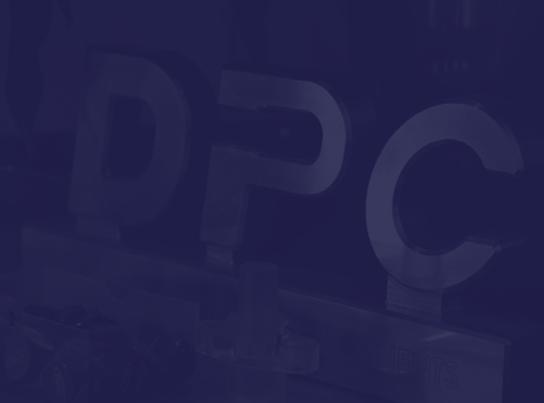
2 minute read
EDM meets automotive demand
Essex press shop and toolmaker Alpine Tools has invested in new wire EDM capacity to keep up with demand from the automotive sector.
With its own press shop serving the production facility of a major automotive plant in Eastern Europe, it needed to invest in capacity for its in-house press operations and various subcontract customers. The company selected a Sodick VL600Q CNC wire EDM machine from a shortlist of six.
Established in 1965, Alpine Tools is an ISO9001-accredited family-owned toolmaking business headquartered in Leighon-Sea, Essex. The company maintains a fully equipped and qualified independent toolroom in support of its own press shop, as well as a broad spread of subcontract customers. The press shop houses both mechanical and hydraulic presses ranging from 12 to 120 tons in capacity, running progression and single-operation tooling for producing automotive parts. All components have full traceability that help Alpine Tools to maintain customer score cards of 100% for on-time delivery and quality.
Although a relatively small company it has a major longrunning automotive contract that sees for a range of pressed stainless steel brackets for vehicles assembled in Eastern Europe.
The new machine arrived in November 2022, with installation, commissioning and training passing off smoothly.
“Since then we’ve kept the machine busy with a variety of tasks, including the manufacture of high-precision press-tool punches and dies,” said Mr Chetland. “We also use our new Sodick wire EDM to undertake press-tool maintenance.”
In addition, the machine will serve the company’s subcontract toolroom operations. Here, the company produces fixtures for machining and welding, along with inspection gauges and other tools from materials such as tool steel, stainless steel and even aluminium. These tools end up in sectors such as medical, heating and lighting.
Mr Chetland added: “We’re an independent toolroom so we’ll take on anything that comes through the door. The new Sodick gives us greater accuracy, better economy and a somewhat larger working envelope than we had previously, providing us with a wider scope of work to pursue.
“Our diversity of skill and knowledge sets us apart from standard milling and turning shops. We have a lot of toolmaking experience and understand the purpose of what we manufacture. Also, we often have customers come to us with a problem, so we set about designing a solution.”
8 alpinetoolsltd.co.uk
The original engine of the A-series Classic Mini included a 32 kg cast iron block. Imagine the improved performance if the latest advances in engine technology were applied today. This is what inspired Smethwick-based subcontractor A&M EDM to create its own engine, a road race version with a block machined from solid aluminium weighing just 20.55 kg with end caps fitted.

Launched in the first quarter of 2023 and marketed worldwide under the Ascaso brand name, the A+5 1273 cc K16V turbo engine was successfully circuit tested in December 2022 at the Llandow race circuit in South Wales by racing legend Jim Lyons. He originally loaned his Mini to the subcontractor so it could laser-scan and reverse-engineer the body and engine bay, while similar was also done on legacy engine components.
Mr Lyons commented, "It's amazing how different the car felt. The steering was so much sharper with the lighter engine block and the engine just wanted to rev! We were still using the multi-piece development crankshaft, so rpm was limited to 7,000, although the engine has revved to 9,250 rpm during test." A lap time of 43.04 seconds was recorded, which is only 0.75 seconds slower than the lap record.
The project is the brainchild of Gary Surman, previously technical director at A&M EDM, a business that has grown since 2002 from two employees and a rented machine to a