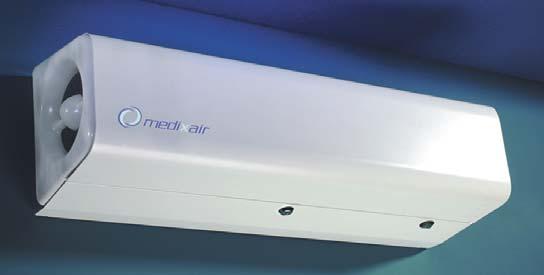
37 minute read
Zapping Covid with UV
Electronics manufacturer CHH CoNeX is helping to produce an ultra-violet air steriliser that could significantly reduce the risk of coronavirus infection.
It is collaborating with air sterilisation specialist Pathogen Solutions on the design and production of Medixair, a portable air sterilisation solution that is proven to eliminate airborne viruses and bacteria.
The patented product, which is the result of 15-years’ development work, was initially derived to help combat hospital acquired infections and Pathogen Solutions now wants to ramp up production.
Following extensive testing over the past few years, the solution has since been installed in Northwick Park Hospital in Harrow among other healthcare environments across the UK. Now, as the world takes action to improve infection control processes, Medixair is playing a significant role, since coronaviruses shares the same morphology as other viruses which the solution eliminates.
There is substantial evidence to indicate that SARS-COV-2, the coronavirus responsible for the COVID-19 pandemic, can be passed from person to person in tiny droplets called aerosols, which travel through the air and accumulate over time. Medixair combats this by providing 24-hour airborne infection control. The 110-watt unit employs high intensity ultraviolet light to decontaminate the air within indoor environments.
The portable machine works by drawing air into the unit and
exposing it to UV light which is a proven method for killing bugs. The clean air is then recirculated back out of the unit. When deployed within medical wards or other indoor settings, the device can provide an additional and effective level of support against infection.
Tim Hughes, managing director of CHH CoNeX, the company responsible for the assembly of Medixair units, commented: “Medixair operates differently to typical fogging machines and uses UV light to clean the air. This method has been used for infection control for several decades. In fact, back in the 1980s researchers found that UV lamps were effective in preventing transmission of tuberculosis and similar technology is now being recommended for use in combatting Coronavirus.
John Burrows, director of Pathogen Solutions, added that Medixair is already in demand across the world. “In addition to interest from domestic customers, we also have demand for Medixair from Indonesia, the Philippines and Europe. Products such as this are going to play a key role in keeping indoor areas safe in our new-normal.” 8 chhconex.com
Visit our website or contact us for a quote or advice
Trade Leads from the EIA
The following FREE OF CHARGE trade leads for the UK engineering industry are currently appearing on the Trade Board pages of the Engineering Industries Association at www.eia.co.uk
Ceremonial accoutrements (UK)
The supply of ceremonial accoutrements consisting of various items (including but not limited to: swords and scabbards, sporrans, feathers and plumes, aiguillettes, etc.) over a 4-year period.
Reference: 34731
Closing Date: 10/12/2020
Carbon steel pipes
The national oil company of Kuwait is looking for a supply of carbon steel pipes.
Reference: 34904
Closing Date: 27/11/2020
Stainless couplings
A Dutch manufacturer of a corrosion free, stainless steel coupling to connect steel pipes is looking to expand and seeks agents or distributors. The coupling are suitable for different streams such as: gas, water, oil, air, etc. and mainly used for pipes used above ground. The company is looking to expand and seeks new agents or distributors.
Reference: JV1434
Closing Date: 04/12/2020
CNC machines
A German SME is looking for commercial and distribution agreements for CNC engraving and milling machines.
Reference: JV1438
Closing Date: 06/01/2021
For more information please email head.office@eia.co.uk quoting reference number. Please remember to use due diligence in responding to Trade Leads. Engineering Capacity provides you with the above information in good faith, but is unable to accept any responsibility or legal liability arising from any use of these leads.
Danielle George MBE
is the new President of The Institution of Engineering and Technology. A professor of radio frequency engineering at Manchester University, she hopes to use her term to get more young people interested in engineering and technology.
Jon Fredrik Baksaas
the former CEO of Telenor, has been appointed as DNV GL’s new Chair of the board. Lasse Kristoffersen will take over as Vice Chair. Experienced in the maritime industry, he is currently the CEO and President of Torvald Klaveness Group.
Helen Blomqvist
has been announced as the new President of Sandvik Coromant where she was previously Vice President of Product Management and Research & Development. She holds two patents and in 2018, she was awarded Sandvik Coromant
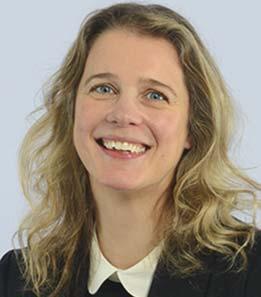
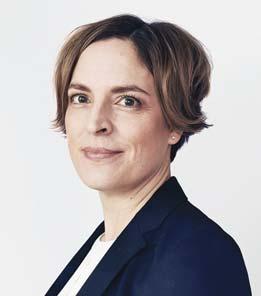
Leader of the Year.
Matt Stevenson
has been appointed as Operations Director Cockayne Systems, a joint venture between Edwards Engineering and DPS Group. The company is a leading manufacturer of cask filling and disgorging solutions, controls and meter calibrations for the whisky industry.
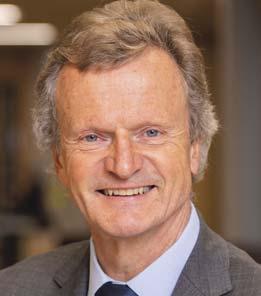
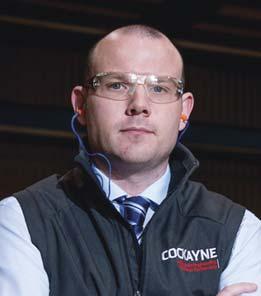
Tooling specialist Cube Precision Engineering has won major orders from prime and tier one aerospace companies.
Cube, which can handle from single op prototype tooling up to complex multi-stage tooling suites, has picked up more than £675,000 of orders over the last two months despite the industry suffering from the effects of the pandemic.
The firm’s ability to deliver quality products on time was instrumental in securing the work and its engineers are now offering additional support in improving the process and manufacturing methodology.
This has helped it bring all but two of its 42-strong workforce back from furlough, with a number of new opportunities across automotive and advanced engineering in the pipeline.
Neil Clifton, Managing Director at Cube Precision Engineering, commented: “2020 had got off to a great start and we were all set for a record year, until Covid-19 took hold and a lot of projects were stalled or put on hold indefinitely.
“Like all of manufacturing, we’ve had to pivot our operations, but importantly we have managed to continue working throughout the pandemic, including making parts that went into a machine that was being used to make face masks.”
He continued: “We have also been looking at how we convert new opportunities during the crisis and this has resulted in us securing additional aerospace work with two strategically vital customers.
“This is more than double the revenue we were expecting and
Aerospace tooling orders
came about thanks to the way we engage with our customers, working with them to deliver the best manufacturing solution, rather than build to print. The experience of Kevin Davis, our Aerospace Account Manager, has been vital in this process.”
Employing 42 people, Cube Precision Engineering can handle tooling of all sizes, boasting a lifting capacity to 35 tonnes and pressing capacity of 1000 tonnes.
The company provides prototyping, design, simulation, manufacturing and full inspection, giving high profile customers across the aerospace, automotive, defence and rail a single-source solution for its complex tooling requirements.
It has recently invested £300,000 on an MTE BF3200, a new state-of-the-art multi-axis CNC milling centre that will support development/low to medium work for a host of UK and international clients.
Neil concluded: “Our tooling produces parts that go into some of the world’s most efficient jetpowered aeroplanes, luxury vehicles, off highway trucks and, in some cases, decorative furniture for superyachts.” 8 cubeprecision.com
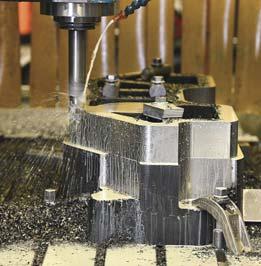
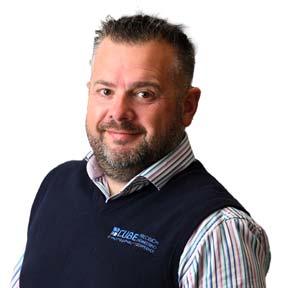
DNow Accredited to
FM10101
Manufacturers of High Quality Mill-Turned Parts
The Nasmyth Group has won a multi-million pound contract Engine supply chain order
from Incora to manufacture
machined components for new Pinxton, Nottinghamshire and CAD/CAM technology to interface and aftermarket aerospace Nasmyth Group’s manufacturing with customer design teams. engine components across a team in Asia. Nasmyth says that excellence in range of platforms and including Nasmyth Bulwell specialises in engineering and technology up to legacy engines. the manufacture of solid machined 5-axis machining has positioned
The seven-year contract will be solutions including precision parts, Nasmyth Bulwell at the forefront carried out by the Nasmyth Bulwell kits, airframe assemblies and of precision machining, producing team at its manufacturing facility in sub-assemblies using the latest quality assured components in steel, aluminium, Nimonics and
SPECIALIST MANUFACTURERS OF super alloys. Nasmyth Bulwell serves its global customers by
ENGINEERED PLASTIC COMPONENTS combining UK manufacturing and • Latest technology one-hit machining a supply chain in Asia. This offering provides options in terms • Standard plastics of cost, quality, delivery, risk • Engineering plastics mitigation and relationship. • High performance plastics Incora, formerly Wesco Aircraft and Pattonair, is a leading • Complex components provider of supply chain • Assemblies management services to the • Flexible batch sizes global aerospace and other industries. Incora incorporates • High volume capability itself into customers' businesses, managing all aspects of supply chain from procurement and inventory management to logistics and on-site customer services. Eddie Jones, Director of Nasmyth Bulwell, commented: “This contract builds on our existing partnership with the Incora team. We look forward to strengthening that partnership as we work together on this new contract.”
Automotive Marine Medical Industrial Retail Utilities ConstructionConsumer Andrew Jones, Chief
Tel: 01920 830 018 Fax: 01920 830 028 sales@plasticturnedparts.co.uk Procurement Officer of Incora added: “This contract solidifies our longstanding relationship with the www.plasticturnedparts.co.uk Nasmyth Group and we look Plastic Turned Parts Ltd. forward to continuing to grow our Unit 2-5 Whitehall Farm, Walkern Road Watton at Stone, Nr Hertford Plastic Turned Parts partnership to provide best in class Hertfordshire SG14 3RP solutions to Incora’s customers.” 8 nasmythgroup.com
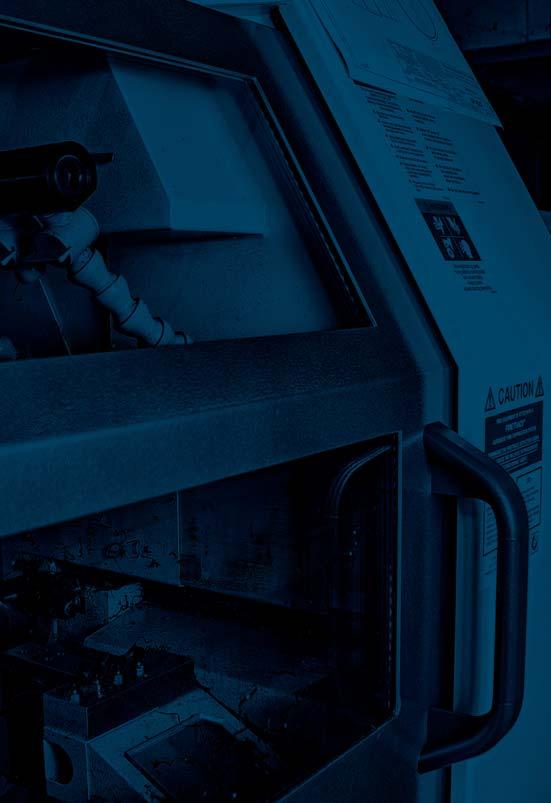
Production control software has played a crucial role in the success of a subcontracting business over the past 21 years by managing requirements for its aerospace customers.
Automatic Industrial Machines Ltd (AIM) started utilising PSL Datatrack production control software back in 1999. The company could not have envisaged then that the system would still be playing a crucial role within the business some 21 years later. The ongoing enhancements to the system keep it up-to-date, maintaining the customer’s investment and providing stable business management. It continues to provide all necessary controls for AIM's complex production needs, especially for customers in the aerospace industry. AIM’s aerospace capabilities include one-off jobs, small to medium batch work, long-term customer contracts and the manufacture of complex sub-assemblies.
With its ability to manage the entire production process, from the generation of quotations right through to final invoices, PSL Datatrack has given AIM greater control over all aspects of its business. Live status updates, the provision of management information including full breakdown of machining costs and reporting on individual customer turnover means the company can continuously assess the strengths and potential weaknesses of its business model.
Working in the aerospace sector (the company has ISO 9001
Their AIM is true
and AS 9100 accreditations alongside various customer approvals) means traceability is paramount. The production control software that deals with customer orders and production processes must therefore be watertight. PSL Datatrack stores all historic transactions relating to the production of any component for any customer. This includes full traceability of all materials and subcontract services, indepth route cards, inspection reports and the generation of Certificates of Conformity (COCs).
Information is readily available for any client or external audit and AIM has received praise from a number of customers for the system it has in place. “We've been told we set the traceability standard for some of our customers' other suppliers. That is great news not only for us, but also for PSL Datatrack in the way that they have helped us achieve this recognition," say Managing Director Rob Kendall.
AIM's ability to quickly quote and process a large number of orders has been central to the company's success which has seen steady growth since establishment in 1972. PSL Datatrack enabled it to achieve this alongside handling calculation of all costs from suppliers, including materials and external processes such as anodising.
Material costs are automatically tracked and updated, if necessary, for future quotation and purchasing purposes. AIM has seen the number of live part numbers it deals with rise from around 120 to 900 and has evolved towards producing smaller batches. With more part numbers and the requirement to produce components in aluminium, carbon fibre, steels and titanium, the need for well-maintained production control software with ongoing development to provide new features is critical. 8 psldatatrack.com
aim-ltd.net
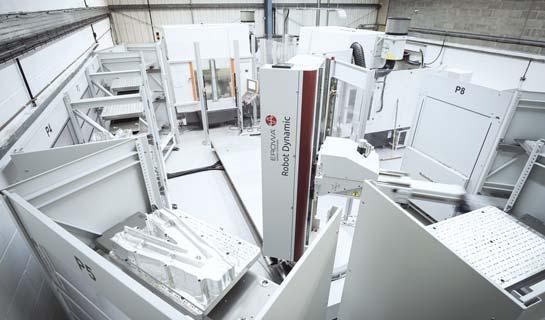
Strategy and growth rewarded
Electronics design and manufacture specialist Jaltek systems has picked up a Make UK Business Growth and Strategy regional award.
Luton based Jaltek won the award in the regional heats of Make UK’s national manufacturing awards programme.
The awards, which recognise excellence among manufacturing companies in seven categories, as well as five Apprentice categories, were held virtually at an online ceremony for the Midlands and East of England.
Jaltek, has designed and manufactured electronic systems across a wide variety of sectors, including aerospace, energy, medical and security, for over 30 years.
Judges of the Business Growth and Strategy category said that they were “impressed with the clarity of the company’s primary growth strategy; offering a service to small disruptive businesses. The financial outcomes were impressive and they showed positive collaboration with Universities.”
Steve Pittom, Jaltek’s Managing Director commented on the win saying; “We feel honoured and thrilled to have won in this highly competitive category. It is a whole team effort that has led us here and I couldn’t be more proud of everyone. Not only the Jaltek team but also our customers and suppliers. Jaltek has evolved and grown significantly in recent years.
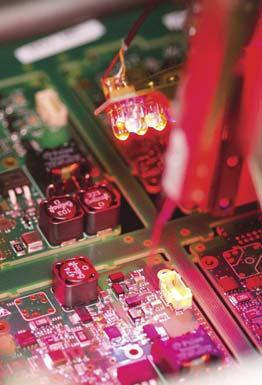
PRECISION ENGINEERING
www.thomas-brown-engineering.co.uk
Tel: 01484 548903
Aerospace Oil & Gas Nuclear Defence Automotive Electronics Hi Fi Industrial & High Volume Machining As part of this we have transferred some of the skills and expertise employed in serving the needs of our larger customers to support smaller enterprises. The team has relished the opportunity to work with new disruptive technologies and partner with high- potential start-ups. The culture within our business is collaborative, enabling and always open to meeting new challenges and I’m excited to see what we do next.”
Charlotte Horobin, Midlands Region Director for Make UK, said: “These awards are a testament to the dynamic companies and individuals working within engineering and manufacturing. The sector has been at the heart of delivering during the crisis and as we rebuild our economy there will be a bright future for companies and individuals that make the most of their talent.”
As a regional winner in their category Jaltek will go forward to attend online national judging in early December with results being announced in January 2021.
Jaltek Systems is a leading AS9100 and ISO 13485 accredited UK contract electronics manufacturer focusing on low to medium volume, high mix product profiles for a range of industries.
Its services include conceptual design, PCBA layout, fast turnaround NPI, manufacture and test of PCBA’s and final product assembly. Using advanced systems Jaltek supports products throughout their lifecycle, offering a single service or complete solution. 8 jaltek.com
MetLase has engineered and manufactured a customised gas shield that will cut welding rework at a major aerospace engine manufacturer.
The Sheffield-based company took just two months from the customer’s initial enquiry to design and manufacture the shield for controlling argon delivery within shielded welding. This prevents oxygen or water vapour affecting the quality of the weld.
Using precision laser cutting technology and patented joining methodology, the Rotherhambased company identified an engineering grade metallic foam that dissipates the argon gas in a precision manner, providing an almost perfect inert atmosphere for the process.
It also developed a digital enhancement, which has the ability to provide constant information and alerts prior to the welding taking place.
“This was a significant challenge for our team, but one we relished as it also gave us the opportunity to ‘prove-out’ some new joining techniques we had developed, whilst integrating digital technologies into the mix that deliver a game-changing solution to the welding process,” explained Jon Ham, MetLase’s lead engineer on the project.
“The aerospace industry has stringent quality standards to meet and we had to find an answer that would produce welding performance better than 10 parts per million and could be used across numerous civil engine variants.”
Shielding cuts rework
He continued: “Innovation and pushing the boundaries of engineering is what we do best and I’m delighted to report that our gas shield provides a significant reduction in welding rework, which saves considerable time and cost.”
MetLase, which is a joint venture between Unipart and Rolls-Royce, is now looking at ways where it can customise the solution for other aerospace customers, with the firm’s standardised manufacturing process meaning it could take just two weeks to provide a bespoke ‘shield solution’.
The introduction of sensors in the system is another example of how the company is keen to embed digital technology into more mainstream manufacturing techniques to deliver digestible and, importantly, actionable data.
One example is the ability to understand how equipment is performing by continually measuring properties and monitoring sensor outputs so earlier positive interventions can be made.
Richard Gould, Business Development Manager at MetLase, commented: “Our digital products, which currently include Digital Gauge, Smart Bench and Smart Cell, have to deliver bottom-line benefits to our clients, who operate in the automotive, aerospace, construction and renewables sectors.
“This involves taking traditional manufacturing principles focusing on assembly, bonding, measuring, workholding and assembly workstations, and exploring how we could digitise them in a way that would allow them to provide their core function whilst also gathering data.
“For us, digital manufacturing is not a standalone entity. Instead, it should be a critical aspect of the process and operation, and it should revolve around data and, specifically, digestible, actionable data.” 8 metlase.com
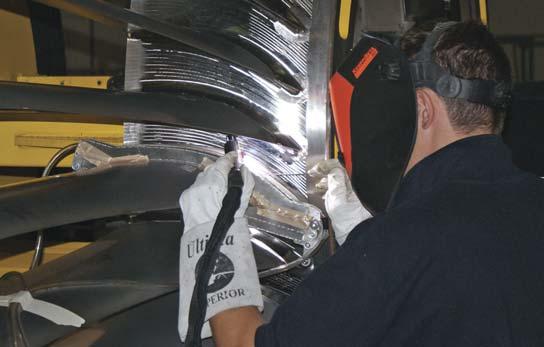
Tube manipulation and pipe bending subcontractor T&T Tubecraft has increased capacity with the installation installed of a new Unison all-electric 130 mm diameter multi-stack CNC tube bending machine.
This is the third Unison tube bender to be purchased by T&T Tubecraft since 2014. It joins a 50 mm Unison Breeze machine and a 100 mm Unison Breeze multi-stack model that are in daily use at T&T Tubecraft’s Woking-based facility.
“Of all our tube benders, our 100 mm Unison machine is easily the busiest,” comments T&T Tubecraft managing director, Ross Turner. “Ironically, when we purchased the 100 mm Unison machine back in 2015, we didn’t have a vast amount of work for it. This quickly changed, however, as we gained the ability to take on new projects. The new 130 mm machine will increase our capability even further, both in terms of capacity and the ability to tender for an even greater range of projects. We expect it to be of particular interest to customers in the aerospace sector.”
The 130 mm tube bender is particularly suited to bending exotic alloys such as titanium and Inconel, as well as super-duplex stainless steels. Able to push bend tubes of up to 6.2 metres in length when in standard mode, it also features a hitch-feed facility, whereby the machine carriage retracts by the length of the next feed, enabling mandrel bending of tubes of up to 8.7 metres long. As a result of this capability, T&T Tubecraft believes that, out of all
Bigger bending capacity
UK tube manipulation subcontractors, it may provide the longest bending range.
Multi-stack tool holding allows the most complex of parts to be formed in one uninterrupted manufacturing cycle, while
Unison’s bar code scanning system ensures that only the correct tools are installed while also configuring the machine automatically. The standard-fit rise and fall pressure die means that tools of very different radii can be used on a part within a cycle.
The power of the machine allows high quality thin wall bending, even on high yieldstrength alloys such as Inconel.
The 130 mm machine has been networked to T&T Tubecraft’s CAD facilities and a coordinate measuring machine (CMM) for verifying bend accuracy and design conformity. The tube bender can be programmed manually or from CAD data using industry-standard IGES or STEP files, while data obtained by the CMM from the first manufactured part can be used to make automatic adjustments to the machine prior to commencing a manufacturing cycle.
“The all-electric architecture and automated Unibend softwarecontrolled setup of our Unison machines offers major advantages over hydraulic machines,” continues Ross Turner. "Bending accuracy and repeatability are dramatically improved. We achieve right-firsttime manufacturing for repeat subcontract work and typically expect even the first bent trial component at the start of a project to be very close to what we are looking to achieve. Machine configuration is also rapid, typically only taking 15 to 20 minutes. As a subcontract tube manipulation company, we also quickly get to hear how well new machines are viewed by our teams. Unison machines are very well received by our workforce. Unison’s Unibend operating software is exceptionally intuitive, meaning much faster programming and accelerated training for new staff members. Our operators consider the Unibend control system to be exceptionally user friendly.” 8 tubecraft.co.uk

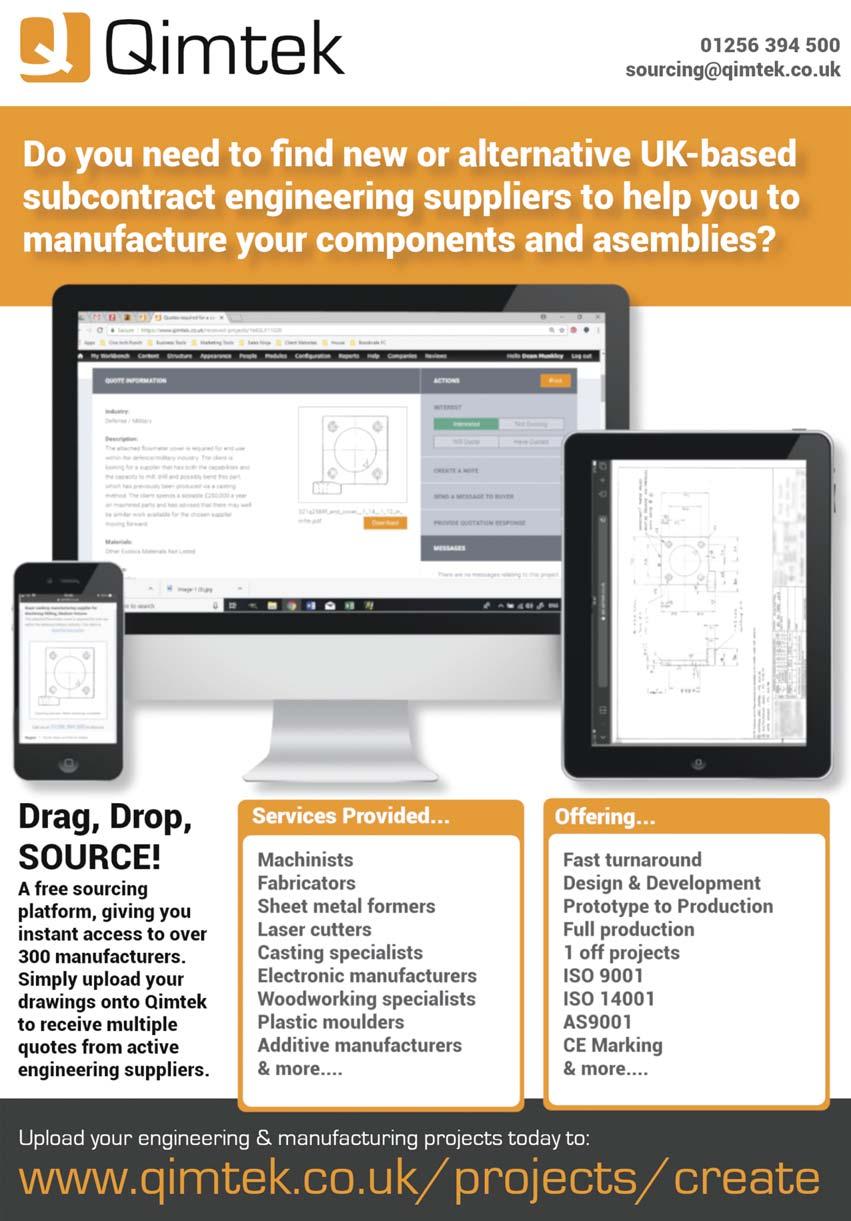
Investment in automated material handling and storage at Alpha Manufacturing has removed work in progress from the factory floor and boosted capacity and efficiency.
The company has expanded its four-bay automated material handling and storage system to a 10-bay system that houses more than 600 tonnes of material and part-processed items.
The STOPA system now has 207 available pallet spaces and runs 62m down the centre of Alpha’s factory near Stafford and serves machines including Trumpf laser cutting, punching, combination laser/punch and bending machines.
The completion of the STOPA marks the culmination of Alpha’s journey to automation and its ‘smart factory’ vision, delivering competitive advantage for both the company and its customers.
Plans for the large-scale installation were first set out in 2015. The aim was to make Alpha Manufacturing the UK’s foremost precision sheet-metal fabricator in just five years, doubling turnover in the process. With the completion of the STOPA system extension in July 2020, the total investment is close to £4 million, securing Alpha’s position as one of the most technically advanced factories in the industry.
Part of the Bri-Stor Group of companies, Alpha Manufacturing is a privately-owned business established in 1989 that specialises in sheet-metal fabrication. Over 150 people are now employed at the firm’s
Alpha’s automation advantage
65,000ft2 facility, where a range of materials are processed in thicknesses from 0.5 to 25mm. Sectors served include automotive, retail, electronics, agriculture, construction, street furniture, security, healthcare, horticulture and petrochemical.
The STOPA system improves daily business at Alpha in a number of ways. For instance, it has allowed the company to automate stock storage, movement and transfer between machines, with all raw sheet metal stored in the towers and called out at the touch of a button. This capability has had a hugely positive affect on Alpha’s performance with regard to both efficiency and capacity.
“One of the biggest benefits is removing all WIP (work-inprogress) from the shop floor,” states Rob Eley, Commercial Director. “There are no more pallets of parts, or need to transport those pallets around the factory using forklifts. The STOPA has led to massive improvements in efficiency, as well as reductions in costed manpower resources. Furthermore, tasks such as stock control and management are now significantly easier.”
Managing Director Paul Clews adds: “We’ve achieved everything we set out to do and more, and this final investment will take us to our goal in terms of automation and efficiency. We’re not unique in buying the best machinery; a lot of companies have high-specification technology. However, we aim to differentiate in our operations, through the highest levels of efficiency and productivity. The STOPA system provides the ability to identify, locate and deliver any piece of sheet steel, punched/laser part or folded subassembly to any location at the touch of a button. In doing this, we dramatically reduce the amount of waste from our processes in terms of people movement and component transportation.” 8 alphamanufacturing.co.uk
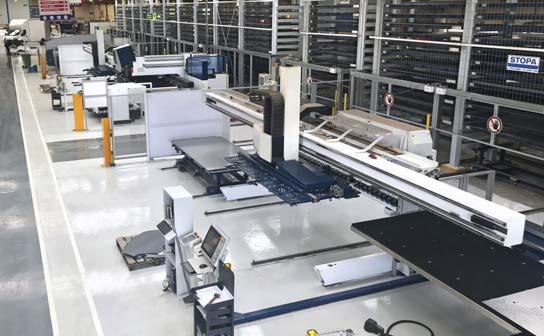
Samuel Taylor Limited (STL) has been selected alongside three other leading low carbon technology innovators to participate in the UK pavilion at The Electric & Hybrid Vehicle Technology Expo at the Messe Stuttgart, Germany in May 2021.
The pavilion is managed by the Advanced Propulsion Centre (APC), in partnership with Department for Business, Energy & Industrial Strategy, Department for International Trade, SMMT and Innovate UK.
STL’s involvement follows the announcement in early 2020 by the Redditch-based metal contact and precision stamping specialists of a significant contract win to support vehicle electrification, a first in what represents an area of significant potential growth for the company.
The Electric & Hybrid Vehicle Technology Expo is run alongside The Battery Show Europe, creating Europe’s largest H/EV and advanced battery technology trade fair. Attended by more than 400 international suppliers, the event is a leading meeting place for powertrain technology.
STL manufactures precision stamped components and assemblies, specialising in the sophisticated bonding of bimetals within the development of battery busbar technology for electric vehicles.
Electric vehicles and hybrid electric vehicles rely on robust electric motor drives, largecapacity battery packs, power inverters, and efficient distribution of power from charging source to
Low carbon innovator

battery and then throughout the vehicle. Busbars, which comprise a system of electrical conductors for collecting and distributing current, provide the means to efficiently distribute power to the cells themselves and onto the vehicles’ various subsystems.
STL said: “ We will be proudly flying the flag for UK industry at The Electric & Hybrid Vehicle Technology Expo. This is an exciting opportunity to demonstrate our ground-breaking technologies to international investors and prospective customers.”
STL will join Autocraft Solutions Group, Eatron Technologies and TWI Ltd on the pavilion representing British industry and showcasing their latest innovations.
Jo Evans, Strategy & Performance Director at the Advanced Propulsion Centre, said: “Our International Events Programme is helping the next generation of low carbon innovators gain a foothold on the global stage, showcasing the latest product developments. This complements our funding programmes, increasing awareness of emerging technologies and how they are the heart of the UK’s green revolution. We look forward to Samuel Taylor Limited joining us on the UK Pavilion at The Electric & Hybrid Vehicle Technology Expo”. 8 samueltaylor.co.uk
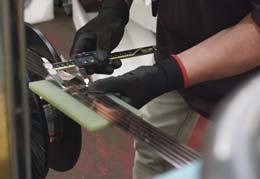
From design, sampling and technical support to manufacture, Simpson Springs & Pressings Ltd provide the complete service.

Tel: 0118 978 6573 Email: sales@simpsonsprings.co.uk
ASCO can now offer a wider range of machining, coating and repair services following the installation of robot-based laser metal deposition and hard-facing system from CNC Robotics.
Based in Skelmersdale, Lancashire, and with a second site in Dubai, ASCO offers a comprehensive service incorporating CNC precision machining, fabrication, surface coating, diamond grinding and superfinishing repair technologies. As well as having an extensive machine shop equipped with CNC lathes and machining centres, the site includes specialist coating equipment, including unique systems specifically designed for the company’s processes. All manufacturing at the company is supported by an in house metallurgical laboratory for testing coatings to international standards and CNC co-ordinate measuring machines for dimensional inspection, ensuring that precision components can be certified to be within microns.
Laser-metal deposition and hard-facing cladding allows coatings such as tungsten carbide, Stellite and Inconel to be deposited with a significantly lower and more localised heataffected zone (HAZ), even with materials that are difficult to weld. This means that the process has minimal impact on the mechanical properties of the substrate material and reduced potential for distortion and damage to the chemistry and structure of the base core
Robot laser metal deposition
material. In addition, the small melt pool that is formed enables the processing of very complex geometries in a single set-up, when depositing protective surfaces, undertaking repairs or creating near-net shapes.
The ability to work with very complex shapes is supported by the flexibility of the robot cell. The robot offers six-axis movement, while specially designed work holding adds a further three axes, giving the potential for nine-axis operation. In addition, a novel head can be fitted to allow the internal cladding of bores up to 2 metres in length and down to 55 mm bore size.
The main challenge for the system resulted from the variety and complexity of the shapes being processed at ASCO Engineering since the laser has to be as near as possible to 90° to the surface of the part. This was overcome with a KUKA robot that includes very few restrictions on its range of movements.
While the new system has been used predominately for adding coatings to new parts, it has also proved valuable in component repair. For these projects, repair material is typically laid down in layers of up to 1mm per pass and then ground back to give the final surface. Dependant on clients’ requirements ASCO is, in reality, able to clad to any thickness.
The main benefit of the new

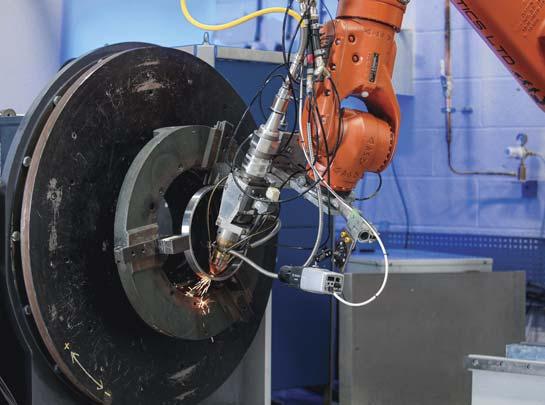
system is the consistency of the results. Many of the coating materials used at ASCO Engineering are very expensive blends that are needed to give the necessary corrosion resistance and wear resistance. Many of the parts made by the company are used in demanding applications in the oil and gas and power generation, mining and aircraft industries where any failures can lead to costly losses in production.
Andy Deegan, Chairman at ASCO believes that the system has made their company more versatile than any equivalent supplier in Europe, creating the ultimate one-stop-shop.
He says: “The robot system is at its best when we are working with batches of parts. We can process the first part, confirm that it is dimensionally accurate and carry out full laboratory checks on the surface integrity. Once we know we have set the correct parameters for the first part, we can rely on the repeatability of the robot to ensure that the rest of the batch will be equally good.
“The repeatability also helps us to ensure on-time delivery. After the first part has been completed, the time the robot will take to repeat any task is very predictable, which makes scheduling easy. If we can guarantee high quality and offer on-time delivery, clients won’t have any need to go elsewhere.” 8 ascoeng.com
Wealdpark Limited
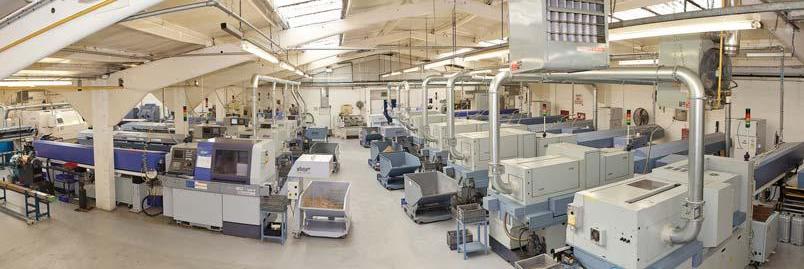

Stand number 5126
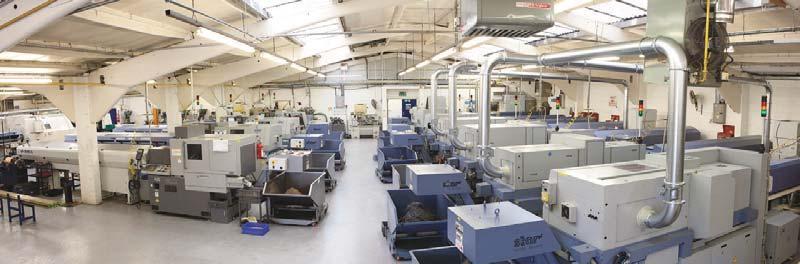
Subcontract Capacity
BS EN ISO 9001:2008. Approved by BSI since 1991.
Company Contact Details
Phil Smith, Director, Wealdpark Limited Sutton Road, St. Helens, Merseyside, WA9 3DJ Tel. 01744 22567 / 732083 Fax. 01744 451339 E: sales@wealdpark.co.uk www.wealdpark.co.uk
A better way to clean parts
Innovation is often driven by regulatory change. Take a commonplace but key process in workshops, factories and manufacturing plants industrial parts cleaning. Mainly to protect the environment, traditional cleaning solvents such as trichlorethane and other hydrocarbons are being phased out. This often creates a big problem for production management.
In contrast, entrepreneur Tom Sands regards new legislation as an opportunity. With a background in chemicals engineering and related product development, he has not only devised a brand new, environmentally-friendly and market leading parts cleaning fluid, but also created a thriving business to develop the market, Safe Solvents (SSEL).
What’s more, based on the technological advance, he and his team designed a machine to make best use of it, as a result patenting a novel process, Ambimization®. It effectively separates all waste particulates and oils, facilitating proper disposal. The innovation means SSEL is enabling customers to achieve greater efficiency, higher productivity and increased throughput from an often overlooked but vital industrial process.
But Sands also faced a problem - the core business of his company is devising, managing and exploiting intellectual property (IP), not designing machines and manufacturing. At first SSEL contracted out production to a small engineering company but as sales and the product range grew, it became clear a larger contractor had to be found, with comprehensive resources to support planned business expansion.
A complete solution from ICEE
To develop his company, in 2018 Sands brought in Aspremont, a venture builder that enables founders of innovative IP companies to achieve their full potential. To work with SSEL’s team, the venture builder seconded a professional with a well proven track record in creating and executing successful go-to-market strategies for early-stage enterprises, Ben Reid.
Reid explains: “We take a business from start-up to scaleup. When it’s a start-up, everything revolves around the founder. Working with the first contractor was absolutely fine when Tom could be involved in
Safe Solvents’ cleaning systems in use at Carwood Motor Units, a remanufacturer of diesel fuel injection, electrical, and turbocharger systems for all types of vehicles

everything. He knew how it was designed, built and what parts went into it. He could resolve any issues that arose. But when Tom and I discussed moving to a scaling strategy, it was very obvious that – to support big expansion ambitions and higher volumes - going forward we had to look at new resources.”
ICEE Managed Services was selected because it has years of successful experience designing, making, fitting out, installing and maintaining its own core product range – robust and high quality, bespoke sheet metal electrical equipment enclosures for the telecommunications and transport sectors, plus solutions for other industries.
The manufacturer also possesses strong industry accreditations and quality control
procedures, all complemented by experienced project management and modern, leanbased manufacturing and administration systems. This was vital for SSEL as customers include Formula 1 and major manufacturers in the automotive industry supply chain. Whether the order is one machine or many, delivery deadlines cannot be missed.
But ICEE soon proved to be more than simply a passive contractor. SSEL regards it as a highly valued innovation and technical production partner, actively collaborating and contributing to product and process improvements.
A vital partner for innovation
First, ICEE converted the customer’s existing drawings into its Solidworks 3D CAD system. Each product was valueengineered, refining design for manufacture and perfecting quality and reliability. In effect, this work produced a second generation of machines, embodying all the feedback and field experience SSEL had gained over several years, coupled to ICEE’s knowledge of supplying complete solutions.
Sands explains: “The rigorous nature of doing that forced us to look hard at the design, components and functionality. ICEE were incredibly helpful. I hadn’t really thought of them as a specific prototype shop, but there’s no doubt they have an inherent skill set [in that area], enabling our processes to be incredibly iterative and productive.” He says they fed their ideas and experience into the process, not just from a theoretical but also a practical, shopfloor perspective. “They have been integral at finessing the final versions of each of those machines. I suppose we hadn’t really thought of them as being a technical partner, but that’s what they are really.”
He points to a design example, a mechanism on an ultrasonic SSEL machine. Actuators lift a workpiece support platform locked inside the cleaning fluid tank. Because of the way it was originally designed and the weight it carries, it was not smooth in operation. ICEE solved the problem with a ball-bearing mechanism and replaced a flat steel plate with an aluminium version, which reduces weight that has to be lifted.
Ben Reid highlights an important business detail: “Other key benefits include reduction of production time, from eight weeks to a target of four weeks, so that’s quite significant. That’s because we are not assembling, yet thanks to the level of transparency offered [by ICEE] there’s much more timely sight of their production and delivery progress.”
Tom Sands sums up: “From
Part of a range of high performance cleaning machines, the Safe Solvents Typhoon 450, made for the company by manufacturing contractor ICEE, is available in three options and replaces traditional sink-on-drum, manual cleaning machines
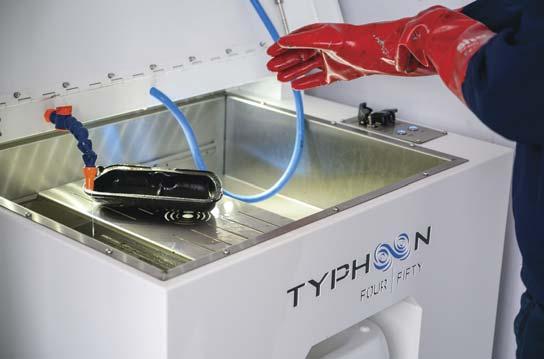
my side - the coalface on design and development - I’m seeing ICEE as an innovation partner, so when we go in there and I say this is what I want to achieve, this is what we’ve got so far, they have helped us get to a perfect product quicker than before. There is no doubt about that. In short, they are as much an innovation partner as simply a manufacturing and assembly company.”
8 For more information
please contact: ICEE Managed Services Ltd. 20 Arnside Road, Waterlooville Hampshire PO7 7UP Telephone: 02392 230 604. Email: sales@icee.co.uk Web: www.icee.co.uk
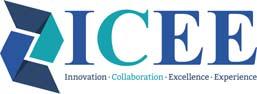
Welshpool based foundry Castalum is using metal additive manufacturing technology to produced advanced die-casting moulds.
CastAlum is an aluminium foundry using high pressure die casting and squeeze casting to supply a range of engineered components for the automotive sector, with 90% of all production being for export.
Investment in new technology and a greater understanding of additive manufacturing (AM) technology, through a 9-year programme of research and development, means that CastAlum is now the first company based in Wales, outside of a university, to independently run a powder bed selective laser melting, SLM, machine.
Back in 2000, the site was a greenfield development, with only one customer. The company now offers cast and machined, or fully assembled and tested parts as required by the customer. Indeed, over 20 years the company has built up to a diverse customer portfolio, supplying castings to the automotive industry. The company now has 10 high pressure casting cells ranging from 1100 tonne to 2200 tonne and 3 squeeze casting cells, alongside 14 3-axis machining centres. Components manufactured by the company go into vehicles produced by VAG, FCA, BMW, Ford, Porsche, Mercedes, JLR, AML and other prestigious marques.
By 2014, the company was already an early adopter of AM technology, working closely with an
Additive innovation in die-casting
Italian company developing conformal cooling techniques in tool steel, with promising early results. “With the good came the bad” explains CastAlum AM Engineer, Rhys Jones. “Despite the overall equipment efficiency, the variables in tool life and high part costs where simply unjustifiable in a competitive commercial business - something had to change.”
However, the potential benefits that additive manufacturing could bring to HPDC were too great for CastAlum to simply ignore. Successfully securing a collaborative R&D award with InnovateUK in 2018 allowed the company to accelerate progress with the technology and work to iron out the early issues.
“The parts that we look to produce on the SLM printer aren’t the traditional 3D printed parts that most of us are familiar with, with lightweight lattice structures and
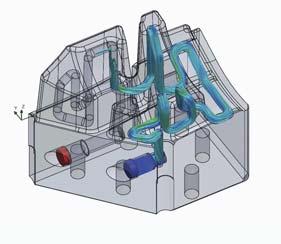

thin walls. The parts that we need are large, dense parts that are capable of withstanding the harsh environment of high pressure die casting,” explains Rhys.
“The SLM process really consists of micro-welding. The machine lays down a thin layer of powder (in our case it’s 40 microns thick) and then the laser superheats the powder, fusing it to the layer below; layer by layer the part is formed. With our large, bulky parts, the more the laser has to melt, the more welding splatter and smoke is generated. This dirties the build chamber over time and can potentially degrade the quality of the part as it is built up this is where we need to work smarter to overcome this issue and maintain part quality,” he explains.
The first step in making a tooling insert on the printer is consider its geometry and determine if it can be built on a SLM printer. Tooling inserts naturally have draft angle for releasing the casting out of the die, this suits the printing process as this means that the geometry is self-supporting and can build without support. The next task is to lay out the cooling channel, and tie this in with the company’s process department and inhouse toolroom, capture their feedback and model it in.
“As all our 3D modelling is caried out in house, this allows us to be very flexible and dynamic when it comes to design changes, we can make the small changes needed to optimize performance” says Rhys. “We use file preparation software from Renishaw to lay out the build and set the build parameters. The printer runs largely independent for the entire build, only needing brief operator intervention to look after the powder. Once we are all happy with the design, we can print it and our builds tend to run from around 80 hours to 120 hours, depending on the part size.”
Once the build has finished, the powder is removed from the part, and it is then taken for final machining. The parts straight off the printer have a rough finish, unsuitable for use in the casting process, so to overcome this the company adds a small machining allowance and a 3-axis XYZ mill to fully finish the parts providing a much better surface finish and ensuring the dimensional accuracy of the parts.
Through the Innovate project, the team at CastAlum worked closely with experts from Coventry University whose role was to develop methods of calculating the amount of cooling needed at each point of the casting, to allow a much more efficient and uniform cooling of the mould and greater optimisation of the process.
Rhys also notes that his team “were very lucky to be able to work with engineers at Renishaw’s solution centre, based up in Stone, where we had access to Renishaw’s considerable AM knowledge. The solution centre allowed us to learn how to use the new technology in the safety of their facility. Through this collaborative team approach, our increased understanding of conformal cooling, combined with the ability to implement and use this knowledge has now enabled the team at CastAlum to change what was thought feasible”, he added.
Key to this was the company’s “Forward Focus” ethos which drives change, as customer needs grow, to meet the new challenges of Electric Vehicle (EV) and Low Carbon Vehicle (LCV) technology.
Rhys is excited about the future. “We now have a wealth of experience and data that we are confident will enable us to support the development of lightweight casting technology without sacrificing properties or durability. We continue to develop additive manufacturing for the foundry industry, developing a number of process solutions to meeting world class quality standards and provide solutions to customers” 8 castalum.com
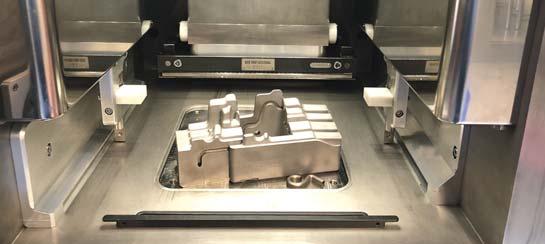
Space bound composites
Pentaxia has been selected by Moog Inc. to design and manufacture complex tooling and subsequent composite components for the Small Launch Orbital Manoeuvring Vehicle (SL-OMV) project.
The SL-OMV is designed to deploy CubeSat constellations and guide small satellites to their final orbit. The first SL-OMV will be supplied by Moog Inc. to Lockheed
engineering, composites

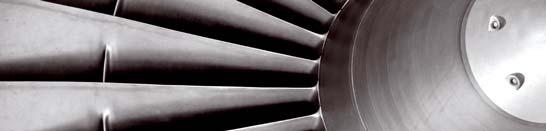
PR | Marketing | | Copywriting | Events Awards | Design | | Web & SEO
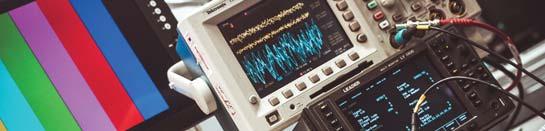
01752 894786 www.aroprandmarketing.co.uk Martin as part of the UK Spaceflight Programme, supported by the UK Space Agency. The lightweight vehicle is a propulsive device to be used on rockets dedicated to the launch of small satellites.
“Pentaxia is delighted to be chosen by Moog Inc. to develop and manufacture critical structures for this exciting Space project. This is Pentaxia’s first major step into the Space sector and the tooling and component requirements are extremely challenging. Nonetheless, it demonstrates our expertise, reputation and “can-do” attitude in the global composite industry. Our team are truly world-class in their respective fields from tooling design and composite material knowledge, right through to manufacturing finished structures. The SL-OMV project is a great opportunity to showcase this expertise and anticipate it to be the first of many future projects working closely with Moog” said Pentaxia’s Sales Director Tim Ollier.
Pentaxia will design and manufacture all tooling and composite activities in-house, offering a turn-key deliverable solution to Moog Inc. 8 pentaxia.com
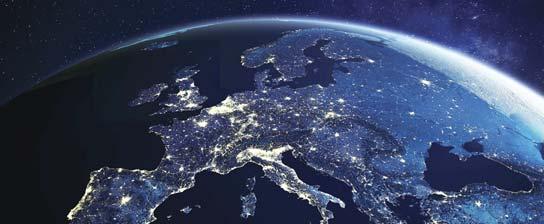