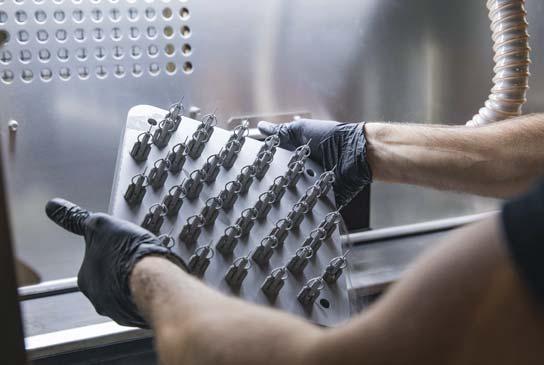
23 minute read
OIL & GAS
Protolabs has achieved DNV certification for 3D printed Inconel parts for the oil and gas industry.
The digital manufacturer worked closely with DNV to achieve ‘Qualification of Manufacturer’ certification. Protolabs is among the first manufacturers in the EMEA region to achieve the certification, and the first certified manufacturer using powder bed fusion technology in its additive process, which gives high resolution and geometrical accuracy.
Daniel Cohn, General Manager and 3DP Lead for Protolabs EMEA said: “Trust is, rightly, an important necessity for the Oil & Gas industry and also the wider energy sector. But now assurance can be given with the work we’ve conducted under the keen eye of DNV - the independent expert in risk management and assurance for the sector. Audits of our manufacturing facilities and processes prove that we comply with the general demands of the Oil & Gas industry so we can now move forward with even greater support for the sector as a whole.”
The certification applies to Protolabs’ direct metal laser sintering (DMLS) technology, specifically for the superalloy Inconel 718 – a high-strength, corrosion-resistant nickel chromium. Combining the exceptional properties of the material with Protolabs’ expertise in DMLS means the company can rapidly produce complex geometries for parts which are exposed to the harsh environments typical of the sector.
Achieving the certification is a process of technical evaluation of a number of probes within the machinery in combination with the material, individually and the system as a whole. The independent certification provides reliable proof that the probes meet the high qualification standard set out by DNV.
Dr. Sastry Kandukuri, Senior Principal Materials Specialist in DNV’s Energy Systems Business Unit, said: “I am very happy our Global Additive Manufacturing (AM) Technology Centre of Excellence was able to support Protolabs to reach this milestone, as the first certified manufacturer using powder bed fusion technology in their additive process. We look forward to continuing our relationship with Protolabs that gives the assurance and confidence of AM products as their use grows in the Oil and Gas and Energy industries.”
Certification of Protolabs’ DMLS process and its Inconel 718 superalloy provides a new level of assurance, but the company offers a variety of materials and technologies that are relevant to the Oil & Gas, Maritime and Offshore industries, as well as the broader energy sector.
Cohn continues: “We offer a number of metals and plastics for additive manufacturing, each suited to the specific needs of a project. We naturally see possibilities in the sector for Inconel 718 but also, in a less extreme temperature range, for Stainless Steel 316L. We also see possibilities with functional polymers in applications where conditions are not so extreme. The DNV certification applies to our Inconel 718 but we see it as testament to our quality process and expect to see that trust extend to our whole offering.” 8 protolabs.co.uk
3D print DNV certified
DNV has been awarded a contract to investigate whether offshore pipelines can be re-used to transport CO2 in carbon capture and storage projects in the Dutch North Sea.
The independent assurance and risk management provider has been awarded the contract for the carbon capture and storage (CCS) pipeline materials study by Neptune Energy Netherlands to assess the fracture and suitability of offshore pipelines for re-use in CO2 transport.
The pipeline materials analysis is part of a wider feasibility study being conducted by Neptune Energy, in cooperation with its licence partners and carbon dioxide (CO2) emitters, to review plans for a large-scale offshore CCS project at the Neptune-operated 10-area in the Dutch North Sea.
If the project is developed, it will be one of the largest CCS facilities in the Dutch North Sea and could meet more than 50% of the CO2 reduction being targeted by the Dutch industrial sector.
Prajeev Rasiah, Executive Vice President, Regional Director Energy Systems Northern Europe at DNV said: “We see CCS as one of the ways to accelerate the decarbonization of the energy sector. DNV is a pioneer in the field of CCS, with a track record dating back to the 1990s, and we are excited to be involved in a project of this size with Neptune Energy. With the potential to be one of the largest CCS facilities in the Dutch North Sea, at scale projects such as these will be significant for CCS technology advancement and cost reduction.”
René van der Meer, Head of New Energy at Neptune Energy said: “Given the existing infrastructure that connects offshore with onshore, there is real potential for the Dutch North Sea to develop new energy faster, more efficient and in a safe way. With support from partners, such as the experienced team of DNV, we are well placed to enable offshore CCS and offshore green hydrogen production using existing infrastructure. Using what is already there, will not only speed up new energy projects, but will cost significantly less and it doesn’t unnecessarily disturb the surroundings like the seabed.”
The first phase of the DNV study will identify the most advanced approaches to ductile fracture assessments in dense phase CO2 pipeline systems and the applicability of such assessments to both welded and seamless subsea line pipe.
The most suitable approach, identified in phase one, will be used in phase two of the study to assess the likely suitability of the existing pipelines for dense phase CO2 transport at up to 120 bar.
The output of the study will inform the ongoing Neptune feasibility study to provide an increased level of confidence in the suitability, or otherwise, of the existing pipelines which would be set to inject between five and eight million tonnes of CO2 annually into the depleted gas fields. 8 dnv.com
Green use for offshore pipelines
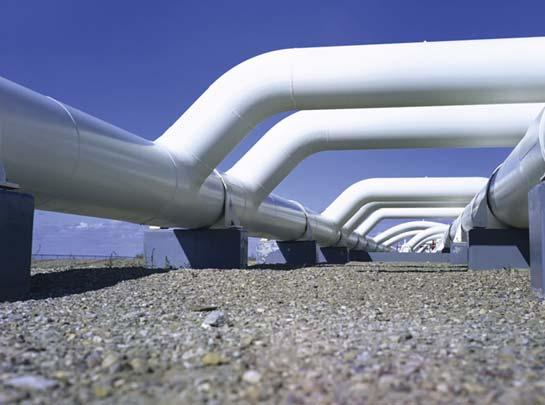
Northumberland-based Arcot Engineering has upgraded its capabilities by installing new 5-axis machining technology.
The company has invested in a Yamazaki Mazak CV5-500 5-axis machining centre, a machine the supplier says is ideally suited for engineering companies looking to make their first move into 5-axis work.
Arcot manufactures parts for a variety of industries and is particularly strong in oil and gas, torque tension tools and hydraulics.
Kevin Graham, Machine Shop Manager at Arcot Engineering, says that the investment will help the company break into new sectors requiring more complex machining work and also help to make Arcot much more productive.
“The company has a long history of working with vertical machining centres, but we’ve had ambitions to move into more complex and lucrative 5-axis work for some time,” says Kevin.
He continues: “The CV5-500 is priced at a very competitive level for subcontract manufacturers like ourselves but still has the usual Mazak build quality. The machine will help take on more complex work and get more jobs through the machine shop.”
Arcot Engineering was established in 1986 by the Graham and Mason families, who continue to be involved in the business that now employs 13 people at its Cramlington site in Northumberland.
“Our new 5-axis capabilities mean we can perform multiple tasks on one machine, which in
Upgraded to 5-axis machining
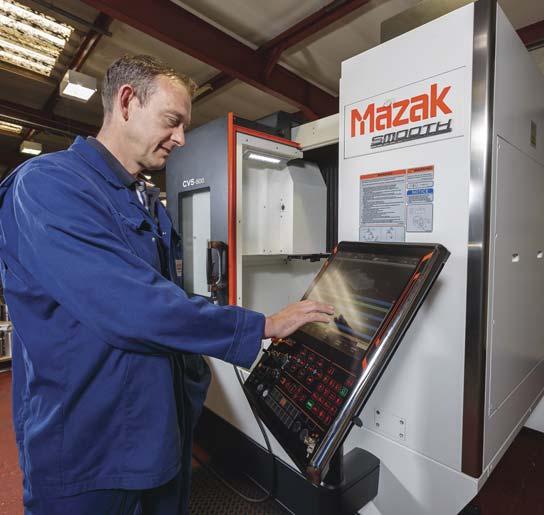
turn reduces setup times,” says Steve Mason, Machine Shop Floor Manager at Arcot Engineering. “We’re now doing three, four or five phases of a job in one setup and also reducing cycle-times by a minimum of 30 per cent thanks to the 12,000 rpm main spindle. This machine is going to make us much more competitive.”
The move into more complex 5axis work was aided by Mazak, one of the world’s leading manufacturers of machine tools, who provided a full week of off-site training. “The CV5-500 is programmed using Mazak’s own SmoothX control. I’ve never run a Mazak before but I’ve found the programming to be really easy and very user-friendly,” says Steve.
Alan Mucklow, UK Managing Director Sales and Service at Mazak commented: “One of the main reasons for developing the CV5-500 in the UK was the need to help subcontract manufacturers make the move into 5-axis work at an affordable price, whilst retaining the quality of machine that people expect from Mazak. It is a more complex type of machining but Arcot Engineering are showing what is possible when a company has the ambition to try and the will to make it work. I am sure that this investment will help Arcot break into new markets and improve the company’s machine shop productivity.” 8 Arcot Engineering
01670 735737
An ExoMars Rover will feature at Advanced Engineering UK as part of the show’s new Space & Satellite Engineering zone.
Over the two days of the UK’s leading engineering and manufacturing event, at the NEC, Birmingham on November 3 and 4, 2021, an original prototype of the ExoMars rover will be on display.
The Airbus Defence and Space UK prototype, commonly known as Bruno, is semi-autonomous and equipped with all the same technology as the final rover, including the sensors, actuators and cameras that allow the rover to see in 3D while navigating the red planet. The final flight rover will be equipped with a drill that can bore two metres deep, and metal wheels that have the same flexibility as rubber, without risking contamination to any life that it finds.
The ExoMars rover will be the first rover used to directly search for life on Mars as part of a joint mission between the European Space Agency (ESA) and Russia. The rover is just one example of how the UK’s engineering industry is leading the way in space and satellite innovation.
“Having Bruno at Advanced Engineering UK will be an extremely important moment for our engineering and manufacturing industry,” explained Aleiya Londsale, Head of Marketing at Easyfairs, organiser of Advanced Engineering. “This year’s Advanced Engineering UK gives our close-knit industry the chance to reunite and do business again and I can’t think of a better place to showcase Bruno’s technology and features. With exhibitor space almost full, and so many exciting speakers and features confirmed, people really can’t afford to miss this year’s show.”
This year, Advanced Engineering UK introduces a new show zone dedicated entirely to space and satellite innovation. The zone, which will be Bruno’s landing site for the show, will be part of Advanced Engineering UK’s existing Aero Engineering floor and will be supported by two of the show’s longstanding partners, the UK Space Agency and ADS Group. It will bring together the UK’s space and satellite manufacturers, research and development partners and supply chain businesses spanning R&D, design, test, production, manufacturing and advanced materials, showcasing the UK’s incredible achievements in this sector.
“ADS has always supported Advanced Engineering UK as it is one of the leading manufacturing and engineering shows covering multiple sectors,” explained Bhavin Vyas, Head of Space at ADS. “The UK’s involvement in space and satellite technology is constantly growing, so the dedicated area on the show floor this year provides a brilliant opportunity for this sector to showcase its innovative space capabilities. 8 advancedengineeringuk.com
Mars Rover lands at Advanced Engineering UK
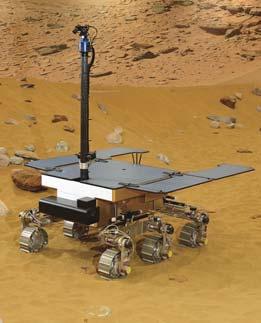
Visit our website or contact us for a quote or advice
CeramTec Group has produced ceramic sample containers for an Electro Magnetic Levitator used for experiments on the International Space Station.
In the course of this and previous joint product developments, CeramTec, together with Airbus Defence & Space and other partners in a project consortium, developed sample containers for experiments as complex components and manufactured them at the Plochingen site in Germany.
The latest pot sample holders and cage sample holders, which are made of silicon nitride, follow a previous lot of containers that were first installed in the International Space Station (ISS) back in 2017. They are used in the so-called Electro Magnetic Levitator (EML), a multi-purpose research facility for natural science experiments on board the ISS.
In the EML, the sample containers are inserted into a coil in which metal alloy samples are fixed all around in a contact-free manner by electromagnetic fields while suspended in zero gravity. For analysis, the samples are melted, cooled in the liquid state and then solidified again. These precision measurements of certain thermophysical properties of metals, alloys and semiconductors, which are not possible on Earth, make it possible to analyse the early phases of the formation of material structures and to expand our understanding of transition processes, atomic structures and material properties.
The objective here is to improve production and casting processes on Earth thanks to the material properties measured in space, in order to achieve an increase in quality while reducing the cost of high-tech castings (e.g., engine blocks).
This will allow manufacturing methods to be refined and materials and products to be improved and redeveloped. This basic research is being carried out by a collaboration between Airbus Defence & Space and the European Space Agency among others.
The ceramic material silicon nitride (Si3N4) is particularly suitable for this purpose due to its zero electrical conductivity, which prevents external influences on the measurements, as well as the required high heat resistance as the measurement cycles take place in temperature ranges between 500 and 2100°C.
The company says that these properties, in combination with the absolute reliability and consistently high product quality it can provide, have once again convinced the project consortium to use CeramTec advanced ceramics for what is perhaps one of the most demanding applications in the universe.
The sample containers of this latest generation started their journey into space with the SpaceX-22 in June 2021 and will significantly support further research activities there. 8 ceramtec-group.com
Advanced ceramics for space
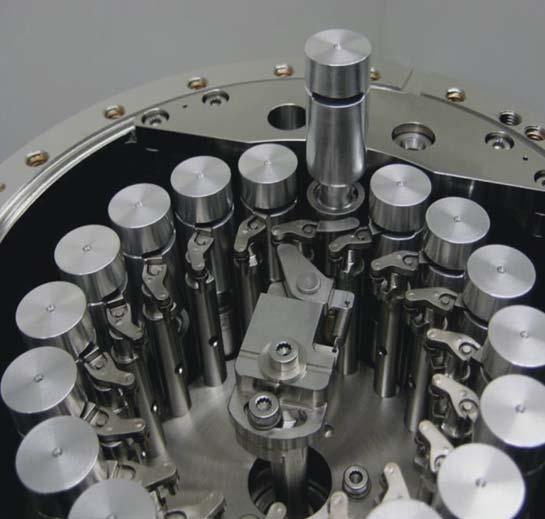
Advanced surface coating technology specialist Hardide Coatings Ltd has received full approval from Airbus to coat and process its components at the company’s new and larger Longlands Road facility in Bicester, UK.
This approval follows the relocation of the Company and its equipment from Wedgwood Road, Bicester to newly built premises at Longlands Road, Bicester last year. The final coating reactor
Airbus site approval
that remained in the Wedgwood Road site specifically to coat Airbus parts has now been relocated to the Longlands Road facility. The old Wedgwood Road site is now in the process of being decommissioned before the lease terminates in October 2021.
Commenting on the approval, Philip Kirkham, CEO of Hardide plc, said: “This approval is very positive news and is the result of extensive testing and verification by Airbus of all the processes at the newly built Longlands Road facility. The Airbus approval is testament to our coatings’ capabilities and means that we can now close the door on our old premises and concentrate all our aerospace processing at our modern and much larger, custom-fitted new site.” 8 hardide.com
Wealdpark Limited
Stand number 5126
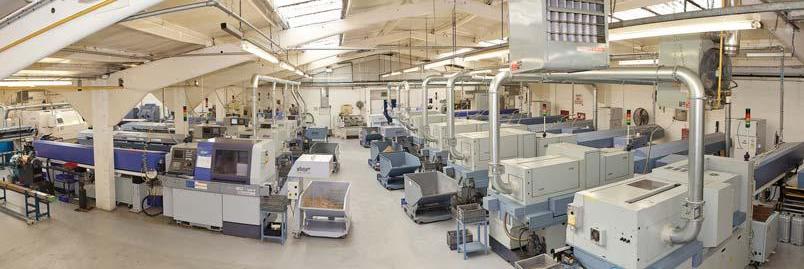


Subcontract Capacity
BS EN ISO 9001:2008. Approved by BSI since 1991.
Company Contact Details
Phil Smith, Director, Wealdpark Limited Sutton Road, St. Helens, Merseyside, WA9 3DJ Tel. 01744 22567 / 732083 Fax. 01744 451339 E: sales@wealdpark.co.uk www.wealdpark.co.uk
Rawtenstall-based RPS Precision Engineering has invested in a new Doosan multi-tasking twin-turret, twin-spindle turning centre to enhance productivity and performance.
The machine, a Puma TT1800SY, was supplied by Mills CNC along with a servo-driven Hydrafeed MSV 110 bar feeder as well as a number of differentsized collet chucks and adaptors.
The package allowed the new machine to be ready for full production as soon as its installation, commissioning and training had been completed.
It is now being used to machine a range of complex, highprecision parts, in medium batch sizes, for a number of customers.
RPS Precision Engineering (previously Rochdale Production Services) was established in 1988 by Michael Sirrell and his father Bryan.
The independent, family-owned business specialises in machining complex, high-precision parts from prototypes and one offs through to small, medium and large batch production.
To add value and strengthen its position within customers’ supply chains, RPS has augmented its precision machining services with TIG welding, fabrication and assembly.
RPS also provides a range of ‘Design for Manufacturing’ services that includes consultancy, 3D modelling and rapid prototyping.
Michael Sirrell said: “The TT1800SY is a productivity powerhouse of a machine. It might appear small from the outside - but its twin-spindle, twin-turret configuration is helping us machine highprecision components quickly and accurately…in one hit.
“Furthermore, by integrating the machine with a servo-driven bar feeder, we have created a ‘de facto’ automated manufacturing cell that is both efficient and reliable, and that we are able to run, unattended, during the day.
“In the near future, when we fully embrace lights-out operations and run the machine unattended overnight and over the weekends, the productivity benefits will be even more impressive.”
Mr Sirrell said: “A significant percentage of the parts we turn are small and have short cycle times. They are made from materials that include hardened and mild steel, aluminium, stainless, copper, bronze, brass and plastics. And they are machined to tight geometric tolerances – generally 0.002mm – and high surface finishes, in relatively high volumes.
“The profile and characteristics of parts being machined led us, at the beginning of the year, to consider investing in our first sliding head machine. And, because Mills CNC supply Doosan Swiss-Turn machines, we naturally approached them for advice.”
An audit into what RPS wanted to achieve from the new investment was undertaken and completed. The results caused a change of direction.
“On the advice of Mills CNC engineers we changed our investment plans and opted, instead, for a multi-tasking (fixed head) turning centre as opposed to going down the sliding head route.
“We believed that the multitasking turning centre integrated with a bar feeder would provide us with more flexibility and, because we were already familiar with fixed head lathes with Y-axes, driven tools, twin spindles etc., we could hit the ground running quickly,” concluded Mr Sirrell. 8 rps-engineering.co.uk
Multi-tasking for productivity
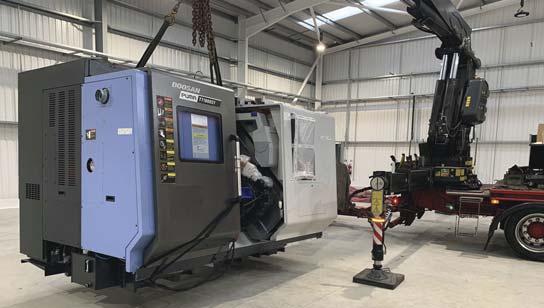
Thread-rolling specialist Dobson & Beaumont has invested in a new twin-spindle turning centre that will enhance its capabilities when processing challenging materials.
Thread rolling is a process that cold forms threads to work harden the thread, strengthen the grain flow and improve overall thread strength by more than 25% when compared to typical thread cutting operations. Before thread rolling, Dobson & Beaumont has to machine some of the most challenging materials known to the industry – this is one of the many reasons the company has just purchased a Nakamura-Tome AS200 twin-spindle turning centre from the Engineering Technology Group.
Managing Director Richard Guest said: “We machine a lot of parts in batches that can vary from 4 or 5-off through to 50, 100 and beyond, and our turning centres were all single spindle machines. This meant that most of our turned parts required secondary operations. We knew we needed a twin-spindle turning centre to reduce secondary operations.”
The company increasingly processes challenging materials such as titanium, Inconel, stainless steel, super duplex and Duraheat to tolerances in the region of +/-0.0125mm, with the thread rolled parts often being critical components in their respective assemblies.
The Nakamura-Tome from ETG was supplied as a long-bed version for our 400-500mm parts with a bar feed, part catcher and the twin spindle for one-hit machining.
Installed at the Lancashire company in April, the new Nakamura-Tome AS200 has reduced the cycle time for a number of parts, including connecting rods, from 150 seconds to just under a minute on parts that used to require a secondary turning cycle to complete the parts. The company has also reduced the cycle time of doubleended bolts from 1 minute 30 seconds to less than 45 seconds.
The most dramatic saving has arrived on hexagonal head bolts where the cycle time has fallen from 8 minutes to 1minute 30 seconds.
Richard Guest said: “We produce a lot of bolts where we have to machine the hexagonal heads, and this is a perfect example of the savings that we can achieve with the NakamuraTome machine. The combination of twin-spindle machining, powerful and robust milling capability and automated production through the bar feed and part catcher has made a significant difference on this component – and it will do on future parts too.” 8 dobsonandbeaumont.co.uk
Thread rolling capabilities
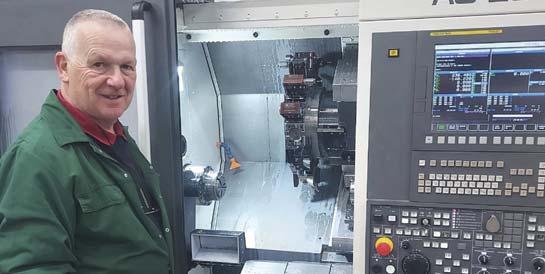
PRECISION ENGINEERING
Aerospace Oil & Gas Nuclear Defence
www.thomas-brown-engineering.co.uk
Tel: 01484 548903
Automotive Electronics Hi Fi Industrial & High Volume Machining
Witon Engineering’s new 25mm bar capacity Citizen sliding head turning centre is taking work off bigger machines and cutting cycle times by 20%.
At Witon’s subcontract machining facility in Barnstaple, turn-milling of relatively complex components from 16 mm diameter bar used to be carried out on 32 mm capacity slidinghead lathes, rather than smaller capacity models, to take advantage of the extra CNC axes and tools available on the larger machines.
This type of work has now been transferred to a nimbler, 25 mm bar capacity Citizen Cincom D25VIIILFV sliding-head turning centre, installed in January 2021. The first two jobs have shown significant cycle time reductions of 20% or more.
Since the mid-90s, the contract machinist has bought 17 bar-fed lathes from Citizen UK, of which one was a 42 mm bar capacity Miyano fixed-head machine, the others being various Cincom sliding-head models for turning up to 32 mm stock. There are currently 11 Citizen machines on the shop floor, earlier models having been exchanged over the years. Lathes from this supplier therefore account for approaching half of the 25 bar autos in the factory, comprising 13 sliding-head models, eight single-spindle fixedhead turning centres and four CNC multi-spindle automatics.
The first component to be transferred to the D25 was an EN1A steel shaft for a lawnmower. The part was formerly produced on an L32-VII, of which there are three on site. As 180,000 have to be produced to fulfil the current contract, the 20% cycle time reduction leads to a significant production cost saving.
The second component benefiting from being machined on the D25 is a 304 stainless steel fuel inlet fitting for an automotive customer. It used to be turn-milled on one of a pair of Cincom M32s in a cycle time of 72 seconds. This has been cut to 53 seconds, representing a 26% saving. With 55,000-off needed, the economy gained is significant.
Ian Clapp, workshop manager at the Barnstaple factory explained, "We operate a couple of 20 mm capacity, dual-platen sliders of another make and knew this configuration offered quick cycle times. "However, we saw what our longstanding sliding-head lathe supplier Citizen was offering in the D25, a machine with larger bar capacity plus the ability to carry out work up to 32 mm diameter without the guide bush for more economical material usage when producing shorter components. "The model also has the benefit of a programmable B-axis, so we decided to go for this option." 8 witoneng.co.uk
New slider cuts cycle times
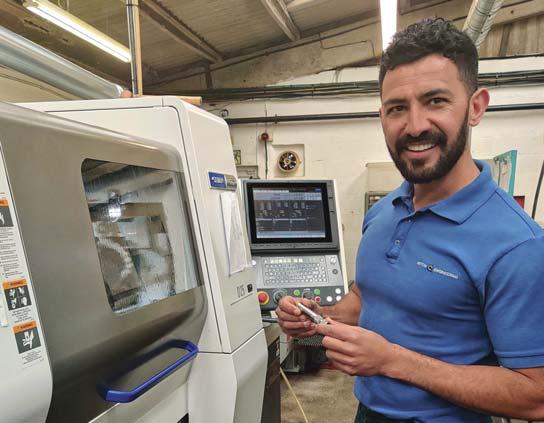
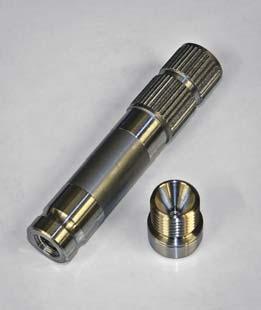
Sheet metal specialist BIZ Engineering, which can trace its origins back to 1816, has invested in the latest laser cutting technology.
In order to meet growing demand it has replaced its previous CO2-based technology with a 3kW TruLaser 1030 fibre laser cutter.
The machine is designed as an entry-level system, while providing high levels of capability, productivity and quality
BIZ Engineering is remarkable in that its history is traceable back to 1816, when it began trading initially as a builders’ merchant from the Commercial Road in Shoreditch, East London.
“We are currently growing yearon-year, which is testament to our investment programme, ongoing diversification and commitment to customers – existing and new,” explains Paul Jones, who joined the company in 2017 as managing director following over 30 years of experience in precision sheet metal and other engineering sectors.
Whilst BIZ Engineering offers a range of subcontract manufacturing services, including CNC punching, routing, bending, welding and shot blasting, the company’s latest investment drive has centred on laser cutting. Two new fibre-laser machines have arrived in the past 18 months, the most recent of which the Trumpf TruLaser 1030 fibre.
“When I arrived, we had two small Trumpf CO2 lasers which were 18 and 20 years old respectively and, although still operational, we took the decision to replace them with fibre-based machines,” explains Mr Jones. “In comparison with our CO2 machines we knew fibre would be around five times faster, provide more capability and cut running costs by two-thirds.”
“We installed the TruLaser 1030 fibre in November 2020, and since then it has become a great asset to our business,” states Mr Jones.
On a daily basis the company is using its recent arrival to process aluminium up to 12mm thick and stainless steel up to 15mm, as well as many different gauges of mild steel.
The 3kW TruDisk laser supplied with BIZ Engineering’s TruLaser 1030 fibre allows users to cut all common type of sheet metal, quickly and to a high standard.
The TruLaser 1030 at BIZ Engineering produces parts in batch sizes from 1-off to 300-off, 12 hours a day, with plans afoot to extend the current single-shift working pattern. 8 bizengineering.com
Laser does the BIZ
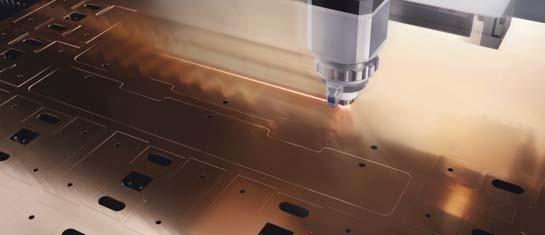

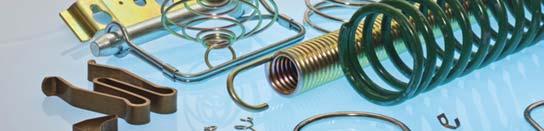
From design, sampling and technical support to manufacture, Simpson Springs & Pressings Ltd provide the complete service.
Tel: 0118 978 6573 Email: sales@simpsonsprings.co.uk
Kloeckner Metals UK has been awarded a multi-million pound contract by BYLOR to produce embedment sleeves for the Hinkley Point C power station.
Part of the global Klöckner & Co Group, Kloeckner Metals UK is a leading multi-metals processing supplier in the UK. It has recently been certified with Fit 4 Nuclear status (F4N) which is a testament to its commitment to continuously improve operational standards in line with nuclear requirements.
This newly awarded contract will see Kloeckner Metals UK supply processed and coated embedment sleeves to Tier 1 Contractor BYLOR – a Laing O’Rourke and Bouygues TP joint venture. Two local South West businesses will assist Kloeckner Metals UK with the coating of the embedment sleeves.
Abingdon-based pressurevessel fabrication specialist LTi Metaltech has acquired Bridgend-based Vessco Engineering Ltd.
The former owner of Vessco Engineering, Julian VanceDaniel, is remaining in the combined group in a senior business development role.
The deal, worth £2.6m, will bolster the company’s capabilities and facilitate access into a number of key sectors, including nuclear energy, oil and gas, utilities and food processing, having itself completed several prestigious projects including specialist fabrication assignments with Tokamak
Multi-million Hinkley Point C win
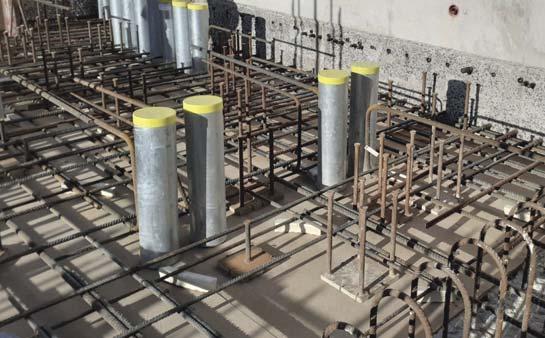
Peter Whiting, CEO of Kloeckner Metals UK said: “BYLOR’s decision to select Kloeckner as their supplier is a huge endorsement for our capabilities and management expertise. We are extremely excited to be part of such an important national project.”
Kloeckner Metals UK thanked Somerset Chamber of Commerce and SWMAS for their contribution on the project. 8 kloecknermetalsuk.com
£2.6m fabrication acquisition
Energy & Reaction Engines.
Founded in 2006, Vessco Engineering Ltd is a Tier 2 supplier to the turbine hall at Hinkley Point C, supplying large pressure vessels for GE Power Systems.
German-owned LTi Metaltech is a major supplier to Siemens in the manufacture of pressure vessel components for its market leading MRI Scanners. Under the leadership and direction of its UK managing director, Edgar Rayner, has broadened the scope and market reach of the £23m business including the hydrogen technology and aerospace sectors.
The acquisition will enable LTi to accelerate its expansion programme as it diversifies its portfolio whilst underpinning existing capabilities in medical technology.
Commenting on the acquisition, Edgar Rayner, said: “Vessco Engineering has built up a great reputation and we’ve had it on our radar for some time. We are obviously delighted to be able to bring it into the LTi family where our combined resources and capabilities will help to broaden and strengthen our offering in a range of important industry sectors.” 8 lti-metaltech.com