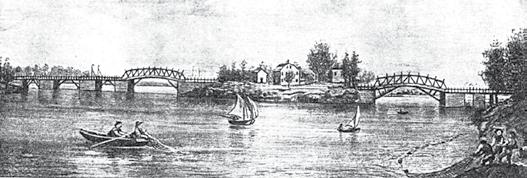
45 minute read
Historic Structures
significant structures of the past
Newburyport – Essex-Merrimack Bridge 1792, Newburyport on the right looking easterly.
This is the first in a series of articles on the historic bridges of the United States. It will include those bridges the writer believes were the most significant structures since 1793 built in wood, iron and steel. Up to then, most bridges built in the country were wooden pile and stringer bridges built in much the same manner as Caesar did when crossing the Rhine centuries before. Newburyport Bridge It remained for Timothy Palmer, a local architect and house wright, to build the first long span By Frank Griggs, Jr., Dist. M. ASCE, truss bridge in the country across the Merrimack D. Eng., P.E., P.L.S. River in Massachusetts. In 1790, Newburyport was a major port city, ranking 13th in population in the country, and was homeport to a large number of ships, brigantines, schooners and sloops. Several rope ferries crossed the Merrimack River in the area. The tolls from the ferries made them very attractive sources of revenue for their operators. Even though tides, seasons, and weather could make the journey across the river dangerous at times, ferries had met the needs of the traveling public. In 1791, a group Dr. Griggs specializes in the of local leaders proposed a bridge across the river restoration of historic bridges, at a point just upstream from the town where an having restored many 19th island split the river into two channels. A formal Century cast and wrought iron petition was submitted to the Massachusetts bridges. He was formerly Director legislature on June 1, 1791 asking for a charter of Historic Bridge Programs for to build the bridge. The petition stated “That Clough, Harbour & Associates a bridge across Merrimack River from a place LLP in Albany, NY, and is now an called the Pines in Newbury in the county of independent Consulting Engineer. Essex to Deer Island, so called, and from the Dr. Griggs can be reached at said Island to Salisbury in said County would fgriggs@nycap.rr.com. in the opinion of your petitioners very greatly subserve the public interest and convenience by affording a safe, prompt and agreeable conveyance to carriages, teams and travelers at all seasons of the year, and at all times of tide, whereas great dangers are incurred and great delays often suffered by the present mode of passing in Boats.” The act of incorporation was approved by the legislature on February 24, 1792 and was signed by Governor John Hancock with the signature identical to his Declaration of Independence signature 16 years earlier. The tolls were in part, • For each foot passenger two thirds of a penny. • For each horse and rider two pence. • For each horse and chaise chair and Sulkey seven pence. The bridge itself was described as follows:
And be it further enacted by the authority aforesaid that the said bridge shall be at least thirty feet wide; that between Newbury &
Deer Island there be an arch one hundred and sixty feet wide; that between Deer Island and Salisbury there be an arch one hundred & forty feet wide, a convenient draw or passage way for the passing and repassing of vessels at all times fifty feet wide with well constructed substantial and convenient piers on each side of the bridge & adjoining said draw sufficient for vessels to lie at securely; and also another arch fifty feet in width; and that the crown of the arch between Newbury and Deer Island be at the least forty feet high, and that each of the abutments thereof be twenty eight feet six inches high in the clear above common high water mark… By early April, the Directors evidently had many proposals consisting of drawings, models, and extensive descriptions of bridge styles. With a new, or enhanced, plan in hand, they decided that the original legislation was not acceptable and submitted proposed changes to the legislature. The revised act was passed on June 22, 1792, modifying the restrictions and limitations of the first act as regards height above high water mark, braces, etc. The legislature required that the bridge not impact negatively navigation on the river, and therefore set minimum vertical clearances and clear waterway distances between abutments and piers. The change evidently came about after Timothy Palmer was selected as chief engineer of the bridge. For this bridge and others, he has been called “the Nestor of American Bridge Builders.” The revised act stated in part,
Sect. 3 And be it further enacted by the authority aforesaid, That the crown of the arch to be erected between Newbury and
Deer Island may not be less than thirty-six feet high, and that each of the abutments
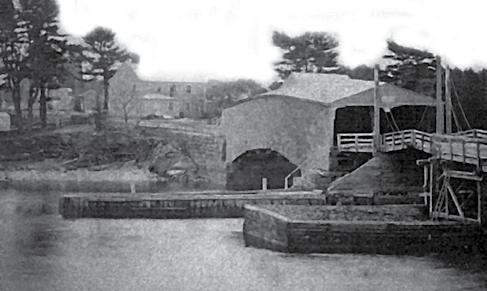
Salisbury Truss then covered, post 1808, with lift span looking south at Deer Island.
thereof may not be less than twenty-four feet and a half high, above common high water mark; and that braces or shores may be placed from the abutments of the said arch, at four feet and an half from common high water mark, to pass up to the said arch, at not more than forty-eight feet distance, from the top of the said abutments; any thing in the said Act to the contrary notwithstanding. averaged 34 feet deep? His bridge, most likely based upon a 16th century Palladio design, would have the longest span of any in the country at the time. A genius has been defi ned as someone who sees what everyone has seen but thinks what no one has thought. Th is phrase applies to Timothy Palmer, who began his bridge building career with this bridge. Early illustrations of the longest span show it with 10 panels of approximately 16 feet with a panel height equal to the panel length yielding compression diagonals on approximately a 45-degree angle. Palmer used what has been called by some a trussed or braced arch as his supporting system with the deck resting on the lower chord. How the truss/arch worked depended greatly on how the members were connected at the upper and lower chord and the stiff ness of the lower chord. If the lower chords Th e Massachusetts Magazine, May 1793, were very stiff , the structure would act more reported, “…this bridge was built, under the like a braced arch if they were built into the prospect of advantages much less encouraging, abutments that prevented longitudinal movethan any which have been granted by the leg- ment of the ends of the members. If the lower islature to undertakings of a similar kind…” chords were less stiff , and not anchored to What made Palmer, who, although an accomplished millwright and house wright, had never built a bridge, think that he could design and build a bridge over 1,030 feet long, the abutment, the whole structure would act more like a highly cambered truss with radial tension posts and compression diagonals. It is believed that the latter case was true. Tedds2013 Now available and packed with exciting new features with one span of 160 feet, over water that continued on next page
ADVERTISEMENT–For Advertiser Information, visit www.STRUCTUREmag.org
Introducing Tedds 2013, the next evolution in structural software
With Tedds 2013 you can now analyze frames, use a broad library of calculations, create high quality, transparent documentation, and even write your own calculations.
You can: You will:
Use a broad library of calculations Write your own calculations Work within Microsoft Word Analyze frames Produce transparent output Archive documents electronically Save time & increase profit Reduce calculation errors
Improve consistency Reduce overheads Enhance QA processes Go online to request your free Tedds trial
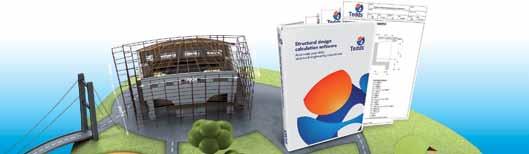
877 710 2053 (Toll Free) www.cscworld.com
#cscworldglobal
The foundations for the superstructure were probably stone filled wooden cribs that were Palmer’s standard foundation, sometimes with wooden piling and sometimes without. In the language of the day, they were called “huge log piers which extended far below the water line to a firm foundation of either stone, hardpan or gravel.” To build the arched lower and upper chords, he used what Theodore Cooper in his fine 1889 paper on railroad bridges called “crooked pieces of timber, so that the fibre might run in the direction of the curves.” Palmer ordered trees with a natural bend in them to match the curvature of his chords. Some of these timbers, in his later bridges, were 16 x 18 inches in cross section and up to 50 feet long. As seen in the engraving of the bridge, he used struts off the piers extending out several panel points to help support his trusses as permitted by the modified Act of the Legislature. His spans, piers, and abutment lengths working from the northerly shore (the Salisbury shore) were 124 feet, 50 feet, 45 feet, 60 feet, 50 feet, a 40-foot draw structure, 50 feet, his arch of 113 feet, and 60 feet to the northerly shore of the island. The bridge then ran from the island 93 feet, his truss of 160 feet, and 185 feet on piers and deck beams to the Newburyport shore. Shortly after the opening of the bridge in 1793, The Massachusetts Magazine wrote, “The two large arches, one of which is superior to anything on the continent, were both invented by Mr. Timothy Palmer, an ingenious house wright of Newburyport, and appear to unite elegance, strength and firmness beyond the sanguine expectation.” In the book Olde Newbury, the author states, “The principles upon which it was constructed were novel and hitherto untested; but the beauty and strength of the structure, when completed, demonstrated their practical value and utility.” The bridge opened in December 1793, but the official opening ceremony was on July 4, 1794. What we know about some of the early wooden bridges in the country came from travelers who wrote about what they had seen on their trips around the country. Timothy Dwight, President of Yale University, wrote about the EssexMerrimack Bridge (he also wrote that the bridge was painted a brilliant white):
Between Salisbury and Newbury the
Merrimack is crossed on Essex Bridge…It consists of two divisions, separated by an island at a small distance from the southern shore. The division between the island and this shore consists principally of an
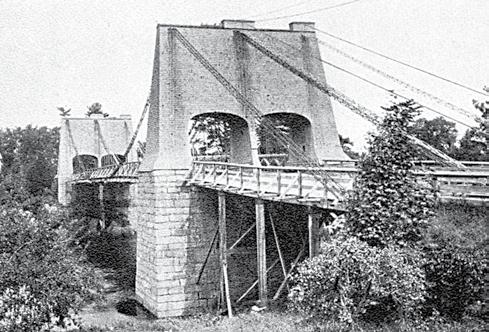
Templeman Chain Bridge 1810-1909. arch, whose chord is one hundred and sixty feet, and whose vertex is forty feet about the high water mark…the whole length of Essex Bridge is one thousand and thirty feet, and its breadth thirtyfour. I have already mentioned that Mr.
Timothy Palmer, of Newburyport, was the inventor of arched bridges in this country. As Mr. Palmer was educated to house building only and had never seen a structure of this nature, he certainly deserves not a little credit for the invention...The workmanship of the
Essex Bridge is a handsome exhibition of neatness and strength.” Another description by John Drayton, who saw the bridge shortly after it opened, gives a little better description of the long span as follows:
Two or three miles beyond Newburyport is a beautiful wooden bridge of one arch, thrown across the Merrimac River, whose length is one hundred and sixty feet; and whose height is forty feet above the level of high water. For beauty and strength, it has certainly no equal in America, and I doubt whether as a wooden bridge there be any to compare with it elsewhere. The strength of the bridge is much encreased above the common mode in use by pieces of timber placed upon it and shouldered into each other. They run upon the bridge in three lines, parallel with the length of the bridge and with each other, so as to make two distinct passageways for carriages. These braces are some feet in height, and are connected on the top by cross pieces affording sufficient room for carriages to pass underneath without
inconvenience. It is said that the upper work has as great a tendency to support the weight of the bridge as the sleepers upon which it is built… Palmer, in a letter to Richard Peters in Philadelphia dated July 11, 1808, wrote, “Last summer, I rebuilt one of the Arches, the span of which is 113 feet and is on the same principle with your Bridge. With much persuasion, I obtained liberty to cover it. There were many doubts in the minds of the Stockholders as to its stability against strong winds.” This covered span survived until 1882. In the same letter, Palmer informed Peters that on “the 17th of June last there came on one of the most tremendous gales of wind ever known in this country…The reason of my being thus particular in this reason is Essex-Merrimack bridge stands nearly in the centre of the direction of this tempest; and stood like Mount Atlas amid the warring elements.” In 1810, John Templeman, using a variation of James Finley’s chain suspension bridge patent, built a chain suspension bridge to replace Palmer’s 160-foot truss. This span had been, in the words of the boatmen, a “menace to navigation.” By going with a 244-foot suspension span as contrasted to a 160-foot truss with abutments extending greatly into the river, it was possible to widen the southerly passage around Deer Island. This bridge, even though suffering a partial collapse in 1827, survived until 1909 when a look alike bridge was built in the same location. This bridge, recently restored in 2003, still serves local traffic across the Merrimack River. It is the oldest continually occupied, long span, bridge crossing (220 years) in the country dating from 1793.▪
A Composition of Dramatic Concrete and Steel Structures
By Sean Fleming, LEED AP BD+C, Jean Libby, P.E. and Paul Endres, FAIA, S.E.
Figure 1: The San Diego Central Library in March 2013.

When the newly built San Diego Central Library opens its doors in autumn 2013, it will be a landmark project for both the City of San Diego and the project’s design and construction teams alike. The project presents multiple unique challenges in its many unique structural frame components, most of which are architecturally expressed with minimal treatment. Prevalent among the structural design elements are the cast-in-place architectural concrete frame beams and columns, exposed concrete waffle slabs, and the iconic steel and aluminum dome structure that provides shade and acclimatizes the eighth floor main reading room. The project encloses 504,000 square feet on its nine above-ground floors and includes reader seating for 1,200 persons, 407 computer stations, 22 wifi-enabled study rooms, meeting rooms and gallery/ exhibition spaces. The site is also home to a new 350-seat community auditorium building. Two subterranean levels provide parking for 250 autos. The project targets a LEED Silver certification. Figure 1.
Special Moment Resisting Frame
Selection of vertical and lateral load-resisting systems for the library is dictated in good part by the building’s use. Programmatic requirements for an open and versatile floor plan with natural daylighting, heavy live loads, and the necessity for perimeter retaining walls below grade lend to employment of a reinforced concrete special moment-resisting frame (SMRF) above grade and reinforced concrete shear walls below grade. Sizing and shapes of SMRF columns are dependent on their location in the structure and on architectural considerations. Moment frame columns occur at the perimeter of the ninth floor, trace down through the structure, and continue below grade to retain ductile detailing to the foundation level. Frame columns and frame beams are also introduced along different lines as the footprint of the floors increases top-down. SMRF columns prevail at 75 inches (1.9 meters) square, but grow to as large as 72 x 92 inches (1.8 x 2.3 meters) in the reading room and east colonnade. Typical moment frame beams are upturned 5 feet (1.5 meters) deep by 27 inches (0.7 meters) wide. Locating the SMRF columns and beams along the perimeters of the floor plates allows the interior of the floors to be supported by smaller gravity columns, which supports the design intent of an open floor plan. Gravity columns are minimized to 34 inches (0.9 meters) square below grade and 30 inches (0.8 meters) square above grade. Figure 2.
Waffle Slabs
The building is designed for a minimum live load of 150 pounds per square foot (psf) at and above the ground level, with limited areas to receive compact shelving designed for 300 psf. The nearly 350,000 square feet of typical floors employ a 23-inch (0.6 meter) thick waffle slab with waffle voids spaced four feet (1.2 meters) on center. The decision for waffle slabs also accommodates the 32-foot (10-meter) wide column bays. The aesthetic of the waffles as viewed from below, as an exposed ceiling, is architecturally appealing and also possesses sound-attenuating properties. Strategic use of in-slab beams, combined with upturned frame beams at the floor plates’ edges, allows maximum daylighting of the interiors via clerestory glazing set between the upturned beams and waffle ceiling soffits. Typical floor to floor heights are 15 feet (4.6 meters).
Heat of Hydration Issues
Heat of hydration was a very real concern, since many concrete frame elements are in excess of six feet square and the concrete gravity arch
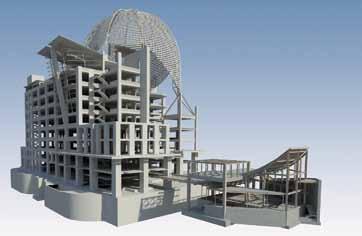
Figure 2: All structural and architectural components were modeled, coordinated, and 4-D scheduled thru Revit, Vico, and Synchro. Courtesy of Turner Construction.
reaches dimensions of thirteen feet radially by six feet wide. Initial mock-ups using the specified cement resulted in internal curing temperatures exceeding 250 degrees F in the first 24 hours. This exceeded the maximum allowable internal curing temperature of 180 degrees – the upper threshold established for control of thermal cracking and ensuring the long-term durability of the concrete. Additional trial batches were ordered to test heat characteristics and compressive strengths of mixes utilizing alternate architectural grade cements. While the alternate trial batches continued, nine mockups were performed to test non-technical heat mitigation strategies. Non-technical controls included placing mass concrete elements as early as possible in the morning to take advantage of low ambient temperatures, batching concrete with chilled water or ice depending on the season, and limiting concrete deliveries to five cubic yards per truck for the largest components. The non-technical strategies were found to effectively maintain concrete consistency between lifts without the need to introduce water at the jobsite – critical to achieving uniformity of color in the finish product. A single mix design of 6,000 psi concrete using locally available Colton, California Type-I cement and a set-retarding admixture was selected, and is employed for all architectural concrete applications within the building.
Architectural Concrete Aesthetic
The program calls for all above-grade concrete to be architectural ascast and fair-faced, utilizing a high albedo architectural grade cement and incorporating an ACI Class A finish. Chief among the preferences for the concrete aesthetic are a light colored matte finish, minimal appearance of forming hardware, and a custom pattern that calls for plywood to be cut to random sizes and oriented to create an organic “quilted” effect. Slight imperfections and offsets are desirable to create an aged appearance. The combined application of mass concreting issues and architectural concrete program requirements resulted in a series of fifteen mock-ups and other research and development efforts to test cement options, concrete mix designs, plywood types, tie design strategies, form releases, and rustication strips. Structural concrete and non-structural concrete components employ different treatments as a visual telling of their role in the building. Ties are located in structural elements at wide spacings on a static series of datums: 5-foot on center (o.c.) vertically and 4-foot o.c. horizontally. A tighter tie spacing ranging from 2-foot o.c. to 4-foot o.c. is applied to non-structural concrete depending on the application. To achieve the vision of a quilted aesthetic, hundreds of concrete shop drawings were translated from the BIM model (Figure 2) to account for every plywood seam and tie-hole in all exposed columns, beams, edges of slabs, and walls as well as in custom structures such as the concrete gravity arch. Due to the complexity and non-repeating nature of the plywood patterns, an unusual step was needed: the creation of formwork fabrication and placing drawings. These drawings were provided to field crews to assist with prefabrication and production in placing formwork. For example, each column form incorporated the deliberately located random patterns into the fascia sheeting, each with wholly unique seam layouts, such that no two were alike. Since forms had to be reused throughout the structure, placing drawings included production notes to assist field crews with a pre-planned strategy to “mix-up” the stock of forms, or rotate column forms from their prior axial orientation, from one pour to the next to further give the allusion of random, non-repeating patterns in the concrete. The regular pattern of the ties, juxtaposed with the scattered seams of plywood sheeting, creates a unique craftsmen quality in the finish product.
Energy Efficiency
As-cast architectural concrete contributes to energy efficiency by minimizing capital costs compared to other building finish systems since surface treatments involve only minor touch-up. The reduced expense for finish systems also translates to reduced maintenance and life cycle costs for the Owner. End-user energy demand is reduced significantly by way of the structure’s concrete envelope and its inherent thermal mass, which reduces day-time cooling needs and evening warming of the interior spaces. Aluminum sunshades on south and east facing clerestory windows further mitigate daytime heat gain.
Concrete Gravity Arch
An open feeling was desired at the library lobby, so a 64-foot (20meter) long by 46-foot (14-meter) tall concrete gravity arch (Figure 3) was designed from the ground level to the fourth floor, eliminating a column from the center of the lobby. Congestion of reinforcing steel at the two ends where the arch was to be supported by vertical columns proved a challenge. Couplers and headed bars were utilized here and in many other locations where congestion was problematic to constructability. continued on next page
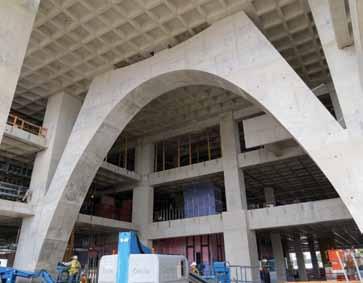
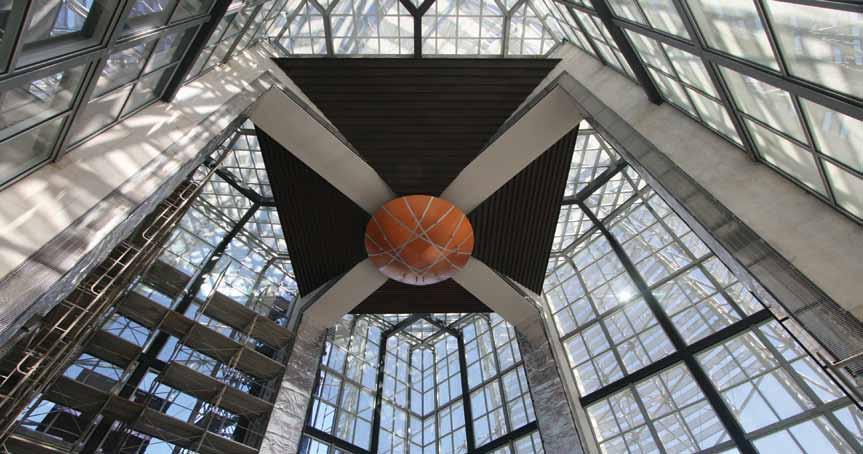
Figure 4: Interior of the 8th floor reading room.
Reading Room
A concrete roof suspended sixty feet (18 meters) above the eighth floor shelters the library’s 4,000 square foot reading room (Figure 3). Structural steel and clerestory glass supported by four 72-inch square concrete columns complete the room. The concrete columns, cruciform in plan, rise 62 feet to support intersecting concrete roof beams spanning 58 feet in either direction and the diamond-shaped concrete roof slab (Figure 4).
Special Events Room
The Special Events Room roof cantilevers 10 feet from the 9th floor deck and is made up of a hybrid system of precast beams laced into a 6-inch cast-in-place concrete slab. The roof is supported by a single 72-inch x 48-inch inclined concrete column, which begins its rake nearly 90 feet below between the 4th & 5th floors (Figure 4). The flanks of the roof structure are supported in part by tubular steel mullions set prior to casting the roof slab (Figure 5).
Project Team
Owner: City of San Diego Engineer of Record: Martin & Libby Structural Engineers – San Diego, CA Dome Engineer: Endrestudio Architecture & Engineering – Emeryville, CA Design Architect: Rob Wellington Quigley, FAIA – San Diego, CA Architect of Record: Tucker Sadler Architects – San Diego, CA General Contractor: Turner Construction – San Diego, CA Concrete Contractor: Morley Construction – San Diego, CA Dome Contractor: SME Steel – West Jordan, UT
Dome
The dome, believed to be the largest steel post tensioned segmental dome in the world, is 140 feet (43 meters) in diameter and rises 221 feet (67 meters) above ground level to provide shade and acclimatize the reading room. It is constructed of more than 3,000 individual members of steel, weighing 285 tons, and clad in 1,500 perforated aluminum panels to shade the eighth floor reading room beneath it. The dome is made up of eight unique truss “ribs” that rise from base to apex in varying heights from 72 to 113 feet (22 to 34 meters) and eight unique “sail” structures located between the ribs. Sails are oriented in plan with a pinwheel configuration, an effect created by offsetting each of the sails’ vertical leading edges to the outside of the ribs while the sails’ trailing vertical edges are connected to the inside rib surfaces. Each of the sails has an external pipe grid that is spherical at the upper part of the dome; however, the spheres are tipped vertically and horizontally so the center of each sail does not coincide with the center of the dome. Unfurled, the largest sail is 123 feet by 53 feet (38 by 16 meters) wide and comprised of 175 members of tubular steel and 60 cable segments. Architecturally, the lower edges of the sails are desired to be as thin as possible. This is achieved through the use of a three-dimensional truss spanning diagonally from rib to rib, and appears visually as a six-inch (15 centimeter) edge thickness. To further reduce the mass of the sails, steel cables are introduced to minimize large members on the interior surfaces close to the glass of the reading room. The penultimate concept, with cables covering the outer and inner surface, was deemed too difficult to erect by the contractor. The final design, a saddle shaped cable net, was chosen because the removal of cables on the outer surface allowed the contractor to erect them by crane more easily. The sails were constructed on-site, two at a time, on large temporary platforms on the ground and lifted into place, one sail at a time. Due to the discontinuous circular form and its peaked pinnacle, the dome behaves as a series of intersecting three hinged arches, or “ribs”. At the base, each rib is supported on a large fixed pin that allows the rib structures to pivot or expand with changes in temperature or seismicity.
Each of the eight large pins falls onto one corner of a fi xed octagonal plan. Th e octagonal plan causes unequal geometry from rib to rib. Th e fi xed pins of the rib supports fall onto varying elevations located atop shear walls, freestanding columns and, in one case, supported by three inclined converging columns. Two of the rib supports fall outside the building envelope and are built on special composite braces made up of concrete columns with tubular steel diagonals.
A Place of Inspiration and Learning
Th e San Diego Central Library is poised to serve its community as a center of knowledge and learning through its planned 1.5 million volumes, internet access terminals, numerous literacy programs, staff , volunteers, and other contributors. Th e design and construction team believe it will also contribute to the city’s character as an iconic structure and landmark. Th e expressive and often dramatic applications of architectural concrete and steel discussed here are intended to inspire the minds of the library’s population, be they children or adults, students or working class, rich or poor.▪ Sean Fleming, LEED AP BD+C, is a Senior Project Manager at Morley Construction in San Diego, California. Sean may be reached at s eming@morleybuilders.com. Jean M. Libby, P.E., is Principal and President of Martin & Libby Structural Engineers in San Diego, California. Jean may be reached at jlibby@libby-lei.com. Paul Endres, FAIA, S.E., is Principal and President of Endrestudio Architecture & Engineering in Emeryville, California. Paul may be reached at paul@endrestudio.com.
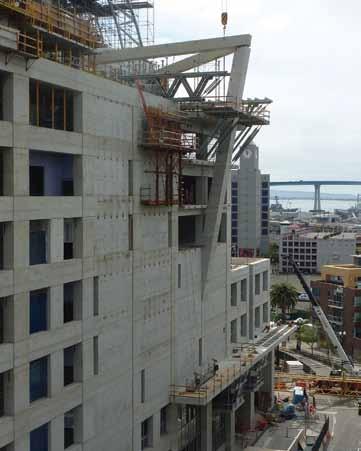
Figure 5: A 90-foot tall inclined column supports a hybrid cast-in-place and precast concrete roof deck at the 9th fl oor.
ADVERTISEMENT–For Advertiser Information, visit www.STRUCTUREmag.org
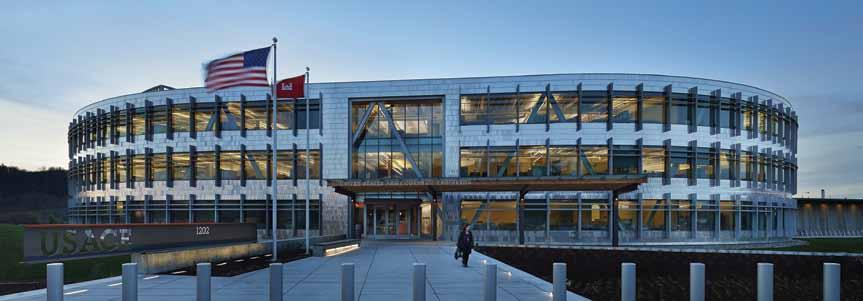
Diagrid on Display
Federal Center South Building 1202
Federal Center South Building 1202, the new headquarters for the United States Army Corps of Engineers in Seattle, Washington. Courtesy of Benjamin Benschneider.
By Daniel Riemann, P.E. and Jason Black, P.E., S.E.
This is the second article highlighting the innovative design features of Federal Center South Building 1202. “A Worthy Wager: The Innovative Use of Composite Concrete & Timber Floors on Federal Center South” was featured in the April 2013 edition of STRUCTURE.
The recently completed Federal Center South Building 1202, serving as the Seattle District Headquarters for the United States Army Corps of Engineers (USACE), is a state-of-the-art office building resulting from architectural, structural, and construction innovation and collaboration. One of the key features that makes Building 1202 so innovative is the use of a diagrid system at the exterior wall of the structure. While the diagrid is a system used in many new buildings around the world, its use in Building 1202 represents a clever solution to meeting the specific requirements of this design-build project. Utilizing this unique structural system strengthens the building while reducing material costs and shortening the construction schedule. Building 1202 was planned, designed, and constructed in less than two and a half years, and stayed within the original $65 million construction budget. In addition to being an effective solution to progressive collapse requirements, the diagrid played an important role during the competition phase of the design-build project and it was a significant part of the architectural expression and story of the building.
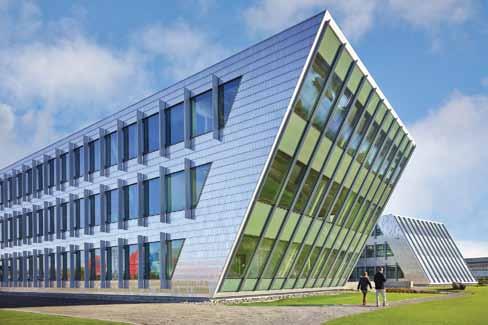
Diagrid Defined
A diagrid system consists of sloping columns (diagonals) and spandrel beams (horizontals). The diagrid system for Building 1202 utilizes a 3-story module (full building height) with bolted connections between spandrels and diagonals. Effectively, the diagrid system is a multi-story truss with pin connections. This system creates an efficient and inherently redundant structure by carrying gravity loads to the foundation through multiple load paths.
Progressive Collapse Requirements
As a U.S. General Services Administration (GSA) project, one of the primary requirements for Federal Center South Building 1202 was that the structure be designed to resist progressive collapse in the event of a terrorist attack. Progressive collapse is the uninhibited spread of an initial local failure to other elements of the structure, eventually resulting in the collapse of the entire structure or a disproportionately large part of it. Examples of progressive collapse include the collapse of the Alfred P. Murrah Federal Building in Oklahoma City, when localized structural damage caused by an explosion spread throughout the gravity load carrying system, eventually resulting in the collapse of a large portion of the building. Building 1202 is designed to the requirements outlined in UFC 4-023-03, Design of Buildings to Resist Progressive Collapse. The goal of this design document is to limit the number of casualties by ensuring that buildings have adequate inherent redundancy to continued on page 36
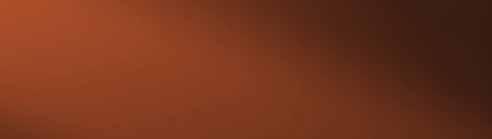
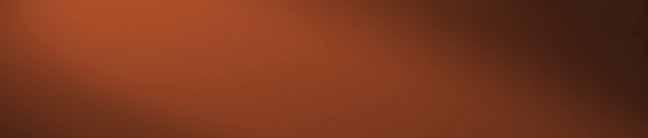
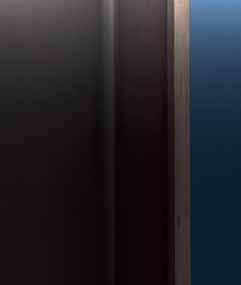
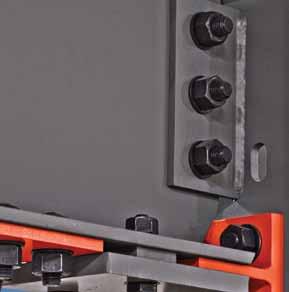
What Gives?
The patented Yield-Link™ structural fuse, that's what.
As the latest innovation from Simpson Strong-Tie, the Strong Frame® special moment frame features four Yield-Link structural fuses that eliminate lateral-beam bracing and are replaceable after a major seismic event. What’s the advantage? It’s easier to specify and it can save building owners signifi cant cost. As with our other moment frames, there is no welding, only bolted connections. Learn more by calling (800) 999-5099 or visiting www.strongtie.com/smf.
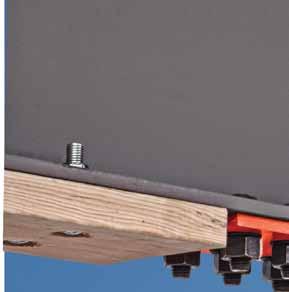
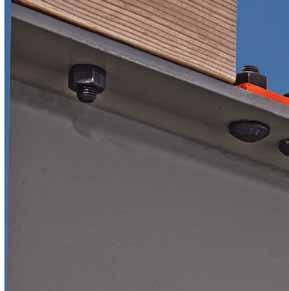
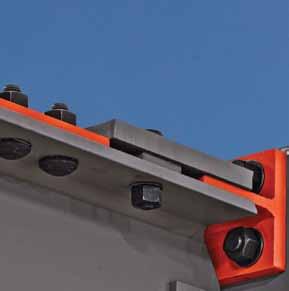
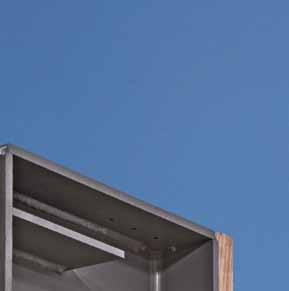
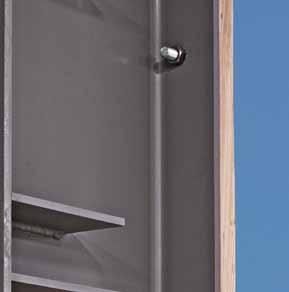
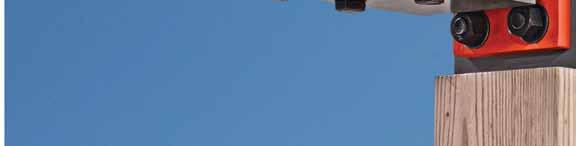
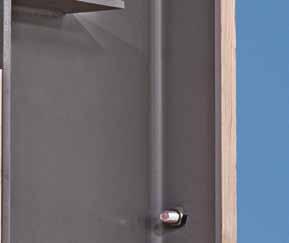
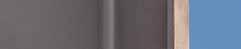
Method Description Tie Force Structural elements are designed and detailed as catenary elements to transfer loads through tension to undamaged portions of the structure. Alternate Path Structural elements are designed and detailed to bridge over compromised portions of the structure. Enhanced Resistance Shear and fl exural capacity of exterior structural elements are increased to minimize the extent of initial damage.
resist catastrophic damage due to unforeseeable events. Th e requirements for progressive collapse design provided in UFC 4-023-03 apply only to buildings which are three stories or taller. Th is three story requirement is based on a maximum casualty threshold set by the UFC and not the mechanics of progressive collapse. Th e level of progressive collapse design is based on the Occupancy Category (OC) and building function. Similar to the OC determined using the IBC, greater risk is associated with loss of structures of higher OC. Th is OC dictates which method of progressive collapse resistance is to be used in design. Th e three methods of progressive collapse resistance prescribed in UFC 4-023-03 are the Tie Force Method, Alternate Path Method, and Enhanced Resistance Method (see Table). Traditionally, requirements for progressive collapse resistance have been met by utilizing moment frames or tie beams at the exterior of the building, or by increasing member sizes to provide enhanced resistance. However, for Building 1202, a diagrid was chosen as the primary collapse prevention system. Th e diagrid is supplemented by moment frames at the canted building ends. Th e diagrid system is an optimal solution for meeting collapse prevention requirements because it is essentially a multi-level truss, with the diagonal columns acting as the web members and the horizontal spandrels at each fl oor acting as the truss chords. Th e 3-story diagrid module used for Building 1202 creates a 3-story truss. Should any of the diagonal columns become damaged during an attack, the remaining portions of this truss can span over areas of localized structural damage.
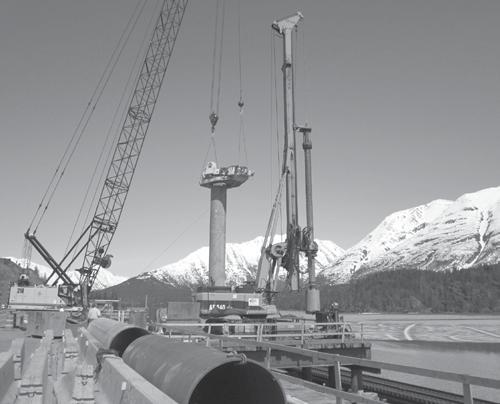
Design/Build Earth Retention Foundation Support Slope Stabilization Ground Improvement Dewatering
800-562-8460 WWW.DBMCONTRACTORS.COM Donald B. Murphy Contractors, Inc.
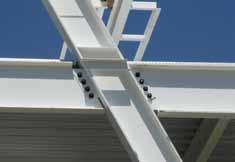
Typical bolted connection.
Diagrid Use as Potential Lateral Force Resistance System
Th e sloped columns of the diagrid are representative of braces in a braced frame. For this reason, the diagrid system was initially explored for use as the lateral system of the building. However, there are drawbacks when utilizing the diagrid as the lateral system. A braced frame is designed to yield and dissipate energy during a seismic event. As the primary gravity load carrying system for the exterior of the building, the sloped columns could not be allowed to yield during a seismic event. Accordingly, the building code requires that systems acting as both the primary gravity and lateral force resisting systems be designed to remain elastic during a seismic event. Th erefore, the response modifi cation factor, R, is required to be in the range of 1.0 to 1.5 to achieve essentially elastic behavior.
At the schematic stage, the diagrid for Building 1202 was analyzed and designed for seismic forces associated with this level of elasticity. For an R of 1.0, member sizes were reasonable, only slightly larger than those required for collapse prevention, and maximum drifts were within the code requirements.
However, the number of bolts required for connections increased signifi cantly when design overstrength factors were considered. Using bolted connections as much as possible was preferred by the contractor in order to maintain a rapid fabrication schedule and save costs associated with full penetration welds. Th e labor costs associated with the increased number of bolts that were required to allow the diagrid system to also meet the lateral system requirements eff ectively mitigated the cost advantage of having a dual system. Ultimately the decision was made to rely on concrete shearwalls at the stair cores as the lateral system for the building, thereby allowing both the lateral and gravity systems to be optimized both in terms of performance and cost.
ROOF LEVEL
LEVEL 3
LEVEL 2
LEVEL 1 (GRADE)

Diagrid system.
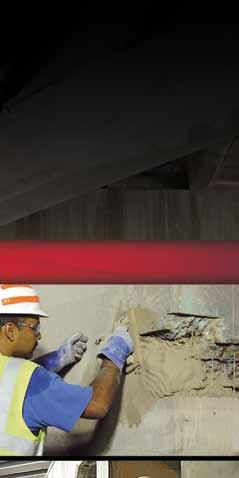
PILE FOUNDATION
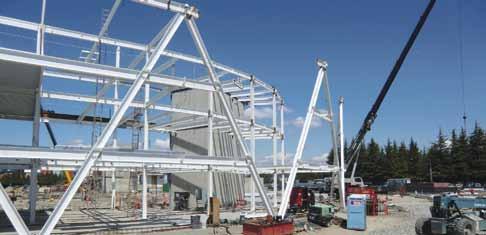
Diagrid erection.
Construction Savings

At the onset of the project, the team developed a progressive collapse resistance scheme utilizing moment frames, to compare to the diagrid scheme. Th is moment frame option consisted of 3-story moment frames at the building perimeter on a 22-foot bay module. From early studies, it was clear that the diagrid scheme provided the greater savings potential for the project in terms of foundations, materials, and fabrication.
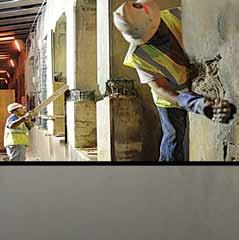
Foundations Building 1202 is located adjacent to the Duwamish River on extremely poor soils, requiring that the building be supported on driven steel pipe piles. Th ese piles typically extend 150 to 170 feet below grade to reach a competent bearing layer. In the moment frame scheme, a single pile is required at each moment frame column, or every 22 feet. In contrast, the diagrid system utilizes a 44-foot bay module, meaning that pairs of sloped diagonal columns meet grade every 44-feet. Th erefore, the moment frame scheme would have required twice as many piles at the perimeter of the building. Material Savings Th e diagrid system results in approximately 30% savings in steel tonnage as compared to a moment frame system. Th is savings is manifested largely in the spandrels, which become primarily tension/compression members when the diagonal columns become compromised. Th e spandrel beams in a traditional moment frame system need to resist much larger fl exural demands in order to span over damaged columns, requiring larger, heavier spandrel sections.
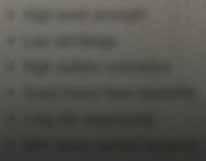
Erection and Fabrication Recognizing the old “time is money” axiom, KPFF worked with Sellen Construction to propose a simple “tilt-up” method for erecting the diagrids. In this sequence, pairs of sloped columns were fi tted up while on the ground and welded together at the apex to form a triangular assembly, which was then tilted in to place. Th e horizontal spandrels were then fl own in and bolted in to place. Th is sequence allowed the diagrids, and therefore the entire steel skeleton, to be erected in a relatively short amount of time. continued on next page
CONSTRUCTION CEMENT FASTER
STRONGER MORE DURABLE 3000 PSI IN 1 HOUR
Speci ed Worldwide
ADVANCED TECHNOLOGY
• High bond strength • Low shrinkage • High sulfate resistance • Great freeze thaw durability • Long life expectancy • 65% lower carbon footprint
Available in Bags and Bulk
800-929-3030 ctscement.com
Owner: General Services Administration (GSA) Tenant: United States Army Corps of Engineers (USACE) Seattle District Structural& Civil Engineer: KPFF Consulting Engineers Contractor: Sellen Construction Architect: ZGF Architects, LLP Funding: American Recovery and Reinvestment Act (ARRA)
When compared to a moment frame, a diagrid system requires far fewer welded connections. For Building 1202, there are 19 apex connections where field welding is needed. Bolted connections are used at all other spandrel to diagonal column connections. By comparison, the moment frame scheme studied by the team would have required a total of 108 full penetration welds at all connections between spandrels and columns – more than five times as required for the diagrid system.
Architectural Expression
One of the key early design decisions by the project team was to have the structure of the building exposed to the western
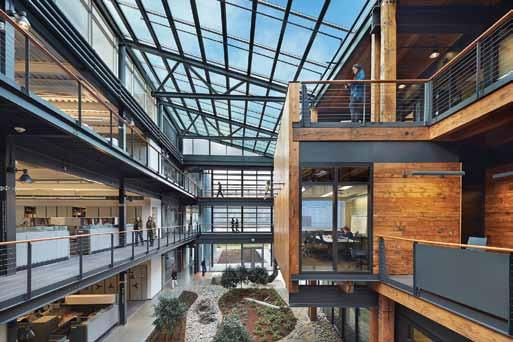
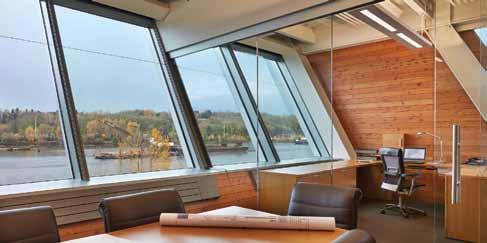
Conference room at canted end. Courtesy of Benjamin Benschneider.
river-facing view as much as possible, to reiterate the Corps’ mission statement of “Building Strong”. The diagrid, by its very nature as a strong diagonal element that contrasts with the orthogonal lines of floors, walls, and windows, is a key element of this expression. The design team moduled the building so that the diagrid naturally ended with a backslope on the southwest corner and an outslope on the northwest corner as a counterpoint. These canted ends of the buildings create light filled office and conference room spaces with sweeping views of the Duwamish River. The diagrid is painted white throughout in
USACE FEDERAL CENTER SOUTH BUILDING 1202 / PHOTO BY BENJAMIN BENSCHNEIDER
Seattle • Tacoma • Lacey • Portland • Eugene • Sacramento • San Francisco • Walnut Creek • Los Angeles • Long Beach • Pasadena • Irvine • San Diego • Boise • Phoenix • St. Louis • Chicago • New York order to assist in diffusing both natural and artificial light inside the building, but also to be prominently visible through the exterior glazing. The stainless steel skin of the building is peeled back at the main entry to fully expose the diagrid, creating a formal entry portal. The diagrid scheme also allowed the building’s unique Oxbow form to be achieved, which drew inspiration from the historic meandering path of the Duwamish River adjacent to the site. Smooth transitions through the curved portions of the building are facilitated with the diagrid by utilizing a tangential variation at each floor line. This allows the exterior skin to easily transition through the corners of the U-shape, resulting in a smoother appearance. Although the use of sloping columns results in a small loss of floor area directly under the column, the diagrid creates unique and dynamic interior spaces.
Summary
The diagrid represents an effective solution to progressive collapse requirements and helps create an iconic identity for Building 1202. The success of this designbuild project is a tribute to the early-on collaboration between the architect, engineer, and contractor.▪
Daniel Riemann, P.E., is a project engineer with KPFF Consulting Engineers in Seattle, W.A and was the lead designer for the diagrid system for Building 1202. Dan can be reached at Dan.Riemann@kpff.com. Jason P. Black, P.E., S.E., is a Structural Principal with KPFF Consulting Engineers in Seattle, W.A. Jason can be reached at Jason.Black@kpff.com.
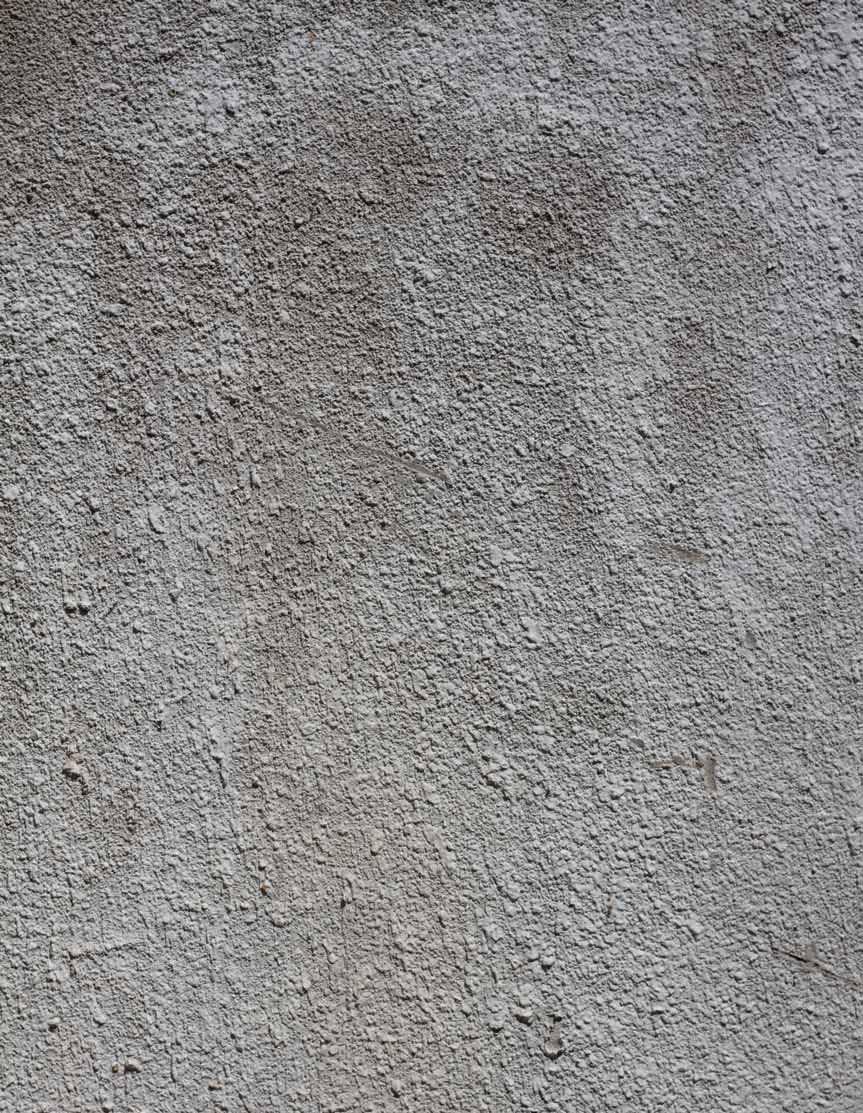
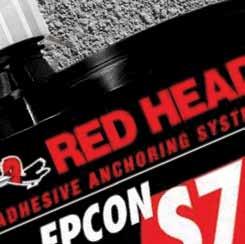
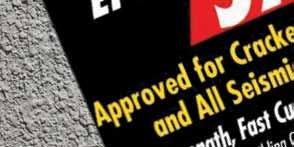
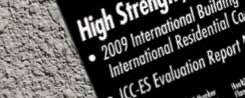
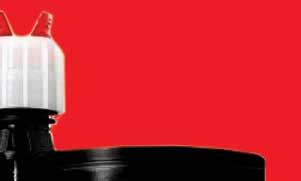
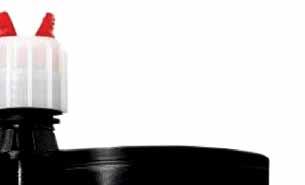
John Jay College Expansion
Transforming a 21st Century Urban College Campus New York, NY
By Jason Stone, P.E.
The CUNY John Jay College School of Criminal Justice Expansion Project is a new 625,000-square foot academic building in Midtown Manhattan. The facility consists of a 15-story tower on 11th Avenue and a four-story podium with a garden roof that connects to the College’s existing Haaren Hall on 10th Avenue. Following significant growth in criminal justice interest over the last decade (partially in response to the attacks of September 11th) the new building was planned to accomplish a doubling of the existing facilities and unification of the campus into one city block – creating an academic city within a city. In explaining the design concept, Abadan Mustafa of SOM said, “Criminal justice is not something that should be hidden away. Glass makes the relationship to inside and outside clearer. It relates to our ideals of transparency and justice, the way justice is applied to everyone equally and openly.” The new facilities offer traditional college campus amenities including classrooms, offices, research laboratories, theaters, lounges, and flexible collaboration spaces. In addition, unique features specific for future investigators and law enforcement officers include a ballistics room, areas for chemical storage and analysis, mock trials, and an emergency control center simulation lab.
Site Challenges
In response to a shallow Amtrak tunnel that cuts through a corner of the site, the John Jay structural system is distinguished by a grid of rooftop trusses which hang the perimeter of eight floors below. This
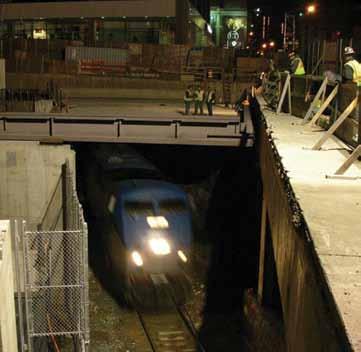
Construction over the tunnel was done at night and coordinated around the train schedule. Noise and vibration were controlled by isolating the tunnel enclosure from the tower structure. The 65,000-square-foot podium garden roof, known as ‘Jay Walk’ by the students, links the College’s existing Haaren Hall to the new tower on 11th Avenue and provides an oasis from the city below. Courtesy of SOM.
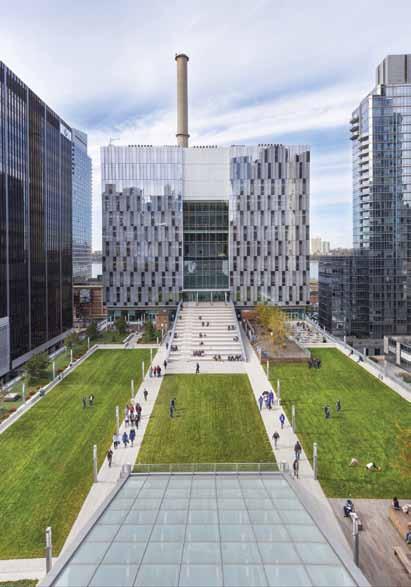
creates a dramatic column-free cafeteria space on the 5th floor, with views of the Hudson River for the full 195-foot width of the building. Two layers of structure were provided to effectively isolate the building from the train vibration and noise. The main building structure spanned over and behind the train tunnel, which was enclosed with a hollow core precast plank ceiling and concrete crash walls. At points of convergence, creative detailing was required to maintain the load path and necessary separation. Another challenge was accommodating the almost two-story change in grade between 10th and 11th Avenue. A second main entrance to the building occurs along 59th Street and negotiates this steep slope. To design for this condition, the perimeter columns – in an area that support heavy loads from the rooftop garden – were eliminated, and the entrance was pulled back to allow room for the necessary steps and ramps. Story-deep trusses were fit inside the walls of the 4th floor classrooms to efficiently accomplish the 40-foot cantilever out to the tip of a V-shaped tapering canopy. The interior architecture also responded to the sloped grade with a series of cascading staircases and escalators that complicated the structure, but allowed for fluid circulation to all parts of the campus. “The cascade replicates a miniature Manhattan, with the ‘travelers’ passing through different building functions and academic departments rather like the squares – Madison, Herald, and Times, among others – that bisect Broadway and function as independent nodes within the city,” Mustafa said. A large skylight
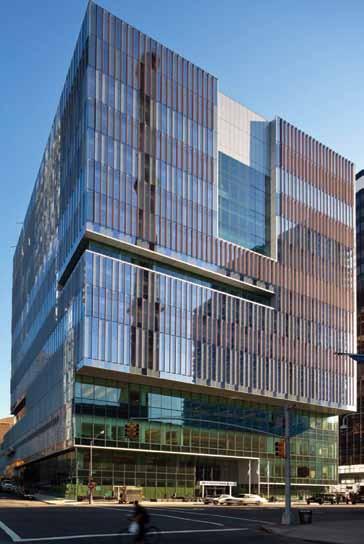
Main entrance on 11th Avenue. Setbacks in the façade were an important aesthetic feature that also reduced the impact of the load on the shallow train tunnel below. With the temporary columns removed, the load path for the hanging structure is clear. The column-free fifth floor cafeteria offers great views of the Hudson River to the west.
supported by architecturally-exposed narrow tube sections provides natural light into these main circulation areas and offers views into the space from the garden roof.
Hanging System
Accommodating the necessary two layers of structure around the train tunnel mandated a practical limit to the weight that could be supported. After exploring numerous options, the hanging solution was favored by SOM and DASNY and adopted for numerous reasons, including assistance in achieving the series of distinguishing setbacks that frame the west façade’s main entrance along 11th Avenue. The hanging system was continued around the full perimeter to balance the weight, complete the column-free aesthetic, and take advantage of the thin plate hangers which could fit inside a standard partition wall instead of traditional column enclosures. To maintain efficiency, the hanging system was stopped where the structure over the tunnel could accommodate conventionally-framed floor weight. In coordination with the architect, the 5th floor was chosen for this transition, allowing the transparent column-free floor to align with the podium roof garden. The primary construction challenge involved achieving approximately level floors when the building opened, and a 2-inch stack joint in the curtain wall at the transition floor between the conventionally framed and hung structure. To simplify the steel frame erection, the design accounted for temporary columns at the 5th floor around the tower perimeter and temporary angles bolted to the plate hangers above the 6th floor, to stiffen these elements during erection. This allowed the construction process to proceed similar to conventional construction, and maintain the project schedule. Once the truss assembly was finished, jacks at the temporary columns slowly lowered the building and engaged the trusses. At this point, the temporary columns and angles could be removed and concreting of the tower could begin. Calculating the required amount of vertical cambering for the perimeter steelwork in order to super-elevate each of the 26 hanger/column locations for the anticipated deflection during construction proved to be a challenge as well. Design estimates were based on the assumed construction schedule, estimated construction loads, and realistic modeling of the structural behavior. During construction, continuous surveying verified whether the perimeter was behaving as anticipated.
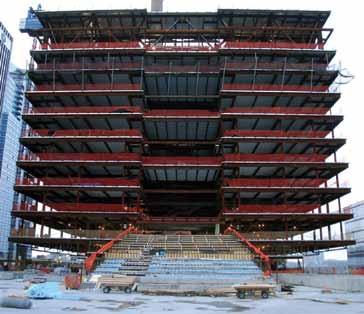
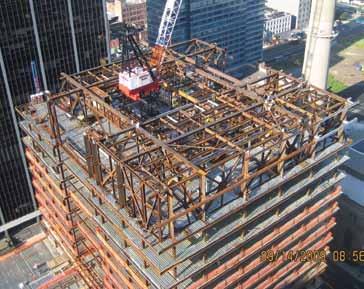
Owner: Dormitory Authority of the State of New York Client Team: City University of New York John Jay College of Criminal Justice Design Consultants: LERA – Structural Engineers Skidmore Owings & Merrill – Design Architect Turner Construction – Cost Estimator & Construction Manager Jaros Baum & Bolles – MEP Engineers Langan Engineering – Civil/Geotechnical Consultant Shen Milsom & Wilke – Acoustic Consultant Scott Blackwell Page Architect–Higher Education Planning Contractors: Owen Steel – Structural Steel Fabrication Cornell & Company – Structural Steel Erector Enclos Corporation – Curtain Wall Designer
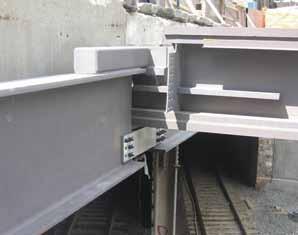
Once shop drawings were available for the nonstructural elements, and there was a better understanding of the schedule, a full reanalysis was done incorporating what was being learned from the surveying. This reanalysis revealed that it was likely the perimeter would not come down as much as originally thought (one reason for this being the curtain wall was actually 30% lighter than assumed in design) and field adjustments were made to lower the steel frame prior to starting the truss erection. Based on the last survey data received, this adjustment proved effective as the perimeter settling and final stack joint were tracking closely with the predicted behavior and targeted final thickness.
Future Expansion
While considered and subsequently ruled out during design, the College revisited the idea of future expansion during construction and decided this flexibility was important. The design team was asked to consider a design that allowed for an additional ten floors over the podium to raise this section to match the height of the new tower. At the time the decision was made, the podium structural steel
The easiest to use software for calculating wind, seismic, snow and other loadings for IBC, ASCE7, and all state codes based on these codes ($195.00). Tilt-up Concrete Wall Panels ($95.00). Floor Vibration for Steel Beams and Joists ($100.00). Concrete beams with torsion ($45.00).
Careful detailing at the train tunnel was required to isolate was already mostly fabricated and the caisson foundations were members supporting the precast tunnel enclosure from the main building structure. actively being drilled in some of the affected areas. than those that could be tolerated in the ceilAfter quick discussions focused on limiting ing package. The alternative solution, which the financial, schedule, and design changes, saved both material and depth, was to separate the College chose to reinforce only the the problematic excitation from the sensitive below grade areas and take advantage of a equipment, adding an isolation joint in the hanging structural system similar to the one floor between the labs and the adjacent main used in the tower to limit the affected area circulation corridor. to the interior core. Additional elevator pits In addition to efficient uses of material, with knock-out slabs were provided along the project specifications were written to be with significantly reinforced foundations environmentally sensitive. The building did based on the anticipated future circula- not officially submit to USGBC, but LEED tion and structural weight needs. Instead of certification requirements were pursued wherincreasing the column and vertical bracing ever feasible. Fly ash and silica fume were member sizes for the expected future loads, substituted for up to 30% of the cement in the additional capacity is intended to come the concrete. The reinforcing and structural from a high strength composite concrete steel were also sourced from mills regionally encasement, allowing the already fabricated close to NYC and produced from over 90% vertical members to still be used. recycled content.
Other Features
The 65,000-square-foot terrace atop the podium serves as a new, outdoor gathering place for students and faculty. The planted green roof is landscaped with large grassy zones, full-sized trees, and decked outdoor dining areas which the students immediately embraced and nicknamed
“Jay Walk”.
To preserve the dramatic views from the large collaboration areas in the tower of the Hudson River and this garden roof, the hanger spacing was increased to nearly 50-feet at the middle of both the east and west faces for the hung tower floors.
These long span conditions created a problem in the laboratories on the 6th , 7th, and 8th floors, where strict vibration criteria needed to be met. Stiffening the floor to control the expected excitations resulted in deeper and heavier members
Conclusion
The John Jay College Expansion project exceeded the expectations of owner and client, giving the students and faculty a new stateof-the-art home to be proud of, along with providing the College flexibility to adapt to whatever the future holds. The project success was due primarily to the collaborative efforts and superior skill of the design and construction team – in particular SOM, Turner, Owen Steel, and Cornell & Company – who also exceeded every expectation in realizing this special structural system.▪
Jason B. Stone, P.E., is a Senior Associate at Leslie E. Robertson Associates (LERA) and an Associate Adjunct Professor of Architecture at Columbia University. Jason can be reached at Jason.Stone@lera.com.