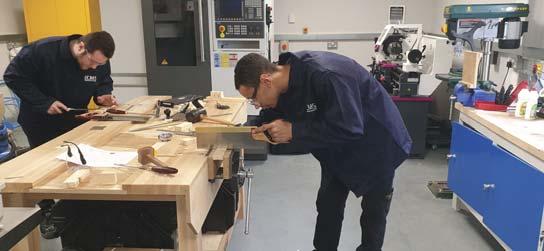
20 minute read
Profile
access. The professional body (the Institute of Cast Metals Engineers, ICME) facilitated this, alongside the CMF, providing the secretariat, identifying a lead employer to chair the employer group and submit the application, organised meetings of the steering group and also funding an ‘industry person’ as a per diem contractor to do much of the legwork to draft the standard.
This was not easy, as none of us were ‘educationalists’ and there was some ‘going round in circles’ with the SFA for a good while in the early days. One of our staff stepped in to facilitate the writing of the End Point Assessment plan as industry people, whilst having the occupational understanding, were not able to sufficiently interpret the SFA guidelines. But the upshot was that industry now has a funded apprentice standard that covers a good part of the industry’s skills needs. But there was a significant in-kind cost to the industry bodies and some of our employers, as well as the very real cost of bought-in expertise.
A new independent training company has since been established (Foundry Training Services Ltd) to deliver the training, with part time tutors recruited from industry and training for them to become instructors, all funded by a loan. There has also been no nationally funded help available for the development of the teaching and learning materials, which has been funded from charity reserves!
Separately the industry (actually the lead bodies in the main) have actively supported the establishment of the National Foundry Training Centre, funded through a local LEP. An employer was willing (and in a position to be able) to make some land available to ‘host’ the new facility, and there were industry suppliers who were keen to support and ‘sponsor’ some of the kit, which was a huge help.
There have been many challenges and difficulties to overcome, not least with getting employers engaged after years of no apprentices and no provision, and there have been significant setbacks along the way. This is a re-build after two decades since the last foundry college closed. But both the professional body and the trade association have promoted and supported this in numerous ways over recent years.
David Bisset of FSE Foundry Ltd says “Without the input from the lead bodies, a company like mine would not be able to access the specific training we need. Foundry and patternmaking courses are not courses that most colleges will be able to offer. Numbers of learners are small, the specialist knowledge does not exist within their teaching staff
8 Learning to use the woodworking
tools in the pattern shop
and learners may be geographically spread. So this creates real challenges. Without the drive and input from the Trade Association and the real financial input from the industry’s Professional Body, the provision would not be where it is today.”
Former student and now Quality Manager at Charter Castings, Sam Edwards, agrees, saying “I have certainly benefited from being able to follow a programme specific to the industry I work in –casting is a complex process with many variables, so having some more formal underpinning knowledge to complement the on the job experiences is in valuable when looking to problem solve”.
Whilst this is not perhaps the pure ideal of ‘employer-led’, the industry bodies have been instrumental in minimising the barriers for their employers - this is a strong argument for the role that industry bodies can play in supporting their industries, but also evidence of some of the challenges that we all face in the more ‘niche’ sectors of the manufacturing sector. 8 castmetalsfederation.com
Based on two sites in Milton Keynes and Bedfordshire, The Engineering Quest sets itself apart from the mainstream volume subcontracting sector. From components for space telescopes to miniature ophthalmic instruments, it specialises in the development and manufacture of components that are hard to find, hard to design and hard to make.
As Managing Director Steve Matheron explains: “When you look at our portfolio you can see that we make lots of incredibly complex parts. Our core competencies encompass producing tightly toleranced items – working at micron and sub-micron machining levels – in some of the most difficult materials there are – including polycrystalline diamond, tungsten carbide and superalloys. We can do miniature and micro-machining, and we can do complexity – some of the parts we make have over 1,000 dimensions.
“We say that If you show us a job that nobody can make for you, we will make it.”
The Engineering Quest was born when two companies in the same group came together – Tracel, a high-end aerospace subcontractor, and Preform Tools, which made carbide compaction tooling for the indexable insert industry.
The first area where they applied their combined capabilities was in the development of highpressure block pumping technology for common rail fuel injection systems operating at up to 3,500 bar.
The specialist SME with a corporate heart
8 This optical telescope casing was
engineered for Surrey Satellite
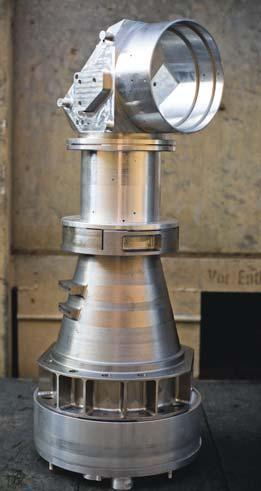
“We started getting into these very tightly tied up components made out of very difficult materials. The parts were going into extremely harsh environments under massive pressures. We solved a lot of problems for them, which meant that they could get the block pump working. It was the highest pressure diesel pump at the time. And the higher the pressures, the harder the materials and the tighter the tolerances. We ended up making things in tungsten carbide to sub-micron tolerances – and we are still making them now,” says Steve.
“We needed a name to pull the businesses together and wanted something that was going to set us apart. We looked at what we mainly do for people, finding answers and solving problems, and so that is where our name came from: Engineering and the Quest to find solutions.”
Diverse manufacturing capability
The Engineering Quest is well equipped with a wide range of manufacturing equipment, including 52 CNC machine tools and an extensive metrology capability.
Steve says: “We have a very diverse set of machinery that we have built up over the years. This allows us to move from market to market and problem to problem. We have invested in a lot of highend equipment, including Swiss grinding and EDM equipment. We always thought that cylindrical grinding was an area that was underserved in the UK and so we have invested over £1m in new Kellenberger machines.”
But the actual manufacturing side of the business is only part of the story. The Engineering Quest also offers customers a complete service to take a new product from design to production – either in-house or at a third party manufacturer.
“We have developed a unique package for customers called the Quest Design Optimisation System (Q-DOS), which is a suite of tools and software that enables customers to evolve their products and save money. With our Q-DOS approach a customer can remove production costs at the design stage, potentially saving them millions of pounds over the life of the part,” says Steve.
“We go into companies and work with them right at the initial concept phase.”
The full process includes manufacturability assessments, design for manufacture analysis, prototyping, and putting the blueprinted part into production. It also features value stream mapping, global product mobility and process flow analysis to optimise the manufacturing process.
At that stage, the customer has a choice. If it is a high-value process that comes within The Engineering Quest’s core competencies, then the components can be made in-house. Alternatively, the customer can be given a ready-to-go production process that they can take to a third party to manufacture.
Embedding best practice
The Engineering Quest has worked with organisations such as Cranfield University and the Institute for Manufacturing at Cambridge University, to ensure that best practice is embedded throughout the company.
At the heart of this is something rarely, if ever, seen in an
8 Engineering Quest Managing
Director Steve Matheron
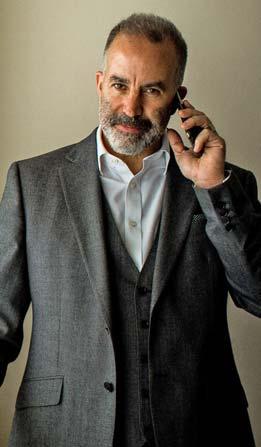
engineering business of this type; a central bank of tools to support people at a thinking and behavioural level. Called the Quest Cultural Engagement Library (Q-CEL) it defines the culture and what is expected of staff in order to deliver the highest quality of products and service. Items in the library include; The 20 essential engineering precepts, the 10 essentials of leadership and the 7S’s of well-being.
Steve Matheron explains: “This is our own internal culture and it gives everyone a clear direction of how to approach things. We take big company thinking and boil it down to SME scale. We’re also extremely proud of how we promote well-being for everyone at The Quest Engineering. The library keeps welfare and key working practices in focus, so that we have a consistent culture across the whole business.”
“We have a long-standing culture of learning and development in the business, so we invited the Institute of Manufacturing to audit our strengths and weaknesses. We also work with some of the world’s largest engineering organisations and constantly review our systems so that we remain aligned to their best practice approaches. We scrutinise ourselves in the same way we take time to analyse a new part. That’s led to the creation of Q-DOS and Q-CEL and our own intranet, called Being Brilliant, that staff access on a daily basis.”
“We are not just a normal subcontractor; we currently have a part on the Mars Lunar Rover and you can’t be at that level without being willing to keep learning and having the creativity to develop new ways of working.
“As we say to people; if you can’t make it, we can!”
Looking ahead, he is very positive, and the company has taken on more work for major customers as other suppliers have closed during the Covid pandemic.
“The outlook for the future is good for us. Our current quotation level is through the roof. We have probably quoted more jobs in the past three months than we did in the whole of last year. The Engineering Quest continues to develop and we look forward to solving more engineering challenges for our global customers.” 8 join-the-quest.co.uk
Turning up medical work
A new Y-axis, sub-spindle, turning centre will help meet increased medical orders, and boost turn-milling productivity across the board at CPTE.
Established more than 30 years ago, Mildenhall subcontractor CTPE uses 3- to 5-axis machining centres as well as fixed- and sliding-head CNC lathes to manufacture complex, high precision components mainly for the scientific, medical, electronics and defence sectors. The latest addition to the plant list is a Biglia B 620 YS fixed-head turn-mill centre with Y-axis and sub-spindle (both optional) supplied by Whitehouse Machine Tools.
It is the first lathe from the Italian manufacturer on the subcontractor's shop floor and only the second of this new model to be installed in the UK, following its launch at the EMO 2019 machine tool show in Hannover. It has a 70mm bar capacity and billet up to 360 mm diameter can be manually loaded for turn-milling.
The B 620 YS is meeting a fivefold increase in demand for a tighttolerance aluminium connector that forms part of medical equipment needed in the fight against Covid-19. CTPE has been making the component for the past 15 years on a Y-axis lathe with a single spindle, which meant that the part had to be re-fixtured by hand on the same machine for a second operation, following which manual deburring was necessary.
The component is now produced in larger volumes much faster as well as more accurately and consistently in a single hit on the Biglia, deburring being included in the machining cycle, allowing 600 to be shipped every week. This elevated supply rate started at the beginning of April and is likely to continue through to September 2020.
Alex Taylor, CTPE's operations director said, "The reason for buying the lathe was a significant uplift in orders from the medical industry in general, not only for the connector part.
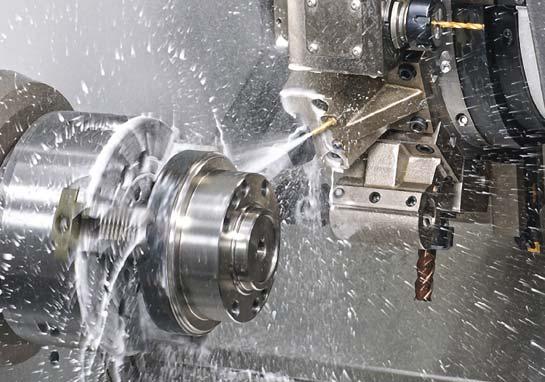
"However, we were also on the lookout for a machine capable of raising turn-milling productivity across the board, including of larger components from billet. "The Biglia provides a good balance for both types of turning of components up to 620 mm long and with its sub-spindle is ideal for one-hit machining.
The machine installed in CTPE’s Mildenhall shop has 15 turret stations, all of which are powered by a 13 kW, 6,000 rpm motor. Up to 30 cutters can be in the machining area at any one time.
The B 620 YS has a full C-axis on the 15 kW, 5,000 rpm, direct-drive sub-spindle as well as on the main spindle, making it easier to plan cycles so that machining is better balanced at either end of a component, minimising cycle times. 8 ctpe.co.uk
Precision turned parts manufacturer AES Precision has invested in a Trimos V5 height gauge from Bowers Group to ensure quality of components used in the medical, defence, aerospace, automotive and electronics industries.
Mark Wilson, Director at AES Precision Engineering, said: “We have strict quality control procedures, and must meet tight tolerances, so accuracy is incredibly important to us. The Trimos height gauge is a great solution for our general inspection requirements.”
AES Precision typically uses a CMM for the measurement of complex components. For basic parts requiring quick and accurate measurements, however, a simple solution was needed that would be fast and easy to use. The business previously used a basic digital height gauge, but decided it was time to upgrade to a more sophisticated model with a few more features.
The Trimos V5 height can either be manually operated or motor driven, and has a clear display and user-friendly functions. It offers exceptional ease of use; so easy in fact that all shop floor operatives and inspectors at AES Precision use the height gauge on a daily basis. Mark continues; “We find the height gauge very accurate, and it has a great range of functions to suit our needs. Training was very straightforward and everyone here was confidently using the height gauge very quickly!”
As AES Precision serves industries where precision is
Height of accuracy
critical, quality is extremely important. The business also offers First Article Inspection Reports (FAIR), including tailored reporting and data collection to suit the individual requirements of clients. This, along with a fully traceable QMS system, means that AES Precision’s quality system meets or exceeds the requirements of most clients’ manufacturing needs.
Based in Ashford, Kent, AES
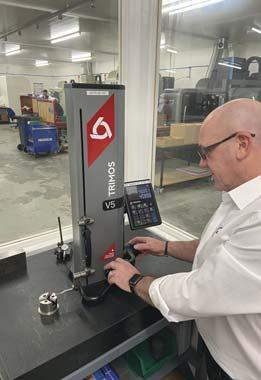
Precision Engineering offers a variety of services including CNC milling and turning, and new product development services including full mechanical design.
AES Precision has recently expanded its facility, including a full refurbishment, as well as investing in new machinery and processes to improve its services and strive for continual improvement in all areas of the business. Services include traditional 3 axis CNC milling and high speed 5 axis simultaneous milling, allowing AES Precision to produce complex, high precision components. 8 aes-engineering.co.uk ‘‘ We find the height gauge very accurate, and it has a great range of functions to suit our needs.
D Now Accredited to
FM10101
Manufacturers of High Quality Mill-Turned Parts
Turn-milling meets demand
Turn-milling investments at Martin Aerospace have helped it to meet a sharp increase in customer demand by dramatically reducing cycle times on tough aerospace materials
The Lanark-based supplier to the global aerospace sector installed a German-built Traub TNL32-9P sliding-head lathe two years ago and followed this with a Traub TNX65 fixed head lathe last year.
Supplied by Kingsbury, sole agent for the UK, Ireland and Middle East, the first machine started producing aerospace components from tough alloys 24/5 from the beginning of 2018.
It has been so successful at fulfilling an ongoing contract for producing aero engine components from titanium, Inconel and stainless steel that the business had no hesitation in returning to the same source for a fixed-head lathe. Installed in July 2019, the Traub TNX65 produces parts from Inconel and Nimonic for the same customer.
Both lathes have reduced multiple operations to one-hit production, making it much easier to hold the required tolerances, which are generally to within ± 0.01 mm although one pin diameter has to be turned on the sliding-head lathe to ± 4 microns.
At the same time, process cycles have been shortened dramatically, by over 90% in one case on the TNL32-9P and typically by 70% on the TNX65, added to which handling time and work-in-progress have been eliminated. Such significant savings are partly a result of the ability on both machines to have three tools in cut simultaneously, each having a different feed rate for optimum metal removal.
Neil Lawson, operations director at Martin Aerospace explained, "In 2017 a customer increased its annual requirement for five different parts, with quantities rising from a few hundred to 6,500 per part number. We were making them on a variety of twin-spindle turn-mill centres of sliding- and fixed-head design. "Such a sharp increase meant investing in a new turning centre to meet the demand and a sliding-head lathe was appropriate in view of the

shaft-type proportions."
Cutting strategies proposed by Kingsbury, balancing the cycle times on the main and counter spindles, allowed major cycle time reductions.
One two-operation cycle time of 6.5 minutes was reduced to a 1.2-minute single operation. In another case, a 55-minute three-operation process was cut to one 15-minute cycle.
All five parts are produced from bar to a process capability of Cpk 1.67, underpinned by 100% inspection, before they go for grinding and thread rolling.
Another component produced by Martin Aerospace that is required in increasing quantities is a nozzle for a borescope. Machined from an Inconel billet 63.5 mm in diameter, 70 mm long and weighing 2.7 kg, it needed 147 minutes for the completion of seven operations on horizontal and vertical machining centres and lathes, during which the weight was reduced to 0.7 kg. The
cycle time was cut to 65 minutes in a single operation on a twinspindle turn-mill centre already on the shop floor in Lanark, on which it was possible to have two tools in cut simultaneously, deployed by the two tool carriers.
To cope with higher volumes the TNX65 fixed head lathe was purchased and this triple turret machine with live tooling was able to make the part in one hit in just 25 minutes. 8 martinaerospace.com
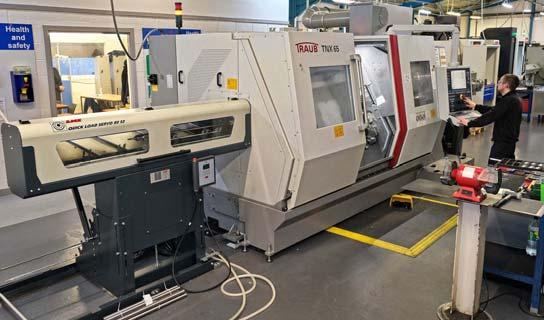
Wealdpark Limited
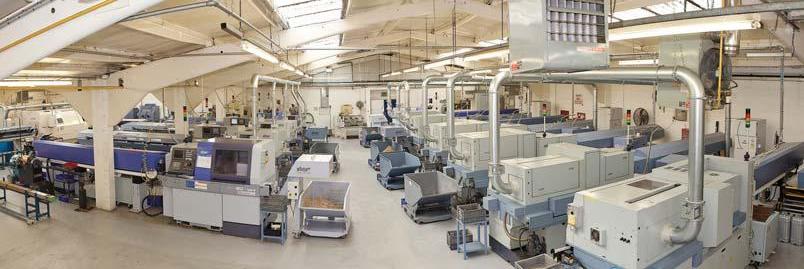
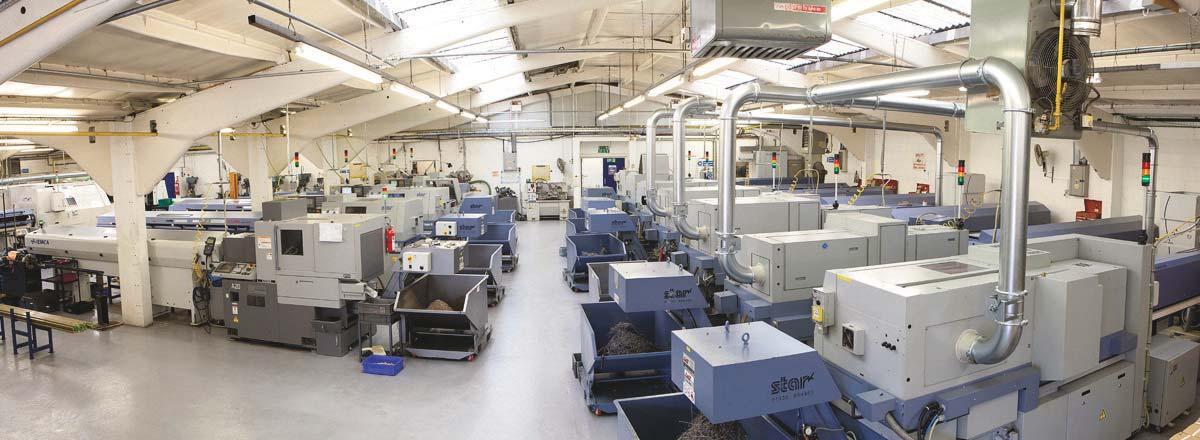

Stand number 5126
Subcontract Capacity
#.#MILL TURNFACILITIESUSINGSLIDINGANDFIXEDHEADLATHESWITH BARCAPACITYUPTOMMDIAMETER-IYANOFIXED HEADLATHESWITHBARCAPACITYUPTOMMDIAMETER(URCO VERTICALMACHINGCENTRE03,$ATATRACKMANAGEMENTSOFTWARE
BS EN ISO 9001:2008. Approved by BSI since 1991.
Company Contact Details
Phil Smith, Director, Wealdpark Limited Sutton Road, St. Helens, Merseyside, WA9 3DJ Tel. 01744 22567 / 732083 Fax. 01744 451339 E: sales@wealdpark.co.uk www.wealdpark.co.uk
The lockdown was no barrier to Cheltenham subcontractor Ferrositi investing in a new multi-tasking mill-turning lathe.
The Doosan SMX 2600S, with 13” chuck, 240 degree B-axis milling spindle, twin opposed spindles, Yaxis capability and 40-station turret was installed in May 2020, at a time when many companies were battening down the hatches.
The machine was supplied by Mills CNC, the exclusive distributor of Doosan machine tools in the UK and Ireland.
Says Nick Furno, Ferrositi’s managing director: “Ever since the company was created (in 2012) we have invested in multi-axis machine tools as a route to improving our productivity, operational efficiencies and competitiveness.
“We serve and operate in a number of global and highlycompetitive sectors and industries – aerospace, oil and gas, automated and special purpose machinery, high-profile architectural projects.
“Central to our success in these, and other sectors, has been our ability to machine high-quality
Visit our website or contact us for a quote or advice
Lockdown investment
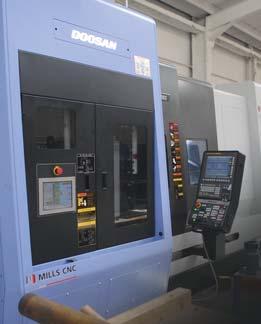
components and deliver them to customers on time, every time and within budget.
“The multi-axis machines we have at our disposal make us more efficient and enable us to make complex high-precision parts quicker, fewer machining operations and, often, in one set up.
“We are always on the lookout to add to, and strengthen, our front line machining resources.”
Despite the lockdown such an opportunity arose in April 2020 and resulted in Ferrositi making its first investment in Doosan machine tool technology, and coincidentally its first mill-turn machine acquisition.
Nick Furno adds: “The Doosan SMX 2600S complements our existing machine tool portfolio.
“Both Doosan and Mills CNC have good reputations in the market and, when I was informed that a mill-turn machine was available immediately from stock at a good, competitive price, I was interested.
“We have had the machine for about four weeks and, during this quieter-than-normal period, are spending time familiarising ourselves with its operations, functionality and its latest Fanuc control.
“Already we can see, and appreciate, that the machine is powerful, fast, flexible and accurate. We are particularly impressed with its rigidity, ergonomic design and thermal stability.
“Using a single set-up, the SMX is capable of performing multi machining processes. As a consequence, this means we can reduce production bottlenecks and limit stop-start operations.
“The SMX will help us consolidate and grow our position in existing supply chains and sectors, as well as helping us to spearhead our move into new sectors and industries - i.e. machining components for the food processing and medical sectors.” 8 ferrositi.com
Plastic machining specialist Stratos Precision Engineering has increased its turning capabilities with its first sliding head lathe.
The Citizen Cincom L32-VIIILFV twin-spindle, 35mm capacity, bar-fed turn-milling centre joined a plant list of five fixed-head, single-spindle chucking lathes for turning parts up to 650mm in diameter.
Purchase of the 7-axis CNC Swiss-type lathe was part of an investment of more than £1 million since the fourth quarter of 2018, which has also seen the arrival at the Gloucester-based company of a new big bore lathe and a 3m by 2m automatic tool change CNC router as well as refurbishment of the 8,000 sq ft premises.
Stratos' managing director Jonathan Caple said, "For some years we had been looking at buying a bar-fed lathe to increase our competitiveness, win new business and enter new industries by machining larger quantities of parts with tighter tolerances. We favoured the sliding-head type over fixed-head lathes, as the short axis movements lead to higher productivity. "The twin-spindle configuration and extensive driven tooling on the machine means one-hit production often supersedes two or three operations on different machines. "However, to reap the full benefits of the investment, we need to be able to leave the machine to run 24/7 either unattended or with reduced labour overnight to maximise production output.
Plastic turning capability added
"That was previously impossible for us due to the stringy swarf that is produced when machining plastic, which regularly needs to be manually cleared by an operator."
Now Citizen’s LFV (low frequency vibration) software breaks up the long strands of swarf normally generated when turning plastics into short lengths of just a few millimetres, preventing it from birds-nesting in the machining area and melting back onto the workpiece, which normally means scrapping the part.
A recent trend in the subcontractor's business has been a shift to machining more metals, notably aluminium for a large packaging machinery contract but also ferrous metals including stainless steel. This material also results in stringy swarf forming around the tool and workpiece and therefore benefits greatly from using Citizen's chipbreaking software.
The importance of improving turn-milling efficiency to increase competitiveness was reinforced when Stratos was required to produce 2,000 parts over a short period and the existing machinery would only achieve 400 per day. However, with the new slidinghead machine and LFV technology, Stratos is now able to produce the 2,000 parts in 48 hours. 8 stratosengineering.co.uk
