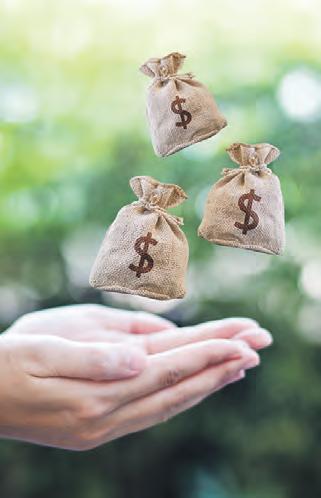
15 minute read
Old Kookaburra Farm Central Plateau
by Sun Media
Season well set up for
Farmers have headed into this season on the back of a financially strong year, meaning the 2020-21 season may be the perfect time to invest on-farm.
The DairyNZ 2019-20 Economic Survey shows farmer resilience to the challenges of Covid-19, price volatility and unpredictable weather, with a positive year for milk production and farm businesses.
DairyNZ chief economist Dr Graeme Doole says operating profit, milksolids per cow and per ha were all up on previous years.
“For the 2019-20 season we were fortunate to receive an above-average milk price of $7.05 per kilogram milksolids, which has continued into this season,” says Graeme.
“This enabled some farmers to catch-up on farm maintenance and debt repayment, while continuing to invest in environmental improvement on-farm.
“Farm costs also increased, with higher fertiliser and supplementary feed costs.
“Although we saw a decrease in interest costs, this was not enough to offset increases in other areas of expenditure.”
The annual survey shows that average operating profit was up 28 per cent on the previous season, at $2750 per ha for 2019-20, while milksolids per cow and ha were at their highest level to date.
“This on-farm success results in a strong contribution to the New Zealand economy, delivering around $20 billion in export value, while employing around 50,000 people on and off farm,” says Graeme.
“It is positive to see such a high operating profit for farms for 2019-20, compared to the 10-year average of $1645 per ha.
“Despite many farms nationwide being affected by a dry summer, production remained strong.”
Operating expenses increased to $5.31 per kilogram milksolids compared to 2018-19, which is above the previous high of $5.17 reported in 2013-14.
“Feed continues to be the largest cost on New Zealand dairy farms, which is important for farmers looking to control farm costs.
“To build their resilience for periods when milk prices are lower, farmers should look at their overall cost structures on-farm and identify where they can trim costs.” Sharemilkers experienced a good year, recording a 35 per cent increase in operating profit on the previous season to $1050 per ha, while faced with similar cost changes, price volatility and weather conditions. Farmers are encouraged to analyse their individual performance and compare their results with similar farms through DairyNZ’s DairyBase and budget case studies. Budget case studies look at several top-performing farms nationwide for the current season, to help identify opportunities to reduce the cost of production. This is a useful benchmarking tool for farmers to get insights and ideas from. The annual Economic Survey analyses a representative sample of farmers, surveying 326 owner-operators and 124 herd-owning sharemilking farms (50:50 sharemilkers) across New Zealand for the 2019-20 season.
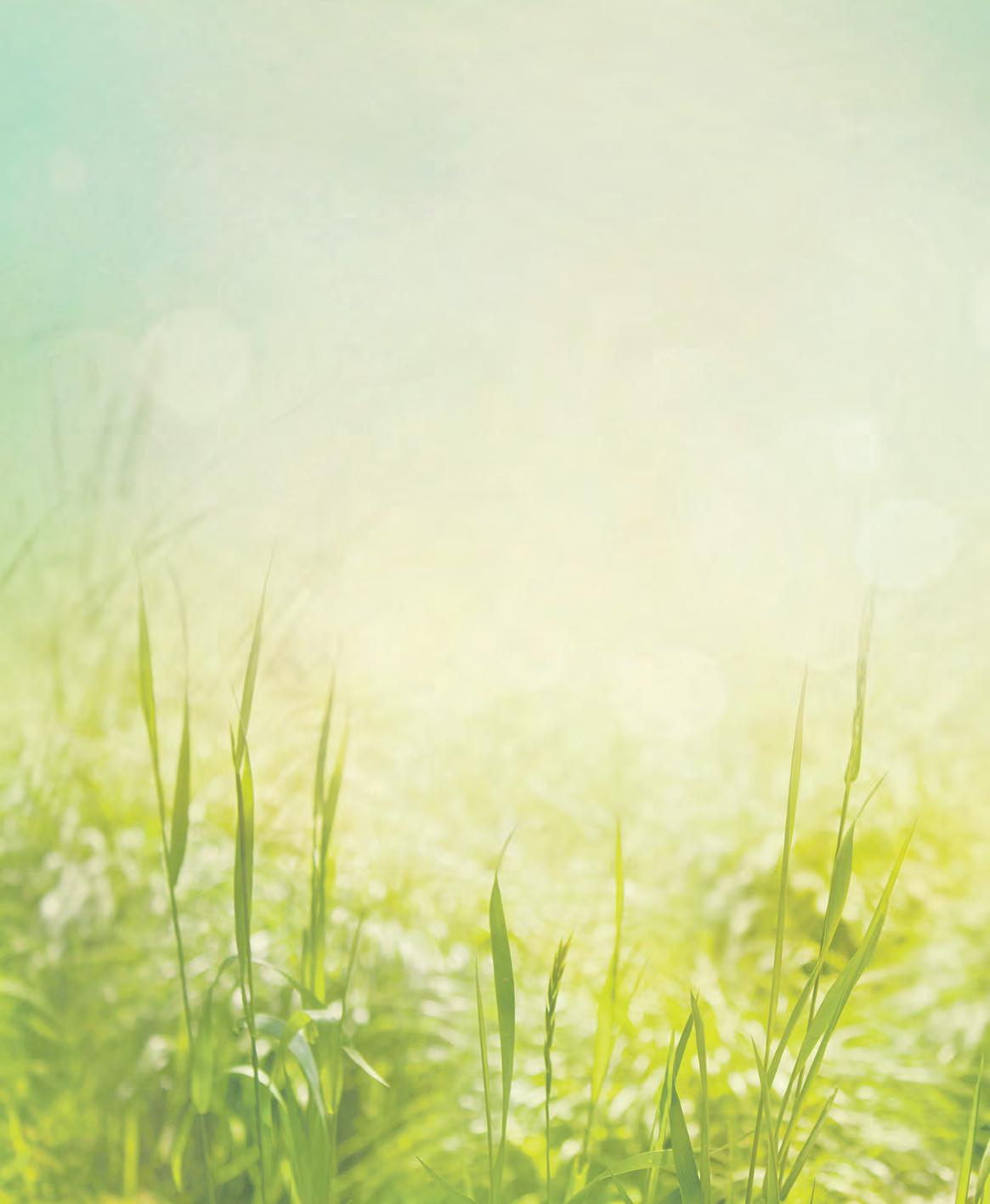
Old Kookaburra Farm Central Plateau 4-7
Waerenga Waikato
8-9
Martin Parks Waikato 10-11
Ashleigh Lodge Waikato 12-15 Darby Sheep Waikato 16-17 Brynn Lands Waikato 18-19 Harris Partnership Waikato 20-23 Rushbrooke Farm Waikato 24-27
Kaimai Farms Waikato 28-31
Crows Nest Waikato 32-33
Golden Elm Farms Waikato 34-37
Arnold Waikato 38-39
Schuler Sheep Waikato 40-43 Alexandra Road Farms Waikato 44-47
Niaruo Farms Taranaki 50-53
Lepper Taranaki 54-57
Twin Creek Dairy South Auckland 58-61 Cawte King Country 62-65
Green Park Sheep King Country 66-69 Glenkylie Farm Southland 70-71 Kaikaha Southland 72-75
Avon Lea Canterbury 76-77 Kairoma Farm Canterbury 78-79 Selwyn Dairy Canterbury 80-83 Omanuka Farming Horowhenua 84-85 Barnes United Kingdom 86-87
Weavian Farms United Kingdom 88-89 Gorey Ireland 90-91 Shengjiang Group China 92-93
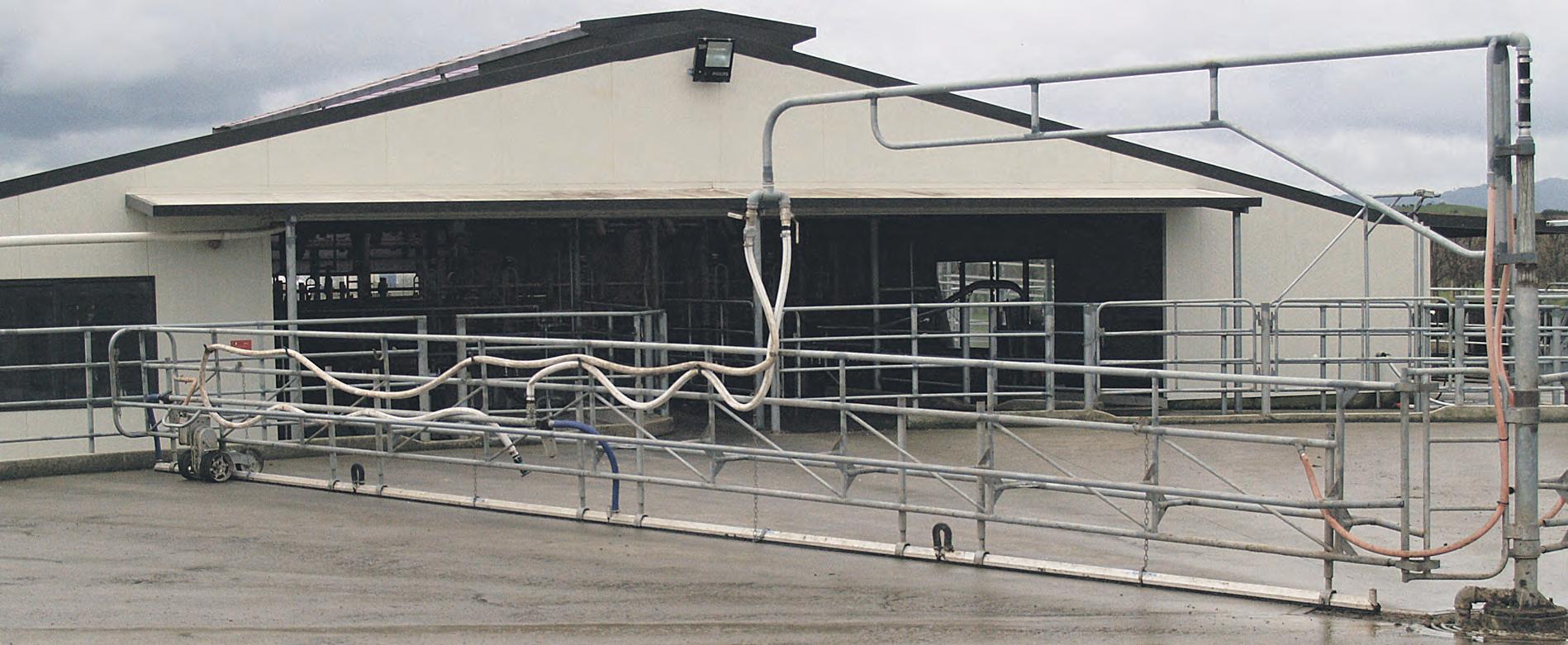
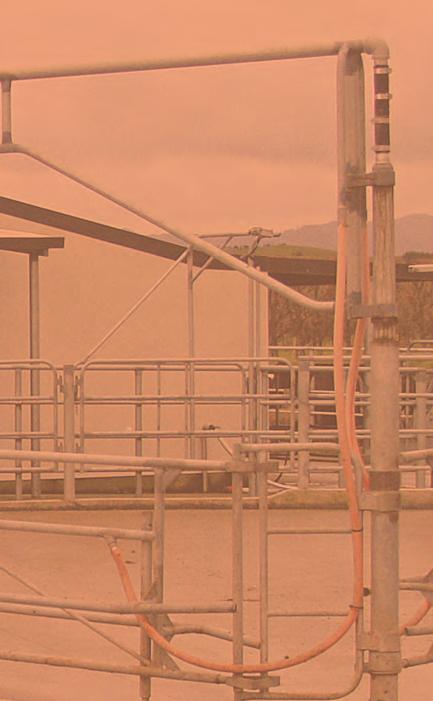
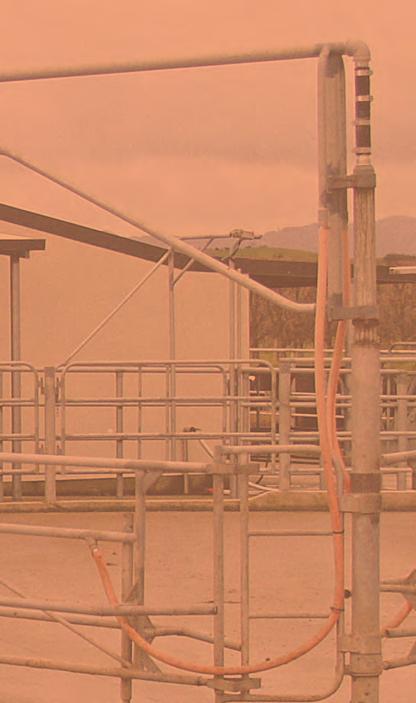
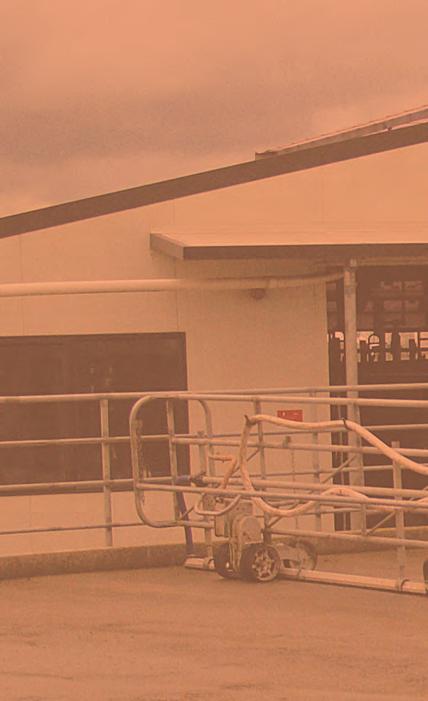

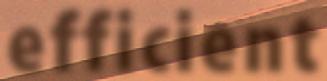
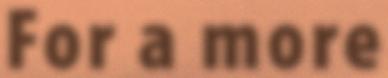












farm, unique name
Clare Bayly The bright interior and rubber underlay in entrance and exit helped the cows transition from herringbone to rotary.
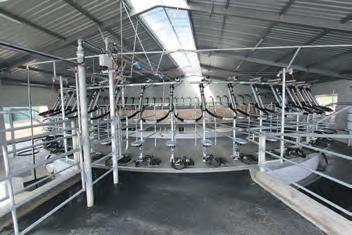
The naming of Old Kookaburra Farm is a nod to Matt Ruthe’s late mother Laurel, who was Australian by birth and had a unique laugh.
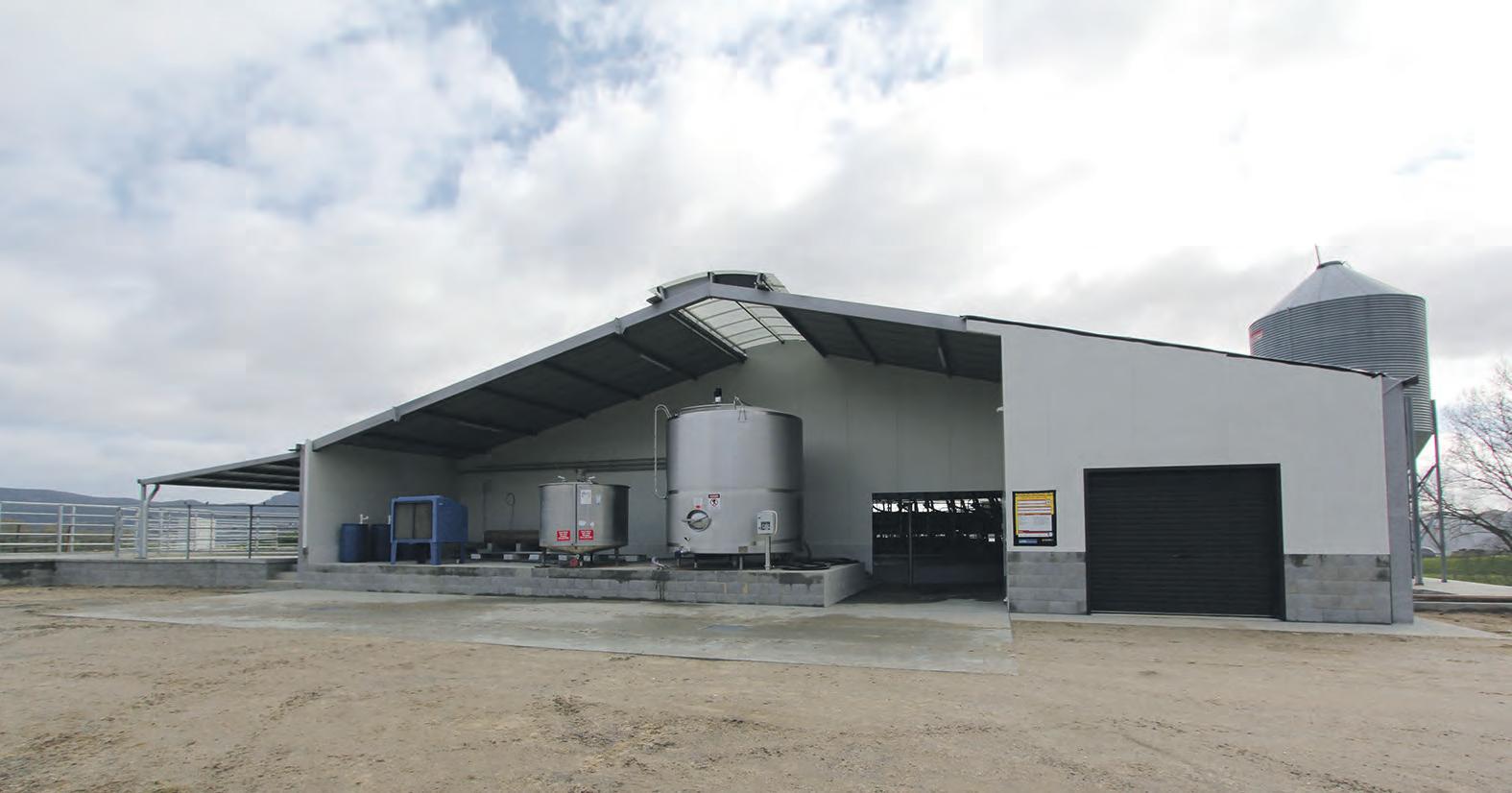
“We came up with the name when Vikki and I bought into the farm and she loved it,” says Matt. The 200ha farm is located at Tirohanga, just North of Taupo, and was originally owned by Matt’s parents who lived and operated the dairy farm next door.
Matt and Vikki started their sharemilking career in 2011 after five years of managing, and in June of this year brought into the farm itself.
“The farm had a 39-aside herringbone which was built in the 1980s and was extended in early 2000s,” Matt recalls.
40-aside but said the pump got in the way, hence the odd number of bails.”
Milking 470 cows in the old shed took around seven hours per day, and a new shed was on the wish list when Matt’s parents bought the farm.
Timing
It was a matter of waiting for the right time – and that coincided with the Covid lockdown in the autumn of 2020.
Today, the perfectly positioned new dairy sits in landscaped grounds framed by retaining walls and grassed lawn, and it is hard to imagine that the hill on which it sits wasn’t always this way.
“The optimum site for the shed was on a hill in the centre of the farm, where the dairy would be protected from the prevailing winds and be ideally positioned to minimise the cows walking,” says Matt.
“The only problem was that the contour of the hill was the wrong way round, so we had to reconfigure the lay of the land.”
Development stage
In the initial stage, McLaren Contracting came in with a scoop and prepared the shed site which Matt and his brother could then develop. Once the site was cleared, Matt and his brother started development of the tanker track and recontouring the top of the hill, using their own scoop and digger.
“I spent lockdown developing the tanker track,” Matt recalls. “All up it took around two months to develop the track and the site.
After 15 years on the wish list, Matt Ruthe is pleased to finally be out of the 39-aside herringbone and into his new 54 bail rotary.
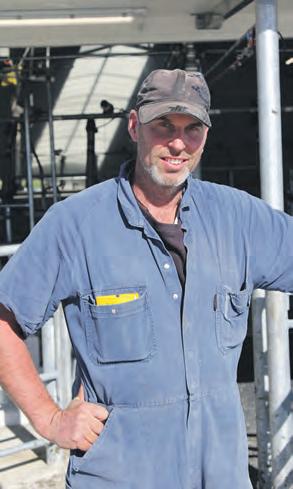
“The new dairy was always going to be a rotary and we looked at quite a few before we decided the ideal would be a 54 bail Concrete Orbit rotary from Waikato Milking Systems.
“We had Waikato Milking Systems in the old shed and have always been happy with the quality and service.
“My list of must-haves for the new shed included a covered vat stand, because it doesn’t make sense to have vats in the sun when their purpose is chilling milk.
“I also wanted the vat stand to be on the south/colder side of the dairy for much the same reason, with the entry-exit and collection yard on the warm north side. I wanted two doors to the vet/animal handling area on the west well of the dairy, with sliding doors to shelter the milking area from the prevailing wind.
M Milking Systems ilking Systems
Effluent Effluent Management Management
Refrigeration Refrigeration + + Water Water Reticulation Reticulation
Milk with confidence Milk with confidence
Oubik are proud Oubik are proud to to have supplied have supplied and and installed t installed the milking machine, he milking machine, water rwater reticulation, eticulation, e effluent system, ffluent system, re refrigeration and frigeration and pr pre e-cooling system f-cooling system for or Matt Matt Ruthe Ruthe. .

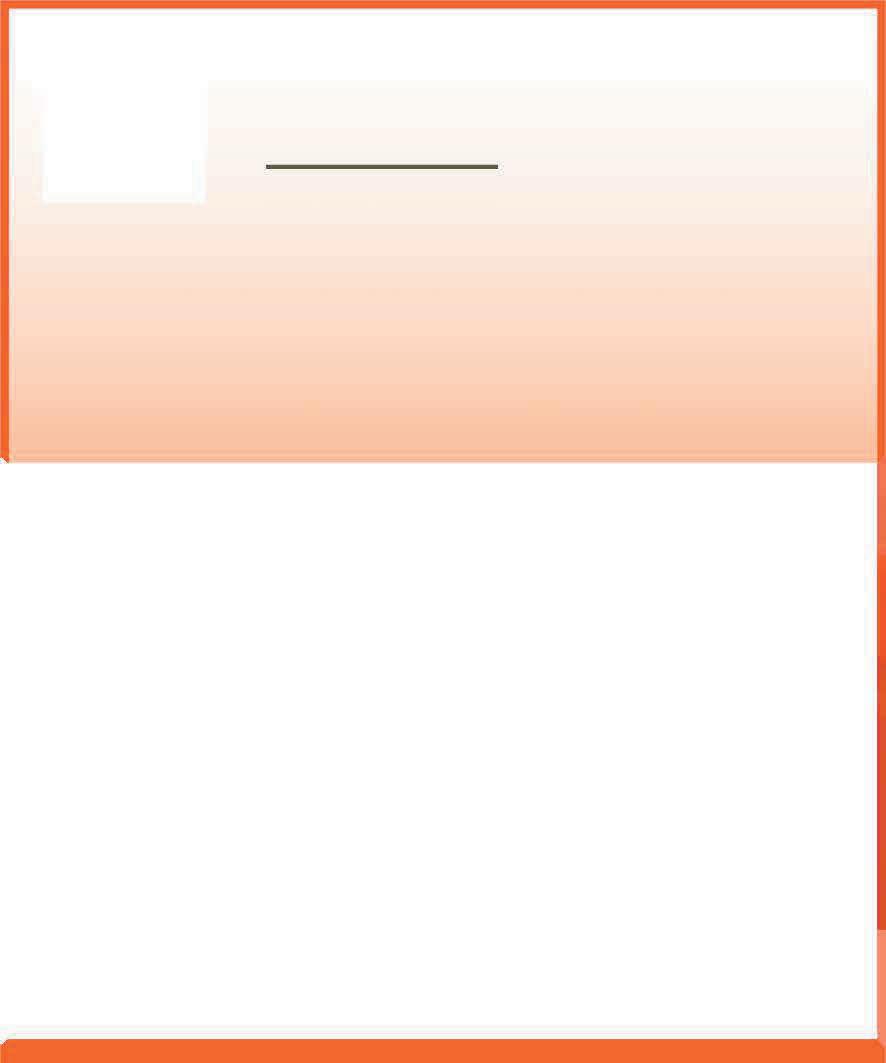

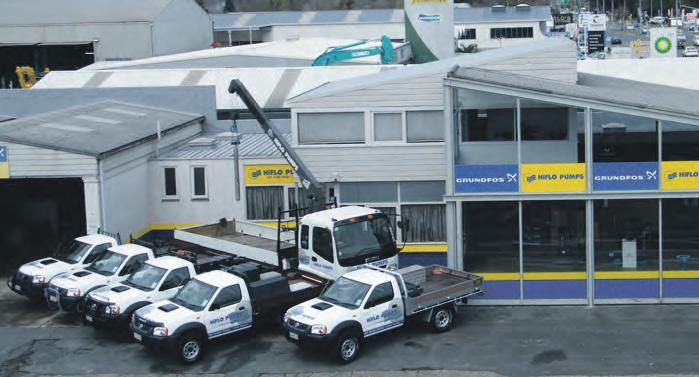
Authorised Grundfos dealer Authorised Grundfos dealer
GRUNDFOS GRUNDFOS ® ®

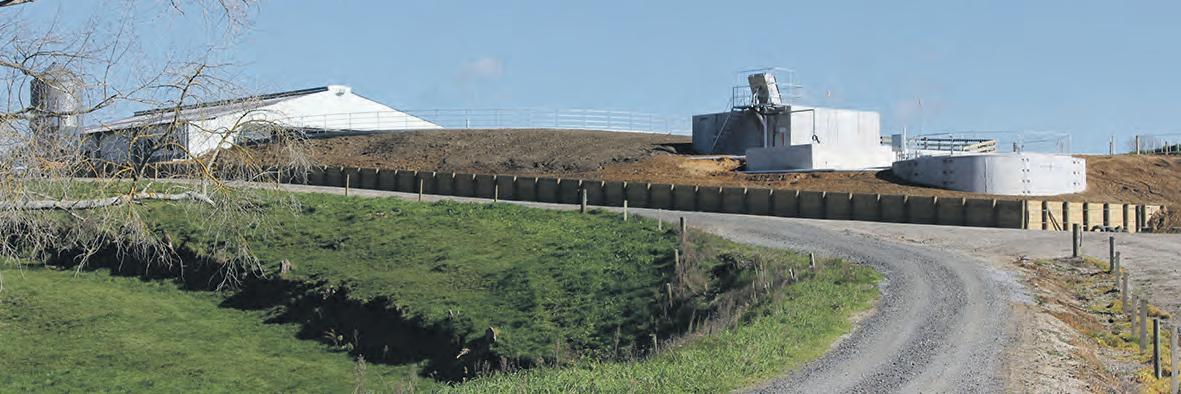
Left to right, builder Rob Broomfield, Matt Ruthe, Qubik general manager Jason Hare and Chris Maughan, Qubik milker manager Putaruru. The dairy is operational ready for the start of calving.
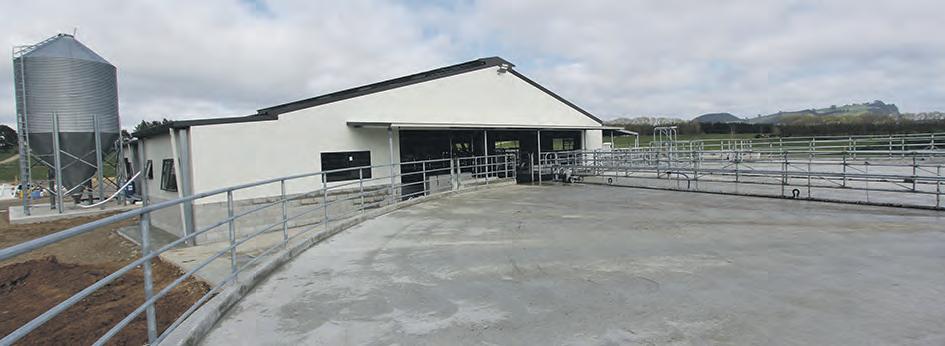
The Waikato Milking Systems 54 bail Orbit concrete rotary platform and an underpass, right, makes it easy to access the centre of the dairy.
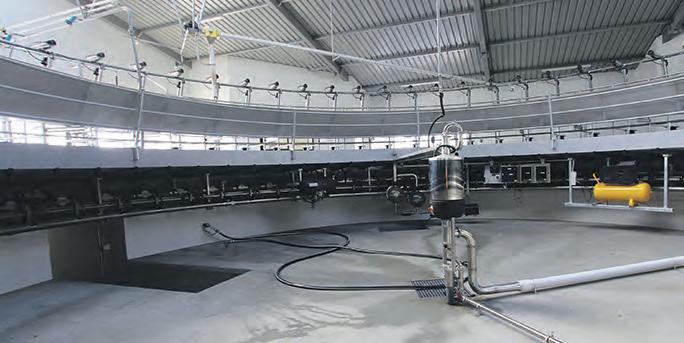
“The yard had to be a decent size and I wanted a scraper on the backing gate to reduce the number of people required to hose the yard.
“The rump rail supports on most rotaries are located close to the platform but, other than at cups on and off, I wanted them stepped out to avoid pinch points around the platform. I also wanted a fold-down vet platform for such things as vaccinations.
“We contracted Rob Broomfield to build the new rotary having seen some of his builds and liking his approach, design and standards.
Tidy and efficient
Rob Broomfield, of Morrinsville-based Broomfield Construction, said knowing the size of the platform determined the footprint of the shed.
“My sheds always have a lot of room around the sides and incorporate all auxiliary rooms under one roof to avoid having smaller sheds around the outside,” says Rob
“It’s tidier and more efficient. We sized this dairy for 500 cows as there’s nothing worse than being too tight on room.”
The new dairy is clad in polypanels with coating on the blockwork and clearlite panels in the ridgeline, providing natural light to the interior.
Construction commenced prior to Christmas 2020 so that the walls and roof were up to provide cover for contractors during the hottest days of summer. The interior fitout began in February 2021.
All concreting of the interior and exterior of the dairy, including yards, were carried out by contractors organised by Broomfield Construction.
The new Waikato Milking Systems 54 bail Orbit concrete platform was installed by Moa Milking and Pumping.
Known for their strength and engineering integrity, Waikato Milking Systems Orbit platforms integrate seamlessly with Waikato Milking Systems milking plants and accessories, and are engineered to allow for technology enhancements and additions in the future.
The platform provides operators with a clean, efficient milking environment and excellent cow flow on-and-off the platform. The 2.7m wide deck protects milking and electronic equipment with a large walkway in front of the cows.
The platform has a twin-track Multi-Roller undercarriage, where the nylon rollers that move together with the platform eliminate the requirement for wear strips and track oilers, making for a cleaner pit and helping to spread the weight across multiple points. This takes pressure off running gear which, in turn, lowers maintenance costs.
Speeding up the process
Qubik installed the milking machine, water, precooling, refrigeration and effluent system. General manager Jason Hare says the dairy features Waikato Milking Systems ECR-S Electronic Cup Removers, which have an AutoStart feature to speed up the milking process.
“We also installed BailGate Straps which, when used with ECR-S, automatically lower and raise when the cup removers are activated.
“The dairy also has a SmartSpray automatic teat spray which applies teat spray to every cow at every milking and acts as a leg spreader, making cupping easier,” says Jason.
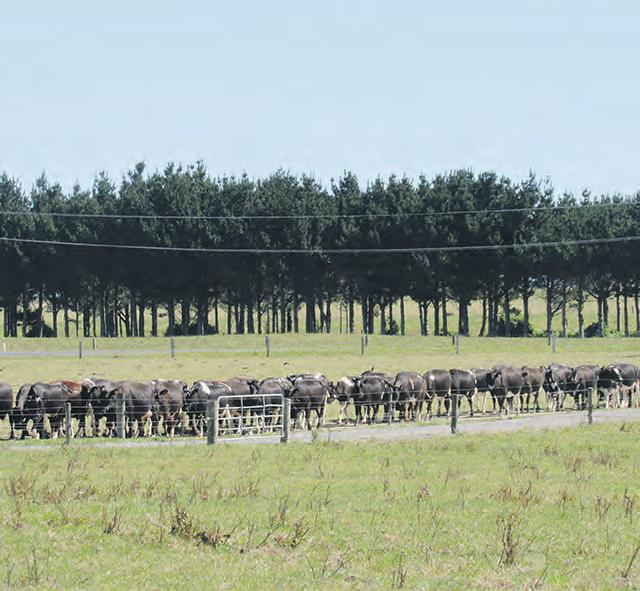
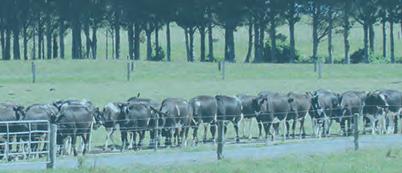
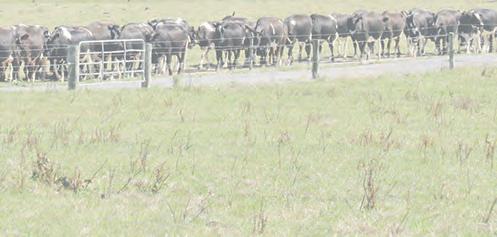


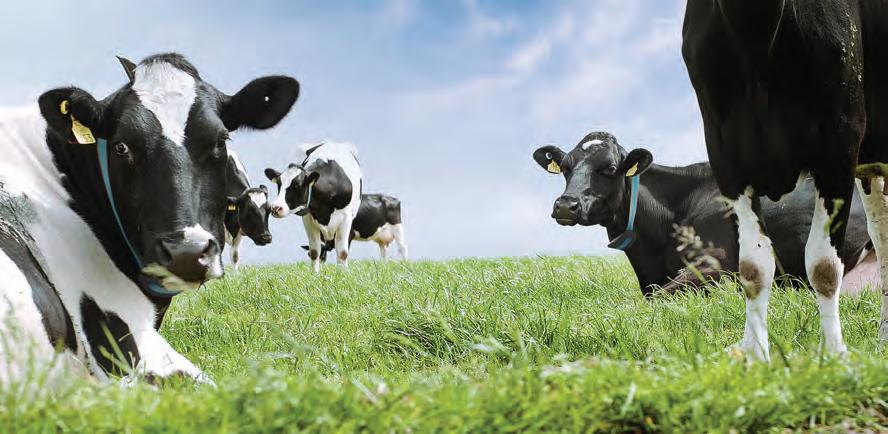

CRIDGE GraiN & SEED DrESSiNG SEEDS quality paSturE SEED

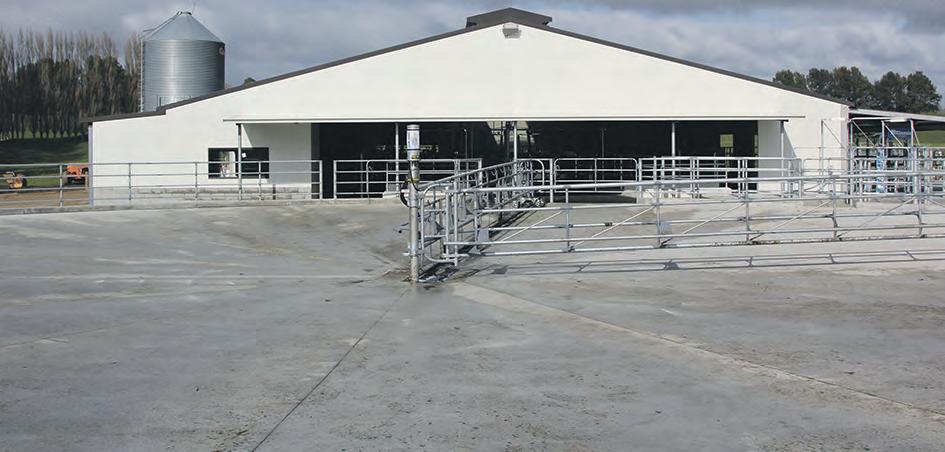



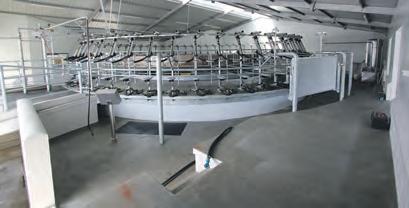
The 2.7m wide deck of the 54 bail Waikato Milking Systems Orbit concrete platform protects milking and electronic equipment.
Effluent gravity feeds to a stone trap which separates solids and liquid before it is further refined in the solids separator. Liquids are then pumped into a 145,000L effluent tank, left. Solids are stored in the bunker, right Cups off position showing the underpass, to the left, and vet stand, right.
Waikato Milking Systems’ Ben Frederickson checks the 320 claws which were moved to the new rotary from the 39-aside herringbone.
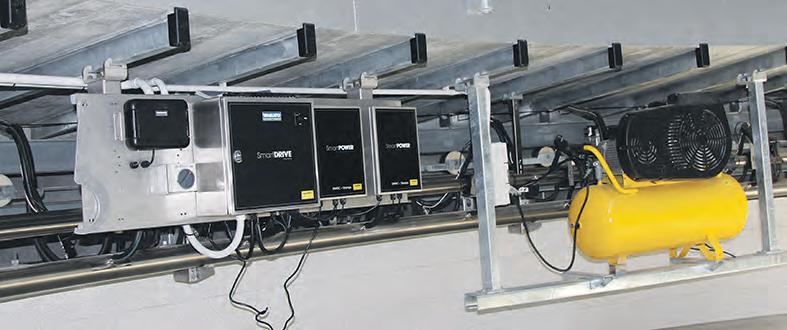
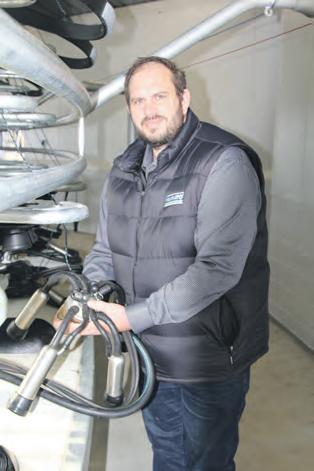
“Over recent years we upgraded a few elements of the old milking system, knowing that they would eventually move across to a new dairy. These included the pulsators, 320 clusters, vacuum pump, plate cooler, filter and chiller.”
The new dairy features four water tanks which collect water from the dairy roof, with the balance of water coming from a bore by the old cow shed. Qubik installed the wash down hoses, backing gate skirt wash, along with the platform and skirt wash.
Effluent from the dairy gravity feeds to a stone trap which separates solids and liquid before it is further refined in the solids separator.
Liquids are then pumped into a 145,000L effluent sump or tank which, along with the other precast concrete elements of the effluent system, was supplied by Paeroa Precast for assembly by Broomfield Construction. Solids are stored in a bunker which is easily accessed by tractor.
The effluent sump/tank is the primary store facility for liquids before they are either pumped to pasture or the bladder, which was installed some years previously adjacent to the old herringbone dairy. Matt is able to irrigate around 25 per cent of the farm via travelling irrigators.
Finishing touches
Matt was three weeks into calving when this article was written, and says the cows are adjusting to the rotary environment very well.
“We included an extra gate to the side of the entrance to the platform to help funnel them in,” he says.
“The colostrum cows come in every day, some walking on at the first milking while others may need a couple – but all happily walk on after four milkings. They have always been fed in the shed, so this certainly helps encourage them on.
“From an operational aspect the dairy is complete. The only items remaining to be done are really cosmetic – like outfitting the office, the bathroom and finishing the interior and exterior.
“My brother and I built the retaining wall which runs around the effluent system area and up to the side of the dairy.
“When the lawn grows, it will look really smart. It has to look good.
“The exit/entrance race is concrete to minimise the amount of mud which will come into the collection yard and the dairy, and we’re able to hose this with the run-off going into the effluent system. The concreted area also acts as another holding pen, which is very handy.
“We don’t get a lot of power outages but when we do, it can be very disruptive so I’ve now got a generator which will cut in automatically if the power goes off.
“At this stage, it’s hard to predict how long it will take to milk but we estimate it should take 1.5 hours per milking. That’s a third of what it was taking before.
One chance
“You only get to build a dairy like this once, so it was important to do it right. I’ve only been milking in it for a few weeks but I’m enjoying it. It was a long time coming but it was worth waiting for; it’s a great shed.”
Once the entire herd is in, Matt estimates that time spent milking, previously seven hours in the herringbone, will be around three hours per day (1.5 hours per milking in the new rotary).
“That’s a potential saving of four hours a day, or 28 hours per week!”

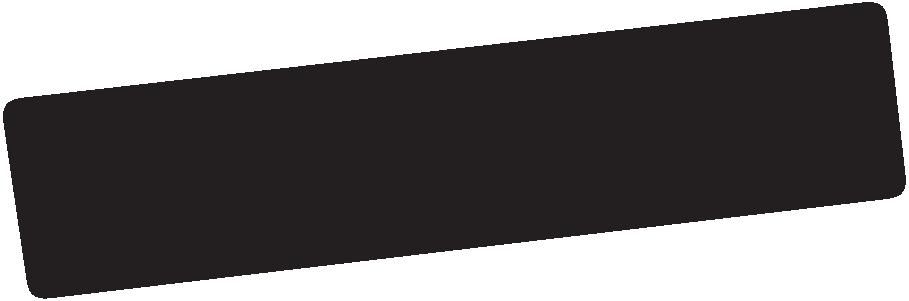
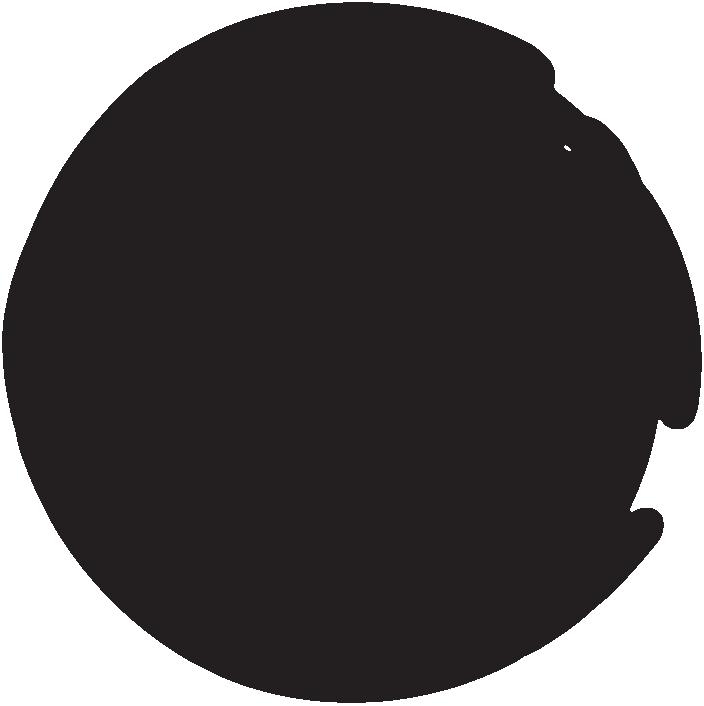



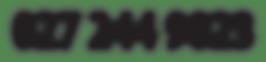



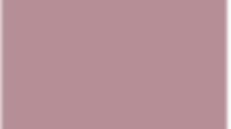

