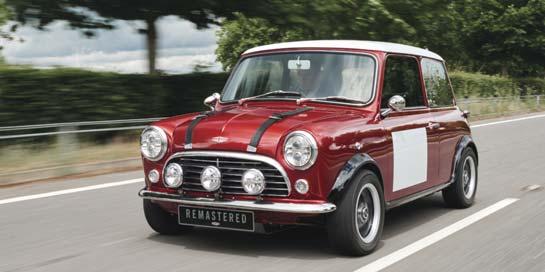
23 minute read
Remastered Mini
Cable loom and harness manufacturer, Convert Ltd, is working with David Brown Automotive to supply full car-sets of cable harnesses for its Mini Remastered model.
Mini Remastered by David Brown Automotive pairs the original, unmistakable body of the classic Mini with modern luxury touches such as LED headlights, an infotainment system and engineered and hand-crafted interior and exterior details.
After some months of careful review and development of plans to prove the quality of Convert’s parts and manufacturing process, the production of samples and performing quality checks, the first production ready cable harnesses have been fitted into the latest Mini Remastered cars to leave David Brown Automotive’s build facility in Silverstone, Northamptonshire.
The next year could see Convert produce harnesses for over 100 Mini Remastered models with 200 Mini Remastered vehicles predicted to be produced in the following year.
The cable harnesses will be fitted across the entirety of Mini Remastered, from engine control, through all the model’s interior, and to the boot harnesses and rear lights. In total, there will be around 500 metres of wiring with 650 multi-branched connection points, across 9 individual harnesses.
Dave Lord, managing director of Convert said: “When we were approached by David Brown Automotive to help with their Mini Remastered model, we knew that we could apply our sharp technical expertise to such a bespoke project. The classic Mini is such an iconic British car that everyone at Convert was very excited to get stuck in to design and prototype production.
“David Brown Automotive’s manufacturing is so precise and authentic to the original Mini; so much so that the wiring is the exact same colour as when the first car came off the production line in the 1960s.”
Rikki Dillon, Operations Director at David Brown Automotive said: “Convert’s highly precise engineering capabilities, partnered with their particular care and attention to detail was something that appealed to us when choosing a supplier. This is something that encompasses our ethos in creating each Mini Remastered.”
Operating predominantly in the automotive, public transport and scientific/medical sectors, Convert manufactures wire cables and harnesses for prestige automotive headlamps and rearlamps, heavy plant & machinery vehicles, passenger control systems for the rail & air industry, transmission and driveline systems and a range of scientific equipment. 8 convertltd.co.uk
davidbrownautomotive.com
Remastered Mini all wired up
PRECISION ENGINEERING
Aerospace Oil & Gas Nuclear Defence
www.thomas-brown-engineering.co.uk
Tel: 01484 548903
Automotive Electronics Hi Fi Industrial & High Volume Machining
Private equity buyer for Formaplex
Lightweight component specialist Formaplex has been acquired by UK Private Equity fund Elaghmore.
The company is an integrated manufacturer and supplier of lightweight component solutions to the global automotive, motorsport, aerospace, medical and defence markets.
The business started as a specialist tooling partner for the F1 motorsport sector before adding injection mould tooling and moulding to its skillset and developing expertise in composite components. Formaplex employs over 500 employees, and, following the acquisition, the business will continue to be led by Mike Bryant, CEO. 8 formplex.com
Visit our website or contact us for a quote or advice
Castings technology MBO

Castings Technology International Ltd (CTI), which provides manufacturing, technology, expertise and services to the cast metals sector has completed a management buyout from the University of Sheffield.
The company has casting capabilities in almost any type of metal alloy and has a 1,200kg titanium vacuum melting capability, which ranks it as one of the largest in the world. In conjunction with customers’ design teams, CTI is casting complex components supplied into the aerospace, defence, chemical nuclear and marine markets.
CTI has completed a £2m fundraising.
The funding raised will allow the company to expand more rapidly by investment into further product development, alongside sales and marketing infrastructure and resource, to expand throughout its world-class manufacturing facility, which is based at the University of Sheffield Advanced Manufacturing Research Centre (AMRC).
The management team is led by Richard Cook, Managing Director and Kevin Parkin, Chairman.
Kevin Parkin said: “This is a unique opportunity to develop and grow this highly efficient manufacturing capability now that the equipment, processes and quality systems have been fully developed and accredited. Working alongside our AMRC neighbours, together with the superb research and development initiatives provided by the University, will give CTI an enviable position in the global supply chain.” 8 castingstechnology.com
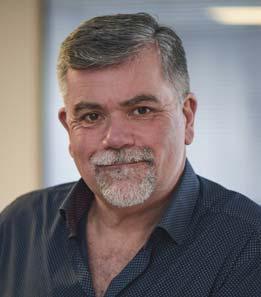
John Atkins
has joined Hampshire precision engineering business RHH Franks as Sales Director. From an early career in engineering to more than 20 years in business management and sales, John has extensive experience across a range of sectors, including defence, aerospace and technology.
Tony Sexton
has been appointed Group Sales Director at Nasmyth Group. He joined the Group in 2007 as Managing Director of IEC and has more recently held the position of Director of Systems and Defence for both the Nasmyth IEC and Nasmyth CE businesses.
Phil Brown
has been appointed as a rail industry consultant by Salamander Fabrications to strengthen its position in the transport sector and secure large-scale project work. He has 30 years’ experience and has worked with OEMs, Tier 1 companies, SMEs and trade associations.
Colin Maver
has joined offshore engineering and fabrication specialist R&M Engineering as Managing Director and will help capitalise on strong growth opportunities. He was Group Director of Dron & Dickson for 16 years, gaining extensive market experience in UK, Brazil and UAE.
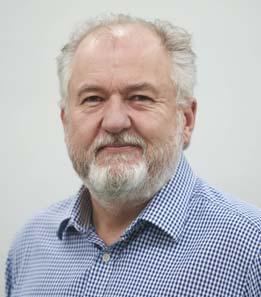
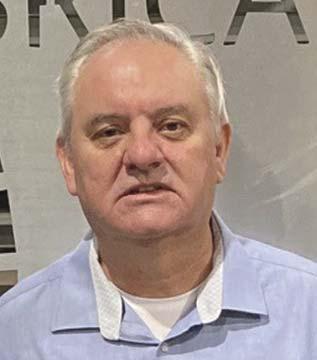
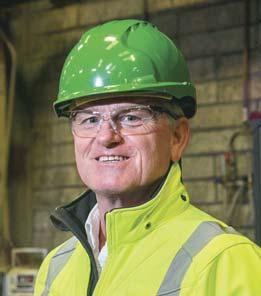
Trade Leads from the EIA
The following FREE OF CHARGE trade leads for the UK engineering industry are currently appearing on the Trade Board pages of the Engineering Industries Association at www.eia.co.uk
India: BSVI (Euro 6) sensors
A company requires sensors for BSVI (Euro 6) emission standards.
Reference: 34824
Closing Date: 31/12/2021
Poland: Cable assemblies
Polish manufacturer of electric wire harnesses, cable assemblies and power cords is looking for a manufacturing agreement for power cords with overmoulded plugs and assembly services for electric elements.
Reference: JV147
Closing Date: 19/02/2022
Spain: Recycled plastics
A Spanish university has developed a procedure for the decontaminationof recycled plastic materials, improving their quality to be used in high added value applications. It is looking for licence agreements and techical cooperation.
Reference: JV1469
Closing Date: 03/10/2021
Ukraine: Paper from leaves
A Ukrainian research and production company which developed a technology for production of pulp and paper made of fallen leaves is looking for partners to establish joint venture or license agreement.
Reference: JV1471
Closing Date: 30/06/2021
For more information please email head.office@eia.co.uk quoting reference number.
Please remember to use due diligence in responding to Trade Leads. Engineering Capacity provides you with the above information in good faith, but is unable to accept any responsibility or legal liability arising from any use of these leads.
The maker of an advanced modular jet trainer for the RAF, which could create 3800 supply chain jobs, has joined NDI, the defence, security, space and aerospace division of Make UK, the manufacturers’ organisation.
AERALIS is building the world’s first modular military aircraft involving a common fuselage and a range of alternative wings and engines to optimally deliver a range of military missions that previously required a range of different aircraft types. The company is looking to revolutionise the way that flying training is delivered, and will seek to support the UK’s future Combat Air System programme.
In the long term, the project anticipates supporting 200 new highly skilled design and manufacturing jobs, and a further 3800 jobs in the supply chain at a time when the aerospace sector has been hit hard. The project will also support the Government’s levelling up agenda with jobs being created across the UK.
Designed to win global market opportunities, AERALIS anticipates the project could be a big player in the global defence market, with the opportunity to promote the UK’s engineering expertise around the world.
Andrew Kinniburgh, NDI’s Director-General said: “AERALIS are a such an important business to the UK’s Defence Aerospace Sector, both domestically and for future export markets. We are very proud to have them as members and to work closely with their team”.
Tristan Crawford, AERALIS’s CEO and Founder said: “NDI membership has been enormously useful in helping us to approach and understand key stakeholders in the Ministry of Defence and Government more widely. Their honest and insightful advice and consistent support for SMEs in the industry is really important to us as a business.”
NDI is a key partner with the MoD and works across the supply chain, especially with SMEs on some of the UK’s most critical defence, security, space and aerospace projects. In particular it acts as a critical interface with the major OEMs in these sectors. It has recently become the lead Trade Association for the MOD’s new Small and Medium Sized Enterprise (SME) Working Group, which has an important role in improving engagement between the MOD, major Primes and the SME Supply Chain. MOD wants to spend around 25% of its total budget with SMEs by 2022.
NDI is a division of Make UK, The Manufacturers’ Organisation, one of the UK’s major business bodies and the representative voice of UK manufacturing, with offices in London, Brussels, every English region and Wales.
Collectively it represents 20,000 companies of all sizes, from start-ups to multinationals, across engineering, manufacturing, technology and the wider industrial sector. 8 makeuk.org
Modular aircraft maker joins NDI
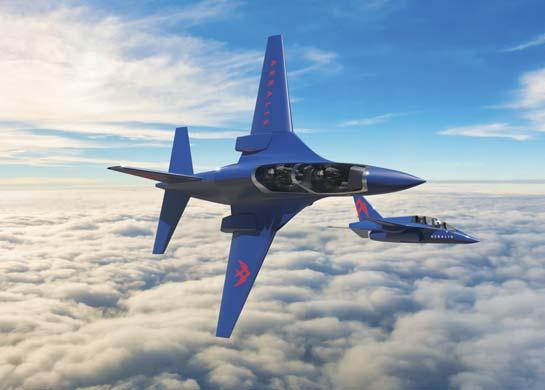
Stratasys has been awarded a contract extension for the production of 3D printed polymer Airbus cabin interior components.
While the initial contract with Stratasys was focused on production parts for the A350, this contract extension expands the range of parts printed for Airbus to include replacement and spare parts for maintenance, repair, and overhaul (MRO) as well as parts for aircraft platforms (such as A300, A330, A340 and A320) in addition to the A350.
This builds on the company’s long-term relationship with Airbus as a technology, material, and part supplier.
In the aerospace sector Stratasys produces 3D printing solutions for flight parts, tooling and prototyping. The company’s industrial FDM systems and materials provide the performance and manufacturing repeatability required by space, commercial aviation and military customers.
As it recovers from pandemic slowdowns, the aviation industry is expected to increasingly turn to
More 3D print parts for Airbus
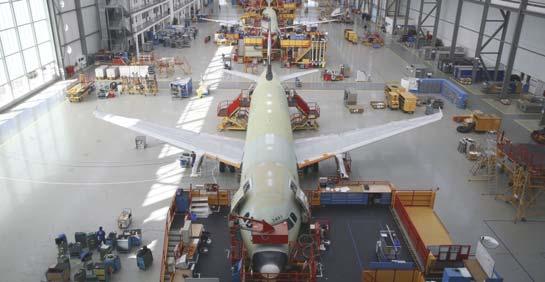
additive manufacturing for strong yet lighter weight parts and consolidated assemblies, while digital inventory of 3D-printable spare parts promises to make MRO operations more agile and cost effective. 8 stratasys.com/aerospace
METALS & PLASTICS
EXPERTISE • COLLABORATION • INTEGRITY DEMONSTRATING
WORKING IN
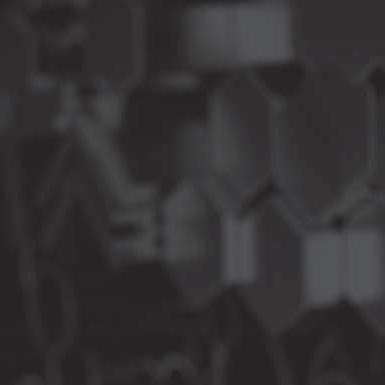
OPERATING WITH
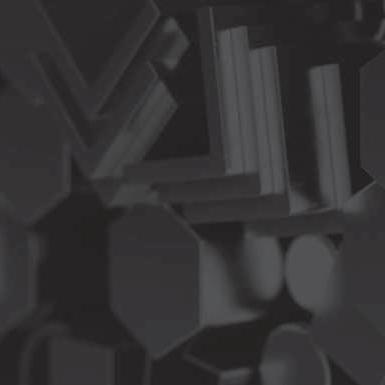
For commercial and aerospace alloy applications, Righton Blackburns has been a trusted supply partner for over a century. Our experience and expertise extends across a wide range of materials, including:
In addition, we are the exclusive supplier in the UK of Hardiall®, a high hardness and low friction copper alloy designed for use in extreme conditions.
Aluminium Stainless steel Brass Copper Nickel alloys Aluminium bronze Phosphor bronze Leaded bronze Copper nickel Bearing steels Titanium Engineering plastics
material. For a dedicated complete supply package to meet choose Righton Blackburns.
Contact your local Service Centre for further information www.rightonblackburns.co.uk
Architecture & Infrastructure Aerospace & Defence Automotive & Transport
Marine & Shipbuilding Process Plant Power Generation & Utilities

FAC prepares for sector take-off
Farnborough Aerospace Consortium (FAC) has added four new members this year as the sector prepares for a post-lockdown take-off.
FAC represents companies in aviation and aerospace and the associated supply chain –mainly centred in the south and south east but with an international membership.
Since the industry was hit hard by the reduction in passenger traffic it has been lobbying the government on behalf of the sector.
The latest companies to join FAC are Oxfordshire-based business consultancy kc4business Ltd, US-headquartered software specialists CGTECH whose UK base is in Sussex, Global Shop Solutions, the software giant headquartered in the US with a Sussex branch, and Adaptix Ltd, an Oxfordshire-based 3D imaging company.
Chief executive of FAC David Barnes said: “Never has the sector been through a more difficult time. Aerospace and aviation have been among the hardest hit of all industries.
“Many companies have suffered greatly but their resilience has been astonishing.
“We initially saw them diversify to help the battle against Covid by making ventilators and other equipment.
“Since then they have diversified to gain entry into different markets in a bid to keep trading. And we’ve seen extra focus on research and development.
“Aerospace is one of the country’s genuine world class industries and it has to be ready to spring back when allowed.
“Those within it understand that sticking together is the best way for us to maintain that worldleading position post-Covid. That is why we have seen more companies join us.
“We offer great benefits, but it is the power of one voice representing hundreds of businesses and thousands of workers that attracts new members.
“We welcome the new companies to FAC and would urge others to join us as we prepare for the sector to be opened up.
“While this could take time, there really is light at the end of the tunnel. Communication between our members is the key to success.
“The nature of the sector means any re-opening requires a global solution and we must be poised to react as soon as lockdowns are eased.”
The country’s aerospace industry pre-Covid provided more than 120,000 skilled jobs with an annual turnover of £35 billion – most of which was generated by exports. 8 fac.org.uk
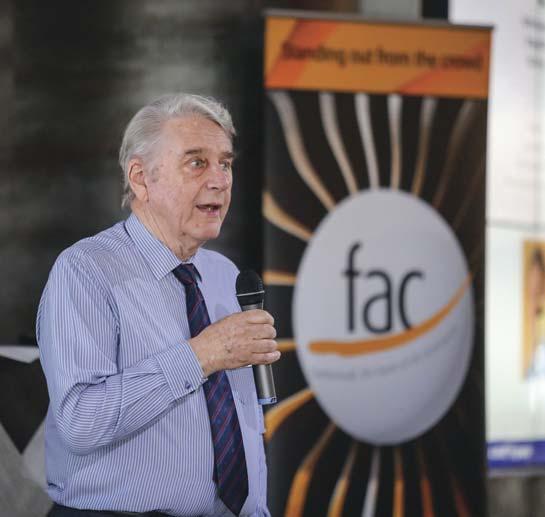
Martin-Baker Aircraft has renewed its supply agreement with composites specialist Pentaxia for the long-term supply of high-performance, lightweight components and assemblies on a multi-year basis. These parts are fitted to MartinBaker’s latest generation of ejection seats and subsequent global fighter jet programmes.
Tim Ollier, Sales Director of Pentaxia, said: “Pentaxia is delighted to renew our supply contract with the team at Martin-Baker. We share many company values and pride ourselves on producing world class components. Working collaboratively with our colleagues at Martin-Baker, our highly talented team are able to ensure quality and consistency in every component we deliver. This new agreement not only demonstrates our customer’s confidence in working with us, but provides an international platform for British engineering. It is a pleasure to continue our working relationship.”
Andy Patrick, Programmes and Commodity Supply Chain Manager at Martin-Baker added: “Martin-Baker is pleased to enhance its working relationship with Pentaxia through this agreement on a commodity that is expanding its usage in the next generation of escape systems”
Pentaxia produces all advanced composite components in-house and will supply Martin-Baker and its international aerospace partners with legacy and latest generation composite components.
Ejection seat contract renewed
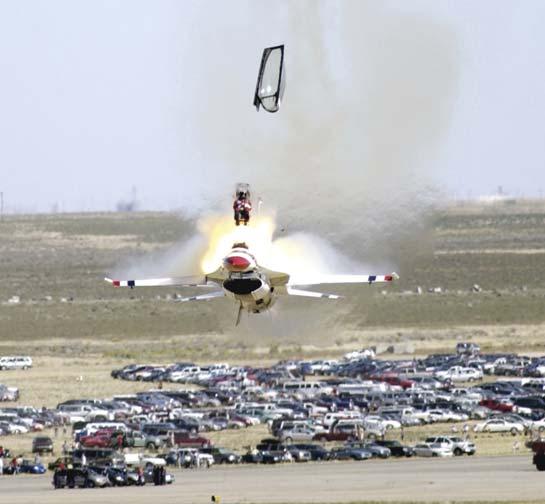
Martin-Baker has been the world leader in the design and manufacture of ejection and crashworthy seats for over 70 years. A family-run business at its core, its seats have saved over 7,638 lives since the company was founded and over 17,000 seats are currently in service. 8 pentaxia.com
DNow Accredited to
FM10101
Manufacturers of High Quality Mill-Turned Parts
Pressing ahead with reshoring
Investment in a high-speed press is helping HV Wooding deliver a significant aerospace contract that has been reshored from Spain.
The Kent-based company, which offers laser cutting, wire erosion, busbars, motor laminations and presswork to customers all over the world, has invested over £120,000 into new tooling and the installation of a Bruderer BSTA 25H to produce more than 28 million precision parts every year.
The contract will utilise the press’ repeatable bottom dead centre accuracy and 1500 strokes per minute capability.
Components will be used in a number of tamper-proof products for the airline sector and should account for 60% of the machine’s capacity, leaving the other 40% for new opportunities in electrification and green energy.
“This is the second Bruderer we’ve installed, after inheriting our first when an electrical client outsourced its press shop,” explained Paul Allen, Sales Director at HV Wooding.
“There are few machines in the world that can offer the speed and accuracy in such high volumes and this is going to make a major difference to our ability to meet the requirement of our aerospace customer.”
He continued: “The material we are using is really thin gauge and tolerances are within microns that’s why we decided on the BSTA 25H. The RAM Guidance System eliminates the possibility of movement during the stamping process, prolonging the tool life and giving us consistent repeatable quality, something the customer wasn’t getting overseas.
“It was a real partnership approach, with the Bruderer experts working with us to identify the right machine and then planning the timeline so that we could manage the install without disrupting production. This meant running the initial parts off at its Luton factory whilst we were putting the machine in place.”
Simon Stewart, Technical Manager at HV Wooding, went on to add: “We have been really impressed with the performance of the BSTA 25H and are already looking at ways where we can standardise the set-up process to move other projects on to it.
“There is also the potential to target new opportunities, with the 1500 strokes per minute speed giving us plenty of capacity to take on high volume electrical, lamination and motor orders.” 8 hvwooding.co.uk
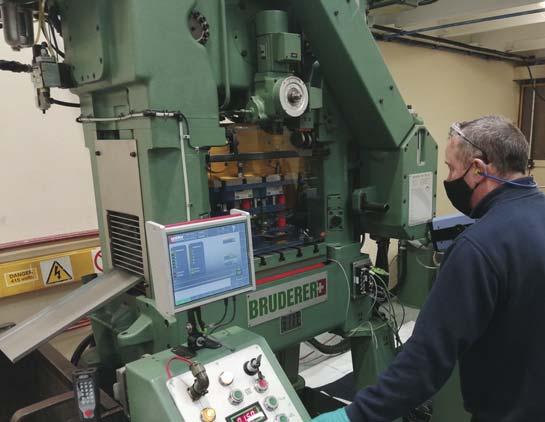
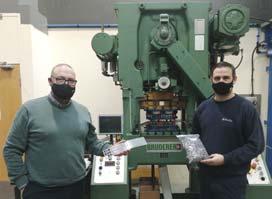
Precision engineering company RHH Franks has unveiled its newly expanded factory in Hampshire, which will increase its manufacturing capacity for the global aerospace, defence, nuclear and marine industries by over 25%.
Following a successful application to the Solent Local Enterprise Partnership (LEP), the business was awarded more than £97,000 towards its investment to acquire and equip an additional 6,600 sq ft of unit space at its premises on Gore Road Industrial Estate, New Milton. It takes the total manufacturing site up to over 30,000 sq ft.
The expansion project, which was completed in January 2021 –RHH Franks’ 60th year of trading –is part of the business’s growth strategy to substantially increase turnover in the next five years.
The extension includes a dedicated and improved Nadcapaccredited heat treatment facility, increased machining and fabrication workshops and storage provision, allowing for all other departments to expand within the existing premises.
New technology worth more than £150,000 has been purchased, including a third heat treatment oven and four-axis CNC machine which will increase manufacturing capabilities at RHH Franks from 130,000 components per year currently to more than 160,000.
Managing director Elsa Hogan said: “As part of our intense growth strategy which we have launched to mark our 60th year, we are thrilled to unveil our newly expanded premises.
“They will significantly increase our manufacturing output to meet the growing demands of our clients and their supply chains.
“Over the past 10 months our team and contractors have worked extremely hard to create a modern and fully-equipped facility, despite the operational challenges, that provides our skilled engineers with a positive and productive working environment, improving capacity and lead times.
“When circumstances allow, we are looking forward to welcoming clients to our new facility.”
Founded in 1961, RHH Franks has grown from a modest sheet metal workshop to a sizeable endto-end subcontract manufacturer providing a complete range of services from CNC milling and turning to fabrication and Nadcapaccredited welding, chemical processing, heat treatment and dip and torch brazing.
Clients include Leonardo Helicopters, Eaton Aerospace, Cobham Mission Systems, SEA Ltd and QinetiQ.
Honeywell Aerospace is one of the firm’s longest standing clients, having worked with RHH Franks since 1967.
Based in New Milton, Hampshire, RHH Franks employs over 40 skilled engineers from the Hampshire and Dorset area and is committed to inspiring the next generation of young engineers through its apprenticeship and work experience offering.
Brian Johnson, chair of the Solent LEP, said: "I am delighted to congratulate New Forest-based business RHH Franks for completing their 60th year of trading; and also to look back to see how the LEP's Local Growth Fund has been put to such good use within the manufacturing sector in the region.
“RHH Franks is one of many innovative and high performing manufacturing businesses based in the Solent who are providing much needed innovation and jobs that will support our economic renewal." 8 rhhfranks.co.uk/
Expanded capacity unveiled

8 RHH Franks managing director
Elsa Hogan
Despite the negative impacts of the pandemic including a fall in demand, the need to pause business operations for a short period and make additional investments to make workplaces Covid-secure, and prolonged supply chain disruptions, the mood remains positive amongst CMF members, with most reporting optimism for 2021.
With 2019 resulting in a significantly better year than recent years for the UK foundry sector, a decline in order books was anticipated during the early part of 2020, with concerns surrounding the outcome of ongoing Brexit trade deal negotiations. By March, the industry was also faced with responding to the global coronavirus pandemic and has subsequently responded with agility and resilience. The rapid change in volumes for the automotive and aerospace sectors saw order books plummet, specifically in the diecasting and investment casting sectors. Two lockdowns and the practicalities of operating facilities under imposed government social distance restrictions – reduced workforce, additional health & safety measures in working and common areas, supply chain disruptions etc. – have taken their toll.
The impact on business has been significant. Throughout the summer order books remained short, but by the autumn business levels were picking up, with the foundry sector well placed to respond. However, a resurgence in infection rates resulted in a
Foundries resilient and optimistic
UK foundries report that there is hope for a return to pre-Covid capacity utilisation levels, despite the impact of the 2020 lockdown measures and the resulting decline in production activity. This is the finding of the Cast Metals Federation (CMF) Business Impact Survey – 2020 Summary Report.

Courtesy Castings PLC
8 Robotic fettling
second lockdown and a slowdown in demand as the year closed.
To counter the negative effects of the pandemic, CMF members have drawn on the assistance made available by various government schemes, such as CBIL loans for additional finance, deferred VAT payments and the coronavirus job retention scheme (CJRS).
By the middle of 2020, the average percentage of employees on furlough was 30%. This lifeline enabled Members to retain staff and meet customer demand, playing to the sector’s strength in terms of skills and responsiveness.
The scheme has allowed companies to maintain production levels when required, most notably in the latter half of the year particularly quarter 4 when orders increased. There were however some redundancies, but the levels were low compared to other sectors.
As expected, business disruption has taken many forms and is not merely confined to a downturn in customer demand. At the start of the crisis, many members significantly reduced or paused production to reorganise workplaces and implement social distancing measures, to enable operations to resume in a safe and efficient manner. In addition, procedures had to be adapted to accommodate operating with a reduced workforce to meet government guidelines and to support the shielding of vulnerable employees.
By the middle of the year, the industry had adapted to the new working procedures, but supply chain disruptions continued thanks in part to the lack of production capacity throughout the supply chain and logistical challenges. This was compounded by significant increases in costs
for waste disposal, energy supplies (specifically in quarters 3 and 4) and insurance.
In some instances, customers also sought notable price reductionswith the foundry industry thus squeezed at both ends.
Despite all of this and as the economy mounted a tentative recovery during quarters 3 and 4, CMF members reported improvements in order books.
There are of course exceptions and those businesses considered to be in an ‘essential’ supply chain – 40 per cent of foundries and 15 per cent of foundry suppliers –had a busy year, often with increased demand and the specific challenges that poses.
Towards the end of the year and the end of the Brexit transition period, a large proportion (73 per cent) of members said they were prepared for a new way of working as the UK exited the European Union. There was concern over the late timing of the publishing of final detailed guidance, but there is also “hope” that there would be increased opportunities for local content in supply chains.
Notably, despite a very testing year, no member has reported the need to close or scale-down operations in the longer term. Members also reported that on average they would return to 2019 capacity levels within ten to twelve months.
Speaking about the results of the Survey, CMF CEO Dr Pam Murrell FICME said: “Our sector has faced an enormous challenge during the past year and CMF members have responded as they always do, with remarkable resilience. Their optimism and robust handling of what has been a challenging year for all industries and society is a reflection of their competence and abilities. With industry gearing up throughout the Brexit transition period and awaiting trade deal news, 2020 was set to provide certain complexities, but nobody could have predicted a global pandemic and what that would throw into the mix. However, the wheels of industry continue to turn and CMF members have an important role to play in contributing to the UK’s GDP and they haven’t disappointed. Our sector has ‘dug deep’ and found solutions during the harshest of conditions and we can be particularly proud of that.”
Contact: Dr Pam Murrell FICME, Tel: +44 (0) 121 809 3500, email: pammurrell@cmfed.co.uk
8 www.cmfed.co.uk
The Cast Metals Federation
is the single voice for the UK castings industry, the Trade Association that represents the interests of foundries and foundry suppliers.
CMF members come from every part of the industry and produce around 85% of all castings output in the UK. With over 120 foundries, ranging from global foundry groups to small jobbing foundries, our members supply precision finished parts and assemblies in a range of sizes, metals and processes to the UK and global markets. A strong casting sector requires and supports a successful chain of equipment and consumables suppliers, over 40 of whom are important part of CMF’s membership. As a proactive trade association, the CMF undertakes activities beyond the resources of individual members that drives the whole industry forward competitively, technically, environmentally and legally. When it comes to dealing with national or European governments, legislation, health and safety and a wide range of other topics, we can represent members’ best interests.
For manufacturers across the world seeking the
the CMF provides a single point of contact, whether for sourcing castings for every application and market sector or general information on the activities of the UK foundry industry.
www.castmetalsfederation.com
To find out more or apply for membership please contact: National Foundry Training Centre, ECMS, Tipton Road, Tipton, West Midlands, DY4 7UW Tel: +44 (0) 121 809 3500 Email: admin@cmfed.co.uk