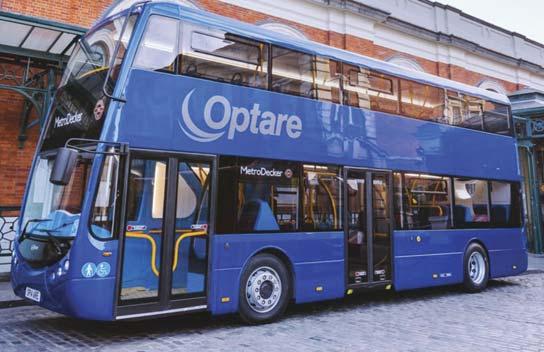
34 minute read
Composites
Swapping diesel for hydrogen
Permali has won UK Government funding to develop a lightweight composite solution that will allow existing diesel-powered buses to be retrofitted with zero-emission hydrogen powertrains.
The objective is to rapidly develop an affordable green technology alternative that can accelerate the ability for the UK to meet its net zero emissions target.
The funding has been awarded by the Office for Low Emission Vehicles (OLEV) through the Niche Vehicle Network (NVN). The Permali R & D team, located at the company’s main site in Gloucester, will be working on this development project in collaboration with leading hydrogen and fuel cell specialist company Arcola Energy and the UK National Composites Centre (NCC). The partnership project is initially aimed at buses, but the new technology concept should be transferable to a wider range of vehicles, such as heavy-duty goods vehicles, trains and even aircraft.
Permali will work in close collaboration with the NCC to design and manufacture the proof of concept system. Arcola Energy will integrate and test the system with the hydrogen cylinders to achieve regulatory compliance and fit the new system to a double decker bus. The NCC approached Permali knowing their extensive experience in handling complex projects and proven track record in the F1 automotive, aerospace, defence, rail and energy sectors as a highly responsive provider of advanced materials solutions.
The project focus for Permali will be on the development and production of a low-cost, lightweight composite system which will structurally support the hydrogen fuel cylinders. The target for the Permali development team is to halve the weight of the current metallic hydrogen fuel tank structure and to increase energy storage by 25%, while still providing the required structural performance to meet the vehicle road safety standards.
Permali’s Sales & Marketing
Director, Fraser Rankin, commented: “This is a fantastic ‘‘This is a fantastic win for Permali demonstrating the ability to create an innovative
win for Permali demonstrating the ability to create an innovative solution within a short time frame and to the complexity of the project requirements. Our dedicated and loyal team have been instrumental in the funding win and I’m excited to see Permali’s influence on a breakthrough project which contributes towards the UK’s carbon neutral goal.”
Hydrogen fuel provides a highly efficient zero-emission alternative to diesel. It is especially suited for buses which operate on longdistance, high-capacity routes. By retrofitting existing diesel engine buses with hydrogen powertrains, bus operators will be able to cost effectively run zero emission fleets, with a combination of retrofitted hydrogen powered buses for longer routes alongside electric battery powered buses for shorter routes. 8 permali.co.uk
Component manufacturer Rockwood Composites has grown its turnover almost ten-fold in the past ten years and grown its workforce six-fold.
This has included over 50% growth compared to last year in the midst of huge uncertainty for the engineering and manufacturing sectors. Rockwood has gone from strength to strength recently in the face of the pandemic increasing turnover strongly and continued recruiting throughout with a 20% increase in staff in the last six months.
Rockwood designs and manufactures composite components using out-ofautoclave techniques, compression and bladder moulding of pre-preg composite material in metal tooling. It delivers cost effective solutions to technically demanding problems, showcasing first class quality components, promptly delivered into a wide range of sectors.
Mark Crouchen, Managing Director of Rockwood Composites, said: “Within the last 10 years, we have vastly expanded our services. We are proud to have worked with so many OEMs across the defence, aerospace, nuclear and marine sectors, to name but a few.
“The relationships that we have built with our customers over the past decade enables us to provide an excellent service. We work closely with customers and strive to over-deliver on product quality and cost effectiveness, providing continual process improvement for cost and performance optimisation.”
Ten year success story
Rockwood has been supplying a wide range of industries, including aerospace, marine, defence and nuclear and has established a proven track record of delivering complex structures.
The company aims to continuously invest in innovation to ensure customer satisfaction, developing new methods when no off-the-shelf product is available, such as manufacturing a high voltage (HV), high stress, electrical insulation systems for cryogenic applications using high pressure moulding (HPM) of prepreg composite and polyimide film, to overcome existing products’ limitations.
This innovative technology has been applied to a new fusion reaction power generation system where the integrity of the HV insulation is a critical element in the construction to inhibit electrical short circuits within cryogenic high-power generation systems.
The press moulding process enables faster cycle times and produces high quality components which require a minimum of finishing. Rockwood started with one press and one CNC. It now has nine presses of varying sizes to cope with a wide range of components and five CNCs.
Mark Crouchen said: “The Rockwood technical and development team has gained expert knowledge and experience in the field of composite materials and manufacturing processes over many years of designing, developing and manufacturing composite components for a wide range of highly specialised applications.” 8 rockwoodcomposites.com
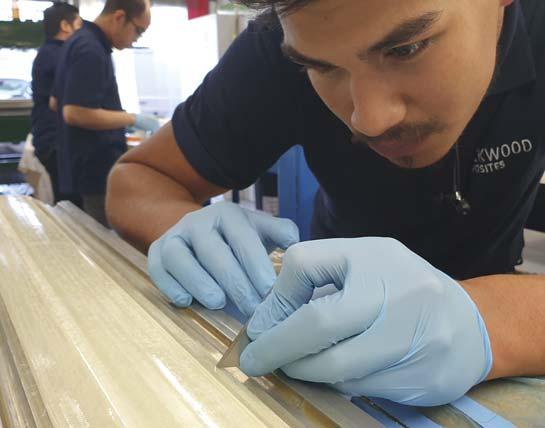
KUKA’s on premise metallurgical laboratory, undertakes the study, development, design and improvement of processes that transform various metallic combinations into products intended for use in high intensity applications, in industries such as; oil and gas, automotive, power generation and aerospace.
This dedicated metallurgical examination service helps our customers to feel more confident, as we examine all possibilities, compare various properties, and advantages/disadvantages of different material combinations to ensure that product integrity, material composition, component design and service life are considered.
Perhaps the most valuable role is in aiding customers to help them to avoid potentially expensive mistakes. Achieving a seamless weld/join is critical, as costly incidents can occur when fatigued products enter the manufacturing process, resulting in defective critical parts. Customers are increasingly under cost pressures and can be tempted to take advantage of what may look like very favorable prices for steel (for example) from a new supplier, perhaps from some distant shores. But cheaper material will not be a real bargain if it does not come up to standard. In fact, the consequences can be disastrous, and the cost implications high.
Rotary friction welding is a solidstate joining process which works by rotating one workpiece relative to another while under a compressive axial force. Some of the components that can be produced include (but are not limited to) drill pipes, truck axles, and engine pistons. Other more tropical components can also be produced from complex material combinations, such as copper and aluminum conductors for use in areas such as power generation. Product integrity in all areas of production/ manufacture, is
Metallurgical confidence
paramount to component performance within their specific applications. It is for this reason that a reliable metallurgical analysis is recommended, pre-production, to ensure that any multiple metallic combinations are not only compatible, but that the strength of the weld thereafter, is sufficient that the component can be used within the application that it is intended.
Rotary friction welding, like any welding process can have an impact upon the properties of the materials that are being bonded, for that reason, prior to a product being released to market, KUKA can conduct a series of testing and analysis using SEM (Scanning Electron Microscope) alongside EDAX methods (Energy Dispersive Analysis X-ray) conducted on premise by Professor Kameel Sawalha – Specialist in the examination of the integrity of all types of welding including rotational and Linear friction welding of all types of materials.
KUKA's metallurgical investigations range from straightforward elemental analysis to in-depth studies of failure or fracture mechanisms, a series of visual, metallurgical and mechanical inspections and checks for instance, hardness surveys, micro and macro inspection, mechanical testing including bend testing and tensile testing. We also offer materials selection advice, assessing their suitability for friction welding and recommending improvements where appropriate. 8 www.kuka.com
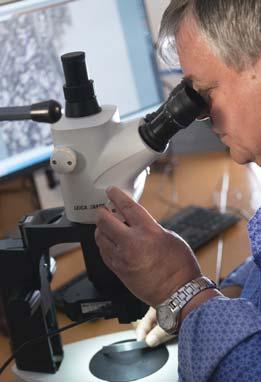
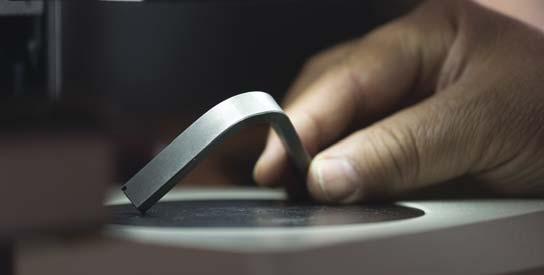
Shaking up battery testing
In response to growing demand from the UK automotive industry for advanced battery safety testing, HORIBA MIRA has invested £1.5m in a new Large Climatic Vibration Laboratory and Battery Abuse Facility.
Set to open in October, the new Large Climatic Vibration Laboratory is the UK’s first battery vibration test facility - or ‘shaker’ as it’s known in the industry - to also offer electrical and thermal cycling. It enables battery charging and discharging whilst in use, along with climatic capability, to carry out tests in ambient conditions ranging from -40°C to 100°C.
The new twin vibration facility can operate in three axes and has the capacity to vibrate up to one tonne of mass, making it ideal for testing the biggest EV batteries on the market to regulatory standards such as UN38.3 and ECEReg100.
The unique ‘shaker’ is the second part of a recent £1.5m investment by HORIBA MIRA into battery safety related testing, which includes its new Battery Abuse Test Facility (BAT) that opened in July. The BAT facility provides abuse and safety testing at cell, module and pack level, in all-weather conditions, supported by high speed cameras, thermal imaging and gas detection.
This £1.5m investment significantly strengthens HORIBA MIRA’s comprehensive battery development capability, enabling end-to-end engineering and test solutions for cell, modules and complete battery packs.
The two new facilities answer demand from the UK automotive industry for advanced battery safety testing capabilities, many of which were not previously available in the UK or did not meet the latest industry needs.
In fact, the distinct advantage of the new ‘shaker’ is that it can electrically and thermally cycle a battery during vibration testing and is fully programmable to reflect actual vehicle duty cycles –a unique function in the UK that will help provide test results that are representative of real-world conditions.
Another major benefit of using the Large Climatic Vibration Laboratory is that tests that have traditionally been performed individually can now be done simultaneously. This reduces the overall test duration and the number of test samples required, providing the added bonus of lower product development costs.
Eamonn Martin, Solution Manager for Electrification and Environmental Validation at HORIBA MIRA, said: “The environmental and societal drive towards zero emissions transport has increased the need for more advanced battery engineering and the testing capability to support that. At HORIBA MIRA we’ve been developing batteries and testing them for our customers for almost 20 years, this latest investment complements our existing EV battery development portfolio with additional capability to validate the latest battery technologies.
“Our new Large Climatic Vibration Laboratory, or ‘shaker’ as it’s known, along with the Battery Abuse Facility opened earlier this year, will enable our customers to access a comprehensive range of battery test capabilities –regardless of size, weight and complexity – with the option of a fully managed test service.” 8 horiba-mira.com
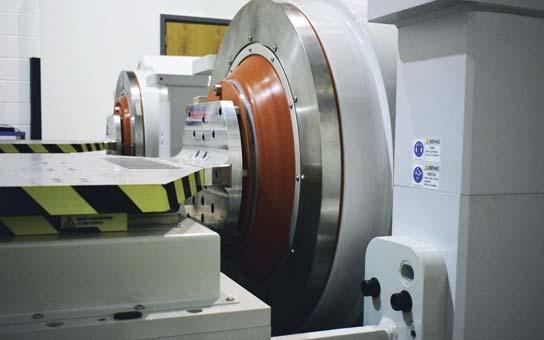
Williams Aerospace Engineering has cut turnaround times after investing in a new CNC vision system that has increased measurement efficiency by 96%.
The Baty Venture XT CNC Vision System is used to measure critical precision machined components manufactured at its facility in Northam, Southampton.
The company specialises in 5-axis CNC turn-milling, 4-axis milling, internal and external gear and spline cutting, internal and external grinding, match grinding and honing. Size range from 0.062”- 6” diameter and the business works to tolerances of .002mm (0.00007”) with 1 microinch surface finish.
Components machined by Williams Aerospace Engineering are used in some of the most extreme environments, including the aerospace, defence, nuclear, medical, Formula 1, performance car and commercial markets.
One of the biggest challenges facing Williams Aerospace Engineering was the sheer amount of time it took to measure components and collate all the data for its customers. For example, for a customer with particularly high measurement requirements, it would take the quality department 1-2 days to measure the positions of 2 holes on a batch of 100 cover plates, in addition to having to input data to an Excel spreadsheet to customer requirements.
Since the investment in the Baty Venture XT CNC Vision System, this measurement process can now be completed in
Faster precise parts
just 2 hours, which is a massive 96% increase in measurement efficiency. The inspection team at Williams Aerospace Engineering is now able to load the fixture onto the machine, insert a part, recall the programme and teach the datum position, completing the batch of the same 100 parts within this much shorter timeframe.
David Fripp, Managing Director at Williams Aerospace Engineering said: “The Baty Venture XT helps to ensure our product quality by giving us a more consistent and repeatable measurement method. Once a program is written, the Venture is far more accurate than our old manual CMM, which is reliant on the points taken by the operator moving the probe by hand, rather than the CNC control on the Baty system. It is very easy to use and the camera resolution is far more accurate than a standard projector using surface illumination.”
Williams Aerospace Engineering uses the vision system for measuring lengths, radii, rads and angles. The measurements are either taken directly from the part loaded on the machine, or if it is an internal feature, it is reproduced using a rubber compound. The mould is then sectioned and measured on the projector as with an external profile.
David continues: “The Venture gives us the flexibility to measure countersink diameters whilst measuring hole positions on the same part. Due to the camera’s focal length, it is also possible to focus on counterbores or countersinks that are located within a bore and take measurements, rather than take a mould and use a standard projector. We’re very much looking forward to seeing how much more we can achieve with this piece of equipment in the future.” 8 williams-eng.co.uk ‘‘Due to the camera’s focal length, it is also possible to focus on counterbores or
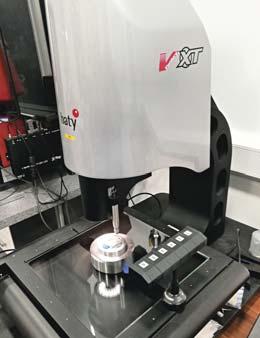
Addition Design has expanded its range of services with the installation of an industrial additive manufacturing (AM) machine for the batch production of components in a variety of highgrade engineering polymers.
The Prodways ProMaker P1000, housed within a dedicated production suite at the Sheffieldbased consultancy’s facility, is one of only a handful of such machines installed in the UK and will enable the company to support high value manufacturers in the scaling up and quality production of their industrial 3D printed components quickly and efficiently.
The new manufacturing capability complements Addition Design’s existing consultancy, design and training services to provide a complete one-stop shop to help companies realise the benefits of additive manufacturing.
“AM can deliver significant added-value to many businesses
3DPRINTUK can now offer an expanded range of services and materials following investment in new post processing equipment.
The new offering includes PrimePartST flexible PEBA material, a shot peening service to enhance surface finish, it has now unveiled new colour options following investment in new DyeMansion equipment.
Nick Allen, CEO at 3DPRINTUK says, “ Introducing PEBA means we can now provide a flexible, rubber-like material in addition to nylon 12
Large scale 3D print
in terms of cost and waste reductions and profitability improvements,” commented Ben Smith, Addition Design’s AM Development Engineer. “Our ability to manufacture and supply AM components in engineering polymers such as nylon, glass and carbon fibre reinforced nylon, polypropylene and thermoplastic elastomers, enables us to support customers in getting the best out of the technology, providing a notable return on investment and boosting their bottom line.”
While 3D printing is more commonly associated with lowvolume production and rapid prototyping, additive manufacturing utilises industrial 3D printing technology for series or volume production of end-use components. AM can deliver production efficiencies and supply-chain flexibility, minimising down time and equipment maintenance.
Addition Design provides specialised consulting, training and component manufacture in 3D printing, tailored to customers’ individual requirements. The company’s objective is to unlock the potential of 3D printing to deliver cost and performance benefits for its clients. 8 addition.design

New colours and services and shot peening means the most comprehensive PBF we can provide a production capabilities in superior surface finish the UK and further afield.” than ever before to our The Dyemansion DM60 nylon parts. Our machine completely investment in the new automates what has until DyeMansion machine, and recently been a manual, our traditional exhaustive testing, uncontrollable colouring process means that we can now provide for 3D printed parts. The dyes parts in blue, green, red and used penetrate to a depth of yellow, with more colours to 200 microns, and the process follow. We have now invested over is totally reproducible, £100K in dying systems, ensuring traceable, and works for that we respond to customer every part geometry. demand and continue to provide 8 3dprint-uk.com
Satair, an Airbus services company, has provided one of its airline customers in the US with what is believed to be the first certified metal printed flying spare part.
This A320ceo specific part is no longer procurable from the original supplier, thus leading to an alternate solution developed by Satair. The tailored additive manufactured solution reduces the likelihood of an AOG (aircraft on ground) for this specific aircraft, and on a larger level leads to an increased flexibility in part production while meeting the same high quality standards ensured by EASA Form1 certification.
The A320ceo wingtip fences are installed in four different versions – starboard, port, upper and lower. These parts are A320ceo specific and no longer in production. The spare parts supplier had difficulties providing the cast part. This led to a regular loss of the moulds, resulting in a potentially high investment cost for Satair to replace the moulds for individual orders. Satair also studied other conventional options such as redesigning the part for machining technology, but the resulting cost and lead-time implications were not competitive.
Felix Hammerschmidt, HO Additive Manufacturing Satair, explained: “We received an order for replacement parts and our AOG procurement department turned to the Additive Manufacturing team for a solution. After a short pre-assessment, the part was handed over to the RapidSpares design offices at
Metal printed plane spare
Airbus. Using a new certification process they were able to recertify the former cast part within five weeks and adapt it to titanium, which is a qualified airworthy additive manufacturing material”.
The printing of the wingtip fence parts was carried out at the Reference Manufacturing shop in Airbus Filton. Four parts (full shipset for one aircraft) are printed simultaneously in a build job, which takes 26 hours, to reduce the cost per piece and the printing time per part.
After printing, the part requires different post-processing steps to become an airworthy part, making it a one-to-one replacement for the original part whilst meeting the same safety requirements as the conventional part.
The shipset was delivered earlier this year – making the airline the first operator with an Airbus metal printed AM spare part. Compared to conventional solutions, total non-recurring costs were reduced by 45% making it a cheaper solution for customers and with a shorter lead-time.
Bart Reijnen, CEO of Satair, added: “Satair is leading the way in providing additive manufactured parts for the aviation aftermarket and we currently have more than 300 part numbers certified for the technology covering every Airbus aircraft family type including tools and Ground Support Equipment. With more than 7,000 A320ceo family aircraft in service worldwide, the demand for this specific additive manufactured part is likely to increase and with this Additive Manufacturing supply chain now in place, we will be able to produce these parts within a shorter lead-time. Four more customers have already requested that same part following this successful delivery.“ 8 satair.com
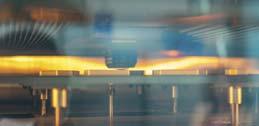
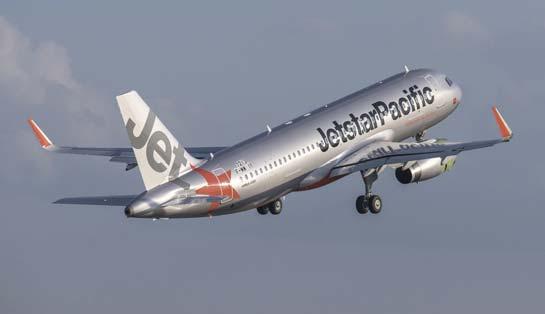
Keeping it clean for packaging
Cleanroom thermoforming can offer ideal packaging solutions for medical devices, writes Todd McDonald, Director of Sales & Marketing at TEQ
The world continues to witness a rapid development in technological brilliance but what must not be overlooked is that the importance of protecting that technology becomes increasingly vital.
Improvements to packaging design are now a necessity. At the same time, there is a demand to deliver products in a packaging solution that adheres to strict specifications while using less production energy and material as well as faster production times.
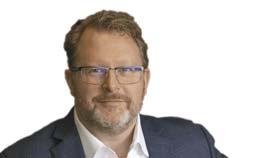
So, what is thermoforming?
Cleanroom thermoforming is widely used for the production and packaging of pharmaceuticals and medical equipment.
This method of thermoforming is carried out in an ISO certified cleanroom meaning any particulates circulating in the air are kept to a minimum.
Thermoform packaging is extensively used to safeguard sterile instruments and implants. This packaging method permits the use of lightweight, clear plastic enclosures that stop microbial and dust particles from contaminating the sterile item.
They also make possible the product’s secure storage for lengthy periods whilst maintaining the sterile environment.
The benefits of thermoforming
This advanced technology has established itself as a preferred option for many industries and applications, including medical devices, with the main benefit of this packaging solution the clear cost efficiency it offers. The stiffness of this type of packaging material also allows for the creation of smaller units and space-saving benefits. The stiff packaging also offers a barrier to odours and resistance to oil and grease.
Packaging from cleanroom thermoforming also has the capacity to offer advanced protection of medical devices and the importance of this cannot be underestimated as the packaging of medical devices is as important as the product itself. Once the packaging’s integrity is compromised, sterility is lost and the device is ruined. This is why thermoforming is an ideal solution.
Thermoformed plastic packaging can offer several other advantages including: 8 Product Orientation: A nurse may need to quickly confirm a product’s orientation and how to grab it. With a thermoformed tray, a nurse can be sure that the medical device stays securely in place in the intended location so he/she can remove it swiftly and confidently. 8 Handling Assurance: To ensure a device doesn’t compromise
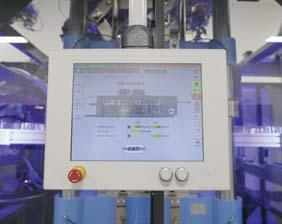
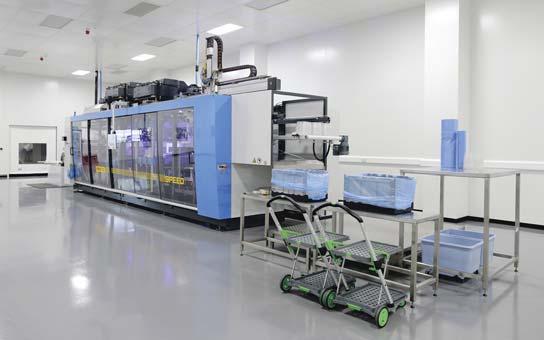
sterility, a nurse needs to control the movement of a device as its package is opened. A thermoformed package is more likely to ensure there is no unnecessary rotation or accidental removal. 8 Clarity: A nurse can find it beneficial to see and identify the product clearly so he/she can better present the device or see any potential defects. 8 Consistent Opening Experience: Incorporating a good peal area in the package design can allow a nurse an easy access point for pealing the lidding back from the package. 8 Additional Protection: With rigid plastic, a medical device is protected in sensitive device areas. For example, a package can be designed so a syringe will not get depressed. 8 More Ergonomic: A pouch can require both wrists to twist to open, putting repetitive strain on both of the nurse’s wrists. With a sealed thermoformed tray, only one hand is opening the seal while the other is holding the tray in place.
Impact of COVID-19 Pandemic
There are clear signs that the COVID-19 Pandemic is having a significant impact on the design and manufacture of medical devices, equipment and implants.
In these uncertain times medical manufacturers have had to ramp up production to meet heightened customer demand.
Cleanrooms have firmly established themselves as an integral part of the production process as cleanliness can be guaranteed in their controlled and sterile environment, preventing potential contamination caused by bacteria or air pollutants.
Companies that make medical devices and the packaging for them have to meet the most stringent regulations from various organisations.
One of them is The ISO (International Organisation for Standardization) which consists of a group of non-governmental bodies operating in 164 countries. It is entrusted with the power to enforce exacting standards for a range of commercial markets.
In 2016 it published the latest edition of its ISO 13485 which sets out to ensure patient safety by the regulation of hygiene and contamination control in medical product development.
It is generally recognised that the main hurdle to overcome when designing cleanrooms is their ability to deal with any air pollutants. Filtration units are used by manufacturers to control airflow and stop airborne particles larger than a pre-defined size from entering. A range of devices can make this happen such as ionisers, carbon filters and nonfilter purifiers.
Another approach to preventing cleanroom contamination is by providing a high standard of training for staff and ensuring they wear correct PPE such as gowns, hairnets and overshoes.
Manufacturers are also advised to keep correct supplies and equipment in clean spaces and, where appropriate, dispose of or sterilise them. Regular risk assessments ensure ongoing improvements can be made to foil any new contamination threats triggered by ever evolving technologies.
One thing is for certain, continued innovation and the advance in technology in the medical sector brings with it unlimited potential.
Manufacturers will face the same pressures to cut costs and be even more efficient by introducing more automation on the assembly line, utilising the likes of robots and smart testing. AI and machine learning can also expect to play a role by boosting quality standards and early detection of any issues.
New developments and a move towards more complicated products such as nanotechnologies and the miniaturisation of devices are another new challenge that has to be faced by manufacturers in an increasingly competitive sector. 8 teqnow.eu
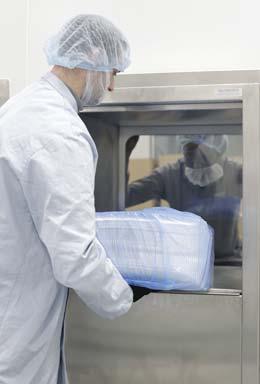
Why is Agile manufacturing so important for manufacturers during the Coronavirus pandemic? asks Atia Bukhari of Grenville Engineering.
According to Wikipedia: “Agile manufacturing is a term applied to an organization that has created the processes, tools, and training to enable it to respond quickly to customer needs and market changes while still controlling costs and quality.”
We are now living in times that are unprecedented and have forced not only businesses but the wider world to adopt practices never implemented before.
It is now a survival of the fittest and who is ready to adapt to change quickly that is successful.
We can give you a taste of our own experiences and how this has benefited us in times of crisis even more importantly as we face the current Coronavirus pandemic
So why is it so important for manufacturers to adopt agile manufacturing?
Culture
Company culture can be a make or break situation in times of crisis and the effectiveness of everyone within the organisation understanding what needs to be done is vital
A committed workforce can rally round to make sure the company fulfils its objectives through ideas and willingness to adapt to change.
Responsiveness to customer demand
A company that adopts agile manufacturing processes can
The need for agility
respond to changes in demand very quickly.
We brief our operational and production staff on a daily basis and make changes on our machines to reflect changes in demand in certain bottleneck areas.
Diversification
Businesses that are successful are the ones that can diversify and open up into markets with fluctuations in demand. Manufacturers have now had to turn their hand to manufacturing ventilators or offering their capabilities in areas outside of their comfort zone.
At Grenville Engineering we have a diverse customer base and ‘don’t have all our eggs in one basket’ which is why the company has grown from strength to strength. We can quickly identify the areas that show signs of growth and adapt to manage that demand.
Our focus has been supplying parts to businesses within the NHS supply chain to maintain a consistent supply of essential parts and to keep manufacturing businesses going.
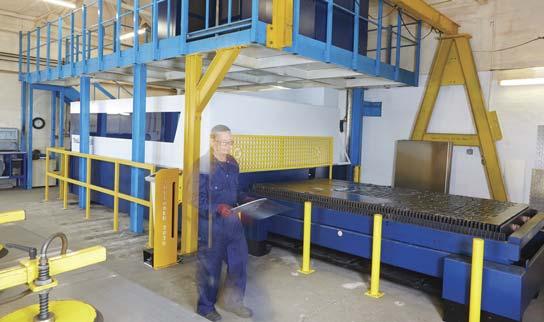
Processes
In an agile manufacturing environment, adaptable processes and the need for continuous improvement can be the driving factors for businesses to be successful.
The nature of our work in metal fabrication is bespoke and our processes have to be adaptable to effectively manage how we manufacture but also changes from external factors.
At Grenville Engineering, customer-centric fabrication solutions are at the heart of what we do. We collaborate with our customers ensuring that we produce the most cost effective solution without compromising on quality. We have a combined experience of over 100 years within the industry, which is invaluable for our customers. 8 grenville-engineering.co.uk
ACSL Precision Engineering sales@acsleng.co.uk www.acsleng.co.uk
Atkinson Engineering sales@atkinson-engineering.com www.atkinson-engineering.com
Auto Turned Products (Northants) Ltd shad@autoturned.co.uk www.autoturned.co.uk
Batchflow Engineering info@batchflow.co.uk www.batchflow.co.uk
Cambion Electronics Ltd sales@cambion.com www.cambion.com
Cambridge Precision Ltd sales@cambridgeprecision.com www.cambridgeprecision.com
CK Precision Engineering Ltd Info@ckprecisionengineeringltd.com www.ckprecisionengineeringltd.com
CTN Group Ltd charlie@ctn-group.co.uk www.CTN-GROUP.co.uk
Currie & Warner Ltd tonyfox@curriewarner.com www.curriewarner.com
Davromatic Precision Limited sales@davromatic.co.uk www.davromatic.co.uk
Dawson Precision Components Ltd. sales@dpc.co.uk www.dpc.co.uk
Dawson Shanahan (Wales) Ltd info@dawson-shanahan.co.uk www.dawson-shanahan.co.uk
DKW Engineering Ltd karl@dkwengineering.co.uk www.dkwengineering.co.uk
Falcon Engineering Productions Ltd sales@falconengineering.co.uk
GS Brown (Precision Engineers) Ltd malcolm@gsbrown.com www.gsbrown.com
G W Martin and Co Ltd sales@gwmartin.co.uk www.gwmartin.co.cuk
H P C Services Ltd sales@slidinghead.com www.slidinghead.com
Haydon Precision Turned Parts Ltd haydontool.co@btconnect.com www.haydon-precision.co.uk
Herve Engineering Ltd sales@herve-engineering.com herve-engineering.com
JCF Engineering Limited john.felton@jcfengineering.co.uk jcfengineering.co.uk
KM Engineering sales@kmengineering.co.uk www.kmengineering.co.uk
M&M Turned Parts Ltd sales@mmturnedparts.co.uk www.mmturnedparts.co.uk
Machined Component Systems sales@machinedcomponent.com www.machinedcomponent.com
Manton Engineering (Bedford) Ltd sales@mantonengineering.co.uk www.mantonengineering.co.uk
MaS Precision Engineering Ltd sales@masprecision.co.uk www.masprecision.co.uk
Muller England Limited sales@muller-england.co.uk www.muller-england.co.uk
NC Precision Ltd sales@ncprecision.com www.ncprecision.com
Neida Products Engineering Ltd sales@neida.co.uk www.neida.co.uk
Normec (Manchester) Ltd sales@normec.co.uk www.normec.co.uk
Plastic turned Parts Ltd sales@plasticturnedparts.co.uk www.plasticturnedparts.co.uk
Precision Component Services Ltd shane@precision-components.co.uk www.precision-components.co.uk
Precision Products (Brighton) Ltd
ian@precisionproducts.co.uk www.precisionproducts.co.uk
Qualiturn Products Ltd
sales@qualiturn.co.uk www.qualiturn.co.uk
Quantamatic info@quantamatic.co.uk www.quantamatic.co.uk
Rodmatic Ltd enquiry@rodmatic.com www.rodmatic.com
Rowan Precision Limited sales@rowanprecision.co.uk www.rowanprecision.co.uk
Salcey Precision Engineering Ltd info@salceyprecision.co.uk www.salceyprecision.co.uk
Swissmatic Ltd info@swissmatic.co.uk www.swissmatic.co.uk
Techfore Turned Parts Ltd info@techfore.co.uk www.techfore.co.uk
Tenable Screw Co Ltd nigel@tenable.co.uk www.tenable.co.uk
Tercet Precision Ltd Alex.Burns@tercet.co.uk www.buyturnedparts.com
Thomas Brown Engineering Ltd info@thomasbrownengineering.co.uk www.thomas-brown-engineering.co.uk
TKM Engineering Ltd Sales@tkmengineering.co.uk www.tkmengineering.co.uk
Trust Precision Engineering Ltd info@trustprecisionengineering.co.uk www.trustprecisionengineering.co.uk
Wealdpark Limited sales@wealdpark.co.uk www.wealdpark.co.uk
Wharf Engineering Ltd sales@wharf-engineering.co.uk www.wharfengineering.co.uk
Wilco Manufacturing Ltd sales@wilcomanufacturing.co.uk www.wilcomanufacturing.co.uk
Yorkshire Precision Engineering Ltd info@ypel.co.uk www.ypel.co.uk
Arno (UK) Limited sales@arno.de www.arno-tools.co.uk
The Amodil Group tkd@amodil.co.uk www.amodil.co.uk
Badger Anodising (Birmingham) Ltd sales@badgeranodising.co.uk www.badgeranodsing.co.uk

Bowers Group sales@bowersgroup.co.uk www.bowersgroup.co.uk
Ceratizit UK & Ireland Ltd info.uk@ceratizit.com www.ceratizit.com
Citizen Machinery UK sales@citizenmachinery.co.uk www.citizenmachinery.co.uk
Engineering Technology Group
sales@engtechgroup.com www.engtechgroup.com
Filtermist Systems Limited
sales@filtermist.com www.filtermist.co.uk
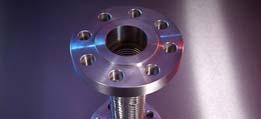
Floyd Automatic Tooling Ltd sales@floydautomatic.co.uk www.floydautomatic.co.uk
Kumi Solutions simon@kumi-solutions.com www.kumi-solutions.com
LNS Turbo sales.uk@lns-europe.com www.lns-europe.com
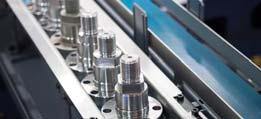
Matsuura Machinery Ltd imichie@matsuura.co.uk www.matsuura.co.uk
Optimum Oils
cliff.thrussell@optimumoils.com www.optimumoils.com
PSL Datatrack
engcap@psldatatrack.com www.psldatatrack.com
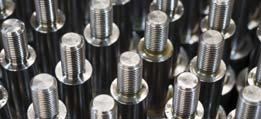
Smiths Metal Centres info@smithmetal.com www.smithmetal.com
Star Micronics GB Ltd sales@stargb.com www.stargb.com
Stelstocks Ltd info@stelstocks.co.uk www.stelstocks.co.uk
Tornos Technologies UK Ltd sales_uk@tornos.com www.tornos.comk
Wickman Coventry Ltd o.coyne@wickman.co.uk www.wickman-group.com
Wieland-Nemco Ltd. sales@wieland-nemco.com www.wieland-nemco.com

JFL Broaches and Broaching JFL are broach and broaching specialists with many years personal experience. We offer a comprehensive broaching service covering keyways, squares, hexagons and special forms. Unit 2, Deethe Farm Industrial Est, Cranfield Rd, Woburn Sands, Milton Keynes, Bucks MK17 8UR Tel: 01908 585103 www.jflbroaches.co.uk
Qualiturn Products Limited
Qualiturn are a very modern subcontract machining service. We offer CNC precision Turned and Milled components to your specifications and quantities. We work with all sizes of customers, offering the same service to all. Supplying various market sectors across the world.
7 Fountain Drive, Hertford, Herts, UK, SG13 7UB Tel. +44 (0) 1992 584499 www.qualiturn.co.uk
8
MACHINING (5 AXIS)
8 PRECISION ENGINEERING
LATHES.CO.UK
Lathes.co.uk
store.lathes.co.uk - where Manuals, Catalogues Drive Belts Books Accessories & Spares are listed The world’s largest machine tool reference archive. Manuals, Catalogues, Books, Pictures Specifications, Technical Guides
Wardlow, Tideswell, Buxton, Derbyshire, SK17 8RP Tel. 01298-871633 (from overseas: +44-1298-871633) from 09:00 to 23:00 UK time www.lathes.co.uk
8
PRECISION ENGINEERING Mini Gears (Stockport) Ltd
Mini Gears is a subcontract manufacturer of machined components, gears and racks. Winner of 17 Industry Awards, it has a global customer base, 35,000 sq. ft. facility and over 100 machines.
Top Gear House, Bletchley Road Heaton Mersey Industrial Estate Stockport SK4 3ED Tel: 0161 432 0222 www.minigears.co.uk
8
PRECISION ENGINEERING
5 High quality precision machined components 5 Trusted technical support service 5 Complete and bespoke service from conception to completion 5 AS9100D & ISO 9001:2015 approved
Oldfield Street, Crosland Moor Huddersfield HD4 5AJ T: 01484 548903 www.thomas-brown-engineering.co.uk
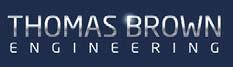
DAWSON PRECISION COMPONENTS
Manufacturing precision machined components since 1965 Services include: CNC milling, CNC turning, turn/mill machining, sub contracted services, finishing and project management.
Greenfield Lane, Shaw, Oldham, Lancashire, OL2 8QP Tel: 01706 842311 dpc.co.uk
8
PRECISION ENGINEERING Wealdpark Ltd
CNC mill-turn facility using Star sliding head lathes with bar capacity up to 32mm diameter. Miyano and Doosan fixed head lathes with bar capacity up to 65mm. Hurco vertical machining centre.
Sutton Road, St. Helens Merseyside WA9 3DJ Tel: 01744 22567 www.wealdpark.co.uk
8
REPETITION TURNED PARTS Kirkham Engineering Co Ltd
13 - CNC Sliding Heads up to 1”; 14 CNC Twin Turret Fixed Heads up to 65mm; 5 - Twin Turret Twin Spindle; 5 - Twin Turret with Sub-Spindle and 4 - Twin Turret; 4 - CNC Single Turret Fixed Heads up to 6” Billet. Centreless Grinding & T/rolling. All materials - Stainless Steel; Nickel Alloys and other exotics a speciality.
Prestwood Place, East Pimbo, Skelmersdale, Lancashire WN8 9QE Tel: 01695 727401 www.kirkhamengineering.co.uk

Grenville Engineering (Stoke-on-Trent) Ltd
With more than three decades of experience and dedication in producing the highest quality products, Grenville maintains its position as the leading precision sheet metal fabrication company.
Unit 3 Newfield Industrial Estate, High Street,Tunstall, Stoke-on-Trent ST6 5PD Tel: 01782 577 929 www.grenville-engineering.co.uk
8
SUBCONTRACT CNC TURNING
Engineering Capacity|INDUSTRY NEWS SEPTEMBER 2017 Growth support helps 1000 SMEs More than 1000 small tomedium-sized manufacturers(SMEs) have been given a business boost over the last tenmonths thanks to a new £9.7mbusiness support initiative. The Manufacturing GrowthProgramme (MGP), funded by theEuropean Regional DevelopmentFund (ERDF) and delivered byEconomic Growth Solutions (EGS),has helped companies across the UK to grow, develop newproducts and overcomeproduction issues that werepreviously holding them back.This has already led to 400 newjobs, with an additional 359 positions expected to be created once ongoing projects arecompleted. By the end of July,£1.6m of grant contributions havebeen made, with money in placeto support another 2200 firmsbetween now and March 2019.Lorraine Holmes, ChiefExecutive Officer of EGS, explained: “We are way above thetargets we have set for ourselves,proving that there is a real appetitefrom SMEs for targeted businesssupport that can help them grow.“The difference with ourprogramme is that it is deliveredby manufacturing experts whounderstand the challengescompanies are facing. Theyunderstand the language MDs are talking and can guidethem on making the right decisions, before bringing inspecialists on specific issues theyare facing or opportunities they’re looking to explore.”She continued: “1000 beneficiaries is just the start. We’ve still got a lot of grants todeliver and we wantmanufacturers to come forwardand see how they can take advantage of the assistance on offer. It’s never been easier, as theprocess is quick and the scope of support can be tailored to the exact needs of the business.” The Manufacturing GrowthProgramme was set up to fill the void left by the ManufacturingAdvice Service (MAS) by providing access to specialistassistance to help manufacturersto grow and improve.This is being achieved throughan 18-strong network ofexperienced manufacturinggrowth managers (MGM), accessto industry specialists and theopportunity to apply for an average grant of £1400, rising to amaximum £3,500. Support can be used for leadership and management,R&D, lean manufacturing, productivity and capacity, qualitysystems and supply chaindevelopment.Martin Coats, OperationsDirector at EGS, continued: “Whenfirms come to us they receive astrategic review from one of ourMGMs that determines what barriers are in the way and whatsupport is needed to help them reach their potential. “Since October 2016, thehighest barrier with 15% of clientswas ‘Continuous Improvement’,followed by ‘Environmental’ and‘Marketing and MarketKnowledge’ (12% each). Once theinitial stage has been completed,we then bring in an expert whoworks with the management teamto address these issues.”8 manufacturinggrowthprogramme.co.uk MACHINED COMPONENTS|Engineering Capacity 14 www.engineeringcapacity.com SEPTEMBER 2017 Mill-turning supports lean approachIn the first half of this year Roscomatic has committed to £750,000 of investment, including the installation of the latest Miyano BNE-51MSY multi-axis turn-mill centre. The Worthing-based subcontract machinist company dispatches some 1.5 million parts a year – ranging from completed assemblies and sub-assemblies to large machined castings and small turned parts – and is currently achieving a record on-time delivery rate of 98%. Managing director Joe Martello explains that the company is driven by a philosophy of constant development of lean manufacturing techniques, supported by investment often exceeding £1 million a year and an ‘open-liaison’ people strategy which keeps the workforce up to date on the company and any issues arising. He says: “We invest in automation and the latest production technology which helps to overcome the shortage of skills we would require. However, it is so important that we still need to grow our own engineers through constant support and by training, in order to maximise our return-on-investment and so improve how we support and what we deliver to customers.”In addition to the new Miyano the company has already ordered two Citizen CNC sliding head turn-mill centre machines. The two machines, a Citizen L20-VIII LFV (LFV featuring low frequency vibration cutting technology) and a top-of-the-range M16-V will bring the total Citizen installations to 14. Cell Leader Sean Keet says: “The levels of operational flexibility in the Miyano BNE has enabled us to significantly reduce machining times and most important, improve overall productivity.” He says the new machine has replaced existing 3-axis machines so that a family of 10 aluminium parts that previously required four turning operations and a separate milling operation can now be produced in one turn-milling cycle. A massive bonus is that average total cycle times per part has been cut from 13 mins to just 2.5 mins. A further complex stainless steel component which had three operations taking 11 minutes is now reduced to a single, four-minute cycle.Further return-on-investment comes from freeing-up setters to perform other tasks and from the reduction of lost time for each first-off inspection, reducing the risk of setting and relocation errors and cutting work in progress. The flexibility of the BNE-51MSY is key to its success as it is capable of single cycle cutting with three tools simultaneously overlapped at both ends of a workpiece at the same time, and using bar up to 51 mm bar diameter. The fixed-head 15 kW main spindle and two-axis 7.5 kW secondary spindle, both with maximum speeds of 5,000 revs/min, have the advantage of synchronised / superimposed control for both 12-station, all-driven turrets. Ideal for
www.engineeringcapacity.com 5
Get your company noticed with an Engineering Capacity classified profile advert
FOR MANUFACTURERS ABOUT SUBCONTRACTORS September 2017
INDUSTRY NEWS | MACHINING | AUTOMOTIVE | SHOW PREVIEWS 8
SPRING MAKING
MACHINED COMPONENTS: Prismatic parts from bar
www.engineeringcapacity.com
Call 01737 270648
Subcontract mill turned Subcontract mill turned parts up to 65mm in parts up to 65mm in diameter from bar diameter from bar and 300mm and 300mm billet billet work. work.
– – – – – s yol l A repuS ssarBleetSssel ni a t S scitnimuAl salPmui
Simpson Springs & Pressings Ltd
Precision manufacturers of a wide range of compression tension and torsion springs. Also circlips, wireforms, contacts, antennas and light pressings. Quality approved to BS EN ISO 9001:2000.
Unit 1, Latimer Road Industrial Est, Latimer Road, Wokingham, Berkshire RG41 2YD Tel: 0118 978 6573 www.simpsonsprings.co.uk
8
TURNING (CNC)
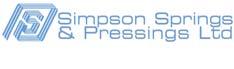
8 TURNED PARTS
8
WATERJET CUTTING Batchflow Engineering Ltd
CNC turning capacity from 2mm200mm using high precision Fixed and Sliding Head CNC Lathes. Experience in machining a range of materials, from Low to Medium volumes, to customers specifications.
Budbrooke Road, Warwick, Warwickshire CV34 5XH Tel: 01926 492889 www.batchflow.co.uk
Precision Products (Brighton) Ltd
A one-stop-shop for high-quality turned parts
Accredited to AS9100 Rev D
Unit 2 Brookside Avenue, Rustington, West Sussex BN16 3LF Telephone: +44 (0) 1903 776 171 www.precisonproducts.co.uk
ICEE Comprehensive fabrication facilities offering complete turnkey solution. Design, Precision Engineering, Sheet Metal Fabrication and Welding. Prototypes, one off or batch work. Waterjet Capacity: 4m x 2.25m & dash; materials up to 230mm depth. Aluminium Alloy Specialists. 20 Arnside Road, Waterlooville, Hampshire PO7 7UP Tel: 023 9223 0604 www.icee.co.uk
