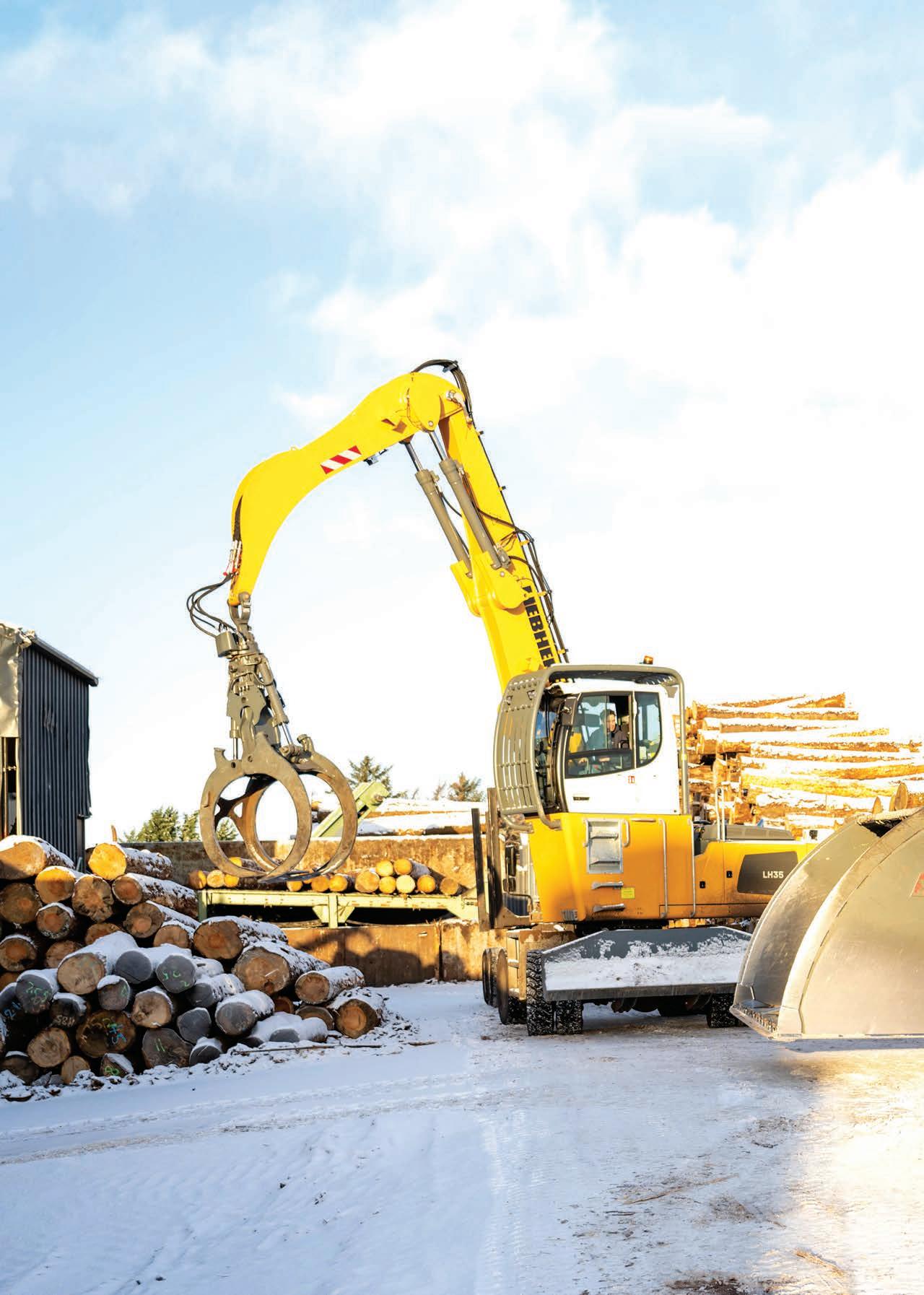
4 minute read
ON BRAND
Paul Argent pays a visit to A&J Scott, a sawn timber supplier based in Northumberland, to find out how its Liebherr fleet including a new LH35 Timber handler is helping to cut costs
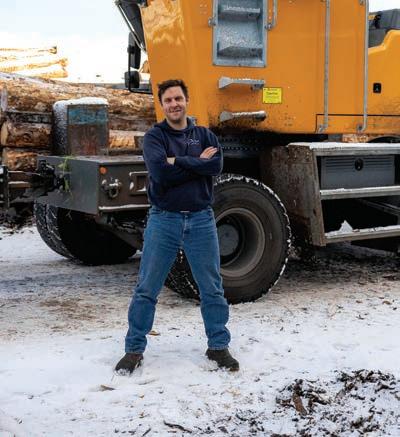
Advertisement
Operating from its headquarters in Wooperton, Alnwick, A&J Scott has been supplying sawn timber for a wide variety of uses, principally in the fencing, landscaping, DIY and pallet and packaging sectors since 1960. The family-owned company still operates from its original Northumberland site but has grown massively over the past 60 years to employ over 150 people and expand its operations to what is now one of the most sophisticated and productive sawmills in the UK.
With a strong team of long-term employees, the company’s vast knowledge of timber and enviable, experienced skill base provides top quality products supported by unrivalled standards of service. Not a company willing to rest on its laurels, Scott’s continuing investment in state-of-the-art production facilities has seen the multimillion-pound investment in further automation of the plant with a new scraper conveyor, grading line and sorting and stacking lines to support its ability to produce large volumes of consistently high-quality products, serving an increasingly diverse customer base.
Fleet Overhaul
Recent times have also seen the company look at investing and installing solar power for the sawmill which, like many industries in the UK has seen their costs increase massively thanks to the wholesale hike in energy costs. “Like many, we have had to endure the ridiculous hike in energy costs and sadly pass some of it onto our customers. The investment in solar power for the plant will hopefully alleviate these increases over the next few years and also allow us to decrease our carbon footprint,” Senior Purchasing Manager, Adana Black commented. The company has also been hit with the change of fuel use moving from red to white almost doubled its running costs overnight. The wider forestry industry still runs on rebated fuel and Scott was hoping that this would be the case for itself as it considers itself an extension of that industry. Sadly, this wasn’t the case, and this has led the company down the road of looking at its core material handling eet savings.
The latest addition to the eet of material handlers has come from the team at Liebherr GB in the shape of an LH35 Timber. The dedicated pick-and-carry machine joins two smaller material handlers, an LH30 and LH26, an L556 XPower wheeled loader and a T36-7 telehandler. “With the increase in fuel costs, we wanted to increase the size of our material handler allowing us to do more with a single machine,” Adana explained.
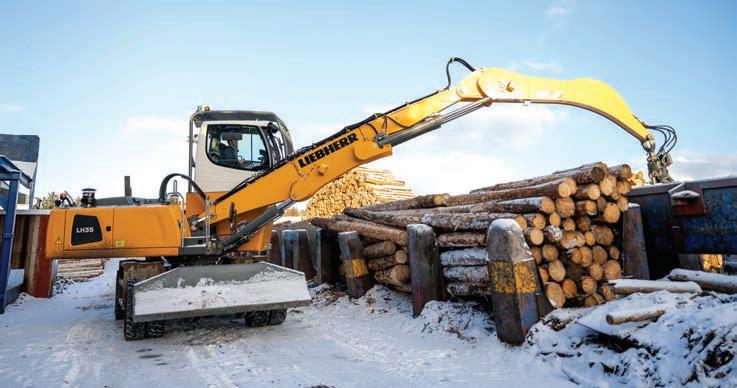
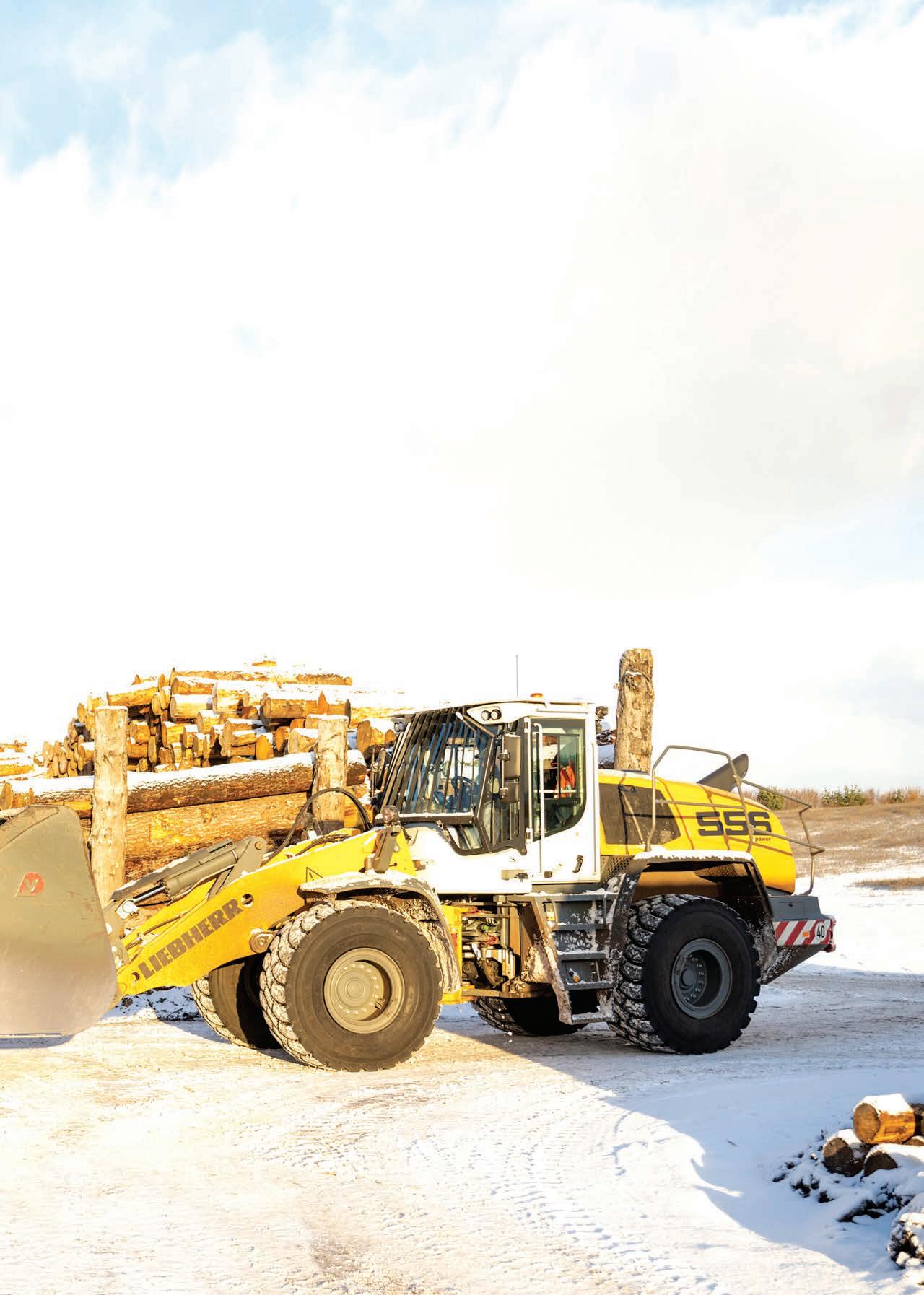
The LH35 Timber is one of four dedicated timber handling machines within the Liebherr range of material handlers. With an operating weight of 30 tonnes and a reach of 11m, the LH35 possesses a similar reach to the smaller LH30 and LH26 models in the eet but boasts a larger 1.7m3 timber grab allowing it to be more productive over the slightly smaller machines. The new LH35 Timber has been handed to one of the company’s longest serving operators James Smith who has been with the company for over 13 years, all of which he has spent operating the company’s material handling eet.
Smooth Operator
“I started off on the green ones we had before moving onto the Liebherrs and it was like night and day!” James joked. “The Liebherrs are a true material handling machine. They’re such a stable machine even at full stretch. This latest one has been supplied with a xed cab riser which I prefer. On the hydraulically raising models there seems to be a little bounce when you travel around. You get used to it, but the xed version is so much smoother even though it’s a bit more of a climb in and out of the cab!”
Unlike a traditional material handler chassis which has one xed and one steering axle, the Timber machines boast steering axles both front and rear with the Scott machine having the single blade option. A blade/outrigger or blade/blade option is also available. The heavy-duty chassis allows the LH35 to pull a small bolster trailer around the yard further improving its versatility and productivity. At 3m in width, the undercarriage provides a very stable base for the machine to operate from yet thanks to the front and rear steering, the LH35 retains a turning circle of just under 6m. A wider, EW version is also available.
Out And About
Power to the LH35 comes from a 7-litre, 4-cylinder Liebherr D934 engine that meets Stage 5 emissions regulations. Four work modes (Sensitive, Eco, Power, and Power+) allow James to select the best combination of power and economy to suit his job at hand.
“I usually keep the Liebherr in Eco mode as it gives the best all round performance,” James con rmed. Whilst the LH30 and LH26 undertake the handling work in the main stock yard, the LH35 is used across the entire site moving a variety of logs around along with feeding the mill from both the trailer and the bins situated at the side of the grading lines. The 2-speed powershift transmission provides stepless speed increases and allows the LH35 to navigate two steep ramps within the yard with consummate ease, even with a full load.
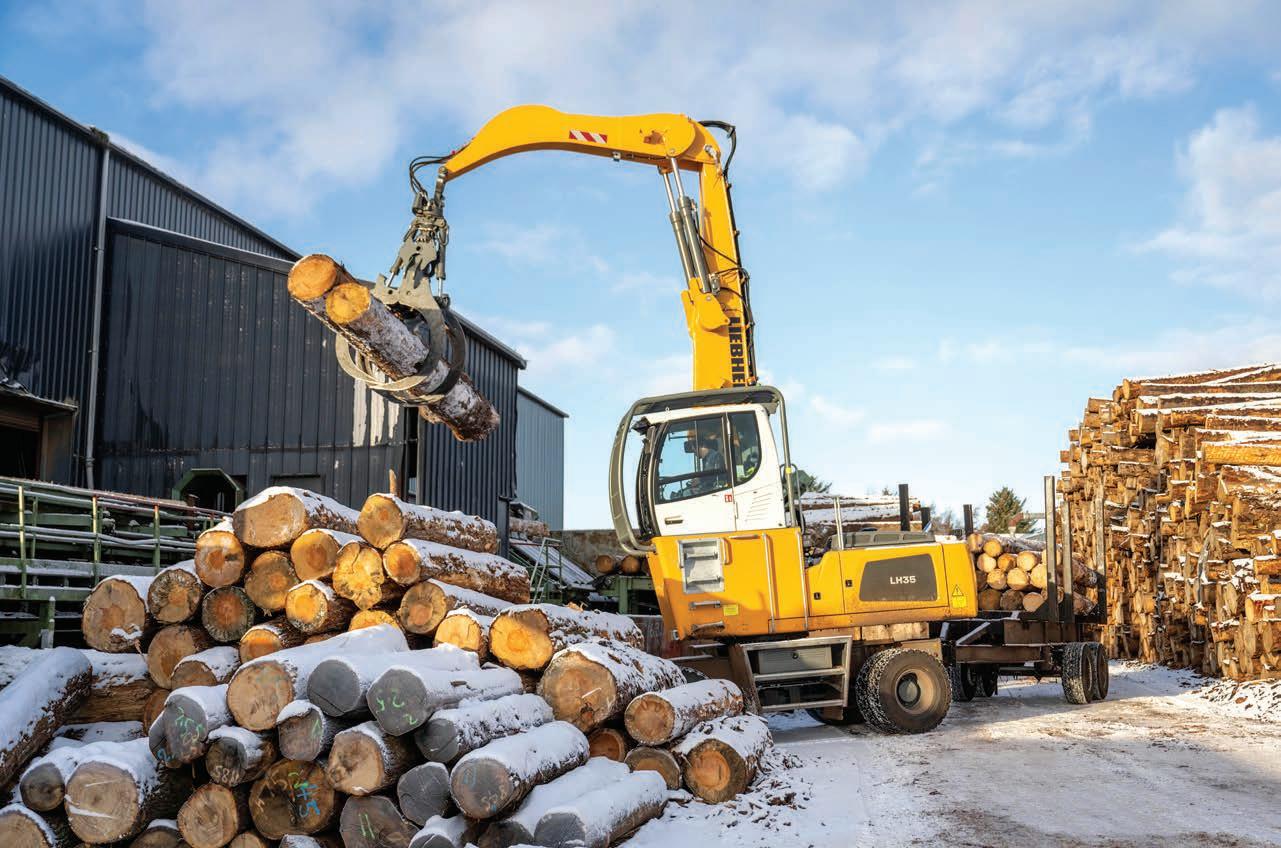

Cost Effective
“With the change in yard and processing plants we looked at our eet of material handlers with a view to looking at how we operate, how the drivers operate and the way in which the material is handled on site,” Adana said. “Traditionally, we have had a 24-hours-a-day operation, which has meant drivers moving between machines. The addition of the new plant has allowed us just to have a single machine on night shift, reducing the hours incurred and fuel used.
“We have also looked at our overall service and maintenance costs for the material handling eet and with every new machine, truck or forklift added into the eet, we enter into a service contact with the manufacturer or dealer,” Adana added. “This gives us a known gure for any servicing or maintenance costs allowing us to document the costing of a particular piece of machinery over its entire life in the eet.”
With the arrival of the L556 XPower, T36-7 and now the LH35, Scott’s switch to a more managed solution for its material handling requirements has put it on the road to managing its long-term costs and requirements far easier than before. The before being replaced and, whilst always open to looking at other makes, Adana and the team are keen to stick with a single brand. “We have been speaking with Mike Hanlon and his team about our requirements for the next couple of years as lead times still remain long for some machines. We have put into place parts price agreements and are very pleased with the response we are getting from the Liebherr GB team.”
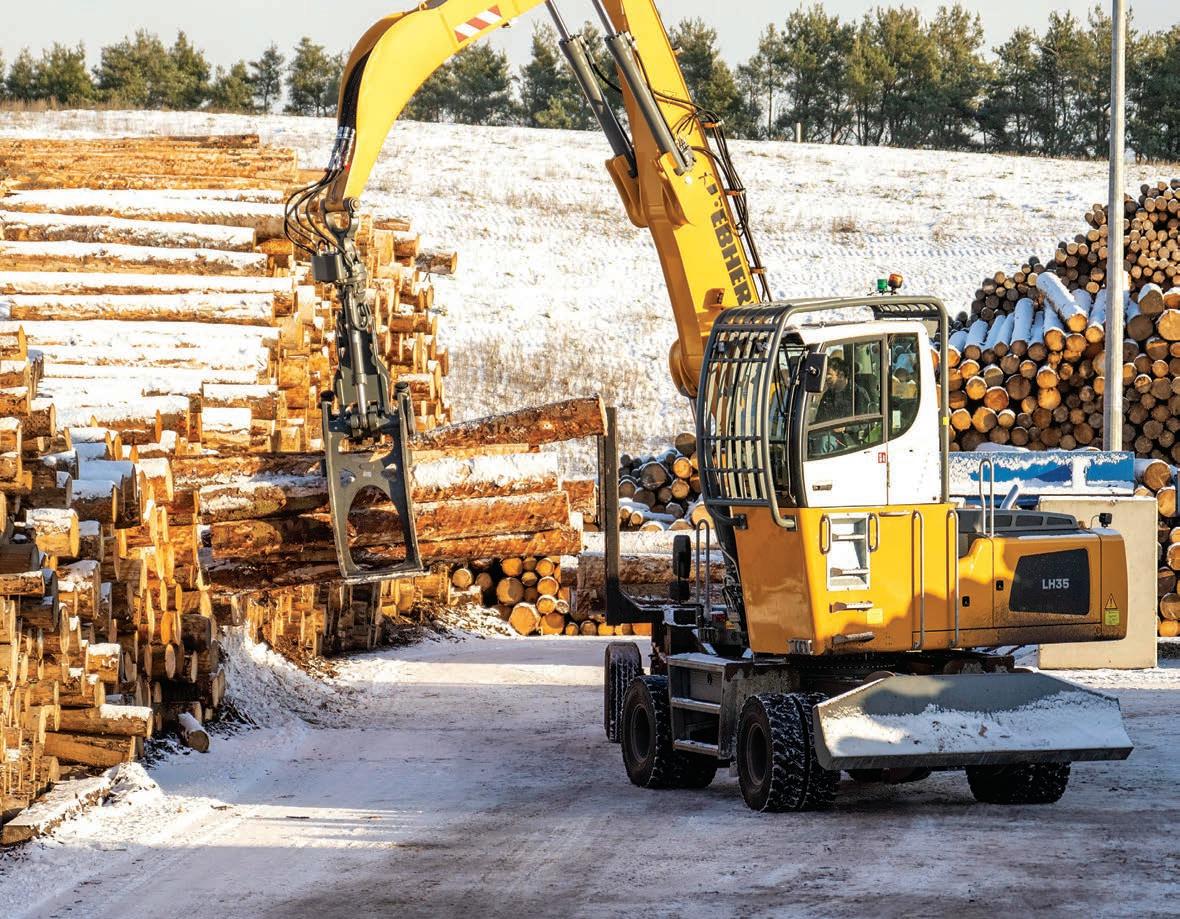

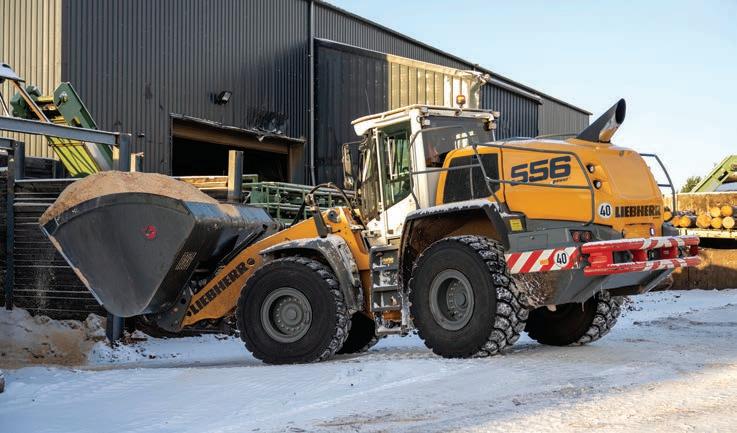