tourists walking the towpath close by, was conducted in different stages. First, the new lock gates were transported to Fort Augustus. There, different components, such as seals and sluice gates, were built onto the gates prior to installing them in the canal. In this way, ECS could considerably shorten the time required to mount the systems onsite.
Subsequently, a section of the canal covering Kytra Lock
upstream and downstream gates was drained to support the removal of the old lock gate systems and installation of the new ones.
Water control on a project of this size is difficult so, after careful consideration, it was agreed to build a temporary dam that would help to regulate the ingress of water in the drained canal section. The 2000-tonne stone structure would provide safe access to conduct the replacement work for the duration of the project.
Brian Rhodes, Project Manager at ECS, explains: "While the design of Kytra Lock historical gates is similar to modern solutions, there are some differences that should be carefully considered during installation. Our extensive knowledge and experience in replacing navigational locks was crucial to complete the project in a timely manner and deliver a reliable and fully functioning lock system."
In addition, the onsite activities were made even more challenging by winter weather conditions. These created a particularly harsh environment for ECS staff, especially when manoeuvring the gates into their lock chambers. Despite these issues, ECS was able to complete the installation efficiently and check its correct alignment as well as the absence of leaks on time.
Unlocking future collaborations
Following the replacement of the lock gates, ECS installed replacement walkways and other ancillary equipment back onsite, the temporary dam was dismantled and access to the waterway and the towpath was reopened to the public. Immediately after the successful refurbishment of Kytra Lock structures, ECS replaced a pair of nearby lock gates, located in Fort Augustus.
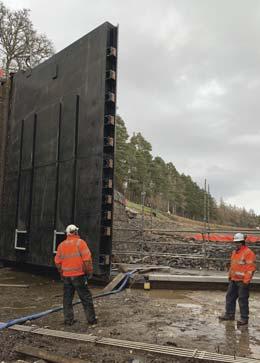
Tom Burgin, Project Engineer at ECS, comments: "This project faced many different challenges, nonetheless ECS managed to handle them successfully. In particular, while onsite operations had to be delayed due to poor weather conditions, ECS was able to work collaboratively with the main contractor in order to minimise the impact of these extraordinary circumstances."
Brian Rhodes concludes: "By completing the refurbishment of Kytra Lock gates, ECS is offering further proof of its comprehensive capabilities to complete challenging water control projects in environmentally sensitive locations as well as in historical and heritage sites. We are delighted to know that Scottish Canals was extremely satisfied with our work and we look forward to supporting the organisation in the future." 8 ecsengineeringservices.com

From design, sampling and technical support to manufacture, Simpson Springs & Pressings Ltd provide the complete service.
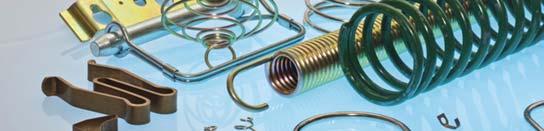
Tel: 0118 978 6573 Email: sales@simpsonsprings.co.uk
The Laser Cutting Co (TLCC) has taken delivery of a new Trumpf TruLaser Tube 7000 at its Sheffield facility.
TLCC is already producing flat sheet-metal ventilator parts as part of the fight against the current COVID-19 pandemic and the new TruLaser Tube is helping the company bid competitively for tube-based parts needed for the same purpose
Established in 1976, TLCC supplies cut round and square tube, structural open sections, beams, and flat/bent metal components to customers throughout the UK. Under the same roof, the company can also provide bending, welding and subassembly services, backed by a large partner network of subcontractors offering further.
The 35-employee, family-run business believes its success is underpinned by continuous investment in the latest technology. So, with one of the company’s laser tube cutters approaching the end of its serviceable life, the search began for a suitable replacement.
“We are heavily focused on processing innovative tube design, so this investment in the Trumpf TruLaser Tube 7000 will further enhance our capability and capacity in this area,” says Director Charlie Day. “Although we’re a subcontractor, our customer slogan is ‘your partner in production’, where we can add considerable value at the design stage. The Trumpf machine will support our efforts in this area, particularly with
Tube laser fuels growth
6-axis 3D cutting and the flow drill and tapping attachment.”
Although laser tube cutting can replace conventional machining processes such as drilling, sawing and milling, it is also now possible to perform threading operations in-cycle, replacing weak and time-consuming fixings such as nuts or rivets.
In the first machining step, the flow drill produces an extrusion that is followed by the cutting of a heavy-duty thread.
Advantages such as the flow drill will provide a competitive edge in many regards, not least when trying to win work required by the healthcare sector as it looks to boost capacity due to coronavirus.
“Ultimately, having the Trumpf TruLaser Tube in place is helping us bid competitively for work that will benefit the COVID-19 effort,”

says Mr Day. “Among the tubebased work we are hoping to capture includes medical apparatus and racking systems. Such items are essential if the system is to avoid becoming overwhelmed. A lot of this work appears to be in preparation for a potential second peak.”
“Investment in the Trumpf TruLaser Tube is helping us have a seat at the table for these new healthcare components,” he says. “As well as providing cost savings, the introduction of the Trumpf machine brings a higher level of flexibility in an ever-changing environment. It will also see lead times reduce dramatically. The market is very competitive and lead times are vital, as is quality. Our parts need to be on time and correct, every time.” 8 lasercutting.co.uk
Salamander Fabrications has installed an automated laser with integrated handling system that will allow it to cut and process sheet metal twice as quickly as on existing machinery.
The 6Kw Bystronic laser and automated warehouse – which should enable the team to switch between profiling one material to the next in under four minutes –had been put on hold following the Coronavirus outbreak.
However, the Slaithwaite firm has now been able to resume activity – with hopes of having the finishing touches applied by the end of July 2020.
The whole system is 25m x 15m x 4.5m in height and can cut a variety of aluminium, steels and yellow metals. It is expected to increase the company’s production capacity by up to 70% and has 24/7 ‘lights out’ running capability.
Up to three people at Salamander will be trained on how to fully operate the integrated system and mentor others. The purchase was part funded by a
Barnshaws Polska has supplied over 2100 tonnes of rolled steel plates for a crude oil storage tank in Nelahozeves, Czech Republic.
The new tank is part of a large central crude oil tank farm, which holds emergency reserves of oil and provides interim storage before the refining process.
With growing demand for energy, the site has been continually expanded since its opening in 1994. Metrostav a.s.,
Salamander fires up new laser
£240,000 grant from Leeds City Region Partnership (LEP).
“It’s a big day for everyone at Salamander Fabrications as we welcome such a stunning piece of kit that will further enhance the speed in which we can react to customer requirements,” said managing director, Michael Haskell.
“This kind of automation not only optimises our material flow, it improves our machine
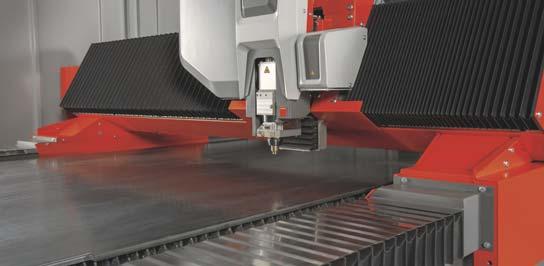
use, provides us with a greater level of reliability and upskills our workforce to operate first-class machinery.”
Salamander Fabrications has already integrated collaborative robotic welding into its operations to cater for a number of substantial contracts – including one to supply components for a large rail refurbishment assignment. 8 salamanderfabs.com
2100 tonnes of rolled steel the largest Czech construction and amounted to 2,100 tonnes of steel fabrication company, was precision curved steel.” approached in 2018 regarding the The completed tank would addition of a new storage tank. measure over 84 metres in
Maciej Walkowicz, Director at diameter. Despite its large size, Barnshaws Polska said: “We were the tolerance on this tank required to roll 531 steel plates diameter was 10-15mm. ranging in thickness from 10 mm Constructed from hundreds of up to 39 mm, in widths from 2 m to plates of varying thickness, 3 m and 10 m in length. There was a ensuring precision during the range of toe-in and toe-out bends bending process was vital. across the plates. All in all, this 8 barnshaws.com