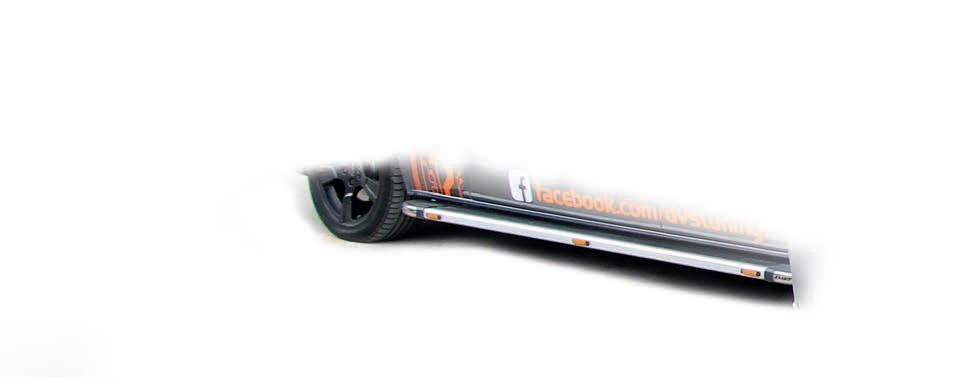
7 minute read
BIG GAINS
After seeing the performance bene ts his Ford Ranger pickup showed following an engine remap, Sam Mepham decided to explore what the technology could do to his forestry equipment. Sam runs operating across the south east of England and his eet of machines including a Valtra T234, a Jenz Hem 581 woodchipper, along with a trio of 360-degree excavators and a Komatsu 855 forwarder.
“The work we do requires a lot of horsepower,” said Sam. “The remap to the Ranger increased power by around 30hp, but in turn improved fuel economy by around 5mpg when I was towing, which is the bulk of its work. This is mainly down to the pickup revving lower to achieve the same output as before, so the engine isn’t working as hard and using less fuel in the process.”
Advertisement
The business has been running 10 years with hard work key to an increasing customer base and a busy work schedule, but reliability and operational ef ciencies were key factors to maintain when installing the remapping software.
The remaps have all been installed by Avon Tuning authorised agent Nathan Peto of DVS Tuning in Kent, and the rst machine was the Valtra T234, which covers

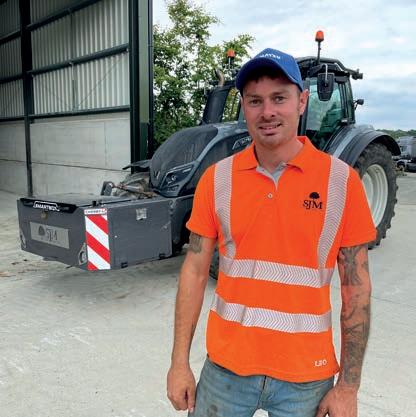
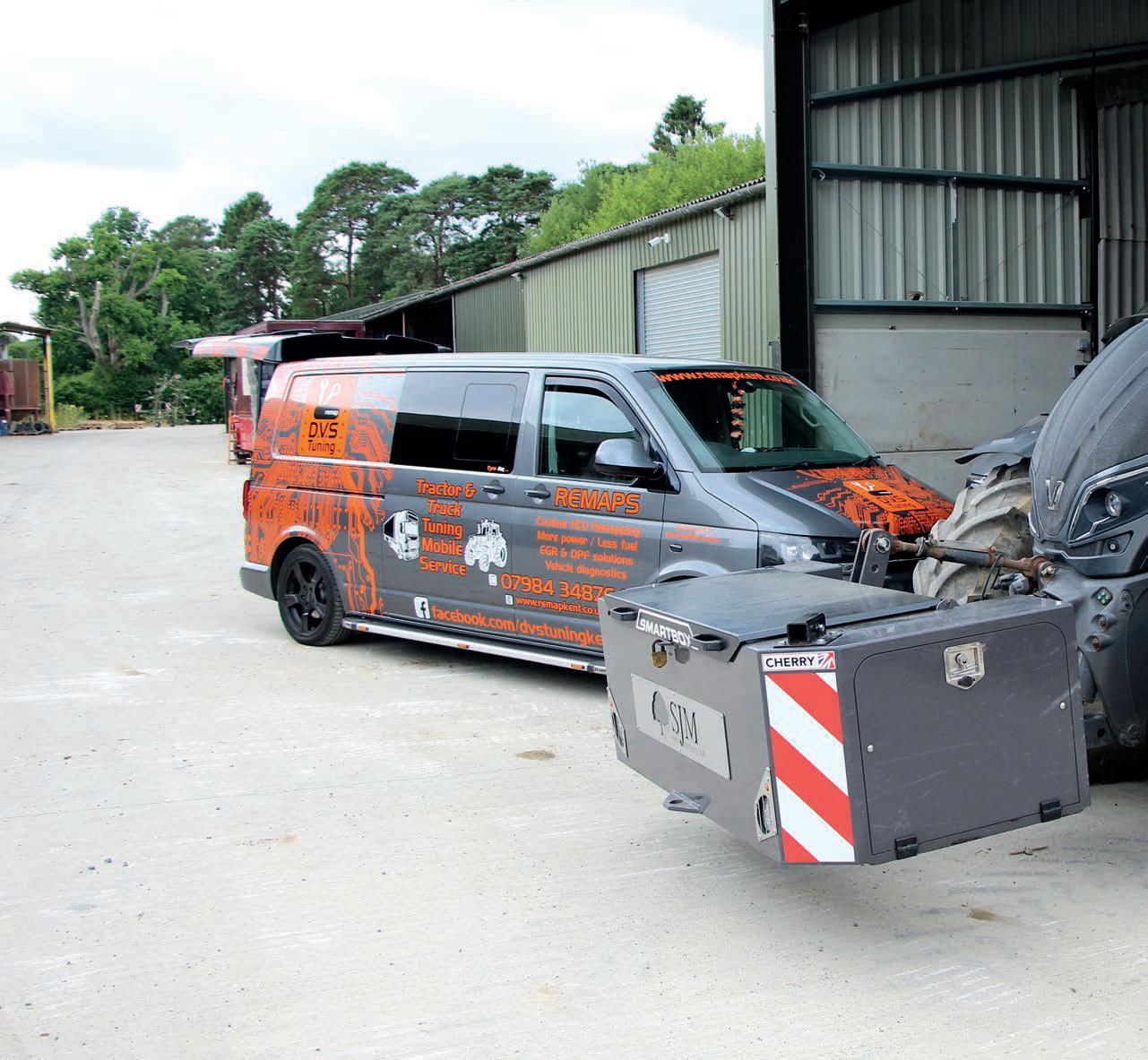
THE VALTRA SPENDS A LOT OF TIME ON THE ROAD TOWING A JENZ HEM 581 WOODCHIPPER”
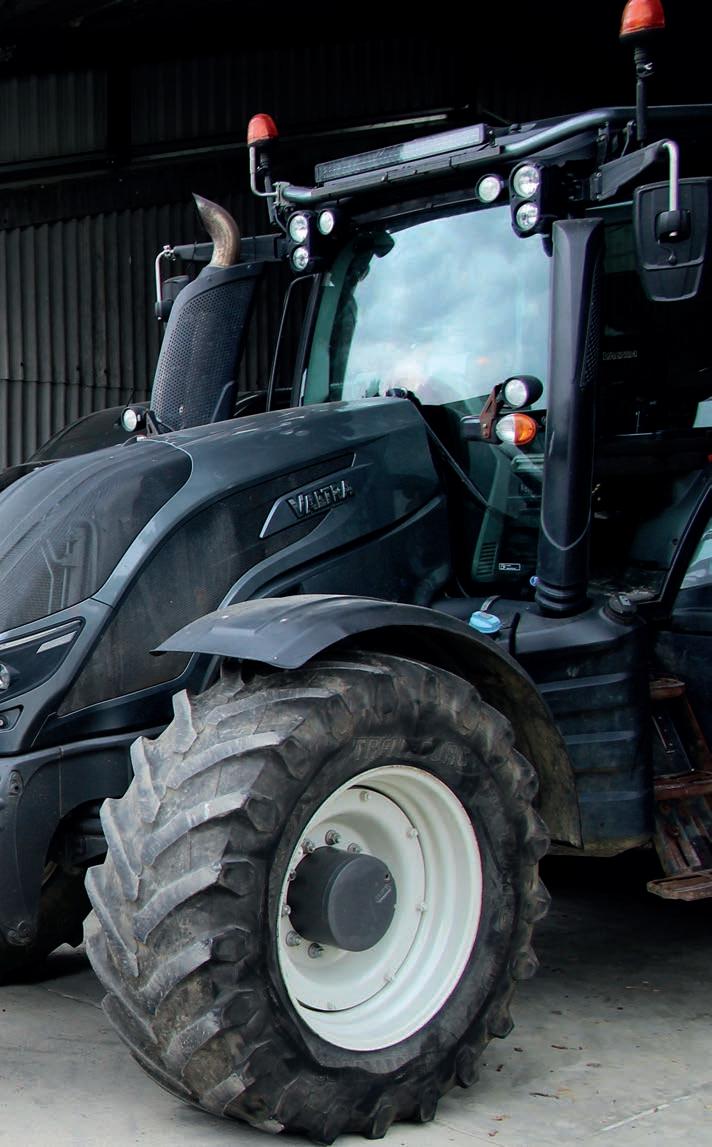
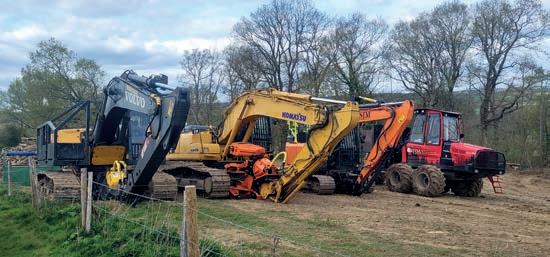


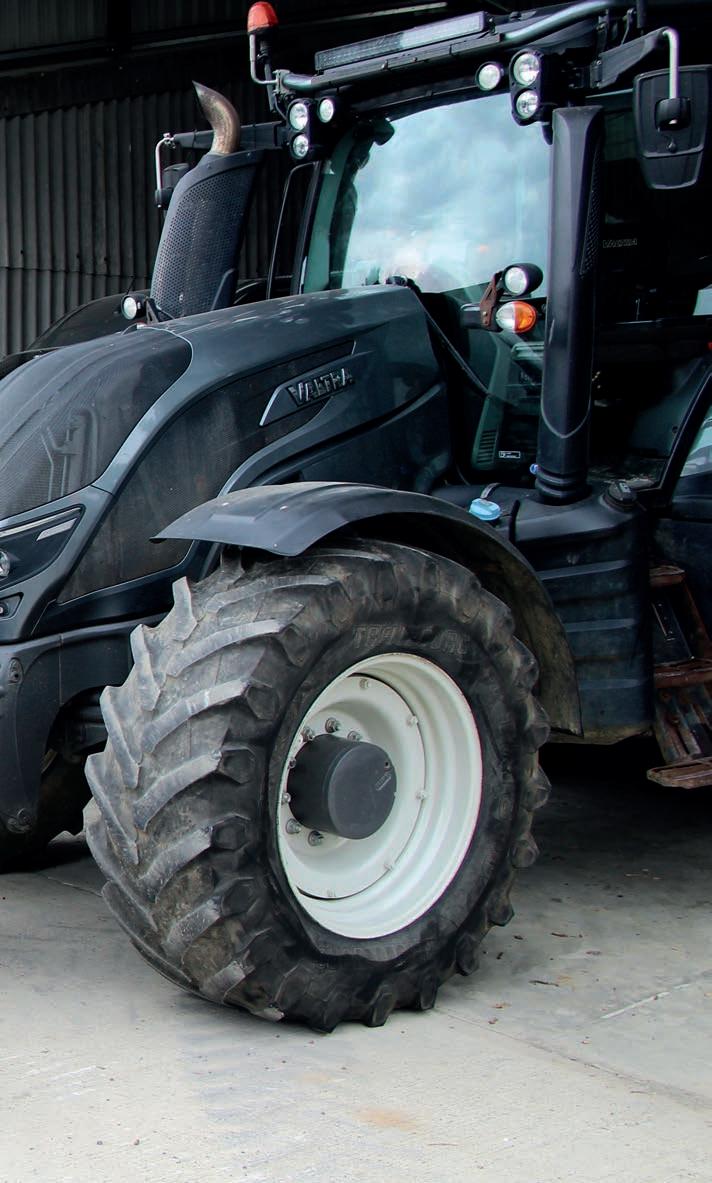
1,100 hours per year. The Valtra spends a lot of time on the road towing a Jenz Hem 581 mobile woodchipper. The chipper has its own 600hp Mercedes engine to process the timber, but the Valtra handles moving the rig between jobs, which tips the scales at a train weight of 32 tonnes. Sam explained that the Valtra was at its limit when it encountered a hill, so a remap was installed around 18 months ago.
The specialised alteration changes the ECU to adjust the fuel delivery and timing characteristics. This alters the points where peak power is delivered and allows more torque and power to be available within the engine’s capabilities. Sam explained how these changes work in day-to-day operation. “The key difference since the remap is the Valtra can pull the chipper up hills in a higher range at lower rpm, as there is more torque available lower down the rev range. This increases ef ciency and allows me to get to the next job quicker but use less fuel in the process. Previously, I had to be in a lower range and a higher gear, which meant I was revving the engine harder and burning more fuel to achieve the same power output I’m now getting at lower rpm.”
It may not seem like a big change, but Sam said the alterations to his eet have seen some signi cant fuel savings and allowed him to keep his current machinery, rather than investing in new kit to achieve greater output. “We use a lot of fuel across the eet, so any small savings add up to a substantial total over the lifetime of a machine. For me, it was more about tailoring the power of our current machines to suit our workload. The Valtra required more power on the road, and with the price of new machinery going up, the most cost-effective solution was a remap that edited the software at the source and saved a backup of the original should I need to put it back to standard in the future.”
Increased Performance
The 600hp Jenz chipper also had a remap installed and used to drink 600 litres of fuel on a full day’s work, however this has almost been 40% less due to the remap. Nathan Peto explained how it works. “The biggest change for these engines is the utilisation of torque, which means the engine isn’t working as hard as it was before to produce the same output. As standard, the engine was revving but wasn’t producing the torque in line with how much fuel was being used.

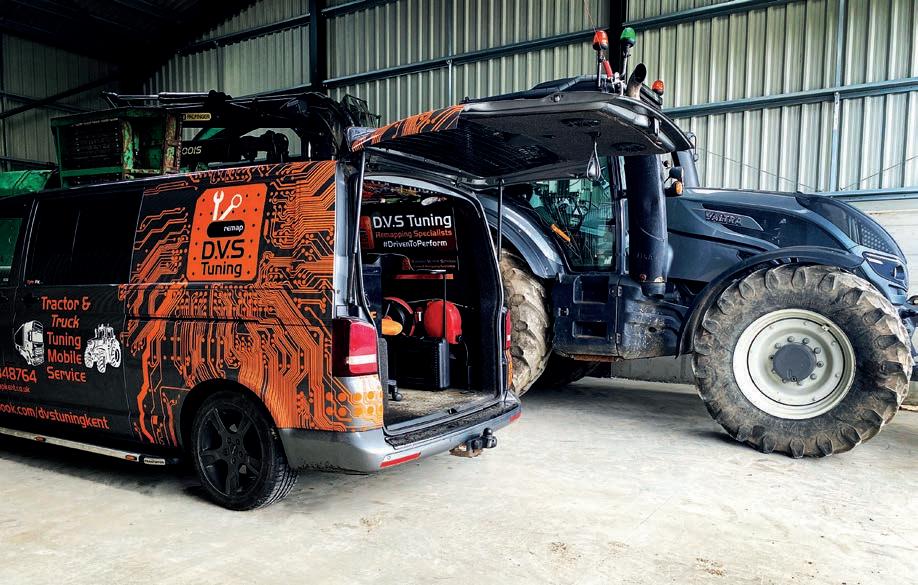
“This meant that a lot of fuel would have been wasted as it was revving beyond where the torque conversion is most ef cient,” Nathan continued. “The Avon Tuning remap edits key engine characteristics, such as throttle pedal calibration and torque and smoke limiters that are based on the engine’s limits, to achieve peak torque lower down the rev range.”
It is common for users having an engine remap carried out to increase power and torque that a by-product of this is a reduction in fuel consumption as the engine isn’t working as hard to reach the same output. One of the biggest fuel savings has been seen on the 2016 Komatsu forwarder, which Sam said is in use nearly every day of the year hauling timber out of woodlands in very unforgiving environments, clocking around 1,800 hours per year.
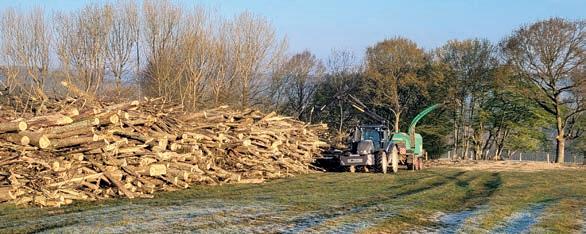
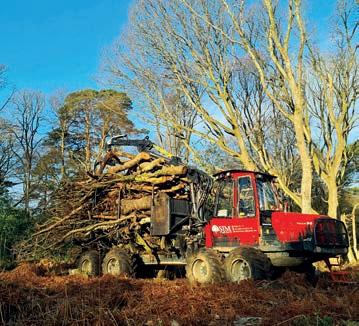
“It used to drink around 200 litres a day, which I wasn’t surprised at given the work it does. However, since the remap, we have seen quite an astonishing fuel saving and it is now only consuming 140 litres per day, no matter how hard we push it. A few weeks ago, between all the machines we used 14,000 litres in 10 days, so by remapping the eet we are seeing savings across the board and some of them are signi cant.”
One thing that was none negotiable with the engine remapping was reliability as keeping clients happy and arriving on time is a key requirement, especially working with road closures. The Avon Tuning remaps are tailored to the customer’s requirements, but within the characteristics and limits of the engine. The maps are created in the UK, and all the parameters of the vehicle being remapped, such as turbocharger size and cooling packs, are checked to ensure the machine can handle the increases.
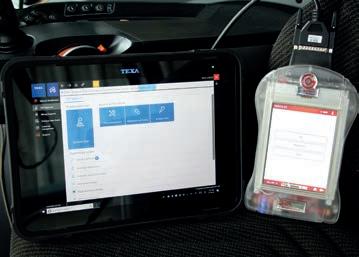
“We haven’t had any negative side effects from the remaps on any of the machines,” Sam con rmed. “The extra power has been really useful, and the fuel economy bene ts are saving us a lot of money across each machine. The machinery we run suits the work we do and is the right size to tread lightly across delicate woodland oors.
“If I had to increase the size of this machine to up work rates, I would not only be spending thousands of pounds to do so, but the customers I have may not appreciate the heavier kit I’m putting across their land. This is where the remap, which matches the power to the application, has been an ideal option for us,” Sam said.
THE TRACTOR REMAPPER!

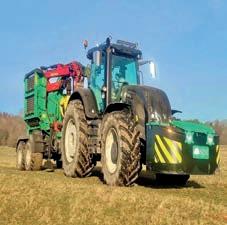
Up to 30% extra power and 10% extra economy with our tuning boxes and ECU re-mapping

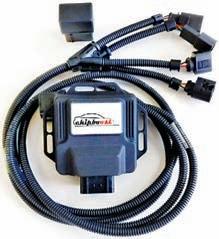
Tuning Boxes
> Will fit most Tier 2, Tier 3 and Tier 4 tractors
> Easy to fit by yourself in around 5 minutes
> Uses OEM style plugs (plug and play!)
Forestry Engineer
UNIT 3A, THE SIDINGS, TEBAY, PENRITH, CUMBRIA CA10 3XR
Mark Beach is based in Tebay, Cumbria and has over 30 years’ experience in many aspects of the Forestry Trade. We travel extensively throughout the UK Repairing, Maintaining and Servicing Forestry Machines, Timber Wagon Cranes, Forklifts and Chippers. We have a wealth of knowledge and experience in Sawmilling and Fabrication and are also a Certi ed LOLER Inspector.
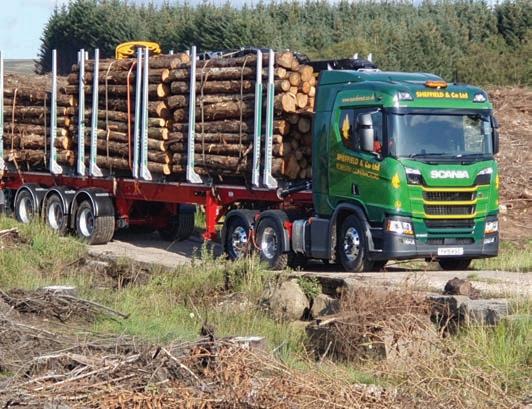

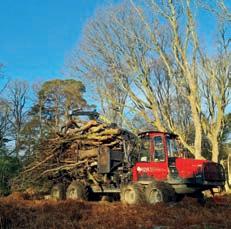
ECU Re-mapping
> Using the latest Dimsport equipment
> We can cover just about anything built in the last ten years.
> Everything can be set to your liking, horse power and torque increased and in some cases fuel usage decreased!
T: 01944 710522 / M: 07977 475955
E: sales@chipboost.com
Est 2004 www.chipboost.com
Crane Service & Repair Specialist
The UK’s main Kesla Truck Dealer
Proud agents for KESLA covering the UK and Ireland
Proud agents f
Tel: 07502 484198
Email: mbforestry@yahoo.co.uk
Website: markbeachforestry.co.uk
Leafy Surrey is home to Greenwood’s Tree Contractors, a company that takes immense pride in its work and vehicle presentation. We visited James Greenwood two years ago (Issue 5) following the purchase of a Volvo ECR145E excavator, which proven a great success particularly with its Vosch grapple saw upgrade.
“The Vosch has been a great addition to the eet.” James commented. “It has the advantage of being capable of being used as a grab, and with its 1m long chainsaw can tackle timber much greater in diameter than the previous attachment could. The Vosch will also leave a much cleaner cut for us meaning we can complete any trimming work to a high standard of nish.”
The company runs an immaculate Iveco Trakker 4x4 hook lift truck which multi-tasks as both chip carrier and tow tractor for the company’s low-loader, and recently acquired Morbark chipper. The package makes the company self-suf cient allowing them to transport machinery to and from site as well as transporting timber and chip back to the yard. The large yard also doubles up as a storage and processing area for materials with a dedicated bay for two grades of chipped material which James says is in demand of late. “We use Sylvagen, part of the huge AW Jenkinson Group to handle all our chipped material. We have seen prices of round timber uctuating over the last few years with the price of chip increasing signi cantly,” James explained. “This led us to look at increasing our chip capacity over the last couple of years to meet the demand and this has led us to invest heavily in two new bits of kit to allow us to do this and more importantly, do it effectively.”
Increasing Capacity
The rst part of the puzzle was the huge investment in a Morbark M20 chipper. Mounted on a wheeled chassis, the original dealer for the chipper left the industry just as the machine was delivered leaving James in the lurch. This improved when Blue Machinery took over the dealership. Capable of handling 584mm diameter logs, the 415hp

WOODCRACKER
|
Caterpillar-powered machine simply devours the timber fed into it. Whilst Morbark is reluctant to give actual production gures for the chipper as there are so many variables, during our time with James he quickly lled the bulk body on the Iveco with approximately 10 tonnes of material, which equates to a potential output of up to 160 tonnes per day meaning the chipper has given the company a huge production increase over their older Bandit model.
Feeding the chipper regular sized logs is one thing but James and his team regularly encounter larger material. “The market for biomass material constantly uctuates. Recent changes have meant that timber we would cut up is now a viable source of income following chipping,” James said.
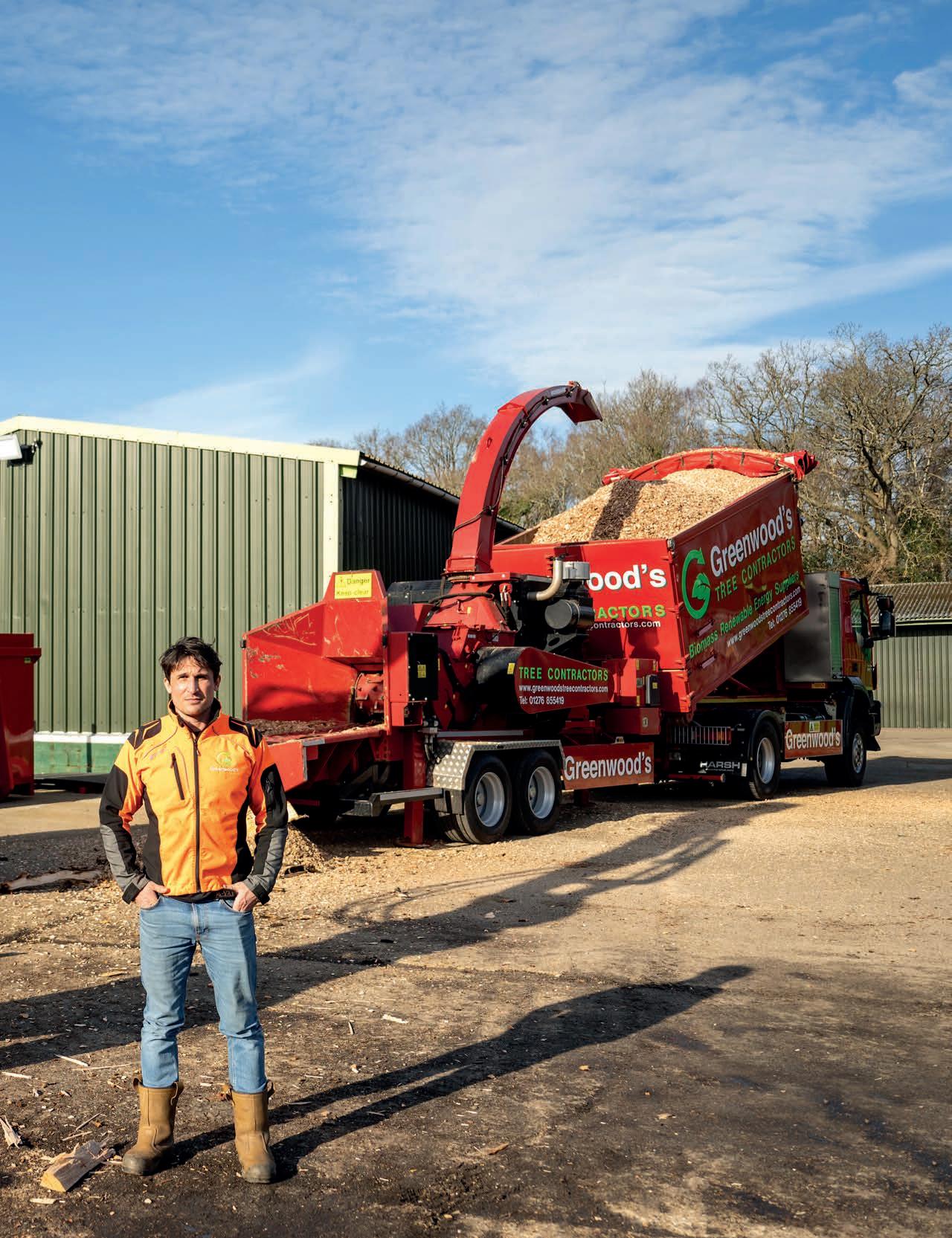