
5 minute read
Brynn Lands Waikato
by Sun Media
Rivertown Electrical staff members Blake Harbottle, right, and Dale Constantine testing their handiwork.
Grant says the sheep are also tempted into the bails by a feed dispensing system supplied and installed by GEA Farm Technologies.
Controlled feed
He says a controlled amount of feed goes into individual bins for the sheep during milking.
GEA also supplied and installed other equipment in the sheep shed, including a new milk plant, clusters, milk lines, cup-wash systems and control panel.
Chemicals for the washdown systems – plant and vat – were provided by FIL.
Area manager Mark Mohring says this included acid, alkali and chlorine. Rhys Darby in the revamped pit.
“We matched products in relation to the water compatibility, type of plant and the animals,” says Mark. He says a programme was developed for the shed in association with GEA, which supplied the washdown equipment and controls. Similar systems are used in goat milking sheds, says Mark.
Trials were conducted, monitoring aspects including washing, water flow and temperatures. Mark says results were gathered every 10 days for the first month of operation then every three months.
The plant is washed down after each milking
FIL area manager Mark Mohring looking over chemical containers used in wash-down. A smooth flow of sheep is key to the milking operation, says Grant Coburn from GEA Farm Technologies.



and the vat after each pick-up, twice a week.
Mark says both systems are fully automated, with the vat-wash controlled by the tanker driver at the flick of a switch.
Cups are removed and teats washed manually, while there is an automated wash system for the clusters.
Wired up
The revamped milking shed was wired up by Huntly-based Rivertown Electrical.
Staff members Blake Harbottle and Dale Constantine say this was the first sheep milking shed the company had tackled, but there were similarities to a dairy cow operation.
“The challenge was that it was an existing building and we had to re-use the old stuff.”
However, they say there was a good existing power supply and the existing switchboard could be upgraded rather than replaced.
Rivertown Electrical wired the existing hot water cylinders and chiller unit, plus a new vacuum pump, and teat-wash, plant-wash and vat-wash.
Out in the milking shed, Blake and Dale wired up existing pulsators and upgraded existing lighting.
They also installed heat lamps and upgraded lighting in the lambing shed.
Rhys says the sheep milking operation produces very little effluent, with the bails hosed after each milking and the yard weekly.
Waste material is piped to an existing lined pond before being sprayed onto pasture via a travelling irrigator.



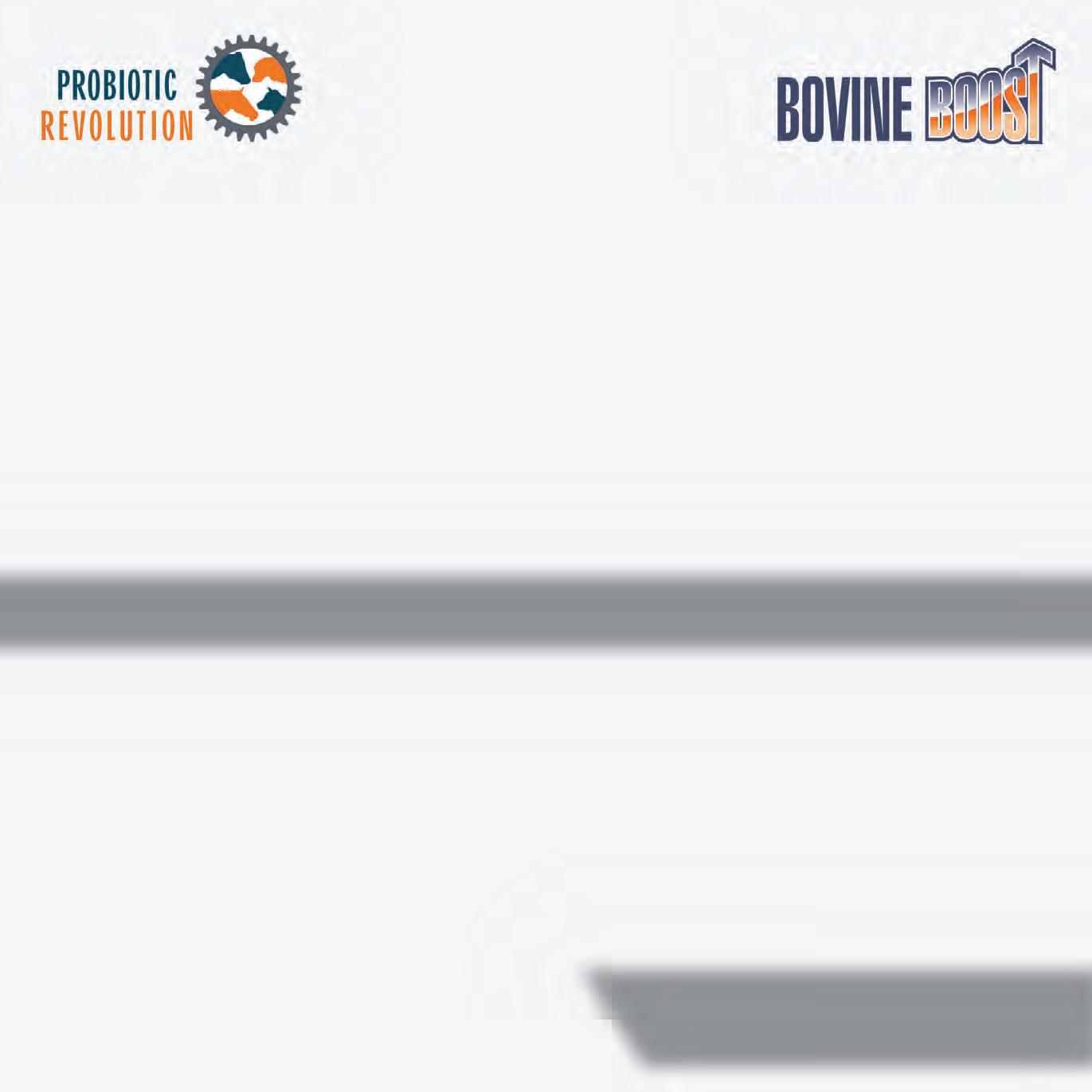



Steve Edwards
Contract milker Lourens Botha with farm co-owner Robyn McLennan outside the state-of-the-art feedpad.
A South Waikato dairy herd has a home away from home.
The 900-cow herd owned by Bruce and Robyn McLennan is fed, watered and protected from the elements in a state-of-the art feedpad.
Robyn says the palatial pad was part of a modernisation project they started on the 221ha property when taking over in 2008.
They have progressively ‘upped’ the herd from 500 cows, replacing an existing feedpad and milking shed on the property at Lichfield, near Putaruru.
Robyn says the old feedpad, built in 2005, had reached its use-by date.
“We were restricted by size.”
Planning began in 2017, with a 180m long by 38m wide structure built on a green-field site next to the 54-bail rotary which replaced a herringbone milking shed.
Robyn says the scale of the feedpad enables the 900 cows to stand for 12 hours or more if required – they generally spend about three hours a day around morning and afternoon milkings. Split in two
The herd is split into two – 450 cows apiece – for milking, which Robyn says makes it easier for farm management particularly in relation to paddock size and floorspace on the feedpad.
Four staff are employed on the Lichfield property. Each cow has 12 square metres of space on the feedpad, which features feed lanes down the middle and along the sides.
A mixture of meal, lucerne and grass silage is fed into troughs running the length of the enclosure via feed-out wagon.
Water troughs are sprinkled throughout the structure, along with special brushes – activated by the cows – which Robyn says reduces itchy skin, improves blood circulation and leads not only to a more relaxed cow but also a healthier herd.
Fabric roof
The entire feedpad and its occupants are protected from the elements by a fabric roof courtesy of Auckland-based Smart Shelters.
Sales consultant Brett Cottle says the polyethylene material, manufactured in Canada, is strong and long-lasting.
He says the roof is held in place by galvanised steel framework, supported by 350mm diameter tanalised timber poles secured 6m-7m into the ground by concrete footings.
There are no central poles or supports, which Brett says makes for a “nice, big, clear” span.
He says the 4200 square metres of roofing material comes ‘like a big carpet’ with guttering added after the roof was in place.
Brett says a feedpad cover improves the overall health of the cows.
“The covers let in up to 90 per cent of natural light, while stopping heat, rain and snow from entering the structure,” he says.
“The cows enjoy conditions that are 3-4 degrees Celsius warmer in winter and 3-4 degrees cooler in summer, increasing herd health and reducing vet bills.”
Complementing this is 3300 square metres of floor covering supplied and installed by Numat.

THE SMART CHOICE FOR A WINTERING BARN

Jeff Rea, Readale West Otago
Increased milk production, benefits in cow comfort and pasture yield SmartShelters clear spans provide industry leading airflow and natural light Reduce mastitis levels and eliminate lameness
e
www.smartshelters.co.nz/composting
MAKE A SMART CALL 0800 566 126