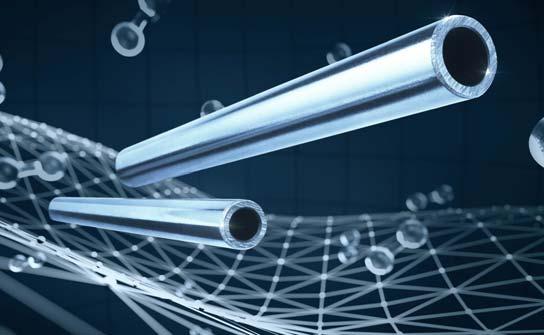
1 minute read
Testing our net zero future
joint projects active and completed at C-ALPS to more than £20 million. This, along with the level of interest we are seeing from collaborators, is a sure sign that we have created the environment and expertise required to support UK companies in meeting future propulsion technology demands.
Besides research and engineering development, the third role of C-ALPS is to create a real-world training environment for engineers and research specialists of the future and the recent £4 million plus contract haul will help deliver more employment opportunities.
So far seven engineers have been taken on as FEV employees - three of whom have come through the university’s undergraduate courseswith 10 PhD students working on joint projects sponsored and co-supervised with FEV in the UK and Germany.
Jörn Behrenroth, Managing Director of FEV UK, emphasised the importance and advantages of the centre: “At C-ALPS, we offer organisations, from both research and industry, the opportunity to put sustainable hydrogen propulsion systems through their paces throughout the entire development cycle, from component up to system performance development.”
C-ALPS also hosts Coventry University’s Hydrogen Energy research group, which supports the Centre’s commercial activities with a wealth of academic expertise and works in parallel on high-impact, industrial collaborative research projects.
These range from fuel cell stack instrumentation, diagnostics, and thermal management to the development of next-generation materials, processes, and electrolyser cell designs for green hydrogen production.
8 coventry.ac.uk/c-alps
A new alloyed carbon steel offers a high strength, low weight alternative to austenitic stainless steels.
Hydrogen systems for mobile or industrial applications are made up of multiple, interacting components. To ensure reliable storage and transport of the gas within the systems, these components, such as pipes, valves, or rails, must be extra robust and resistant. The components used in hydrogen applications are often manufactured from austenitic stainless steel to fulfil these demanding requirements.
This solution, however, has some disadvantages. For example, stainless steel has relatively low strengths, so the components must be designed with greater wall thicknesses for higher pressure resistance. This increases their weight, while the higher material input leads to higher component costs.
One way to counter these disadvantages is to use carbon steel for hydrogen applications. The Poppe + Potthoff Group has many years of experience in the manufacturing of components made of carbon steels from the field of diesel applications. Building on this expertise, Poppe + Potthoff has designed an alternative specifically for pipes and rails in hydrogen applications: PPH2.
PPH2 is an alloyed carbon steel with high mechanical properties, which are further enhanced by the innovative PPSH annealing treatment. These special