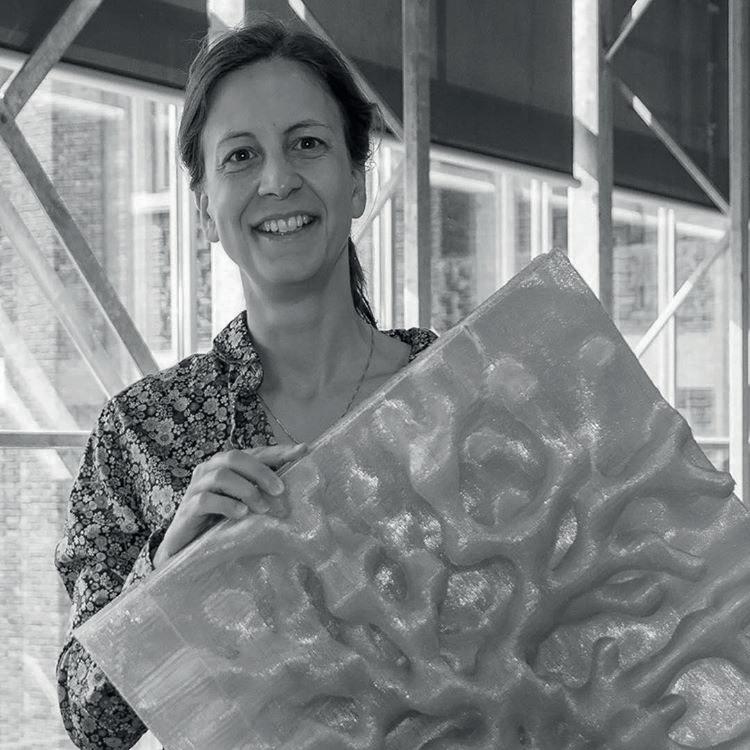
3 minute read
DESIGNERS FROM THE FUTURE
Michela Turrin
Paul de Ruiter
Advertisement
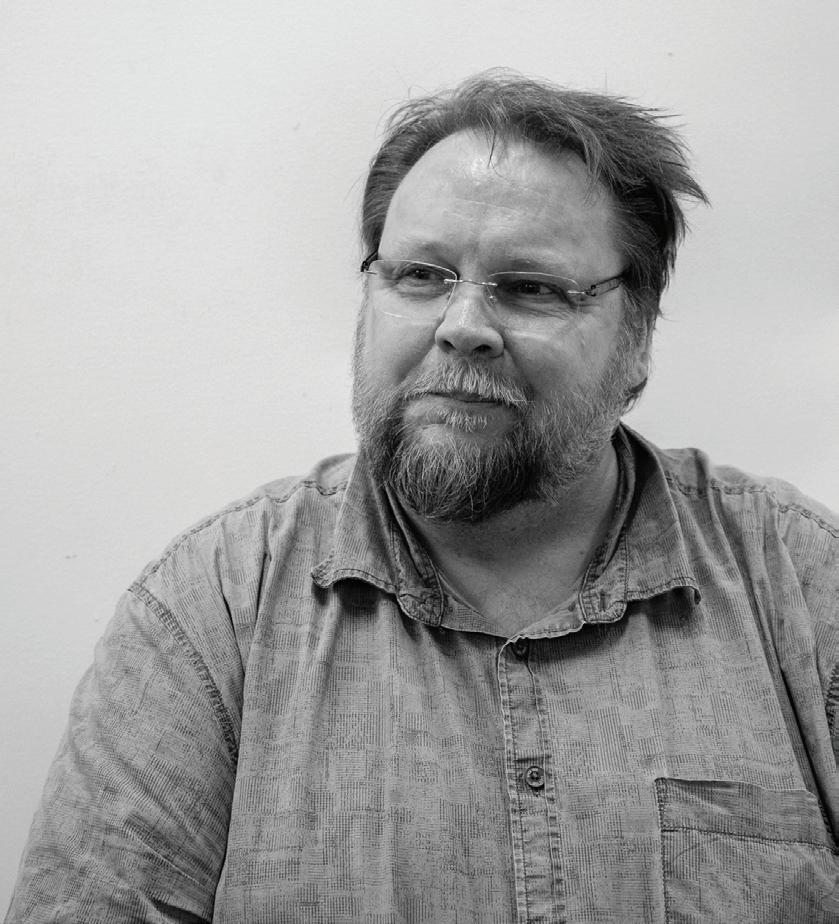
It’s two minutes to one and together with my fellow committee member and photographer Bart Claver I’m entering the 3D-printlab at BK-city. My mouth drops as I take a good look around. Half of the room is filled with prototypes, from translucent art objects to perforated organically formed walls, the other half gives space to machines that look like having arrived from the future. Michela Turrin, assistant professor at the faculty and leader of several projects containing computational design, comes over from her desk. ‘Hello, I’m Michela. Paul will be there in a few minutes. Please take a seat.’
Paul de Ruiter is lecturer at the Faculty of Architecture and the Built Environment at TU Delft and head of operations of LAMA (Laboratory for Additive Manufacturing in Architecture). Paul and Michela are both working in the 3D-printlab, next to the section Urbanism. Here they design and research several aspects of 3D-printing and computational design. Their point of interest is large scale 3D-printing and how to optimize this so that it can compete with conventional building methods. The lab gives them the opportunity to both design and manufacture. Since 3D-printing and computational design go hand in hand, this happens in a fully integrated process, the manufacturing process reflects on the design process and vice versa. The design process demands a kind of manufacturing technique, but the manufacturing technique also demands a kind of design methodology. It’s a feedback loop.
Design projects that they’re doing are often with a team of people from different companies with varying skills. This follows the essence of the method; put a maximal amount of knowledge into the design process for a product that’s got it all. When did the fascination for this subject start?
Paul: ‘Nothing is more fun than finding a solution for a problem. I always see how technology around me is developing with high speed. At a certain point 3D-printing exploded. This happened when people could buy themselves a 3D-printer. Soon people started asking if 3D-printing could battle with other manufacturing methods. After a lot of research with Michela and my other colleagues I think it’s possible.’ Michela: ‘The thing I really like about 3D-printing is that you can use your creativity in the process of exploring sustainable building methods. We used the opportunity we saw in making free forms to change technical systems into design features like we did with the acoustic wall.’
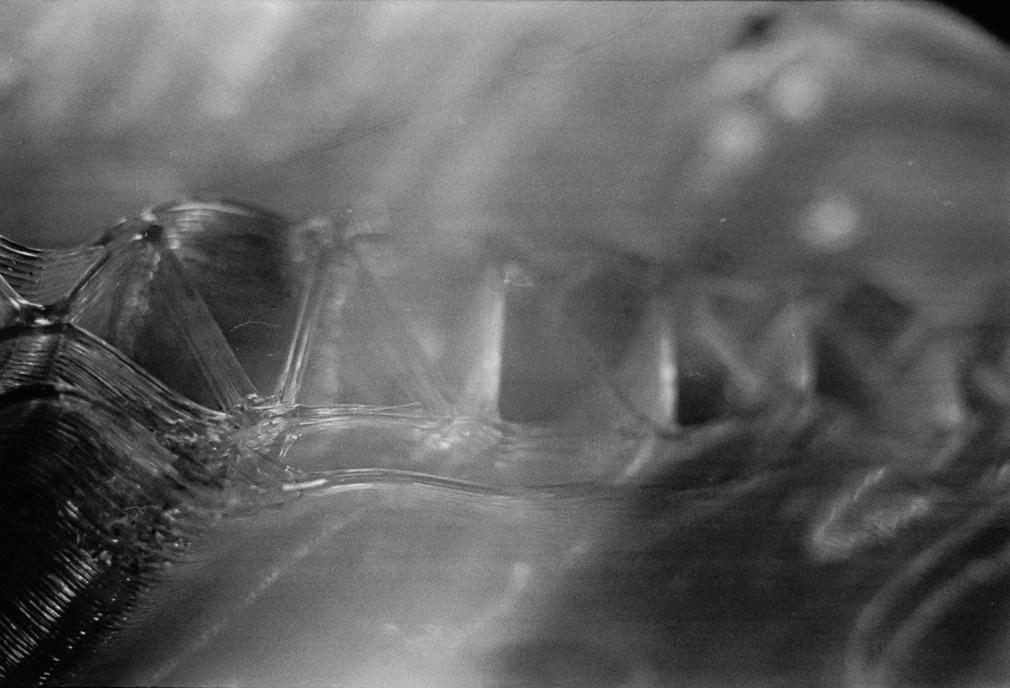
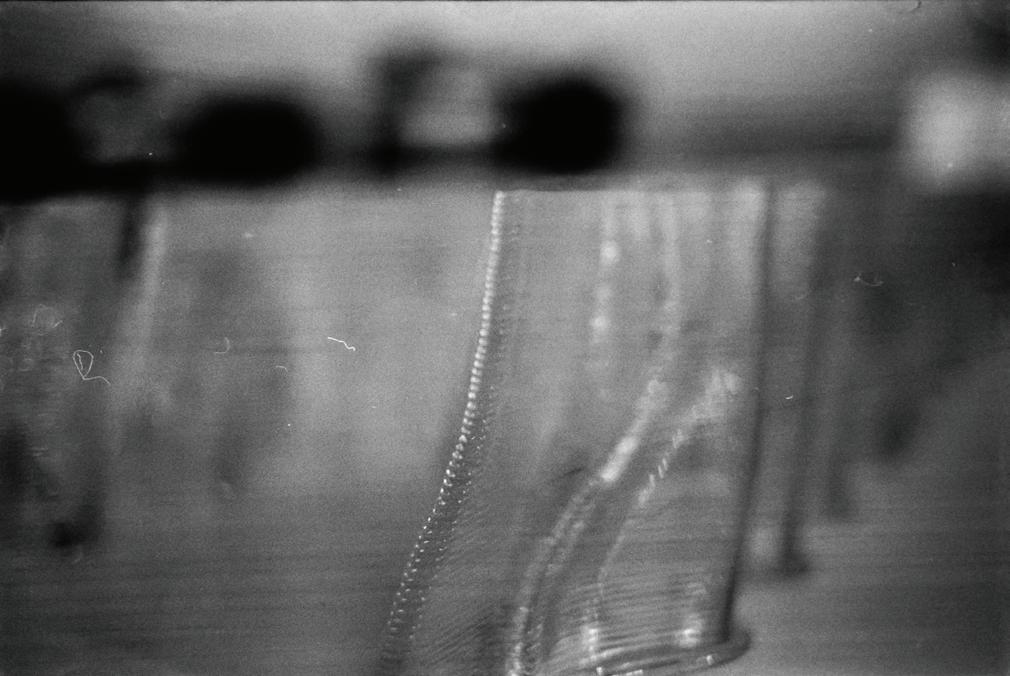
A good example of a project where 3D-printing fulfills a main role is one of the graduate projects ‘Living in a bottle.’ The goal here is to print a tiny house that’s completely made out of PET, a kind of plastic. A mono-material building would be the result. PET is a transparent material, but by applying multiple layers the walls get translucent. This makes the house feel like a tent, there’s plenty of light coming in, but nobody is able to have a clear look through the fabric. This would be a very sustainable building method, since the required material is nothing more than plastic waste. Expanding is quite easy also. Extra PET is the only requirement to print an additional structure. By shredding and reprinting it’s even possible to build a whole new building. In this case, the value lays in the material and the printer is the tool that forms this material.