
7 minute read
Localisation
Safety footwear factory.
Last year the manufacturing sector lost 9.1 per cent of turnover and 10.6 per cent of total income, According to South African Insights. There are a several reasons for this, including decreased demand, a reliably unreliable supply of power from Eskom, and an over-reliance on imported products.
Imports have hurt a range of manufacturing industries. Silvio Ceriani, CEO of BBF Safety Group, knows all about this: it’s what led to the formation of the company he heads.
“The advent of cheap imports really put the local footwear-manufacturing industry under strain: companies were shutting down and margins were closing. As individual footwear manufacturers, we just couldn’t compete.”
In 2014, realising the only way they could survive was by combining forces, the four main local safety footwear manufacturers – Bagshaw, Beier, Frams and Wayne – joined to form
In this together In this together
Local producers need to support each other to remain competitive in Local producers need to support each other to remain competitive in the face of cheap imports. By the face of cheap imports. By ANTHONY SHARPE ANTHONY SHARPE
BBF Safety Group, enabling them to pool local companies, the onus is also on us to resources and compete across categories and procure locally as far as possible and develop price points. local suppliers,” says Ceriani. “It’s easy to get
Ceriani says that the weakening rand has imported clothing, fi nish the garment in South driven up the cost of some imports, bringing Africa and claim local manufacturing, but them in line with local pricing, but there remains that’s not really being part of the solution.” a never-ending line of low-cost importers. He believes that government’s intentions “Where this really hurts the local market are right when it comes to support for local is that smaller manufacturers struggle to manufacturers, but there are frustrations with maintain a consistent competitive edge. the turnaround from regulatory bodies, and We have to accept nominal margins on implementation and enforcement among some ranges just to move volume through companies and state-owned enterprises the factory, but at least we have that is lacking. “We believe stricter fl exibility because of our size.” implementation of procurement KEEPING IT LOCAL FAST FACT policies will help grow SMMEs. For example, Deepening the local value South African when we submit for certain chain requires more than production fell 16.3 per cent procurement, we submit just assembling products in June compared with local content letters for in South African factories. 2019. This was the our footwear that explain It means sourcing all the smallest downturn since how we work towards requisite components locally lockdown hit the 80–90 per cent local raw too, as far as possible. “If economy in March. materials and manufacturing. we as a local manufacturer Source: Trading Economics. That level of scrutiny is what will are asking the market to support drive real growth of SMMEs.”
Levelling process and nd changes need to be made, these can be fed directly back to the design level instantaneously.” The advantage of this in the the playing field local context is that manufacturers can produce a product designed anywhere in the world and prove The local manufacturing sector is building that they’re doing it to the required its digital capacity. By ANTHONY SHARPE standard. “In the aerospace CSIR advanced material testing lab. industry, for example, this is critical,” says Sanne. “They have clear CREATING JOBS speci cations that must be adhered If the fourth industrial revolution has multipliers are in high-value manufacturing and to. If you’re a manufacturer supplying to an taught us anything, it’s that every company advanced materials.” original equipment manufacturer (OEM) you in every industry globally needs to keep have to show your quality control processes. pace with technology to remain relevant DIGITALISATION The same applies to medical devices and and competitive. A number of key advances in manufacturing chemical processes.”
While South Africa is a producer of are linked to digitalisation of factory processes. Sanne says the CSIR is driving best more basic commodities, it’s important Sanne says this involves digital capturing practice and that this starts with skills for the country to focus on high-value of line processes, starting at the development. “We’re building a smart manufacturing and advanced materials, requirement level. learning factory. We have a number of says Martin Sanne, executive at the Council “All process around functional descriptions, advanced manufacturing machines. for Scienti c and Industrial Research (CSIR). CAD designs and so forth are linked to these We’re supporting companies in additive (CSIR). “Manufacturing is a job multiplier: for original requirements, so once a product has manufacturing, and our National Centre every manufacturing job you create, been designed it can be veri ed against the for Nano-Structured Materials has, over you can create between two and 15 original specs. the past 10 years, built up full capability to additional jobs, so it’s a huge boost to “We call this closed-loop manufacturing. make virtually any materials, including new the economy,” says Sanne. “And the big As you’re going through the manufacturing plastics and nanoclays.”

NEXT-GENERATION BAKKIE
Isuzu Motors of Japan has awarded a R1.2-billion programme to South Africa to build a next-generation bakkie in South Africa, while an additional total local content value of R2.8-billion will be generated through the life cycle of the programme. The Isuzu project team members in Japan, Thailand and South Africa are fully engaged in ensuring that the relevant project milestones are achieved. Source: Billy Tom, Isuzu Motors South Africa

Driving the FUTURE economy
South Africa’s largest manufacturing sector is rethinking localisation to deepen the value chain. By ANTHONY SHARPE


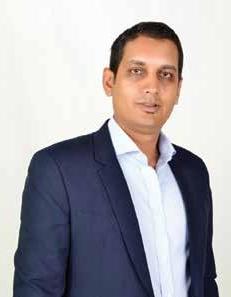
The automotive industry accounts for a third of South Africa’s manufacturing output and contributes roughly seven per cent of GDP. Those are not small gures, so the industry is a vital one that government wishes to cultivate. In 2016, the Department of Trade and Industry commissioned the South African Automotive Masterplan 2035 (SAAM), which has some ambitious goals: contributing 1 per cent of global vehicle production by 2035; increasing local content from 39 to 60 per cent; doubling employment in the value chain to 240 000; achieving minimum level 4 BEE by 2021; and basing support on value addition rather than just production sales value.
Key to this is the Automotive Production and Development Programme (APDP), which comprises an interrelated set of incentives and rebates designed to promote local manufacturing.
“The APDP has, for a number of years, enabled vehicle manufacturers in South Africa to be sustainable by offsetting the inherent disadvantages of operating in this market,” says Billy Tom, CEO and MD of Isuzu Motors South Africa. He believes the industry can help South Africa in its transition to a higher-value economic model. “Government and the industry need to Renai Moothilal
Billy Tom

work together to enable a shift from raw material or commodity export business models to ones focused on the benefi ciation of raw materials, as well as the local manufacture of components and commodities such as batteries and controllers. These can then be consumed by local OEMs and also be exported to other markets.”
Quality over quantity
Renai Moothilal, executive director of the National Association of Automotive Component and Allied Manufacturers (NAACAM), says the existing APDP has helped build automotive manufacturing capacity, but prioritises production volume over local value addition and sourcing. That’s why it’s being extended from the beginning of next year with some notable revisions.
“The biggest difference is the implementation of the Volume Assembly Localisation Allowance,” says Moothilal. “This is an assembly incentive for OEMs linked directly to levels of localisation on their respective platforms. The current-generation APDP ending in 2020’ has a similar assembly incentive, but without any localisation element. Allied to this is a re-weighted Production Incentive with higher levels of reward for manufacturing value-add.” It’s hoped the APDP will deepen the automotive value chain by encouraging OEMs to fi nd new localisation opportunities due to reduced import incentives. As there is a limit to what they can localise themselves, they will pressure their tier 1 suppliers to produce locally, with an anticipated knock-on effect to tiers 2 and 3. Localisation is not a nice-to-have, says Moothilal, but an economic and competitive necessity. “It’s common knowledge that the true economic benefi ts in any country’s automotive sector are found in deep value chains with high localisation levels. Job opportunities, technology and skills development, and transformation enhancing new business opportunities will be found as long as we keep striving for that 60 per cent localisation objective. Studies show that countries having localisation levels around the 60 per cent mark are regularly touted as global competitiveness benchmarks.”