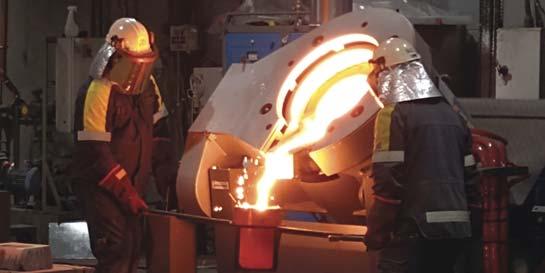
8 minute read
INDUSTRY NEWS
A £600,000 upgrade will increase efficiency and reduce the environmental impact of Wall Colmonoy’s casting facility at Pontardawe, Wales.
Wall Colmonoy manufactures surfacing and brazing allows, castings, and engineered components for the aerospace, automotive, glass, oil & gas, mining, energy and other industrial sectors.
The casting upgrade includes new induction melting equipment and magnetically screened furnaces. The new casting furnaces offer increased capacity and reduced processing times, due to improved reliability and reduced downtime. The upgrade also incorporates better controls on pouring practices with data-driven monitoring sensors and software.
Andrew Williams, Project Leader, explains: “It is very satisfying to successfully complete the project, with a brand new high-specification foundry. The investment puts us on the leading edge of cast alloy melting technology and helps us facilitate our drive for innovative growth to meet the increase in global demand for our castings.”
With the disruption of global supply chains following the pandemic, Wall Colmonoy has seen increased demand from EU and UK customers for its engineered cast or fully machined components which are designed to optimize wear, corrosion, abrasion, and heat resistant properties. The foundry supports multiple casting methods including investment, centrifugal, sand cast, and vacuum cast processes across such industries as food, steel, glass, aerospace, and oil & gas.
This significant foundry upgrade forms part of a strategic investment program at Wall Colmonoy Limited, which has included the purchase of advanced measuring systems, upgraded machinery, such as a new Hurco 5Axis Milling Machine and a Desktop Metal Shop System for additive manufacturing – all of which are designed to position the Precision Components division at the forefront of manufacturing technology.
The casting facility investment is partly supported by Welsh and European funding with a £150,000 contribution from the Economy Futures Fund. 8 wallcolmonoy.co.uk
Leading edge metal melting
s – – sarB –
leetSssel ni a t S muinimuAl alP
repuS s yol l A scits n Subcontract mill turned parts up to 65mm in diameter from bar and 300mm billet work.
billet bar and 300mm and 30 billet work meter diameted300mm mill turnedto65mm inu up to 65 eterfrom mill turned parts to65 m bcontSubcodparts k.
Foundry Training Services Ltd (FTSL) has helped Belfast Metropolitan College to get its onsite foundry working and to train new staff members.
FTSL was approached during the pandemic by the college and embraced the challenge.
After a few virtual meetings the FTS team attended the college in Belfast for two days and carried out the initial start to the training. The training included carrying out various activities as the foundry had not been operational for some time. Now, with the support of FTSL, the foundries furnaces have been switched on again. The first phase of training will continue into 2022 with further phases to be arranged.
FTS says that this is the start of a great relationship with the college and again another example of how it is keeping the industry alive.
In other news, Michala French, operations managers at FTSL says that it has worked hard with Dudley College to secure another group of apprentices.
She said: “We are pleased to welcome our fifth cohort to the centre who are all embarking on their journey in becoming the foundry technicians of the future. The first cohort of apprentices are about to enter gateway to their end point assessment, and we wish them all the luck in achieving their qualification. This, of course, will be the first group to achieve a qualification of this nature in the foundry industry in over 20 years.” 8 foundrytrainingservices.co.uk
The Manufacturing Technologies Association (MTA) has announced a new show dedicated to buyers looking to source precision subcontracting products and services from UK suppliers.
The Engineering Supply Chain Show which will take place alongside MACH 2022 at the NEC, Birmingham, on 5 to 7 April. Engineering Capacity is exhibiting at the show on Stand 7-510.
To exhibit, companies must be UK registered and offer capacity in subcontract or supply chain services. Examples
Training foundry revived

UK supply chain show
include precision machined-parts subcontracting, castings and forgings, coatings, mechatronic and electronic design and assembly, extrusion, fabrication, finishing, forming, pressings and stampings, tool making, forming and manipulation, vacuum technology and design, development and testing services.
This show-within-a-show is part of the MACH exhibition but sits as a separate 3-day event with its own location and entrance in Hall 7.
Commenting on the new exhibition, James Selka DL, Chief Executive Officer at The Manufacturing Technologies Association said; “This is a very exciting time for the UK’s engineering and manufacturing supply chain. More and more UK OEMs and Tier 1 companies are looking to re-shore their supply chains or develop new ones. This new exhibition, sited alongside the established MACH exhibition, will provide a focused showcase for their products and services.” 8 engineeringsupplychain.co.uk
Custom magnet and magnet assembly manufacturer MagDev Ltd has been acquired by Bunting, one of the world’s leading designers and manufacturers of magnets, magnet assemblies and magnetising equipment, which has its European engineering manufacturing facilities in Berkhamsted and Redditch.
The move will expand Bunting’s product portfolio and magnet engineering knowledge.
MagDev was part of the Delta Magnet group of companies, based in Swindon UK. The facility features testing and in-house machining facilities as well as over 1,100 square meters (12,000 sq ft.) of warehouse space. MagDev is a leading custom magnets and industrial magnets manufacturer specialising in supplying permanent magnets, magnetic assemblies and soft magnetic solutions in various shapes, sizes and grades, with magnetic properties tuned to specific applications.
The origins of MagDev date back to 1973, with the company becoming part of the MMG group of companies in 1986. In August 2003, the merger of MMG GB Ltd and Magnet Developments Ltd in Swindon, UK formed MMG MagDev Ltd. After the Delta Magnets Ltd acquisition of MMG MagDev Ltd in June 2010, the company became part of the DMG group of companies.
With an experienced technical development team, MagDev Ltd has the capability to meet a wide range of magnet material
Custom magnet move

requirements, both with permanent and soft magnet materials, whether from a stock of standard parts or through bespoke development.
MagDev magnetic applications engineers will join forces with the existing team at Berkhamsted. As one engineering entity, the scope of magnet design and specification extends across an expansive range of sectors and applications. This includes the dynamically changing automotive, aerospace and electronics sectors, especially concerning low carbon transportation.
“The acquisition of MagDev expands our range of magnetic solutions, especially in relation to soft magnet materials,” explained Simon Ayling, Bunting’s European Managing Director. “The present demand for magnet application engineering has never been higher. We are working with companies across the manufacturing sector, especially in automotive, aerospace and electronics. The addition of the MagDev products and, more importantly, the technical team, significantly expands our magnet knowledge and capability. This is an exciting development enforcing Bunting’s position as the leading European designer and supplier of magnets, magnetic components and magnetising equipment.” 8 bunting-berkhamsted.com
DNow Accredited to
FM10101
Manufacturers of High Quality Mill-Turned Parts
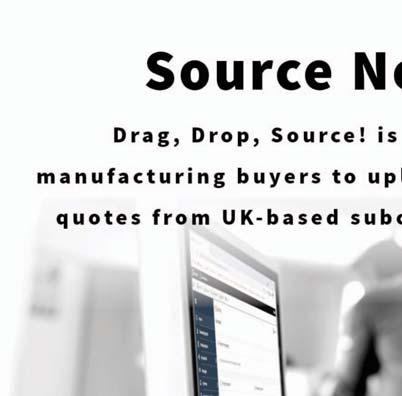
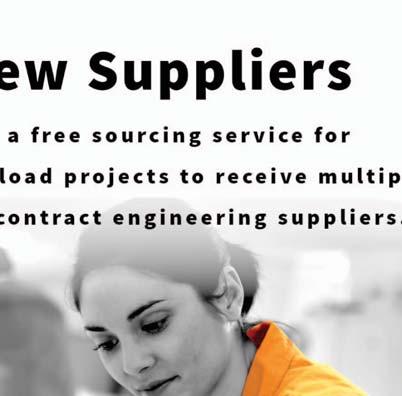
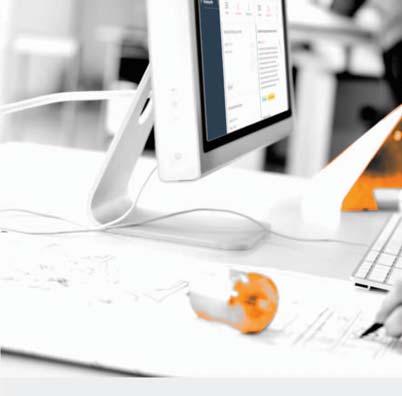
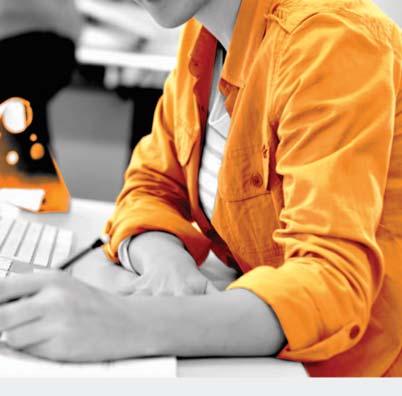
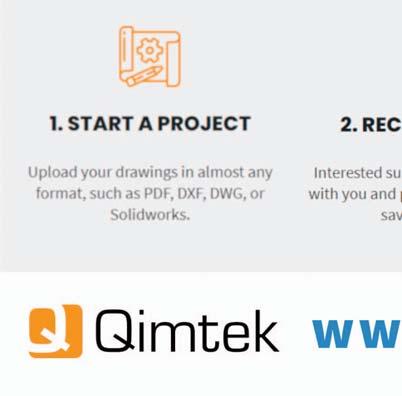
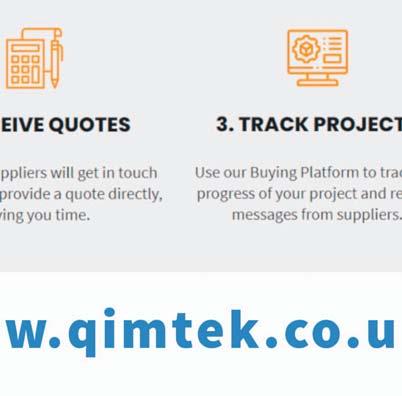
Hague Fasteners, which produces non-standard fasteners and bespoke bolts, recently turned 50 years-old and marked the big anniversary by investing more than £100,000 into a new three-axis CNC lathe to help it deliver more complex parts and increase capacity.
The XYZ CT 65 LTY is already being used to deliver contracts for the oil and gas sector, with the company hoping the additional turnover will help it move towards its target of £2m sales by the end of the year.
It marks what has been the busiest period in the family-run firm’s recent history, with current Managing Director Jon Hague joined at the helm by his wife Claire and sons Jack (Technical Director), Tom (Customer Service) and Max (Finance).
“My father John Hague started the business 50 years ago and back then it was founded on technical expertise, the same technical expertise that is still crucial today in helping us supply parts to more than 30 countries across the world,” explained Jon, who joined Hague Fasteners straight from school in 1989.
“I think he’d be very proud that we have been able to withstand global recessions and the recent pandemic and the fact that the business now has the third generation of Hagues working here.”
He continued: “The family ethic extends to all members of our 16strong workforce. They have been fantastic during Covid-19, allowing us to remain operational and ensuring we continued to provide critical fasteners and bolts to the NHS and for power stations all over the world.
“The new 3-axis CNC machine is a perfect way to celebrate five decades in business and puts a marker in the sand for the technology we are trying to embed into our future capabilities.”
Hague Fasteners has been manufacturing in the Black Country for the last fifty years, its most recent move being to an 8500 sq ft factory on Monmer Close in Willenhall in 2017.
From here, the company produces specialist fasteners, headed bolts, studs, nuts and milled components in high integrity materials and critical nickel alloys.
Working with high integrity steel and superalloy bar, the company can work to customer drawings to produce parts ranging in size from 2mm to 250mm in diameter.
Claire Hague, Company Owner, went on to add: “We also wanted to do something in our 50th year that left a lasting positive legacy, so made the commitment to become Carbon Neutral by 2024.
“This has seen us create the ‘Hague Forest’, where we will endeavour to plant and grow 200 trees every year in Haiti, Kenya and Madagascar to offset the 75 tonnes of CO2 we create manufacturing specialist fasteners for use across the globe. 8 haguefasteners.co.uk
CNC investment at 50
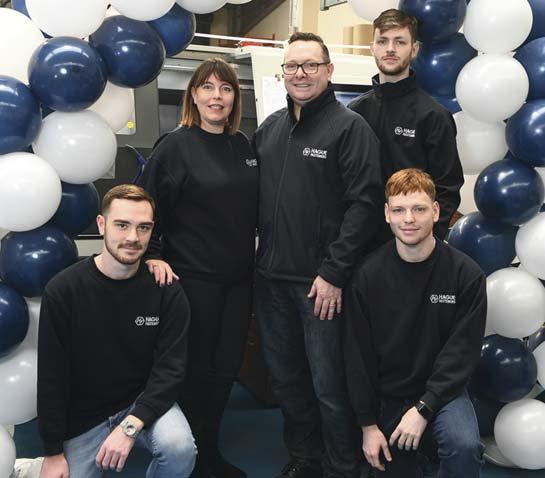