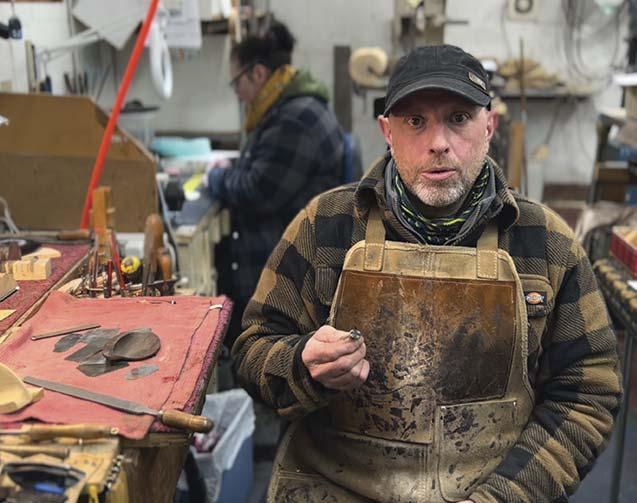
20 minute read
TURNED PARTS
APT Leicester has been supporting Alexander Accessories in the manufacture of intricate chinrests and tailpieces for violins and violas.
APT has worked with the highly skilled luthiers since 2016, playing a key role in the supply of musical accessories to some of the world’s most famous players.
Having specialised in the handcrafting of musical accessories for more than 40 years, Alexander Accessories fully appreciates the need for exceptional turned parts. However, it had been disappointed with the supply of oily and poorly finished parts prior to working with APT.
Positive feedback has subsequently focused on the efficiency of the APT manufacturing process and the exceptional levels of customer service. This has been essential to the continued fulfilment of demand for the most comfortable and luxurious accessories.
Luke Sibley, owner of Alexander Accessories, said: “We’re delighted with the working relationship we have with APT. Their knowledge and engineering capabilities are impeccable, also their advice about materials and what can be accomplished.”
“We are able to use their blanket order system to order large amounts of fittings, which has proven to be very costeffective for us. The parts are always clean, well-labelled, and delivered on time. APT’s attention to detail is exemplary.”
He continued: “As our customers have spent many hours perfecting their violin and viola playing, it’s important that our chinrests are handcrafted and APT’s parts are of the highest standard. We look forward to many more years of working in partnership with them.”
Drawing on their extensive engineering experience, APT Leicester has supported Alexander Accessories in the production of 25 turned parts of different lengths and sizes. Special tooling, milling, and countersinking methods have been used in the manufacture of threaded studs, barrels, and clamps.
Between 2,000 and 3,000 mill-turned parts are produced each year, with all brass, titanium, and nickel silver components delivered directly to the Alexander Accessories workshop. Such projects have provided the APT team with the opportunity to work with an interesting local business, maintaining the same high standards that other customers have come to expect.
And the partnership with Alexander Accessories looks set to continue, with APT Leicester having helped in the design and engineering of a new upper clamp in recent months. 8 aptleicester.co.uk
Making music together
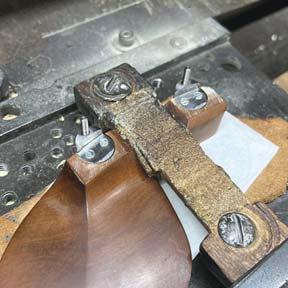
Investing in the future at 165
Family-owned manufacturer JJ Hardy & Sons is celebrating 165 years in business by investing in new CNC turning and additive manufacturing technology.
Hartlepool-based JJ Hardy & Sons was founded in 1856 by John James Hardy before being bought out by Ald. T.H. Pailor, the grandfather of the company’s current owner and managing director, Andrew Pailor.
Originally set up to support local traders and seafarers, the company has since transitioned from local brass founders and finishers to supplying precision machined components to customers across the UK.
“My family have been involved in this business for three generations and have guided it through incredibly dark times,” says Andrew Pailor. “However, even when our backs have been against the wall the most, our determination and grit has helped pull us through and bounce back from every single setback we’ve faced.
“From raising money during the first and second world wars to fund the war efforts, to producing parts for ships and arms, we’ve risen to every challenge thrown at us and as a true UK manufacturer, we’re proud of our heritage and to be still here today, investing in the North East and continuing to grow.”
Following a visit to Japan in the mid-1970s, Andrew’s father, Tom, became one of the first people in the UK to invest in a CNC turning machine.
While orders slowed slightly during the pandemic, Andrew –like his father before him - took the opportunity to plan for the future and begin writing the next chapter in the company’s history.
After tapping into support from the Sustainable Advanced Manufacturing (SAM) Project at the University of Sunderland, the company invested in a Mazak QTE-200 SG CNC turning machine and a Ultimaker S5 3D printer, allowing it to ramp up productivity, slash production costs and diversify its product offering.
Andrew added: “The new machinery we’ve purchased represents a significant investment for the company and will be key to not only sustaining our future for another generation, but for nurturing the next generation of talent that comes through the business as we continue to invest in the region.
“Both the new CNC machine from Mazak and the Ultimaker 3D printer will help us provide an even better service to our clients, running low-cost machines on lights out production and expanding the services we offer. For example, in the few months since we purchased the 3D printer, we have produced pattern making equipment for the casting industry and reverse engineered plastic components for the rail industry, it’s really opened doors for us.”
Surviving the pandemic proved not only a key milestone for the business, but also for the Pailor family. As the company celebrates its 165th anniversary last year, it will also mark 83 years since Andrew’s grandfather led a buy-out of the company and will mean the Pailor family have now owned the company longer than its founding Hardy family. 8 jjhardy.co.uk
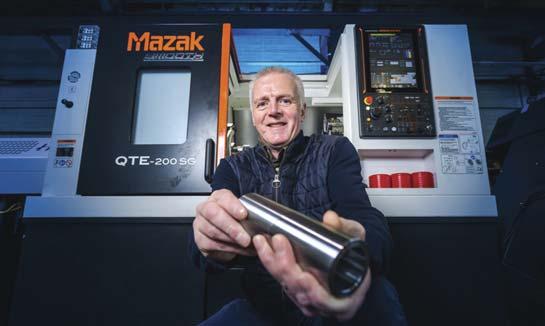
Two new Nakamura turning centres – an AS200L and an AS200 – at Riverside Precision Engineering have halved lead times on some parts.
With a range of sliding head turning centres machining components for the hydraulic, medical, brewing, valve, marine, rail and oil and gas industries, the Blackburn company was utilising an ageing Nakamura WT250 turning centre for components beyond the diameter capacity limits of its sliding head machines.
Riverside Director, Mr Scott Whalley said: “Components in the
Lead times halved
50 to 65mm diameter range that are beyond our sliding head machines have been an issue. We have a lot of small-batch work typically from 50 to 500-off that is relatively simple to produce – for this we bought the Nakamura AS200 single-spindle chucking machine. For the more complex work in the 300 to 2,000+ batch range, we bought the bar-fed twinspindle Nakamura AS200L. We have the AS200 chucker machine manually loaded with billets and the AS200L runs unmanned with a barfeed for longer batches.”
He added: “The cycle times on both Nakamura machines are much faster, there is less idle time and the kinematics ensure less ‘air cutting’. We are extremely busy at present and our larger components up to 65mm diameter was a bottleneck. The new Nakamura machines have cut lead times from 6 weeks to just 3 weeks on these larger parts.” 8 riverside-engineering.org.uk
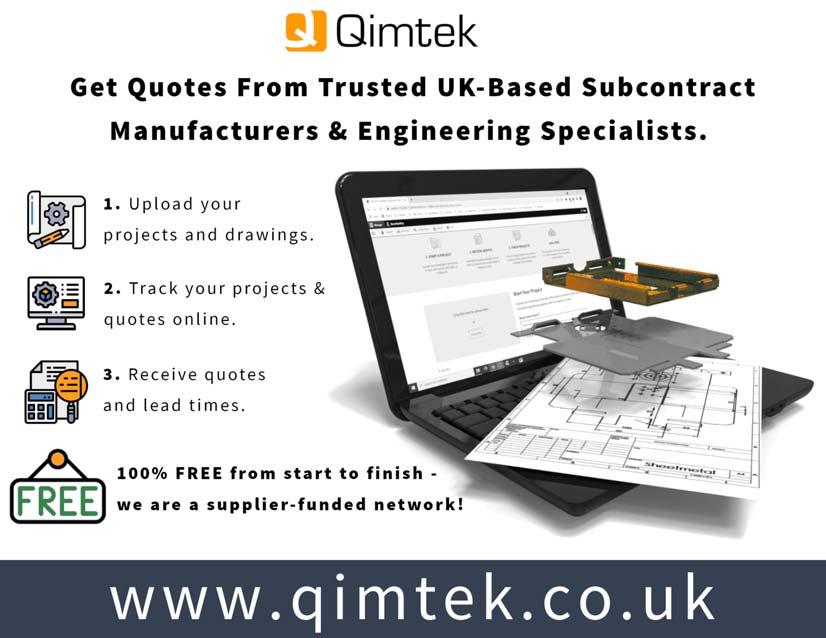
Turned parts contract machining specialist Precision Products has weathered the recent turbulent times well and says it is now more competitive than ever.
Established 48 years ago, and based in Rustington, West Sussex, the company had to downgrade its turnover target in April 2020 at the start of the last financial year due to a collapse in aerospace contracts, which normally accounted for 10% of turnover. This loss was largely offset by winning Covid-related medical contracts for the production of components for ventilators, hospital beds and testing kits. Some new medical work is ongoing, such as the manufacture of parts for micropumps used in disinfectant spraying equipment.
Consequently the firm met its planned turnover for the period to April 2021 and is ahead of target or the year to April 2022. Profitability has increased following a detailed analysis of cost structure and working practices by managing director Sally Thorley, enabling the company to quote more competitive prices. Around-theclock running five days a week has continued and there have been few staff changes, except for a couple of retirements and the appointment of two additional personnel.
One is finance manager Charlotte Turner and the other is Sales and Estimating Engineer Sean Keet, who has a wealth of experience in a similar role. They bring the total number of staff to 32. Following on from all personnel having been trained to Level 2 in NVQ Business Improvement Techniques, four managers are currently undergoing training with the Institute of Leadership & Management, two at level 5 and the others at level 3.
Extra business received from UK sources that have helped the company to achieve a positive result during such a difficult period includes machining families of stainless steel spindles, studs and end caps to tight tolerances for top-end mountain bike pedals manufactured by Pembree in Heathfield, East Sussex.
Helping to boost turnover further has been an increase in direct exports. It now accounts for 12% of turnover, due in part to a major new contract for the supply of brass air caps to the Chinese factory of a multinational air humidifier manufacturer. Other overseas markets that are regular recipients of the subcontractor's components are Hungary, Mexico and the USA.
Mrs Thorley commented, "Brexit has had very little impact on our business practices, except for a few delays in some tooling deliveries. On the contrary, it has
Powering through the pandemic
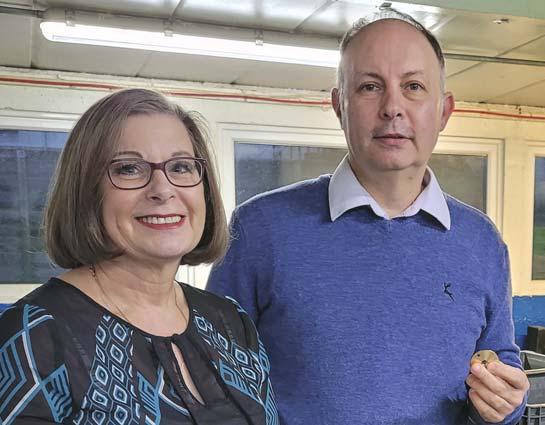
8 Sean Keet, newly appointed
Sales and Estimating Engineer at Precision Products, with Sally Thorley, Managing Director
helped UK manufacturing by making domestic OEMs less likely to source components from abroad. "We are already seeing the beneficial effect, with an increase in orders from companies that traditionally use continental European subcontractors. "Moreover the problems that Asian suppliers are currently experiencing due to the pandemic are also resulting in more work for UK subcontractors, including us."
Things have not been standing still on the shop floor either. The subcontractor's first Citizen Cincom slider with LFV (low frequency vibration) software for automatically chipbreaking difficult materials arrived in early 2020. The 20 mm bar capacity L20-VIIILFV with B- and Y-axes, which can be operated with or without a guide bush, allows technically challenging components to be produced more efficiently from normally long-chipping plastics and stainless steels.
Mrs Thorley advised that customers are increasingly asking for components produced from both materials, with plastics being used more and more for medical work, while stainless steel accounts for as much as 40% of throughput.
Citizen trained five of Precision Products' operators in the use of LFV and feedback from the shop floor on the software's effectiveness has been positive. It is proving particularly useful in view of the current trend towards industry increasingly asking for miniature parts machined from these and other problematic materials to tolerances measured in microns.
This was the first sliding-head lathe in Rustington to be fitted with a Wogaard Oil Saver system for recycling the neat oil used, although four of the Miyanos onsite are already equipped with a similar Coolant Saver unit. The maintenance-free device sits at the bottom of the swarf bin, continuously sucking up cutting fluid that has been transported there on the swarf and automatically returning it to the machine's coolant tank for reuse. It not only saves oil or coolant but also reduces subsequent energy expenditure required for spinning the swarf prior to recycling it.
Again with the environment in mind, the subcontractor's MecWash aqueous cleaning machine has been replaced by a more efficient, environmentally friendly Duo 400 model that combines flood and spray washing, followed by heated spray rinsing and hot air drying. The rinse stage can be used to apply a corrosion inhibitor to ferrous components. The machine incorporates the Aqua-Save system for treating and recycling up to 90% of the waste water, minimising expensive off-site treatment and disposal.
Other energy-intensive areas addressed by Precision Products include the replacement of an old air compressor with a new model that consumes considerably less power, resulting in a saving in carbon dioxide emissions of more than 12 tonnes; and replacement of the tungsten and fluorescent lighting throughout the factory with LEDs, saving the release of a further 4.8 tonnes of carbon dioxide annually.
On a final note, Mrs Thorley said that Precision Products is proud to have been able to keep going virtually unaffected during the difficult trading conditions created by the pandemic. She added that the company manufactures high quality CNC turned parts backed by CBS EN ISO 9001:2015 approval and AS 9100 Rev D accreditation in the case of aerospace components.
Shortly before the end of last year, the subcontractor had its former approval recertified. The company that carried out the online reassessment is on record as saying that it was one of the best audits it has ever completed and that Precision Products was the only company it dealt with during the pandemic that achieved or exceeded all of its key performance indicators. 8 precisionproducts.co.uk
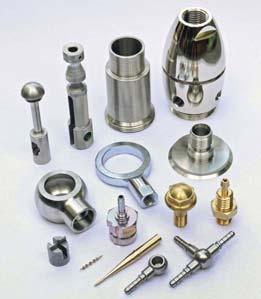
Nottinghamshire based Boneham & Turner has increased its ability to offer more complex parts within its tooling and precisionengineered component operations with the help of a Sylvac Scan F60L optical measurement machine, supplied by Bowers Group.
A fourth-generation, family-owned precision engineering solutions provider established in 1918, Boneham & Turner serves the aerospace, defence, motorsport, composite and yellow goods industries by manufacturing and supplying drill bushes, dowel pins, both simple and complex shims for the manufacture and assembly of jigs and fixtures, work holding, hydraulic systems and machine-building.
With previous processes in place, the company needed to decline work. This was not due to the complexity of manufacturing the parts, but to the limitations on inspection. The inspection of micro-pins had always proven to be a time-consuming challenge for the production and quality teams.
To improve its inspection capabilities, Boneham & Turner applied for funding through the Aerospace Unlocking Potential project, provided through the European Regional Development Fund Revenue Agreement, to help fund the purchase of the Sylvac Scan equipment.
Used by quality personnel, machine operatives completing first-off checks, as well as the engineering team for samples and R&D, the Sylvac Scan F60L is designed to measure even the most demanding of cylindrical parts.
With a brand-new camera and optics offering superior image processing and fast inspection times, the optical measurement machine uses Reflex One-Click technology with part recognition and auto measure, allowing measurement with one click of a button. Quick-release tooling for making rapid part changeovers, combined with sophisticated software delivers immediate visual results, assisting in providing essential efficiencies in a busy working environment.
The Sylvac scanner is used daily as part of the standard inspection procedure at Boneham & Turner. Primarily measuring a range of micro-pins that start at approximately 1mm diameter and 3mm long, the unit has proved to be easy to use and extremely precise.
Stacy Denton-Beaumont, Operations Manager at Boneham & Turner said: “Quality is absolutely paramount to our customers – supporting industries such as aerospace, defence, military and F1, there is zero room for defects, in both time and cost. We have an outstanding record for perfect quality and investing in equipment such as the Sylvac demonstrates our commitment to continuous improvement in our metrology capabilities.”
“The Sylvac-SCAN F60L has vastly improved our scope of metrology. As an AS9100 Rev D certified manufacturer, we pride ourselves on offering outstanding quality to our valued customers and core markets. With its Swiss precision engineering, the Sylvac
Improved inspection adds capabilities
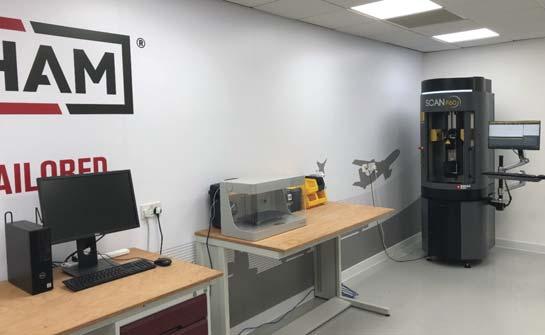
SCAN F60L offers an efficient, exact and effective inspection method, complimenting the current catalogue of equipment here at Boneham & Turner Ltd.”
Having worked with the University of Nottingham for many years in research and design, as well as Graduate Placements, whilst also, as a member of Midlands Aerospace Alliance, Boneham & Turner have attended various courses and networking events which have proved highly beneficial in terms of new business but also improved knowledge.
Stacy explained: “Having a Technology Manager designated to us from MAA, made the project run a great deal smoother and it was on their recommendation that we began looking at a Mark Forged Mark II 3D Printer. This was supplied by Additive X, who also did the training and over the past 6 months have been incredibly supportive with many of our projects.”
The project has enabled Boneham & Turner to innovate in both metrology and new products and services. It has established a new measurement process and has enabled new products to be made and inspected.
The team are currently looking to re-shore some parts, as they are now able to offer the full level of inspection required for mission-critical parts. 8 boneham.co.uk
Wealdpark Limited
Stand number 5126
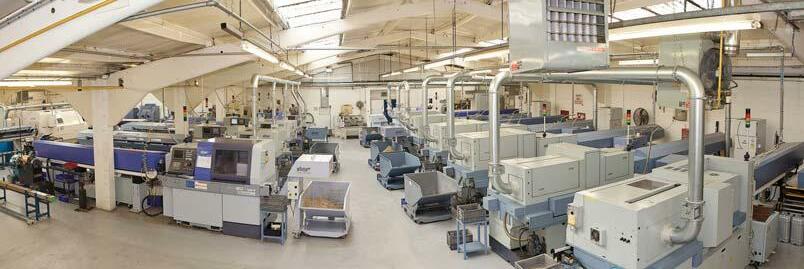
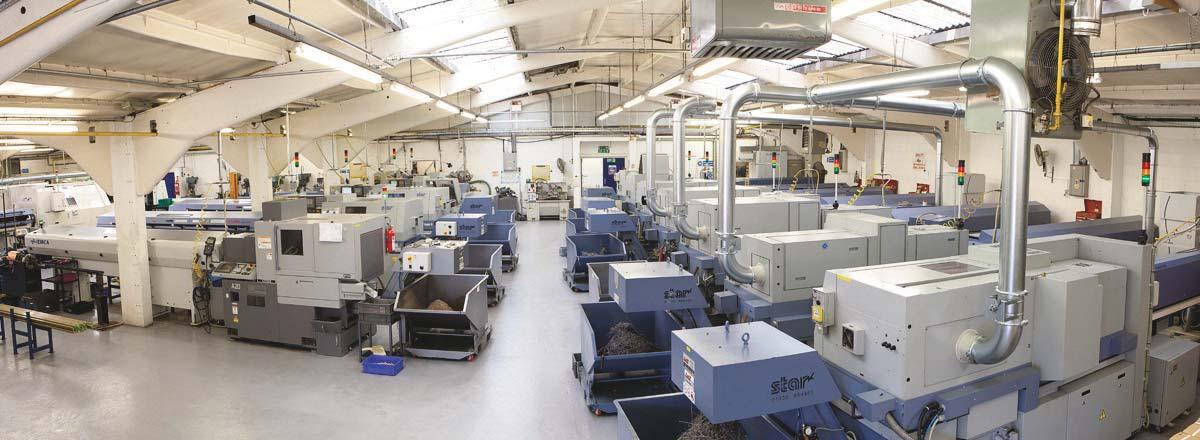
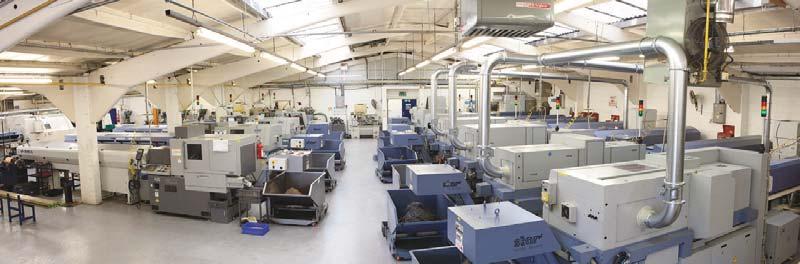
Subcontract Capacity
BS EN ISO 9001:2008. Approved by BSI since 1991.
Company Contact Details
Phil Smith, Director, Wealdpark Limited Sutton Road, St. Helens, Merseyside, WA9 3DJ Tel. 01744 22567 / 732083 Fax. 01744 451339 E: sales@wealdpark.co.uk www.wealdpark.co.uk
Complex machined parts supplier RE Thompson has recently invested £1m to extend its automated 24/7 lights-out production facilities with advanced CNC gear manufacturing and metrology inspection capabilities.
The company is now able to offer aerospace, defence, automotive and other industrial customers a complete gear design and manufacturing service to exact custom specifications.
Gear manufacturing capabilities now offered by RE Thompson include power gear skiving, straight and helical teeth hobbing, internal and external spur gears, straight and spiral bevel gears, hypoid and flat gears.
RE Thompson has a long established reputation as an innovation-led business which continuously invests in new production technologies, realtime digital infrastructure and software. End-to-end capabilities and services provided range from design, prototyping and rapid turnaround supply of one off components, to low, mid and high volume batch order fulfilment.
This major capital investment originated from a long standing UK based aerospace defence customer which had a problem that was solved by an RE Thompson engineer. However, the solution required internal spur gear production capabilities. In order to continue providing a complete supply package to this important customer, as well as opening up new sales opportunities for continued growth, the strategic business decision was taken to install small to mid-sized gear manufacturing capabilities in-house.
Power skiving machine benefits At the heart of this gear manufacturing capital investment is the now fully operational Okuma Multus U4000 5-axis high speed multitask CNC machine, which combines turning and milling functionality with power skiving. The power skiving method, suitable for both straight and helical gear production, uses a combination of gear hobbing and shaping by continuous hobbing with axial feed. Power skiving has been proven to be a significantly faster, highly efficient alternative to conventional broaching or gear shaping, with added quality, productivity and cost saving benefits.
A major accuracy and part consistency quality advantage of power skiving is that it avoids reclamping errors and so eliminates subsequent radial deviations. This is due to turned datum surfaces and teeth finish-machining being done in a single clamping operation. The process is also more flexible than traditional gear shaping, enabling high speed continuous machining of internal and external teeth, either against a flat collar or with an undercut.
Managing Director Michael Thompson commented: “We extensively researched and evaluated various methods to produce a close tolerance, precision machined gear inside a component to enable us to make the internal spur gear part for our defence customer. Power skiving came out as the best overall solution. The versatile Okuma Multus U4000 5-axis multitasking CNC machine was chosen as it combines very high
Advanced gear making capabilities
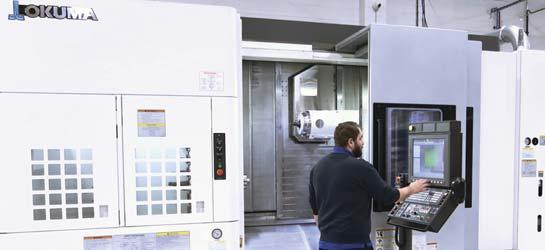
8 The Okuma Multus U4000 5-axis
multitask CNC machine combines turning with power skiving
quality precision machining of the established gear designs and configurations we anticipate customers will need with high productivity. It provides us with the process flexibility to manufacture everything from one-off parts to medium volume batch orders, and enables us to be both lead time responsive and price competitive.”
Additional options specified An extensive list of additional options offered by Okuma was specified by RE Thompson to enable all types of gears from Ø20mm up to Ø350mm (dependent upon gear type), machined from metal or engineering plastic materials, to be accurately produced cost effectively. Key machine options specified include enhanced helical gear production with slope cutting functionality, plus an additional gear machining package with programming for internal teeth hobbing and gear cutting.
Two software upgrade options were also included in the Okuma Multus U4000 specification to provide the highest level of fast machining speed accuracy and finish quality: tool centre point control software with posture compensation, which provides enhanced control of tooling geometry length, offset and tool centre movement; Super NURBS (Non-Uniform Rational Base Spline) 5 axis software which enables curved surfaces with a smooth surface finish to be cut at high productivity processing speeds with very high accuracy, which further benefits complex bevel gear geometries.
Quality inspection upgrade In-house quality control metrology facilities have also been upgraded for gear part inspection. An essential part of the £1m capital investment included purchasing a new Hexagon Leitz Reference HP 5.4.3 CMM (coordinate measuring machine) with Hexagon Quindos metrology software; both the hardware and software are specifically designed for submicron tolerance gear inspection and form testing. The new CMM system, fitted with a fixed head Leitz single point probe technology, has a volumetric length measuring error (MPE) of 0.7 + L/400μm. The system can accurately measure spur gears up to Ø350mm and bevel gears up to Ø200mm.
RE Thompson’s quality and inspection department follows APQP, PPAP and PFMEA procedures. Quality accreditations include being ARB certified with multiple aerospace customer approvals, alongside AS9100, UKAS ISO9001, ISO14001, and ISO45001 certifications.
The attention to detail by the RE Thompson team to ensure the highest quality precision gear manufacturing possible included the surveying and construction of purpose built reinforced foundations for the Okuma Multus U4000; being more than 1 metre deep the new foundations isolate it from external vibrations or from other machines in the factory. Key production and quality control inspection personnel have undergone an extensive training programme and learnt how to get the very best from the new investments.
Additionally, in response to feedback from key stakeholders, including design engineers and quality controllers, who flagged customer issues that can occur due to burrs, RE Thompson has developed a new proprietary process which achieves a 100% burr free machined gear part, eliminating the need for any additional manual deburring. 8 rethompson.co.uk
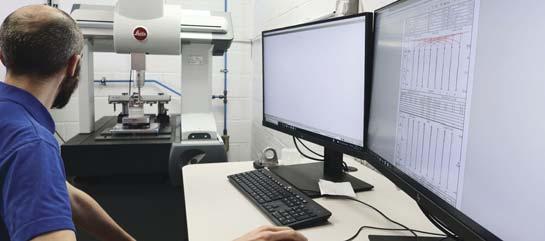
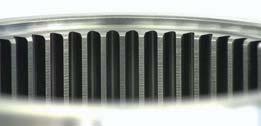
8 100% burr free machined gear parts eliminate manual deburring
The new Hexagon Leitz Reference HP 5.4.3 CMM system
Jaltek joins Sharing in Growth
Luton based electronics manufacturing company Jaltek has been accepted on to the UK's leading aerospace transformation programme, Sharing in Growth (SiG).
SiG was established in 2013, as a non-profit organisation to work with UK aerospace supply chain companies so that they can be better placed to win a share of the global aerospace market. Today their clients include all the key manufacturing growth sectors, including Aerospace, Off-Shore renewables, Defence and Off-site Construction.
Jaltek participated in a holistic business diagnostic process and will now work alongside Sharing in Growth’s team as they share their industry expertise in areas including Leadership & Culture, Business Strategy, Business Development, Operational Excellence and Productivity improvement.
Darren Cheetham SiG Business Transformation Manager said "We are delighted to welcome Jaltek on the programme and are looking forward to working together on a multi- year basis. The scheme will provide Jaltek with a comprehensive programme of training, coaching and development, tailored to their specific needs. With over 2,000 years of cross sector industry expertise, our team applies global best practice intervention, enabling UK companies to create sustainable growth. We are motivated by the transfer of knowledge and capability to teams and individuals to enable ambitious supply chain companies to grow and compete globally. Our aim is to support the Jaltek vision towards world class competitiveness and productivity."
Jaltek’s Managing Director, Steve Pittom, said, “We are truly honoured to have been selected by Sharing in Growth and to have their support and guidance. The scheme is the epitome of government and industry working together to drive improvements in operational competitiveness, leadership behaviours, and business strategy for UK companies such as ours."
Jaltek’s Steve Blythe added, “Sharing in Growth has already started to change how we do things. Jaltek has grown in recent years, but SIG will enable us to develop even further, along with the confidence and ambition of our people, this will continue to improve how we support our customers and in turn create more jobs in the future.” 8 jaltek.com
PRECISION ENGINEERING
www.thomas-brown-engineering.co.uk
Tel: 01484 548903
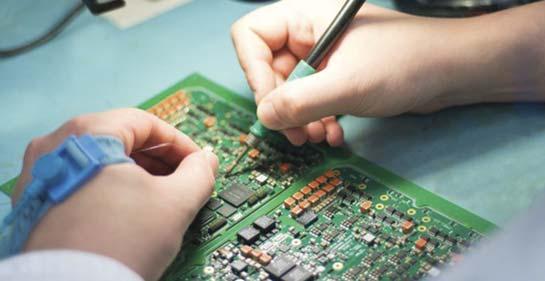
Aerospace Oil & Gas Nuclear Defence Automotive Electronics Hi Fi Industrial & High Volume Machining