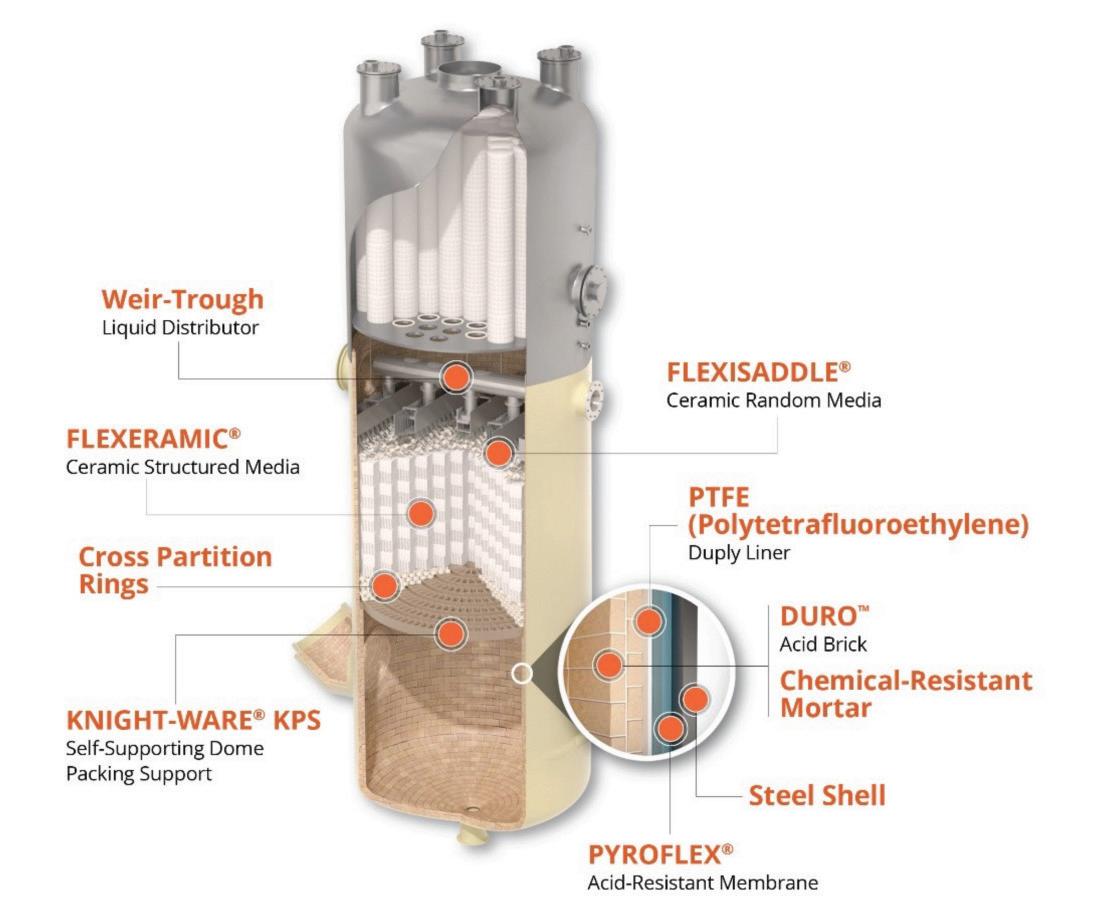
10 minute read
Knight Material Technologies leverages power of three companies for sulfuric acid protection
Feature Knight Material Technologies leverages power of three companies for sulfuric acid protection
Three companies specializing in advanced corrosion control technologies are now affiliated, enabling Knight Material Technologies (KMT) to offer more comprehensive protection and engineered solutions to the sulfuric acid processing industry and end users. This provides processors the 3 in 1 leverage in global sulfuric acid protection by working with three companies, each with it’s own specialty, under one corporate umbrella. Within the past year, KMT added Electro Chemical (EC) as a new division, at the same time gaining the fluoropolymer expertise of its subsidiary, Superior Dual Laminates, Inc. (SDL). As a result, these companies’ complementary technologies now supply the broadest selection of products and core competencies for corrosion protection during the production, storage and use of sulfuric acid and other corrosive substances.
Layered protection creates absorption tower efficiencies
KMT’s capabilities, including engineering, design, installation, manufacturing, and service support provide start-to-finish solutions for sulfuric acid processing absorption towers. A variety of proven media can increase capacities, improve gas-liquid distribution, and help operators realize a longer service life by lowering pressure drop. This yields energy efficiencies that last the life of new towers or a tower upgrade.
Tower construction begins with KMT’s extensive experience with and vast knowledge of ceramics, alloys, thermoplastics, and fluoropolymers and their application for corrosion resistance. KMT has prepared and lined hundreds of sulfuric acid towers of varying heights, beginning with one of the most effective protective lining systems for absorption towers, its proprietary PYROFLEX® Acid-Resistant Membrane System. This flexible, uniformly thick sheet membrane acts as an acid-resistant barrier and expansion joint between acid-resistant brick and the absorption tower shell, whether steel, alloy, or concrete. The membrane is a non-porous, non-aging thermoplastic that supplies a continuous, uniform lining. Tower preparation begins with: • Sandblasting the outer steel shell to SA-3 specifications; • Applying black PYROFLEX® 1080 Primer as a binding layer; • Adding the PYROFLEX Acid resistant sheet lining in sections; • Conducting spark testing to assure barrier protection.
As a secondary layer of protection in sulfuric acid applications, KMT overlays the PYROFLEX with a PTFE film sheet or DUPLY lining. This supplies acid resistance through a continuous, uniform lining without joints. This lining is: • Highly resistance to thermal decomposition; • Simple and easy to apply without steam, curing or aging; • Unaffected by climatic conditions.
DURO™ Acid Brick courses add an extra layer of protection, maintaining corrosion resistance in high-temperature environments. KMT acid bricks conform to ASTM 279 specifications and are either pressed or extruded, with different degrees of water absorption, acid solubility, and compressive strength. This is a true acid-resistant brick, secured with acid-resistant mortar.
Unique dome configuration provides uniform gas flow
In a sulfuric acid absorption tower, the KNIGHT-WARE® self-supporting dome configuration offers a uniquely designed open area for gas flow to reduce pressure drop. It also provides a more uniform gas flow from the gas inlet up the tower leading out through the gas outlet. The dome requires little to no maintenance and is suited for retrofit applications or new construction projects.
Open ceramic rings of different heights are installed above each dome level to provide the flat area required to place the FLEXERAMIC® ceramic structure packing.
KMT structured media with proprietary designs supply greater resistance to fouling than random or monolithic media. Its geometric-waved cross-channel design helps reduce bed depth by offering a greater surface area per volume unit. As a result, it provides more efficient mass transfer than an equivalent amount of random saddle packing. At the same time, it effectively minimizes channeling and radially distributes gas and liquid uniformly over the tower cross-section. The structured media: • Minimizes channeling and radially distributes gas uniformly; • Offers more efficiency per unit volume; • Improves film formation and enhances mass transfer efficiency; • Increases flow and lowers pressure drop.
The lower pressure drop enables a higher flow capacity through the packing, leading to a reduced tower diameter design. The lower pressure drop also translates into lower energy consumption and reduced utility costs.
PFA-expertise ends costly company shutdowns
Outside of sulfuric acid absorbers, when a different chemical mixture calls for a high-end fluoropolymer lining, KMT can offer a broad range of protection after adding EC as a new company division. The fluoropolymers, such as PVDF, ECTFE or PFA, can provide a robust barrier membrane behind brick, or without it, in applications when the protection of brick is not needed or when the weight-bearing load is a significant factor.
For example, a company in the copper refining and precious metals processing industry had to shut down a production line every two to three months to repair the lining in an elbow pipe that was venting sulfuric acid steam from an evaporator unit. This process raises the strength of the sulfuric acid solution to 70%, creating highly corrosive steam at 300° F that requires venting. Contributing factors to its previously installed lining failures included high temperatures, temperature fluctuations, and vacuum pressures, causing pinholes, cracks, and leaks.
These frequent shutdowns caused costly repairs and lost revenue due to interrupted or halted production schedules. As a result, the company called on EC to install a new bonded PFA lining using recently developed technology. Other alternatives were either too heavy for the weight load of the ductwork, too expensive, or too time-consuming.
EC lined the steel ductwork with an advanced PFA fluoropolymer to maintain an acceptable weight while protecting the elbow joint from sulfuric acid steam. The key to the project’s success was a new, high-temperature epoxy. It offered the right degree of elasticity while tolerating elevated temperatures without cracking or becoming brittle. After the relining, the company could maintain its production schedule without the devastating impact of unplanned shutdowns or unexpected maintenance and repairs.
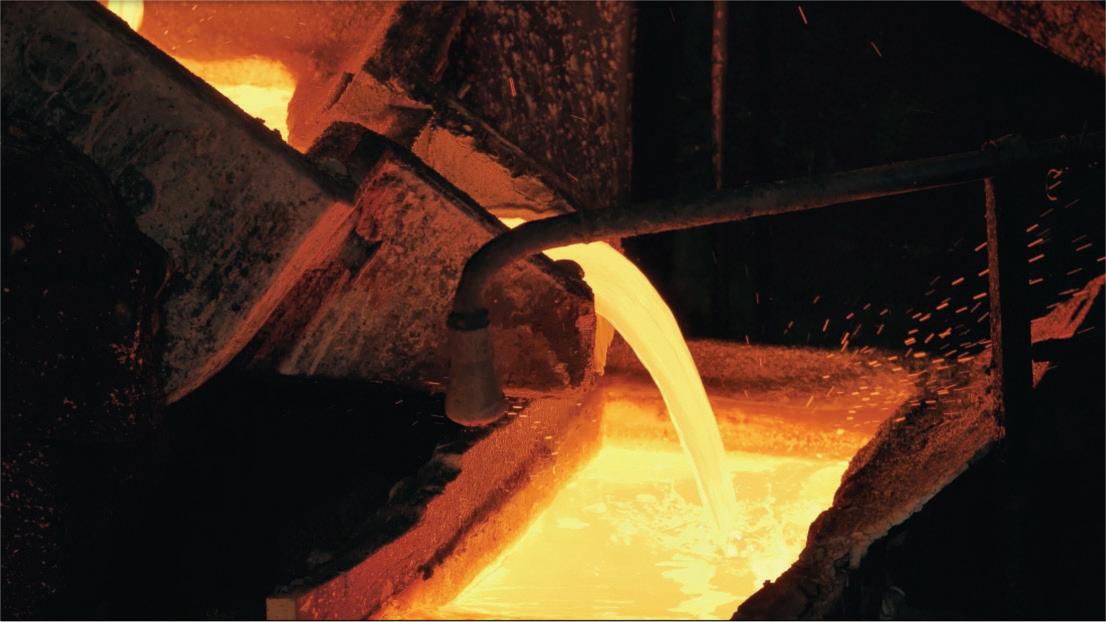
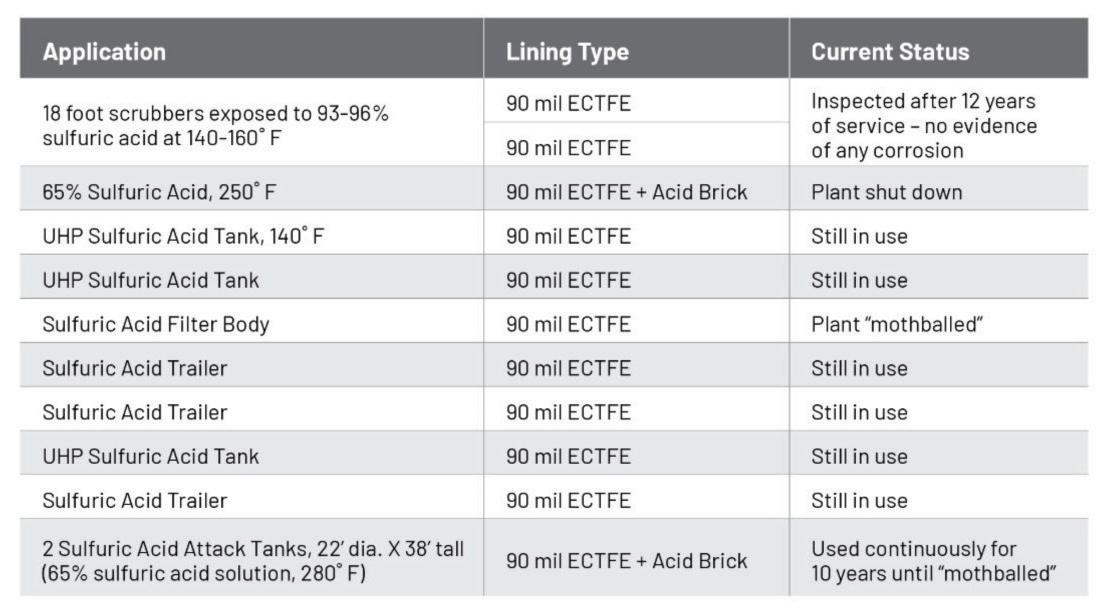
Independent lab testing of ECTFE.
Fluoropolymer linings fill the gaps
Fluoropolymer lining systems supply a sweet spot option for operators looking for a solution with a lower life-cycle cost than some alternatives. Fluoropolymer linings work best at temperatures below 250° F for strong acids, alkalis, oxidizers, or solvents. Fluoropolymer linings can supply a protective barrier in corrosive conditions typically in the range of 500° F if used in combination with chemical-resistant masonry, such as KMT DURO bricks for absorption tower builds. Some of the fluoropolymers where KMT can offer material expertise include PVDF, ECTFE, ETFE, FEP and PFA for new builds, relining work, or repairs.
Another spared shutdown included a multinational chemical company operating a specialty silicone production facility looking for field repair options for a spent sulfuric acid storage tank. EC was able to perform a cost-effective in-situ relining with a swift turnaround. First, the vessel was stripped, repaired, and grit blasted. EC then installed a 90-mil thick, fabric-backed polyvinylidene fluoride (PVDF) sheet lining system. EC utilized a proprietary adhesive to form a bond between the fluoropolymer and the substrate. The adhesive, which is tested in accordance with ASTM D-903 for secure adhesion, helps extend the lining surface life and reduces the risk of a bulk storage tank failure. The tank was restored to trouble-free service after a short time period.
Other fluoropolymer linings, such as ECTFE, have a long history of serviceability in sulfuric acid with many dating back to the initial introduction of these systems. Many systems have outlasted the chemical process industry plants where they were installed or are still in service today.
Bonded linings virtually eliminate failure from expansion differential
As part of the business acquisition, the specialty services of Superior Dual Laminates, Inc. are also available in conjunction with KMT sulfuric acid expertise, specifically dual laminate and FRP materials for custom-designed manufacturing of corrosionresistant process piping and equipment. The bonded SDL dual laminate system prevents the concentration of stresses, thereby eliminating the potential of mechanical damage due to expansion differential and providing excellent corrosion resistance.
Trust the trifecta of companies within Knight Material Technologies for global leadership in the sulfuric acid industry, from complex projects to reline installations, from flange to flange, for companies located anywhere around the globe.
For more information on Knight Material Technologies, Electro Chemical, or Superior Dual Laminate, Inc. products, please visit www.knightmaterials.com/our-companies. q
Department CONTRACTORS’ CORNER
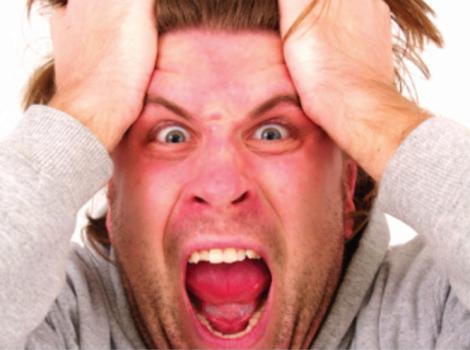
The status quo of stressful outages
By: Ian Legg, Chemical Area Manager, CMW
In this article, I aim to provide critical feedback from a contractor perspective that may help you reduce the risks of outage/turnaround delays, over-runs or over budget costs, and overall downtime. In a business environment marked with labor shortages and supply chain issues, it is imperative for outage planning teams to understand the importance of time and reduce the risks of a stressful outage.
When I mention time, I’m not only referring to the time it takes to perform the outage. I’m talking about the pre-time, or some would call it lead time, to put everything together before an outage start date. This is a critical step that seems to be shrinking or almost non-existent in some cases. This puts a strain on everyone involved, including vendors, contractors, owners, and in some cases, the end user of product you manufacture. Of course, this is not about emergency or unplanned outages—that’s a separate topic for another article. This is about the routine annual, bi-annual, and in some cases tri-annual planned turnaround.
For many years it was an industry standard to spend 12 months or more planning a turnaround. During this time your team would build worklists and create scopes, have ample time to identify and select contractors, procure all materials and long lead items from vendors, and identify and procure fabrications and equipment needed. As a contractor in several major industries, I have seen this amount of planning time decline dramatically. Some producers report 6, 3, or even 1 month of time to prepare. There are also any number of reasons producers move these outage dates and get off schedule. But do they really understand the effects? Most companies have a team that evaluates the risks, but do they capture all of the risks that impact the outage as a whole? This usually ends up with the producer having to answer questions or explain why an outage went too long or where all the money went.
Here is a brief list of the risks when moving an outage or turnaround up or forward: • Planning not finished or complete • Schedule not complete or inaccurate • No time for meetings • Preferred contractors/vendors not available • All materials must be expedited • Additional costs associated • Premium time required by producer side and contractors • Availability of equipment and cranes • Critical scope cancelled due to long lead items • Overall stress on the outage team, contractors, and suppliers
Here is a brief list of pros and cons for delaying an outage start:
Pros: • Planning is done but may shorten time needed for other projects • Availability of contractors • May help supply chain issues
Cons: • Additional costs for cancellation fees or multiple mobilizations • Equipment and cranes are no longer available
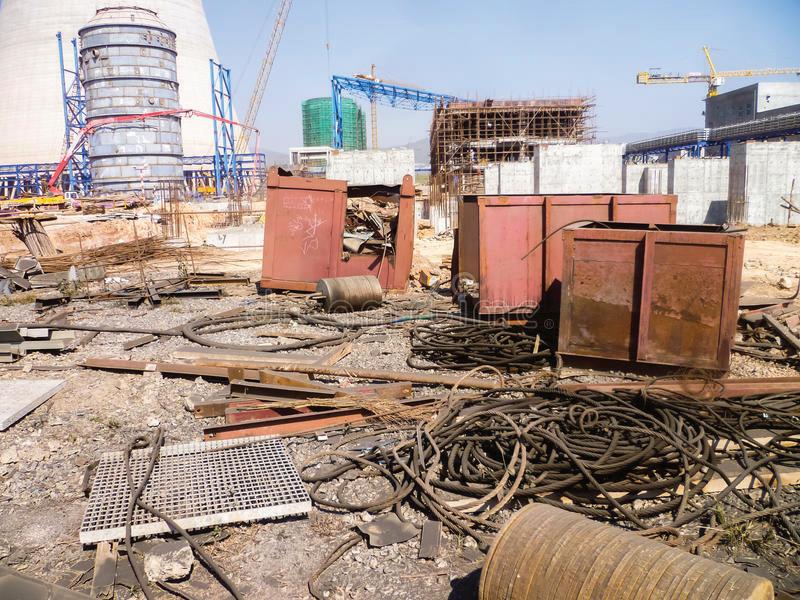
Does your facility’s site look like this during an outage?
As you can see, the risks of pushing out an outage will likely be fewer than moving one up sooner. But it really depends on the amount of pre-work that can get done ahead of time. These are just a few risks we have seen and I’m sure each of you could add many more. I believe that outages and turnarounds that are planned well are executed better, less stressful for everyone involved, and are typically safe, on time, and on budget.
For more information, please contact Ian Legg at Central Maintenance and Welding Inc. at iLegg@cmw.cc or 813-365-2085. q
FindusatBooth39
Process Technologies for Harsh and Corrosive Process Streams
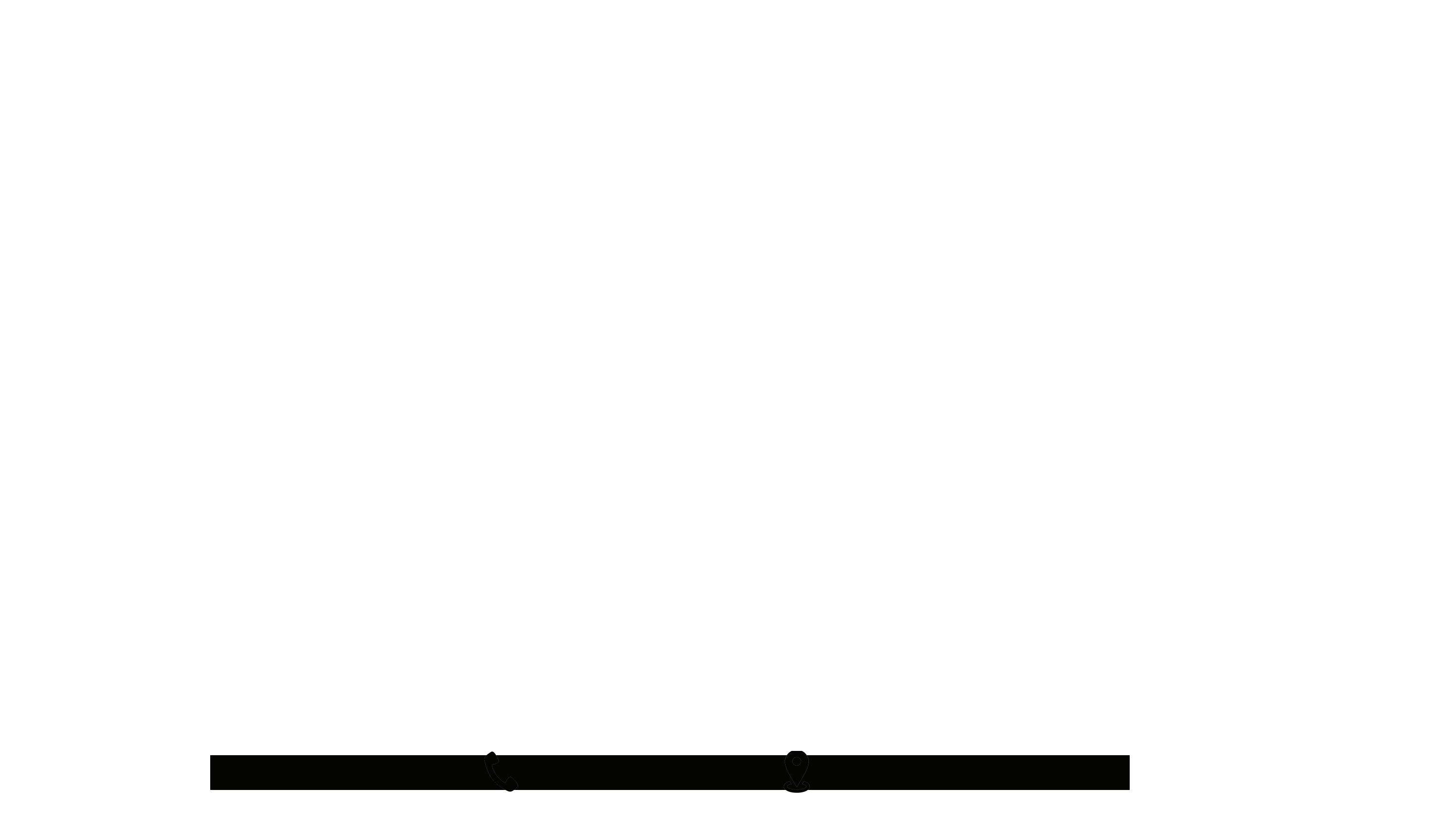
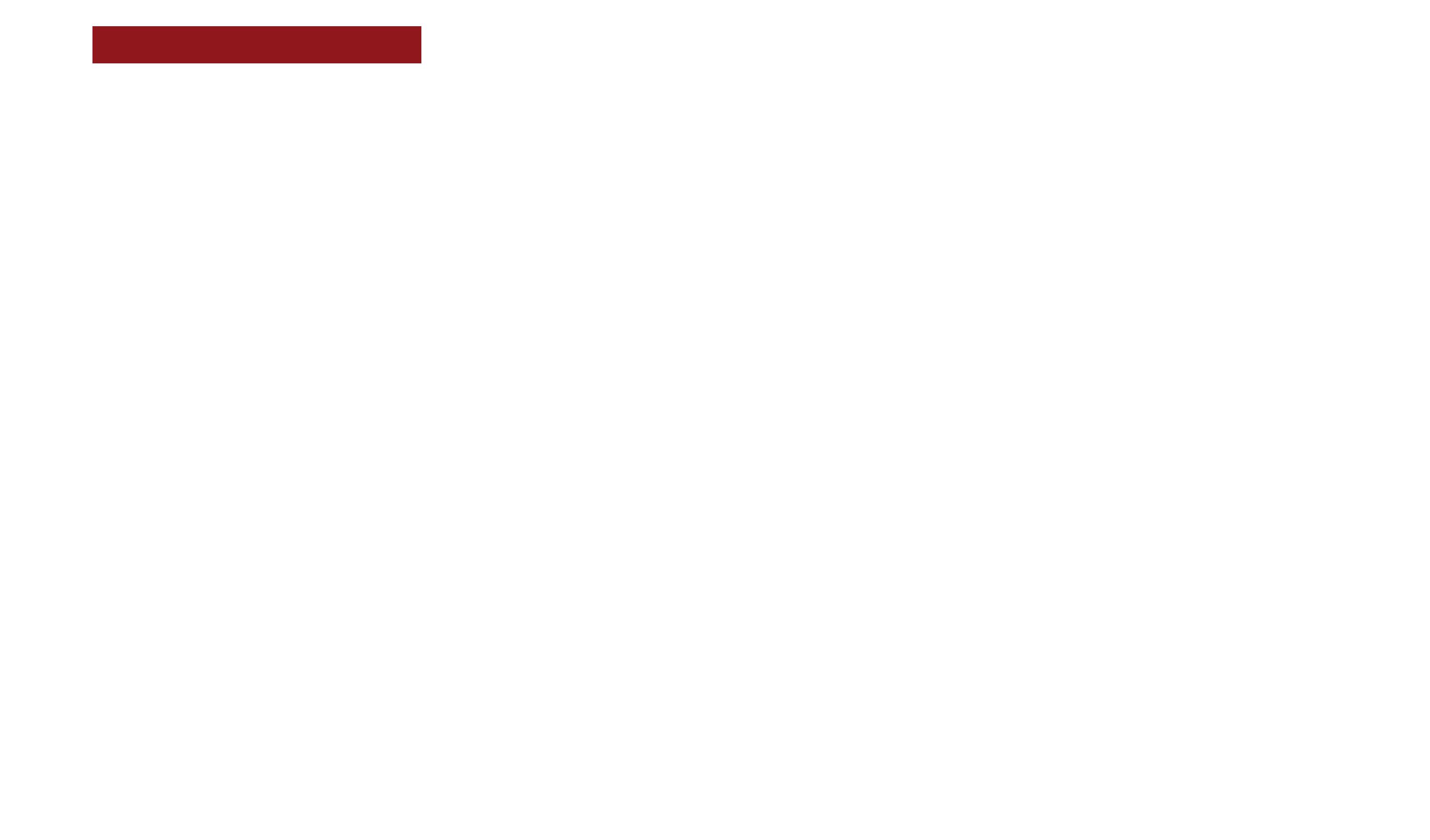
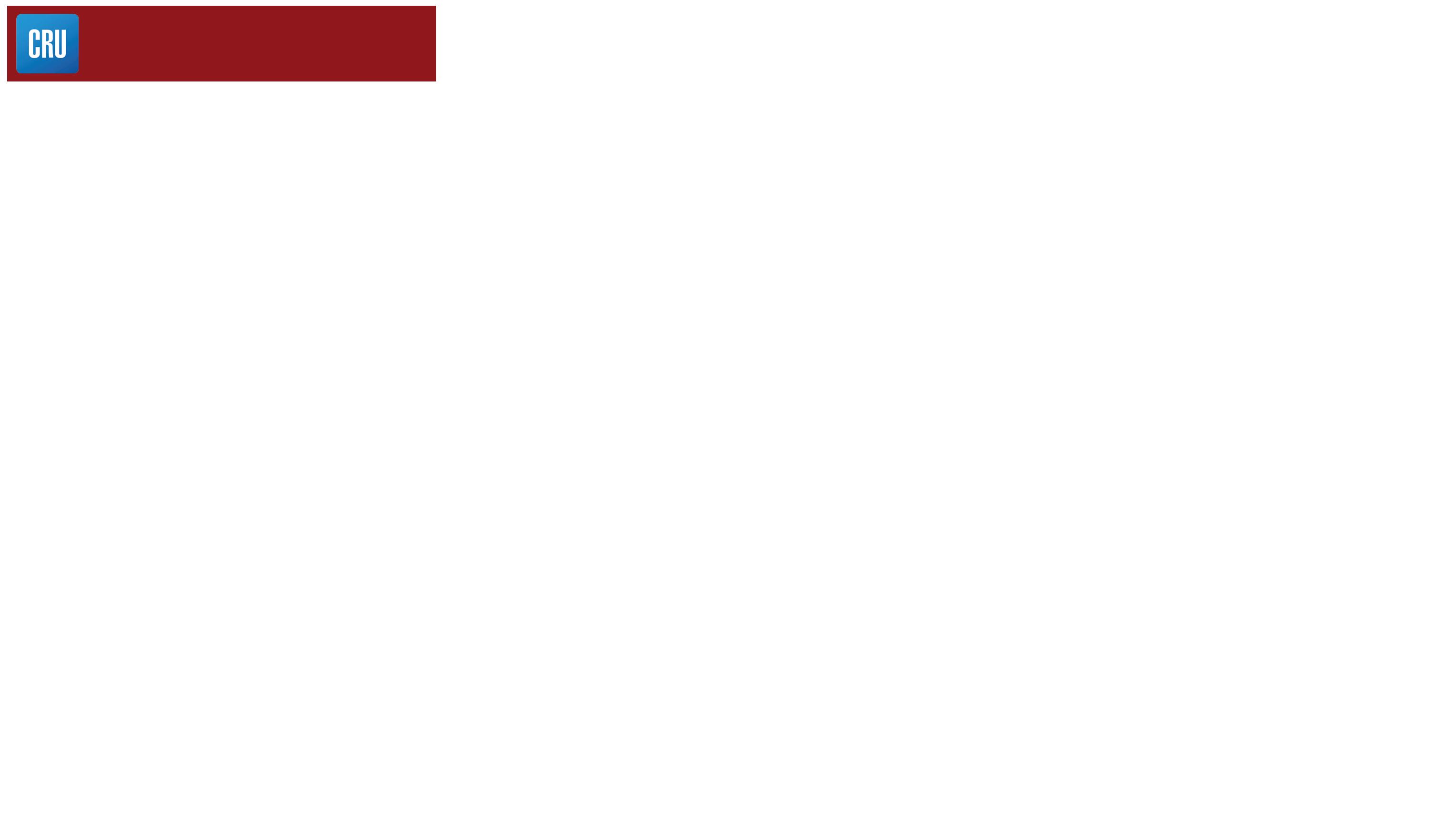
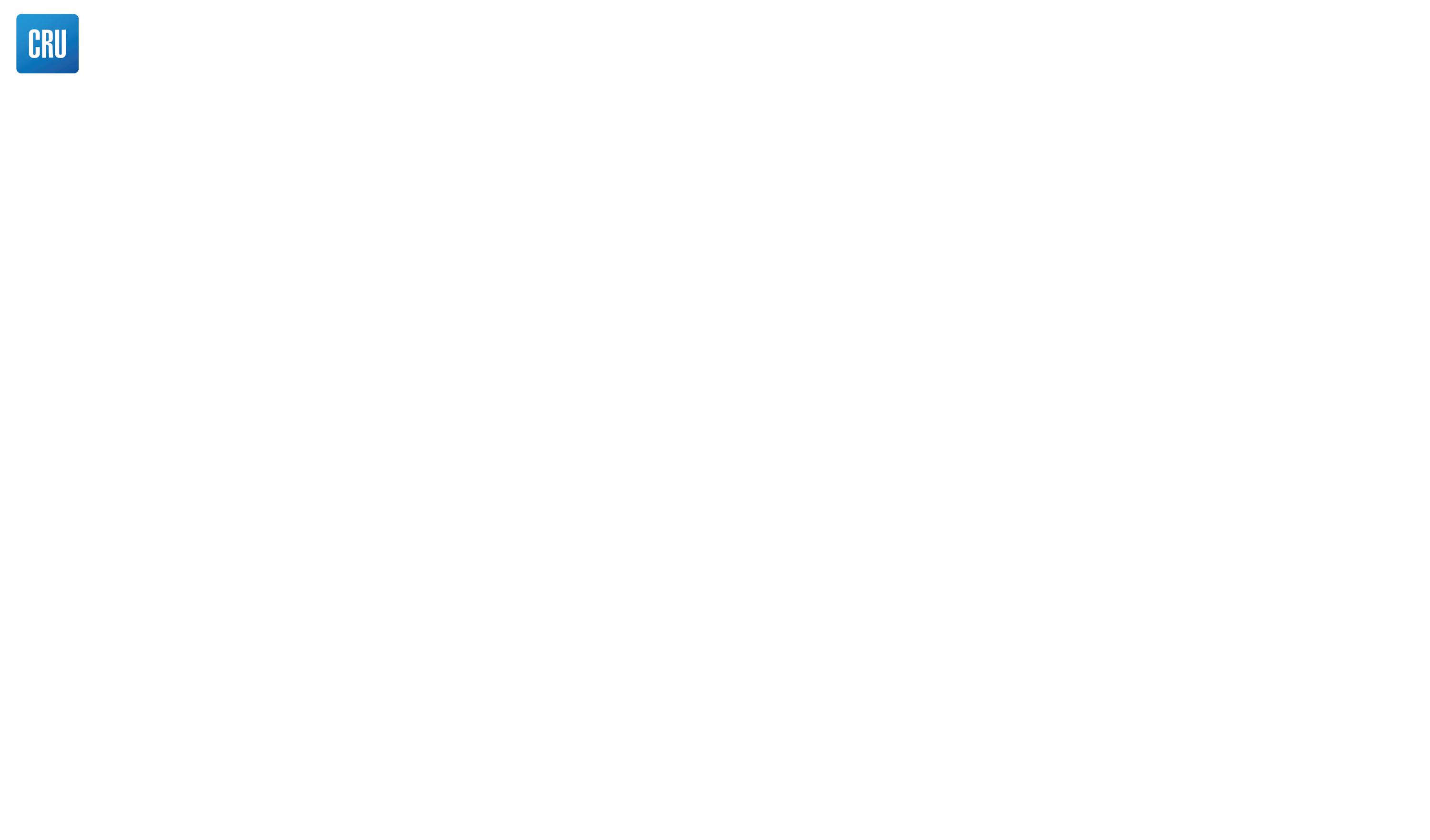
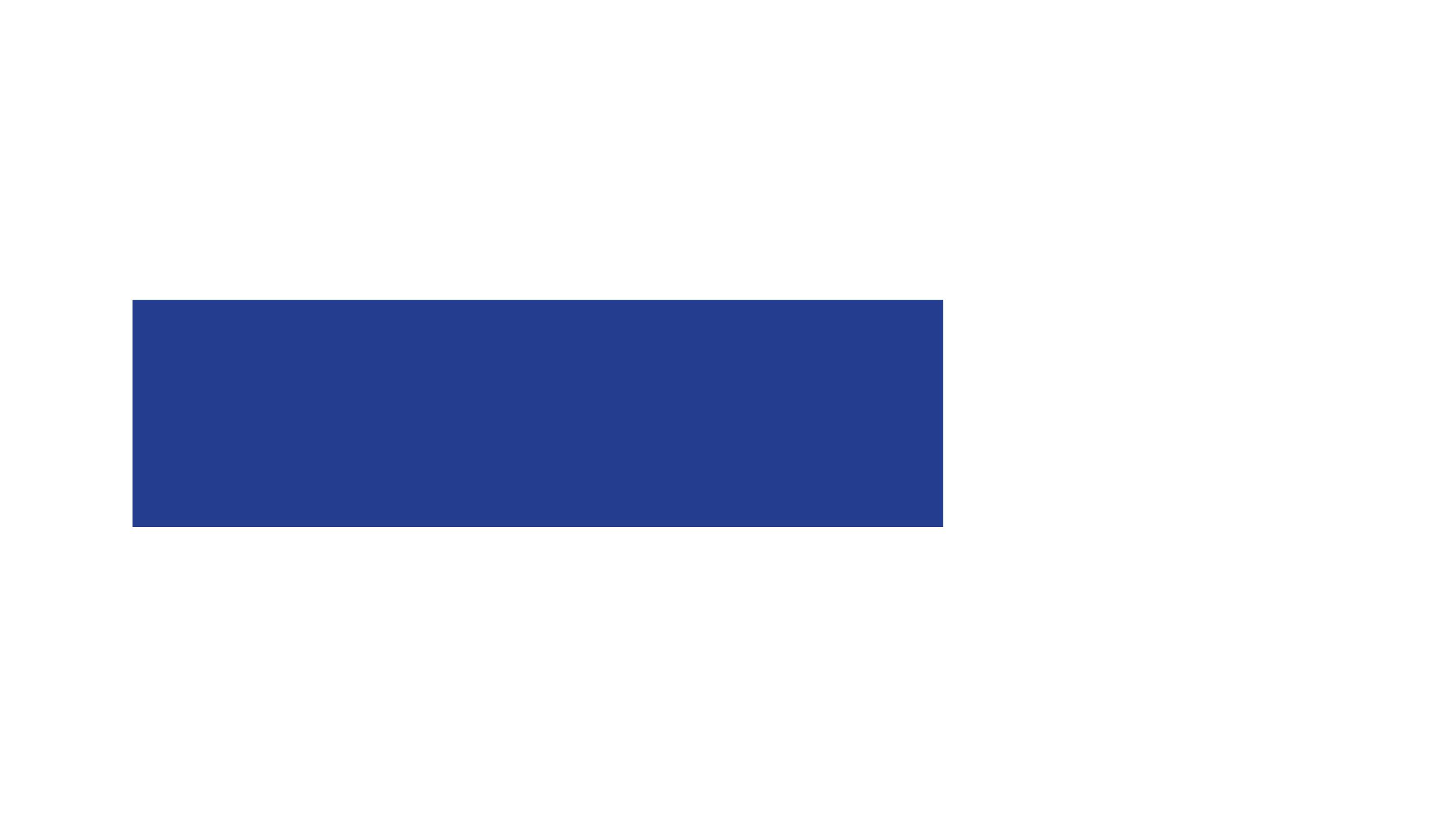
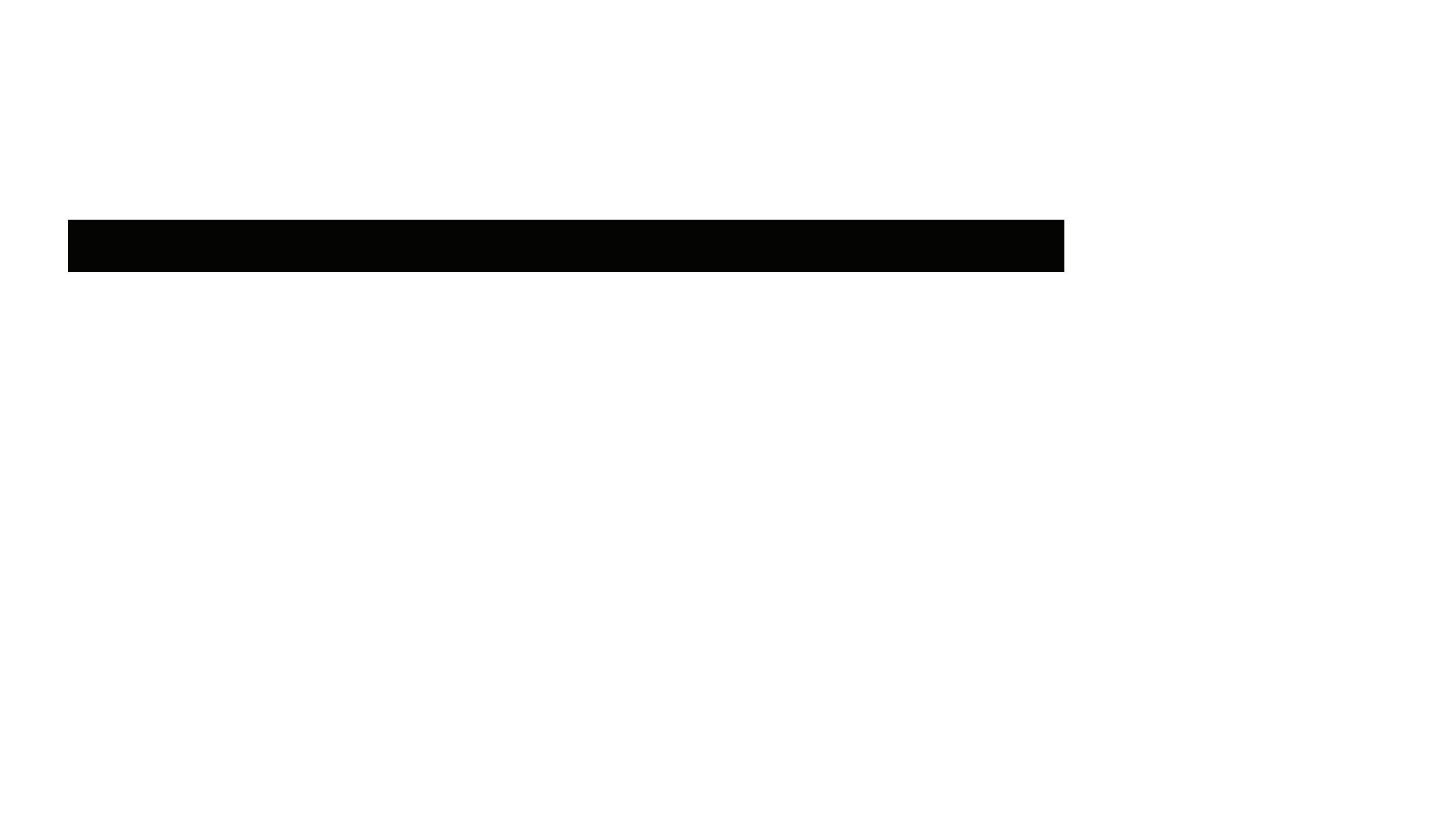
Avoid cold end corrosion and diminish fouling Eliminate stress failures Reduce pressure drops Maximize thermal efficiency
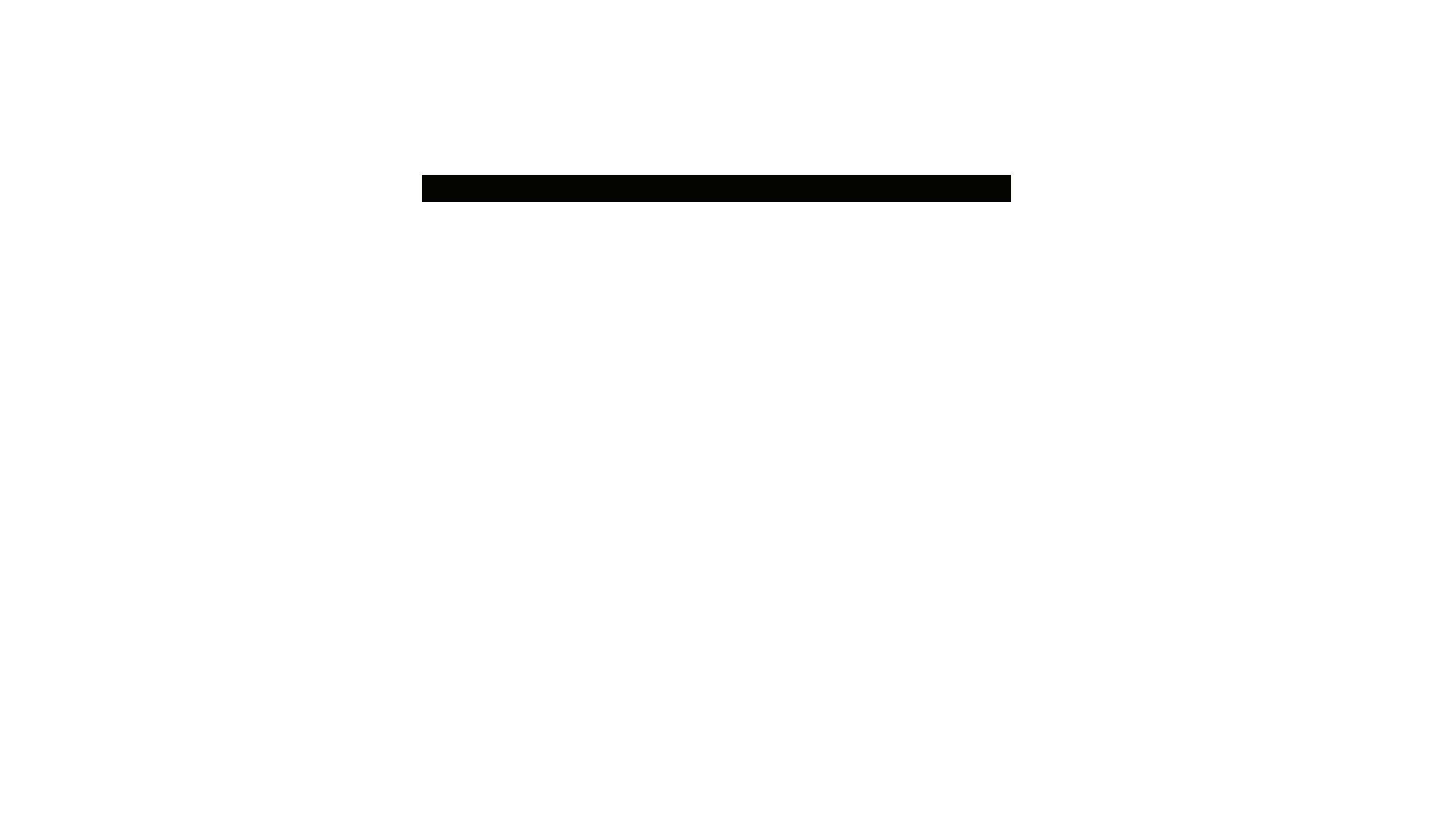
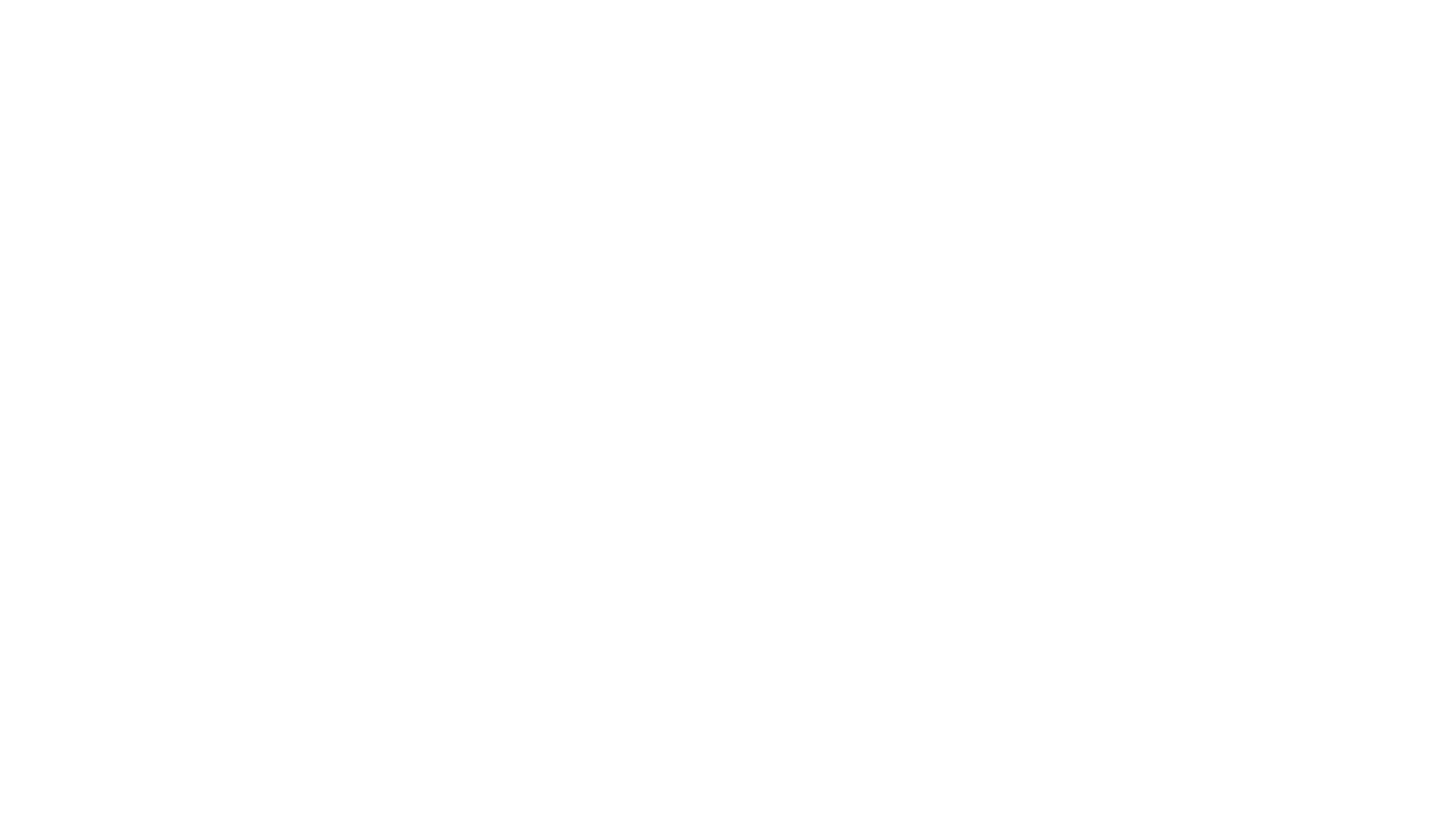
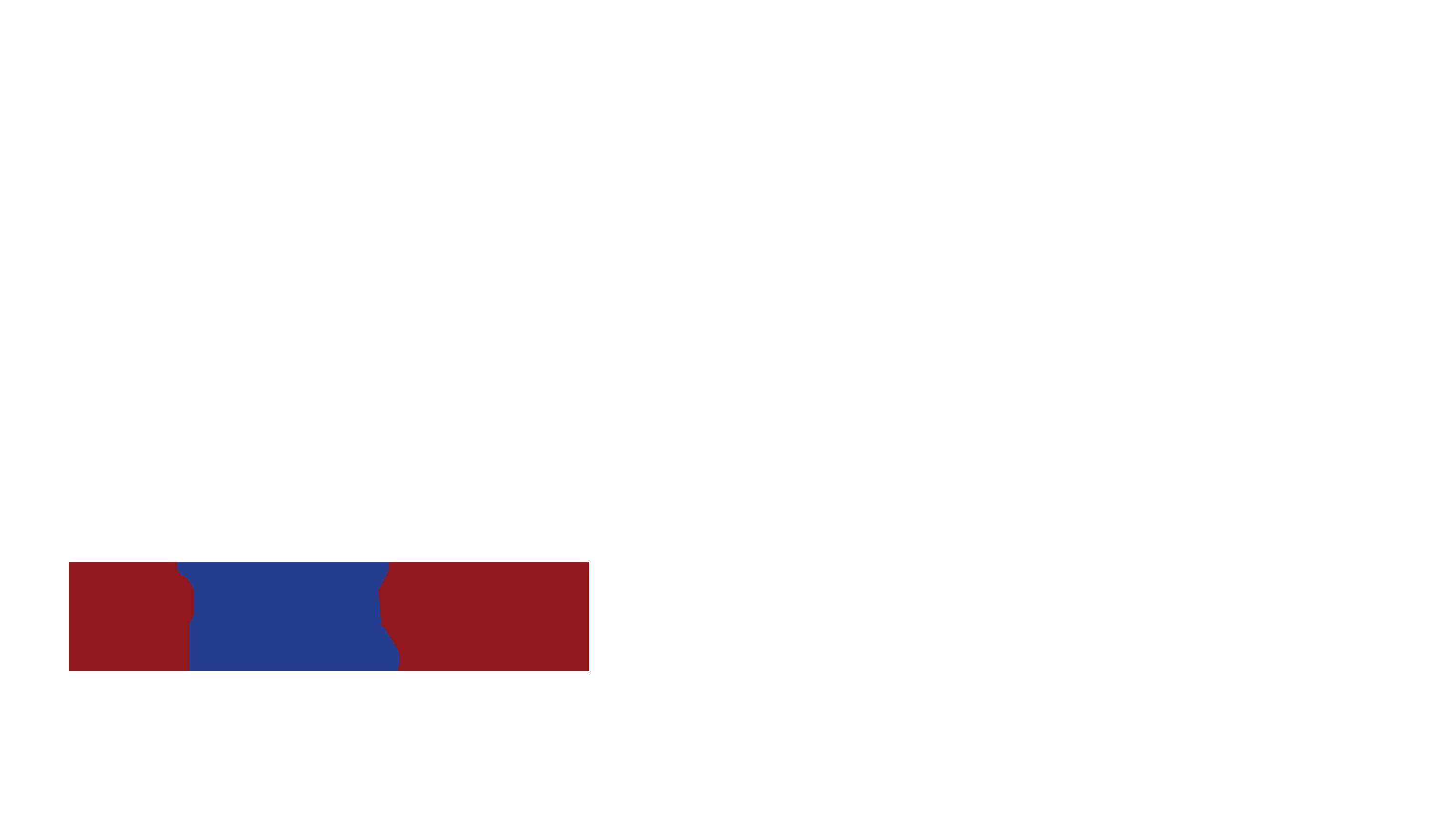
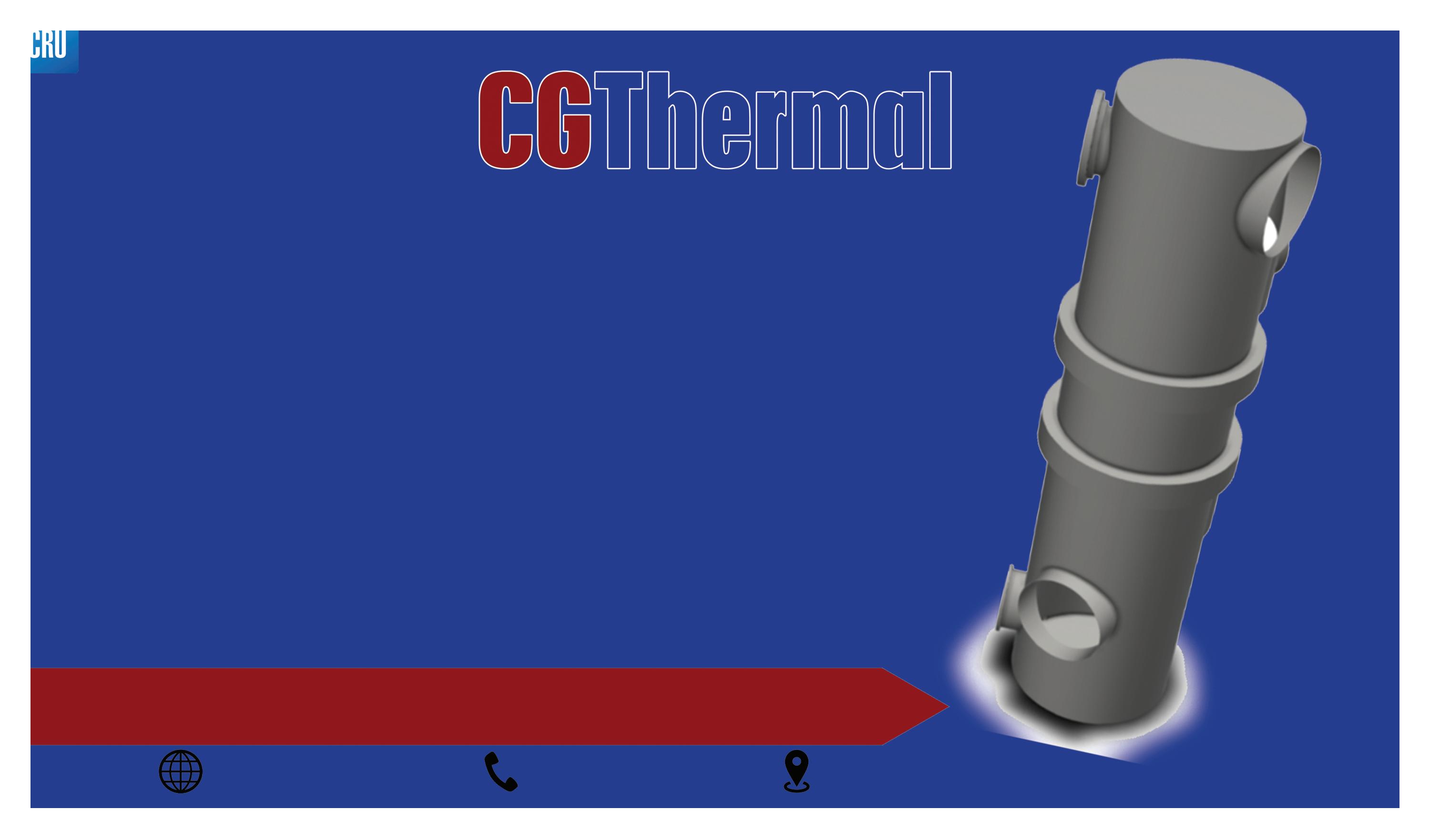
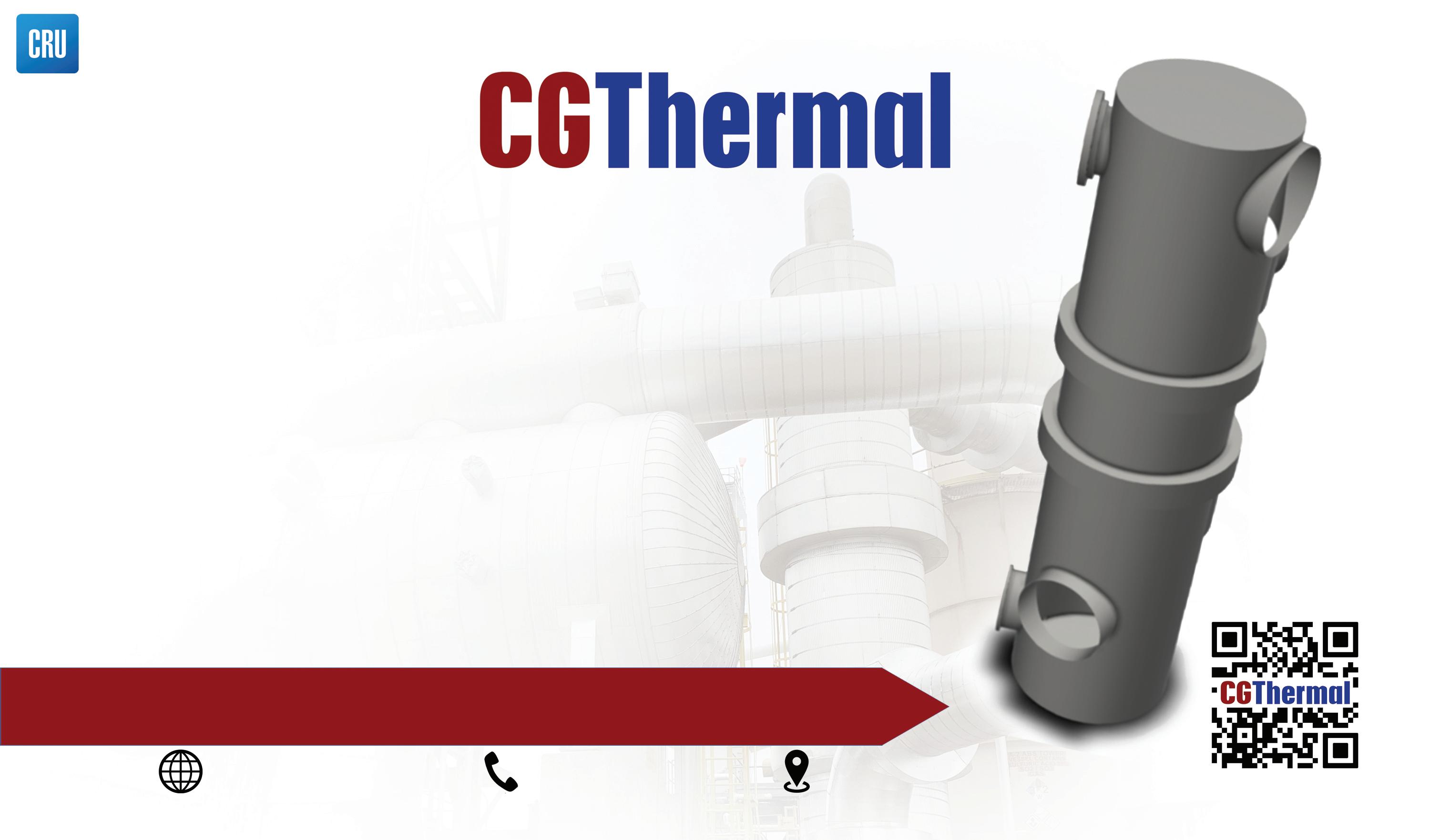