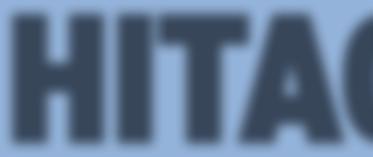
7 minute read
OWNER-OPERATOR
HITACHI
Below and inset: AJ Browne Civil Engineers is a specialist drainage contractor running three frontline Hitachi excavators.
Advertisement
DRAINAGE FAN
Paul Argent visits a key site in the manufacture of rolling stock for the HS2 project to speak to an ardent fan of Hitachi excavators A
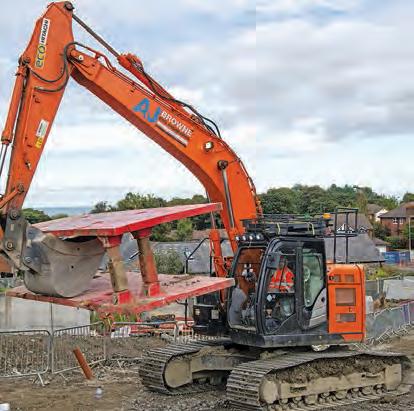
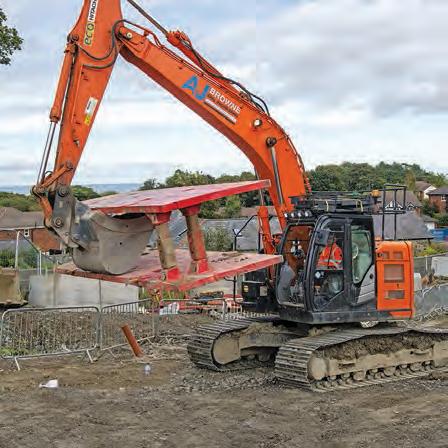
lan Browne is a man who loves his Hitachi excavators, stating that he wouldn’t have anything else. A native of County Kerry, he is based in Birmingham and works across the UK undertaking drainage work. Supported by a small team, he has extensive experience of installing drainage systems: from housing developments to new industrial complexes, he has done them all.
We first met him working for one of North Wales’s leading civil engineering companies, John Kelly Construction. He said, “John had asked us to put in all the deep drainage throughout a site in Colwyn Bay. It was a typical housing development, where we had some deep excavations to undertake in what was going to be the main road through the site, while still keeping access to the project open at all times.”
Alan and his team then completed another large project for Kelly Construction, before undertaking similar contracts through the Midlands. They are currently looking forward to returning to North Wales to work with this company once again.
Alan undertakes and manages projects from the cab of his 2019 Hitachi 350-6, which he says is probably the best excavator that he has ever owned. In long carriage (LC) configuration, it remains planted to the ground during extreme lifting and excavation operations. For example, during our subsequent site visit, he was excavating 1050mm-diameter concrete pipes out of the ground and then lobbing them into an adjacent dumper, with apparently little effort. He commented, “We’ve lifted some big pipes and manhole bases with her and she’s always a stable machine. It’s also a very fast machine and there’s also plenty of power there, but this doesn’t make it undriveable, as it’s very smooth and precise.”
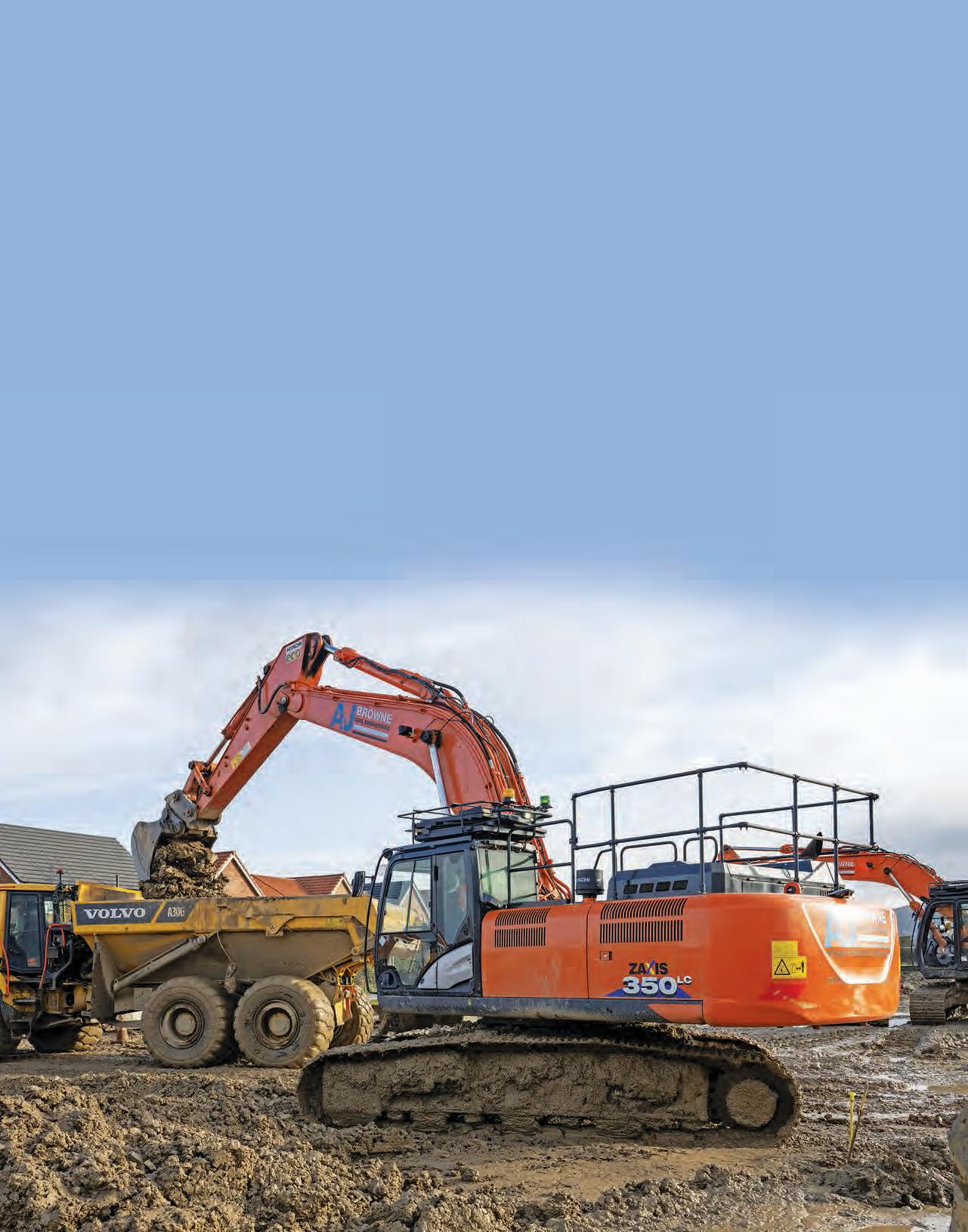

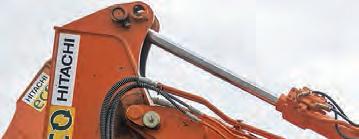
Alan has removed the auxiliary hydraulic services from the dipper stick of his 35-tonne excavator, except for the quickhitch line, to minimise its width and the potential for damage, as he explained: “It’s just too easy to snag them on a trench box. Not only does this cause damage to the machine, with the associated downtime, but there’s also the risk of contaminating the ground you’re digging in.”
SITE BACKGROUND
We later met Alan and his small team in a very different working environment to a new housing development, at the former Bombardier train works in Derby. This site has been used to build and repair trains since 1840 and has recently been taken over by Alstom, one of the world’s leading engineering companies. In a joint venture with Hitachi, Alstom will build phase one of the rolling stock requirements for the new HS2 route, and the Derby facility will play a major role in delivering this contract.
Alstom is undertaking a significant programme of upgrading works on the site, and infrastructure specialist Buckingham Group has won the contract to deliver additional train manufacturing and testing capabilities. In the limited space between an existing maintenance facility and the busy mainline railway, a new manufacturing shed is to be constructed, along with additional rolling stock testing and storage lines.
WORKING METHOD
Working on behalf of RMF Construction Services, Alan’s first task on site is to remove sections of the existing concrete drains and associated gullies. He will then immediately replace them with new HDPE drainage elements. Working across the footprint of the new facility in this way ensures that the site doesn’t flood as the works are in progress, allowing early access for the chain of sub-contractors.
Alan said, “It would be a lot easier if we were able to rip up the existing drains and then re-lay the new. As there is a tight timescale for the project, we have to complete the works as we progress, so other trades can follow on behind us.”
Saying that, Alan’s approach to undertaking drainage work seems ideal for such working limitations, as he deploys all three of his front-line excavators to such jobs. All Hitachi models, they include a wheeled Zaxis 145W, which on this contract is used with a hydraulic breaker and to undertake general loading and carrying work. A short-tailswing 225USLC-6 excavator with a suitable hydraulic attachment undertakes the compaction work.
Alan continued, “We have a limited amount of time to complete the works: whether on this site or any other one we work on, we have to work productively at all times. We have my Zaxis 350 doing most of the excavation and laying works, while the Zaxis 225 undertakes backfilling and compaction works.”
With Alan stirring the levers on the 35-tonner, he quickly changed buckets to allow him to excavate a new location for a manhole base. With the ground being made up during the installation of the previous pipework, he ensured there was sufficient room around the base to stop any ground from slipping in. This chamber is just over a metre below the finished ground, so trench boxes weren’t being
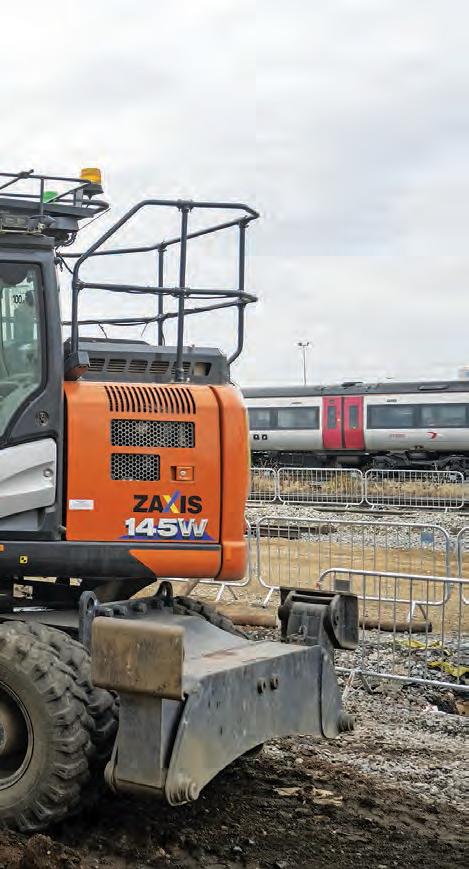
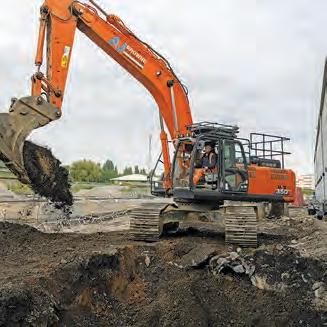


Left, inset and below: Using the 350 for excavation and pipe-laying, the short-tailswing 225 for compaction and backfi lling and the wheeled 145W for breaking and loading resulted in rapid progress.
Above, inset and right: Alan Browne loves his Hitachi excavators; he reckons that his three-year-old 350LC-6 is the best machine he has ever owned.
used. As the work progresses, deeper cuts will be required, as Alan commented, “That’s another thing I like about the 350. Even in the stickiest of ground, the digger will always have the power to lift the trench box clear.”
The Zaxis 225USLC-6 is used for compaction duties around the pipework with an Allied compactor plate, Alan said, “It’s a quicker and a far safer option than putting a man in a trench with a compactor. We know there’s going to be no issues with any of the ground subsiding around our pipework in the future. This puts our minds and those of our clients at ease.”
The 145W wheeled excavator is configured with a front blade, rear stabilisers and a two-piece boom to provide a versatile workhorse for the team. It was originally purchased for works at London City Airport, which mandated the use of the Fhoss Halo safety lighting system.
The system is great in the dark, but according to Alan is useless in the daytime: “We do wonder why these systems have to be fitted sometimes. At night, the machine is all lit up with working lights both front and rear. Having a Halo light doesn’t help people identify the machine, it’s just another thing that detracts from using common sense on site.”
The 145W was kept busy at the Derby project breaking out the gullies and bends round the existing shed, using an OKB hydraulic breaker. Following a quick change to a bucket, the machine was then off to the top of the site to load pea gravel into the two nine-tonne capacity dumpers. Alan hired them in for the project, saying, “We tend to hire dumpers in for each specific project, as it’s more cost-effective for us.”
As this project is on track to finish on schedule, Alan is already starting to look at other projects, including a return to North Wales to work for the John Kelly team. He said, “We like North Wales,” and then, with a grin, “It’s like being back on holiday.”
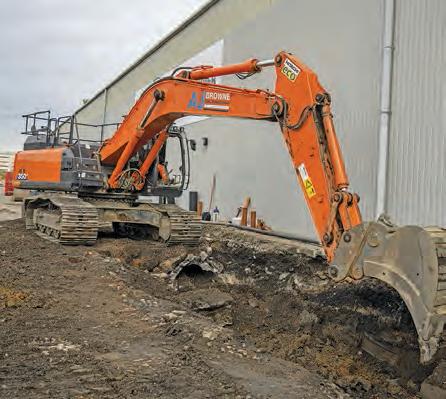
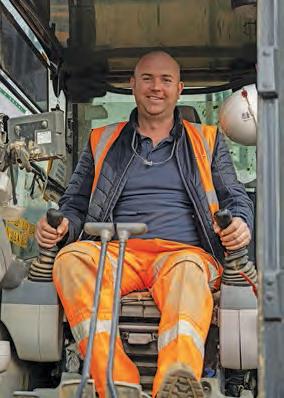
