
9 minute read
MODIFIED EXCAVATOR
The HX’s raised clearance has opened up new specialist opportunities for Keightley.
FOR ALL SEASONS
Advertisement
Eoghan Daly reports on the early experiences of brothers Thomas and Michael Keightley, of Keightley Plant & Civil, with a high walker Hyundai conversion complete with Geith tilt hitch and improved hydraulics
IMAGES EOGHAN DALY
Having established its plant and civil engineering business with secondhand machines in the form of a Fiat Hitachi FH130.3 and more recently a Hyundai Robex 140LC-7, when the time came for Keightley Plant & Civil to add a second machine to its fleet just over a year ago, the County Laois-based company took the opportunity to specify an excavator suited to a much broader range of jobs.
“Forestry may not be our main type of work, but it has become an important part of what we do throughout the year. It’s hard on standard machines, which is why we decided on a high clearance excavator,” Thomas Keightley explained. “Used excavators have always seemed to provide the best value for money, but getting a high walker excavator used is very difficult, so having one converted was the only option.”
ON THE UP
Following positive experiences with a used, 2007 Hyundai Robex 140LC-7, which now has over 14,000 hours of reliable service under its belt, the company felt confident in taking on another Hyundai in the form of an HX140LC sourced from the UK through Irish Hyundai importer and dealer, Whelan Plant Sales Ltd. Upon its arrival in Ireland, the machine went straight into the workshop of County Offaly-based Mooney Engineering Ltd in Shannonbridge, where its undercarriage clearance was increased without ruining stability, and other features were added to future-proof the machine’s abilities.
To achieve greater clearance, the central portion of the undercarriage’s X-frame was detached from the track frames and a newly-fabricated mounting formation slotted in between, with all stress points reinforced.
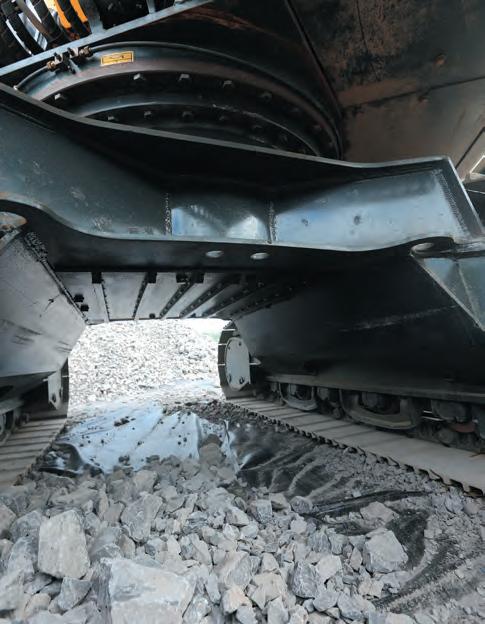

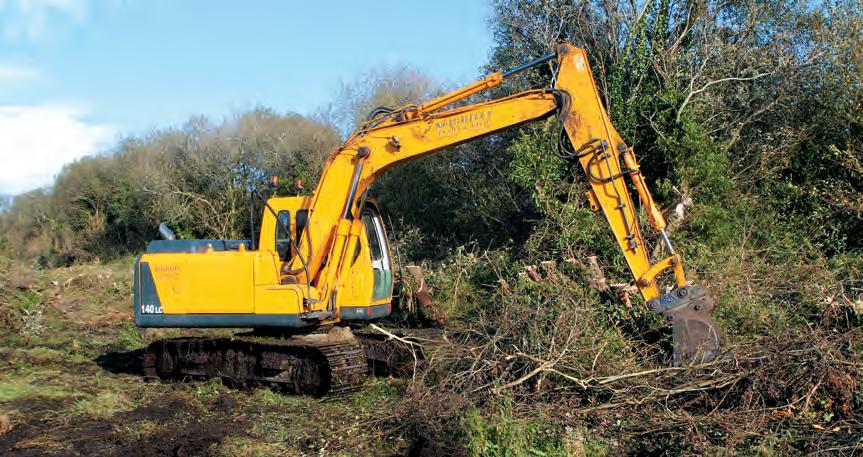
The end result is an increase in ground clearance from the standard 440mm to a maximum of 680mm. Three additional track guides were also fitted at the idler end of the track frame, and the top rollers were redesigned. Providing much enhanced “THE MACHINE carrying capability of the track chains, IS WELL the two top rollers BALANCED, positioned on each side have raised EVEN WITH mounting frames, THE HIGHER which results in a spacing of 300mm CLEARANCE between the top of AND TILT HITCH” the central track frame and the top of the roller on which the track chain runs.
Despite the greater height at which they carry the track, there is still generous clearance between the tracks and the upper structure. This means that any stray branches from the brash mat carried on the tracks in reforestation sites have sufficient space to pass through without being wedged between the track and upper structure. Clearance beneath the lower edge of the rear counterweight is also generous at 1,170mm – some 230mm greater than standard.
Underbody’s clearance, durability and protection are very impressive. Left: Reliable Hyundai Robex 140-7 machine.
Below: Geith tilt hitch provides extra versatility.
Above: Bespoke grading beam by Fairbrother.
Below: Fast and precise grading with Geith hitch.
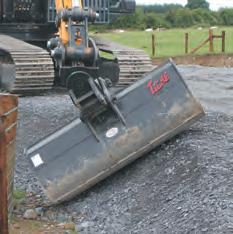
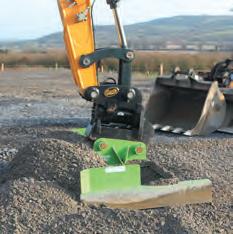
LIGHT ON ITS FEET
Turning its attention to the digger’s upper structure, Mooney Engineering fitted side impact protection along both flanks and constructed a ribbed steel guard for the lower front window area that doesn’t affect visibility too much. “When working on rough ground, the machine doesn’t get hung up on stumps or rocks, and as a result doesn’t break the surface,” Thomas explained. “Even on very bad ground, it travels very well compared to a standard excavator and has great tracking power.”

Running on 700mm triple grouser track shoes, the machine offers a good combination of low ground pressure and high tractive abilities, while the standard 2.7m width ensures decent stability. The machine is well balanced even with the higher clearance and tilt hitch, and Thomas added that heavier attachments don’t faze it either.
Having decided from the outset that the machine needed to have a tilt coupler, Keightley’s Hyundai became the first machine in Ireland to receive a new generation tilt hitch from Geith. Utilising a more comprehensive range of attachments and specialist works tools than most, the Geith tilt coupler has proved its worth many times over, as Thomas explained. “Geith stood out as the hitch of choice based on the already proven design and continuing improvements, such as running the hoses through the unit, which means there is nothing exposed to damage or wear on the outside of the unit.” The hitch was fitted by Whelan Plant Sales shortly before the newly converted machine’s delivery to its eager new owners.

ROOM WITH A VIEW
Above: Stones pushed to edge with beam.
“There isn’t any noticeable effect on digging depth with the raised clearance and anything that is lost is regained with the tilt hitch,” Thomas explained. “For many kinds of work, such as clearing drains or opening trenches, the higher clearance has an advantage in the form of greater visibility, as the cab sits higher over the work.”
Digging performance also remains strong and is not affected by the fitment of the tilt hitch, with breakout forces remaining consistently good, as demonstrated on a range of one-off housing developments where Keightley Plant conducted all site clearance, earthworks and subsequent groundworks.
Further boosting the Hyundai’s versatility is a grading beam attachment fabricated by Philip Fairbrother of local company Fairbrother Engineering. Offering just the correct working width of 2.1m, the grading beam provides decent ground coverage without being overly cumbersome, and doubles as a makeshift bucket.
“Until I had used the grading beam, it was hard to imagine the difference it makes in getting a final finish,” Thomas admitted. “It has been used on site access roads, yards and farm roads, and the tilt hitch makes it easy to
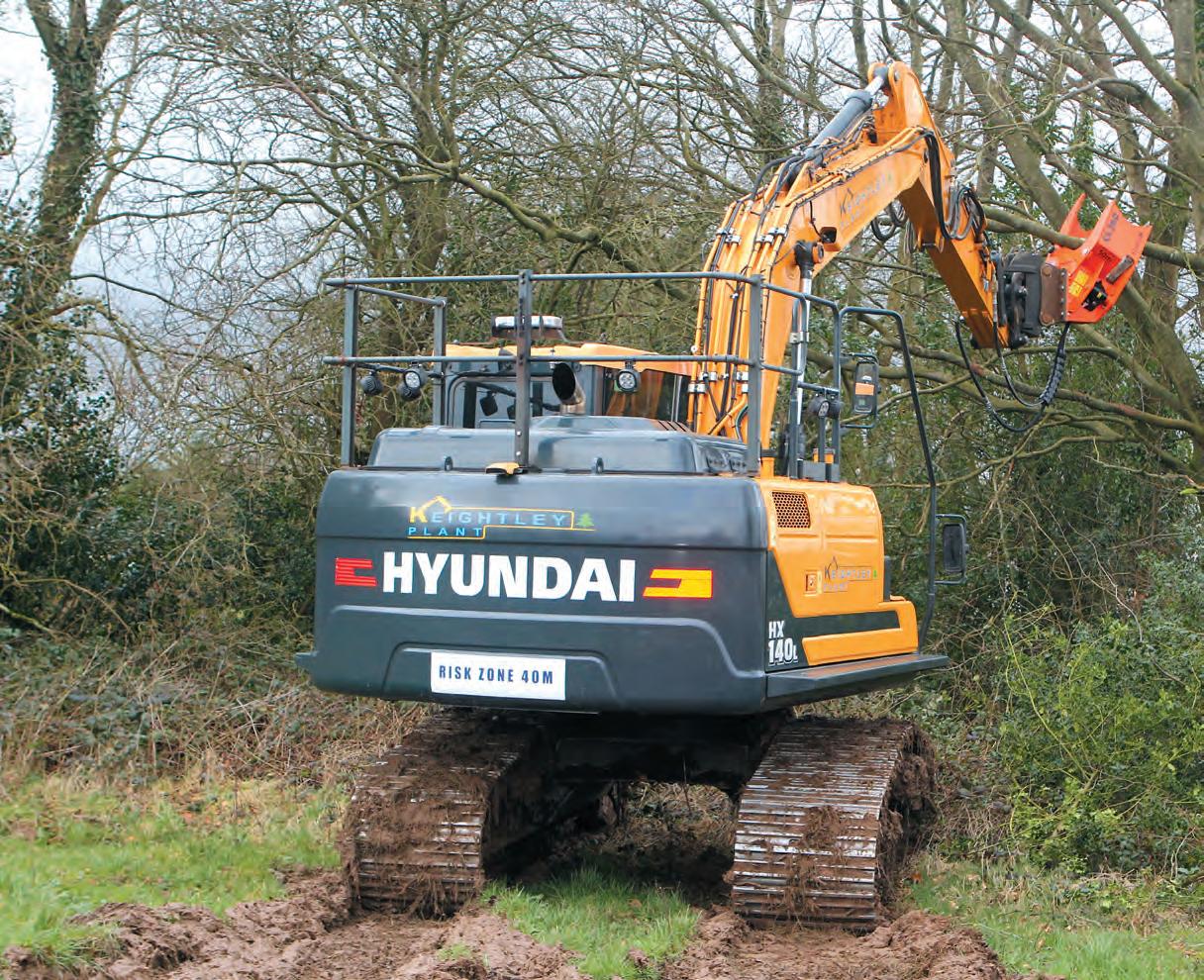

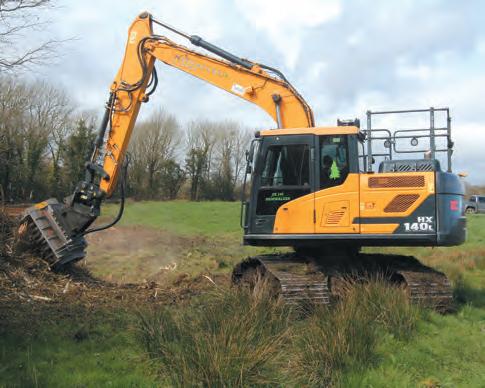
Above: FAE UML 100 mulcher a recent addition.
Right: Circular saw benefits from Geith kit.
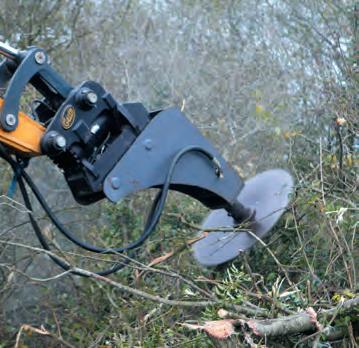
Left and below: Westtech Woodcracker CL260 shear used for crown reduction. Above: Thomas Keightley at the controls of the HX140L with his dog Larry.
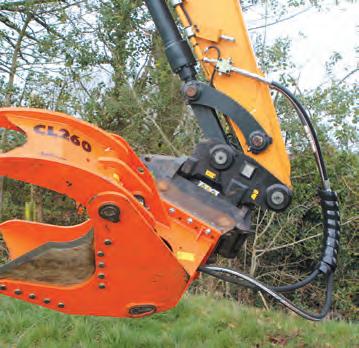
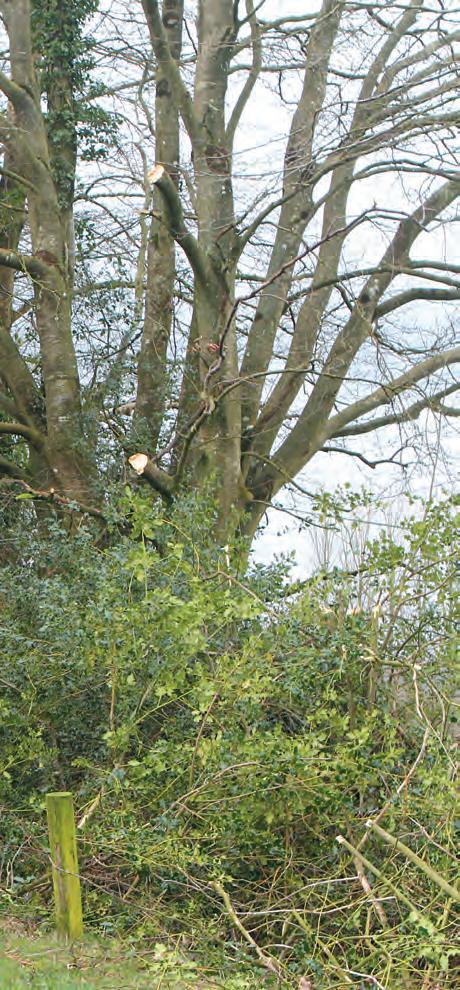
maintain the correct slope angle for drainage.”
As the winter of 2020 drew closer, many other areas were being explored to further the machine’s working potential. While the hydraulic brash grab lay in readiness for windrowing of harvesting residues on reforestation sites, Keightley added a circular saw head to its toolset for use on a number of land reclamation jobs involving cutting overgrown trees, hedgerows and invasive scrub as part of a process to return the lands to full production.
“Positioning the saw head to cut overhanging tree branches was no problem with the tilt hitch, and it also allowed me to angle the blade to cut the side of overgrown hedgerows which would not be possible with a standard hitch,” Thomas said.
Continuing the theme of hedgerow and tree maintenance, mulching heads were accepted for brief periods of demonstration on the in-house HX140L. From these efforts, the most desirable unit was identified as a FAE UML100, which was to be delivered later in the season. However, in the interim period, there was plenty to keep the HX140L occupied. Clearance of dangerous trees overhanging public roads from farmland was undertaken through the use of a Westtech CL260 tree shear.
The Geith tilt hitch also made a real difference to placement on the branches and crowns being shorn, with the CL260 affording positive cutting and gripping characteristics for controlled and precise cutting. Working with traffic management, a considerable volume of trees were removed, with even the largest mature Beech trees greatly reduced, easing the process for felling of the main trunks by tree surgeons brought in to complete the process.
TIME TO MULCH
Even though the HX140L HW demonstrated good stability at maximum reach while utilising the tree shear attachment, the ultimate test of its abilities came with the delivery of the new FAE UML100 mulching head. Arriving just before the onset of the hedgerow maintenance deadline with commencement of the bird nesting season, the mulcher proved its worth in scrub and ground mulching operations.
However, this is just part of the unit’s broader working brief as it has been specified to handle a wide range of
mulching operations, as Thomas outlined. “To make sure the new mulcher could handle a full range of work, it was delivered with two sets of cutting teeth, which can be changed to best suit the type of work we are doing. It has standard tungsten carbide teeth suited to mulching scrub and ground mulching, and also came with carbide chipper teeth for working on larger diameter standing trees and forestry mulching work.”
ALL ABOUT THE FLOW
With 14-tonne excavators often considered lacking in oil flow performance to deliver maximum mulching performance, Thomas acted to ensure his HX140L HW was up to the task. In standard form, the HX140L on which this high walker conversion is based delivers an oil flow capability of 126.8L/min from each of its twin hydraulic pumps.
While this is obviously adequate for standard operations and less demanding attachments, when tasked with delivering the maximum from the mulcher it was considered best to take hydraulic performance up a level. “We had the hydraulics modified through an upgrade to
This picture and right inset: Mulcher’s effectiveness boosted by hydraulic improvements. Above: HX140L still great on regular sites.

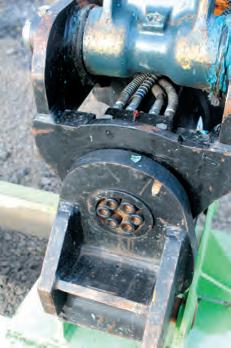
Left: Sensible hose routing through unit.
get the maximum from the mulcher especially in heavier material. It now runs at 350bar pressure, which is a step up from the standard 280bar,” Thomas explained.
Despite the greater hydraulic output, there has not been a dramatic increase in fuel consumption from the machine’s Cummins QST3.8 four-cylinder diesel engine, which offers a power output of 95kW. While the undercarriage modifications have greatly assisted in the machine’s do-it-all capabilities, praise must be given to the base Hyundai.
“The HX140L is a great excavator with plenty of power and comfort,” Thomas confirmed. “Hyundai has really brought its machines forward over the years, as shown by the amount of changes it has made since our 14,000-hour Robex 140LC-7 was built. They are definitely a machine for the long haul.”
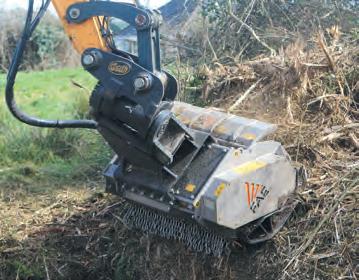
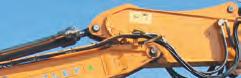
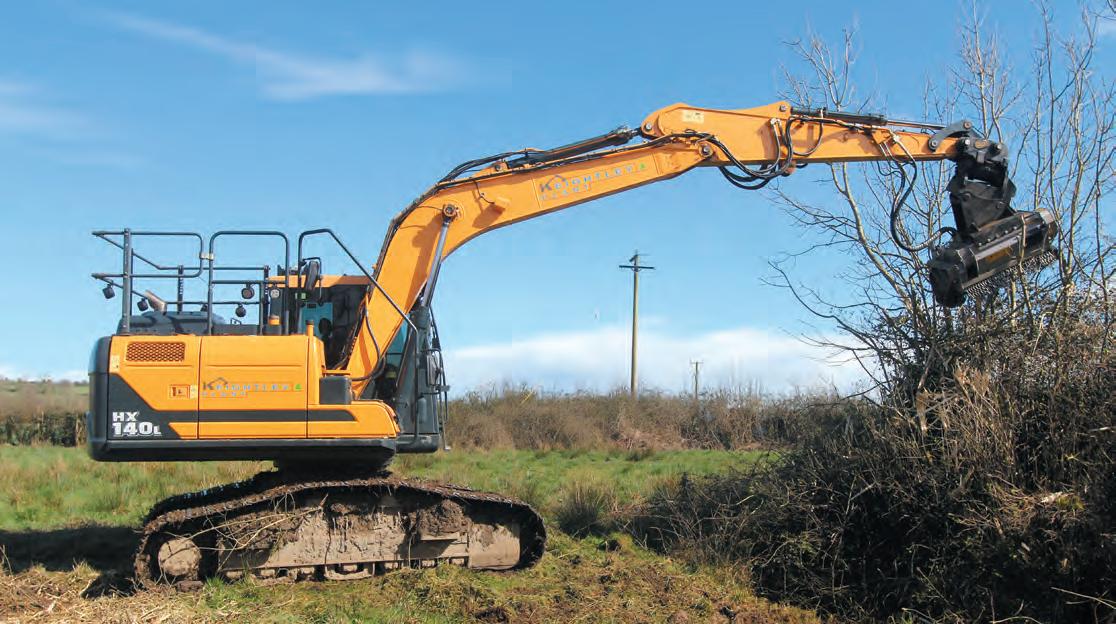