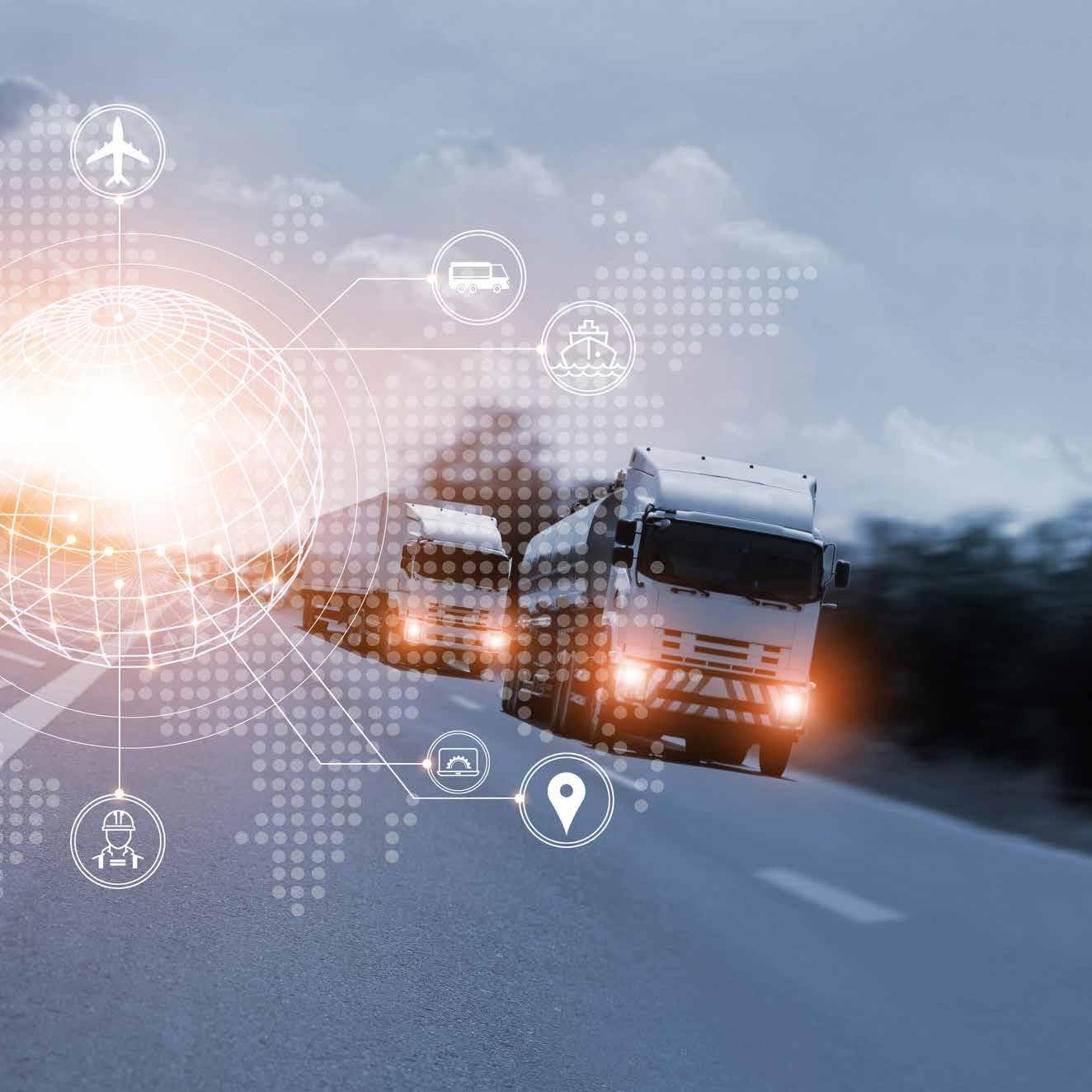



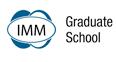

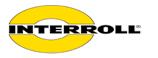
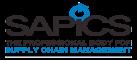

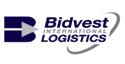
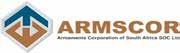
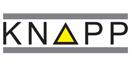

Africa’s major Retailers, the largest Beverage companies, the biggest Chemical Company and hundreds of small and medium-sized businesses ON THE LINEBOOKER PLATFORM
Unitrans has long understood the importance of making a difference in the communities where it operates, and continues to commit itself to driving change
Driving social change through impactful partnerships is core to Unitrans. The company is committed to uplifting and improving the quality of people’s lives.
“At Unitrans, we firmly believe in the power of doing,” says CEO Terry Bantock. “It is integral to our values and culture as a company. As part of our ongoing commitment to driving change in the communities where we operate, we have partnered with several leading organisations that are making a difference at ground level.”
Adopt a River is a passionate nonprofit organisation (NPO) dedicated to making a difference in the waterways. According to Liesl de Wet, Unitrans’ sustainability executive, the programme focuses on finding communitybased solutions to the myriad of river health
issues, from clearing the riverbanks of solid waste to providing work-based training programmes. Understanding that each river, each stretch, and each community is different and a one-size-fits-all approach does not work, the NPO delivers bespoke solutions for each project it undertakes.
“As a transport and logistics business, we understand the impact of our operations on the environment, and we intend to make a difference going forward,” explains de Wet. “We have prioritised several sustainability goals and have made a firm commitment to making a positive impact and being responsible in our consumption and everything we do.”
Working with Adopt a River, Unitrans has recruited a team of workers from the local community for a clean-up project of the Umhlatuzana River that runs past Unitrans’ Clairwood depot. The project, says de Wet, involves waste collection from the river,
tackling illegally dumped waste and cable theft, as well as controlling the alien invasive species along the riverbank. Within just two months, the on-site team collected more than 300 bags of waste – highlighting the need for action.
“We are extremely proud to partner with Unitrans and expand our environmental work into yet another river system,” says Janet Simpkins, founder and director of Adopt a River. “It is amazing to work with caring corporates, actively changing green spaces and directly impacting our waterways and lives.”
Highlighting the importance of protecting water resources and keeping them pollution-free at all times, de Wet says the need for water security, particularly in the face of global climate change, cannot be overemphasised. Furthermore, considering the multiple stressors impacting our rivers, now more than ever, a unified approach is required to protect our rivers, wetlands, and broader catchments.
Through the sponsorship and adoption of this river, Unitrans has not only contributed to the upliftment of the environmental space, but also the employment and capacity building of
“We have prioritised several sustainability goals and have made a firm commitment to making a positive impact and being responsible in our consumption and everything we do.” – Terry BantockInvesting in children in partnership with The Forward Foundation Unitrans has recruited a team of workers from the local community for a clean-up project of the Umhlatuzana River that runs past Unitrans’ Clairwood depot.
local community members. A future challenge is to engage communities and businesses upstream and downstream to join hands in cleaning up the Umhlatuzana River.
At least one-third of the food in South Africa is dumped. This comes as millions of South Africans face widespread hunger daily. Unitrans joined hands with FoodForward SA, an NPO that connects a world of excess to a world of need by recovering quality edible surplus food from the consumer goods supply chain and distributing it to community organisations that serve the poor.
“As an organisation involved in the distribution of food, we acknowledge and understand the importance of food systems. As a business, we have been creating innovative supply chain solutions for decades,”
comments Bantock. “By assisting with the maintenance of FoodForward SA’s fleet of vehicles, we ensure that the organisation can easily undertake the collection and preservation of food that would otherwise go to waste.”
But, says Bantock, it is not only through financial support and the servicing of vehicles that Unitrans supports FoodForward SA. “Several of our staff members volunteer at FoodForward SA’s Cape Town and Johannesburg warehouses – providing much-needed extra hands for the packing, sorting and labelling of food.”
Child protection and development is everybody’s responsibility. Supporting organisations that advocate for a better life for children is important to Unitrans, which is why it has partnered with the Forward Foundation to make a difference in communities by assisting with early childhood development (ECD) programmes.
According to Le Roux Conradie, founder and managing director of the Forward Foundation, a lack of ECD further entrenches poverty and marginalisation in the country.
“We give children in under-resourced communities access to physical education to afford them equal opportunity to succeed in life.”
Many South African children have no access to physical education. A variety of reasons
for this exist, including a lack of resources, confined spaces, no equipment and a lack of teacher training in the subject. Physical education is an essential building block for ECD and a vital part of learning to master control of one’s body and mind.
“Unitrans is committed to making a difference in the communities where we operate,” explains Bantock. “Partnering with the Forward Foundation enables us to do exactly that, by providing early childhood development skills and resources where they are needed most.”
Unitrans has helped fund the implementation of the Forward Foundation’s physical education programme at Raithby Primary School in the Western Cape and Kings Harvest Academy in KwaZulu-Natal. The company is also involved in projects at the Bienvenu Shelter in Gauteng, and the Home from Home children’s home and Emmanuel Educare Creche in Touws River in the Western Cape. For
“As a transport and logistics business, we understand the impact of our operations on the environment, and we intend to make a difference going forward.” – Liesl de WetFighting hunger in partnership with FoodForward SA Unitrans has helped fund the implementation of the Forward Foundation’s physical education programme at schools in the Western cape and KwaZulu-Natal.
10 TRENDS
The Fourth Industrial Revolution is transforming logistics by intelligently connecting all aspects of the supply chain.
11 THOUGHT LEADERSHIP – BOOSTING YOUR PERFORMANCE EDGE
Making the supply chain more effective by leveraging technology to connect people, assets and data.
20 TECHNOLOGY
Gaps still exist in the digital supply chain, but these can be closed through the implementation of relevant technology.
22 THOUGHT LEADERSHIP – OT AND IT CONVERGENCE
The continuing convergence of information and operational technology is set to significantly and positively impact the modern supply chain.
23 LOCALISATION
COVID-19 demonstrated the challenges of long and complex supply chains. How would shortening and localising these chains improve things?
26 THOUGHT LEADERSHIP – ELECTRONICS AND EPR COMPLIANCE
Producers of electronics are accountable for the whole life cycle of the products they market and sell, from conception to post-consumer waste disposal.
30 GLOBAL TRANSPORT
Multimodal shipping hubs hold enormous potential for the future of the supply chain.
38 THOUGHT LEADERSHIP – DE-RISKING THE SUPPLY CHAIN
International supply chains have many complex and foreign networks, policies, and practices - how can risk in such complex environments be minimised?
39 MATERIALS HANDLING
It is vital that South Africa’s rail network be improved to reduce the impact transport logistics is having on our roads. The answer is to allow private operators access to Transnet’s rail infrastructure.
42 THOUGHT LEADERSHIP – PALLET POOLING
As supply chains become increasingly complex, global pallet-pooling systems offer adaptability, efficiency, and sustainability.
44 TRAINING
In a world where the environment is top of mind, we look at how training entities are bringing together the increasing need for supply chain skills and the growing demand for sustainable practices.
48 ELECTRIC VEHICLES
Electric vehicles are the future, but what roles will these ultimately play in the supply chain and what sort of impact are they already having?
49 THOUGHT LEADERSHIP – REDUCING SUPPLY CHAIN COSTS
Retreading of tyres and utilising remanufactured spares from the OEM are
54 SUSTAINABILITY
The principles of the circular economy are being implemented in the transport industry through more efficient vehicle utilisation, better route planning and improved recycling processes.
58 THOUGHT LEADERSHIP – MANAGING MASTER DATA
Effectively managing your organisation’s master data is an ideal method by which to optimise supply chains.
64 PROFILE: LINEBOOKER
While the “as-a-service” model has taken root in many industries, we investigate how its application in the transport space is revolutionising the logistics arena.
65 THOUGHT LEADERSHIP – THE SUPPLY CHAIN TECHNOLOGY GAP
How we can overcome the technology gap that creates the disparity between potential and actual supply chain digitisation gains?
69 CONSULTING
The supply chain has faced multiple new challenges in recent years, and the role of the supply chain consultant has become
The supply chain sector has been severely impacted in the past couple of years. The challenges of COVID-19, the desire to shorten supply chains or to digitalise them, and the growing clamour for sustainable practices to be implemented are just some of the issues facing this industry.
In this issue we consider how the latest Fourth Industrial Revolution technologies will affect the supply chain arena, and which of these solutions will most effectively drive real transformation.
At the same time, there remains a disparity between the potential and actual gains achieved from supply chain digitalisation. We look into why these gaps exist and how to plug them.
There is a theory that shorter, more localised supply chains might be the future for this industry, especially in the
wake of the challenges created by the pandemic across world-spanning supply chains. Despite this, others see a future in global supply chains, placing their faith in multimodal shipping hubs as the future of worldwide transport and logistics.
One thing that is clear is that materials handling in South Africa can only be improved by allowing private operators access to Transnet’s rail network. In this issue we look into the benefits that might spring from adopting such an approach.
We examine the role electric vehicles will play in future supply chains, how the “as-a-service” model is being adopted into logistics, and the manner in which more efficient vehicle utilisation and better route planning can impact the circular economy.
Finally, none of the above can be achieved without relevant skills, so it is worth considering the supply chain competencies that are most in demand – notably those focused on sustainable practices – and the deepening role of the supply chain consultant in an industry facing constant change.
With continuing advancements in technology and ongoing changes in the people and processes spaces, it seems clear that the supply chain industry is one that will remain in a state of flux for some time to come.
Rodney Weidemann EditorPicasso Headline, A proud division of Arena Holdings (Pty) Ltd, Hill on Empire, 16 Empire Road (cnr Hillside Road), Parktown, Johannesburg, 2193 PO Box 12500, Mill Street, Cape Town, 8010 www.businessmediamags.co.za
EDITORIAL
Editor: Rodney Weidemann
Content Manager: Raina Julies rainaj@picasso.co.za
Contributors: Gary Allemann, Sean Bacher, Trevor Crighton, Heinrich de Leeuw, James Francis, Neil Gouveia, Gareth Griffiths, Velile Malaba, Denise Mhlanga, Itumeleng Mogaki, Trevana Moodley, Elvis Mutseura, Chris Perumal, Patricia Schröder, George Senzere, Anthony Sharpe, Benjamin van der Veen
Copy Editor: Anthony Sharpe
Content Co-ordinator: Vanessa Payne
DESIGN
Head of Design: Jayne Macé-Ferguson
Senior Design: Mfundo Archie Ndzo
Advert Designer: Bulelwa Sotashe
Cover Image: ipopba/istockphoto.com
SALES
Project Manager: Tarin-Lee Watts wattst@picasso.co.za | +27 87 379 7119 I +27 79 504 7729
PRODUCTION
Production Editor: Shamiela Brenner
Advertising Co-ordinator: Johan Labuschagne
Subscriptions and Distribution: Fatima Dramat fatimad@picasso.co.za
MANAGEMENT
Management Accountant: Deidre Musha
Business Manager: Lodewyk van der Walt
General Manager, Magazines: Jocelyne Bayer
COPYRIGHT:
Some feel that shorter, more localised supply chains might be the future, while others look to multimodal shipping hubs, which depend on global supply chains.
A strategic partner of choice for defence and security solutions.
South africa’S preferred cu S tom S clearing, forwarding and accounting S oftware provider
Efficiency through technology meticulously designed for the freight industry make the change to the
There is little doubt that 4IR will change the supply chain arena significantly, but how will these technologies shift the dial, asks
RODNEY WEIDEMANNDigitalisation brings about Supply Chain 4.0, which will be faster, and more flexible, granular, accurate and efficient. It will also allow for new transport concepts, such as drone delivery, and facilitate new business models, such as supply-chain-as-a-service.
Source: McKinsey
Like every other area of business, the supply chain is being impacted by the growing adoption of Fourth Industrial Revolution (4IR) technologies, as businesses increasingly digitise their processes. Moreover, the speed of this evolution has increased as the supply chain has had to adapt to multiple global factors that have significantly impacted it in recent years, including the pandemic, increasing shortages of components and international conflicts.
Neil Gouveia, director for Africa at Zebra Technologies, says that one of the key benefits technology offers is the ability to automate the supply chain from source through transport, processing, dispatch and delivery. “When technology isn’t automating, it should be augmenting front-line workers, giving them and their managers greater visibility, making tasks easier, and ensuring workers are better connected to each other, the assets they need and the inventory they’re working with.”
Jonathan Duncan, VP of Anglophone Africa for Secure Power Solutions at Schneider Electric, has seen increasing demand for real-time smart supply chain solutions. “Digitalisation supports the building of a streamlined customer-centric supply chain. Unless operating processes are connected, systems and tools cannot truly operate in
conjunction to support the needs of customers or the business. System connectivity also allows the supply chain to react better to customer demand and mobilise accordingly.”
Duncan notes that suppliers can be fully integrated into an “extended supply chain”, thereby enabling transparency and traceability. Digitalisation also becomes the foundation for circularity, he adds. “It can open manufacturing to all shareholders in the product chain and often changes the relationship, with informed discussions between suppliers.”
Gouveia agrees that the volume and pace of demand mean higher levels of accuracy, speed and productivity are needed across the supply chain. “However, before technology can solve problems, it is imperative that industries are made aware of what’s available. It’s not about having the newest 4IR technology, but rather the most appropriate one for a business.
“I would say that the Internet of Things (IoT) as a framework is useful, but we are already well beyond thinking about IoT as the goal. Businesses instead need to be able to sense what’s happening across the supply chain, using various tools like barcodes, QR codes, radio frequency identification and temperature sensors.”
With these come fixed and handheld scanners to capture all that data. However, it must be remembered that IoT and big data aren’t enough if they’re not being used to provide analysis of what’s happening, says Gouveia. “That’s where things like software using machine learning for predictive analytics comes in. What patterns are in my supply chain data? What correlations are there, and what external factors are affecting the supply chain? From there, we can move to turning analysis into action and decision-making, as artificial intelligence and advanced analytics build upon IoT.”
Duncan says that digitalisation involves using intelligent devices and sensors that collect data from equipment, storage bins and processes. However, to successfully collect, manage and analyse the data, supply chain operations also require edge computing solutions. “Edge computing supports digitalisation by placing computing power, storage, and analytics close to these data sources and the users. It reduces latency and enables the efficient management of massive amounts of industrial IoT data in real time.”
Gouveia believes today’s goals will become tomorrow’s trends, suggesting that ecosystems of automation using machine-vision systems, robotic automation and software will become diffuse and much more the norm. “Some businesses and industries are further along than others, but they’re all heading in the right direction. We can expect to see optimal productivity, speed, accuracy and harmony among different parts of the supply chain, including a real-time loop between data, analysis and decision-making.
“We’re now seeing more discussion about Industry 5.0, where things like sustainability and a more human-centric approach to the role and well-being of workers will have more prominence,” Gouveia concludes.
“It’s not about having the newest 4IR technology, but rather the most appropriate one for a business.” – Neil Gouveia
NEIL GOUVEIA , director for Africa at Zebra Technologies, outlines the three technological steps that help to connect people, assets and data
Supply chain challenges continue as retailers, warehouse operators and manufacturers struggle to keep up with accelerated demand that shows no signs of slowing. E-commerce is driving rapid growth in volume and speed of orders and returns. It’s hard to keep pace, and we know that visibility is a top supply chain goal. In fact, in a recent study on technology and the supply chain, 91 per cent of respondents said that a lack of real-time inventory visibility was their top priority for overcoming supply chain obstacles.
While you may be doing some things right, without visibility you won’t be able to reach excellence and exceed customer expectations. If you want to achieve a supply chain edge, you need to start seeing what’s happening throughout your supply chain – from inventory to transportation, logistics and fulfilment.
Start with sensor and RFID technology
Barcoding technology has been around for decades, providing insight into the inventory across the supply chain and offering visibility into what you have, but developments in technology now allow us to do more.
Take sensor technology, which offers additional visibility in your normal or cold supply chains. Rather than having manual processes, you can use wireless temperature sensors and colour-changing, temperature-sensing labels that automatically capture heating, freezing and shipment temperature data, giving you the ability to see inventory conditions across the supply chain.
An important added sensing layer is radio frequency identification (RFID), which may be reaching a pinnacle moment as businesses face the same or greater volumes of work at higher speeds, without additional labour. RFID tags, readers and systems enable you to see assets and inventory in your supply chain in near real time, delivering visibility into inventory, logistics and fulfilment.
Handheld RFID readers can make asset and inventory counting highly accurate and fast, even across distances, while fixed RFID readers can automate the tracking of goods on the conveyor, and in and out of the warehouse.
Businesses can reduce complexity and cost by leveraging an intuitive, unified software platform with a modern user interface that can easily set up, deploy and run fixed industrial scanning and machine vision solutions, as well as integrate them into factory or warehouse systems.
In a warehouse setting, fixed industrial scanners can look for the presence or absence of labels and data, while machine vision systems can be trained to look for shapes or logos on a label. When the item passes under the camera, it will check for that shape/logo to ensure presence and proper positioning. In sorting, it will look for the courier logo and redirect the package to the right line for onward distribution.
Machine vision systems can also measure brightness or perform a pixel count within a search region on the label. These are powerful solutions that imaging engineers, programmers and data scientists can use with software tools to match different levels of expertise.
Our third step is robotic automation. These are easy-to-deploy solutions for a range of warehouse and factory materials movement use cases. There are autonomous mobile robots (AMRs) for pallet transport and cart connections, as well as rollertop and order fulfilment. These robots can help solve efficiency challenges related to storage carousel transport, work cell and lineside delivery, replenishment, cycle counting and recycling and rubbish removal.
Solutions come ready out the box, so setup and deployment can be achieved in a matter of hours or days. Robotics software features easy-to-use graphical drag-and-drop interfaces, enabling customisable workflow solutions. API add-ons allow data from external devices like mobile computers, tablets and barcode scanners to trigger or continue a workflow. Software also provides an easy way to assign robots to workflows and define when and how often workflows are executed.
Depending on the use case, businesses have secured two or three times their previous throughput, obtained floor space and productivity gains, and saved operators over 30km in manual travel per day through these solutions.
Zebra’s recent Warehouse Vision Study found that 90 per cent of warehouse operators around the world plan to deploy some form of AMR within five years. In addition, 83 per cent of associates working alongside AMRs today confirm they have increased productivity and reduced walking/travel time, while 73 per cent reported reduce errors.
Robots can help solve efficiency challenges related to storage carousel transport, work cell and lineside delivery, replenishment, cycle counting and recycling and rubbish removal.Neil Gouveia
They work the night shift, do the heavy lifting, sort, create sequences, calculate packing patterns and know how to stack sensitive items gently and precisely. Today’s robots are highly intelligent, high-precision tools that come in a variety of forms. How do they do it all? It’s simple: with the help of smart software. The software creates a network among the robots while their artificial intelligence (AI) has them learning from each other or getting the data they need on items. Below are three ways that robots and their software can be used in a warehouse to improve efficiency.
Delivery to grocery stores made easy. KiSoft Pack Master calculates the optimal packing pattern for the load carrier as soon as an order is started. This information is then provided to RUNPICK, our Robotic Universal Picker. RUNPICK processes and palletizes the entire range of food items fully automatically for delivery to stores. This technology is capable of multiple picks and building mixed layers on the load carrier, which results in an improved performance in the warehouse. All the “blocks” fit neatly into the pre-calculated space. The employee at the store has also been considered – the software provides everything necessary for a store-friendly delivery
Warehouse-internal transport and supply with smart robots. Universally applicable, the fleet control system KiSoft FCS efficiently manages our Open Shuttles as well as manually operated vehicles or the AMRs of other manufacturers. What’s more, a simulation environment that the customer can operate themselves allows them to immediately determine whether an AMR can be given tasks, what the size of the fleet should be and make adaptations to processes.
Discover more about KiSoft FCS for easy fleet control.
Goods-to-robot picking: how to make fully automatic bin picking work. The KiSoft Artificial Intelligence software program helps our Pick-it-Easy Robot to collect and securely save data from live operation, train neural networks, as well as validate, manage, and roll out generated models to robot cells in the customers’ systems. Open interfaces as well as IT and data security solutions make many applications possible. Quality assurance and demand forecasting are other successfully established applications of KiSoft Artificial Intelligence.
KNAPP Logistic South Africa (PTY) Ltd
Long Point Building, 2nd Floor
Bradfield Drive
Magaliessig, Gauteng, 2067 South Africa
E-Mail: sales.za@knapp.com
Find out more about the advantages of the Pick-it-Easy Robot.
Further information on full automation in food retail.Today’s consumers want their shopping to be low-effort, ideally 24/7 and a great user experience. As a result, new business models have developed. But where does software come into play? How does data add digital value? Our logistics concepts support our customers as they implement their new, up-to-date business models. Our software plays a central role in these concepts and creates added value along the entire value chain. Let’s have a look behind the scenes of some of our solutions.
In Lyon and Paris, our partner Intermarché handles 1,000 orders every day with two micro fulfillment centers (MFCs). A single order can comprise up to 40 different food items from four temperature zones. The software calculates which items can be processed automatically and where the best storage location for each item is. It also makes sure that all items end up in the correct shopping bag.
Intermarché works with our software solution for MFCs, the Multi-Site Control Center (MSCC). The service solution
Our in-store solution RetailCX lets end customers shop around the clock with ease. They can order a wide range of goods, such as cosmetics, cleaning products, groceries, electronics, tools and DIY supplies, jewelry or shoes with a few taps in their smartphone app or at the terminal in the store. Their order is dispensed fully automatically. The end customers can choose to see targeted offers and news in their apps based on the data collected. The perfect user experience is just a few clicks away: The user interfaces on
Another solution that adds digital value is our Apostore, a smart dispensing robot designed specially for pharmacies. In the Netherlands, a pharmacy uses Apostore to serve their patients remotely, around the clock. The pharmacy is located in Eindhoven, while the 24/7 terminal is a few miles away in Veldhoven.
• The patient uses their health insurance card to identify themselves at the terminal. The pharmacist and the patient can then talk using video cameras connected through the web. The pharmacist checks the prescription.
supports round-the-clock operation for food retailers with MFC concepts. Continuous system checks detect any incidents early, before they impact the operation at all. In one overview, the MSCC displays all our systems and all logistical and technical processes. We check the software as well as the hardware of the system. Specially developed index numbers show the MSCC team the system’s status. This is one of the special advantages of the MSCC: The service solution can combine and analyze key figures from multiple locations.
the terminal can easily be updated to show new dynamic content. Another advantage is that RetailCX employees at the point of sale spend less time at the checkout counter and restocking shelves, leaving more time to create an outstanding experience for customers. The store can also operate efficiently with fewer employees, a bonus in times of high personnel costs and labor shortages.
• Then the built-in robot retrieves the medicine and applies a sticker with information on how and when to take it.
• Before dispensing the medication, the system transmits a photo to the pharmacist who double checks and documents the medication. If everything is correct, the medicine is dispensed to the patient.
• If there are any questions, the patient can ask them using the video link.
Apostore makes it possible for patients to receive medicine and competent consultation round the clock.
As you can see, combining digital solutions and innovative automation technology has great potential for more efficiency, better service and reduced costs at the point of sale and on the last mile.
KNAPP
Long Point Building, 2nd Floor
Bradfield Drive
Magaliessig, Gauteng, 2067
South Africa
E-Mail: sales.za@knapp.com
Despite much innovation, the disparity between potential and actual gains from supply-chain digitalisation can be blamed on technology gaps. ITUMELENG MOGAKI looks into what these gaps are and how to fill them
Transformation of SMEs using digital technologies is critical to their internal operations, because these are used for a variety of purposes. These include communication, transactions, sales recording and processing, automation, production planning and stock control, document management, marketing, general accounting and finance.
Source: Graduate School of Business Leadership – Unisa
The implementation of a truly digital supply chain is being hindered by technology gaps, which exist for the simple reason that there is no one-sizefits-all technology solution for creating a perfect value chain.
Leon Steyn, CEO of Dante Deo Consulting, explains that from 2020, organisations began accelerating their digitalisation journeys to ensure survival and weather the storms of uncertainty. “Companies found new delivery models, organisational decision support systems and process control solutions. All of these advances did, and are continuing to, place pressure on to the supply chain. However, despite technological innovation, the disparity between potential and actual gains from supply chain digitalisation can be blamed on the technology gap.”
So what is this gap and where in the supply chain does it exist? Steyn indicates that analysing the available technologies that could meet the supply chain’s visibility, insight, research and administration (VIRA) needs, it is clear there are several solutions in the market that can address the organisational requirement for the VIRA, but there is not, and there will never be, a single solution.
“Organisational supply chain functions require an ecosystem of technologies that work together, integrate and automate. However, sometimes organisations focus only on a component or two of the VIRA – most often visibility and administration – but they neglect other components.
“In the context of the supply chain VIRA, the technology gap will exist within the component that has the lowest level of maturity. In today’s supply chain, this creates a weak link that inhibits the digitalisation potential.”
Complex supply chains also find it more difficult to reach VIRA maturity, which requires greater investment in the technological ecosystem and a higher degree of organisational change. “Therefore, the technology that is needed to enable the actual gains of a supply chain digitalisation journey will be dependent on the complexity and VIRA maturity, combined with the adoption and integration of the VIRA technology environment,” says Steyn.
According to Corrie Janse van Rensburg, MD of KNAPP Logistic South Africa, in this day and age, logistics concepts such as process optimisation, personnel assignment
planning and efficiency are all part of the world of software. “This makes mastering the management and optimisation of entire logistics systems across multiple steps of a value chain one of the most demanding challenges. The old software hierarchies in logistics have served us well, but they are now changing. There used to be clear boundaries between the enterprise resource planning and supply chain levels, whether in warehouse management systems or warehouse control systems.”
Growing integration, higher-performing systems and, above all, cloud computing have allowed systems to overlap increasingly. This creates exciting new opportunities for process design along value chains because data is generated every step of the way, says Janse van Rensburg. “Data that can be integrated in real time and made available in different systems means that the intelligent solutions in software suites provide more insights than ever before into the processes taking place in the value chain.”
Artificial intelligence (AI) and robotics are two other technologies that are now developed enough to be used in the industry. These have the potential to change the world of logistics
“Organisational supply chain functions require an ecosystem of technologies that work together, integrate and automate.” – Leon SteynCorrie Janse van Rensburg
forever, especially considering issues regarding shortage of skilled workers and increasing costs. Janse van Rensburg says AI allows for continuing optimisation and reserves labour-intensive tasks, such as maintaining master data, for robots.
“Although there is no one-size-fits-all solution for creating the perfect value chain, using intelligently integrated solutions makes optimising and reviewing processes across multiple levels, from the manufacturer to the end customer, significantly easier,” says Janse van Rensburg.
Jona Pillay, Omnia’s group executive for manufacturing, operational and supply chain, says that a lack of digital literacy, combined with a shortage of affordable and accessible internet connectivity, is hindering the adoption of new and innovative technologies in the supply chain. “The cost of digitalising supply chains can be prohibitively expensive for many small and medium enterprises (SMEs), particularly those in rural areas. The high cost of equipment, software and training can make it difficult for these businesses to make the necessary investments in technology, which further exacerbates the technology gap.”
The consequences of this gap are significant, not just for individual businesses, but for the wider South African economy, continues Pillay. “By failing to take advantage of the latest technological advancements, businesses are losing out on the many benefits of digitalised supply chains, including increased efficiency, lower costs and improved customer satisfaction.”
Pillay adds that in order to bridge the gap and fully realise the potential gains of supply chain digitalisation, it is essential that local businesses, particularly SMEs, receive the support they need.
According to the Körber 2022 Supply Chain Benchmarking Report, nearly two-thirds of leaders in end-customer experience say they have IT vulnerabilities, despite security measures – a worrisome statistic, as an attack on one system can impact the entire supply chain.
“This could include government initiatives to provide affordable and accessible internet connectivity, as well as investments in digital literacy and skills training programmes.”
Grant Marshbank, CEO of VSC Solutions, explains that budget is often a barrier to the implementation of technology, even that which is ultimately designed to result in a saving of between five and 25 per cent in supply chain costs, over the medium and long term.
“There is also no doubt that there is currently a skills shortage in South Africa when it comes to experienced technology resources in the supply chain,” says Marshbank. “Technology in this space is always evolving and, depending on the function it performs, has many degrees of complexity and automation. A lack of experienced resources to drive these technologies in day-to-day operations creates large gaps in getting optimal outputs, cost savings and automation, as well as a faster return on investment on the technology investment.”
He indicates further that although technology by nature is designed to streamline and automate, it is the combination of the people, processes, and technology that ensures successful implementation. “Companies are faced with the difficult decision to transfer or promote current employees, to look for experienced resources in the market, or to employ and train new entrants to the job market for these positions. Promoting current employees to technology-related roles requires at least some experience in the industry and day-to-day operations of the organisation, but often these people lack either the technological background or the aptitude to get the maximum value from the investment.”
Marshbank says that for business continuity and resource retention, it is crucial to spend
the necessary time finding the right-fit people for these positions. “This includes conducting psychometric tests with a specific focus on behavioural assessments, ideally benchmarked against a pool of previously successful and high-performance recruits.”
Marshbank cautions that investing in the wrong technology will impact productivity negatively, by increasing the dependence on people and processes to compensate for its shortcomings.
“Configurability and ease of integration are key in this decision, to make sure that the technology can be easily adapted to the ever-changing supply chain. Due diligence is crucial when investing in technology to improve productivity, and enable automation and optimisation in
“There is no doubt that there is currently a skills shortage in South Africa when it comes to experienced technology resources in the supply chain.” – Grant MarshbankGrant Marshbank Jona Pillay
Supply chains across industries are notoriously complex at any time, and even more so for companies with a global reach. The industry is extremely competitive, with some companies utilising mind-boggling innovations, which means these organisations continuously have to ensure they stay one step ahead of the competition.
Supply chains remain fragile, but if all the proverbial cogs are running smoothly, the benefits are numerous: cost reduction; decreased inventory; and increase in asset utilisation.
To realise the above, many organisations are moving towards supply chain digitalisation, which in turn provides them with visibility and an entry point allowing them to gain a full view of their end-to-end supply chain networks.
Big data is also driving the move towards digitalisation, with huge amounts of information being collected across the entire chain network. With real-time, accurate data, companies can swiftly pivot and respond to drastically changing situations, and ensure that their responses are on point. Access to the latest available information is vital, for example, when dealing with constraints on supplies and transportation.
In challenging environments, industry is also implementing digital track-and-trace systems, using radio frequency
identification (RFID) tags instead of barcodes, increasing visibility into the supply chain by providing valuable real-time data.
RFID offers great benefits, as it can be read by proximity sensors remotely, with the data quickly aggregated into the cloud and interchanged through various other Internet of Things systems. When data is gathered this way, it enables quicker execution of equally important tasks or processes, which might include observing transit conditions of goods, inventory automation, various forms of reporting and dashboarding and, of course, automated replenishment of inventory – all without human intervention.
The collected information also supports business intelligence with the visualisation of various metrics, which offer rapid updates of vital information such as tracking staff levels year-on-year, or inventory volumes. In short, digital track-and-trace simply outperforms humans in terms of processes.
and flexible, and offer the ability to speak to other systems outside of their primary domains.
The interoperability of OT systems can break down information silos, while providing organisations with the ability to integrate with various IT systems. In fact, we are going to see IT functionality increasingly being built into OT, allowing these systems to connect seamlessly with the cloud and work in conjunction with on-site edge applications, for example.
There is no doubt that the continued convergence of IT and OT has a lot to offer, but it is also worth noting that the human element remains key. Training must be prioritised to ensure employees are well versed in newly deployed technologies and systems.
George SenzereConsidering the above, it’s clear that operational technology (OT) needs to evolve – and quickly. Traditionally, OT controls physical hardware and takes care of safety. Today, the lines between OT and information technology (IT) are blurring rapidly. In the past, OT systems such as supervisory control and data acquisition and distributed control systems were proprietary; today, these systems are open
Here, an interesting and even immersive training approach would be to use the simulation of the actual processes in a digital twin environment. In this setup, a virtual environment mimics real-world operations, with processes very similar to the real thing. This environment can be used to provide training for the would-be operators. It is indeed a powerful training tool, as the environment can be made available prior to actual implementation. This is vital, as it means that employees are familiar with the necessary processes and can hit the ground running.
The continuing convergence of information and operational technology is set to significantly and positively impact the modern supply chain, writes GEORGE SENZERE , solutions architect at Schneider Electric
With real-time, accurate data, companies can swiftly pivot and respond to drastically changing situations, and ensure that their responses are on point.
The pandemic demonstrated the challenges that extremely long and complex supply chains face in the wake of a global crisis. Many are now suggesting that shorter, more localised supply chains might be the future. ANTHONY SHARPE investigates
Gobalisation changed supply chains, stretching their filaments further across the globe, tangling them ever more into the cat’s cradle of design, production, logistics, sales and consumption that characterises life in the 21st century. Shifting consumer demands and expectations have only served to ensnarl things further.
These globe-spanning supply chains have been established with maximum efficiency in mind, but when one link is disrupted, the ripple effects are felt up and down the chain.
The greatest disruption to have occurred in the history of supply chain management began in early 2020, as the COVID-19 virus swept across the world. The initial response of many businesses to the disruption of their lengthy supply chains was to begin exploring ways to shorten them by localising or regionalising their supply and production networks, reducing reliance on manufacturing giants like China. However, many soon realised how difficult this would be. A May 2020 McKinsey survey revealed that many businesses had plans to nearshore production or regionalise their supply chains; a year-and-a-half later, a follow-up survey found that in practice, they were much more likely to increase their inventories instead.
The trend towards moving away from China was actually underway before the pandemic hit, says Mungo Park, senior director of consumer, retail and fashion at DSV. “It was initially driven by
A survey of supply chain executives found that increased efficiency and visibility, along with retaining and reskilling the workforce, are the top priorities for businesses over the next three years.
Source: EY
rising labour costs there. The pandemic disrupted it as businesses scrambled to get products wherever possible.”
Park says that as the pandemic has receded, the potential disruption of the China/Taiwan situation, other geopolitical factors in Asia’s largest country, and the desire for reduced costs and greater logistics control have driven this trend further.
Nearshoring initiatives will look different around the world, adds Park. European nations, for example, will look to Eastern Europe as an alternative to the East, while the US will look to
Latin America and also try to promote production internally.
“This creates opportunity for local companies in South Africa to catch the manufacturing wave as production moves away from China,” he notes. “These companies need to promote their capabilities as suppliers for the larger retailers. These retailers have built relationships with reliable suppliers over years. They understand the quality that they get out of their various suppliers, so identifying a new bunch doesn’t happen overnight.”
Localising supply chains requires South Africa to ramp up its manufacturing capacity, which has steadily eroded over decades. “We’ve always had good apparel manufacturers, for example, and I think they can develop some high-tech manufacturing capability,” says Park.
Developing these advanced capabilities is key. Park points to the example of China, which has moved away from low-cost, low-tech manufacturing towards more complex sorts, because these generate higher return. “South Africa is going to have to find a way to reskill and upskill its labour force in order to play in the more technically competent manufacturing space. The intellect is there, and there’s a lot of good scientific capability. The challenge comes when you look labour costs and productivity levels, as well as upskilling the labour force, which is necessary to move into a more high-tech manufacturing capability.”
For South Africa and the continent at large to shorten supply chains, we need efficient logistics infrastructure. Park says East Africa, in particular, has seen major investment in such infrastructure. “I’ve recently seen a couple of global customers looking at sourcing more out of Ethiopia too, so they’re moving even further north and widening that East African footprint. By and large, Africa does have the infrastructure, as long as it continues to be maintained.”
One element of effective, cost-effective local supply chains that has seen poor maintenance, particularly within our borders, is rail infrastructure. “The rail-versus-road debate goes on in every country,” says Park. “The fact is that rail is slower, and once road transport operators control the movement of goods, it’s really difficult for rail to wrest that back, no matter what they invest in upgrading their facilities. However, I think that infrastructure does exist and that as the movement of goods increases, there should be greater investment in this space.”
“South Africa is going to have to find a way to reskill and upskill its labour force in order to play in the more technically competent manufacturing space.” – Mungo Park
The legal criteria for Extended Producer Responsibility came into effect in May 2021, aiming to ensure that producers are accountable for the whole life cycle of the products they market and sell, from conception to post-consumer waste disposal.
By PATRICIA SCHRÖDER , spokesperson for Circular Energy NPCIn South Africa, potential producers are defined under the Extended Producer Responsibility (EPR) regulations to include the full value chain: from manufacturers and converters to refurbishers, importers and brand owners.
Any persons or category of persons involved in the commercial manufacture, conversion, refurbishment, or import of any new or used EPR items also fall under this category. Manufacturers and importers of packaged goods also fall under the definition of “producers” of packaging materials, and will be impacted. The onus now also falls on producers, a decision that is a game changer.
Before the passing of the EPR regulations, the public – including local governments and businesses – bore the full financial burden and responsibility of waste collection and disposal. These regulations return the onus of responsibility to the producers of electric and electronic equipment, lighting and light equipment, and paper, packaging, and single-use goods. They must be accountable for a product’s whole lifespan.
It is intended that by making manufacturers financially and/or operationally accountable for their end-of-life products, more waste will be kept out of landfills, and more recycling and other circular economy initiatives will gain traction.
A producer of electric and electronic equipment, lighting and light equipment, and paper and packaging must be either the brand owner of the items using the packaging, the retailer in the case of house brands, or the importer of the goods contained in the packaging, according to international best practice. As it engages all stakeholders at every level of the packaging value chain, this innovative strategy might be a workable means to move towards sustainable waste management and a circular economy.
A PROs primary goals are to:
• Use a compliant, effective and efficient system, while adhering to stringent governance principles
• Promote and put the concepts of the circular economy into practice
• Contribute to the Sustainable Development Goals (SDGs), in order to make a real difference in the world
• Care for the environment with a multifaceted, best-practice strategy
With the development of the 2023 EPR plans under way, it goes without saying that the focus now falls on the submissions and ability of producer responsibility organisations (PROs) to meet the legislative requirements. It is now mandatory for producers to register with the Department of Forestry, Fisheries and the Environment (DFFE) on their website, and to ensure that all recognised products are covered by an appropriate EPR Scheme. PROs can assist in reducing the administrative workload by ensuring that they also join an existing PRO, or create and submit an independent EPR scheme to the DFFE for their electric and electronic equipment, lighting and light equipment, and packaging.
Joining a PRO is extremely beneficial, as it can help producers to become compliant through its take-back scheme. In order to ensure that their producer members are fulfilling their legal obligations under the EPR regulations, PROs are ideally positioned to offer them the advice and services they may require.
In addition, the interests of the various sectors should be safeguarded to ensure the entire takeback scheme is both effective and affordable for producers. This entails meeting all legal requirements in accordance with bestpractice principles.
It is the responsibility of the PRO to drive sector-based waste minimisation programmes; manage financial arrangements for funds to promote the reduction, reuse, recycling and recovery of waste; drive awareness programmes; and innovate new measures to reduce the potential impact of products on health and the environment.
It is intended that by making manufacturers financially and/or operationally accountable for their end-of-life products, more waste will be kept out of landfills, and more recycling and other circular economy initiatives will gain traction.Patricia Schröder
Our Mission
Through our expertise, innovative technology, and absolute commitment to service, we ensure that all our customer’s needs are met.
Main Service Offerings
Our reach
South Africa
Namibia
Botswana
Lesotho
Swaziland
• Long haul transport throughout South Africa
• Cross border transport to and from South Africa
Zimbabwe
Zambia
Malawi
Mozambique
The DRC
• Local transport solutions including dedicated and ad hoc requirements of bulk and part load consignments
• Consolidation services in South Africa and to cross-border countries
• Container transport and tri-angulisation
Before COVID-19 hit, e-commerce was growing at a steady rate, but the pandemic disrupted the traditional retail market by driving consumers towards online retailers.
Logistics companies had to adapt to this new trend to meet both consumer and retailer needs at a time of disruption.
DSV’s Johan Roos and Christopher Rugg say e-commerce’s growth and future potential is being driven by consumer safety, accessibility and convenience needs. They point out that it is also broadening the retail space because it offers entrepreneurs exceptionally low barriers to entry.
“A growing number of shopfront platforms are creating low-barrier opportunities for entrepreneurs. This is especially powerful when coupled with end-to-end logistics solutions that offer order fulfilment and eliminate the need for retailers to own warehousing and delivery vehicles. DSV shares the vision of a diverse and expanding e-commerce market and is investing accordingly,” says Roos.
The latest NielsenIQ Barometer Study, which surveyed 11 000 consumers from 12 different countries, including South Africa, found “53 per cent of grocery purchasers … bought groceries online in the past 6 months, of which 16 per cent bought more than half of their groceries online”.
Statista, a leading provider of market and consumer data, says e-commerce revenue is “expected to show an annual growth rate (CAGR 2023–2027) of 12.46 per cent, resulting in a projected market volume of US$11.12-billion by 2027”.
Statista also expects the number of users in the retail delivery segment to reach 5.8 million by 2027, and “user penetration will be 7.2 per cent in 2023 and is expected to hit 9.1 per cent by 2027”. Revenue in the retail delivery segment is “projected to reach US$0.64billion in 2023. Revenue is expected to show an annual growth rate (CAGR 2023–2027) of 10.49 per cent, resulting in a projected market volume of US$0.96-billion by 2027”, according to Statista.
Roos and Rugg say the data confirms DSV’s experience of a South African market that’s growing exponentially. Importantly, outsourcing your fleet reduces cost and risk for new and existing businesses.
By utilising DSV’s customer-centric software, customers can access an end-to-end logistics solution. Collection and delivery addresses are verified and georeferenced upfront to ensure first-time collection and delivery.
DSV can integrate customers’ order fulfilment needs with online shopfronts such as Shopify, Magenta and WooCommerce, leaving retailers free to focus on their core business. DSV’s solutions include:
• Easy onboarding;
• Address verification;
• Inbound customs clearance;
• Warehousing (whether in a single market or multiple locations);
• Several picking and packing options, including automation; and
• Sustainable returns handling. DSV effectively gives entry-level and smaller retailers the same fulfilment capabilities that larger rivals enjoy.
“A customer can start with a cash account with DSV and access all the benefits we offer, nationally and internationally. As your company grows and becomes an account-holding customer, we provide a dedicated sales organisation that can support you to expand your reach at tailored pricing, and provide industry insights relevant to you,” says Roos.
In addition to these services, more than 457 DSV lockers are located strategically at fuel forecourts and other publicly accessible locations around the country.
This means a consumer or business can send or receive a parcel at any time at a discounted rate, adding another dimension to fulfilment.
“The DSV locker is a popular anytime courier option that offers flexibility and convenience as the driver, parcel, recipient, or sender don’t need to be in the same place at the same time,” says Roos.
Roos and Rugg say there’s no limit to what online shops are selling, from solar equipment
and pet accessories to jewellery and alcohol, and they are using both DSV’s courier options and the DSV locker to reach their customers.
“The DSV Locker is a popular anytime courier option that offers flexibility and convenience as the driver, parcel, recipient, or sender don’t need to be in the same place at the same time.” – Johan Roos
1. On average, international airfreight to and from South Africa daily is about 400 tonnes inbound and 250 tonnes outbound, resulting in an average of 650 tonnes per day.
2. On average 12 097 TEU (20 foot equivalent unit) of containers pass through our ports daily.
3. A tonne-kilometre is a unit of measure of freight transport in the trade that represents the transport of one tonne of goods by a given transport mode over a distance of one kilometre.
The modern global supply chain consists of many complex networks, creating risk. GARETH GRIFFITHS considers how they should evaluate risk and use this knowledge to optimise their supply chains
According to the South African Association of Freight Forwarders (SAAFF), the global economic climate in which supply chains move goods has recently been characterised by a series of severe and mutually reinforcing shocks, causing a bleak outlook for the global economy. South Africa in particular has been enormously challenged both by the global and local situations. Our supply chains are not healthy, it appears.
SAAFF CEO Dr Juanita Maree says that shocks to the global supply chains have included the COVID-19 pandemic, the war in Ukraine and its resulting food and energy crises, surging inflation, debt tightening and the climate emergency. “There are several challenges currently, which can be grouped into capacity shortage, logistics and transport asset deterioration, inefficient operations, and lack of market liberalisation.
As an example, inefficient logistics operations –including long ship workings and reductions in efficiency – have led our container terminals to be rated as the least efficient in the world by the World Bank, worse than 10 years ago.”
The multimodal approach
South African trade patterns typically involve several handover points, since the country’s economic hub is far away from the ports, which handle more than 85 per cent of merchandise trade. As our freight demand is very high, at nearly 500 billion tonne-kilometres, a multimodal approach is essential.
For example, depending on the multimodal strategy employed, a container from Johannesburg to Durban will typically be handled three times: long-haul and then short-haul transport via truck, after which it will be loaded upon a container vessel at the Durban Container Terminal (Pier 1 or Pier 2).
4. COVID-19 restrictions significantly affected supply chains as airfreight capacity into South Africa reduced in line with passenger air cancellations. Where operators utilised passenger belly capacity, insufficient capacity supply to meet demand led to inflated prices.
5. Income from the transport and storage industry stands at about R 592.65-billion, 19 per cent of South Africa’s GDP.
6. Transport costs are the dominant contributor towards South Africa’s logistics costs, amounting to 57 per cent of the total.
7. Labour disruption caused by disputes and strikes have wreaked havoc. Estimates are that South Africa lost the opportunity to move R65.3-billion worth of goods due to strikes.
Source: SAAFF
The same is true for import cargo: a short-haul transporter will evacuate the container from the terminal to a distribution centre or backup port facility, after which the goods might be unpacked or kept in the container, and transported to the hub in Johannesburg.
Consequently, backup port facilities such as dry terminals – examples of which include City Deep, Belcon and Cato Ridge – are important to alleviate congestion. With the ongoing poor efficiency and drop in rail freight volumes, road freight usage has increased tremendously.
“The global literature, backed by numerous international working examples, favours a multimodal approach, with backup port facilities and dry terminals in close proximity to ports, which are our key points.” – Dr
Juanita MareeDr Juanita Maree
“The global literature, backed by numerous international working examples, favours a multimodal approach, with backup port facilities and dry terminals in close proximity to ports, which are our key points,” says Maree. “There is a sweet spot, for sure, especially considering specialisation and comparative advantage. The critical factor is to maintain a fluid ratio, with containers coming in and going out at the same pace. For that to work, one needs a multimodal approach.”
Similarly, in terms of transshipments, Maree notes that the “hub-and-spoke” model is still the main approach, whereby the hub ports handle the majority of volume from large vessels, with the smaller spoke ports feeding and receiving volume via smaller regional vessels.
Maree admits that while the challenges are numerous, and there is not one single major fix that will improve logistics performance and efficiency, we should however focus on “every single win that we can muster, no matter how small, to rebuild an integrated logistics system from the start”.
However, not all solutions proposed by government make sense to all the role players. Maree says that SAAFF is aware of a new tender on the Container Corridor. “We don’t need another monopoly. We need inter- and intra-competition with a strong independent regulator, which has extended power to regulate the transport or multimodal in an improved transparent structure, with acceptable and best practice key performance indicators.”
To fix the current crisis, she suggests that we need unified business, a committed labour force, a strong and decisive government, and a collective social compact between all parties. “SA Inc can no longer wait for the volatile global economy to calm down; we must first get our own house in order!”
“There is excess capacity on some routes and if rates drop to unsustainable levels, airlines will consider reducing availability on those routes until demand improves.”
An operator’s view
DSV serves the main airfreight and ocean lanes into and out of South Africa. These include the primary lanes for China and India, Europe; perishables exports, primarily to the northwest and automotive and industrial in select Eastern European countries; and then North America (industrial). DSV directors Brad Braga (ocean freight) and Andre Koekemoer (airfreight) are key players in the industry, and speak to a multimodal approach in efficient transshipment.
“Tough global economic conditions have dampened consumer spending, reducing demand for airfreight,” says Koekemoer.
“There is excess capacity on some routes and if rates drop to unsustainable levels, airlines will consider reducing availability on those routes until demand improves. However, it absolutely pays to use multiple modes of transshipment.
“There is, however, always a trade-off between
Retail giant Shoprite Group says it continually bolsters its supply chain resilience by procuring from local suppliers as far as possible, with a focus on growing private-label suppliers and growers. But the group has to source specific products from other parts of the world when the local market is not able to meet the supply required. It also exports local products to several markets in Africa.
Commenting on supply chain logistics for the Shoprite Group, chief supply chain officer Andrew Havinga confirms that the group already uses multimodal transport to ensure it has the most efficient route to market for its products, depending on the nature of the product, service levels required and origin relative to destination realities. “It pays to do so. The group’s world-class supply chain, which includes 29 distribution centres covering 673 843m², provides it with a competitive advantage in the retail industry to deliver consistently on its business imperatives.
“Our supply chain extends from our suppliers, through our own logistics operations, to our stores and is managed through our fully integrated enterprise resource planning and supply chain planning systems, spanning across our local, import and export activities.”
The impacts of the COVID-19 pandemic and the war in Ukraine did constrain supply, but with the lifting of the pandemic restrictions globally, Havinga concludes that “supply lines have mostly stabilised and we have seen good retraction in shipping costs as a result”.
– Andre Koekemoer
Armscor is a strategic partner of choice for defence and security solutions
The Armaments Corporation of South Africa SOC Limited (Armscor) is an acquisition agency for the South African Department of Defence (DOD), and other organs of state and entities.
Armscor’s mandate is to provide the armed forces with state-of-the-art defence material delivering innovative defence solutions efficiently and effectively.
The organisation manages the strategic capabilities of the DOD, producing research and vanguard technological solutions required to provide safety and security for South Africa, its citizens and the continent.
AB LOGISTICS
AB Logistics (AB Log), a corporate service division of Armscor, is a shipping and travel company that provides clearing and freight
forwarding and travel management services to Armscor, the DOD, the defence industry, and domestic and global commercial clients. AB Log specialises in domestic and international transportation and distribution.
Services offered:
• Clearing and freight forwarding – provision of state-of-the-art freight services, as well as customs clearances and requisite embargo clearances.
• Road, rail, sea and airfreight services –transportation of goods and cargo via road, rail, sea and/or air depending on client needs and requirements.
• Transportation of explosive and sensitive cargo – adherence to all relevant regulatory provisions in the transportation of such sensitive cargo.
• Travel management services – provision of travel requirements such as flights/bus and/ or coach transportation, accommodation, shuttle services and car rental hire.
For more information:
AB Logistics
+27 (12) 428 2455/082 4671818 (senior manager)
+27 (12) 428 2484/082 4671822
(shipping manager)
+27 (12) 428 2164/082 467 1821
(warehouse supervisor)
+27 (31) 337 7647/083 252 1012
(branch manager, Durban office)
+27 (12) 428 2038/083 655 6702 (travel manager)
ARMSCOR’S MANDATE IS TO PROVIDE THE ARMED FORCES WITH STATE-OF-THE-ART DEFENCE MATERIAL.AB Logistics, a corporate service division of Armscor, is a shipping and travel company that provides clearing and freight forwarding and travel management services.
• Facilities hire – Gerotek’s well-maintained venue is suitable for work and play. It is a unique venue for conferences, product launches, seminars, team-building activities, exhibitions, on- and off-road test tracks, and an accredited shooting range, among others. Gerotek facilities are ISO 14001 and ISO 45001 certified.
• Events, recreation and conferencing –Gerotek’s event services are tailored to unique client needs, enabling corporate clients to get down to serious business in the conference venues and then have fun outdoors as they take advantage of the many recreational pursuits on offer.
• Restaurant and catering – The Africanthemed Sidibane Restaurant offers excellent catering facilities for any occasion, from a relaxed cocktail party or a spit braai to more formal events.
Gerotek Test Facilities (Gerotek), a subsidiary of Armscor, is an internationally accredited multidisciplinary facility offering various ISO 17025 accredited tests. The facility primarily aims to meet South Africa’s needs in testing defence-related and commercial vehicles and products.
Gerotek’s well-maintained facilities are located just 20km west of Pretoria in the Gauteng province. The 520-hectare site has been designed and built in accordance with international standards to offer unparalleled technical and service excellence to local and international markets.
Gerotek offers world-class ISO-accredited and certified facilities and services that can be used by local and international clients to test and evaluate the performance of their vehicles and products. Services are designed to cater to the exact requirements of clients and to meet and exceed customer expectations.
Services offered:
• Vehicle and product testing – Gerotek offers ISO 17025 accredited testing that adheres to international standards to promote the repeatability and accuracy of tests. Gerotek offers a broad range of vehicle and product testing services, including vehicle characterisation, endurance evaluation qualification of electronic, electrical and mechanical systems and components, fatigue testing and analysis, electromagnetic compatibility, antenna testing, and more.
• Advanced driver training – Gerotek’s advanced driver training focuses on safe driving practice in a controlled environment under expert supervision. Training interventions include defensive, advanced, high-performance, offensive, and 4x4 driver training. Gerotek advanced driver training offers TETA and SASETA accredited and other noncredit-bearing driver training courses.
Scan this QR code to go directly to the Armscor website.
For more information:
Gerotek
+27 (12) 371 2000/2065/2059/2052
+27 (82) 800 5932 info@gerotek.co.za www.armscor.co.za
The Armaments Corporation of South Africa provides defence and security solutions to the Department of Defence to ensure the nation’s safety
The Armaments Corporation of South Africa SOC Limited (Armscor) is an acquisition agency for the South African Department of Defence (DOD), and other organs of state and entities. Armscor’s mandate is to provide the armed forces with state-of-the-art defence material, delivering innovative defence solutions efficiently and effectively. The organisation manages the strategic capabilities of the DOD, producing research and the vanguard technological solutions required to provide safety and security for South Africa, its citizens and the continent.
One of Armscor’s core businesses is acquisition. Its key functions include, requirements analysis, technology development, design and development of products and product systems, and the industrialisation and manufacturing of mature products and product systems that fully meet user requirements. It also entails the procurement of existing and qualified products and the acquisition of product system support for user systems during the operational lifetime of the systems.
Armscor, through its Research and Development, conducts defence research and scientific research, test and evaluation services, technology management, analysis and industrialisation and intellectual property management services. The organisation has the capability to perform an independent, centralised co-ordination and management role for technology acquisition and technology commercialisation.
The Dockyard provides repair and maintenance services to the South African Navy on various product systems, from tugs and small craft to frigates and submarines. Maintenance and repair services cover both planned and ad hoc projects. It is one of South Africa’s strategic national capabilities, housing the country’s naval defence maintenance and repair facilities.
The Alkantpan Test Range (ATR) is an all-purpose ballistic test range for all types of weaponry, ranging from 5.56mm to 155mm calibre to large calibre weapons and ammunition. An ISO 9001- and ISO 14001-accredited facility, this 85 000-hectare facility is equipped for testing artillery, mortars, armour, rockets, short-range missiles, insensitive munitions, sequential environmental testing and
unmanned aerial vehicles. ATR also provides customised ordnance testing and related services to local and international clients.
The Armour Development facility has been conducting research, development and testing of armour protection systems and technologies for the DOD and the defence industry for more than 40 years. Services provided include, analysis of customer protection
Armscor’s mandate is to provide the armed forces with state-of-the-art defence material, delivering innovative defence solutions efficiently and effectively.
needs, development of armour, testing, and qualification of vehicle hull ballistic resistance. Expertise also includes designing and fitting armour packages on lightweight vehicles and main battle tanks.
The Defence Decision Support Institute (DDSI) has offered defence support for over 30 years. It focuses on enabling the DOD, state organs and commercial entities. The DDSI assists in developing insights and holistic solutions to decision-making challenges over the full cycle of defence capabilities and systems. This facility also offers a range of services, including policy and weapon systems analysis, war conflict studies, defence capability analysis and engineering support.
Ergonomics Technologies (Ergotech) is Armscor’s leading research institute, providing military defence and commercial ergonomics research, design and development of human-machine systems and the evaluation of environmental stressors. The broad range of services it offers in ergonomics and occupational health and
safety aims to optimise human performance and efficiency, reduce work-related risks and improve the overall safety and productivity of employees.
The Fluid and Mechanical Engineering Group (Flamengro) provides integrated modelling and simulation support on the design, development and operations for the DOD and the broader engineering and software sector. The group provides cost-effective holistic solutions in the areas of computational mechanics, test and measurement, software development and small-scale manufacturing.
Hazmat Protective Systems (Hazmat) is a major manufacturer and supplier of purpose-designed quality respiratory and filtering products for the commercial and defence industries. Hazmat is one of the few companies capable of impregnating activated carbon in its products. As an ISO 9001:2015-certified company, processes are in place to ensure that clients consistently receive high-quality, safe products at competitive prices.
Armscor’s Institute of Maritime Technology (IMT) is an ISO 9001-accredited centre of excellence, providing science-based technological and engineering support to the South African Navy and the broader maritime community. IMT specialises in maritime technologies, sciences for military defence applications, defence research, development, testing and evaluation of maritime systems that have led to several cutting-edge innovations.
Protechnik Laboratories is a multidisciplinary scientific laboratory focused on high-end research and development work in chemical and biological defence solutions. An ISO 17025/IEC: 2017-accredited testing laboratory with a 30-year history, Protechnik Laboratories offers a wide range of analytical services to verify and detect the presence of highly toxic and prohibited chemical and biological agents. This research benefits the defence and commercial industry, agriculture, food manufacturing, mining and environmental sectors.
The organisation has the capability to perform an independent, centralised co-ordination and management role for technology acquisition and technology commercialisation.
Interroll South Africa manufactures a globally recognised quality-assured product termed, “global yet local”. It offers the product with shorter lead times at a competitive local price. Over the years, Interroll South Africa has increased its manufacturing facility to cope with the demand of the local industry, which requires a quick turnaround time on small- to medium-sized projects. Larger projects normally have a longer project timeline, which allows the flexibility to supply part of the project locally and part to be imported if required.
The new showroom was completed in 2021 and allows system integrators and end-user customers to bring their products to Interroll South Africa, which can then simulate how the product will be conveyed. The showroom has most of the products available, including high-speed diverts, transfer modules, lift-up gates, inclines and declines, all operated with the DC platform that incorporates zero pressure accumulation (ZPA).
Sorters are required at various points in intralogistics, such as incoming goods, the picking area and outgoing goods. With the horizontal and vertical cross-belt sorters, Interroll has offered two proven solutions with over 400 installations completed worldwide.
The Interroll Group is a leading provider of material-handling solutions. Founded in 1959, the company has been listed on the SIX Swiss Exchange since 1997. Interroll supplies system integrators and equipment manufacturers with a comprehensive range of platform-based products and services in the categories of Rollers (conveyor rollers), Drives (motors and drives for conveyor systems), Conveyors and Sorters and Pallet Handling (pallet conveying and storage).
Interroll solutions are used in express and postal services, e-commerce, airports, and the food and beverage, fashion, and automotive industries, as well as other sectors. The company counts leading global brands such as Amazon, Bosch, Coca-Cola, DHL, Nestlé, Procter & Gamble, Siemens, Walmart and Zalando among its users. Locally in South Africa, customers include Takealot, Shoprite, Pick n Pay, CourierIt, The Spar Group, Mr Price and TFG, to name a few. Headquartered in Switzerland, Interroll has a global network of 36 companies with sales of CHF 640.1-million and 2 600 employees, based on 2021 figures.
Interroll South Africa is located in Spartan, Gauteng, and this year, the company celebrates 25 years of servicing the South African market. This facility produces the majority of Interroll products that service the South African market and includes rollers, conveyors and pallet flow lanes.
In 2020, Interroll launched the high-speed horizontal sorter to answer market demands for high speeds and the capacity to sort heavier items. The sorter can sort goods up to 50kg and 20 000 parcels per hour. Based on the proven mechanical design principles of Interroll sorters, Interroll has added a fourth sorter to its line-up with the launch of its new Split Tray Sorter. This allows for a wider range of potential users of its already successful range of automated sortation solutions on the market.
The new Split Tray Sorter ensures maximum availability, long service life, and fast payback times for the automatic sortation of conveyed goods weighing up to 12kg. This makes these compact and flexibly expandable systems particularly suitable for companies that want to implement e-commerce or omnichannel strategies that are as powerful as they are economical, for example, in the fashion or pharmaceutical industries.
Interroll’s Modular Conveyor Platform (MCP) offers perfect functionality for conveying within the manufacturing, distribution, tyre and automotive, and e-commerce industries.
Interroll solutions are used in express and postal services, e-commerce, airports, and the food and beverage, fashion, and automotive industries, as well as other sectors.Interroll Head Office in Spartan
The applied ease-of-use philosophy provides customers with a smart, flexible, economical and reliable solution for their material handling.
It starts with the planning: Interroll provides an AutoCAD-based layout tool to easily help design and select a system with integrated modules. The modules are delivered largely pre-assembled to accelerate on-site installation while setting a high standard for reliable and solid technical performance. The MCP’s independently adjustable side guides, infinitely adjustable supports, integrated electrical conduits and a universally applicable master gauge for holes to attach add-on components are only a few of the details that reduce the installation effort and ensure simple handling during assembly and expansions.
Customer needs, conditions on-site and the type of materials to be conveyed define the requirements for a system. Zero-pressure-accumulation conveying can be implemented with proven DC RollerDrive.
For higher performance, efficient DC drives that enable future-proof ZPA conveying are used together with roller conveyors with 400V flat belt drives. Pneumatics, which creates high operating costs, is completely omitted here, adding to the cost-effectiveness of the MCP.
A feature that has stood out with customers is the energy savings experienced with the EC5000, 24V and 48V RollerDrive. Compared with the 400-volt technology, a 24-volt solution achieves around 30 per cent energy savings; as far as the accumulating function is concerned, energy consumption can be reduced by as much as 50 per cent.
Most companies involved in the distribution of goods on pallets would like to smooth operations between incoming and outgoing goods with automated processes that are as lean as possible. System integrators and plant engineers can fulfil this wish in a tailor-made way with the Modular Pallet Conveyor Platform (MPP) and the Pallet and Carton Flow offering from Interroll. Thanks to the technology provider’s modular platform and plug-and-play strategy, this applies to standard and special solutions through to complete high-performance systems that integrate compact flow storage solutions.
The MPP is a modular pallet conveyor platform. Depending on the application scenario and customer requirements, conveying of pallets is provided by gear motors or compact drum motors, and even ZPA conveyor sections for pallets can be realised in normal ambient temperatures and deep-freeze
areas. With the Pallet Control Configurator, the direction of rotation and other parameters can be changed easily through the USB connection of the pallet controller without having to change the wiring. Power and performance can be monitored and the current status displayed. In addition, the total operating time of the respective pallet drive is displayed so that necessary maintenance work can be arranged preventively.
Combined with the Interroll flow storage solution, compact high-performance systems are created from a single source where the usual engineering interface problems between the driven and gravity-based systems are eliminated.
Flow storage systems for cartons and pallets offer many advantages. In addition to their particularly space-saving design and high operational reliability, these dynamic storage solutions also impress in terms of operating costs. Pallets are not moved using electrical energy, for example, by a forklift or a radio shuttle system. Instead, flow storage systems use the principle of the inclined plane: the pallets “flow” automatically, using gravity, through flow channels from the point of entry to the point of retrieval. These systems can be connected to autonomously operating stacker cranes, transfer cars and lifts, which can handle an hourly throughput of up to 100 pallets for fully automated retrieval.
At the heart of a highly dynamic pallet-handling system is a stacker crane, designed to connect seamlessly to the Interroll Pallet Flow storage system. The lightweight construction and integrated energy recovery make the system extremely energy efficient. The overall height is 12 metres, the horizontal travel speed is 3 metres per second, and the lifting speed is 0.8 metres per second. The system is equipped with integrated lifting speed control and powerful braking systems. Thanks to the modular and pre-assembled design of the steel construction, the stacker crane requires little maintenance and is easy to deliver and install. The initial system is designed to transport pallets with a maximum weight of 1 000kgs.
InterrollSouth
Africa has increased its manufacturing facility to cope with the demand of the local industry, which requires a quick turnaround time on small- to medium-sized projects.Carton Flow Splittray Sorter
International supply chains carry many risks due to their complex and foreign networks, policies, and practices. Consumers are also more curious and vocal about ethical and sustainable businesses, as watchdogs wag their tails.
Today’s supply chain is under massive scrutiny, and for good reason: the supply chain impacts so much of a company’s output, reputation, workforce and consumer behaviour. It’s where the “governance” in environmental, social and governance (ESG) gets to shine. Basically, your business asks your suppliers to comply with your standards, and your suppliers ask for compliance from their suppliers, creating a cascade of sustainable practices that flows throughout the supply network.
However, these standards vary greatly, especially when you are part of an international network. This is where laws become really important. Lawyers de-risk and evaluate a business from a compliance position, but we also look at the business and the changing legal landscape in the various countries it operates in to advise on how to de-risk the business continuously.
De-risking through appropriate actions can optimise the supply chain, offering benefits through tangible money-saving solutions. As an example, NEC contracts allow for adjustments when the supply chain is interrupted, putting the cost on the supplier and de-risking costs for you.
Under the four broad different types of risk – environmental, economic, geopolitical and ethical – all can be identified through sustainability audits and ESG scorecarding. Risks are evaluated according to the individual country within which an international transaction is taking place. High-risk countries should thus naturally warrant stricter protection and more defences against breach.
This risk is determined by various factors, with geopolitical influences being a major factor to consider. You should also ensure that domestic and international laws are complied with by the supplier, and that a termination may occur if there is a violation of these laws. It is also important to consult a legal team with experience in that country.
Supply chain operators need to ensure that they are protected in case of a disruption. Considered contracts give contractors and subcontractors a great advantage, as these eliminate the element of surprise and ensure everyone is aware of their contractual responsibilities prior to entering into operations. This is important, because it offers certainty to all parties and allows everyone to prepare effectively and reduce the effects of disruption in an unpredictable environment.
Supplier data becomes invaluable information when it comes to understanding the sustainability of your business suppliers. Having a great relationship with suppliers ensures the flow of information needed to report on compliance is much more collaborative than transactional. We see clients who operate like this increase efficiency, output and their relationship with their communities. Naturally, their bottom line increases too.
Your supplier’s compliance with laws, labour practices and other legal requirements has a direct positive or negative impact on your company’s risk and compliance. Avoid exclusivity agreements with suppliers or ensure that the supplier contract does not include any exclusivity provisions, as this enables you to seek the product from an alternative supplier should there be a disruption in the delivery of the product.
The mining and construction industries are no strangers to these types of international transactions and supply chains, along with the risks that come with them. Mining and construction supply contracts often deal with specialised equipment needed for operations, such as trackless mobile machines, specialised drills and other building materials. If there’s a delay or non-delivery of these products, a project or mine can be significantly impacted due to the halting of its operations. By undertaking these processes for evaluating risks, you will be protected through the pre-emptive inclusion of the relevant clauses in the contract. This will protect you before the breach or risk happens – thereby de-risking the supply chain process.
Considered contracts give contractors and subcontractors a great advantage, as these eliminate the element of surprise and ensure everyone is aware of their contractual responsibilities prior to entering into operations.Velile Malaba Trevana Moodley
De-risking is an approach that creates immediate impact for an organisation’s operation and output. TREVANA MOODLE Y and VELILE MALABA , candidate attorneys at NSDV, unpack the issues around staying compliant in an ever-changing policy landscape
Materials handling and the supply chain will improve significantly if private operators are allowed to access Transnet’s rail network.
DER
VEEN BENJAMIN VANexplores the potential impacts of such a move
To help address the current challenges
Transnet faces, it is crucial for the parastatal to implement the correct reformatory frameworks. These might include:
• Allowing private operators on the rail networks, as Transnet can’t achieve the necessary efficiencies
• Creating a system to allow private operators to utilise idle Transnet stock
• Devising a programme where private companies can use their own rolling stock
to create synergies with the movements of a larger volume of product between the different geographies within South Africa.”
While South African companies are searching for solutions in the face of a failing national carrier and the chaos this creates in their supply chains, the private sector needs to accelerate its programme of involvement in order to create more effective logistics corridors.
The last 18 months have seen state-owned ports and freight rail operator Transnet declare six forces majeures. These came as Transnet weathered circumstances outside its control that made it difficult to fulfil its contractual obligations, including a strike, floods in KwaZulu-Natal and the closure of a significant coal line due to an accident. However, underpinning these circumstances is an enterprise that is incapacitated and therefore constantly fails to fulfil its mandate optimally. This is due to years of crippling mismanagement and corruption, affecting the country’s overall economic performance, and resulting in challenges for both the public and private sectors.
When asked about the most significant challenges South Africa currently faces with its road, rail and shipping networks, RMB sector head of public-private partnerships and concessions Siyanda Mflathelwa says: “Rail and ports are a
good place to kill many infrastructure birds with one stone. We find that railways are spending increasing amounts on security and protecting infrastructure from theft – this is because they are currently not being utilised enough. When there are a lot of trains on a line, there are fewer opportunities for vandalism and theft.”
Road freight challenges in South Africa
South Africa faces a number of key challenges, including:
• Cost of logistics
• Environmental concerns
• Regional connectivity
• Road safety
Feroza Grosso Ciponte, the supply chain director for East and Southern Africa region at Nestlé, says it is imperative to allow private operators access to Transnet’s rail network. “This will facilitate a move in the industry towards a greener route to market. It will reduce the pressure we have on the road infrastructure of the country, as well as reduce the national road fatality and accident rates.
“The effect this will have on Nestlé will be to provide more reliable deliveries to our customers, reduce our impact on the environment and reduce our distribution costs, as the rail network is able to scale up. As Nestlé has multidirectional flows, we would expect a reduction in cost, as we are able
Regarding the current issues that businesses like Nestlé face when tackling supply chain management and distribution, Ciponte notes: “Macroeconomic headwinds from rising costs across the industry to supply/demand constraints are putting pressure on the company’s bottom line. There is also increased risks of road accidents, fatalities and hijackings across the national roads of South Africa.”
She adds that the ageing road infrastructure has resulted in longer travel times, leading to increased lead times and higher safety stocks within the supply chain. The industry is also limited by the availability of reliable transporters during peak periods and seasons, so there tends to be a shortage of available transport resources.
Over and above the macroeconomic challenges, Ciponte says the South African economic retrogression does not work in Nestlé’s favour. “Access to Transnet’s rail network will in the long term result in fewer road fatalities and reduced CO2 emissions, and will further develop progress towards a sustainable supply chain. This will create more reliability on customer lead times, allowing us to streamline upstream operations and cut out waste in the end-to-end value stream,” she concludes.
“We find that railways are spending increasing amounts on security and protecting infrastructure from theft – this is because they are currently not being utilised enough.” – Siyanda Mflathelwa
Interroll offers key solutions for units handling in specific industries such as Warehousing & Distribution, Courier Express and Parcel, E-commerce & Retail, Airports, Food & Beverage, Tire & Automotive and Industrial Manufacturing.
High-Performance
Crossbelt Sorters
Horizontal
Crossbelt Sorters
Vertical
Crossbelt Sorters
Split Tray Sorters
Carton
Wheel Flow
Carton
Versi Flow
Pick Tunnels
In a time of rapidly changing supply chains, global pallet-pooling systems offer adaptability, efficiency and sustainability, writes CHRIS PERUMAL , director of FMCG for
Supply chains are becoming increasingly complex, with global reach, non-negotiable health-and-safety compliance, and developed markets demanding sustainable processes.
Markets have also become more competitive than ever. Manufacturers must aim to find greater efficiencies wherever possible, while driving a socially and environmentally positive organisational agenda.
The solution to many of these challenges is an established supply chain function: pallet pooling. Pooling is based on the concept of the share-and-reuse model underpinned by the principles of the circular economy.
For a manufacturer, distributor, or retailer, owning a pallet means the pallet becomes an obligation whenever it’s not in use. After usage, there are several costs then associated with the overall purchase of a pallet, comprising its retrieval, quality assurance, storage and maintenance, to name a few. Customers who purchase their own pallets inevitably incur a higher overall cost to manage this function.
It makes far more sense for organisations to hire their pallets and pay for usage while their goods are in transit. With the pallet-pooling model, pallets are returned to the pool after use, and are no longer the responsibility of the customer.
This circular business model enables a business like ours to serve its customers by devising smart solutions for every partner in the supply chain. This minimises the environmental impact, and improves the efficiency and safety of supply chains across the world.
In the last year, this model for partnering and sharing resources has helped customers achieve the following savings:
• 2.4 million metric tonnes of CO2 – equivalent to the CO2 emitted by 454 500 homes
• 3 160 megalitres of water – or approximately 1 240 Olympic-sized pools
• 3.1 million cubic metres of wood
• 3.2 million trees
• 1.4 million tonnes of waste Pallet pooling works due to scale and an extensive global infrastructure. These pallets require constant monitoring and maintenance, and specialist supply chain businesses have the systems to facilitate this efficiently. It’s all about leveraging asset-management expertise and connecting supply chain participants, facilitating collaboration, and ensuring a more efficient flow of goods through the supply chain.
Besides the financial benefits, there are also quality benefits to pallet pooling. Many multinational brands use established pallet-pooling providers to ensure the highest quality for their products. When white-wood pallets are exchanged, there is a high likelihood that the quality is inconsistent. This can cause pallet and product damage as well as returns, meaning more repairs and replacements are required.
Products must be presented on shelf or delivered to the end consumer in the same condition they leave the factory. This requires pallets that can withstand the rigours of moving from factory to truck, to warehouse, and then to the retail or wholesale store. Standardisation has been key to unlocking the value benefits
of pooling. In a pooling network, pallets are collected and sent to specialised service centres, where they are inspected and, if necessary, reconditioned to ensure they meet the required quality standard. This also ensures that standard-size pallets are of a consistent quality and suitable for automated processes.
Worldwide pallet suppliers like CHEP must always comply with the latest industry standards for customer service, technology and pallet maintenance. By using a major pallet-pooling supplier, customers are then also following global best practice.
Having an international presence means that pallet-pooling organisations are always collaborating with partners across the globe. As such, when unpredicted situations arise – such as the COVID-19 pandemic – we are able to take lessons and implement best practices from our partners on techniques to handle the risks and adapt quickly. This makes pooling operators agile and able to help customers become more competitive.
The pooling model also accommodates seasonal demand changes. Customers can always find pallets available during peak periods, and can then return pallets to the pool during off-peak periods.
The pay-per-use approach used in the pallet-pooling model is inherently sustainable. The share and reuse of pallets means fewer resources are wasted, thereby decreasing overall costs – the very definition of the circular economy model that many sectors are shifting toward.
Ultimately, any manufacturer or consumer-goods supplier wanting to be globally competitive should consider becoming part of the circular economy and partnering with a globally integrated supply chain solutions company.
In a pooling network, pallets are collected and sent to specialised service centres, where they are inspected and, if necessary, reconditioned to ensure they meet the required quality standard.
In a world where sustainability practices are increasingly vital, DENISE MHLANGA investigates how training organisations are bringing together supply chain skills and sustainable practices
In the wake of the COVID-19 pandemic, which caused global supply chains disruptions, the need to manage these chains effectively has become even more important, as have the skills needed to survive in a changing business environment.
“Supply chain management is constantly evolving, and it has an effect on every other aspect of any business,” says Prof Rose Luke, an associate professor at the University of Johannesburg’s Department of Transport and Supply Chain Management. “The ability to adapt readily to change is thus essential.”
Luke says that since 1968, the Department of Transport and Supply Chain Management has been offering training in supply chain skills. Initially considered from a transport perspective, physical distribution was later included into the training, followed by logistics and supply chain.
“We always attempt to ensure that our course offerings cater to the needs of the evolving marketplace, meaning courses range across operational, tactical and strategic levels.” Regular industry surveys and engagement with industry leaders keep the institution abreast of industry needs, enabling them to craft relevant courses.
The university offers courses at vocational level (diploma, advanced diploma) and academic level, including BCom, BCom Honours, MCom/ MPhil/MCom Business Management with supply chain specialisation. There are also industry-level courses like Transport Management Diploma, Diploma in Road Transport Management, Logistics Management Diploma
industry short learning programmes. Several subjects within these courses deal specifically with sustainability within the sector.
“Successful supply chain programmes should recognise that, apart from a broad range of hard or technical skills, supply chain operatives need to have a broad and diverse range of soft skills, which should always be incorporated into any successful training programme,” adds Luke.
A booming field
Wesley Niemann, programme lead for MPhil Supply Chain Management at the University of Pretoria, says successful supply chain professionals require leadership, communication and relationship management skills, while understanding that digital and analytical skills are the future. “Developing and improving supply chain management skills levels is important not only for productivity but also for enhancing the innovation capacity of the supply chain management industry and economy.”
Niemann points out that, worldwide, there is a substantive increase in the development of undergraduate and postgraduate degree and training programmes with specialisations in supply chain management. Locally, many public and private higher education providers now report soaring enrolment numbers in this field.
The University of Pretoria recognises the importance of remaining at the cutting edge of developments and trends in this dynamic industry, says Niemann. “To this end, we designed a game-changing series of short courses and programmes to equip learners with the necessary skill set and insights to apply the latest technologies and find solutions for increasingly demanding customers.”
Organisations may also customise courses to meet the specific needs of their workforce and skills development goals. Formal supply chain management programmes include
Big data, advanced analytics and automation will become supply chain pillars, while artificial intelligence and machine learning will have a much greater impact, as processing huge datasets in real time demands these capabilities.
Source: Association for Supply Chain Management
bachelor’s, honours, master’s and doctoral programmes for full-time and part-time students. Sustainability is a core value of the University of Pretoria, and therefore embedded in all supply chain programmes and curricula.
Priya Ramgovind, senior head of programme at the Independent Institute of Education (IIE), says their courses prepare students for the workplace with soft skills built into some modules. The IIE offers qualifications at various National Qualification Framework levels including the Higher Certificate in Logistics and Supply Chain Management, Diploma in Logistics and Supply Chain Management, and Bachelor of Business Administration in Logistics and Supply Chain Management, as well as short programmes.
“Given the technological evolution and the subsequent effects on business, supply chain professionals require certain competencies relating to strategic management, data analytics, demand and supply management, and relationship management,” says Ramgovind.
Ramgovind notes that since the onset of the pandemic, supply chain management has changed, and now requires flexibility to accommodate new contingencies in order to retain customers. “In the current business environment, an optimised supply chain with streamlined operations, processes and participants ensures that value is created and passed down to the consumer in an economical manner,” she concludes.
Wesley Niemannand customised
“Successful supply chain programmes should recognise that, apart from a broad range of hard or technical skills, supply chain operatives need to have a broad and diverse range of soft skills.” – Prof Rose LukeProf Rose Luke
SAAFF moves towards overall digitalisation the supply chain.
Digital FBL, the new generation FIATA Lading, will be launched for SAAFF Members exporters in South Africa. An important opment step forward that will positively supply chain efficiencies and South Africa’s petitive position as a provider of world-class logistics services
Industry recognises the digital FBL and its tracking service as a strong solution that will capacity and, increase security of cargo movement through the entire logistics process – a valuable development in a challenging trading environment.
• Save time and money - Issue digital documents within seconds and save money by avoiding costs generated by paper documents.
• Optimise your processes - Issue secured digital FBLs directly from your TMS to avoid double data entry.
• Bring trust and security - Give the possibility to your stakeholders to verify at any time: the validity of the eFBL, your identity as well as the document content integrity.
• Achieve your sustainability goals - Embrace a green solution, and help save paper and unnecessary courier services.
• Flexibility of format - Decide in which format you want to share your FBL with your stakeholders: in a digital format (PDF) or you can always print it if needed.
The tracking solution used by FIATA for the digital FBL is already implemented and used by banks, corporates, warehouses, and inspection companies to protect other documents. Software providers worldwide make the secured digital FBL accessible in 17 territories so far through FIATA Association members.
Forwarders can implement the digital FBL solution on their own in-house system or use a free digital FBL generator tool.
• Make sure your association offers digital FBLs to their members.
• Fill-in the secured digital FIATA BL onboarding form.
• FIATA will verify that your company fulfils all conditions to issue FIATA BLs.
• Pay your package of digital FIATA BLs.
• Start issuing secured digital FIATA BLs through your everyday tool.
Electric vehicles are the future –but how far ahead is that future in the logistics space, asks TREVOR CRIGHTON
In the face of rail infrastructure challenges, road freight transport looks set to play a vital role in South Africa’s supply chains for the foreseeable future. However, the sector is estimated to account for over a third of South Africa’s 43.3 million tonnes of annual greenhouse gas emissions per year.
The ideal, then, is to work towards decarbonisation – and one critical avenue lies in accelerating the deployment of electric vehicles (EVs) into the supply chain.
Maretha Gerber, vice president of sales and marketing at Daimler Truck Southern Africa, says introducing EVs into the supply chain is complex, because it fundamentally changes the system – from design to production, supply and operation of vehicles to clients, to the way the fleet is deployed and managed. “We are aware of the work that lies ahead as the adoption of EVs increases across the continent. However, we remain confident of the groundwork that has already been done in South Africa.”
Daimler Truck is basing its transition on the understanding that diesel-engined vehicles will be part of the supply chain for a long time yet, so the focus needs to be on cutting emissions. The company continues to lead the way for sustainable solutions as it conducts further tests on a variety of e-vehicles under local conditions.
“This year, we are waiting with great anticipation for more test units to arrive in South Africa for further evaluation, and we have no doubt that they will perform exceptionally,” says Gerber.
Dr Alicia Weber, lecturer in the Department of Applied Management at Unisa, says that she’s been surprised to find executives from the retail industry placing particular emphasis on redefining their operations to incorporate more sustainable
“While charging stations can be powered by solar power, even some of the most sophisticated EV trucks have range restrictions that require careful planning on vehicle routing and optimisation.”
solutions, including EVs. “In addition, they have indicated that consumers are becoming more environmentally conscious, placing increasing pressure on them to redefine traditional ways of managing logistics. Therefore, logistics companies will need to be flexible and should be able to build custom EV solutions that suit every retailer’s needs. As a result, a hybrid model may become more common in the short-to-medium term.”
Gerber says that since EVs are heavier than diesel-engined commercial vehicles, largely because of the battery technology, more power is required to haul the extra weight – and the weight of the load – around. “We’ve found that, on average, a 100 kilowatt-hour battery will allow a vehicle to run for 100km. Depending on space, we can add more batteries, but with each battery currently weighing just under a tonne, we need to balance range and efficiency. The impact that has is that solutions currently need to be tailored for each customer, taking into account their operating needs, capacity for charging the vehicles at their depots, the geography of the operational area and how much charging time is required for each trip.”
Weber agrees that the main challenge with the roll-out of an 18-wheeler EV fleet in South Africa is not necessarily how they will be charged, but rather how often they need to be charged. “While charging stations can be powered by solar power, even some of the most sophisticated EV trucks have range restrictions that require careful planning on vehicle routing and optimisation, especially for longer-range deliveries. Even in countries leading the roll-out of EV fleets, these vehicles
are only used for local deliveries, as retailers are still struggling to find workarounds for these range restrictions.”
Telematics is an area that will need to evolve as part of the transition, according to Gerber. “The technology will have to adapt not just to include how the vehicle and driver perform, but also to play a pivotal role in the planning of trips around battery consumption and range, as well as the availability of different types of charging stations. Our telematics teams are thinking big about taking the technology to the next level, incorporating infrastructure detail to be able to deliver an optimal solution.”
• 60 per cent of all global emissions are generated by supply chains.
• 49 per cent of CEOs say they’re grappling with supply chain interruptions due to extreme climate events.
• 26 per cent say supply chain disruptions are a top-three risk in shifting to a low-carbon economy.
• 72 per cent say sustainability is a priority as they deal with the fallout of the pandemic.
– Dr Alicia WeberMaretha Gerber Dr Alicia Weber The Mercedes-Benz e-Actros is the company’s first all-electric truck – and part of the integrated eActros solution which aims to bring the company closer to the target of zero local emissions. Source: United Nations Global Compact–Accenture CEO Study
Retreading of tyres and utilising re-manufactured spares from the original equipment manufacturer are two ways for transport companies to reduce costs and their carbon footprint, writes ELVIS MUTSEURA , product marketing manager at Iveco Group
Transport companies of all sizes and specialisations are under incredible cost pressures due to rising fuel costs and deteriorating road and operating conditions, not to mention traffic congestion exacerbated by load shedding. Users of transport are also increasingly asking transporters to reduce their carbon footprints. The good news for transport operators is that these pressures are interchangeable, and vehicle manufacturers are constantly working to solve both challenges.
As primary suppliers to and enablers of road transport, commercial vehicle manufacturers task their engineers with devising solutions to reduce the energy consumption and overall life-cycle costs of their vehicles. Engineers can also influence the efficiency of drivetrains to get the most out the fuel consumed, look to improve the aerodynamic performance of vehicles and reduce the tare mass of their vehicles.
Lightweighting involves leveraging advances in materials and manufacturing technology to design and build vehicles (including truck bodies and trailers) that weigh less, without compromising their strength or performance. This increases payload capacity and improves fuel economy, and the effect is even greater on those empty journeys that cannot be charged to a client.
After selecting the right vehicle for the job, the operator needs to get the most out of the vehicle for as long as it is economically viable. The longer that the vehicle is available, at a reasonable cost, the greater its earnings potential and the better it is for the operator. Vehicle manufacturers are increasing their offerings of re-manufactured spares to complement new spares offerings and give operators alternatives at different price points. Re-manufacturing is the
process of repairing, rebuilding, and restoring components to their original specifications. The range of re-manufactured spares extends from complete engines to brake callipers.
The re-manufacturing process is very strictly controlled by vehicle manufacturers, who have enough confidence to provide warranties for these components, often at the same level as new parts. Thus, operators are provided with a reliable and cost-effective alternative to new spares, which they can use to extend the useful life of their vehicle fleet. It is of course advisable to buy re-manufactured parts only from the original vehicle manufacturer.
According to the vehicle cost schedule published by the Road Freight Association (RFA) in December 2022, tyres contribute 1.2 per cent of the total cost of running a two-axle truck in a typical South African delivery operation, and can be as much as 7.2 per cent of the cost of running a seven-axle rig in long-haul transport. Incorporating a well-managed tyre-retread programme can thus significantly reduce overall operating costs. Tyre retreading extends the life of the original tyres and reduces the amount of waste that would otherwise find its way to landfills.
Fuel contributes 27–41 per cent of the total operating costs for the respective example operations mentioned above, as per the RFA, and nothing impacts fuel economy more than driver behaviour. Good driving habits reduce fuel consumption, and have an immediate and significant effect on the longevity of a vehicle and the associated maintenance costs.
Monitoring and managing driver behaviour is one of the most important functions of a fleet manager’s role. While there are many technological enablers for this activity, the chief one being good vehicle telemetry, there are a great many other critical things that the fleet manager is tasked with managing.
In his book The Power of Habit, Charles Duhigg outlines how Paul O’Neill was appointed CEO of The Aluminum Company of America at a time when the business had posted poor results for some years. It is said that O’Neill surprised journalists and investors by focusing his turnaround strategy almost exclusively on worker safety. This approach paid handsome dividends and demonstrated that focus on one cornerstone issue at a time produces far-reaching benefits.
If fleet managers focus their attention on encouraging drivers to increase the amount of time that they coast (correctly with the gearbox engaged) as a percentage of total driving time, the benefits are immediate and far reaching. This single key performance indicator is easy for drivers to remember and easy to measure, and can have an enormously positive impact on road safety, maintenance costs and fuel economy.
Established in 2007 as a freight brokerage, NGL Logistic Solutions (Pty) Ltd, NGL Direct Africa (Pty) Ltd and NGL Africa (Pty) Ltd is a solutions-based logistics group specialising in line-haul, direct deliveries, medical device movement and high-value cargo deliveries across Southern Africa. We spoke to the NGL team, Mark Scott (Owner/Director), Gert Blignaut (National Operations), Konrad Bassett (National Sales), and Troye Scott (Group Finance) to learn more about the industry and how the right partnerships can be a game-changer in this sector.
Please summarise what NGL does?
“With the rise of e-commerce and a pressing need for reputable logistics services and flexible warehousing solutions, NGL is well positioned as a strategic acquirer with an opportunity to tap into a rapidly growing industry. We are ISO, TAPA, SAHPRA and SAMED accredited, allowing the group to transport specialised, as well as medical cargo.”
How has the industry changed over the years?
“We are seeing an increase in the consolidation of logistics businesses, resulting in smaller businesses being bought out by the bigger players. The pricing levels to the market have also been driven down by the bigger
businesses, who are attempting to get volumes into their operations and achieve a better CPK (Cents per Kilogram), as a result “cheaper” pricing has made an impact on the industry.
We’ve also noticed that bigger logistics businesses in the industry are moving away from a large asset-based model or asset heavy business and are outsourcing to smaller logistics companies that specialise in the relevant markets and own the necessary assets (vehicles and facilities).”
What are some of the biggest challenges you have faced and how have you overcome them?
“With the proliferation of competition in the industry, it has become increasingly difficult to separate our customers from competition. It has therefore become imperative that we ensure we do not compete with our customer base. NGL has refused a great deal of business to make sure that we are transparent and above board with our customers ensuring ethical practices and maintaining our reputation as such in the market.
We have our areas of expertise within the logistics and transport market, and we place focus on educating
current and potential customers about our offerings, so they understand that service is what we guarantee, and we would rather turn away business if we cannot guarantee our high service level.”
Why did you choose IVECO vehicles for your fleet?
“When we were in the market for vehicles, we looked at many different manufacturers, comparing price, reliability, and aftersales service and support. One thing that stood out for us was that we got many IVECO referrals from others within the industry. Once we got into contact with the team, the willingness from IVECO to help and guide us was outstanding. And even after purchasing the vehicles, the dealers were great, the service was amazing, and the vehicles never gave us issues. Our IVECO vehicles are incredibly reliable – and has made the decision to add more IVECO vans to our fleet an easy one!”
What are some of your favourite features of the IVECO vehicles?
“It has to be the reliability! We have some IVECO vehicles with mileage ranging from 500,000km to 1,000,000km and we haven’t had to change the motor,
We chat to the NGL executive team to gain some industry insights and discover how their partnership with IVECO is driving the business forward in the delivery and logistics space.
gearbox or diff; it’s been running amazingly with just regular services. We also love the Chassis Cab – it gives NGL the flexibility to offer different options to customers. Each of our IVECO vehicles are also incredibly comfortable and sturdy, making both longand short-distance trips a breeze!”
Does IVECO offer any additional support or benefits to you?
“Yes, they are amazing. We enjoy 30,000km service intervals which is something that not all suppliers provide. Plus, their workmanship is of high quality and their breakdown services is by far one of the best we have encountered. And Mickey from Randburg IVECO is someone you can phone any time of the day or night and he will always assist. That kind of service and dedication in the market is hard to find.”
How do your drivers feel about the IVECO vehicles?
“All our drivers love the IVECOs; they say it’s like driving a car, because it’s comfortable, durable, and they enjoy smooth driving. We have around 12 Daily vans that all run long distance, from 17,700km to 28,000km a month and the drivers report that they are reliable, strong, and very stable – they don’t want NGL to look at other vehicle brands or makes for future purchases.”
Would you recommend these vehicles to another transport operator?
“YES, I most certainly would! They offer a fantastic aftersales service, along with reliable products and other services. IVECO parts are often easily available so there is less downtime for your vehicles, plus their response times and the communications with dealer workshops are top-notch. You’d be hard-pressed to find another brand that takes such good care of their customers once the sale is done.”
What does the future hold for NGL and the transport industry as a whole?
“The industry is seeing more consolidation happening, it’s happening as we speak. Very large logistics businesses are trying to fill enormous warehouses, just to make up costs and a small profit margin. This is creating competition resulting in a “price war” driving prices down – but they are not concentrating on service to generate more profitable margins. As we see it, the smaller players will need to create a niche in order to last and not be wiped out. At NGL, we have had to make sure that what we offer is different. We believe that service is the most important factor in any business and we are working hard for a service level conformance of 98% and above. We are working to offer services that no large logistics business could offer
and that does not fit into their model. NGL is VERY flexible, giving customers what they need when they need it for a guaranteed service offering. We plan to keep doing what makes NGL successful and becoming 100% part of a customer’s supply chain.”
With the logistics and transport industry continuously growing, it has become increasingly important to ensure that these companies establish and maintain the right partnerships for success. IVECO has been offering outstanding products and services to South African businesses for over 25 years, making sure that the industry can keep their wheels turning. IVECO is here as your total transport solution, sustaining your business and enhancing your productivity and profitability as you get your enterprise on the road to success - just like NGL!
If you’re interested in partnering with IVECO and adding an IVECO vehicle to your fl eet, then contact your nearest dealer for a quote or call our National Sales Line on 011 243 6065 and let us help you fi nd the right IVECO for your unique business needs!
Unitrans believes in creating close and trusting partnerships. Decades of deep relationships have laid the foundation for a growing network of operations spanning many Sub-Saharan countries. By offering tailored innovative solutions and entrenching long-term partnerships, our market presence spans multiple sectors and industries in Africa.
100 K+ 18M + 10 M+
Hectares covered People moved Tons hauled Kilometres travelled Litres delivered Vehicles in operation
176 M+ 2.8 B+ 5 K+
Unitrans is a leading provider of integrated operational services that enables growth across many Sub-Saharan African markets. Our successful business model incorporates the design, implementation, and ongoing supply of services that allow our customers to focus on and grow their core business.
Safety
It’s our priority to create a safe environment for our colleagues, our customers, our families, and the public at all times.
Innovation
We continuously stretch our imaginations to do things smarter and better
Operational Excellence
With a passion to always do the right thing, we set the bar high and strive to deliver excellence and continuously improve in everything we do.
Partnership
We pride ourselves in being a committed partner and work together as a team to support each other and achieve our common goals and purpose.
The industrial and modern eras changed this. As Thibaut Wautelet writes in his 2018 paper, “The Concept of Circular Economy: its Origins and its Evolution”, Over the last 150 years, our industrial economy has been dominated by a one-way model of production and consumption, in which goods are manufactured from raw materials, sold, used, and then incinerated or
700+ fully vetted transporters
17 000+ trucks available
It may sound counter-intuitive, but transport can help create a more sustainable world, writes JAMES FRANCIS
“Logistics companies’ volumes and routes change constantly, so for them to create circular economies within their own networks is difficult.” – Hugo Derksen
CE efficiencies. One of the most accessible is to recycle tyres.
“Companies recycle tyres because it is an environmentally responsible practice, with a financial incentive,” says Dr Mehran Zarrebini, CEO of Mathe Group. “In South Africa, companies that recycle tyres receive a processing fee. This recycling reduces the need for virgin materials, which can be costly to obtain. Additionally, many countries have implemented regulations that require the proper disposal of used tyres, which can be costly for companies that produce or use large numbers of tyres.”
Tyres are recycled through refurbishment and reuse, shredded for other applications such as filler for construction materials like asphalt and rubber mulch, used for garden pest control, or repurposed into rubber surfaces for playgrounds.
Most CE goals can create significant operational efficiencies, boosting interest in improved warehousing and logistics management. New technologies are helping transport companies and clients better coordinate and reduce the number of empty trucks on our roads. Digital platforms that connect these parties help include more transport businesses, says Derksen. “For the customer, finding a truck that needs a return load results in lower costs. For transporters, finding a customer who can utilise their truck on its return leg results in increased efficiency and revenue for the same leg.”
Derksen says that traditionally, customers did not have the ability to vet a new transporter, while the transporter was wary of the risk in getting paid by a customer with whom they did not have an existing relationship. “Digital platforms bring these customers and transporters together quickly, on a seamless platform, while managing the
operational service risk for the customer, as well as paying the transporters.”
Warehousing also impacts transport efficiencies. Trucks may stand idle waiting for goods to move, resulting in lost productivity that is compensated by putting more vehicles on the roads. By streamlining and integrating warehouse systems, logistics companies make significant CE progress. “Technology plays a major role in optimising efficiencies in warehousing and transport,” says Ellappan. “We have brought our warehouse and transport operations together to optimise processes, reduce wastage and maximise the resources we have, both in terms of machines and people.”
Technology also helps realise CE goals through modern fuel alternatives. A growing number of companies are experimenting with hydrogen fuel, and interest is growing in electric vehicles (EVs). Shoprite Group is testing a heavy-duty electric trucks, and Woolworths has introduced electric delivery vans into its fleet. Local companies such as AEVERSA and Everlectric are also slowly bringing EVs into company fleets.
“EVs inherently have very few service items,” says AEVERSA CEO Rick Franz. “In a normal internal combustion engine, we’re used to
changing the oil, filters, clutches and things like that. In EVs, those items are not present, reducing service and waste drastically. The fuel value chain is also much simpler. You’re not dealing with oil from a tanker that goes to a refinery, then to a depot and a service station. Electricity is simpler to install and manage. Both the operational and management efficiencies are much higher.”
EV adoption is still slow in South Africa, though AEVERSA already counts several large enterprises and logistics companies among its clients. Franz says that while importing EVs remains expensive, if there is more investment in local component manufacturing – such as batteries – those prices will go down. Retired EV batteries can also be recycled into home-use batteries, boosting broader energy sustainability that resonates with CEs.
Demand for efficiencies drives CE adoption, and hard economic times might be to its benefit, but CEs also need healthy financial and infrastructure environments.
Kelly notes key challenges we face locally: poor availability of alternative fuels; packaging materials and environmentally sustainable waste management; the cost realities of such economies and who carries these; and general public apathy for the concept and their role in it. Ultimately, circular economies are about a general attitude. As Boulding wrote in his essay, “In the cowboy economy, consumption is regarded as a good thing and production likewise,” whereas in a spaceship earth, ‘The essential measure [is] the nature, extent, quality, and complexity of the total capital stock, including in this the state of the human bodies and minds included in the system.’”
Transport and logistics companies can do much to realise circular economy goals, but not in isolation. Hopefully, other sectors and consumers will also play their roles and create a sustainable world where future generations don’t suffer the debt of past excess.
Circular economy theory attracts a variety of different views and methods, but one can simplify the overall concept to four approaches:
• Narrowing: Use less energy and resources per product.
• Closing: Recycle output back into inputs towards zero losses.
• Slowing: Consume fewer products over time or use products for longer.
• Regenerating: Replenish natural resources used.
“Many countries have implemented regulations that require the proper disposal of used tyres, which can be costly for companies that produce or use large numbers of tyres.” – Dr Mehran Zarrebini
Technology and innovation are a top priority at Bidvest International Logistics, with the company continuing to improve its processes throughout the business.
Digital technology has improved logistics operations enormously, says Lesiba Sebola, Bidvest International Logistics’ (BIL) IT director. “Using big data and analytics to optimise business processes and improve visibility into supply chains, we integrate with the shippers and carriers on our digital platforms to exchange information. It’s all about keeping up to date and forecasting how we can best meet and exceed our customers’ expectations,” he says.
Working closely with customers, BIL consistently develops new tailor-made products to meet the demands of an ever-changing
supply chain landscape. The company has implemented technology in its fleet of vehicles to enhance fuel consumption and driver comfort. State-of-the-art warehouses are fully compliant in the storage of hazardous products.
“A few years ago, we started on the cloud transformation journey, which has allowed us to be scalable and flexible in terms of the
IT services provision. We can quickly scale up resources and storage to meet business demands without worrying about the turnaround time of acquiring the physical infrastructure.
“In fostering creativity and innovation with the organisation, we have embarked on establishing our centre of excellence to enable our employees to use this cloud service offering
“A few years ago, we started on the cloud transformation journey, which has allowed us to be scalable and flexible in terms of the IT services provision.” – Lesiba SebolaAn extensive transport and distribution infrastructure caters for container cartage, LCL/break-bulk, FMCG, primary and secondary distribution of hazardous and non-hazardous freight and bonded cargo throughout South Africa and across borders.
for easy testing of new ideas and design new applications with the readily available services and marketplaces,” explains Sebola.
The freight forwarding industry is driven predominantly by paper-based processes. This poses several challenges in terms of the manual data capturing into BIL’s business operations platform. Sebola says that after the numerous proofs of concept of the various technologies, the company is in the final stage of completing the implementation of a platform that utilises both artificial intelligence and optical character recognition capability to enable automation of data into its integrated digital global logistics management platform.
He says: “This will bring about the efficiencies and improve the data accuracy in
our customs entry operations and accounts payable process, eliminating human error from manual data capturing.
“We continually monitor market trends and new technologies and apply technology where it will make us better at what we do. We also use a lot of forecasting data to see how we can best meet and exceed our customers’ expectations.”
BIL’s wide range of logistics services includes air and ocean freight, transport, warehousing, customs brokerage and supply chain management. Year on year, the company makes an enormous investment in its fleet of vehicles, warehouses and technology. Of equal importance is BIL’s investment in its people, with training and upskilling through its own academy and outsourced suppliers.
A global network of partners and agents that match the company’s expertise and work ethic provides access to an international network of 250 offices in 120 countries, offering international logistics regardless of location and with the comfort of a single point of contact. The company has built a reputation locally and globally for delivering goods on time and in good order. Its customer base continues to grow with an increase in extended business for existing customers.
For more information: 011 570 6000 info@bidvestil.com www.bidvestil.com
Data is considered to be the lifeblood of organisations in our digital world. GARY ALLEMANN, MD at Master Data Management, explains how effectively managing data can help businesses to optimise supply chains
As with any business in a challenging economy, organisations within the manufacturing sector are looking for ways to optimise the way they operate. Typically, this focus has been around the factory and the physical manufacturing processes, but there are limits to what can be achieved without insight. Data is the missing ingredient to inform better decisions, and unlock greater value and optimisation across not only the factory, site, and machinery, but throughout the supply chain – including the customer, vendor and the end product.
Data impacts every area of every manufacturing business, and is generated through many different mechanisms, from suppliers and customers to the machinery itself. There is substantial opportunity to be found in leveraging this data, both from optimisation and cost-saving perspectives, as well as from the view of increasing revenue.
Many manufacturers are investing in solutions to assist with integrated planning, but the reality is that without the right data, these investments will be wasted. If manufacturers cannot access and leverage the various pockets of data from typical silos like enterprise resource planning systems, customer-facing systems and sales information, the capabilities of integrated planning cannot be leveraged.
This particularly affects larger manufacturers that have grown via acquisition, as they are now faced with the challenge of running multiple systems with inconsistencies, complexities and silos, all of which need to be addressed to leverage true value.
Effective use of data empowers manufacturers to allocate their resources, capital and inventory to build the most desirable goods, at the right time, to maximise end-customer purchasing. It also helps manufacturers to gain a more granular understanding of the actual costs involved in manufacturing a product, incorporating all elements from the cost of raw materials and equipment right through to aspects like electricity, the cost of running the factory, and the costs of packaging, delivery, staffing and more.
Without effectively managed data, it is impossible to gain insight into these areas. This means that products thought to be profitable may actually be costing more than they generate, and those that were not thought to be money makers could become greater sources of revenue. What begins as a data problem can quickly become a business problem, impacting long-term sustainability.
Manufacturers are also now faced with the need to perform anti-money laundering initiatives on their suppliers, as part of a global effort to reduce financial crime. What this means is that data has now become more important than ever, as there is now an additional compliance risk.
Optimisation relies on data, from supply chain optimisation on the buy side, which helps to ensure that bulk discounts and buying on contract are effectively negotiated, to optimisation on the sell side through delivery schedules and just-in-time delivery. Even optimisation at the factory level can only be guaranteed if it can be measured. In reality, every area of manufacturing requires data to be effectively managed in order for its performance to be measured and improved. Perhaps even more crucially, data needs to be seen from an executive level as a strategic business asset that has a significant impact on the goals that are set for a business. For example, if the goal is to improve sales, executives need to ask questions like: Is the strategy to obtain more customers or to serve existing customers better? Do we fully understand how much it costs to manufacture goods and which areas need to be improved? How will data impact the goals we set for the business?
Ultimately, the key to unlocking value lies in understanding critical business objectives and the role that improving data integrity will have in achieving this. It should be clear that in the modern digital economy, data lies at the heart of understanding business – and this understanding is key to making better decisions across all areas.
Many manufacturers are investing in solutions to assist with integrated planning, but the reality is that without the right data, these investments will be wasted.
The Department of Business Management is a centre of excellence in the Faculty of Economic and Management Sciences at the University of Pretoria, with the aim of contributing towards the development of supply chain management practice, education and research in Africa. We strive to keep South African industry at the cutting edge of new development through access to both local and international knowledge.
The Department of Business Management offers a progressive range of formal qualifications and continuing education programmes in supply chain management designed to develop management potential and competencies at all managerial levels.
For more information visit www.up.ac.za/business-management or contact us on uscm@up.ac.za
Formal Qualifications in Supply Chain Management:
• BCom (ELA Accredited programme)
• BCom Honours
• MCom/MPhil
• PhD
Continuing Education programmes and short courses in Supply Chain Management:
• Programme in Supply Chain Management
• Advanced Programme in Supply Chain Management
• Executive Programme in Supply Chain Management
• Programme in Production and Operations Management
• Fleet Management
• Contract Management
• PFMA Bid Adjudication
• Business Process Management
• Business Process Modelling
• Customer Service Excellence
• Negotiation Skills
International experts in logistics have observed that the transportation and logistics industry is rapidly evolving, and it is imperative for companies to adapt to these changes to stay competitive in the market. In today’s fast-paced and demanding business environment, manual processes to source and procure transport are no longer effective. The world is moving towards sophisticated technology solutions
that connect with large networks instantly to always ensure transport availability and reduced transport costs.
Linebooker, a leading transportation and logistics platform in Africa, leverages technology to connect companies with a network of over 17 000 trucks across Africa from the top 700-plus transport companies. This platform has become the go-to solution for several of Africa’s biggest corporations,
including retailers, beverage companies, chemical companies, industrial giants, mega farmers, and hundreds of small and medium enterprises.
The reasons for this shift are clear. The cost of transport has risen significantly due to fuel price hikes, and consistent truck supply is becoming challenging. Companies are looking for ways to reduce their transport costs while ensuring a consistent supply. This is where Linebooker comes in. With its network of over 700 companies, clients can conduct a formal tender process on the platform to obtain fixedlane rates, request same-day ad-hoc trucks in just 30 minutes, and have the peace of mind knowing that Linebooker operational teams take full ownership and liability for loads.
TheLinebooker allocation platform allows companies to efficiently transmit load requests to chosen transporters, while the Linebooker bidding platform sends load requests to over 17 000 trucks. Transport Procurement has moved online, run a tender process to 700+ transport companies on the platform.
Linebooker is more than just a transportation platform; it has access to a network of over 700 top transport companies across Africa without any of the complexity of finding, onboarding or managing transport companies.
‘’Linebooker, South Africa’s Uber for freight, beats the stress test after month-on-month growth accelerates to 20 per cent,” said Alec Hogg, editor and broadcaster of BizNews.com in an interview.
The stress test, executed to ensure Linebooker’s platform could handle high volumes of freight during peak season, was a huge success and demonstrated the platform’s ability to handle large volume fluctuations and react quickly to maintain consistent supply.
Linebooker CEO Naudé Rademan attributes the growth to Linebooker’s unique quick access to over 17 000 trucks that can deliver reduced costs and its consistent supply of trucks. He says this is what has set Linebooker apart from traditional freight transportation companies.
• Customer 1: managing total volume of third-party supply; 99.7 per cent supply reliability (same day order cycle); plus 10 per cent reduction in total transport cost.
• Customer 2: managing total volume of third-party supply; plus 12 per cent reduction in total transport cost. Unexpected volume increase of 36 per cent and 100 per cent supply of trucks achieved.
• Customer 3: managing primary volume; plus 11 per cent reduction in transport costs and 99.8 per cent truck supply through peak season (same-day order cycle).
• Managing total volumes: 100 per cent truck supply, plus 13 per cent reduction in transport costs.
The company is now focused on expanding its services and continues to attract new clients due to its innovative and reliable platform.
Linebooker offers several options for companies to digitise their transport operations and choose the setup that best fits their needs. For example, companies can use the Linebooker procurement/tender platform to run a tender process with over 700 fully vetted and pre-approved transport companies. The Linebooker allocation platform allows companies to efficiently transmit load requests to chosen transporters, while the Linebooker bidding platform sends load requests to over 17 000 trucks and books trucks in just 30 minutes. One of the key benefits of Linebooker is the level of control and transparency it offers. You can monitor the progress of your deliveries to ensure they are on track. This level of control and transparency is essential in today’s fast-paced business environment, and Linebooker provides it in spades.
Another key benefit is the platform’s scalability. As your business grows, Linebooker can grow with you. With its network, Linebooker is equipped to handle even the largest transportation and logistics needs, making it the ideal solution for companies with fluctuating and unpredictable transport needs. Experience the future of transport procurement and operations with Linebooker, which reduces costs and ensures consistent supply.
As the supply chain embraces digital technologies, SEAN BACHER talks to a company that is bringing the “as-a-service” model to the field of logistics
The “as-a-service” concept has been with us for some years now, the most common being software-as-a-service (SaaS). The model is now migrating into a number of vertical markets, as seen by solutions like banking-as-a-service, games-asa-service and even identity-as-a-service. The main reason for using a product as a service is to cut costs. For example, renting a Microsoft Office 365 SaaS solution on an annual basis ends up being more cost effective than buying it outright, as you pay only for what you use.
So the real question is how as-a-service technology can be leveraged in the logistics space. A recent logistics report from Deloitte notes that customers and companies are becoming more data enabled, and thus expect their cargo companies to keep them up to date from A to B. They also want to deal with one person who understands their business and expectations, and who can provide feedback in real time.
One company that has made great strides in implementing the necessary digital solutions required to make the as-a-service principle work within the transport and logistics arena is Linebooker. In this article, we talk to the company’s chief technology officer, Hendrik van der Walt, about how it is taking the principle to new heights and is using it to streamline the logistics industry.
Please explain exactly what Linebooker does Linebooker improves supply consistency and reduces transport costs
by giving customers fast access to the largest network of transport companies in Africa. To do this, the company has engaged multiple freight companies across Africa, which are managed daily. The Linebooker platform and operations team facilitate this through efficiently managing tenders, transport operations, risk and payment of transporters for our customer base.
How many freight companies are currently on the Linebooker platform?
At present, the company contracts over 690 freight companies, each of which has been fully vetted in terms of insurance, service, assets, customer references and trade history. The 690 transporters equate to more than 17 000 trucks, which are designed to transport any load to any location in Africa.
How does the business differentiate itself from other logistics companies?
Linebooker differentiates itself in that it offers cloud-based products, accessible from anywhere, on any device. It is not just technology or a marketplace, but rather a digital freight and procurement platform that leverages a massive transporter base to bring clear benefits to its customers.
What are some of the key benefits of the platform?
The system is designed as a model where customers deal with a large number of service providers through a single channel. Customers can run a tender to the Linebooker network and contract multiple freight companies. Loads can
• Linebooker has over 300 customers from South Africa blue-chip companies, mining operations, mega farmers and more.
• More than 17 000 trucks operate on the system.
• Over 690 fully vetted and preapproved transport companies utilise the platform.
• Linebooker is a 66.85 per cent black-owned, level 2 BBBEE, 125 per cent enhanced procurement recognition supplier.
be done to more than one address and route. On the open-market bidding platform this can be done in under 30 minutes. As everything is done through the Linebooker platform, there is no need for numerous emails and phone calls.
How does the system improve things for customers?
The Linebooker platform makes a customer’s transport movements visible and gives them real-time data to improve decision-making in their business. Data supplied includes daily vehicle supply percentages, daily tonnage moved/remaining per supplier, full transport cost per tonne, analysis per route per transporter, and other live data that can be downloaded at any time.
Additionally the platform can be used to transmit load requests efficiently to chosen transporters as per a customer’s service level agreement (SLA). For example, one can plan and allocate 20 000 tonnes to any number of transporters in under 30 minutes. All transporter details and tonnage moved reflect in real-time, and the Linebooker team handles all operations, risks, and payments according to a customer’s SLAs.
“Linebooker improves supply consistency and reduces transport costs by giving customers fast access to the largest network of transport companies in Africa.” – Hendrik van der WaltHendrik van der Walt
Bursts of innovation in the supply chain have enabled companies to streamline routine processes, improve system capabilities and boost analytics. These gains are often followed by a lull, which is why technology gaps have occurred.
Far too many South African SMEs are unable to leverage the benefits of digital supply chain management fully because of inadequate access to the internet and digital infrastructure, particularly in rural areas. In addition, lack of funding, limited access to effective solutions, or a lack of internal technological expertise can also have a negative impact. Limited government support for digital innovation and a lack of investment in research and development further exacerbate the technology gap.
Without sufficient visibility across the extended supply network, companies are unable to see their risks. They don’t have the systems to understand the status of their inventory, project stock shortage of direct materials and optimise production, or project stock shortages of finished
goods to optimise customer allocation. They also lack the logistics flexibility they need to ensure the profitable movement of goods.
The pandemic showed how many businesses are vulnerable to global shocks through their supply chain relationships. It exposed weaknesses like long lead times, lack of visibility leading to higher risk of disruption, and the dangers of lack of diversification that come from excessive reliance on one location or supplier.
Technologies such as SAP Business One are available to improve visibility across the end-to-end supply chain, and support greater supply chain agility and resilience. By adopting digital technologies and accelerating the automation of business processes, companies can gain a vital edge in a tough market.
Digital supply networks like these are being built and designed to anticipate disruptions and reconfigure themselves appropriately to lessen the impact of events. They will enable the digital supply networks of the future, regardless of industry sector.
Seidor Africa recommends SAP Business One as a solution to enable companies to build a more productive and data-led business. The solution closes the identified gaps in three key ways:
• Businesses gain access to the real-time, reliable information they require to align components such as stock levels (in-stock and on order) with customer orders (current and backorder) and accurate delivery schedules.
• Businesses move from a reactive, back-capture methodology to continuous manufacturing processes where material consumption, stage updates and quality control data are entered in real time on the production floor to aid accurate stock management and replenishment, and efficient order fulfilment. Continuous manufacturing and electronic tracking are also key to identifying any potential inefficiencies in certain production lines or phases of production.
• Sales reps are able to view pricing and stock availability, and place orders in real time from their mobile phone or tablet while in the field or with a customer. Having these orders added to the manufacturing and subsequent delivery cycle automatically provides an invaluable advantage for businesses in the supply chain industry.
Without sufficient visibility across the extended supply network, companies are unable to see their risks.
Sustainability is not an uncharted topic for the transport and logistics industry. But in the race to profitability, fleet operators have tended to put sustainability on the back burner, but not anymore. The growing demand for sustainable transport – driven by government, shareholders, suppliers and customers, demanding greater transparency and accountability around the environmental impact of daily operations – is pushing the corporate world to be more conscious of its social and environmental responsibilities.
Companies that develop and invest in sustainable business practices and technology to aid their sustainability efforts can improve trust and engagement with their stakeholders and build credibility. Several key sectors have shown that telematics technology can help reduce harmful CO2 emissions. Fortunately, businesses can take actionable steps to contribute to the reduction of road transport emissions without overhauling their operations.
Investing in and optimising the use of telematics can help push fleets towards sustainability. The only way for fleets to achieve sustainability goals and remain competitive is through the data insights available through telematics.
Drivers and operators are the heartbeats of fleet-first companies. This is where significant changes can be made when fleet leaders are looking to impact tangible measures across their operations. Fuel inefficiency is an area that can increase a company’s carbon footprint considerably. The main contributor to this wastage is poor driver behaviour. Telematics is key to monitoring drivers’ behaviour and creating sustainable driving habits.
MiX Telematics’ fleet management technology is developed to monitor the driving behaviours that increase fuel use, such as excessive idling, harsh braking and acceleration.
MiX Fleet Manager Premium is an online platform comprising a sophisticated onboard computer that collects and transmits valuable
vehicle and driver data. Driving events, such as harsh braking, speeding, excessive idling, over-revving and harsh cornering, are captured by the hardware, providing insight into driver behaviour that negatively impacts the fleet’s energy consumption and carbon emissions.
Paired with the power of video telematics, businesses can further curb inefficient driver behaviour with a solution such as the MiX Vision AI camera solution. Systems capabilities: The AI-powered dashcam is enabled with Advanced Driving Systems (ADAS) capabilities, which gives drivers real-time coaching feedback during trips and the ability to review driving performance after the trip. The MiX Vision AI in-cab and road-facing cameras help prevent collisions, alert drivers to risky driving behaviour and save on insurance costs from wrongful claims against drivers with the available video footage of incidents.
“Telematics can help you reduce your carbon footprint while simultaneously increasing the efficiency and productivity of your fleet. MiX Telematics’ customers can significantly reduce their carbon footprint due to more efficient driving practices and optimising fuel utilisation,” says Henry Smith, Fleet Sales Director at MiX Telematics Africa.
The solutions provided by MiX Telematics also track a range of connected data metrics that impact your sustainability efforts in real-time. Driver behaviour is monitored, performance is tracked, and the location of all assets can be accessed, while engine diagnostics for preventative maintenance is available. Optimised route planning further aids business standards for productivity and efficiency.
“We aim to provide both the driver, operator and fleet leader with real-time alerts to mitigate risks, as well as interpreting the driver and vehicle data to provide insights into problem areas before they have a marked effect on sustainability efforts,” adds Smith.
For telematics solutions that offer tangible sustainability results, contact MiX Telematics.
For more information: www.mixtelematics.com/za/
The need for sustainable business practices in the transport industry can be met by telematics technology, writes MiX TeleMaTics
With so much in flux since the dawn of COVID-19, BENJAMIN VAN DER VEEN investigates the role of consultants in making supply chains shorter, more digital and increasingly sustainable
The past two-and-a-half years of disruption have demonstrated the insufficiencies in traditional and historical supply chain processes. Companies have increasingly discovered their actions can’t contend with constantly changing environments and new challenges.
Aside from COVID-19 lockdowns, supply chains have been impacted by numerous other chaotic disruptions in recent years, including the blockage of the Suez Canal, riots and unrest in parts of South Africa and issues at the Port of Durban, the container shipping crisis, and the power predicament across Asia and Europe.
“In 2022, we experienced yet another interesting and challenging year for supply chain professionals, as they continued to manage the disruption and volatility of the world,” notes MJ Schoemaker, president of the South African Production and Inventory Control Society. “Just as we thought that our supply chains could not be stretched any further, we all watched in horror as the twin disasters of floods and droughts affected South Africa. Business continuity has been difficult, and cracks in the armour of resilience are showing.”
Gary Benatar, chairman of Relog, adds that COVID-19 exposed the weaknesses of the supply chain sector, the risks of distance to sourcing, the impact of any disruption to the chain, and the issues of reliance on multiple countries, touches and infrastructure. “As a result, the importance of supply chains and the challenge of gaining a competitive edge from them are now front and centre. Of course we as consultants have been saying this for years, but now we are being believed and respected.
Even the US president is now talking about supply chains. So good and bad have both come from COVID,” he says.
The role of the consultant is critical, says Benatar, as businesses need to understand how all the relevant strategies and techniques can be applied and developed in an environment where constant change is standard and disruptive events must be managed.
The role of supply chain consultants
Consultants help businesses accelerate global supply chain realignment, and provide practical guidance and investment advice to help companies overhaul their supply chains. Consultants make a business’s supply chain more efficient, more resilient and faster, including by reducing costs and minimising inventory.
“A good supply chain consultant will bring a broader base of knowledge and experience than a company itself will usually have,” explains Benatar. “In a company, the focus is often on its own profitability and delivery, and the bigger picture of overall efficiency is missed. The internal operators get measured on internal metrics.
“A consultant, on the other hand, has only one objective: to bring efficiency and savings to the business, which should be their measure. Often suppliers offer consulting services, but then their focus becomes supplying more of their equipment. It’s how they are measured and focused. A good consultant brings independence and alternative ideas and thinking, as well as a broader focus.”
The most crucial supply chain trends emerging in 2023 will be geared towards future-proofing supply chains so they are equipped to
Companies must do things differently to mitigate risks and succeed in today’s challenging and constantly changing environment. South Africa needs forward-thinking supply chains so businesses, communities and economies can withstand future disruptions and volatility.
The main topics that will be topping the agendas of organisations aiming to future-proof their supply chains include:
• Supply chain resilience
• Flexibility, agility and transparency
• Human resources
• Training and education
• Digital transformation
• Sustainability and the circular supply chain
• Entrepreneurship and innovation
Sources:PlanetTogether,NortonRoseFulbright
anticipate and manage disruptions. For one
“A good consultant brings independence and alternative ideas and thinking, as well as a broader focus.” – Gary BenatarMJ Schoemaker
Logistics
War, raw materials shortages, rising energy costs and extreme weather conditions are just some of the factors that will disrupt global supply chains in 2023, warns SAPICS, the nonprofit organisation that strives to elevate, educate and empower the community of supply chain professionals across Africa.
“In South Africa, the electricity crisis will continue to challenge businesses across all sectors. Its negative impact will resonate through entire supply chains – from manufacturers to consumers, who will have to pay more and have fewer competitive options available on shelves,” says SAPICS president MJ Schoemaker.
“This year, businesses must aim for optimised execution, risk reduction, and enhanced agility and responsiveness in their supply chains. It will also be critical to identify new ways to gain a real competitive advantage,” she stresses.
The latest supply chain trends report compiled by the US-based Association for Supply Chain Management (ASCM), of which SAPICS is a Premier Elite channel partner, unpacked the supply chain trends that businesses must leverage in 2023 to achieve these goals. The report ranked big data and analytics as the most important topics in supply chain in 2023. These enable organisations to mitigate disruption through greater visibility, synchronised planning and execution, data-driven decision-making, predictability and supply chain agility.
Digital supply chains were ranked second in ASCM’s key trends in 2023. “Leading organisations will be advanced in their adoption of digital supply chain capabilities. If not, they will be left behind by agile, more proficient competitors,” cautions Schoemaker.
She notes that supply chain risk and resilience will be prioritised by successful organisations in 2023. The diversification of suppliers, production capabilities and transportation processes will be some of their key strategies. Forward-thinking organisations will also explore alternative materials and nontraditional partnerships, while many supply chains will become more compact and localised. Resilient supply chain design will also be critical for mitigating adverse events faster than the competition, providing excellent customer service and generating value and market share.
In 2023, artificial intelligence and machine learning will have a much greater impact on supply chains because processing huge data sets in real-time demands these capabilities. Using smart logistics solutions, based on the internet of things and next-generation robotics, will be a focal point of supply chain design.
Data security and cybersecurity are also hot topics that will impact supply chains this year. The more digital supply chains become, the more vulnerable their global networks are to cyberattacks. More organisations will invest in redundancy, firewalls, advanced antihacking technologies and employee training in 2023.
Circular and sustainable supply chains will be on the agenda of all organisations aiming to future-proof their businesses. “There is growing recognition that the traditional linear business model of take, make and waste must change. It has ecological as well as economic disadvantages, making raw material more expensive and increasing the likelihood of shortages and volatility,” explains Schoemaker. Continuous logistics disruptions in 2023 will drive the need for constant master data maintenance, as well as refined logistics parameters and inventory levels.
“While supply chain challenges will continue in 2023, we can expect to reap the benefits of lessons learnt in recent years,” Shoemaker states. “The pandemic and other disruptions highlighted the importance of supply chains for everyone. Supply chain management is better understood today. It is an increasingly attractive and sought-after profession. There is more emphasis on supply chain qualifications and continuous skills development.
“As the professional body for supply chain management, SAPICS will continue its drive to professionalise supply chain management. By professionally designating individuals, SAPICS aims to increase supply chain management competence, knowledge and skills, and industry professionals will have prescribed values and ethics to uphold. This will enable the profession to rise to the challenges of the continuing Great Supply Chain Disruption,” she concludes.
For more information:
010 013 3442
info@SAPICS.org.za
www.sapics.org
The Great Supply Chain Disruption will continue to challenge industries around the world this year, writes SAPICS, the professional body for supply chain management in Southern AfricaScan this QR code to go directly to the SAPICS website.
“This year, businesses must aim for optimised execution, risk reduction, and enhanced agility and responsiveness in their supply chains.” – MJ Schoemaker MJ Schoemaker
Following the severe impact of the pandemic on global trade, astute organisations worldwide are prioritising the supply chain and its contribution to overall business efficiency and competitiveness, as well as economic growth, writes SAPICS, the professional body for supply chain management in Southern Africa
Forward-thinking South African businesses committed to building strong, resilient supply chains that will withstand future disruptions are increasingly recognising the benefits of partnering with SAPICS.
“By joining the SAPICS supply chain community as a corporate partner, organisations demonstrate their commitment to improving their own supply chains and those of their clients, and supporting their employees in their professional development,” says SAPICS director Chantalle Wilson. “These organisations are also helping to shape the supply chains of the future and are at the forefront of developments and improvements in supply chain management, which, in turn, grows economies.
“Training requirements in the supply chain have increased,” Wilson notes. “Our profession has rarely been more challenged than in today’s volatile environment. There is a greater need than ever before for suitably qualified, professional, skilled and knowledgeable supply chain practitioners. One of SAPICS’s core focus areas is the professionalisation of supply chain management. Our corporate members share our commitment to this imperative.”
“SAPICS offers different levels of professional designation for supply chain practitioners, as well as impactful education and learning programmes, with special members’ rates for partner organisations. The SAPICS membership packages enable organisations to train, upskill and reskill more people costeffectively,” Wilson says.
“SAPICS corporate membership also provides organisations with vital opportunities to build their brand among the expansive and diverse SAPICS community, share their thought leadership articles, case studies, lessons and learnings, and use the available event opportunities to network and benchmark themselves,” she adds.
SAPICS corporate members come from organisations across the industry spectrum, from the automotive, consulting and manufacturing sectors to retail and information technology. The benefits of SAPICS corporate membership are available to businesses of all sizes – from large multinationals to small, medium and micro enterprises (SMMEs).
SAPICS is committed to the ongoing development of SMMEs. Through its Small Business Hub, SAPICS plays a vital role in the growth of SMMEs.
“SAPICS offers education and training geared to the specific needs of SMMEs. A series of SAPICS webinars offers content tailored to upskill and support small businesses,” explains Wilson. “We also provide mentoring and coaching to SMMEs.
“SAPICS has developed a basic business assessment tool that enables a small business to identify potential areas for improvement in the business. A special SAPICS membership package for SMMEs is offered to give all small businesses the opportunity to access our extensive network.
“Our aim is to provide the support and guidance that small businesses need to become successful, sustainable organisations that will grow and prosper. SAPICS is also proud to be a valuable conduit for corporate businesses to support SMMEs and participate in the development of their suppliers,” Wilson says. She explains that by taking out SAPICS memberships for their suppliers, organisations can earn enterprise and supplier development points and boost their B-BBEE scorecards.
for more information: 010 013 3442 info@SAPICS.org.za www.sapics.org
“One of SAPICS’s core focus areas is the professionalisation of supply chain management. Our corporate members share our commitment to this imperative.” – Chantalle Wilson
Supply chain practitioners from around the world will meet in Cape Town from 11 to 14 June 2023 for the annual SAPICS Conference, writes SAPICS
This year’s 45th SAPICS Conference –Africa’s foremost knowledge-sharing and networking event for the supply chain profession – features an exciting collaboration between SAPICS (The Professional Body for Supply Chain Management) and the South African Association of Freight Forwarders (SAAFF)), co-hosts of the 2023 event. This powerful partnership will benefit SAPICS and SAAFF members and the supply chain community as a whole, says SAPICS president MJ Schoemaker.
“We are delighted to be hosting the 2023 SAPICS Conference in association with SAAFF. Collaborative relationships between professional supply chain organisations are vital for driving knowledge-sharing and problem-solving, enabling communication and co-operation between different industries and different stakeholders and enhancing continuous innovation in the supply chain, which we need now more than ever,” comments Schoemaker.
SAAFF was established in 1921. For more than a century, it has played an essential role in freight forwarding and international trade, with members facilitating these activities through their dedicated involvement in the management of transportation, customs clearing, documentation, third-party payments, and many other elements of the international supply chain. “Consequently, we call the freight forwarder the ‘architect of the supply chain’,” says Juanita Maree, chief executive officer of SAAFF. “Globalisation has shrunk the market and accelerated the need to speed up processing and reduce costs across the entire supply chain. As such, this drive has refocused the freight forwarder on innovative and
functional ways. In addition, SAAFF is actively working towards a safe, secure, and compliant logistics network, ensuring greater benefits for security and transparency. We are honoured to partner with SAPICS in the 45th annual SAPICS Conference,” she says.
Reflecting the unprecedented challenges facing supply chain professionals in today’s increasingly volatile, uncertain and complex business arena, SAPICS has announced that the theme of the 2023 conference is “Forward Thinking Supply Chains”.
“The past two and a half years of disruption have shown that traditional and historic supply chain processes are insufficient,” Schoemaker says. “Business continuity has been difficult, and cracks in the armour of resilience are showing. Companies must do things differently to mitigate the risks and succeed in today’s challenging
and constantly changing environment. We need forward-thinking supply chains that can anticipate disruptions and have processes to manage them in an environment where constant change is standard.”
The 2023 SAPICS Conference will explore the leading topics that should be topping the agendas of organisations aiming to future-proof their supply chains. These include:
• Supply chain resilience;
• Flexibility, agility and transparency;
• Human resources;
• Training and education;
• Digital transformation;
• Sustainability and the circular supply chain;
• Entrepreneurship and innovation. Local and international experts will share their insights on these and other supply chain issues and opportunities at the 2023 SAPICS Conference.
“Because supply chain management is a constantly changing and evolving profession, it is vital for all supply chain professionals to keep updating their skills sets and knowledge and honing their expertise. The SAPICS Conference is the ideal place to do this,” Schoemaker explains.
For further information or to register for the 2023 SAPICS Conference, call the Conference Secretariat at Upavon Management on 011 023 6701 or email info@upavon.co.za. Up-to-the-minute information is posted on the SAPICS conference website.
For more information: 010 013 3442
info@SAPICS.org.za
www.sapics.org
The 2023 SAPICS Conference will explore the leading topics that should be topping the agendas of organisations aiming to future-proof their supply chains.Juanita Maree
The Chartered Institute of Logistics and Transport (CILT) is a family of 35 000 members in 35 countries, dedicated to giving individuals and organisations access to the tools, the knowledge and the connections vital to success in logistics, transport and supply chain. Through our educational suite of programmes and our commitment to high standards, we help professionals at all levels to grow, to develop their careers and to access better jobs.
• Professional designations – get the local and international recognition you deserve: MILT/CMILT/FCILT
• Connection
• Professional voice
• Professional recognition
• News and publications
• Personal development
The future of our industry rests in the hands of the next generation, and we have a responsibility not just to support today’s leaders, but to nurture tomorrow’s.
Through CILTSA’s Next Generation Forum, we provide enhanced networking and support opportunities for members in the early stages of their career.
WiLATSA is a CILTSA interest group designed to support women in the logistics, transport and supply chain industries. It is part of the wider CILT International network with branches in 14 countries and over 1 600 members worldwide. Its vision is to be the most soughtafter group for advocacy, professionalism and empowerment of women.
In the transport, logistics and supply chain industry. WiLAT exists to:
• promote the status of women in the logistics, transport and supply chain industries
• bring together those who support the talent and career development of women
• provide a support network and mentoring opportunities for women working in the industry
The Chartered body for professionals involved in the movement of goods and people, and their associated supply chains. Delivering career development, relevant information, networking and professional recognition.
I belong to CILTSA because it provides an unrivalled conduit for me to learn and stay up-to-date on industry developments.
Martin Bailey FCILT Chairman: Industrial Logistic SystemsI joined CILTSA to assist in enhancing the professional profile of transport, logistics and supply chain industries. Being a member of CILTSA enables me to mentor and empower youth looking to pursue a career in the industry.
Dr Khulumane John Maluleke CMILT Doctor of Commerce in Transport Economics and Honourary Professor in Logistics Management – University of PretoriaI joined CILTSA because I recognised how critical it is to stay ‘current’ with developments in the supply chain space if I wanted to stay relevant. I’ve spent most of my career in business development roles and our clients are becoming more sophisticated. CILTSA makes it easy to stay connected and informed in terms of industry dynamics.
Nobantu Mqulwana MILT Managing Director at Rising Tide Advisory & Project ManagementCILT is a professional body that demonstrates various ways of impacting members and associates - with knowledge and platforms that bring insight, development and exposure. The level of CILT’s determination to reach out to professionals in the logistics, transport and supply chain industries is commendable. I foresee massive positive changes in our logistics world in the next 5 years if we carry on in this manner. These, and many more reasons, are why I’m glued to CILT!
Josephine Ofori-Amlankwah CMILTNext steps
Contact us today for more details on individual and corporation membership options
Contact Details
087 822 2858 � 083 300 0331 � info@ciltsa.org.za � www.ciltsa.org.za
@ciltsa
@Chartered Institute of Logistics and Transport South Africa Twitter (use icon): @CILTSA
OUR CILT-ACCREDITED TRAINING PROVIDERS
BIZZCO Ansonet van Deventer 010 001 0283 ansonet@bizzco.co.za www.bizzco.co.za
Commerce Edge Clintin Chetty 0861 133 4326 clintin@commerce-edge.com www.commerce-edge.com
Harley Reed Olive Gumikiriza 011 312 8411 olivegumikiriza@harleyreed.com www.harleyreed.com
Harvesthouse Gift Muzimba 012 753 8007 giftmuz@harvesthouse.co.za www.harvesthouse.co.za
IMM Graduate School Christa Kavungo 011 628 2000 christak@immgsm.ac.za www.immgsm.ac.za
Institute for Quality
Adrian Petersen 011 472 0981 adrian@iqetd.co.za www.iqetd.co.za
Supply Chain Academy
Truman Hadebe 087 057 6577
cilt@supply-chain.academy https://supplychainacademy.co.za/diplomascourses/
upply chains in Africa face many challenges. These include the prevalence of dual carriageways, port congestion, delays in border crossings, foreign exchange and economic uncertainty, and many more.
At CEVA Logistics, we have met these challenges head-on to make a meaningful difference in the supply chain. In October 2021, we created a Centre of Excellence Control Tower in South Africa, where we are able to provide better services for seven countries in Southern Africa, including:
• Angola
• Botswana
• Malawi
• Mozambique
• South Africa
• Zambia
• Zimbabwe
In Africa, one of CEVA’s core strengths is ground transport services. To further develop our ground services, we made the bold decision to acquire Manica, a ground services company located in the Zambezi region. We were able to strengthen and transform the former Manica business into a stronger business by centralising operations under our Centre of Excellence in South Africa. With looming uncertainties in the supply chain industry and the overall economic outlook at the time of the transformation, we knew we had to find a way to optimise operations for our clients – and this acquisition was just the ticket.
Our customers needed an efficient supply chain solution that would provide them with end-to-end logistics services across the seven transit countries at an affordable price. Our Centre of Excellence was pivotal in establishing a model that enabled distribution from multiple source locations to multiple destinations using various service providers. This solution offers customers a single point of contact for their transport needs across the seven countries. By creating a lean operation, we managed to reduce our customers’ supply chain costs by approximately 10 to 15 per cent.
A majority of the beneficiaries of our Centre of Excellence project include exporters of African products, such as vermiculite, copper,
tobacco and pigeon peas, among others. Prior to launching our project, many shipping containers with imported cargo were returning empty, however, with a better co-ordinated operation, we were able to offer exporters our transportation services to the port at heavily discounted rates. In addition, the introduction of CEVA global technologies helped our clients track their shipments.
With regard to our own operations, in less than one year of launching the project, we witnessed soaring volumes in shipments from Beira (Mozambique). In response, we created a solution whereby transport planning and management is centralised into a supply chain Centre of Excellence and is supported by a robust technology platform, managing everything from daily administration to analysing data and providing business intelligence insights.
Our centralised approach has established an environment that thrives on continuous improvement and seamlessly connects different parts of Africa under one supply chain model. We’re committed to innovative solutions that benefit our customers and improve their supply chain and overall business success.
Our customers needed an efficient supply chain solution that would provide them with end-to-end logistics services across the seven transit countries at an affordable price.
Keep
With Ctrack’s 35 years experience, we can help you unlock better diagnostics, support compliance reporting, as well as provide tailormade analytics for both short term, and long-term decision making. Ctrack will optimise the right solution for your specific business needs.