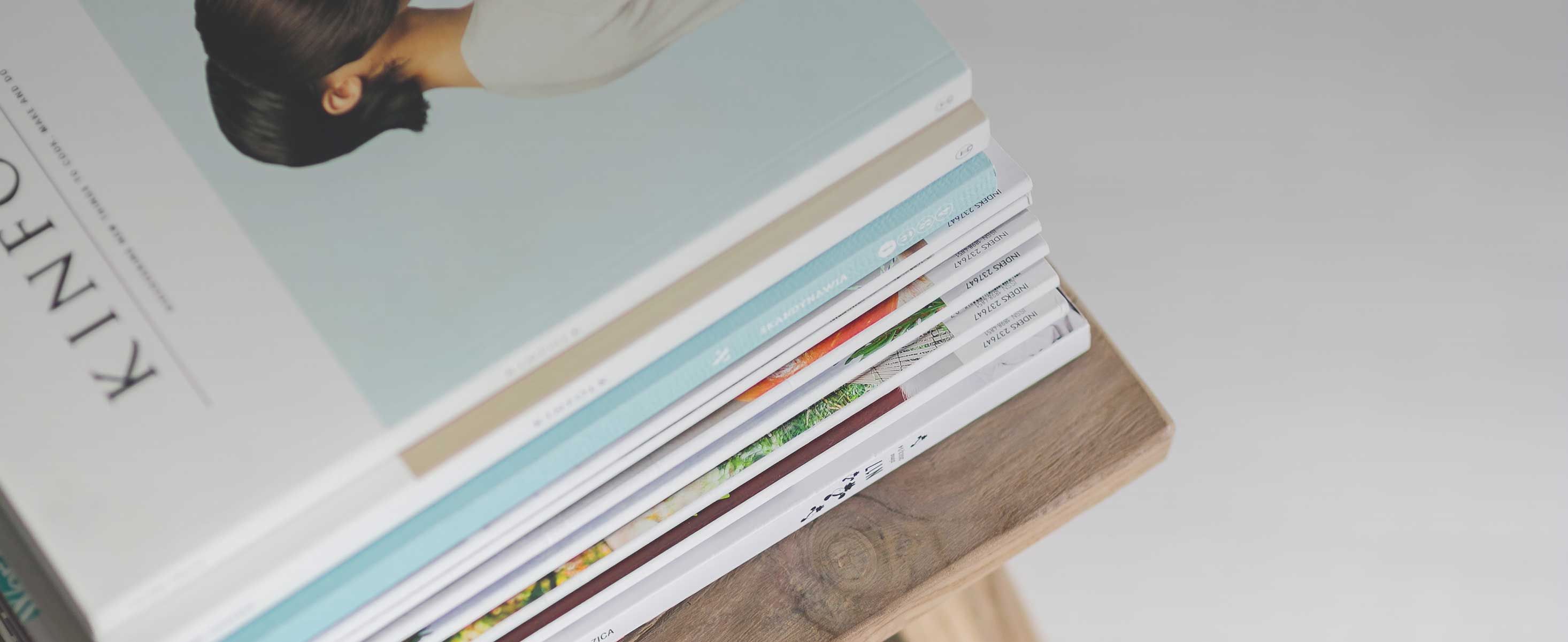
1 minute read
Midtherm goes full fibre
and a host of other materials. It gives us more capacity to target new opportunities and, importantly, means three quarters of our machines are now fibre technology instead of gas.
“With this in mind, and when you consider we have also invested in LED lighting, sensor switches and electric vehicles and charging for our staff on the road, it’s not difficult to see how we have managed to cut our energy usage in half since 2018.”
Midtherm was originally established in 1968 by Ray Andrews and operated through sister companies offering powder coating, enamelling and UV flues.
There was a laser cutting machine that was occasionally being used at one of the factories and the decision was taken in 2000 to put it to better use by creating a ‘laser’ business that initially employed just three people.
With orders starting to take off, Ray’s son Richard Andrews moved the business to its current 20,000 sq ft factory on Peartree Lane in Dudley in 2004, with the next big milestone taking place in 2018 when Mark Hannon replaced Dean Cockayne as Director and took over the operation alongside Richard and Kate Birt.
Today, Midtherm Laser works with more than 500 companies across 20 different sectors, cutting or forming various sheet metal from 0.5mm to 30mm to a +/- 0.25mm tolerance.
It can offer the cutting of nonferrous materials without the risk of cross contamination for industries, including food processing and chemical manufacture.
8 midthermlaser.co.uk
William Hughes, a specialist manufacturer of springs and wire components, has enhanced the capabilities of its 80 m2 Class 7 cleanroom with its investment in a digitally controlled Ultrawave Neon 60 Ultrasonic Cleaning System.
The new Neon machine, which is Class I Medical Devices compliant to MDR (EU) 2017/745, compliments existing assets and capabilities in the ISO 14644-1 accredited cleanroom, which include further solvent and aqueous cleaning systems, a UVinspection dark room and various