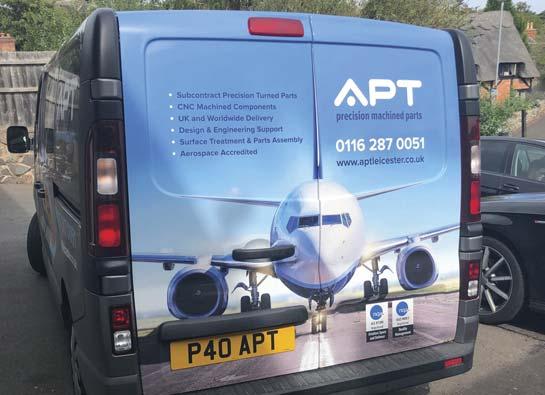
21 minute read
TURNED PARTS
Covid-19 has had a seismic impact on the aerospace industry, with a great reduction in the number of passengers and strict travel restrictions imposed across the world. However, APT Leicester says it is confident of recovery in the aerospace sector and the continuing demand for their high quality parts.
While the negative impacts of the pandemic are undeniable there have been some positive signs of recovery in recent months. The travel restrictions have been eased and there’s been an increase in the numbers of people making international travel bookings. Covid has accelerated a number of pre-existing trends, highlighting the need for continued innovation. APT says it is well placed to respond, as an established supplier of aerospace turned parts.
Having been accredited with the AS9100 standard for 15 years, the APT team have earned an international reputation within the aerospace sector. They are able to guarantee the creation and maintenance of a comprehensive quality system for the provision of safe and reliable products. Customers can also be assured of full traceability and tracking throughout the production process.
No matter the complexity of part design or engineering, APT offers a complete and personal service in line with the specifications set out in AS9100 Rev D. Its engineers work in collaboration during the design and CNC machining process,
Relaunch for aerospace
producing parts that satisfy customer demand. Fulfilling engineering demands across a wide range of sectors, it has a definite advantage over those manufacturers specialising exclusively in aircraft parts. Even if the pandemic has a sustained impact on aircraft production, it will be able to cater to the demands of customers across such sectors as defence and security. "APT saw demand drop for the manufacture of aerospace components for a couple of months as a direct result of the pandemic. However, we are confident that the worst of the storm has been weathered. Committed to the highest standards, we look set to maintain our established relationships with aerospace subcontractors. APT is working at full capacity again, with government guidelines being followed and measures being taken for the assurance of staff and customers," explained Nick Baller, Managing Director of APT Leicester.
Using materials such as titanium, aluminium, acetal plastic and stainless steel, APT can produce high-specification aircraft mill-turned parts with exceptional accuracy and detail. Its engineers use CNC machining for the greatest precision, making for unrivalled functionality, durability and safety. From landing equipment to aircraft seating, there is a selection of APT aircraft components available to view on the APT website.
The company says it is focused on continual improvement and dedicated to the production of high quality parts, making it a trusted leading supplier to the aerospace industry. 8 aptleicester.co.uk
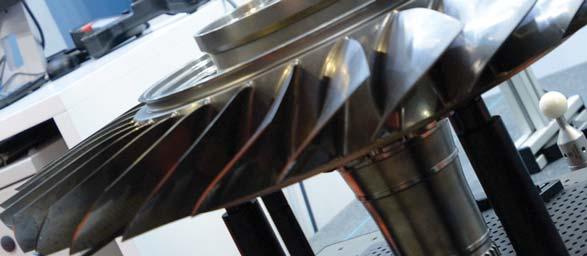
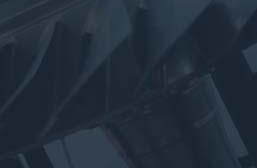
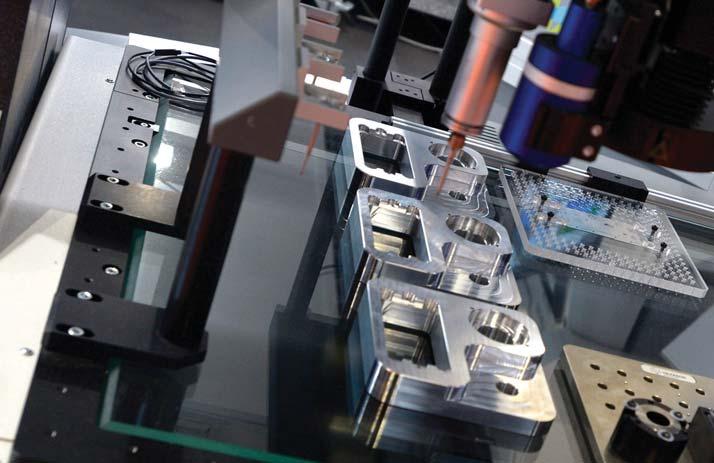
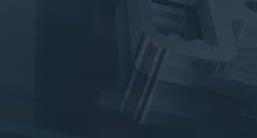
Aluminium turning transformed
Citizen sliding head lathes with guide-bush-free capability and chip breaking software are keeping IML (UK) competitive on aluminium turned parts.
Joint owner Dave Zollo said: "We believe that investment in the very latest technology is the key to quality, reliability and competitiveness."
He and Jerry Way started the business in 2011 and a year later installed its first sliding-head lathe, a Citizen Cincom A32-VII with 32 mm bar capacity. This was followed in 2013 by a 16 mm bar model, a Cincom C16-VI.
The early investments were triggered by an increase in contracts from the medical industry and a desire to be able to manufacture components in one hit, such as endoscope cleaning equipment parts. To cope with an ever increasing level of work, including for the high-end automotive sector which has grown over the past couple of years to become more than 50% of turnover, there are now four different models of sliding-head lathe on site from the same supplier.
The latest two, designated L20XLFV and L32-XLFV, were installed in 2018 and 2020. Unlike the first two Cincoms, they offer the flexibility to allow removal of the guide bush, as well as having the notable benefit of low frequency vibration (LFV) software built into the operating system of the control. Mr Zollo noted that the more modern machines are also more userfriendly, allow better access and are quicker and easier to set.
He explained, "These advanced, twin-spindle, sliding-head lathes are helping to keep us competitive on the world stage, as is automation throughout the factory. "All of our lathes including four fixed-head models are bar-fed and work 24/7, with the sliders able to accommodate a wide range of batch sizes from typically 50- to 30,000-off. Dimensional tolerances of less than ± 10 microns may be easily held. "Even smaller quantities are economical to produce, partly because we have adopted a policy of standardising on one size of stock on each of the Cincoms, so we do not have to waste time changing over bar sets. "We have also invested in automation on the milling side of our business, which accounts for more than half of turnover. Our four vertical machining centres are equipped with robotic loading and remote monitoring, while two horizontal machining centres on the shop floor have a twin automatic pallet changer to minimise idle times. "It all helps to keep costs down and allows us to quote our customers prices that are very similar to those we were charging two decades ago."
Aluminium bar, which accounts for a significant proportion of throughput of turn-milled parts, is the villain of the piece as regards sliding-head turning in the Weymouth factory. The material is often of variable quality in terms of straightness and diameter variation, so can jam in the guide bush of sliders and requires frequent supervision by the operator to adjust the collet.
The ability to remove the guide bush on the L20 and L32 in less than half an hour allows the subcontractor to turn aluminium bar into shorter components in fixed-head mode without

problems. It also has the advantage of reducing the remnant length from typically 275 mm to 100 mm. Completion of one recent IML (UK) contract consumed 300 bars, so it is clear that a lot of material and money can be saved.
When turning difficult to chip materials, Citizen’s LFV software, which is part of the control's operating system, breaks swarf into manageable chip sizes, whereas normally it would be stringy and entangle itself around the tool and component. This capability to manage the size of swarf is in addition to any chip breaking features that may be ground into an indexable insert. Mr Zollo singles out aluminium as well as stainless steel bar to be particularly problematic in terms of bird's nesting.
LFV oscillation lifts the tool tip clear of the component surface by tens of microns for ultra-brief periods to allow coolant to penetrate the cut more efficiently. It reduces heat and prolongs cutter life, while at the same time enabling depth of cut to be increased, even when processing tough materials. It often eliminates the need for a roughing pass and significantly shortens cycle times. Mr Zollo advised that it is of major benefit during attended day and night shifts and especially so during the weekend when staff are not present. 8 imluk.com
Wealdpark Limited
Stand number 5126
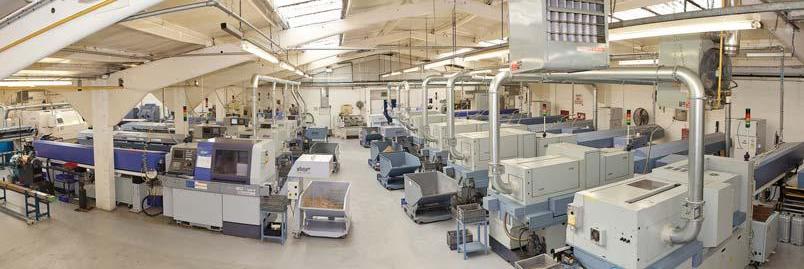
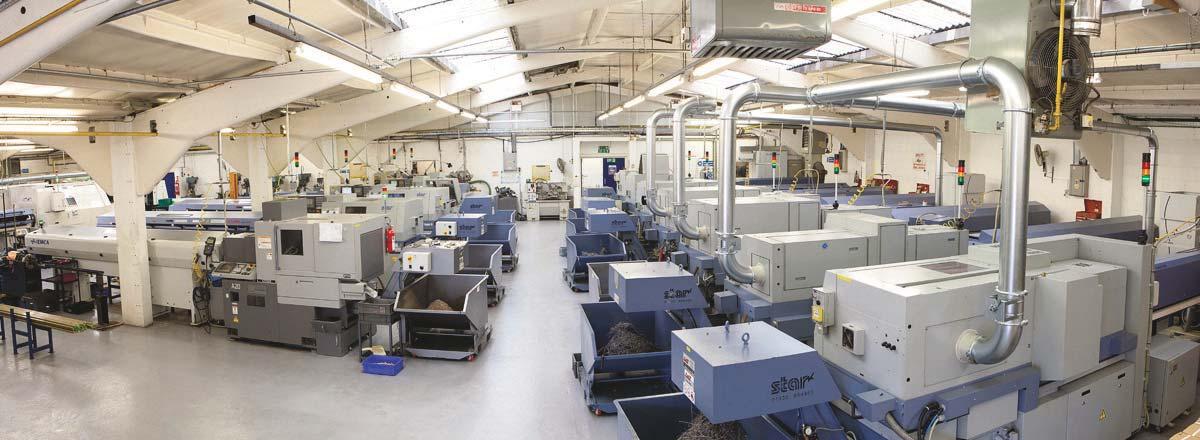

Subcontract Capacity
BS EN ISO 9001:2008. Approved by BSI since 1991.
Company Contact Details
Phil Smith, Director, Wealdpark Limited Sutton Road, St. Helens, Merseyside, WA9 3DJ Tel. 01744 22567 / 732083 Fax. 01744 451339 E: sales@wealdpark.co.uk www.wealdpark.co.uk
The quality team at DKW Engineering is using Bowers Group pistol grip bore gauges to ensure the quality of its machined components in the face of soaring demand.
As a subcontractor, DKW Engineering receives a constant influx of new jobs in addition to its more regular work. This means that the team is faced with new inspection challenges daily, depending on the type of work and the diversity of components that they must manufacture.
Traditional plug gauges aren’t always appropriate as there are only limited sizes available, and become costly if new gauges need to be purchased to suit the requirements of a single job.
Instead, DKW Engineering decided to invest in a more flexible and cost-effective measurement solution in the bore gauges from Bowers Group.
Used several times a day, the bore gauges are an integral part of the inspection process. They are also used by operatives on the shop floor to measure parts with particularly tight tolerances during the production process.
Vitalij Cernomorec, Quality Inspector at DKW Engineering said: “We find the Bowers bore gauges much better than your standard plug gauges; they’re far more versatile, flexible for our needs and perfect for subcontractors like ourselves. As subcontractors, the types and size of components vary, so it helps that we’re able to use the bore gauge to check a range of measurements, including series of step bores, all in one go. They’re quick and easy to use on the shop floor for in process checks and we always trust the bore gauges; the accuracy is excellent.”
Based in Portsmouth, DKW Engineering manufactures and supplies quality, high value, and complex machined components for critical industries including automotive, medical, gas and oil, and more. Established in 1969 it has been providing subcontract manufacturing services on a global scale, producing both simple and complex milled/turned parts from a wide range of materials in various batch sizes.
The business prides itself on its team of highly skilled engineers who utilise the latest CNC machines to ensure all manufactured components are produced efficiently and to specification. By continually investing in the latest manufacturing technologies and ongoing training of engineers, DKW Engineering aims for exceptional quality control and professional management, throughout the entire procurement process.
The bore gauges provide an accurate, repeatable, and costeffective measurement solution. They can be used for a variety of sizes of component depending on what’s required on a particular day, instantly meeting the needs of individual customers. The digital pistol grip bore gauges also offer an ergonomic design with a large, clear LCD display, along with IP67 electronics protection and proximity output with built-in Bluetooth, allowing bi-directional communication for flexible data acquisition and storage. 8 dkwengineering.co.uk
Measuring up to quality demands
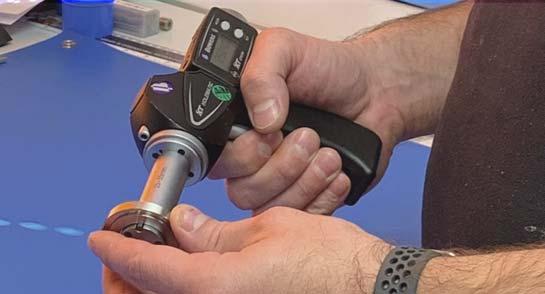
Maintaining quality in upturn
As the effects of the Covid pandemic eased during 2021, certain industry sectors saw a strong upturn in orders as some normality returned, reports quality management provider G&P.
It saw first-hand how for some sectors, the recovery was far stronger than expected and this put huge demands into supply chains that were not prepared for a return to that level of load.
As a result, G&P was approached by a number of manufacturing businesses, initially to audit supplier performance and expedite delivery of conforming stock to support increasing OEM build rates.
However, as build rates rose to normalised volumes, some of G&P’s clients saw a reduction in quality as the supply chain creaked under the pressure.
Meanwhile, consideration also needed to be given to working towards building increased capacity to meet revised demands in the future. The solution from the quality management provider was two-fold.
In the first instance, where possible, G&P pulled orders forward where demand fluctuated below maximum capacity later in the year as a remedy to relieve immediate short-term pressure.
Secondly, G&P’s engineers then analysed the medium to long-term security of supply for the client facilities.
G&P examined hundreds of supply chain businesses by stress testing capacity plans at the OEM’s Tier 1 suppliers, as well as performing deep dives into Tier 2 and 3 dependencies such as subcontract processes or raw material supply.
Where shortfalls in the suppliers’ ability to deliver at rate could be solved with investment, G&P included costs and lead time in our client report.
The solution is that through G&P’s analysis the client can be confident in the supply chain supporting its growth.
Through engaging G&P to perform this service, clients were able to get detailed information from a third-party, at pace, including gap analysis and costs to resolve identified shortfalls.
Clients received a detailed, but macro view of their supply chain, enabling confidence when accepting record orders for their products that their supply chain could support their growth. 8 www.gpgm.com
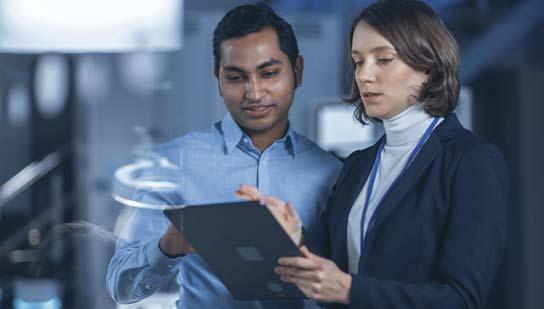
Visit our website or contact us for a quote or advice
Coordinate measuring machines at WLR Precision Engineering give greater inspection flexibility and can be used by production staff as well as quality inspectors.
The two LK Metrology machines have been supplied with LK Launchpad, an icon-driven, touchscreen operator menu, and a network of viewing screens and tablets. The simplified operator menu lists all the available inspection programs and the exact position the part should be placed on the machine table for inspection, giving operators the confidence to perform measurement tasks in just a few clicks.
It enhances flexibility and opens up the system for use by nonspecialist CMM operators. Measured results and automatically generated reports may be shared between screens, tablets and other networked devices for easy access and viewing from any location.
WLR aims to cover the entire production process in its contract manufacturing service, with a proportion of the value of each part lying in rigorous metrology, often involving 100% inspection.
Contracts are received mainly from the oil & gas, pharmaceutical, medical, laboratory and scientific instrumentation industries, which place great reliance on the accuracy and consistency of parts delivered.
The company's sales manager Tom Parr said, "The increasing confidence that our customers have in the accuracy and consistency of components they receive from us has resulted in our winning considerably more business in virtually every sector that we serve."
Installed in 2015 the first LK CMM an AlteraS 15.10.8 quickly transformed quality control activities in the Wilford factory, making it faster, much more efficient and less labour-intensive in respect of both measuring parts and preparing inspection reports. The machine's acquisition was triggered by a steep increase in components ordered by key customers coupled with a requirement for more comprehensive, 100% inspection and detailed reporting. Soon afterwards, a customer in the defence sector had a similar requirement for the provision of traceable measurements and certified reports covering the supply of critical, matched components.
A major benefit of the CMM is its large table area, approximately 1.0 x 1.5 metres, which is able to accept up to twelve identical components at a time for batch inspection, instead of just one as on either of the older CMMs. It is unusual within manufacturing industry to see a measuring machine nested with multiple components in this way, but the subcontractor attests that it is a perfectly feasible way of operation. Typically, five batches can be inspected during a day shift with a load time of about five minutes between each batch.
By May 2021, a further increase in batch measuring capacity was needed. A requirement was also introduced for in-process inspection of a particular family of components for one customer. This time a smaller LK AlteraS 10.10.8 with a working volume of 1,016 x 1,016 x 813 mm was purchased, together with the latest CAMIO 2021 and the additional LK Launchpad software. 8 wlrprecision.co.uk
Quality gives customer confidence
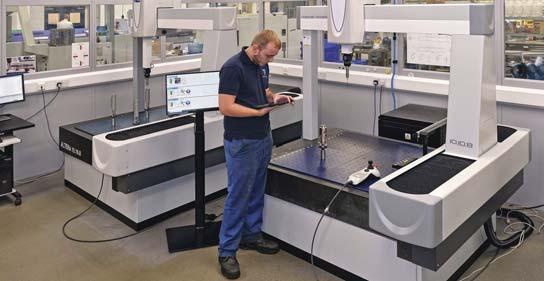
New technology Quins inspection machines at Newbury Electronics are speeding inspection times on difficult PC fabrications and assemblies.
Chris Hobson, Newbury Electronics said: “We have a policy of continuous investment in latest technologies, practices and manufacturing equipment, often driven by our client’s process innovation requests, to make sure we can deliver the best possible product for our customers now and into the future.
“The Quins product line offering by Altus had a great feature set and suitable equipment footprint to deploy into our inspection team versus its price point. Recommendations from other users also reduced the risk and gave us the confidence to invest in the product, with direct support through Altus.
“This has been born out in our initial deployment, where it has exceeded our expectations and has proven to be a great addition to our inspection department, aiding in accelerating inspection flow for boards that have taller devices or through hole components that would normally struggle with other AOI machines specified with SMD / lower profile components in mind.”
Anthony Oh, Technical Applications Manager- Altus added: “Since adding Quins inspection equipment to our product offering we have seen huge interest. The equipment has proven itself to be a safe investment and is increasing the quality of the finished product thanks to its impressive inspection abilities which inspects, captures and records high quality images of every PCBA being produced for traceability purposes.
“Newbury Electronics required an inspection process that allowed clear data capture of larger assemblies. Quins equipment can take away a process that was once only achievable through manual
Speeding inspection flow

processes and increase efficiency and quality assurance.”
Newbury Electronics installed the Quins Pro UV. This innovative machine protects employees from harmful UV radiation when testing the assembly coating. Thanks to its combination of scanners and innovative software, Pro UV delivers high-resolution images and a simple optical test environment. 8 newburyelectronics.co.uk
PRECISION ENGINEERING
Aerospace Oil & Gas Nuclear Defence
www.thomas-brown-engineering.co.uk
Tel: 01484 548903
Automotive Electronics Hi Fi Industrial & High Volume Machining
John Pearce, CEO of Made in Britain, explains how British engineering companies are shaping the post-Brexit, post-pandemic economy
In May, UK manufacturing growth hit a 30-year high, as the relaxing of lockdown measures unleashed pent-up demand. This was music to the ears of everyone who cares about the strength of the sector and the renewed focus on exactly where goods come from and how safe they are. This had to be a sign that the worst economic effects of the pandemic were drawing to a close, and that making goods in this country and expanding our overall capacity was happening, or at least the green shoots were emerging.
In the months since then, as our country began returning to some form of ‘normal,’ Made in Britain has been inundated with member companies describing order books that are full to bursting and instances of demand far outstripping supply. The increasing appetite for British goods post-Brexit and postpandemic, has also been reflected in our membership which has
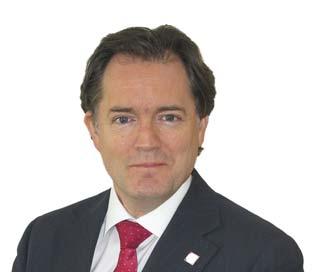
Making it in Britain
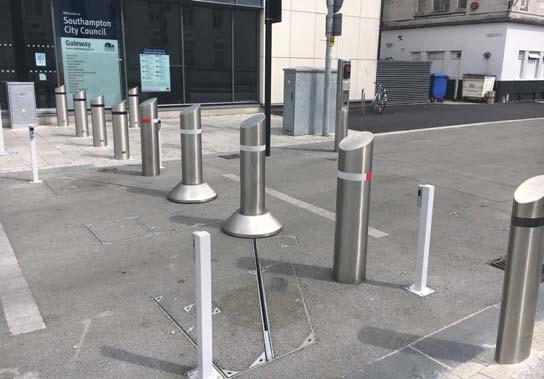
been growing at its fastest-ever rate as our community seeks to capitalise on rising domestic demand for British made.
Indeed, over the last 18 months, there has been genuine, measurable growth and real progress in British manufacturing. We have seen evidence for cautious but very real optimism about the future of our industry in general, and the engineering sector in particular a clear signal that British innovation is not just alive and well, but thriving.
More recently, conversations have been dominated by the HGV driver shortage and the supply chain disruptions affecting companies up and down the country. This serious on-going logistics crisis is just the latest in a series of extraordinary challenges for British engineering firms who’ve already been weathering the upheavals of Brexit, as well as the unprecedented limitations and restrictions of the lockdowns.
One of the positives to be gained following more than a year and a half of uncertainty is being compelled to look into what can be produced on our shores. A recent survey of Made in Britain members showed that over a third have completely localised their supply chains.
And our annual ‘Buying British’ research speaking to consumers and businesses to understand purchasing motivations and factors affecting shopping habits and attitudes towards British goods, showed that the majority of both consumers and businesses are now more likely to
8 Yorkshire-based Heald is a pioneer in hostile-vehicle mitigation systems
buy British goods than before the coronavirus outbreak.
Eight in ten businesses and consumers would happily pay more for products made in this country, while two-fifths of consumers and two-thirds of businesses would prefer to buy British regardless of the cost.
Britain’s engineering sector has a long-held reputation for quality, reliability and innovation. Within our membership - of which around a fifth are from the engineering sector - we have numerous examples of companies perpetually conceiving, creating and implementing new ideas and technologies.
Yorkshire-based Heald is a pioneer in hostile-vehicle mitigation systems. Following a growing number of attacks on high-profile bridges, the company set out to find a new way to better protect these structures. The challenge was that effective perimeter protection options had always been limited due to the impact on a bridge’s structural integrity.
Heald’s Bridge Bollard System, launched last year, found a solution to the problem. The system, consisting of fixed pillars on individual base plates bolted together, has revolutionised the bollard market as it requires a depth of just 50 millimetres.
Engineering supply firm Heap and Partners has been making valves for more than 150 years and has proven that a company is never too old to evolve and embrace the new. Founded in 1866, the company is now introducing QR codes and cloudbased technology into its manufacturing process. A move Heap and Partners believes will accelerate growth and create jobs.
Innovation is embedded in the business DNA of British engineering firms. That flair, together with the other hallmarks of the sector - quality and reliability - are jewels in the crown of industry in this country. Meanwhile, internationally, ‘brand Britain’ holds a value that hasn’t faded, with British businesses and consumers keener than ever to buy homegrown products.
On top of that, buying products that don’t have to be transported into the country from 1000s of miles away has obvious measurable benefits for the environment, so it’s not surprising to see a preference for products manufactured or sourced locally.
The government has moved their British-made procurement target from five percent up to fifty percent and we want to help them move that needle even further with proximity and quality our absolute priorities.
We know that British consumers want to buy more British goods, but confusion over provenance can be an obstacle. Some four in ten consumers say they can’t tell if a product is made in this country or not. When asked about the car we drive, for instance, we tend to know the country that owns the brand but not where the model was built.
To help cut through the confusion around product origin, manufacturers should make it as easy as possible for consumers and businesses to identify and buy British. The registered Made in Britain accreditation, for example, certifies a product’s place of origin while also recognising the producer’s ethical and sustainable business practices. The mark can also serve as a product ambassador around the world - an easy way to identify where a product is from, and who really takes responsibility for it.
The extent of the many business challenges faced by engineering firms and other manufacturers makes it difficult to ascertain whether things will correct back to normal by next year, or even the year after that. However, what we can be sure of is the incredible longevity in the British engineering community.
It’s not unusual to hear of British engineering firms that have been around for 100 years or more. Some of these companies have survived one or even two world wars and multiple recessions. They have resilience embedded in their DNA and will be able to adapt to whatever comes next.
British innovators will continue to be at the forefront of shaping the post-Brexit, postpandemic economy. And as we usher in this new era, the spotlight will rightly grow ever larger on the ideas and the goods created on these shores products that are made in Britain. 8 www.madeinbritain.org
Under-body protection for EVs
TRB Lightweight Structures has developed a composite under-vehicle protection plate for electric vehicle batteries that dramatically improves impact absorption while decreasing weight.
These panels have been created from a combination of materials and a proprietary, toughened TRB resin, using a manufacturing process that enables production at high volume. Cost-effective and high volume manufacturing, often the critical missing piece hindering composite adoption, has been developed in parallel with this new solution, and is now operating in both North America and the UK.
The new protection plates utilize a sandwich construction of advanced materials, layered intelligently to provide varying impact absorption strengths depending on location. Testing has shown impact absorption rates that are typically doubled compared with best-in-class steel solutions, while halving the weight. The plates can be painted although, unlike steel, paint is not required for corrosion protection, while the low weight construction simplifies installation and replacement.
“Skateboard chassis designs require better battery protection for both on and off-road vehicles,” said Richard Holland, Managing Director of TRB Lightweight Structures. “Our approach leverages decades of knowledge in the development and testing of materials and manufacturing methods, resulting in a costeffective solution for automotive components that decreases weight and increases performance.” 8 trbls.com
engineering, composites
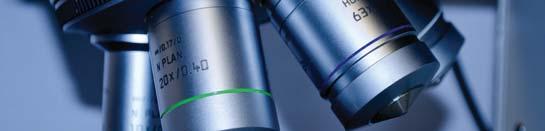
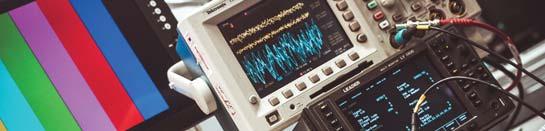
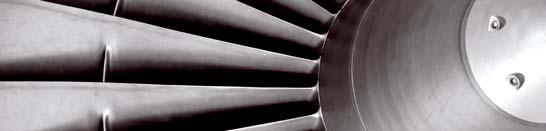
PR | Marketing | | Copywriting | Events Awards | Design | | Web & SEO
01752 894786 www.aroprandmarketing.co.uk
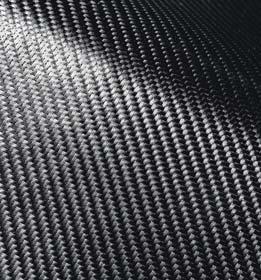