
6 minute read
Warehousing
Chain of command
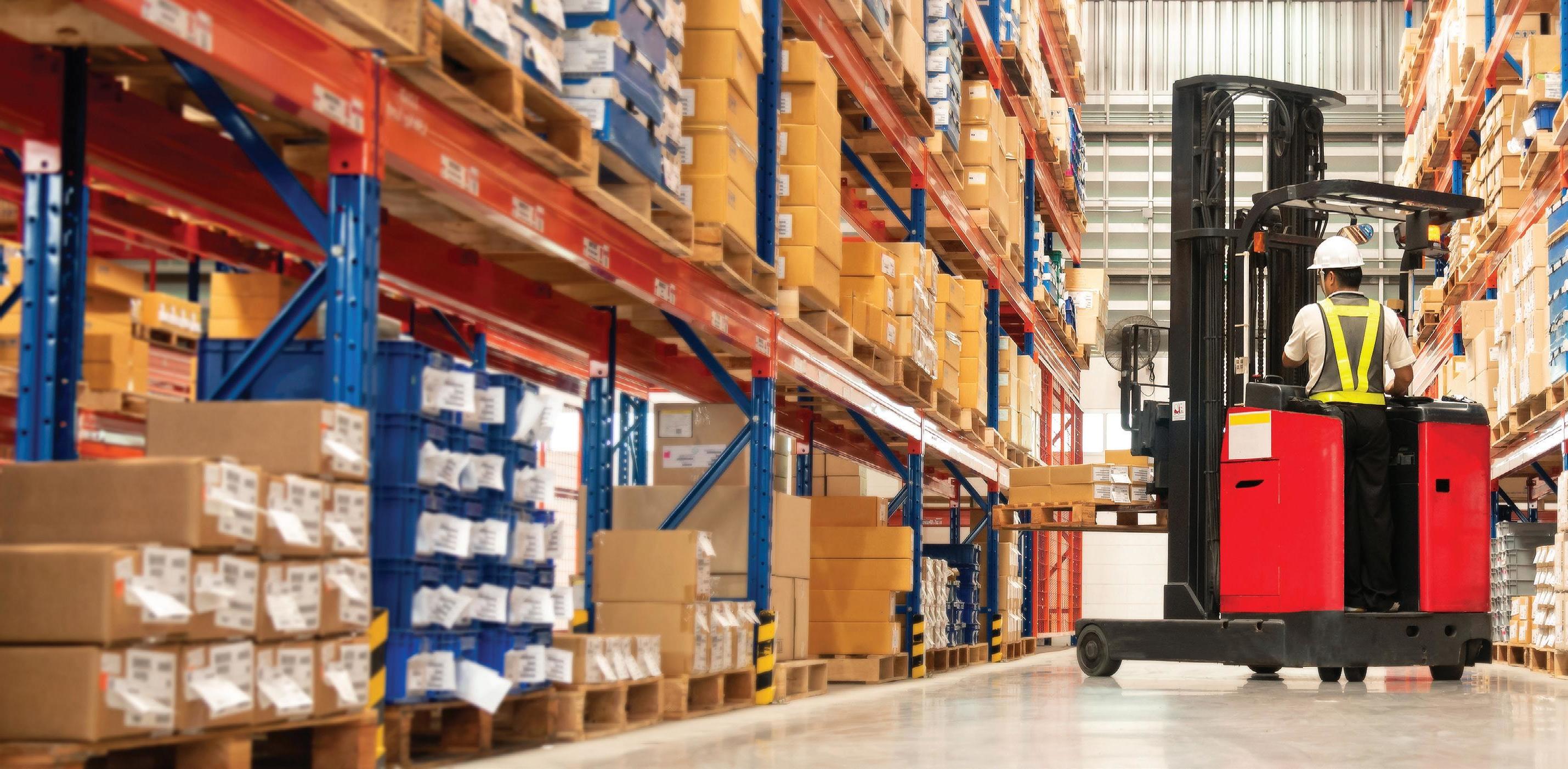
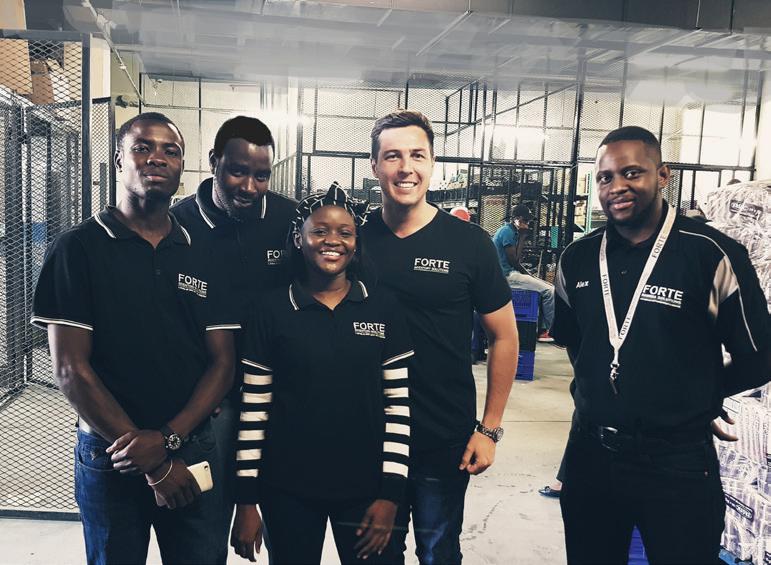
Far from the stuffy repository of goods of old, today’s warehouses are evolving, connected spaces where a warehouse management system (WMS) is used to manage warehousing, inventory and picking, to effi ciently process goods in high-volume and quick-moving sectors.
A variety of industries use it, says Tom Villet, owner of The Inventory Optimization Zone, an end-to-end supply chain consultancy that assists companies with selection, design and implementation of appropriate technologies and processes, to improve their warehouse competitiveness.
“Each warehouse and company is unique in terms of their product mix – fashion isn’t frozen food – transaction mix and volumes,” he says.
“Add to this the different levels of maturity and legacy systems that may be employed by companies, and we see a multitude of solutions being developed, some for broad industry use such as optimising product slotting and pick paths, with others only for a specifi c customer or warehouse.” In an average warehouse, a “pick” is done to collect goods from a “pick face” – the designated area from where the user picks. In most southern African warehouses, forklifts, Software and data management connect for improved supply chain capacity and operational effi ciency, delivering better goods warehouse processing and business effi ciencies. By KIM MAXWELL
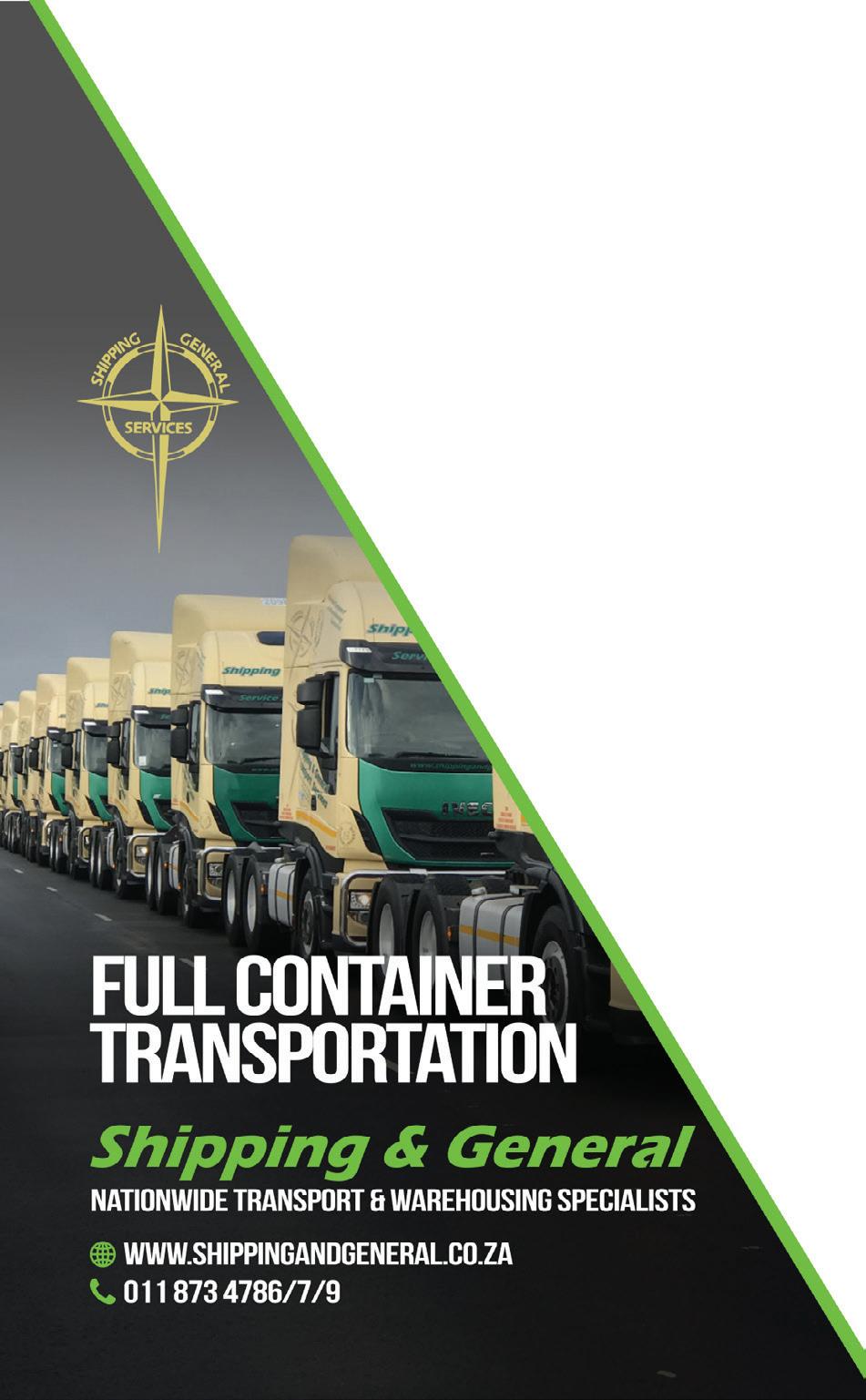
Team Forte Inventory Solutions at PnP warehouse in Windhoek.
baskets or trolleys move into an area, use scanners and pick stock.
A WMS uses machine learning to adapt to changing warehouse conditions and pick orders more effi ciently.
This instruction is automatic
“Our respective warehouse software partners are continuously developing and keeping abreast of latest developments,” says Forte Supply Chain Consulting COO Renko Bergh. “For example, one of our cold store retail clients, Econo Foods, uses automatic replenishment, which happens as they pick, to ensure the pick face has enough stock to fulfi l orders.”
He says automatic replenishment is a feature within the WMS that triggers an instruction to replenish and reorder. It ensures a pick face always carries suffi cient stock, plus backup stock.
Forte serves as a bridge consultancy, partnering with specialised WMS providers, and is responsible for the implementation of and utilisation of these software systems for warehouse operators across South Africa, Namibia and Botswana. Bergh says Forte doesn’t just “drop a box” when implementing warehouse software, but instead takes into account best practices and tries to understand each client’s needs before mapping requirements to the software abilities.
Value chain insights
According to Bergh, insights fed up and down the supply chain can be used to improve product visibility and guide business strategy, using WMS software that adapts to user behaviour, to improve distribution time slots and delays at dispatching level.
FAST FACT
Effi ciencies achieved through scale, competence in logistics and supply chain management contributed signifi cantly last year (FY 2020) to Shoprite’s achievement of its industry-leading food retail gross margin of 23.9 per cent.
Source: Shoprite Holdings Limited Integrated Annual Report 2020
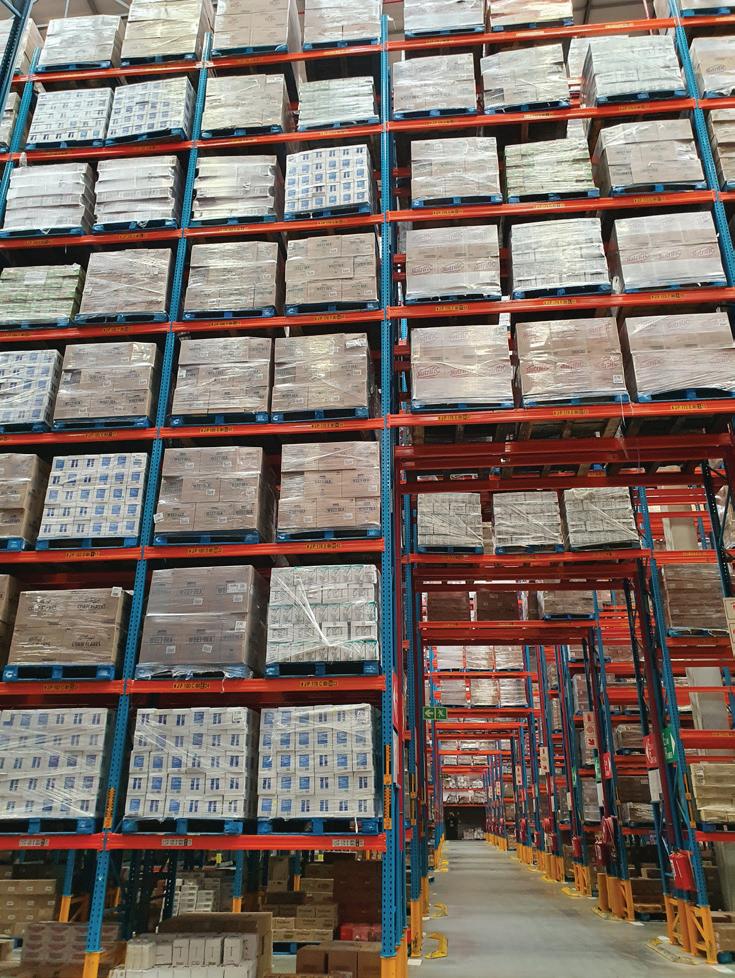
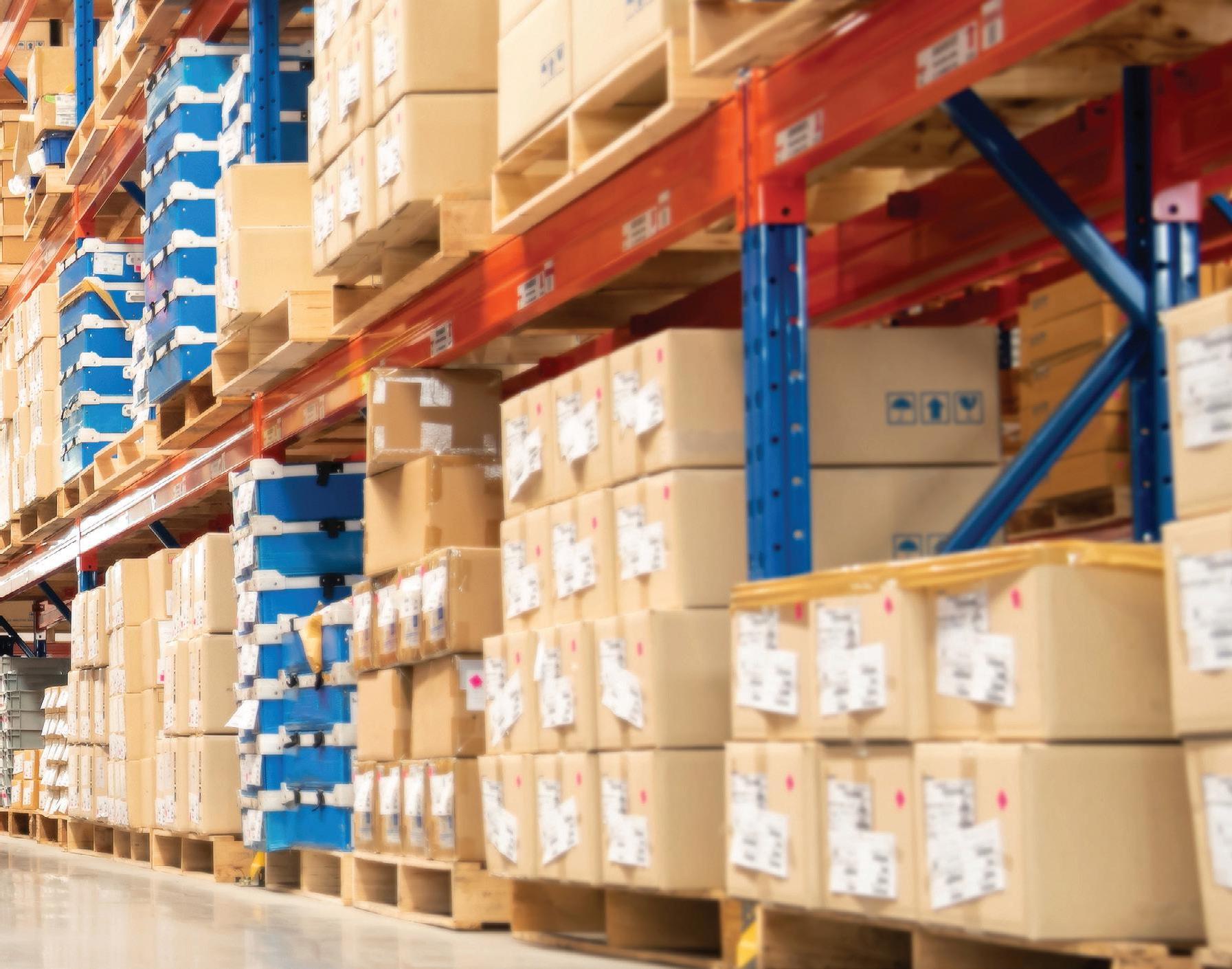
How wMS iMproveS tHe Supply cHain bottoM line
A leverage situation sometimes applies for a supply chain project, where implementing multiple solutions can provide significantly greater value than a single one.
• Inventory optimisation and a new WMS was implemented for a food distributor.
Inventory solution outcome: reducing inventory by approximately 20 per cent, availability improved by 5 per cent. The WMS outcome: almost 20 per cent productivity improvement. This led to an increase in sales (and margin – no unnecessary specials/markdowns), shortened delivery times and a 25 per cent staff saving, mostly through no overtime payments. In addition, the lifespan of the existing warehouse facility was extended by three years. • New storage facilities and a
new WMS were implemented for a hybrid wholesaler/retailer, to support new storage and picking methodologies.
Outcome: an average of one-day improvement in turnaround times, and a 10 per cent improvement in productivity.
Source: The Inventory Optimization Zone
A Shoprite Distribution Centre.
Villet notes the trend of more data points being collected in the total value chain, from internal and external sources. “an example is a company that started tracking the market prices of key raw materials. this allows them not only to impact the future cost price of a product but also to predict possible consumer trends based on these cost price drivers and trends. it ultimately feeds back into detailed operational planning at the warehouse.
“another company is collecting detailed manufacturing statistics from the various sensors in their plant. they use this to predict future maintenance requirements to schedule these in off-peak periods,” he says.
Harnessing these sorts of insights can help optimise a company’s focus on cost prices, profitable customers, and category and product performance.
Data-wise departments
Data analytics are crucial to the future competitiveness of companies, says Villet. “We’re seeing a seamless integration of these tools with enterprise resource planning (eRP) systems as well as Wmses. a starting point would typically be optimising the product mix and levels, often the most overlooked element of a successful warehouse.”
it’s also important to align the various data-intensive cycles within a warehouse such as receiving, picking and dispatch with those of procurement (ordering) and sales departments. But Villet says the success of these data-intensive cycles also hinges on greater cross-departmental collaboration happening within a company.
“the shoprite group has embedded sustainability metrics into its world-class reporting system to enable us to capture and use real-time data to influence decision-making and to make our operations more efficient, responsive and environmentally responsible,” says shoprite Holdings ceo Pieter engelbrecht. africa’s largest retailer and private sector employer, the business declared an annual turnover of R156.9-billion in the 2020 financial year. says engelbrecht: “at R48.5-billion in sales, our checkers and checkers Hyper businesses have become a formidable presence in the south african food retail market.” in shoprite Holdings Limited integrated annual Report 2020, the group attributes its “investment in digital transformation and specifically our integrated eRP system” as directly contributing to improved efficiency, by consolidating all critical information into a single database. the group says its centralised supply chain – controlling the majority of local imports and cross-border export movements – is fully merged with the group’s eRP system.
“this allows for greater collaboration across all supply chain aspects, creating benefits in planning, procurement, warehouse logistics and distribution, and enables us to manage efficiencies to keep costs to a minimum,” explains engelbrecht.
Online shift
online shopping is a growing sector with different requirements to those of a typical warehouse. Villet says often these are “switching points” where large volumes are received, split and then sent to either stores, customers or other warehouses in relatively large volumes. “online retailing requires the fulfilment of small volumes (often single units) in a relatively short space of time,” he explains. “Volumes are hard to predict and tend to be ‘spiky’, supported by promotion activity.” solutions might include building separate online warehouses, outsourcing or allocating specialised online space within an existing warehouse with its own unique Wms. the shoprite group annual report notes that when consumer shopping behaviour “changed drastically” during coViD-19, data analytics systems and a centralised supply chain saved the day: “With real-time data and flexibility in our supply chain, we could immediately react to reallocate and redistribute stock appropriately,” says engelbrecht. “efficiencies were improved, as we could give suppliers real-time information of stock status across the supply chain with associated rate of sale information.”