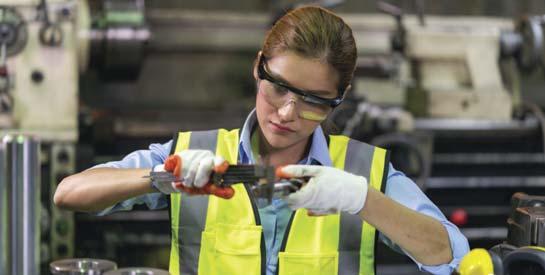
8 minute read
AEROSPACE
As the aerospace sector plans for the post-pandemic future, Stephen Molloy, discusses how quality cannot be compromised.
While some predict that there will be a rapid recovery for the aerospace sector when Covid-rates are under control internationally, aerospace companies must strive to be as efficient as possible while delivering on time to be competitive during this regrowth phase and beyond.
Core to this is protecting buildlines from disruption and inferior quality, while maximising their production effectiveness. This is achieved by defining the problem through measurement, analysis, audit and data, and then working to develop a permanent fix, to improve quality levels and drive problems back to root cause to ultimately eradicate them.
G&P itself has prepared for this upturn by maintaining employment levels as high as possible throughout the pandemic so that it can offer the flexibility and strength in depth that aerospace customers require. To support this, the company has also provided employees with opportunities to work in new sectors, so enhancing their skills in the interim.
As in most manufacturing industries there is also a growing focus on sustainability in aerospace, which in itself creates fresh challenges and new opportunities - an increased number of electric aircraft, hybrid power plants and sustainable aviation fuels as examples. These environmental changes are already at the centre of the automotive sector, primarily through the rapid development and adoption of battery and electric vehicles, and are growing considerations within the aerospace industry.
G&P’s established presence in the automotive sector means the company has already developed relevant services and employee training programmes that are contributing to sustainability results while maintaining quality standards throughout the production process. The result is that the company is in a strong position to serve the equivalent emerging environmental focuses of the aerospace industry which will become more widespread in the coming years.
Commitment to a long-term diversification strategy is also key to G&P and is possible because many of the services – including inspection/containment and rework, supplier management and quality audits, finished product acceptance, and scanning services – are transferable to multiple industries beyond aerospace and automotive such as off-highway, household goods, marine and rail.
Therefore, in an ever-changing world where disruption reigns, quality in production, whether it’s in aerospace or another manufacturing sector, must be maintained and should be given even greater priority than before as the world adjusts to a ‘new normal’. 8 gpqm.com
Don’t compromise quality
8 G&P’s Stephen Molloy
Stephen is Aerospace, Defence and Industrials Director at G&P Group Holdings Ltd, and an IMechE Chartered Engineer whose previous roles include senior positions in aerospace OEMs and aircraft systems providers.
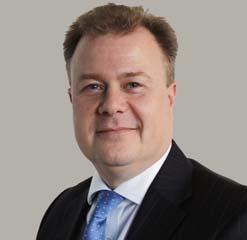
HV Wooding has invested in a new punching machine that gives an immediate 40% increase in capacity along with greater flexibility and shorter lead times.
The £400,000 EHRT FlexPunch machine completes a £1.5m investment drive at the Hythe-based company.
The machine has three CNC axes that virtually guarantee perfect accuracy on production parts destined for electrical switchgear, data centres, electric vehicles, and energy markets.
It follows investments in a high-speed Bruderer BSTA 25H press, Xpert 80 Bystronic and a Trumpf TruLaser 3030 that can produce thin gauge laminations and busbars for use in electric cars, lorries, buses and commercial vehicles.
Matt Lacey, Sales & Marketing Manager at HV Wooding, commented: “Since the pandemic has eased and we’ve got back to a more normal trading environment, we have seen monthly sales increases of between 15% - 25%.
“This is being driven by our ability to take on complex projects from prototyping through to volume production, taking in multiple manufacturing methods, including wire erosion, laser cutting, presswork and tooling, assembly and electroplating.”
He went on to add: “These capabilities make us a very attractive proposition for companies involved in developing new components for electrification and we wanted to cement this position with the £1.5m investment in four different, but complementary technologies.
“Our quality team has been really pleased with the parts produced on the new FlexPunch and we’re looking forward to taking on more projects that utilise its accuracy, repeatable quality and speed.”
HV Wooding, which has enjoyed strong export growth over recent years, is also investing in the skills of its workforce to help it meet the surge in demand from within the UK and overseas.
A new Buyer and a Systems Development Engineer are the latest recruits, and they will soon be followed by six more staff spanning a range of positions from Production Manager, Production Supervisor and Technical Team Planner to Process and Project Engineer and two Quality Inspectors.
This will give the company the strength in depth it needs to push the boundaries of its manufacturing activities, including its involvement in a Faraday Battery Challenge project to develop a new powder coating process for the insulation of Busbars destined for electric vehicles, energy storage and battery applications.
“We will also optimise the spraying facility for manufacturing high quality insulated busbars with complex geometries required by various battery OEMs. By semiautomating the process we can also reduce operator risk and further minimise the product failure rate, which can be as high as 25%.”
He concluded: “The project will produce best practice testing methods for manufacturing quality assurance. These new standard testing specifications and methods will benefit customers, manufacturers and trade associations by improving the efficiency of design, manufacturing and procurement in the battery manufacturing supply chain.” 8 hvwooding.co.uk
Investment adds punch
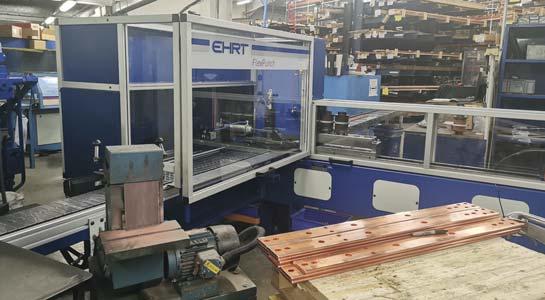
Advanced assembly, forming and fabrication assets from Sertec’s recently closed springs and wire forms division have been given a new lease of life at Dorset-based William Hughes Ltd.
When the assets became available, Engineering Director at William Hughes Ltd., Emma Burgon, spotted an opportunity to not only bolster her company’s existing capabilities, but also introduce new ones.
“We’ve been able to increase our welding capacity,” she explains, “growing from eight weld cells to 12, and we will be adding a further four bending machines, taking us up to 10 in total. We’re also planning to move some plant to our facility in Bulgaria.”
Some of the machines are upgrades too. “We already have Itaya machines, but they are 10 years older than the Sertec machines, which also have some added functionality, so we are just going to swap them out and put the older machines into storage. We picked up some extra coiling machines too, so five new coiling machines will be coming through the door.”
William Hughes has also gained some new capabilities thanks to an EDM wire eroder. “We’ve never had EDM capabilities before. It will allow us to pre-cut blocks prior to CNC milling, meaning a lot less work will need to be done. Our customers don’t normally give us very much time to make weld jigs, but if we can get off tools quicker than anybody else, we will win the project.”
The new assets have almost immediately resulted in new business too, with the company recently winning significant business for welded-assembly work and contracts for six new wire frames for two of the world’s leading tier one automotive suppliers.
“It’s all looking very positive,” Burgon concludes. “Our additional capacity and capabilities, not just here in the UK, but also in our Bulgarian and Polish plants, will put us in an amazing position to go into 2022 with some real optimism.” 8 wmhughes.co.uk
New tech, capacity and capabilities
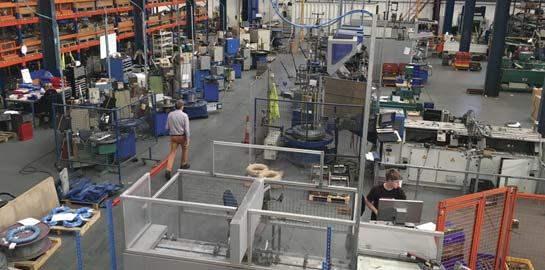

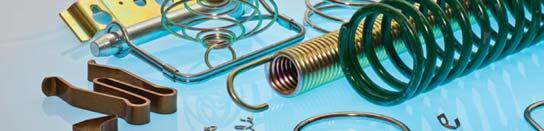
From design, sampling and technical support to manufacture, Simpson Springs & Pressings Ltd provide the complete service.
Tel: 0118 978 6573 Email: sales@simpsonsprings.co.uk
More laser speed and capacity
Thatcham-based Taylor Made Fabrication (TMF) has invested in new laser capacity and moved to a new facility.
The new Mazak Optiplex Nexus Fiber 3015 III laser will improve processing speeds and increase production capacity in order to meet demand.
Ray Baker, Director at TMF, says strong demand led the company to approve the investment. “We’re always busy and given our levels of demand we felt that it was important to upgrade our laser cutting technology.”
He continued: “Our previous unit was becoming slower and needed more maintenance to keep operational. We can’t afford any downtime or let customers down, so the new investment, which has coincided with our move to a new facility, is very important for the future of the company. Mazak’s Optiplex Nexus ticks all the boxes for us in terms of price, performance and capacity.”
The Optiplex Nexus is equipped with a powerful 3.0kW laser has dramatically improved production throughput. “We’ve been able to make significant improvements in processing speed and also begin processing thicker aluminium and stainless and mild steel which has opened doors for us with new customers.”
“One of the main things that stood out about the Optiplex Nexus was the flexibility offered by its twin pallet design, as opposed to our previous machine, which was only equipped with a single pallet,” say Ray. “Because we work in general subcontracting, we’re always busy. Being able to save time on loading in new sheet metal while we take out the completed workpieces has made a significant improvement to our productivity.” 8 taylormadefabrication.co.uk
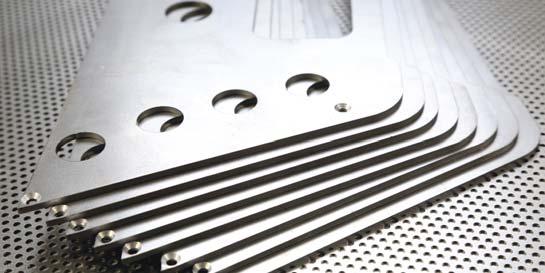
Subcontract specialist and sheet metal fabricator, KMF, has seen substantial growth of over £1.5m following its backing of the nationwide move towards increased availability of electric vehicle (EV) charge points.
KMF is utilising its 24/7 highvolume capacity to support blue chip electric vehicle charge point manufacturers in response to the Government’s drive towards zero emissions vehicles.
As the UK continues to adopt
Charging ahead with EVs
the use of reduced emissions vehicles, EV charge point manufacturers are looking for partners who have the breadth and depth of experience to meet their long-term needs.
Keith Nicholl, Commercial Director at KMF Group said: “In 2021, demand for electric vehicles soared by 78%. KMF welcomes this increased demand for its metal fabrication services and is well equipped to support the nine-year target towards a full roll out of zero emissions vehicles.
“The group’s 255,000 sq. ft. of sheet metal and precision engineered component manufacturing facilities is ideal for the fabrication of weatherproof and vandal resistant EV charging stations.” 8 kmf.co.uk