
6 minute read
SITE VISIT
STRATEGIC SAFETY SPOTLIGHT
Paul Argent visits the largest construction project currently underway in the UK, to report on a Volvo EWR130E rubber duck fitted with Xwatch’s 1500th slew and height restrictor
Advertisement

B
ritain’s new high-speed rail line, HS2, is being built from London to Birmingham, the second stage taking the line through to the heart of the rail system at Crewe in Cheshire. The project will see over 170 miles of a new high-speed rail route installed between London and Crewe. A third phase, yet to be approved, is planned to link Crewe with Manchester. Allied to other rail upgrade projects, the Government hopes that this huge investment will bring fresh life to the rail network, making it better able to serve future generations.
PROJECT BACKGROUND
Due to the sheer magnitude of the HS2 rail project, at a very early stage it was decided that it was just too large for only a single main contractor to undertake the work. Indeed, some sections of the route would require a collaborative approach, combining the skills and specialities of different main contractors. With this in mind, several joint venture partnerships were formed to bid for, then undertake the most challenging aspects of the project.
We met SCS joint venture, one of the leading contractors on this project and comprising Skanska, Costain and Strabag. The last is a giant Austrian-based transport infrastructure, tunnelling and civil engineering contractor. SCS is delivering the southernmost section of the HS2 route, the 26.4km stretch in and out of the London Euston terminus.
A variety of new structures are required along the route, but for all practical purposes this section of the new high-speed rail link will be carried in tunnels. SCS will be running seven tunnel-boring machines (TBMs), of which five will operate simultaneously.
Left and below: Congested, safety-conscious sites are increasingly asking for excavators to be fi tted with height and slew limiting systems.
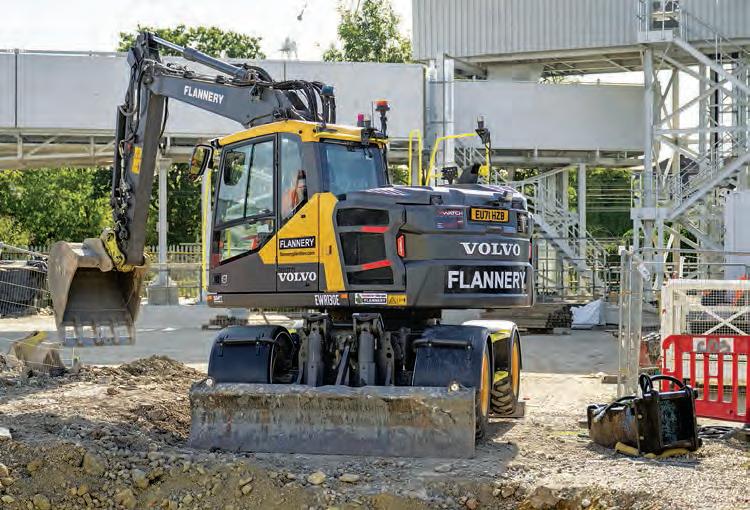
While the TBMs excavate the tunnels, there is a huge amount of overground work to undertake. One of these tasks is the installation and maintenance of a massive conveyor system, to transport the tunnelled material to a nearby railhead. This conveyor and train combination replaces hundreds of daily truck movements in central London, which would have been required to remove the spoil generated by a fleet of TBMs.
SAFETY FIRST
the British company Xwatch Safety Solutions.
Flannery has been using Xwatch systems for two years, and was an early adopter of the XW range of easy-to-use slew and height restrictors, followed by Xwatch’s RCI (rated capacity indicator) systems. Xwatch says that its system is the only slew and height restrictor approved by Network Rail to work adjacent to the rail.
Such major public-funded projects are pioneering modern methods to organise and manage this work (see panel overleaf), which includes delivering the desired result with the highest possible levels of site safety. This ethos is clearly evident within the SCS joint venture and its principal machinery supplier, Flannery Plant Hire.
In addition to establishing a plant operator recruitment and training regime specifically to serve its work across the HS2 project, Flannery has also pioneered the widespread fitment of movement and lift restrictors across its fleet of excavators, specifically the emerging technology from
SITE VISIT
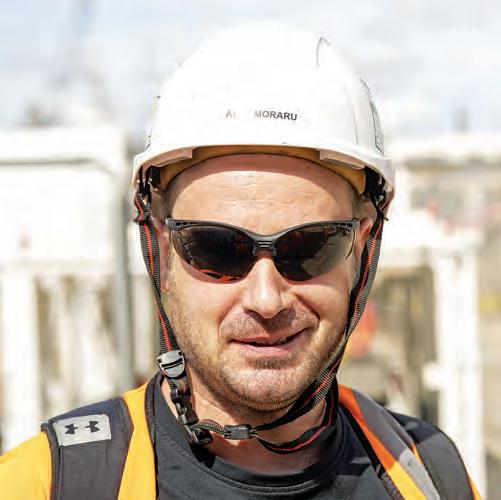
In three years of trading, Xwatch has supplied over 1500 safety systems around the world. Appropriately, the 1500th unit was fitted to a new Flannery excavator, a compact radius, 13-tonne class, wheeled Volvo EWR130E. We discovered it on site at the Victoria Road Crossover Box, near Old Oak Common in West London, which will allow HS2 trains to switch tracks underground.
Flannery has a number of these high-spec rubber ducks, which are equipped with a two-piece boom carrying a 2.4m dipper and a Miller quick-hitch, with an undercarriage configured with both blade and stabilisers. They are proving to be increasingly popular on the HS2 project and are finished with a full suite of LED lighting, hi-vis handrails, a travel alarm and additional flashing beacons. It also has the Xwatch XW4 height and slew movement protection system fitted, handy in what can, at times, be a tight and congested working environment, particularly in view of the various roles that such a wheeled excavator is put to on such a project. Its operator, Alex Moraru, makes best use of the EWR130E’s all-wheel steer system to position the machine exactly where it’s required.
Jason Wells, the SCS manager for the Victoria Box section of the HS2 project, explained, “We take our health and safety very seriously. Having the Xwatch ensures the machines are always working safely within their prescribed zone. We have a very busy and often congested site. Any technology that can make the working day safer is welcomed by SCS.”
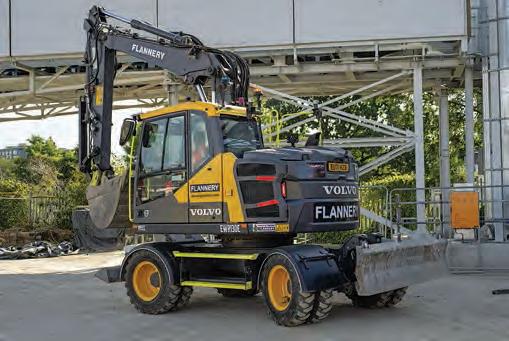
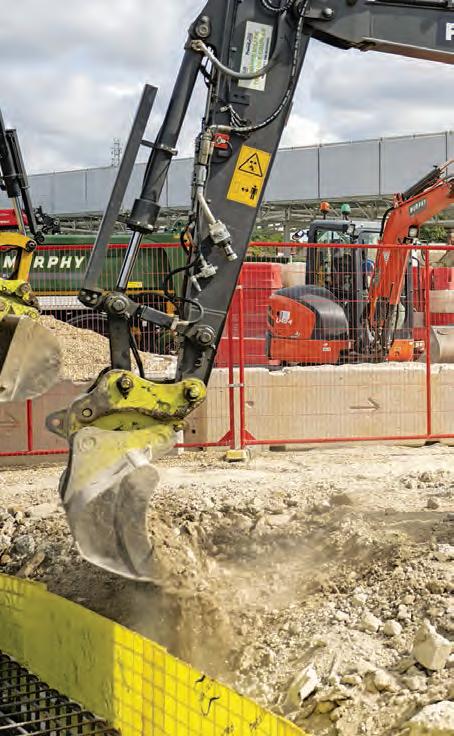
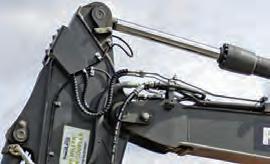

Above, left, inset and below: Commenting on the Volvo EWR130E, operator Alex Moraru said, “It’s a very good machine to operate, quiet and comfortable and with plenty of digging power.”

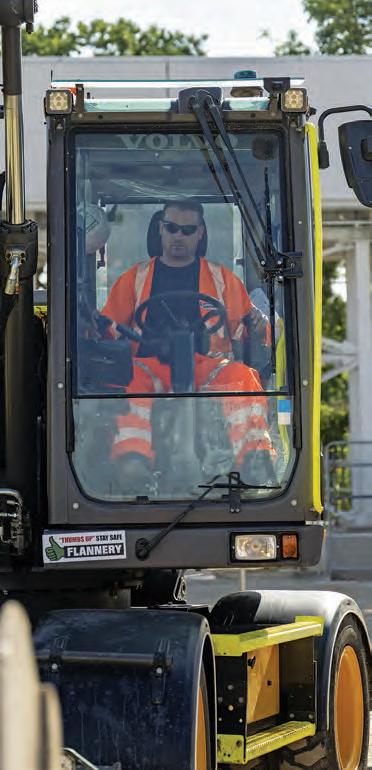
“WE HAVE A VERY BUSY AND OFTEN CONGESTED SITE, ANY TECHNOLOGY THAT CAN MAKE THE WORKING DAY SAFER IS WELCOMED” EDITOR’S COMMENTS: CONSTRUCTION 2025
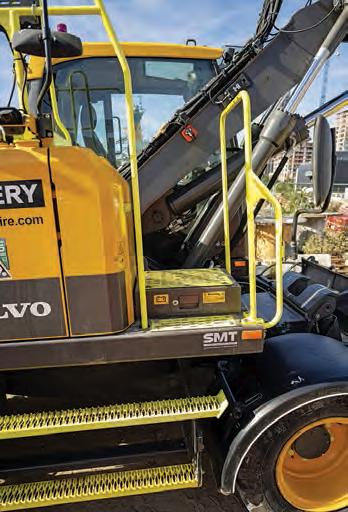
Almost a decade ago, the UK Government published its ‘Construction 2025’ document, which outlined a vision of the future of the construction industry. It set ambitious targets for lower costs and emissions, together with faster project delivery times. In turn, this would encourage growth in the wider industry, particularly on the international stage.
This was to be achieved by a variety of means, including the widespread adoption of new technologies and major changes to how the supply chain was organised. We fi rst saw the practical results of the thinking behind Construction 2025 on major road projects undertaken by National Highways. They pioneered a far more collaborative approach between all the interested parties, in addition to introducing a range of new digital technologies, all to improve how the site and fl eet assets were managed, particularly in the mass muck-shifting stage of the project.
One result of this is the change in status of the plant hire companies serving major public sector projects. Such fi rms are no longer just a potential source of machinery, but are an earthmoving contractor to the project. It’s a role that requires the establishment of an extensive infrastructure, particularly to train machine operators and ensure the highest standards of site safety, in addition to supporting the machines on site.
The fi rst item in the summary of the aims of Construction 2025 includes the words, ‘An industry that attracts and retains a diverse group of multi-talented people, operating under considerably safer and healthier conditions.’
UK Construction PLC is a far safer and healthier industry than it was a decade ago, but it is still a dangerous occupation. As the single largest client of the labour-intensive industry, the UK Government is, quite rightly, demanding further improvements in site safety.
They will come from how the work is planned, undertaken and managed, but we are already seeing an impact when it comes to machinery selection and specifi cation. For example, the A14 road project pioneered the use of cabbed site dumpers, together with a range of operator visibility and anti-collision aids. An early result of HS2 appears to be the far more widespread use of excavator height and slew restrictor systems.