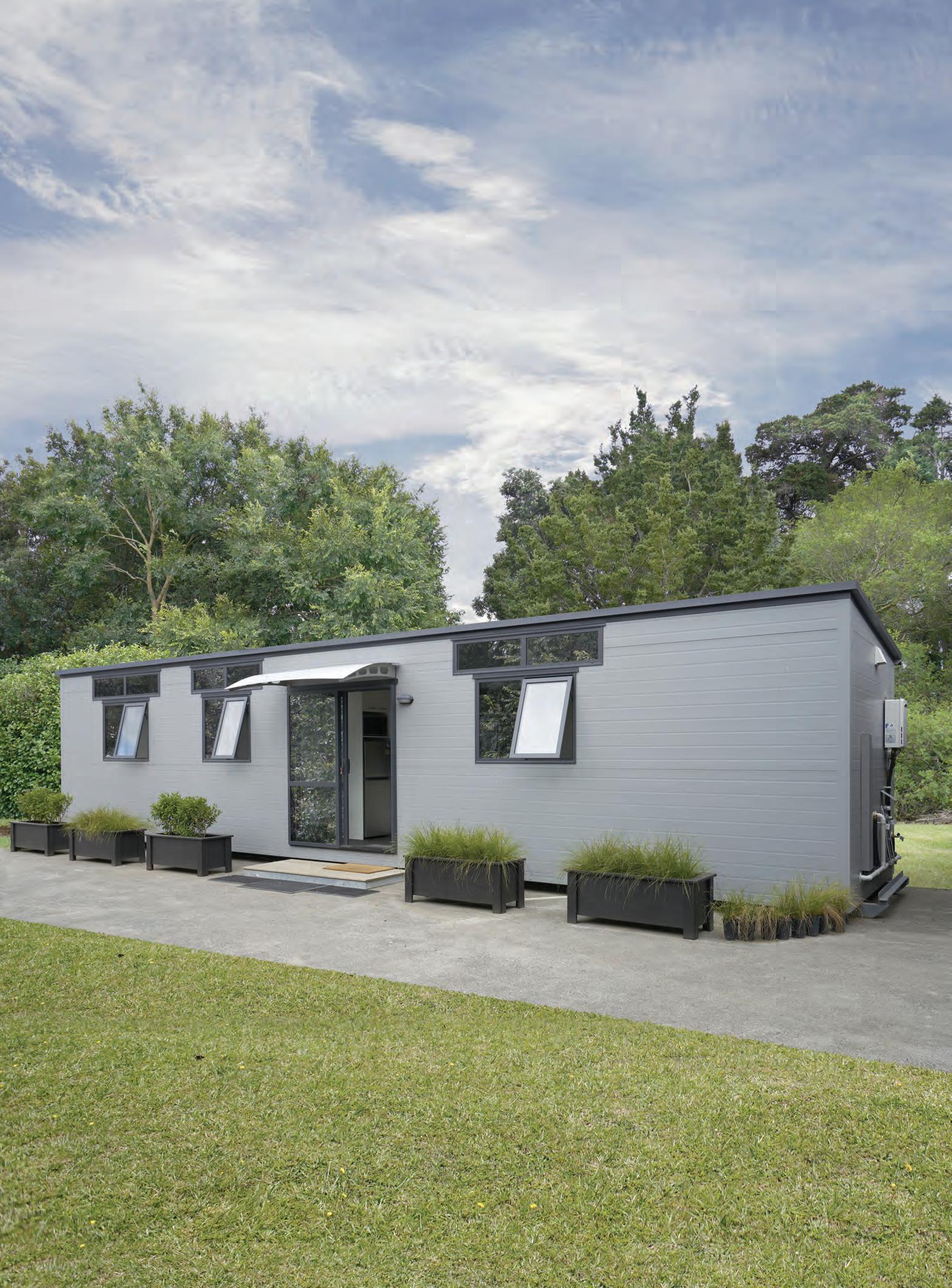
9 minute read
Kaimai Farms Waikato
by Sun Media
A front-on view of the new rotary shed.
It’s no
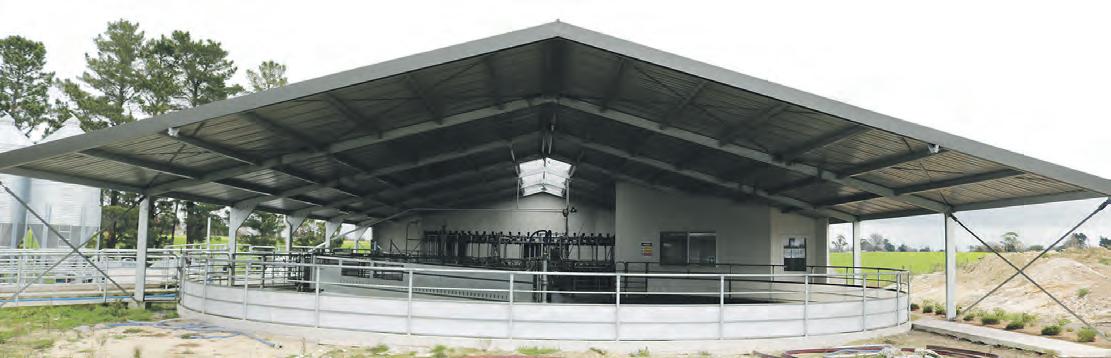
A Waikato dairy goat farm has evolved dramatically since its days as cow country.
Family business Kaimai Farms merged two properties to now run 1050 milking goats, centred on a new 90-bail rotary shed, on a combined 90ha.
With a history of goat milking in the Te Aroha area, Kaimai Farms acquired a 40ha block (used for grazing heifers) on Manawaru Rd in 2017 and a neighbouring 50ha dairy farm a year later.
Initially, Kaimai Farms ran the 90ha in a mix of cropping (potatoes) and grazing.
However, with eight years’ experience in goat milking on another Manawaru Rd property, the owners made the decision to follow a similar path on the merged operation at the end of 2019.
Steve Edwards
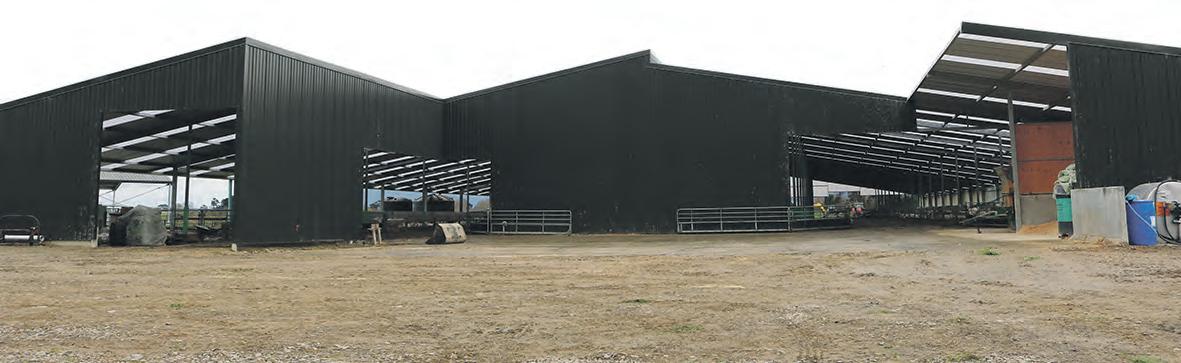
A front-on view of the goat barns.
Just right
“It was in the right place at the right time.”
The new rotary milking shed – designed by Chapman Dairy and built by Don Chapman Waikato – and goat barns were established on a greenfield site.
Kaimai Farms says the rotary operation and barns fill about half each of the 2ha footprint.
The barns were built first at the rear of the milking shed.
Don Chapman Waikato managing director Shanan White says the 90-bail rotary was built from scratch.
“Building on a greenfield site is easier than working around an existing shed and milking times,” he says.
Shanan says the owners, with experience in the industry, had a fair bit of input into the design.
Tick list
“They knew what they wanted.”
The milking shed was tied into the barns, with an access way created between the two facilities.
Shanan says the yard included backing gates and pipework closer together than a dairy cow operation due to the smaller size of milking goats.
Don Chapman Waikato also built the associated milk room, plant room and office. Shanan says materials were chiefly pre-cast concrete panels for the walls and a coloursteel roof.
Kaimai Farms says the new facility has similar technology to its other Manawaru Rd goat farm, including automatic cup removers.
The milking shed has an in-bail feeding system, with the goats enjoying a pellet and maize mix.
Kaimai Farms runs an all-Saanen herd, as per the other property, supplying the Hamilton-based Dairy Goat Co-operative.
A new effluent pond and associated irrigation system was also part of the plan.
Kaimai Farms says the goat barns are light and airy, featuring robots that push feed silage and grass across to the animals as required.
The feed-sweepers run along concrete lanes in the barns.
Wood shavings are used for bedding.
Natural and electric lighting is used in the buildings.
DAIRY TECH
DESIGN, CONSTRUCTION AND AUTOMATION SYSTEMS DESIGN & CONSTRUCTION www.dairytech.co.nz
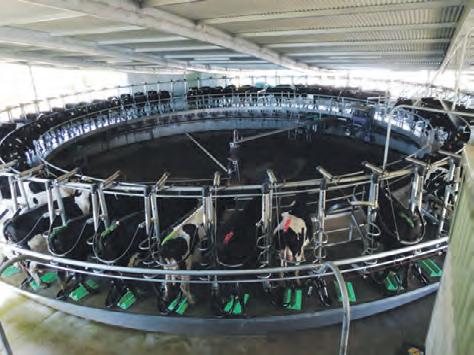
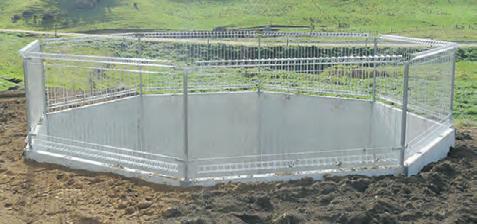
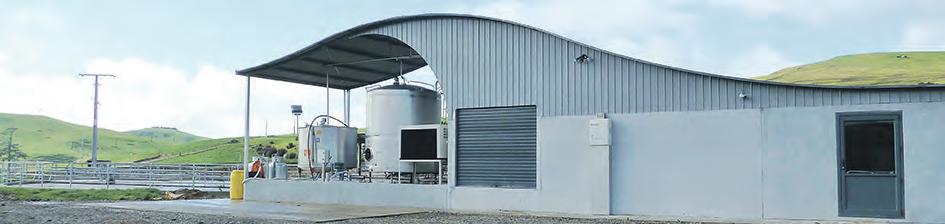


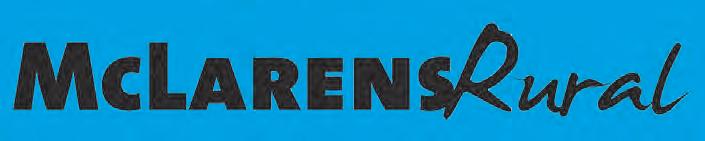
Proud Service Partner of:

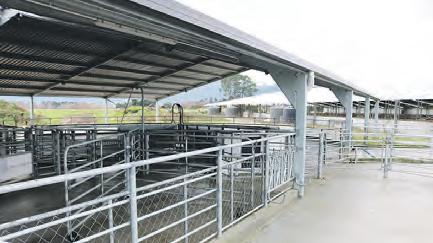
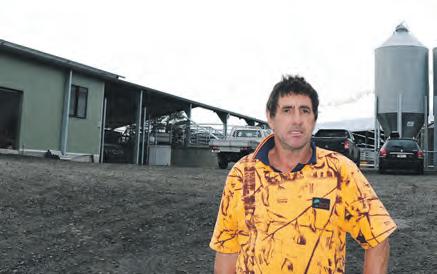
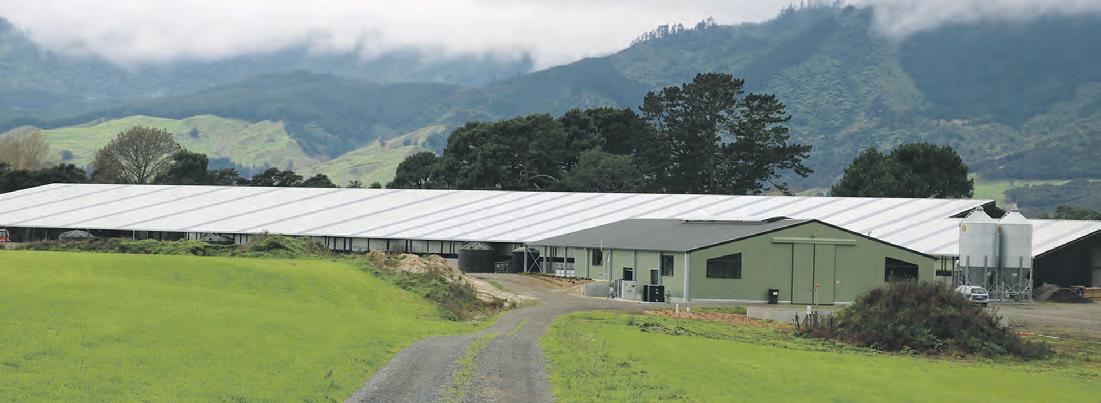
Goats have easy access between the milking shed and barns.
The barns were built by Otorohanga-based Dairy Tech, extending previous facilities used for goat-rearing.
Managing director Peter Gray says galvanised iron framing was used for the barn walls, with the flat-steel roof including skylights.
The walls are pre-cast panels, with steel supports featuring plastic covers to protect the inhabitants.
Dairy Tech also created the concrete laneways for feeding, along with concrete buffers in stone traps for the farm effluent disposal system, sited between the milking shed/barns and effluent pond.
Morrinsville-based McLarens Rural Services joined forces with GEA Farm Technologies in the respective installation and supply of the milking plant and equipment for the Kaimai Farms’ operation.
MRS director Tony McLaren says his company provided the vacuum and control system, primary plate cooling, milk filtering, hot water and washdown systems.
GEA area sales manager Paul Convery says the 90-bail platform is future-proofed, with capacity for 1200 goats.
It also has the capability to add-on an in-bail milk measurement system.
GEA and McLarens combined to supply and install the central gland in the rotary shed, along with the automatic cup removers and clusters.
Team work
Both companies played a similar role in providing and setting up controls for the platform and in-bail feeding system, backing gate and automated drafting system.
In the goat barns, GEA and McLarens supplied and installed automatic feed pushers (GEA FRone) and drinking water

DonBrownExcavatorsLtd
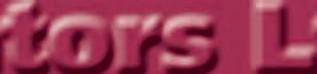
Introducing ournewED150BladeRunner. Zeroswing excavatorwithapowerangle,powertiltbulldozerblade. AveryhandyadditiontotheDonBrownExcavators fleet!
• MetalCartage • MotorScraper • GraderHire Yourearthworks&drainagesolution! Phone 07888-7417 anytime
The team from Don Brown Excavators, including owner Don Brown (pictured) had a big part to play on the greenfield site
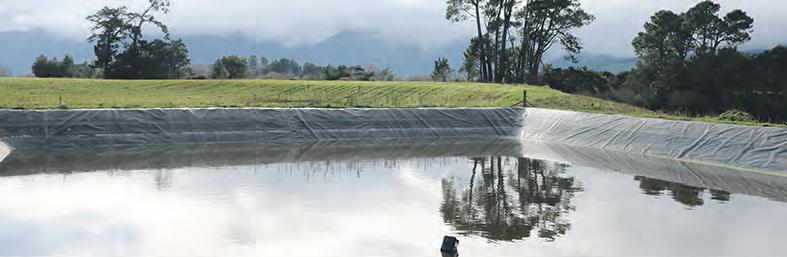
The effluent pond liner supplied and installed by Total Lining Solutions
systems in the goat barn.
Paul says robots move feed towards the feed fence at times defined by operators and according to routes set by the Kaimai Farms’ team.
“This ensures all of their milking stock has access to fresh, high-quality feed around the clock, including lower-ranking animals,” he says.
Matamata-based Compass Refrigeration installed and commissioned the vat refrigeration system.
Compass director Phil West says his work included the control centre for this part of the operation.
The Manawaru Rd facility has a 16,000L vat, while Phil says another concrete pad was added during construction to future-proof for a second vat if required.
Kaimai Farms used a milk chilling unit, which previously served the old cowshed on the property.
“Making use of the secondhand unit helped keep the cost down,” says Phil.
Compass Refrigeration also commissioned the snap chiller (a glycol/water mix), which brings milk temperature down immediately after the milking stage.
“Milk comes out of a goat at about 36 or 37 degrees, and you want to get it close to zero quickly without freezing it before it goes into the vat,” says Phil.
Detergents
A comprehensive range of dairy detergents and teat care products was supplied by GEA FIL.
Tom Laurent, FIL area manager for South Auckland and Hauraki, says an iodinebased teat spray with added emollient was recommended – FIL Iodoshield Active and Active Teat Conditioner year-round.
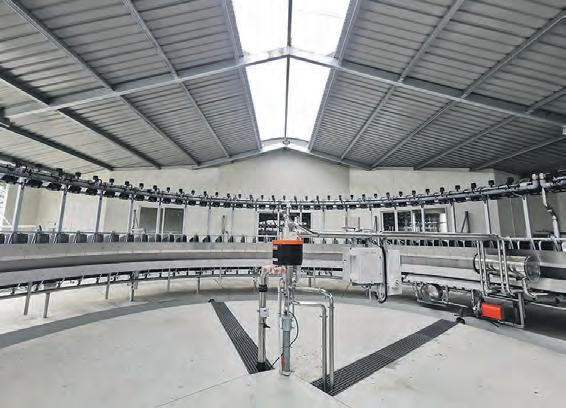


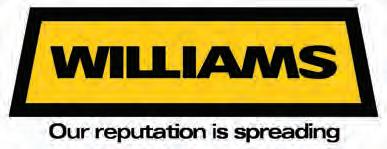
Farm Effluent Equipment Full System Design Installation Service
The rotary shed includes automatic cup removers. Goat-rearing facilities were extended to become goat barns.
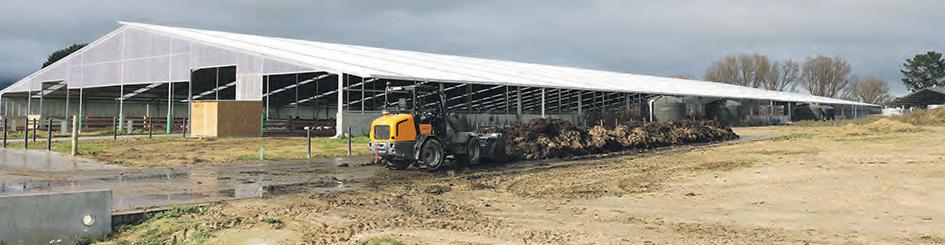

GEA Farm Technologies and McLarens Rural Services combined to supply and install the central gland in the rotary shed.
The GEA Farm Technologies control panel at the nerve centre of the milking operation.

Tom says the additional emollient is ideal for adding to the FIL teat spray during early lactation and challenging periods in the goat milking herd.
It also contains special skincare ingredients including manuka honey, aloe vera and allantoin to increase overall teat condition.
“It leaves teats supple and soft which means less chance of damage that can lead onto mastitis,” says Tom.
The Kaimai Farms’ shed has a fully automated milking plant wash system.
Tom says the plant wash consists of acid and alkali cleaning chemicals.
“The acid detergent can be used in hot and cold washes, with the alkali being hot water only,” he says.
Tom says goat milk tends to have a higher fat content than cows’ milk, so the wash programmes are different to traditional dairy cow programmes.
Tom says the wash-down system works on a timer, with calibrated quantities of detergent added to the hot and cold washes.
It is all done ‘at the flick of a switch’ at the end of each milking, he says.
Concealed wiring
Making sure everything was powered-up on site was the domain of Te Aroha-based Ben Collins Electrical.
Director Ben Collins says it is more about what you can’t see (cables and wiring) which highlights his company’s work on site.
Conduits and cables were laid underground in the shed’s sand base before the concrete floor was poured.
Ben says other wiring above ground for items such as the milking plant, refrigeration/ wash-down systems and lighting are all well concealed from view.
His part in the Kaimai Farms’ project started with an 11,000-volt cable from the road-side to a transformer.
This included a temporary power supply for the builders and also connections to the pump-shed, kidding shed and farm effluent system.
In the milking shed, Ben says a new switchboard was required, with his company putting up lights in the milking area and goat barns (operated on a timer), while also wiring up the plant-room and pump-room.
Ben Collins Electrical fitted the milking platform control panel and separate backing gate control.
The company also hooked up the in-bail meal feeding system and all electricity requirements for the kitchen and office in the Manawaru Rd facility.
Ben says an 11kW motor, installed by his team, powers the farm effluent system’s pump and switching equipment.
Feed for the Kaimai Farms’ herd is stored and conveyed in equipment provided by Matamata-based BCL Feed Systems.
Foreman Bill King says the company provided one 16-tonne silo, plus an auger and piping system to feed into the individual bails on the rotary platform.
Magic eye
As the goats enter the platform, he says a ‘magic eye’ recognises this and automatically fills a dish in each bail.
Bill says goats and sheep are generally served pellets in such systems.
The goats are even given a regular pedicure, courtesy of Goat Care, based out of Tauwhare near Cambridge.
Leading the way
Leaders in goat milking technology throughout New Zealand, GEA’s product range gives you the option to either build new or convert an existing parlour.
We provide you with more bang for less buck with solutions for both internal and external rotaries, double-up or swing-over rapid exit parlours, and state-of-the-art automation for a future proof milking system.
• Design & build • Internal & external rotaries
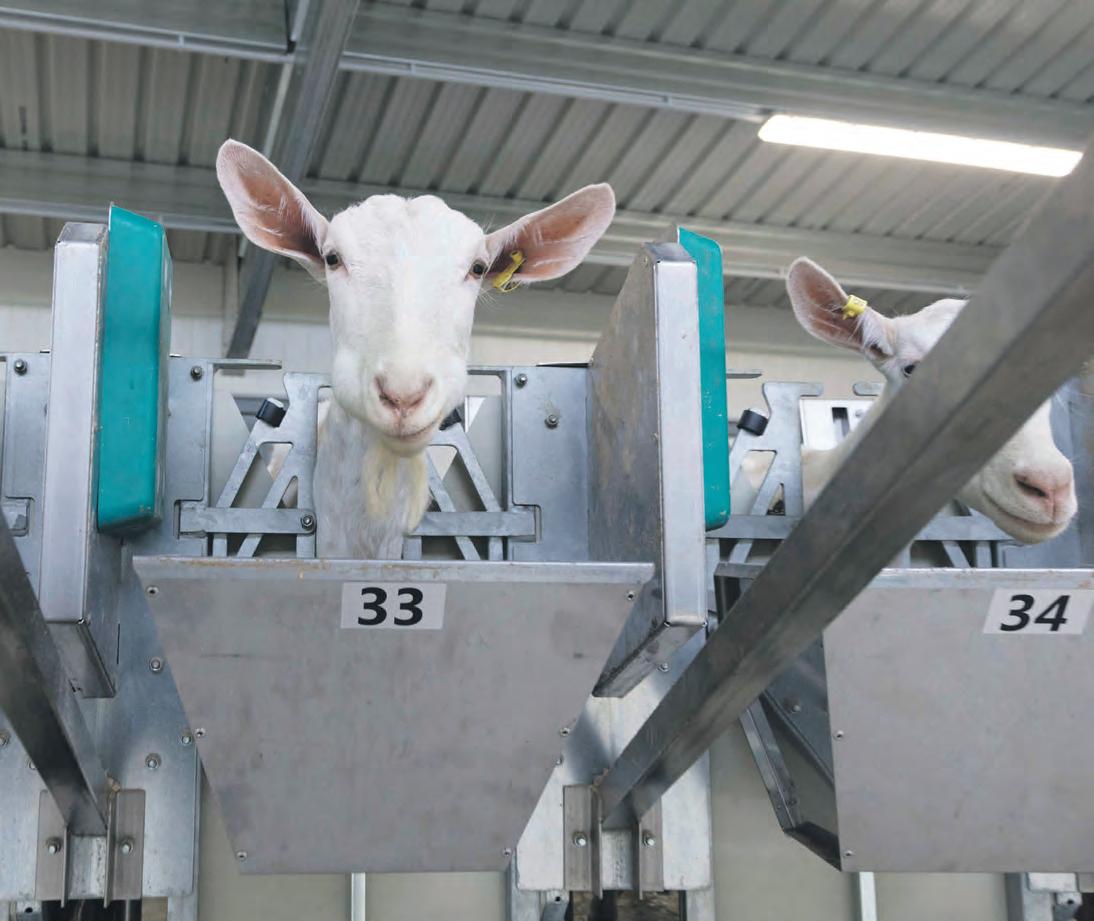
• Side-by-side & double-up rapid exit parlours • Milking & automation equipment • Feeding systems • Hygiene solutions
Let us show you the way. Get us on-farm for a free consult today – 0800 GEA FARM.
Driving dairy efficiencies? We can help.