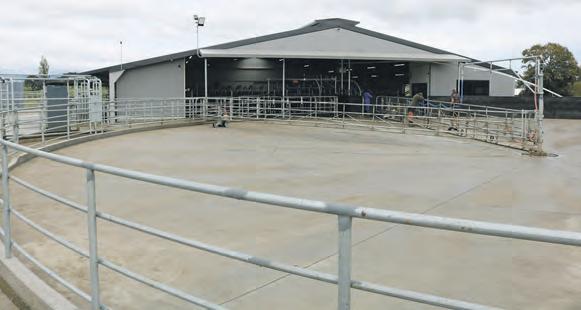
13 minute read
Ashleigh Lodge Waikato
by Sun Media
The Race Works Wrangler aids hoof care.
An underpass to the pit is a feature of the Martin shed. A view across the expansive yard.
Three 16 tonne silos, supplied by Buster Cover, supply the in-shed feeding system. The crew behind the concept and construction from left: McGregors Farm Services water services manager Brendan Wahrlich, Don Chapman Waikato managing director Shanan White, equity partners Peter and Karen Martin, grandchildren Carly, Olly and Adelene, equity partners Melanie and Shane Martin, McGregors Farm Services business development manager Shaun Killalea and owner/managing director Daniel Peake.
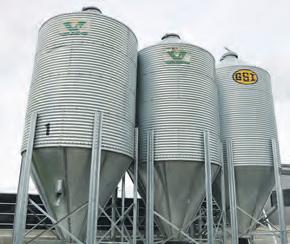
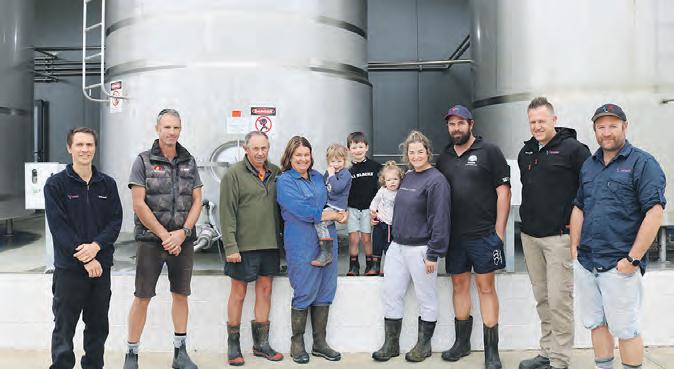
DeLaval farm monitoring cameras have also been installed to view the yard and vat areas from the cups-on milking area.
McGregors Farm Services operations manager Brendan Wahrlich says the shed has DeLaval’s latest plant cleaning system with the addition of a custom control to operate the three vats and second wash system.
He says these are fully automatic, using a series of valves and sensors to control the wash cycles and switching between vats.
McGregors also installed a 6000L Lobe vacuum pump with VSD (Variable Speed Drive) control in the plant room to ensure reliable vacuum at optimum levels to the plant.
The pump room houses the latest in water technology with VSD controlled pumps, water monitoring and digital dosing to supply the shed and farms water demands, says Brendan.
Peter Martin says the former cowsheds on the property, both 30-aside herringbones, were simply past their use-by date.
“Building a single, modern shed in the middle was the obvious choice.”
Peter says the new shed’s effluent disposal system features three sand traps and a main sump for pumping out of, plus a lined effluent pond which feeds back into the bottom of the sump and can be pumped back on the paddocks.
The sand traps and sump were designed and installed by Paeroa Precast.
Peter says two travelling irrigators are used to spread liquid effluent onto the property.
Nutritional needs
The Martin herd’s nutritional needs are met in the milking shed through equipment and technology provided by Matamata-based BCL Feed Systems.
Foreman Bill King says the project included three 16-tonne silos, which are filled with custom feed grain.
This material is conveyed to the milking shed, via an 80mm spring auger system, and delivered into a 250kg hopper fitted above the milking platform.
Bill says the grain is then discharged into feed trays in the bails by a second discharge system, which gives accurate and consistent amounts to each cow.
“When the cows walk into the bails a sensor is activated that automatically fills the feed trays,” he says.
BCL Feed Systems also fitted out the Kereone Rd farm’s former herringbone shed about six years ago.
“So when Peter made contact to fit out his new build, we felt privileged to be asked to once again supply the feed system,” says Bill.
The Martins opted for the Race Works Wrangler gate from Whakatane-based The Wrangler.
The Wrangler’s Wilco and Waverley say the Race Works’ model is ideal for holding stock for hoof-trimming.
While stock are secure in the ‘lame cow handler’, Wilco says the design also has staff safety in mind.
He says the Race Works Wrangler features front foot support along with a rear leg winch and rubber matting.
Family farm
The origins of the Martin family’s Kereone Rd block go back to pioneer owners Stan Goosman (a former Piako MP and Government Minister) and Butland Industries (makers of Chesdale cheese).
Peter’s father acquired part of the property which Peter worked on until the age of 22, moving to nearby Matuku Rd for 19 years before returning to the home farm.
Succession planning with Shane and Melanie began six years ago.

Triangle & Chain ATV Harrows
HILL
Cowshed Construction General Engineering Hydraulic Hose Repair Cowshed Repairs Machinery Repairs Steel Sales
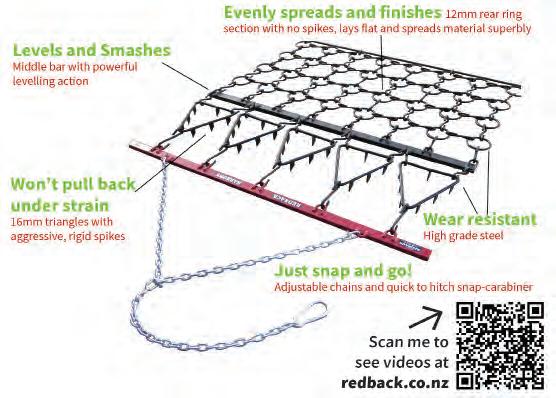
WORKSHOP & ON-SITE SERVICE
18 Francis St, Paeroa 0211 734 545

REDBACK Harrows: Ideal for manure spreading, harrowing -aerating, break feeding, cultivation finishing, levelling sand arenas and much more. ATV Harrows from $1,060 +GST 0800 55 11 55
Scan me to see videos!
www.redback.co.nz

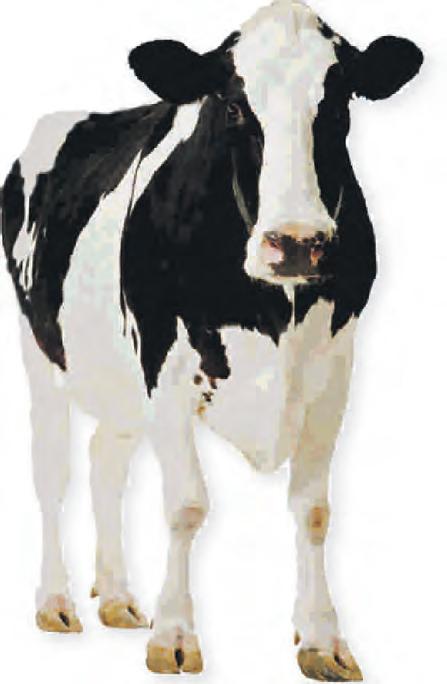

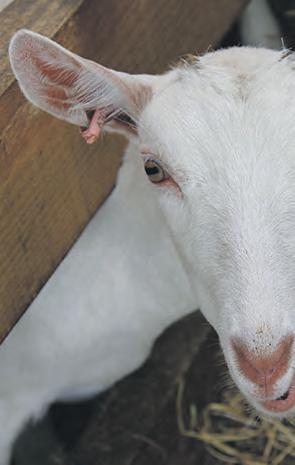
One of the kids. Trent and Gwen have been involved, with family, in the build of four dairies but say this is the last. The farm team, from left, Gwen and Trent Bonnar, Ben with Diesel the dog, Nathan, farm assistant Jenny Johnson and farm manager Janette Andrews.
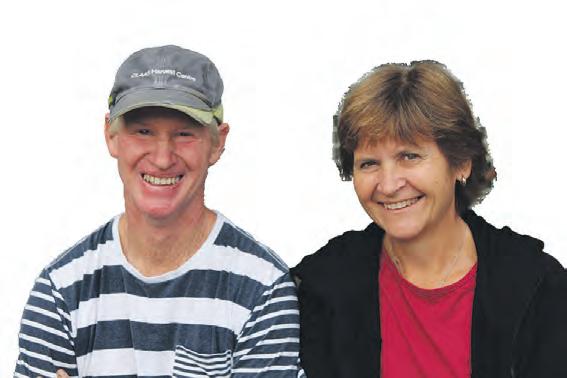
Clare Bayly
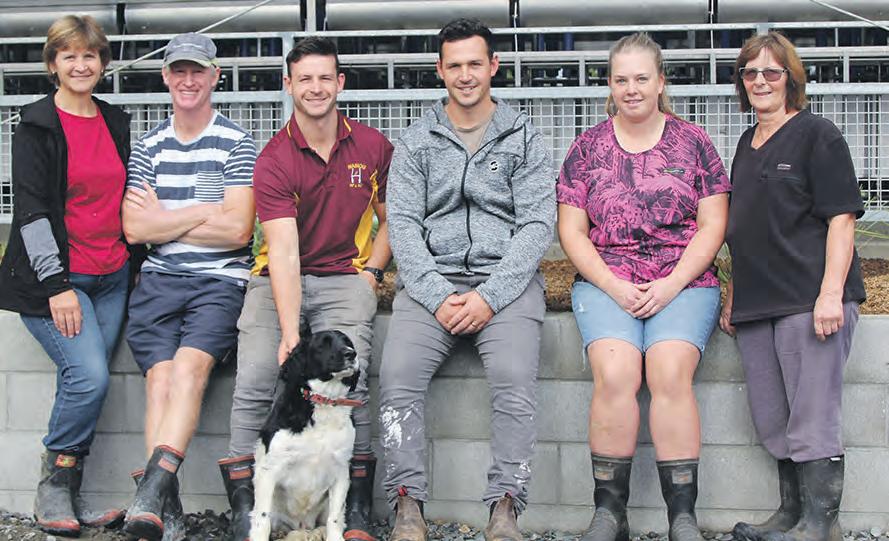
The day before New Zealand went into its first Covid lockdown, as others stockpiled things like flour and toilet paper, Trent Bonnar went into town and bought a two tonne PTO cement mixer and a trailer load of builder’s mix.
He had no choice. He and his family were days away from pouring the slab for their new goat dairy. Lockdown meant the concrete would not be arriving pre-mixed in trucks and would, instead, need to be manually mixed and poured.
The dairy had to proceed, lockdown or not. Kidding started in June and they were going to be ready.
Gwen Bonnar recalls her careful project planning “went out the window” with the announcement that the country was locking-down.
“There was no clarity in those early days about what we could and couldn’t do, so we had to rely on the skills which existed in our ‘bubble’.”
Trent is a mechanic by trade, and there’s also an extensive skill set amongst Trent and Gwen’s sons: “Ben is a jack-of-all-trades, Nathan is an electrician and Josh is a builder and bricklayer.
“One of our biggest worries in those early days of the Covid lockdown was the surge in demand for products and services which would ensue once the lockdown was eased,” says Gwen.
“We weren’t alone – everyone around the country, immersed in any level of construction, was in the same boat with their projects stalled. We were naturally concerned that, once the doors opened again, there would be a gridlock of demand which could compromise our ability to get what we wanted when we wanted it – and we had to have the new dairy completed for kidding in July.” Integrated system
Gwen and Trent farm in the Waikato, midway between Hamilton and Morrinsville. Originally they milked cows on the 290ha property, but converted part of the farm to dairy goats in 2013.
“We wanted to diversify, so in 2013 we looked at goats and developed our first goat dairy,” Trent recalls. “Five years later, in 2018, Nathan, Ben and their families wanted to move back to the farm, so we looked at creating a second unit.
“We reduced cow numbers and converted part of the farm into a dairy goat unit for Ben, the intention being that once that unit was up and running we would repeat the process for Nathan.
“The first conversion saw us transform an existing cow dairy to a goat herringbone. The second conversion was always going to be a new build.”
The new herringbone was always going to feature a rapid exit system. Some years earlier Trent’s brother imported a rapid exit goat dairy from Greece; Trent and Gwen liked its simplicity, ease of use, quality and durability and cost.
“The Greek rapid exit system incorporates meal feeding so you avoid the cost of buying and installing two separate systems – it’s all integrated, constructed out of high-quality stainless steel making it very cost effective.
“We started talking to the Greek manufacturers and it all just came together – the 36-aside double-up rapid exit system taking up around half of a 15 foot shipping container.”
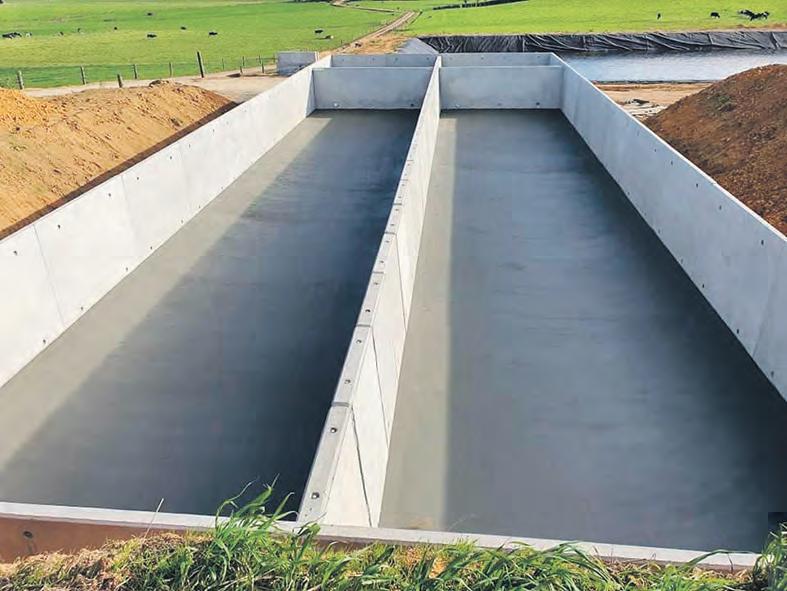
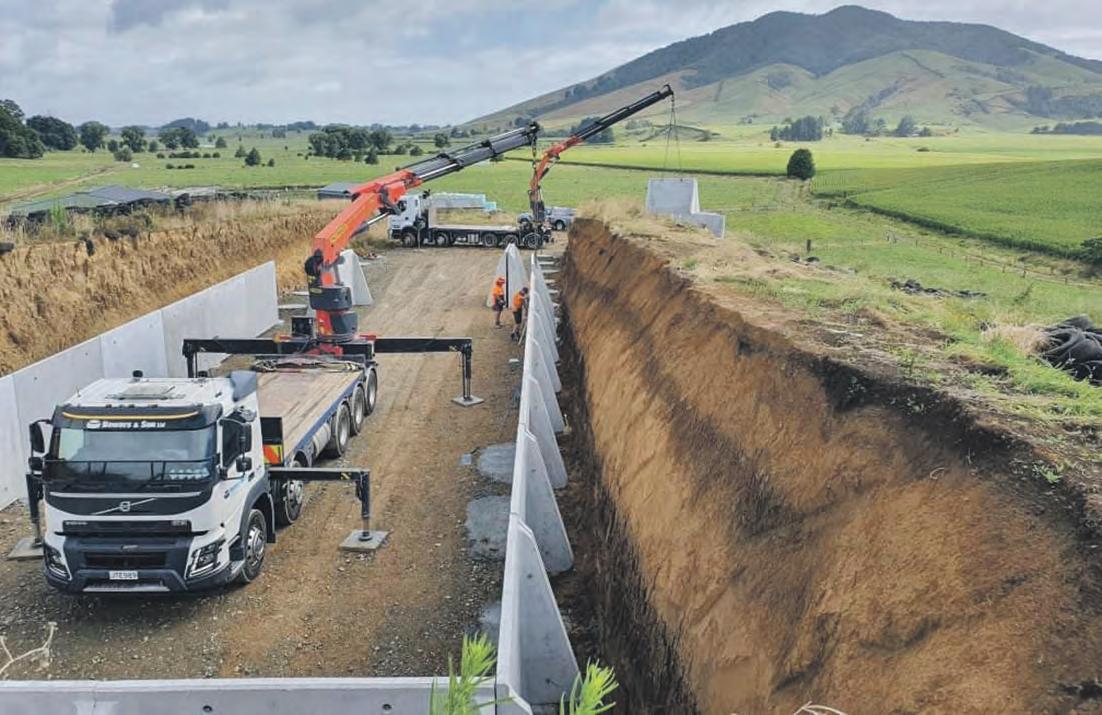
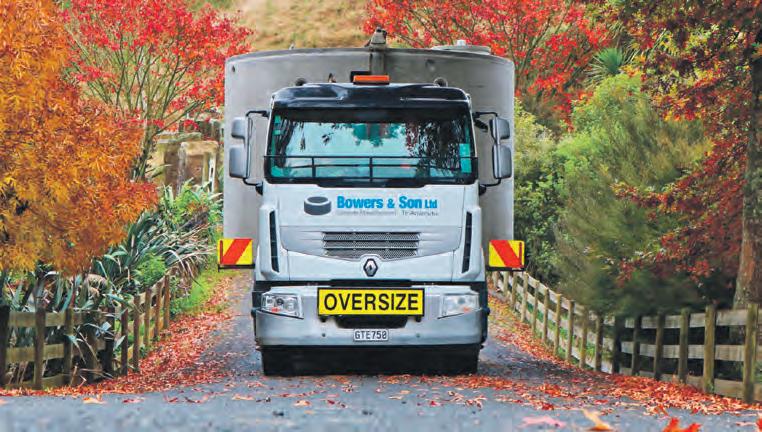
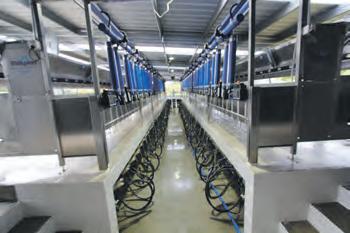

The view from the milk room looking down the pit. The new dairy looking from the collection yards to the rapid exit and milkroom.

The milking herd tucking into silage in the purpose-built barn.
The receiving cans are positioned under the deck.

The container arrived at the farm on March 24, the day before lockdown – as Trent dashed into town to buy the concrete mixer.
“Construction of the new dairy started in February 2020. Our builder’s son, Josh, came up from Wellington ready to do the foundations and building work but within weeks had a farm-bike accident which saw him relegated to being an advisor with some of his builder mates stepping into the breach,” says Gwen.
Hand mixed
Once the dairy roof was erected, Trent, Nathan and Ben poured the concrete for the yard and milk room, recalling they hand-mixed ‘the equivalent of a few truck loads’.
The Bonnars visited a number of goat dairies before the build to ‘see what we liked and didn’t like’, says Gwen.
“The pit in a goat dairy can be quite deep to ensure the milking platform is at the right height for milkers, and steps are usually a feature. We didn’t want that. We wanted easy access in and out of the pit – to the yards and the milk room.”
As a consequence, the yard end of the pit has a small set of steps, the floor of the pit then sloping up to one step into the milk room. The result is light and airy with exceptionally easy access.
“Within weeks of lockdown we finally gained clarity about site restrictions,” says Gwen. “Essentially it meant that, at any one time, there could have been several bubbles on site – each needing to stay separate from others. But once we knew the rules, we were able to apply the necessary disciplines and get on with the build.
“Ensuring supplies of vital components was another matter but thankfully Daniel Peake of McGregors Farm Services oversaw most of this, ensuring we had the equipment we needed when we needed it.”
Building a Lego shed
Daniel laughingly recalls that, when first called in by Trent and Gwen to discuss the new build, he asked if there was a plan for the new dairy.
“I expected a drawing of some sort but Trent presented me with a scale model of the new dairy he had built out of Lego blocks. It was fantastic and very detailed; we had to make it work from that.”
Lego was to become an enduring theme of the new dairy.
Trent, Nathan and Ben assembled the rapid exit system.
“It was like a giant Lego with two pages of instructions in relatively good English,” says Trent.
“The first side took a week to put together and the second took a day. There were a lot of pieces and we had to work out what bolts went where.
“We had a few spares left over, which concerned us a bit, but they were really just that, spares – every bolthole had its corresponding bolt! In the end it all fitted really well.”
“We opted for a DeLaval milking system because we wanted to start with a basic system that could be completed with all the bells and whistles, like EID readers, when the budget allowed.”
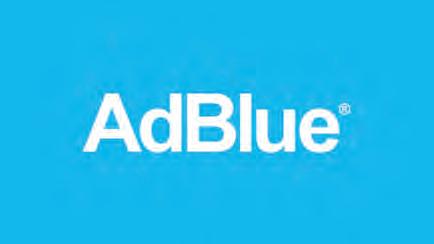
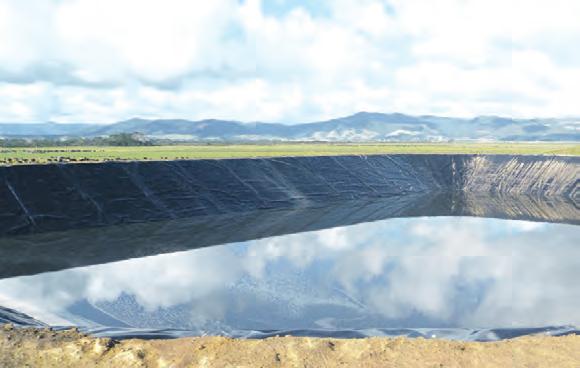
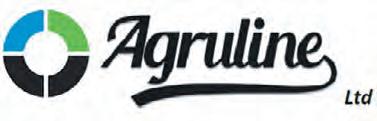
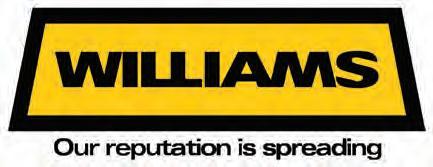
• Farm Effluent Equipment • Full System Design • Installation • Service
0800 4 EFFLUENT www.williamsirrigation.com
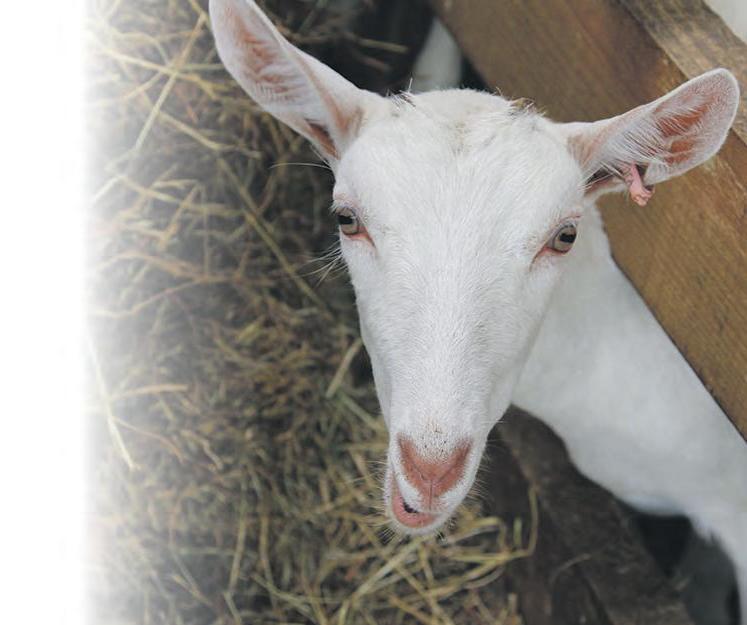

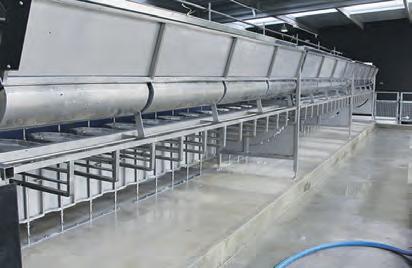
Looking from the dairy to the purpose-built barn which houses the milking goats. The goats exit from the rapid exit system and return to the barn via covered walkways.
The Greek rapid exit system is constructed of stainless steel and incorporates feed bins. The photo, left, shows the system in the raised position. Ease of access to the milk room – with only two steps – is a design feature that complements milking in the new dairy.

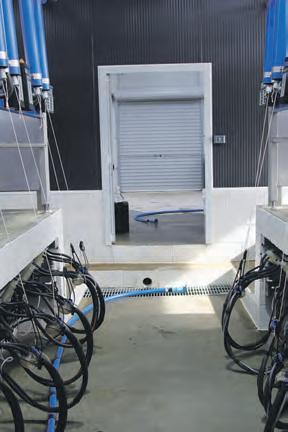
Daniel Peake from McGregors Farm Services.
Daniel describes the dairy as “a Ferrari running on space savers – once we add EID readers the system will be a Ferrari”.
“The current system features DeLaval Milking Point Controllers (MPC580) and FI7 Milk Flow indicators, TF100 LL Clusters, DelPro Flock management system, C200 automatic wash system, CWC15-A Compact water chiller, LVP3000 Rotary Lobe Vacuum pump and Variable Speed Drive,” says Daniel.
Milk volume
“The electronic milk meters measure milk volume and can, at a later stage, be extended to also measure components.
“Every aspect of the milking system had to be modified to fit the rapid exit system – we custom designed and fitted most aspects. It was time consuming but ultimately very satisfying to see the quality and performance of the dairy.
“The receiving can, for example, is positioned unobtrusively under the deck and the vacuum and milk lines are encased in stainless poles either side of the pit steps. It’s all very streamlined and innovative; it had to look right.”
To manage effluent and washdown from the dairy, Williams Irrigation supplied and installed an effluent pump on a Williams four drum pontoon. The advantages of floating an effluent pump with a pontoon is that it pumps from a set depth, floating on the surface of the pond. The pontoon is attached to the edge of the pond by a boom.
Family legacy
The first milking in the new dairy took place on July 15, a few weeks later than originally planned but a great result considering the challenges they faced, says Trent.
“We are currently milking 450 goats but the dairy is sized for a maximum of 1100 goats. Two people take around an hour and 15 minutes to milk the herd with another 20 minutes for washing.” Nathan is delighted with the new dairy.
“At the start the goats weren’t used to having to flick the bails but they adapted very quickly. The DeLaval system is intuitive and easy to use – you can easily tailor it to the herd, switching to manual, for example, for slow milkers.”
The new dairy is the third dairy the Bonnar family have built together – Trent helping construct a fourth with his brother – and the new dairy is a tribute to a ‘can do’ attitude in the face of seemingly insurmountable odds.
Trent and Gwen say the new goat dairy will be the last they will build and if it is, what a high point to finish on.



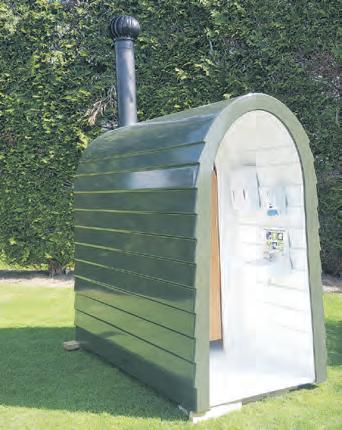
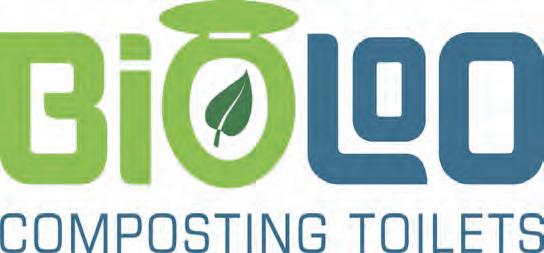