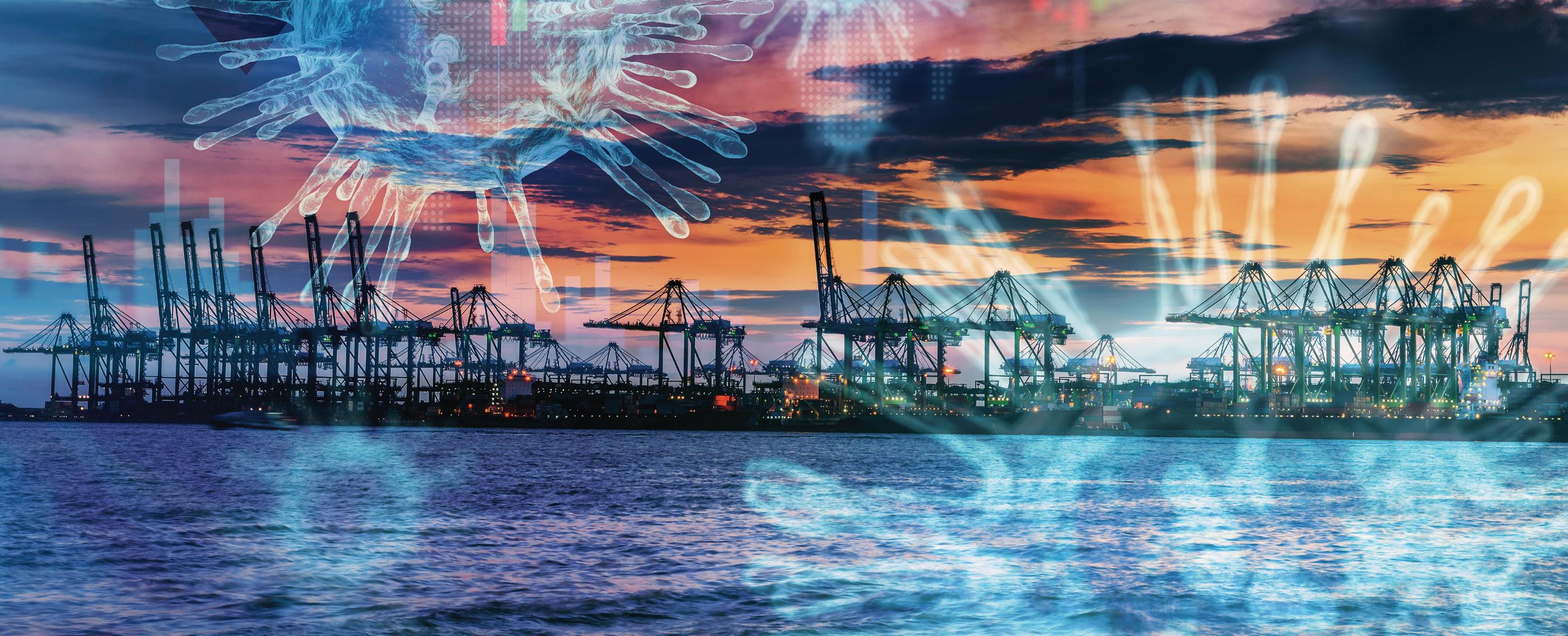
6 minute read
Customs
COVID-19 and customs: breaking the bottlenecks
Restrictions on non-essential goods, reduced staff numbers and new protocols have all played a part in creating bottlenecks across the supply chain, says LISA WITEPSKI
The panic buying that set in at the beginning of the pandemic included the very real prospect of shops running out of imported products. That’s because, as Dr Ayanda Nteta, supply chain executive at Pula Research and Consulting, says “the supply chain simply isn’t agile enough”.
The pandemic also shed a “cruel” light on the industry’s shortcomings, especially when it came to leveraging data and all the paperwork that needs to be completed.
Nteta maintains little has changed 12 months on. “The status quo is likely to remain in place until entrants to the industry are trained in a Dr Ayanda Nteta way that inculcates an agile mindset.” Doug Hunter of Syspro also believes there’s a need for new ways of thinking and recommends matching differently skilled crews for different goods, both essential and non-essential. He says it’s vital that players call on predictive analytics (or their past experience) to learn how to prioritise. “For example, because system constraints are a reality, reliable shippers should be subject to random inspections only, unless they make an error. It may also be a good idea to set up special teams to handle new products like the vaccine, using private labs on site to speed up clearance.”
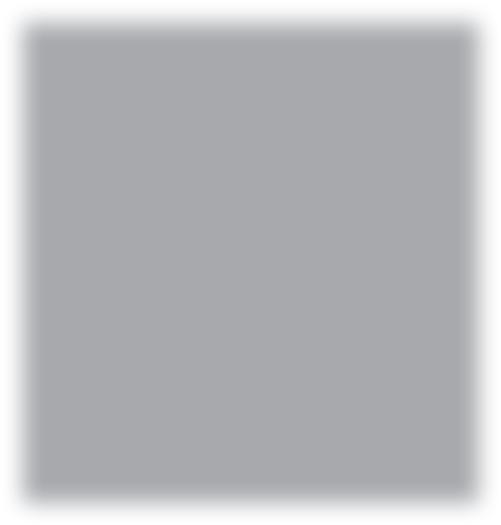
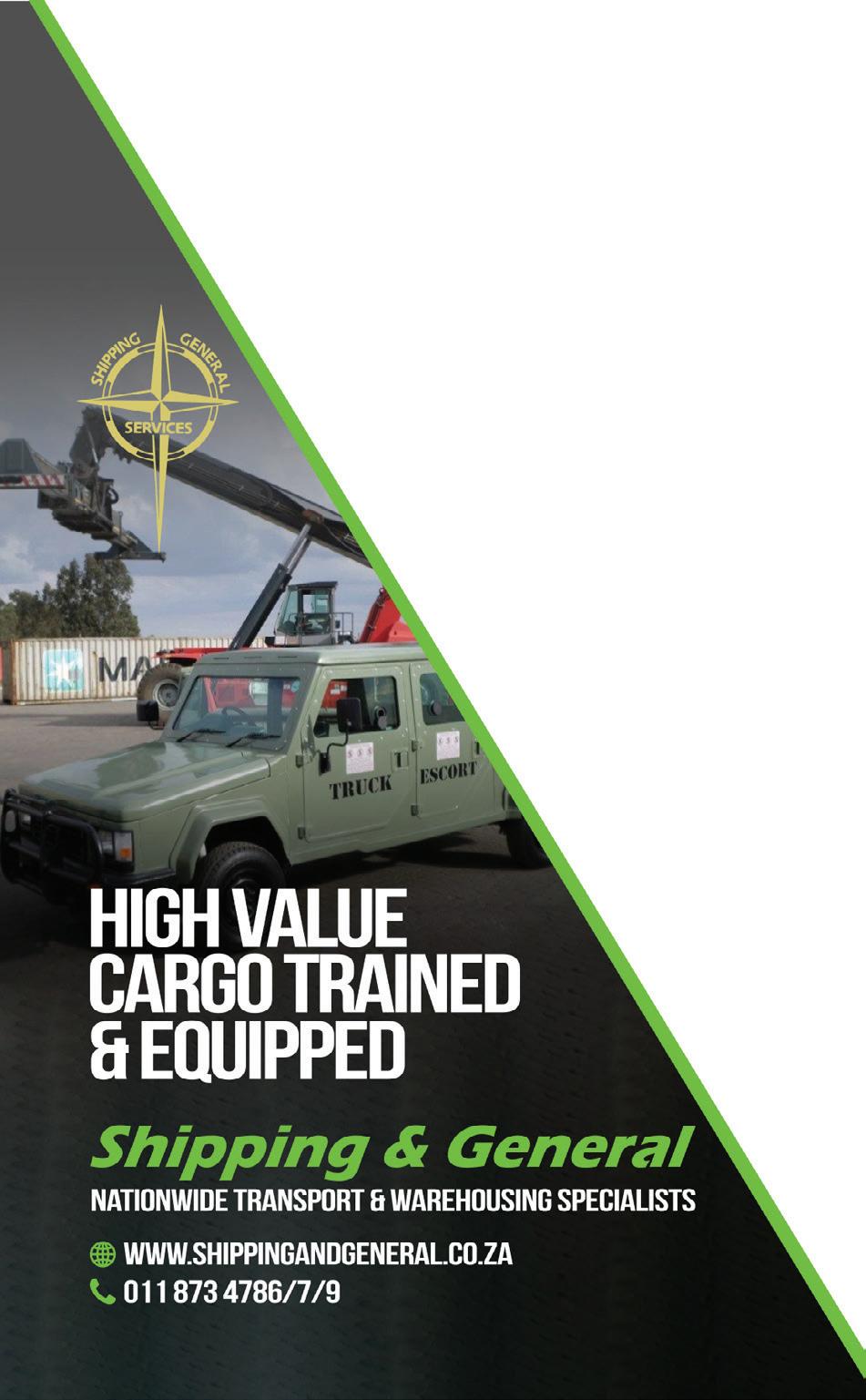
Risky business
Denys Hobson, logistics and pricing analyst for Investec Business, believes that “systems also play a role, especially in terms of automation”. Manual data capturing may be affected by human error, which can lead to delayed custom clearance or the application of incorrect tariffs. He says a reliable tracking system is equally important because it affords customs agents the visibility to prioritise workfl ow and workloads. That’s as Kearney’s Sujeet Morar insists that South Africa needs to apply a deliberate green lane approach, so that preapproved and supplied data can speed up fl ow. But what about risk? Hunter says that in crisis conditions, an element of risk is unavoidable, and the best that management can do is try to mitigate it. “Public-private partnerships are necessary here, because crime is a reality. If scanning or comparison checking equipment is available, it should be used; if not, and the cargo is high priority, it is important to arrange and
CHECKING CHICKEN
The supply chain crisis has impacted industries to a varying degree – but none are exempt. Siya Ngcukana, chief supply chain offi cer at KFC South Africa, says that the company has secured capacity with overseas manufacturers, and reliance on forecasts has been replaced by actual purchase order placement.
However, this impacts payment, which in turn affects cash fl ow cycles. To alleviate fi nancial pressures, KFC has partnered more extensively throughout Siya the supply chain. Ngcukana
coordinate plans for it to arrive at a port where equipment can be organised.
“Non-intrusive methods should be used unless the shipper is new or unknown, or suppliers are sending a product with no previous history or with a sudden change to tariff codes. We cannot slow entire supply chains because we overcheck.”
– Doug Hunter
RECOVERY ON THE HORIZON
Hervé Perron, Bollore Logistics’ MD of international freight forwarding and contract logistics: South Africa, says that challenges notwithstanding, he anticipates a recovery for the industry. “The logistics sector is very resilient and goes from crisis to peaks in activity in a very short period of time. We also believe that to a certain extent, some of the sourcing might be more regional than global – particularly with the Far East – and this will support the development of local and regional industries.”
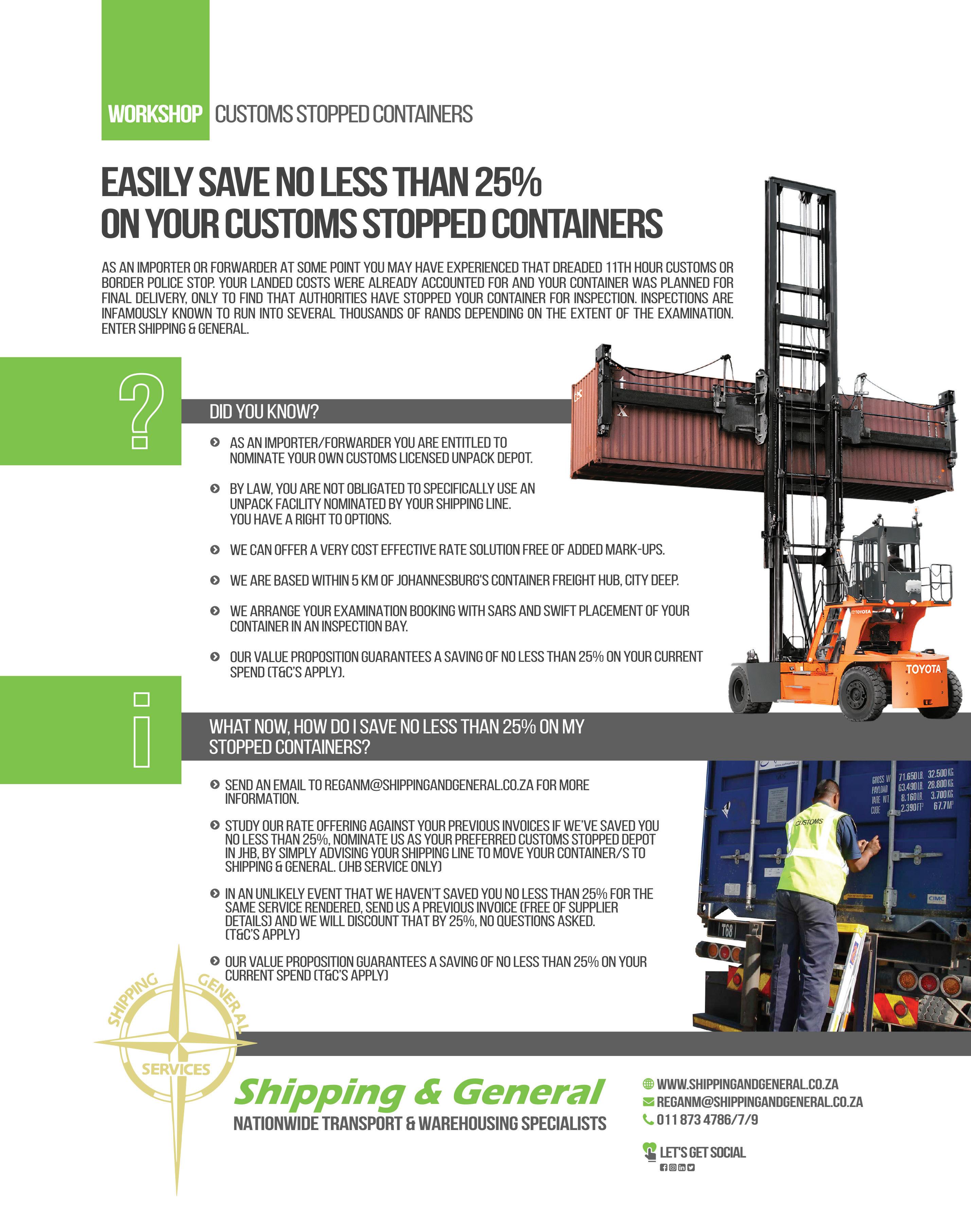
Technology and the evolution of customs clearance
While electronic processes help delays in custom clearance, it’s not all smooth sailing, says LISA WITEPSKI

As the gatekeeper of our borders, customs clearance plays a critical role in securing revenue, ensuring compliance with domestic laws and ultimately protecting society, says Zama Mgwedli, customs and excise consultant at CMS South Africa.
According to Nico Nel, customs manager at Ziegler South Africa, it should take no more than fi ve minutes for a company using customs clearance software to receive a response from SARS once they have submitted a clearance declaration.

“This is made possible by through the implementation of effective controls – effective being the operative word here – as the effi ciency of customs procedures can infl uence a nation’s economic competitiveness, as well as the growth of international trade and the development of the global marketplace.”
That’s why human error, as one of the biggest contributors to customs delays, is particularly concerning, points out Ridwaan Mohammed of ACS – and also why many previously manual processes have become electronic.
Clifford Evans, who holds the public relations portfolio for South African Association Freight Forwarders (SAAFF) Western Cape, says that this change was kickstarted by the introduction of the Customs Modernisation Programme in 2009, “which led to the implementation of, for example, the Electronic Data Interchange, a paperless releasing system, as well as electronic refund applications Zama Mgwedliand e-fi ling”.
Physically unfit
But, while these systems boost effi ciency – or, at least, intend to – they are far from foolproof. “The biggest concern is that other government agencies involved in the import and export of goods have not followed suit,” says Evans. “Port Health, the Department of Agriculture and Forestry, the State Veterinary Service and the National Regulator for Compulsory Specifi cations are just a few of the agencies that still use manual application processes, and require physical visits to obtain the release of goods.”
The disconnect is exacerbated further by the fact that these agencies act independently, not only of customs, but of each other, too – which often leads to the duplication of physical inspections and other processes. This, in turn, says Evans, may result in delays to release and delivery, fi nancial losses to the owners of goods, and the creation of a false economy.
Mgwedli says that custom delays may be managed by “doing the homework regarding the import or export of products” – in other words, making sure that you have the relevant permits, certifi cates and letters of authority to hand. It’s also important to ensure that the goods have been correctly classifi ed, and that the correct import taxes have been declared and paid.
“It should take no more than five minutes for a company using customs clearance software to receive a response from SARS.”– NICO NEL
CUSTOMS CLEARANCE IN A POST-COVID-19 WORLD
Clifford Evans of SAAF says that no new documentation or certifi cates have been necessitated by the pandemic, as all requirements are based on the classifi cation of goods by HS Codes.
“Goods which require specifi c permits or certifi cates are specifi ed in the Prohibited and Restricted Goods Index, along with the detailed requirement,” he explains.
Although some importers, such as those bringing PPE into the country, were issued additional documents negating the need for duties or VAT, Nico Nel of Ziegler South Africa notes that the relevant permits were valid for a limited time only. These rebates have been removed since lockdown restrictions have been eased and goods are able to move freely across borders.
Requirements regarding fumigation and sanitary certifi cations for bulk cargoes haven’t changed either. “These certifi cates are based on the commodity, not the type of shipment, so the same certifi cate is required whether the commodity is shipped as air freight, sea freight in containers or as bulk cargo,” explains Evans. “These certifi cates would be required based on the classifi cation by Tariff Heading and, in turn, the requirements stipulated in the Prohibited and Restricted Goods Index.”
Nel says that this index is updated on a weekly basis, and may be viewed on SARS’ website.
