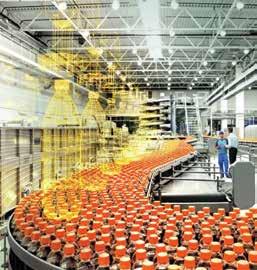
3 minute read
Beverages
BUYING LOCAL
A spotlight on ... Twizza. By BETH AMATO
The founder of local soft-drink manufacturing company Twizza, Ken Clark, took a leap of faith in 2003 when he decided to establish a soft-drink manufacturing line in a dairy factory in Queenstown, Eastern Cape. He saw the gap to produce locally fl avoured soft drinks. Now, 17 years later, through sheer grit and innovation, Twizza has 3 manufacturing sites and 13 distribution centres around South Africa.
While competition from well-known international soft-drink brands is high, Twizza CEO Lisle Clark says that the company is expanding into Africa. “We’ve adapted our soft drinks to local palates and taste preferences. We’ve mixed the everpopular ginger fl avour with the timeless cola fl avour and named it Ginger Cola.”
When the COVID-19 pandemic hit South Africa, Clark said Twizza adapted quickly to the situation, allowing customers to buy the company’s drinks online through Takealot.com and have them delivered. “We are constantly looking at ways to improve our service and to adapt to changing circumstances,” says Clark, adding that the partnership with Takealot.com is an important one. “We’re both proudly South Africa companies, and in these trying times buying local is a step towards sustainability.”
We’ve adapted our soft drinks to local palates and taste preferences.” – LISLE CLARK, CEO, TWIZZA
Lisle Clark
SNAPSHOT OF THE GLOBAL MARKET
There are two major categories and eight subcategories in the beverages industry. According to Beverage Industry Magazine, the global carbonated soft-drink market has been declining annually to 2019, thanks to consumers opting for healthier choices. But falling alcohol consumption in some markets means that the carbonated soft-drink market can reposition itself, especially if options include diet, and caffeine- and arti cial sweetener-free. Product life cycle management is one of the key ways to reduce waste in the beverage manufacturing industry. From design to disposal, a beverage can or bottle typically goes through ve life cycle stages, requiring signi cant resources and inputs to deliver a nal product. Sourcing raw materials, manufacturing and packaging, transportation, usage by the consumer and throwing away the waste are key points in a product’s journey and can be “made greener” to produce less waste.
“The design stage of the product is the best time to address sustainability,” says Lee-Hendor Ruiters, regional manager of the National Cleaner Production Centre. Ruiters is a fan of “eco-designing”, which uses less raw materials and energy and extends the life of the product. “If a product can easily be reused, repurposed or composted, then it is designed with the environment in mind,” he says.
Most South African beverage manufacturing companies will have to embrace eco-design practices. Ruiters explains that the pending Extended Producer Responsibility legislation will ensure producers take responsibility for the impact of their products on the environment.
DID YOU KNOW? Twizza has invested in improving its manufacturing capabilities to ensure that the PET in packaging is sustainable and reusable. Twizza also provides these manufacturing services to several local players. FROM RAW MATERIALS TO BOTTLING
There are several steps in bottling or packaging a soft drink, with greater ef ciencies being introduced all the time. Raw materials such as avourings, chemicals and sweeteners are mixed to different ratios according to a brand’s recipe. This “syrup” is then mixed with distilled water, carbonated and readied for packaging. Carbonation occurs by cooling the soft drink mix in large, ammonia-based refrigeration systems, which gives carbonated drinks their effervescence. Ninety-four per cent of the soft drink is made up of carbonated water. The bottling and lling process is highly automated (sophisticated lling lines can ll and bottle 1 200 containers per minute).
Source: Encyclopaedia of Occupational Health
ADDRESSING SUSTAINABILITY
and Safety
A LONG WAY TO GO
“We still have a long way to go in terms of recycling beverage cans and bottles in South Africa,” says Ruiters. About 95 million tonnes of waste still makes its way to 826 land ll sites and less than 40 per cent of that waste is recycled. “Encouragingly, though, there are more than 4 000 glasscollection points in South Africa, which is home to 32 dedicated ‘Collect-A-Can’ companies. These companies collect 72 per cent of all beverage cans and recovered more than 75 per cent of all metal packaging in 2019.”
Indeed, water shortages and load shedding are pushing companies to implement energy- and water-saving processes. “Together with local legislation and a global economic system that is becoming more circular-thinking towards sustainability, this means that South African beverage manufacturers need to adopt green policies urgently,” says Ruiters.