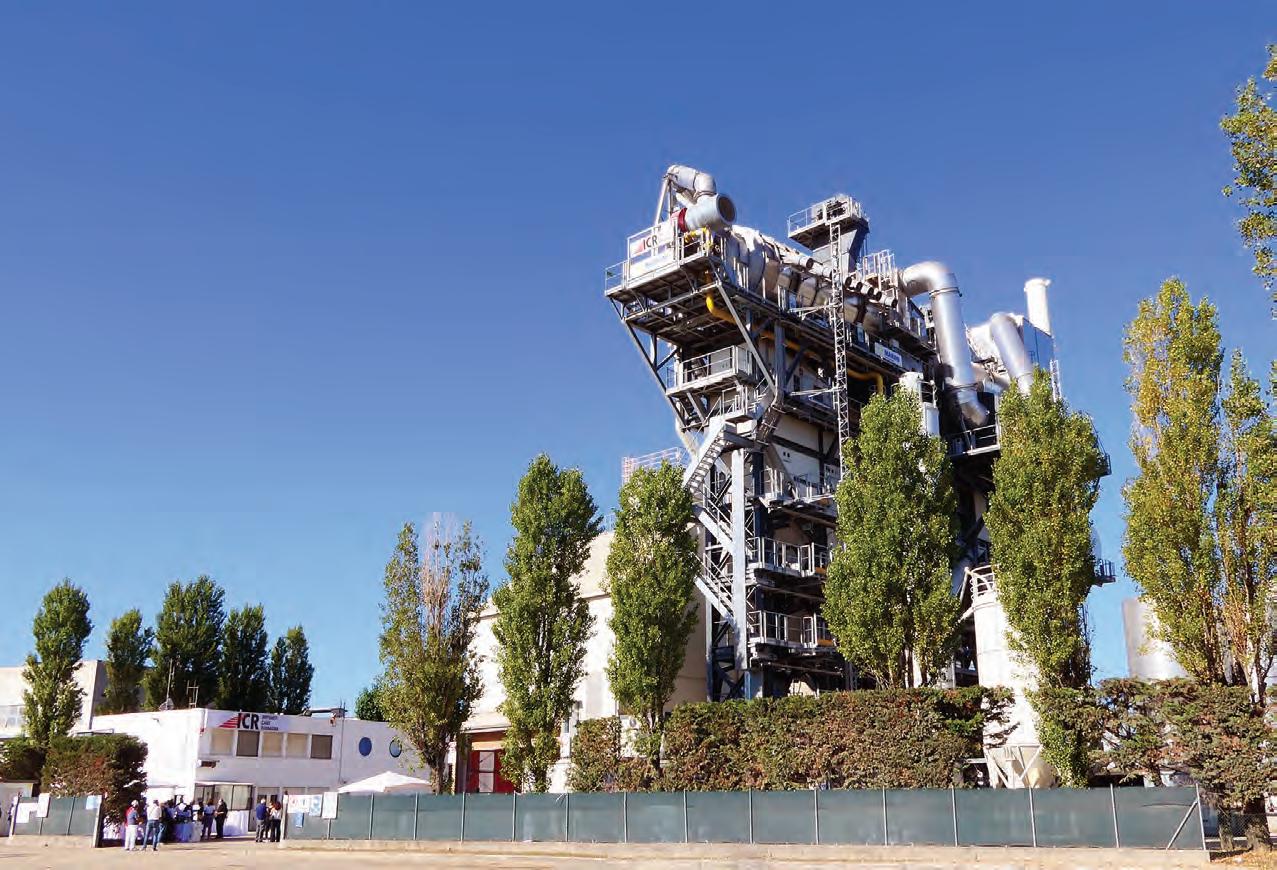
10 minute read
Circolarità, minori consumi e rispetto dell’ambiente
asfalti&bitumi
CIRCOLARITÀ, MINORI CONSUMI
Advertisement
E RISPETTO DELL’AMBIENTE
IL PRIMO IMPIANTO MASTER TOWER PER LA PRODUZIONE DELL’ASFALTO A CALDO VENDUTO IN ITALIA DA MARINI STA LAVORANDO GIÀ DALLO SCORSO ANNO A PIEVESESTINA PRESSO LA SEDE DI ICR (IMPIANTI CAVE ROMAGNA)

1. La rappresentazione in 3D dell’impianto Marini Master Tower Lo scorso mese di Settembre è stato presentato ufficialmente a Pievesestina (FC) il primo esemplare “italiano” del Marini Master Tower, l’impianto di ultima generazione per la produzione di asfalto a caldo che costituisce un caso senza precedenti nel suo genere, dal momento che utilizza materiali riciclati ad alte percentuali, opera con miscele a basse emissioni e fornisce un elevato risparmio energetico (si veda “Strade & Autostrade” n° 134 Marzo/Aprile 2019 a pag. 102). Il Master Tower guarda anche ai mercati internazionali, che ne hanno accolto l’uscita con grande interesse in occasione del BAUMA 2019. Nel nostro Paese, la prima a puntare sulla sua tecnologia di ultima generazione è stata l’Azienda ICR (Impianti Cave Romagna): alla presentazione ufficiale del suo impianto, insieme ai vertici ICR e Marini, sono intervenuti il Prof. Cesare Sangiorgi dell’Università degli studi di Bologna, che insieme a Marini ha condotto la sperimentazione sul Master Tower, il Presidente della Regione Emilia-Romagna, Stefano Bonaccini, la Presidente dell’Assemblea Legislativa della Regione EmiliaRomagna, Emma Petitti, e il Sindaco di Cesena, Enzo Lattuca.
IMPIANTI PER CONGLOMERATI
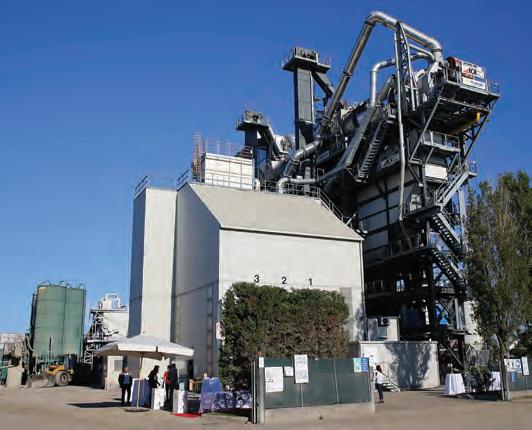
2. L’impianto Marini Master Tower installato a Pievesestina (FC) presso la sede ICR
“La sostenibilità ambientale, l’innovazione tecnologica e una importante riduzione dei consumi energetici sono i motivi che hanno spinto a realizzare un impianto così all’avanguardia proprio a Pievesestina” ha dichiarato durante il suo intervento Valerio Brighi, Presidente di CBR (Cooperativa Braccianti Riminese), che dirige e controlla la nuova realtà territoriale rappresentata da ICR. “Nell’ambito della pavimentazione stradale, il riutilizzo di materiali esistenti e, nello specifico, del fresato proveniente da pavimentazioni di infrastrutture viarie sottoposte ad usura, la capacità di produrre miscele a ridotte emissioni di anidride carbonica (CO2) e il risparmio energetico sono temi imprescindibili per chi voglia produrre un asfalto che rispetti l’ambiente”, ha commentato l’Ing. Luca Camprini, CEO di Marini. “Il Master Tower rappresenta, proprio in quest’ottica, un nuovo traguardo nella produzione di conglomerato bituminoso”. La soluzione proposta è il risultato della semplificazione del processo di produzione delle miscele di conglomerato bituminoso, attraverso l’ottimizzazione e la razionalizzazione dell’impianto e un completo ricircolo dei gas prodotti, con uno sfruttamento massimo dell’energia introdotta. Il risultato è tale da consentire la produzione di nuove miscele di conglomerato bituminoso contenente percentuali di fresato elevate, che raggiungono anche il 100%, recuperando totalmente i materiali provenienti dalle pavimentazioni stradali esistenti. L’innovativo sistema di gestione dei fumi, che consente di ridurre enormemente le emissioni in atmosfera, fa del nuovo impianto una tecnologia perfettamente capace di integrarsi in ogni contesto ambientale.
IL MASTER TOWER DI ICR DOPO IL PRIMO ANNO DI LAVORO
L’impianto è stato montato e messo in funzione presso la sede ICR tra l’Agosto e il Settembre nel 2019. Da allora, pur con le limitazioni legate alla pandemia da Covid-19, la macchina ha lavorato con continuità. “I dati in nostro possesso” ha commentato Marzio Ferrini, Responsabile Product Marketing di Marini, “indicano una produzione di circa 170.000 t dal momento in cui l’impianto è divenuto operativo alla fine di Luglio del 2020, ma da allora i numeri sono senz’altro cresciuti, perché il Master Tower di ICR ha lavorato moltissimo rispetto alla media nazionale”. L’Azienda di Pievesestina ha creduto da subito al concetto tecnologico e alle caratteristiche offerte dal Master Tower, tanto da perfezionare l’acquisto già al termine del 2018, prima della presentazione ufficiale al BAUMA, dove è stata esposta la dicitura “macchina venduta a ICR”. In particolare, Ferrini sottolinea come la scelta del Cliente sia stata dettata da tre fattori, corrispondenti al senso stesso del progetto Master Tower: possibilità di riutilizzo del fresato in altissime percentuali, con una qualità del risultato finale equiparabile alle miscele vergini e a costi notevolmente inferiori; risparmio di energia; contenimento delle emissioni. “L’Università di Bologna - spiega Ferrini - ci ha aiutato nella prima fase del progetto di sviluppo del prototipo e di analisi delle modalità di realizzazione, che si è svolta dal 2016 al 2018. Il prototipo ha lavorato per sette-otto mesi presso la sede Marini di Alfonsine, dopodiché abbiamo consegnato a ICR la macchina definitiva, pronta per lavorare. La collaborazione con l’Ateneo bolognese prosegue tuttora e ci sta aiutando a spingere la macchina verso la sua massima performance, corrispondenti alle specifiche di progetto, ovvero realizzare conglomerati con alte percentuali di fresato e un’altissima qualità delle miscele. Dal punto di vista del prodotto, il risultato è equiparabile a quello che si ottiene con miscele basate sul 100% di materiale vergine: questo era il primo obiettivo che ci siamo posti con la Master Tower.
3. La tecnologia Master Tower comprende due tamburi essiccatori, posizionati sopra il mescolatore e dotati di un unico bruciatore: questo permette un elevato risparmio energetico
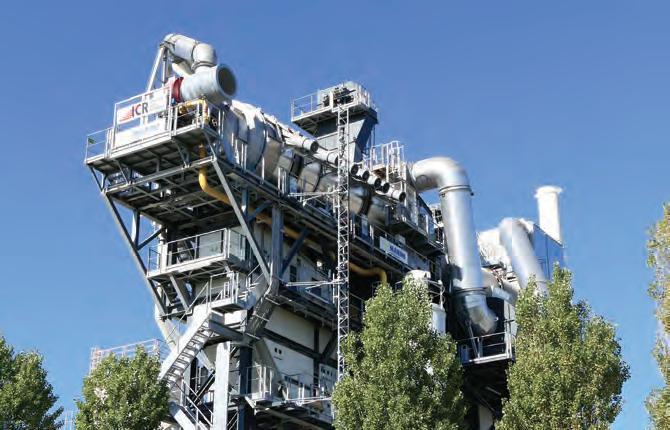
asfalti &bitumi
Il secondo consisteva nel risparmio energetico e nell’efficienza: in termini di kWh per tonnellata e in rapporto all’energia occorrente per far funzionare altri impianti, compresi quelli di produzione Marini, i risultati forniti dal Master Tower evidenziano, senza possibilità di errore, un risparmio che va dal 20 al 25%. Questo si traduce in una serie di vantaggi per la comunità, legati al minor quantitativo di combustibile utilizzato, ma anche in un risparmio rilevante per l’Azienda. Il terzo obiettivo, sempre strettamente legato all’ambiente, è nella limitazione delle emissioni. I test operati dall’Università di Bologna sono stati affiancati in ogni fase da prove di emissioni a percentuali progressive di fresato, con relativo monitoraggio di tutti i parametri, compreso quello dei COV (Composti Organici Volatili), ovvero il più sensibile all’utilizzo del fresato; in questo ambito, il risultato del Master Tower si mantiene ampiamente al di sotto della soglia di 50 mg/m3 a livello europeo, quando il limite in molte province italiane si spinge anche fino a 100 mg/m3 o 150 mg/m3: tale risultato, vale la pena di sottolinearlo, viene ottenuto con una macchina che durante le prove svolte con l’università di Bologna produceva con il 70-80% di impiego di fresato”. Le tecnologie del Master Tower, completamente diverse da quelle solitamente in dotazione a un impianto tradizionale - come il raffinato sistema di controllo, che va dalla modulazione del bruciatore al ricircolo d’aria - hanno richiesto una fase di formazione al Cliente, ritenuta fondamentale da Marini. Tuttavia, la macchina è concepita per limitare al minimo l’intervento dell’operatore, chiamato quindi a limitarsi a un’attività di supervisione e alla scelta di ricette e temperature, mentre la gestione del processo è prevalentemente automatizzata. “Un altro aspetto particolarmente apprezzato da ICR è la possibilità di mantenere elevati livelli di produzione e aggiudicarsi appalti importanti sul territorio” - ha aggiunto Marzio Ferrini, interrogato sulle impressioni di utilizzo da parte del Cliente dopo questo primo periodo. “Stiamo riscontrando una piena soddisfazione e la nostra vicinanza prosegue, perché questa macchina rappresentava una scommessa per entrambe le realtà: ICR e Marini. La fase di affiancamento è terminata negli ultimi mesi dell’anno scorso, ma in cantiere siamo ancora presenti, stiamo monitorando la macchina e la stiamo conoscendo insieme a ICR giorno dopo giorno, grazie anche alla vicinanza tra le due sedi, fondamentale dal punto di vista logistico: per essere sul posto è sufficiente una mezz’ora di tragitto in automobile e, quando l’Università di Bologna deve compiere i test, abbiamo la possibilità di essere sempre presenti. Il Cliente, dal canto suo, ci offre la sua disponibilità, in una sorta di partenariato che presenta benefici anche per il perfezionamento del suo impianto. Per quanto ci riguarda, il monitoraggio e la diagnostica da remoto sono una possibilità offerta da tempo su tutti gli impianti Marini, ma la riteniamo ancora più fondamentale nel caso di un progetto chiave come il Master Tower”.
LA VIA VERSO LA CIRCOLARITÀ E IL RISPETTO DELL’AMBIENTE (NON SOLO IN ITALIA)
I rappresentanti delle Istituzioni locali intervenuti nella giornata di presentazione dell’impianto lo scorso Settembre hanno sottolineato entrambi l’importanza dei concetti di circolarità e sostenibilità ambientale. Il tema è centrale, a maggior ragione in presenza di Decreti ministeriali che hanno riabilitato il fresato, trasformandolo da rifiuto a risorsa utilizzabile nelle miscele. “È come avere una “mine road”, una cava sulla strada, che consente di riutilizzare il materiale in loco oppure in zone limitrofe” - commenta Ferrini. “Le Amministrazioni pubbliche stanno cavalcando con decisione il tema dell’economia circolare e poter contare su macchine che, di fatto, la rendono realizzabile, abbattendo al contempo e in modo drastico le emissioni - in particolare odorigene - è un fattore decisivo. Master Tower consente tutto questo”. La possibilità di reintrodurre tutti i gas generati dal riscaldamento del fresato nella zona della fiamma, trattenuti grazie allo speciale design del tamburo essiccatore, presenta anche il vantaggio della reimmissione di fumi già caldi. “Il principio - prosegue - è lo stesso della caldaia a condensazione: quello di non disperdere del calore che è già stato prodotto”. L’impianto permette di ottenere miscele con altissime percentuali di fresato senza problemi o settaggi particolari. “Se

4. Le Autorità presenti all’inaugurazione del Master Tower: da sinistra, Cesare Sangiorgi dell’Università degli Studi di Bologna, Enzo Lattuca, Sindaco di Cesena, Stefano Bonaccini, Presidente della Regione Emilia-Romagna, Valerio Brighi, Presidente di CBR, Luca Camprini, CEO di Marini, Emma Petitti, Presidente dell’Assemblea Legislativa della Regione Emilia-Romagna, e Massimo Giorgini, Presidente di ICR 5. Un momento della visita guidata sull’impianto Master Tower nel giorno dell’inaugurazione
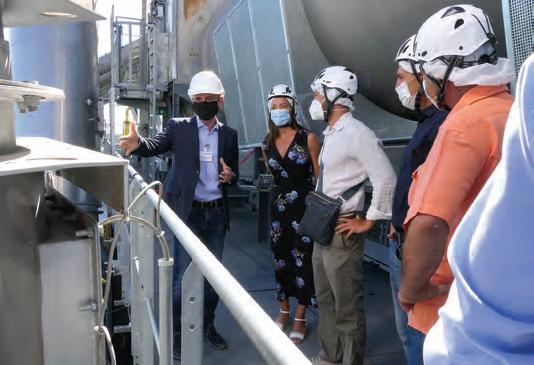
IMPIANTI PER CONGLOMERATI
parliamo di percentuali che per certe opere possono raggiungere anche l’80% - puntualizza Ferrini - sottolineo l’importanza della nostra collaborazione con Iterchimica e un’opportuna lavorazione del fresato che può comportare costi aggiuntivi. Nonostante questo, i costi di produzione risultano essere significativamente inferiori rispetto a un’equivalente produzione con solo materiale vergine, sempre garantendo equivalenti se non superiori prestazioni”. Non mancano manifestazioni di interesse anche dai mercati esteri, attenti sia all’aspetto della percentuale di fresato che a quelli del risparmio energetico e dell’abbassamento di emissioni. Varie richieste, ad esempio, sono già pervenute a Marini dall’Europa Centrale, dal Sud-Est asiatico e dall’Australia. Laddove si presenti l’esigenza di avere un impianto in una città o, come nel caso di ICR, in una posizione strategica al crocevia tra assi autostradali, il Master Tower può quindi offrire una risposta importante anche a livello internazionale. L’impianto è, in ogni caso, interamente made in Italy. Tutti i suoi componenti, incluso il
tamburo da 3,30 m di diametro, sono infatti prodotti ad Alfonsine, in accordo con la scelta strategica di Marini volta a mantenere esperienza e capacità produttiva nei vari territori serviti, oltre alla salvaguardia del lavoro e delle competenze maturate. n 6. La presentazione in 3D dell’impianto Marini Master Tower con alcune sezioni in trasparenza
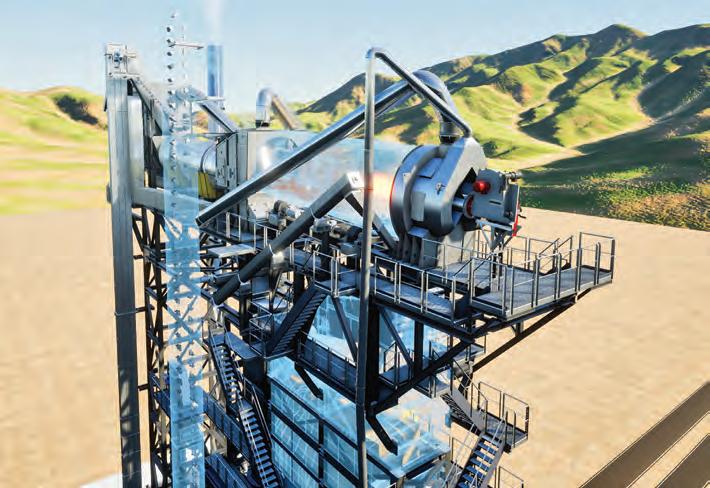
PRO PATCH è un conglomerato a freddo per la manutenzione permanente del manto stradale. Ottenuto al 100% da riciclaggio. Pro Patch a sua volta è riciclabile. Caratteristiche straordinarie: - la forza del prodotto sta nella sua facilità di impiego. - una volta steso il prodotto, si può aprire la strada al passaggio del traffico. - sarà il traffico stesso a sistemare il materiale facendolo aderire alla pavimentazione. La caratteristica principale di Pro Patch è quella di non attaccarsi agli pneumatici. SEALING FAST è un prodotto bituminoso bi-componente da stendere a freddo per lasigillatura delle crepe del manto stradale. L’impiego di questa tecnologia è ideale per la sigillatura di fessurazioni di pavimentazioni in conglomerato bituminoso o in calcestruzzo, per il ripristino dei giunti di dilatazione di ponti e viadotti, per la sigillatura e l'arresto degli ammaloramenti stradali cosiddetti a pelle di coccodrillo e per i lavori di posa e ripristino di pavimentazioni discontinue in pietra. La posa di Sealing Fast deve essere eseguita con Sealing Set o Sealing Set Pro, macchine proporzionatrici appositamente progettate.
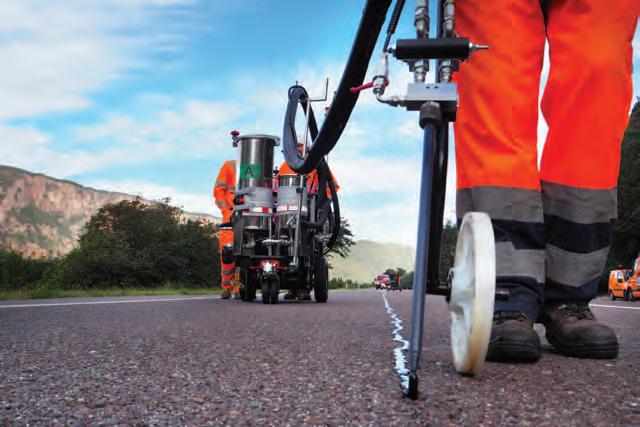
DAL TETTO... ...ALLA STRADA!
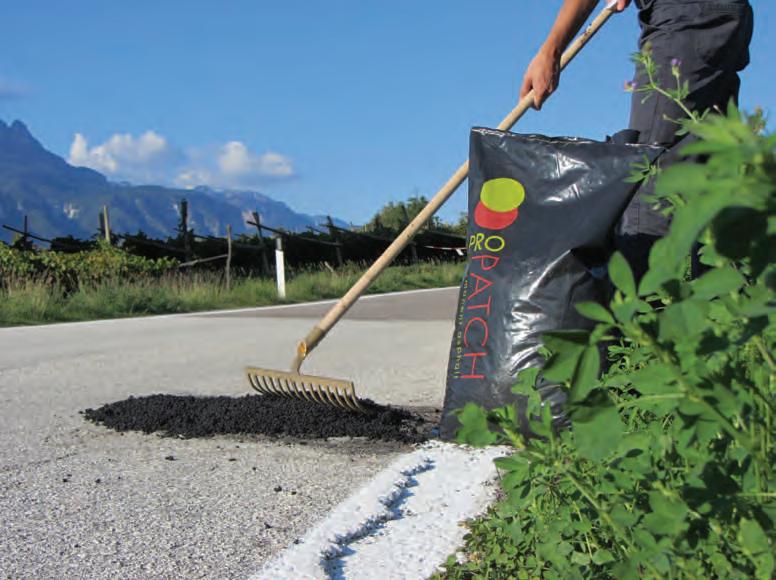