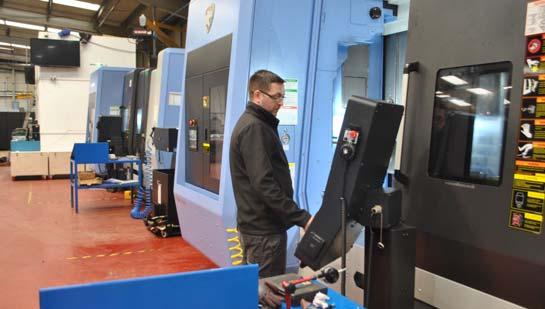
2 minute read
Tooling up for product launch
Investment in a second-hand mill-turning machine will help Glenhead Engineering fulfil a new, three-year contract to machine complex, high-precision metal components for a new product that will be unveiled later this Summer.
Mills CNC supplied the DN Solutions 10” chuck/81mm bar capacity SMX 2600S, equipped with powerful, high torque 26kW/4,000rpm (700N-m) opposing spindles, a 40-tool position ATC, a B-axis 12,000rpm milling spindle and a self-centring steady rest.
The machine was installed at Glenhead’s facility in Clydebank in February 2023, and has been positioned adjacent to the company’s first mill-turn machine, a Doosan 12” chuck/102mm bar capacity SMX 3100, acquired by the company in March 2022.
Bob O’Donnell, Glenhead Engineering’s managing director, said: “Publicity and promotion surrounding the collaborative joint venture is limited until the launch. NDA’s are in place, and we can’t say too much about the initiative at this moment in time.
“Suffice it to say, this is a major machining contract for us and one that will, for the next three years, take up the entire machining capacity of our two mill-turn machines.”
With the launch fast approaching, both machines are currently in pre-production mode and are being used to fine tune the machining process before moving into full production in the next couple of weeks.
Glenhead, which employs 34 members of staff, provides customers with a comprehensive range of integrated in-house services from Design for Manufacture (DfM) and reverse engineering through to high-quality machining and assembly.
Bob O’Donnell added: “We are always looking to improve the services we provide to customers.
“As a matter of course, we systematically benchmark and review our performance against KPIs and, if and when we identify areas of the business that need to be improved, we act decisively and invest.
“We know, from our own experience, that multi-axis machines, and their ability to machine complex, high-precision parts in one-hit, have been more than instrumental in helping us increase our productivity, improve our process efficiencies and give us a distinct competitive edge.”
8 glenheadengineering.co.uk
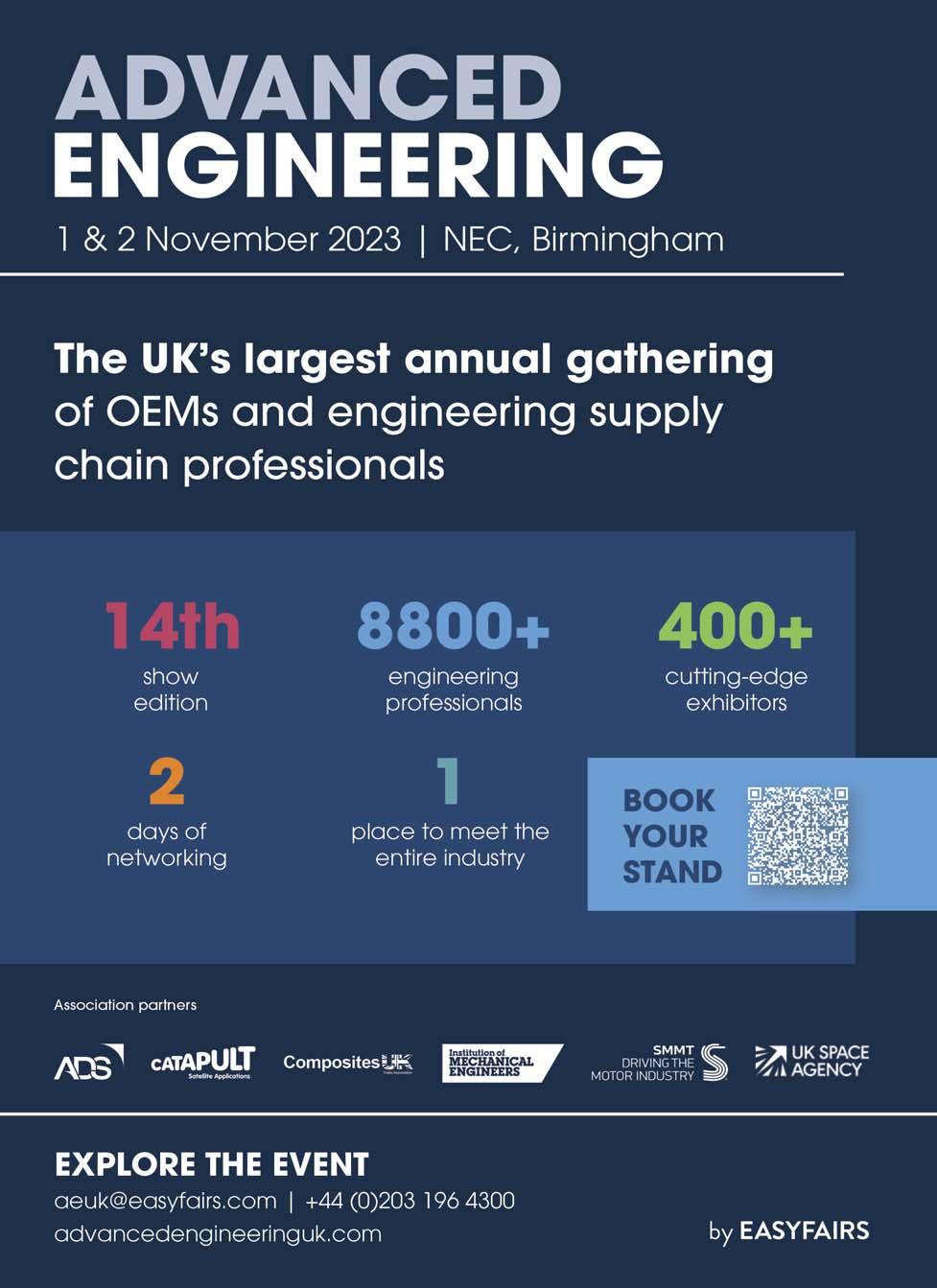
A new tube laser means Lasercell can eliminate the additional cost and lead time associated with outsourcing and can design parts more efficiently.
The Trumpf Trulaser Tube 3000 fibre system not only eliminates the cost of outsourcing tube cutting and reduces lead time, it also allows Lasercell to design parts more efficiently.
Lasercell was set up in 2012 and now employs 25 people. The company initially focused on architectural sheet metalwork using a flat-bed laser, but now it has diversified into areas such as shop fitting, marine and general engineering.
“Primarily we are a laser profiling subcontractor, both sheet and now tube laser,” said one of three company directors Kieran Bernstein. “It provides a good balance – a fairly even split – with the other side of our business, architectural metalwork. From a subcontract perspective we take on almost anything, although we tend to pick up a lot of thinner gauge laser work in attractive metals such as brass, copper and stainless steel.”
With business growing the company investigated the potential for adding an in-house tube laser facility.
“Not only would a tube laser eliminate the cost of outsourcing, it would allow us to design some of our architectural metalwork differently,” explained Mr Bernstein. “Previously, if we had an urgent job, we would have