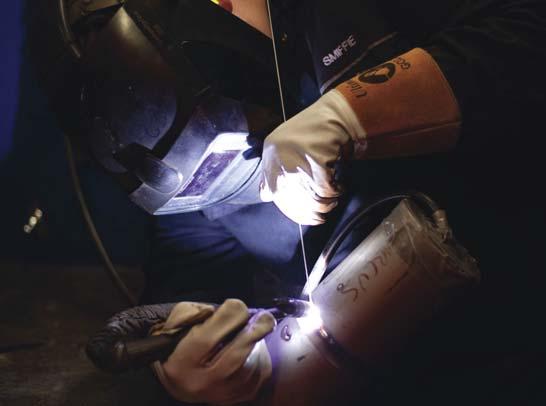
8 minute read
FORMING FABRICATION
Stainless Metalcraft (Metalcraft) is to enter into the second phase of a contract to provide high integrity stainless steel storage boxes for Sellafield.
The 3M3 (three metre cubed) box contract is now worth up to £70m and represents an approximately £20m uplift to the original contract awarded in 2015. The agreement to exercise the option marks Metalcraft’s successful transition to the second phase of the 3M3 box work with Sellafield.
The boxes will be used to store intermediate level waste (ILW) retrieved from silos at legacy locations in Cumbria.
As part of this transition, Metalcraft will be producing circa 1,000 boxes over phase two of the programme, which is currently expected to take 6 years
Austen Adams, managing director of Avingtrans’ Process Solutions and Rotating Equipment division, which includes Stainless Metalcraft, said: “Moving on to phase two of the contract is just reward for the hard work and expertise the team has put into developing the 3M3 programme over the last five years.
“Having proven the technology and manufacturing processes involved, we are now in a position to ramp up production and begin the transition towards volume production, which will enable us to support Sellafield in this essential decommissioning work over the coming years.
“Metalcraft and Avingtrans are proud to be working alongside a number of suppliers and the Nuclear Decommissioning Authority on the project of decommissioning the Sellafield nuclear site, in a way which is both safe and environmentally friendly.”
Susan Lussem, Supply Chain Director, Sellafield Ltd, said: “Retrieval of wastes from Sellafield’s legacy ponds and silos is nationally important work, and we’re dedicated to ensuring this is done as safely, quickly and costeffectively as possible.”
“Moving the waste into modern storage will mean a huge reduction in the UK’s nuclear hazard, but before we can remove the waste, we have to be confident we have somewhere safe to put it and that we have a reliable supply of containers for decades to come.”
“The development, innovation and investment that Sellafield Ltd and Metalcraft have delivered on this project to date gives us this confidence.”
Steve McQuillan, CEO of Avingtrans PLC, said: “Winning the initial contract back in 2015 was a landmark moment for Metalcraft, allowing us to invest significantly in both infrastructure and personnel to create a world-class centre for the manufacture of ILW containers, and boosting our apprenticeship programme. This training programme can now be securely extended for the long term, providing skilled engineering apprentice roles in a relatively deprived area of the UK.”
“Securing the next phase of works wholly justifies that investment and vindicates the Board’s decision to refocus what was our Energy and Medical Division on new markets. Sellafield’s trust in Metalcraft to deliver this next phase of the project endorses the quality of our management processes in this highly sensitive technology.” 8 metalcraft.co.uk
Phase two Sellafield box contract
In the past two years, MJH Fabrications has invested in two automated 9kW fibre laser cutting systems and two press brakes.
The equipment was supplied by Amada UK and comprises two ENSIS-3015AJ 9kW fibre laser cutters with MPF load/unload automation systems and two HFE3i series press brakes.
This significant capital investment is helping the company to better serve its UKwide customer base in sectors that include shop-fitting, agriculture, yellow goods and factory automation.
Mike Hemming formed MJH Fabrications in 1990 with little more than a MIG welding set but by the time it was incorporated as a limited company in 2002 it was supplying finished fabrication and components to customers’ requirements.
Driven by its success, MJH Fabrications has grown to become a progressive subcontract fabrication specialist with £2½ million annual turnover, 20,000 ft2 premises and 18 employees. And, as the company’s recent investment programme indicates, Mr Hemming has no plans on stopping there.
“Our investments with Amada reflect my determination to continue increasing capacity and moving forward,” he states. “The most recent ENSIS arrived in spring 2020, just when the COVID19 pandemic forced the UK into its first national lockdown. It was a worrying time but we opted to press ahead. As things turned out, it was the best decision as our workload just seemed to get busier and busier from there on.”
The company’s entry into laser cutting arrived a number of years ago when it acquired a secondhand machine. A number of other preowned laser cutters followed before MJH Fabrications purchased its first new model: an Amada F1 4kW CO2 laser with automation tower.
“With the industry transitioning from CO2 to fibre laser technology, it made sense to think about new investment,” explains Mr Hemming.
“To be competitive we knew that adopting fibre technology was the only option and, sure enough, we immediately noticed a difference in speed capability with the new ENSIS – it’s unbelievably fast.”
In December 2019, the company decided to boost its bending capacity and help keep pace with the new laser cutter. As a result, MJH added HFE3i-1003 and HFE3i- 5020 press brakes to its existing HD-1003 and HFE-1704 machines. The company also leverages the benefits of AMADA software for both its press brakes and laser cutters.
“We quickly reached our threshold with the first ENSIS and found ourselves running flat-out day and night,” explains Mr Hemming. “We were constantly under pressure, so it was time to take action and acquire a second ENSIS machine an identical 3015AJ 9kW model.”
“We work closely with customers to make sure their components and our manufacturing operations are optimised in line with demand.
“Essentially, we want to offer the most cost-effective way of achieving customer requirements. Having the capabilities of the Amada ENSIS laser cutters and HFE3i press brakes makes this process all that bit easier.” 8 mjhfabrications.co.uk
Fabrication system investments
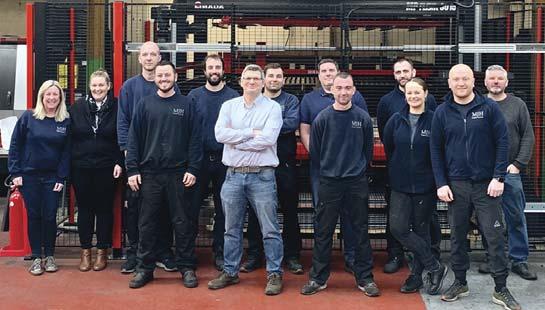
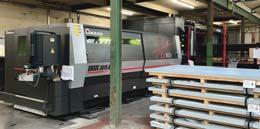
There are multiple benefits from using subcontract rotary friction welding (RFW), including the ability to draw on proven expertise and access industry-leading friction welding machinery without the need for capital investment. A multitude of components can be manufactured across numerous sectors in a range of geometries and material combinations. The subcontractor can advise on materials, geometry, metallurgy and pre and post weld processing.
In the case of bi-metallic, copper-aluminium connectors, there is simply no other viable method of joining these two materials directly thanks to their very different thermal expansion coefficients. Low-cost aluminium is joined directly to high cost copper. Other than the obvious benefit of cost reduction by reducing the use of expensive high conductivity copper, direct costs, waste and the increased threat of theft are also reduced. Aluminium does not impede conductivity and is useful for ease of crimping to electrical cabling. The electrical connector market for power distribution and rail is a significant market for this process.
RFW is a standard bonding method in the automotive sector for producing axles, CV joints, turbo-chargers, airbag canisters, while the aerospace industry uses RFW to manufacture landing gear shafts, steering shafts, ejector seat components and other high integrity parts. The construction industry uses friction welding for piston rods and hydraulic cylinders,
Subcontract rotary friction welding
where large diameter high quality steel chromed rods are joined to eyes, yolks and pinions for heavy duty industrial service.
RFW also shows its strength in oil, gas and mining applications where joint integrity in the harshest conditions is paramount, such as drill pipes and rods for deep hole water boring, directional drilling and rock drilling.
The cost of failure in these components can literally cost the operators millions of pounds in lost revenues. The integrity of the friction welded bond is so superior to other joining processes that most OEMs across these industries own and operate their own rotary friction welding equipment to produce their safety critical components in-house.
Cryogenic applications also benefit from the processes’ ability to join dissimilar materials. For instance, stainless steel to copper and interlayered transition joints consisting of stainless steel welded to titanium with an aluminium alloy interlayer.
Friction welding has also proved highly successful for welding tools, such as drill bits for example. Stronger than conventional welding, friction welded drill tools have an enhanced join integrity, as the weld is as strong as the parent material.
Whatever the sector, or application in which the component shall be utilised, rotary friction welded products have proven to have an enhanced structural integrity.
The question that engineers and manufacturers ask when considering their production joining and manufacturing processes is can we do this better, cheaper and more efficiently?
The answer is ‘yes’ and the solution lies in subcontract friction welding. 8 kuka.com
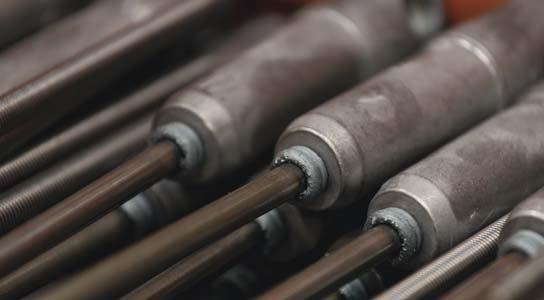
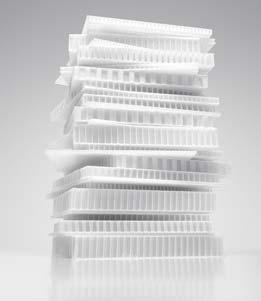
Efficiency beats material problems
Resource-efficient production has helped lightweight honeycomb core manufacturer ThermHex keep raw material usage to a minimum and overcome supply problems.
Since the beginning of 2021 there has been a shortage in raw plastic materials. This has resulted in an exponential increase in their price. The cost of polymer resins
engineering, composites
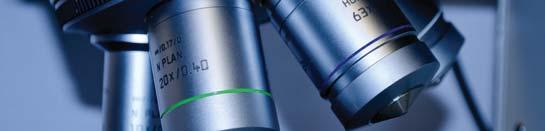

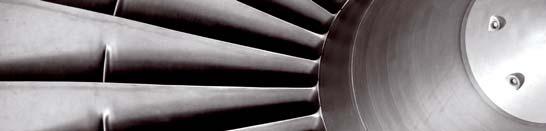
PR | Marketing | | Copywriting | Events Awards | Design | | Web & SEO
01752 894786 www.aroprandmarketing.co.uk used to make plastic rose by a quarter between December 2020 and May 2021, the highest price in the last six years.
More than 90% of plastic converters within Europe were directly affected by the supply crisis. This has resulted in many companies having no choice but to take on little to no new business and only able to honour agreements with their existing customers.
Recyclates specifically have seen a huge decrease in availability at sufficient quantities and a consistent level of quality. This has led to increasing in price and decreasing in availability for both virgin and recycled polymers.
Fortunately for ThermHex its highly automated and patented production process of polypropylene honeycomb cores and Organosandwich have barely been impacted. Its production process for honeycomb cores is continuous and saves resources by using much less raw material compared to monolithic materials, like plywood.
Dr Jochen Pflug, CEO of ThermHex said “The shortage of raw materials over the past few months has been difficult for the entire industry. Using of the sandwich construction principle makes especially sense in times of material shortage. Our ThermHex honeycomb cores help customers, which require only thin skins to make stiff and thick panels and can thus contribute to solve the recent shortages of raw materials”. 8 thermhex.com