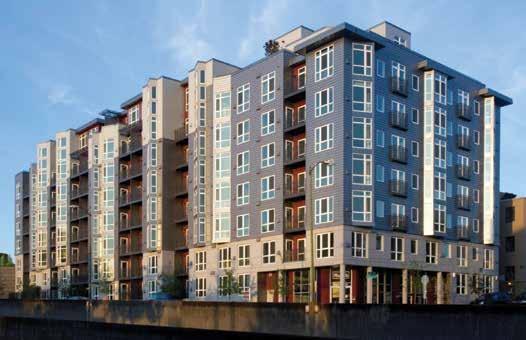
18 minute read
INFOCUS
InFocus new trends, new techniques and current industry issues Your Mileage May Vary Are You Taking Full Advantage of CEU Opportunities?
By Barry Arnold, P.E., S.E., SECB
Are you investing in your future or wasting your time and money on CEUs? CEUs are an investment in your future and, like all significant purchases, should be taken seriously. At eighteen, I was ready to make an investment in my future by buying a reliable, affordable, and economical car, so I headed to the used car lot. Among the numerous options in color, age, make, mileage, and models, I found a car that fit my budget, appeared road worthy and, according to the Dealer’s Data Sheet, got high gas mileage. I was in heaven. Within two weeks I was stranded on the roadside twice and had to pay for major repairs. It also became apparent that the only way the car was going to achieve the advertised mileage was if it was freefalling or being towed, so I returned to the dealer to complain. The salesperson pointed out the fine print on the bottom of the Data Sheet which read: Your mileage may vary. He followed up with, “You get what you pay for.” My money was spent, and I did not get what I needed. I was in misery. Adages like “Your Mileage May Vary” (YMMV) and “You Get What You Pay For” (YGWYPF) are subcategories of Caveat Emptor (Latin for “Let the buyer beware”) that are more than just witty sayings and apply to more than just purchasing used cars. A college education was my next big purchase, and the phrases YMMV and YGWYPF were in the forefront as I thoroughly researched various universities. I considered location, convenience, cost, professor credentials, and the college’s emphasis (teaching, research, etc.). Because college would be the foundation of my career, I was determined to get the biggest return on my investment and make the best choice. After securing my degree, I came to realize that college was not, and could not be, the end of my education. I realized that I had not only a chance but a responsibility to continue my education by earning Continuing Education Units (CEUs or PDHs), which give me an opportunity to not only refine and improve my engineering skills but to achieve greater success. Self-Development Guru Brian Tracy pointed out that, “Those people who develop the ability to continuously acquire new and better forms of knowledge that they can apply to their work and to their lives will be the movers and shakers in our society for the indefinite future.” CEUs provided the opportunity to acquire new and better forms of knowledge. Beyond the personal gains an engineer may receive through continuing education, CEUs are important to the profession and the safety of the public. They offer opportunities to learn about new procedures, materials, and techniques. CEUs help engineers stay up-to-date with current code requirements. Ultimately, CEUs are an investment in your future and, therefore, should be taken seriously. Although some states accept almost any CEUs to retain a professional engineering license, it is important to maximize the return on your investment of time and money by participating in CEU programs that will build on your college education and fill gaps where additional training is needed to open doors to new opportunities. As Benjamin Franklin said: “An investment in knowledge pays the best interest.” YMMV and YGWYPF apply to our investment in CEUs. CEUs require an investment of your time and your money – both of which are non-refundable – so it is important not to get caught in the YMMV and YGWYPF trap. The easiest way to avoid the trap is to have a plan. I recently spoke to a group of engineers and suggested a 4-step process for securing the most from CEU opportunities: 1) Determine where it hurts. What problems are you currently facing? What challenges are preventing you from achieving your highest potential? Determine your weak points and address them by obtaining CEUs in relevant technical or non-technical courses, such as business development, marketing, networking, human resources, writing, accounting, or team management. Be open to new learning opportunities. 2) Consider before you buy. Not all CEU programs are created equal. Some are true educational opportunities filled with valuable content while others merely give you something to do for an hour. Look for providers with a proven record of offering quality programs. 3) Be prepared, be present. Request the instructor’s slides/notes before the presentation, so you will know what the course will cover and you can prepare questions. You paid to participate in the event. You know where it hurts. Now ask your questions and get answers. Be actively engaged in the educational experience. 4) Have a retention plan. The information you acquired is of little value if you do not remember it. Research indicates that you will only remember 50% of a 10-minute presentation immediately after you hear it. By the next day, you will lose 75% of the information. Within a week you will only remember 10% of what you learned. The best way to receive long-term benefit from a presentation is to review the related written material early and often. If you feel like you are not receiving the mileage you should out of your career, or that your career has stalled and left you stranded on the side of the road while your competition and colleagues pass you by, I recommend reevaluating your continuing education vehicle. Engage in programs that will provide a return on your investment. Carefully consider available CEU options and strengthen your long-term success by investing in educational opportunities that will benefit your career and protect the public. What are your thoughts? Would you like to share your ideas? The discussion continues at www.STRUCTUREmag.org. ▪
Barry Arnold (barrya@arwengineers.com) is a Vice President at ARW Engineers in Ogden, Utah. He chairs the STRUCTURE magazine Editorial Board and is the Past President of NCSEA and a member of the NCSEA Structural Licensure Committee.
Structural SyStemS
discussion and advances related to structural and component systems
Nationwide, there has been an increase in the demand for multi-story mixed-use and multi-residential structures. Common configurations include up to five stories of residential use over retail, commercial, office, and parking occupancies, similar in configuration to the building shown in Figure 1. Podium designs are one way to maximize the number of stories, increase unit density, and lower construction costs. This article covers important design considerations and traditional approaches related to the design of a five-story wood-framed structure over a two-story concrete or masonry podium. The 2012 and 2015 editions of the International Building Code (IBC) allow a maximum building height above grade of 75 feet using Type IIIB construction and 85 feet for Type IIIA if NFPA13 sprinklers are used. However, they only allow up to five stories for Types IIIA or IIIB structures under those same conditions. Structural provisions in the American Society of Civil Engineers’ Minimum 5-over-2 Podium Design Design Loads for Buildings and Other Structures (ASCE 7) limit the maximum height of wood structural panelPart 1: Path to Code sheathed shear walls to 65 feet above the base Acceptance of the seismic force-resisting system (SFRS) in Seismic Design Categories (SDC) D, E, or F. In By Terry Malone, P.E., S.E. order to gain additional stories, increase building area, and stay within the allowable building and seismic system heights, the IBC and ASCE 7 each have provisions which enable podium designs. IBC 2015 Section 510.2 allows an upper portion of any construction type to be built over a lower portion where the two portions are treated as separate and distinct structures. This is for purposes of determining the allowable area limitation, continuity of firewalls, type of construction, and number of stories. This allowance only applies when: • The building portions are separated by a horizontal assembly with a minimum 3-hour fire resistance rating, • The building below is of Type IA construction and is protected throughout with NFPA13 sprinklers, • Shafts, stairways, ramps, and escalator enclosures penetrating the horizontal assembly have a 2-hour fire resistance rating, and • The maximum building height measured in feet above grade is not exceeded. In versions of the IBC up to and including 2012, the lower portion of the construction described by these provisions, commonly referred to as the podium, can be no more than one story above the grade plane. However, the 2015 IBC allows multiple story podiums. This allows two stories of podium with five stories of wood framing above to meet the 85-foot maximum building height limitation and also meet the 65-foot SFRS height limit. For buildings designed in jurisdictions enforcing codes preceding the 2015 IBC, this would require an alternate means and methods request approval by the Authority Having Jurisdiction (AHJ). However, knowing that this allowance is provided in the 2015 edition often eliminates the AHJ’s concerns. Example floor plan configurations typically encountered in mid-rise multifamily construction are shown in Figure 2. These plans are frequently rectangular in shape with or without exterior shear walls, or they can have multiple horizontal offsets and wings. The lateral force resisting system for the flexible upper portion is typically built with wood-framed shear walls sheathed with wood
Terry Malone is a Senior Technical Director of Architectural and Engineering Solutions at WoodWorks. He is the author of The Analysis of Irregular Shaped Structures: Diaphragms and Shear Walls, published by McGraw-Hill and ICC. He may be reached at terrym@woodworks.org.
The online version of this article contains references. Please visit
Transverse
SW Typical
Corridor Walls
Ext. SW Typical Transverse SW Typical
Corridor Walls
Ext. SW Typical Typical Unit
Typical Unit
Open Front
Non Open Front Blocking used to fasten wall board and reduce vertical shrinkage Concrete topping
Top flange hanger
Joists or trusses Rim joist
Open Front & Non-open Front Floor Plan w/ and w/o offsets
Figure 2. Typical floor plans for mid-rise multifamily construction.
Semi-Balloon Framing Platform Framing
Figure 3. Typical framing details for load-bearing wood-framed walls.
structural panels (WSP). Many, if not all, of the walls separating the dwelling units are used as interior shear walls in the transverse direction. Lateral forces in the longitudinal direction are typically resisted by the exterior walls and corridor walls. If a rigid diaphragm analysis is warranted, the transverse walls would also act to resist torsional forces. Designers of these buildings should avoid having more than one SFRS in the flexible upper portion. ASCE 7-10 Section 12.2.3 notes that, when combining different seismic-force-resisting systems in the same direction, the most stringent applicable structural system limitations of ASCE 7-10 Table 12.2-1 shall apply. For example, lightframed shear walls with WSP sheathing have a response modification coefficient of R=6.5. Combining light-framed shear walls sheathed with other materials (e.g. gypsum wallboard) having a response modification coefficient of R=2 would require the WSP walls to be designed for forces in excess of three times greater (6.5/2) than if only WSP walls are used. Similar force modifications for wind demands do not apply. Framing systems for gravity loads in the upper portion commonly consist of loadbearing wood-framed wall configurations as shown in Figure 3. Semi-balloon framing can be used to reduce vertical shrinkage. This system utilizes top flange joist hangers to support the floor framing off the bearing walls. Considerations with this system include the eccentric gravity load effects on the wall studs caused by top flange joist hangers. This must be accounted for in the design and can in some cases increase the size of the studs. Another consideration is the detailing and added framing challenge of placing the interior wall sheathing between or behind the joist hangers. Several connector manufacturers now have joist hangers that are unique for this type of installation, which simplifies the process. The other option is to use platform framing, which is easier to install, reduces stud heights, takes less time to install, and can eliminate the joist hanger and costs associated with semi-balloon framing. However, this method of framing has an increased potential for vertical shrinkage. Proper detailing for either framing system can address this issue.
Two-Stage Seismic Analysis
Structurally, ASCE 7-10 Section 12.2.3.2 provides a two-stage analysis procedure that can be beneficial for seismic design of podium projects. The procedure treats the flexible upper and rigid lower portions of the structure as two distinct structures, thereby simplifying the seismic design process. Only the weight of the flexible upper portion has to be considered in its design, not the entire weight of both portions. The two-stage analysis also allows the seismic base of the upper portion to be the top of the lower portion. This allows measuring the maximum SFRS height for a wood structural panel-sheathed shear wall system, in SDC D through F of 65 feet, from the top of the podium. The requirements for a two-stage analysis are: a) The stiffness of the lower section is ten times the stiffness of the upper section. b) The period of the entire structure is not more than 1.1 times the period of the upper portion considered as a separate structure supported at the transition from the upper to lower portions. c) The upper portion is designed as a separate structure using the appropriate
R and redundancy factor, ρ. d) The lower portion is designed as a separate structure using the appropriate R and ρ. The reactions
from the upper portion are determined from the analysis of the upper portion amplified by the ratio of the R/ρ of the upper portion over the R/ρ of the lower portion. This ratio is not less than 1.0. e) The upper portion is analyzed with the equivalent lateral force or modal response spectrum procedure, and the lower portion is analyzed with the equivalent lateral force procedure. Some confusion exists regarding the required amplification of forces that are transferred from the flexible upper portion into the podium slab. The amplification factor in ASCE 7-10 Section 12.2.3.2 (d), when used, applies to only the seismic component of the reaction forces, not the entire reaction-included gravity loads. Gravity framing (e.g. beam, post-tensioned slabs, columns) supporting a discontinuous shear wall is designed for over-strength where required by ASCE 7-10 Section 12.3.3.3. Connection requirements to the podium slab are shown in Figure 4 (page 12).
Diaphragm Design
Distribution of forces to the vertical resisting elements are based on analysis methods where the diaphragm is modeled as follows: • Idealized as flexible – The distribution is based on tributary area. In common multi-family shear wall layouts, this can under-estimate forces distributed to corridor walls and over-estimate forces distributed to exterior walls with a similar impact on diaphragm forces being delivered to the walls. • Idealized as rigid – The distribution is based on relative lateral stiffnesses of vertical-resisting elements of the story below. This more conservatively distributes lateral forces to corridor
and transverse walls and allows easier determination of building drift, but can over-estimate torsional drift and underestimate forces distributed to exterior walls, including diaphragm forces. • Modeled as semi-rigid – e diaphragm is not idealized as rigid or exible.
Shear is distributed to the verticalresisting elements based on the relative sti nesses of the diaphragm and the vertical-resisting elements, accounting for both shear and exural deformations. In lieu of a semi-rigid diaphragm analysis, it is permitted in the American Wood Council’s Special
Design Provisions for Wind and Seismic (SDPWS) 2015 Section 4.2.5 to use an enveloped analysis, analyzing for both exible and rigid conditions and taking the largest forces. Current practice for light-frame construction commonly assumes that wood diaphragms are exible for the purpose of distributing horizontal forces to shear walls. ASCE 7-10 Section 12.3.1.1 (c) allows diaphragms in light-frame structures to be idealized as exible when 1½ inches or less of non-structural topping, such as concrete or a similar material, is placed over WSP diaphragms, and each line of vertical elements of the SFRS complies with the allowable story drift of ASCE 7-10 Table 12.12-1. Using the exible diaphragm assumption would allow distribution of diaphragm forces to shear walls to be based on tributary area. In 1999, the Structural Engineers Association of California Code and Seismology Committees recommended that relative exibility requirements outlined in ASCE 7 Section 12.3.1 be considered for wood framed diaphragms. 12.3.1 Diaphragm Flexibility e structural analysis shall consider the relative sti nesses of the diaphragms and of the vertical elements of the seismic forceresisting system. Unless a diaphragm can be idealized as either exible or rigid in accordance with Sections 12.3.1.1, 12.3.1.2 or 12.3.1.3, the structural analysis shall explicitly include consideration of the sti ness of the diaphragm (i.e. semi-rigid modeling assumption). Even though diaphragms may be idealized as exible, it is sometimes good engineering judgment to consider other exibility conditions. Currently, some designers only perform a exible diaphragm analysis and some a rigid diaphragm analysis, but a few use semi-rigid modeling (enveloping). On that basis, some confusion and lack of consistency exist regarding which type of diaphragm analysis should be employed for a given project. Verifying the
Wall element, hold downs and connections are designed for std. ld. Comb.
SW4 Wall element designed for std. ld. Comb.
Connections are designed for std. ld. Comb.
Support beam/collector V2
n olu m c o rt upp S
Concrete Podium slab
Conc. wall
Concrete beam Elements supporting discontinuous walls or frames require over-strength factor per Section 12.3.3.3
• Collector • Columns • Podium slabs • beam
SW5
Conc. wall Seismic reactions from the flexible upper portion shall be amplified by the ratio
> 1.0
for connections embedded into slab (does not apply to gravity reactions).
ASCE 7-10 Sections 2.3 or 2.4-Standard load combinations ASCE 7-10 Section 12.4.3-Over-strength factor load combinations
Figure 4. Discontinuous shear wall at podium slab.
VRf
H3
T3
V3rd
H2
Compression blocking
V2nd T2
H1 Discrete hold down system
T1 3rd Flr. SW C3
2nd Flr. SW C2
Rim joist
1st Flr. SW
∑M
C1 Wall displacement
Semi-balloon framing n g n i t u r r O v e Rod coupler Shrinkage Comp. Brg. Pl.
Crushing
Shear wall Deflection (Typ.) Shear wall boundary elements sta n ce
R es i Tension Side
Platform framing
Compression Side
Continuous tie rod system w/ shrinkage compensating devices
Figure 5. Typical shear wall components and summation of lateral forces.
diaphragm exibility is becoming increasingly more important given trends toward larger openings in exterior shear walls, shorter wall lengths, and a greater number of wood frame stories over the podium.
Shear Wall Design
Traditionally, shear walls are designed from oor to oor, assuming that they are pinned at the top and bottom at each oor, and the out-of-plane sti ness of the oor framing is rigid. e sum of the lateral forces from the walls above is transferred to the walls below as shown in Figure 5. Overturning forces are typically determined by dividing the sum of the moment applied at the top of the wall by the distance between the center of the tension anchoring device and the centroid of the compression boundary members. ese
overturning forces are cumulative to the foundation. Traditional shear walls must comply with the allowable height-to-width, (h/b), aspect ratios of the 2015 SDPWS, which can be found in Section 4.3.4 and Table 4.3.4. Where the aspect ratio is greater than 2:1, the nominal shear capacity must be adjusted to account for the reduced unit shear capacity in high aspect ratio walls due to the loss of stiffness as the aspect ratio increases. This can significantly affect multi-story shear wall stiffness and capacity. Two types of anchoring systems can be used as shown in Figure 5, discrete hold downs and continuous tie-rod anchoring systems. Continuous tie-rod systems with shrinkage-compensating devices are becoming the preferred method of anchoring for multiple narrow stacked shear walls because they account for vertical shrinkage at each floor level and provide better control over story drift. It is recommended that bearing plates, rod couplers and shrinkage-compensating devices be installed at each floor to provide a more efficient system and reduce story drift. As overturning forces develop, the bearing plates at the tension boundary members act to resist these forces causing bearing perpendicular-to-grain stresses and crushing at the bearing plate, sole plate, and top plates of the wall. The number of boundary studs on the compression side of the wall are often controlled by these stresses. Varying rod diameters help reduce rod elongation and wall rotation and produce a more efficient and cost-effective system. Shear wall deflections and story drifts are determined floor to floor. Traditional shear wall deflection is determined by calculation using the familiar three-part deflection SDPWS Equation 4.3-1, the four- part deflection SDPWS Equation C4.3.2-1 or equation 23-2 found in the 2015 IBC for stapled shear walls.
Δ bsw = + + 8vh3 EAb vh 1000Ga hΔa SDPWS Eq. 4.3-1
For SDPWS Equation 4.3-1, the first term represents the bending deflection resulting from the lateral forces applied at the top of the wall. The second term accounts for shear deflection and nail slip. The last term accounts for rigid wall rotation. Wall rotation for shear walls typically includes the consideration of rod elongation, anchor slip, and the crushing effects at the bearing plate and wall plates. Traditional methods of calculating wall deflection using the three- or four-part deflection equation do not account for multi-story shear wall effects on structures having more than three stories. New studies and discussions are taking place to consider including the effects of wall bending and rotation of the walls acting together as a unit, as will be discussed in Part 2 of this article.
Conclusion
Mid-rise structures using podium designs provide many opportunities for cost-effective, higher-density construction. It has become increasingly important to consider the relative stiffness of diaphragms and shear walls, and the effects of multi-story shear walls as buildings become taller and more complex in shape. Research, full-scale testing, and performance-based studies continue to evolve, which impact both changes to the building code and guidelines for engineers. Recognized, comprehensive guidelines and design examples providing in-depth coverage are available, demonstrating traditional methods of analyzing mid-rise and podium designs.▪
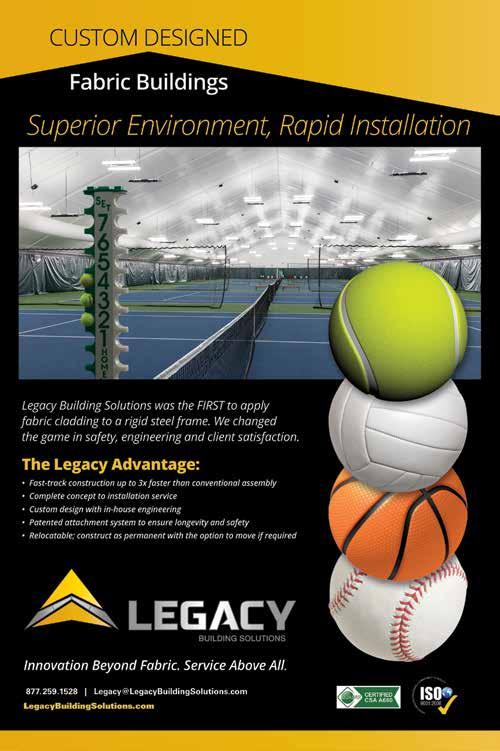