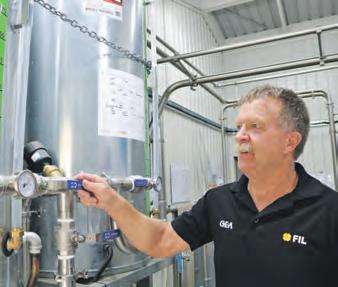
13 minute read
Golden Elm Farms Waikato
by Sun Media
The robotic feedpushers from GEA Farm Technologies in action.
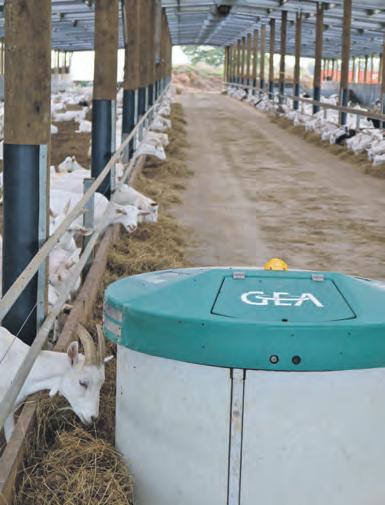
The components are mixed with water and pumped through the plant after each milking in a fully automated operation.
Wash cycle
Greg says the automated wash system is installed to match the recommended wash programme and required chemicals for each day of the week.
The manual vat wash uses a powdered alkali and liquid acid, with staff following the wash programme; they add the designated chemical to hot water, followed by a cold-water rinse again to finish. Greg says this is undertaken after each milk collection.
The milking shed was designed and built by Te Awamutu Construction.
Owner/operator Pat Gibson says he worked with the Roach family in the planning stage, tailoring the design to the current herd size while also catering for future growth.
FIL Area manager for Cambridge, Matamata, Putaruru, Greg Duncan, checking out the hot water component of the plant cleaning system. Jenny and Lance Roach in the goat barn.
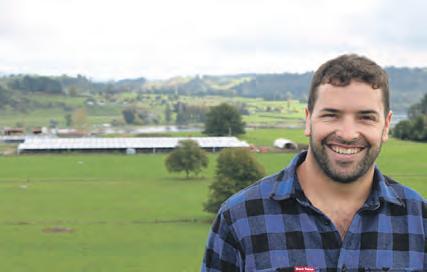
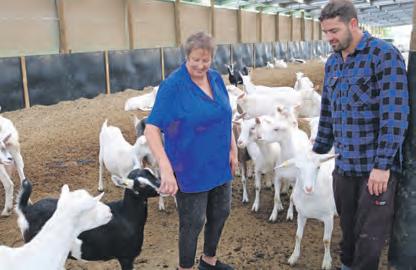
Lance Roach on the top tier of the farm, with the Waikato River in the background.
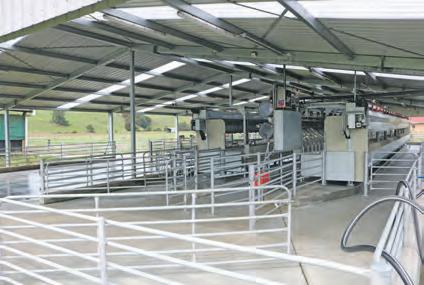
Initial siteworks were undertaken on the former paddock by Te Awamutu Construction, with top-soil taken away and hard-stand area built up.
Pat says the pit and amenities – plant room, milk room and staff kitchen – were then added.
A feature is the roof which covers the entire yard as well as the milking area.
Wiring Work
Putaruru Electrical completed all the wiring required for the new shed.
Staff member Richard Keijzer says the goat facility was able to tap into the cowshed’s existing electricity supply, via underground cabling.
His work extended to all wiring required in the bails including lighting, milk lift, milk pump and pulsators. In the milk room, Richard says he wired up the vacuum pump, hot water cylinders and vat wash, plus the vat refrigeration system.
In the goat barn, Te Awamutu Electrical looked after the required lighting and power points.
A combination of old and new was used in the shed by Matamata-based Compass Refrigeration. Owner/operator Phil West says a new refrigeration unit was needed for the supply vat, while the glycol system from the old shed was transferred over to the goat operation.
Other refrigeration equipment at the former cowshed was past its use-by date, he says.
Phil says the system was sized accordingly for the current goat herd and volume of milk produced, while also allowing for future growth.
Goats’ milk hits the vat at 6.3 degrees Celsius, he says, with the primary water source taking the initial hit before the glycol unit comes into play.
Painting of anywhere where cleaning is required was undertaken by Hamilton-based Dairy Wall Coatings.
Director Greg Fulton says an Acraflex dairy wall coating system was used in the pit and surrounding milking area, along with the milk and plant rooms.
Along with hygiene, he says farmers also like to have a good working environment for themselves and staff. “There’s the feelgood factor.”
The surfaces can be cleaned quickly, saving operators 30 to 45 minutes at each milking, says Greg.
He says a brush/roll/spray method is used to apply Acraflex – seven applications including two coats of glaze to finish.

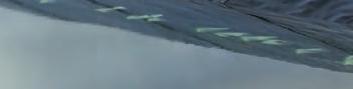
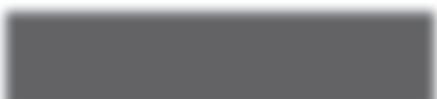





NATION WIDE
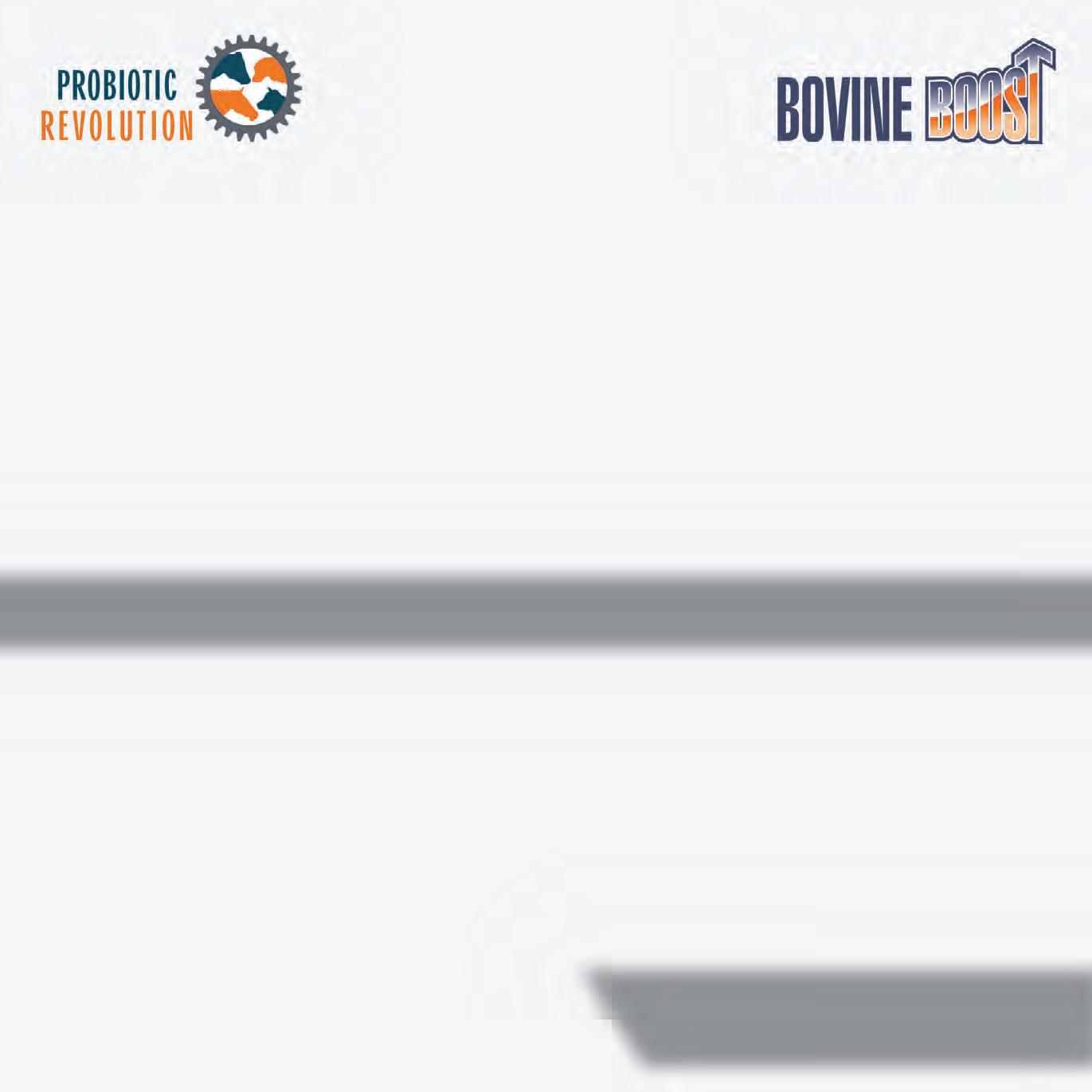

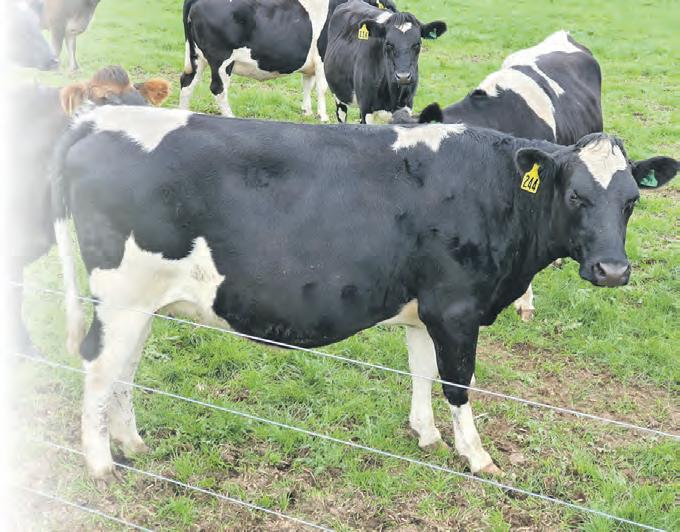



Steve Edwards Project manager Ang Finnerty, left, with farm owners Ray and Arna Curtin, 2IC Len Keoghan, farm manager Sharon Finnerty and project manager Dean Finnerty.

The Toa Rd complex - including milking parlour, barn and “baby barn” - covers about one hectare.
Practical experience and family support are key ingredients to a dairy goat operation in the Waikato.
Dean and Ang Finnerty, who featured in last year’s New Farm Dairies after adding a goat milking parlour and barn to an existing dairy farm, have repeated the process.
This time around the goat amenities are on part of a Waitoa property, between Te Aroha and Morrinsville, owned by Ange’s parents Ray and Arna Curtin.
Dean and Ang are project managers at Toa Rd. She laughs that they have “stolen” 40ha of her parents’ 182ha dairy farm to run 850 milking goats through a new 50-bail milking shed.
“We always wanted to diversify,” says Ang.
She says the move also means the dairy herd’s farthest distance from their 40-aside herringbone milking shed has been “taken away”, making for a more compact dairy farm.
The design and construction of the goat milking shed and barn is based simply on that used by Dean and Ang in a similar project of their own along nearby Paeroa-Tahuna Rd, with Morrinsville-based Chapman Dairy and Don Chapman Waikato again engaged for the Toa Rd contract.
Ang says the Toa Rd shed is a mirror image, with an emphasis on efficiency.
“Two rows of cups means we cut milking time by putting through 100 goats at a time,” says Ang.
Efficient design
A smooth entry and exit is also key to the Toa Rd design, again mirroring the Paeroa-Tahuna Rd model.
Ang says this includes linking the barn to the milking parlour.
Don Chapman Waikato director, Shanan White, says features of the project included the depth and width of the pit and rapid exit from the bails.
The milking shed roof at Toa Rd was made one metre wider than its Paeroa-Tahuna Rd counterpart to keep out rainwater, with a bigger milk-room built to accommodate two vats.
Overall, Shanan says the parlour chiefly involved adapting a traditional dairy cow herringbone to suit milking goats.
“The details were pretty standard,” he says.
This included the rooms housing the milk plant and wash-down systems, which Shanan says were in line with a dairy cow operation, while vats holding the goats’ milk for collection are indoors.
The milking shed on the Toa Rd property is built on the site of an old cowshed, which Ang says wasn’t worth saving for the new venture.
She says the opportunity was identified three years ago, with capacity for 1200 goats. “A thousand is the ideal.”
Physical work started on the property last June, with the first pick-up in early December for NIG Nutritionals at Paerata.
The company tanker visits three times a week, with the milk destined to become infant formula.
Associated with the milking parlour is a 70m x 65m covered goat barn, with pens and feeding units.
Dean says the roof, supported by treated wooden poles, has skylights in every bay to give the goats well-lit surroundings in natural light.
“It’s warm in winter and cool in summer,” says Dean.
Catering for goats
Dean and Ang say they were advised that milking goats run outdoors are more subject to worms and sore feet than those housed in a barn.


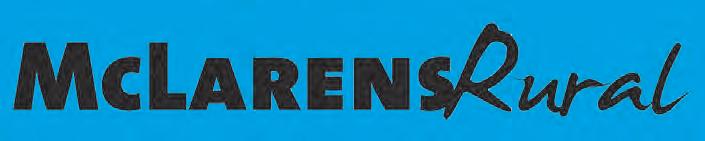
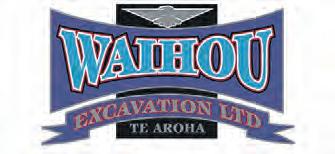
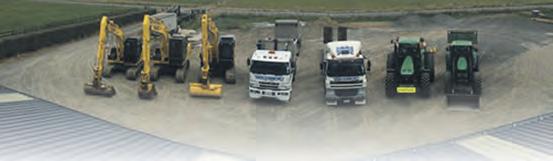

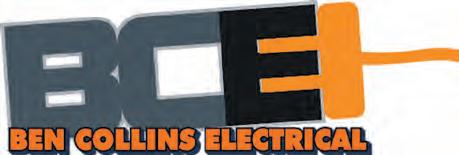
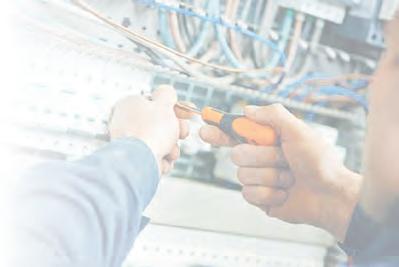
Proud Service Partner of:
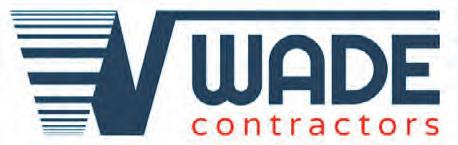



The nerve centre of the operation – pit and bails – including feed dispensers. The Fawde F56 generator supplied by Invercargill-based Cowpower.

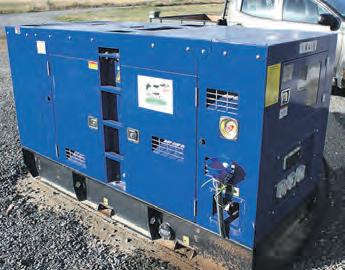
Goats have a nice runway from the milking shed back to their barn.
The Baby Barn. Goats have easy entry and exit between the milking parlour and barn. A view down the 50-aside pit.
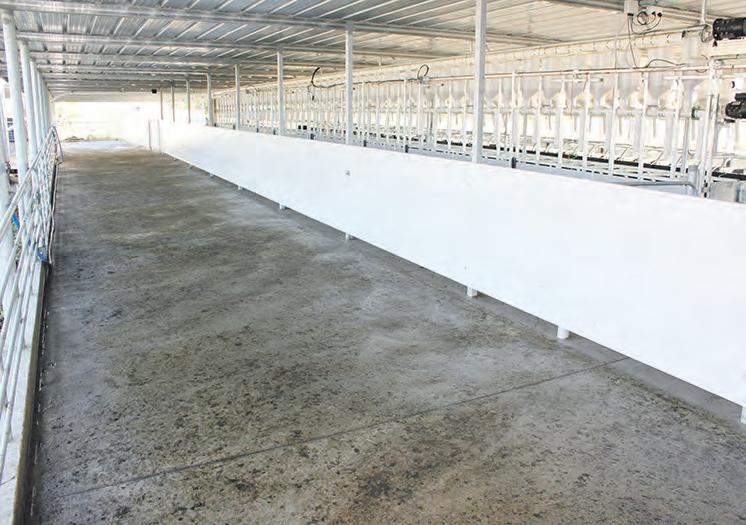
Milk production is also reportedly higher from an indoor herd.
“Most milking goat herds are now kept housed indoors,” says Dean.
The goat barn has three concrete laneways for feed-out purposes, with maize and barley dished out into troughs in front of the pens.
Crushed sunflower seeds and pellets are also fed individually in the bails of the milking shed.
Ang says the herd is predominantly Saanen, a white Swiss breed, and British Alpine.
Morrinsville-based McLarens Rural Services installed the entire milking plant “from goat to vat”, says director Tony McLaren.
He says it is similar to a dairy cow operation, except for the speed of the pulsators and smaller/lighter claws.
Tony says his company also handled all water works including the washdown, cooler and chilled water pumps.
A pressure pump was installed for the shed toilet and handbasins, while they also supplied and connected the hot water system and wash system for the vats.
The complete milking system was supplied by GEA Farm Technologies.
GEA area sales manager Paul Convery says this included a 1000 litre washtub in the milk-room, plus associated milk cooling and filtering equipment.
Paul says this is all controlled in a networked system in the milk-room and pit by a single switch.
In the pit, GEA also provided the milk receiving tank and sanitary trap, along with the clusters and pulsators. Pneumatic bails
Paul says a feature of the Toa Road project, from a GEA perspective, is the manufacture and installation of the pneumatic bail system.
Paul says this is the same system GEA supplied to Dean and Ang Finnerty for their Paeroa-Tahuna Road operation.
Wash-down programmes and systems at Toa Road, including associated dairy detergents, were set up and supplied by GEA’s subsidiary FIL.
FIL Area Manager Mark Mohring says his team worked with GEA and McLarens on the project.
The GEA iNTELWASH system controls the amount of FIL alkali, acid and chlorine used in wash-down of the milking plant and vat.
Mark says specifications are based on all aspects of the operation including shed/herd size and water supply/quality.
The plant wash is automatically programmed to activate after each milking, using a regulated amount of chemicals, with a cold rinse followed by a hot wash.
Mark says the vat is similarly washed after each collection, with the system activated by the tanker driver.
Feed systems, serving both the milking shed and barn, were supplied and fitted by BCL Feed Systems (Buster Cover Ltd).
Foreman Bill King says this involved two 16-tonne galvanised iron silos, with associated auger systems.
Tailored to suit
Feed for the barn is conveyed straight into a feed-out wagon, while the milking shed system has the meal/grain piped to individual dispensers in the bails.
Bill says when each row is released after milking, the feed bins are re-filled in the fully automated system.

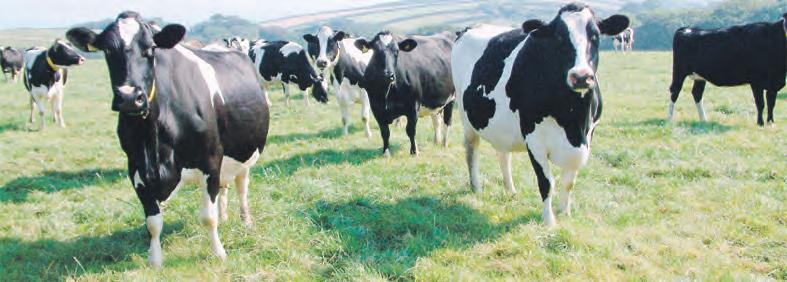
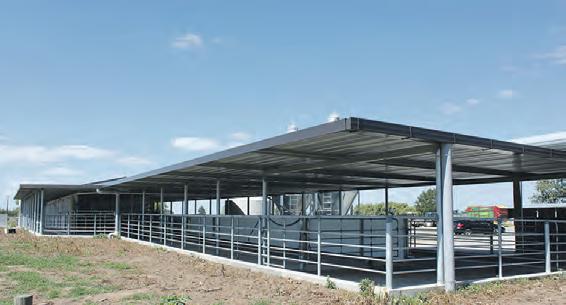

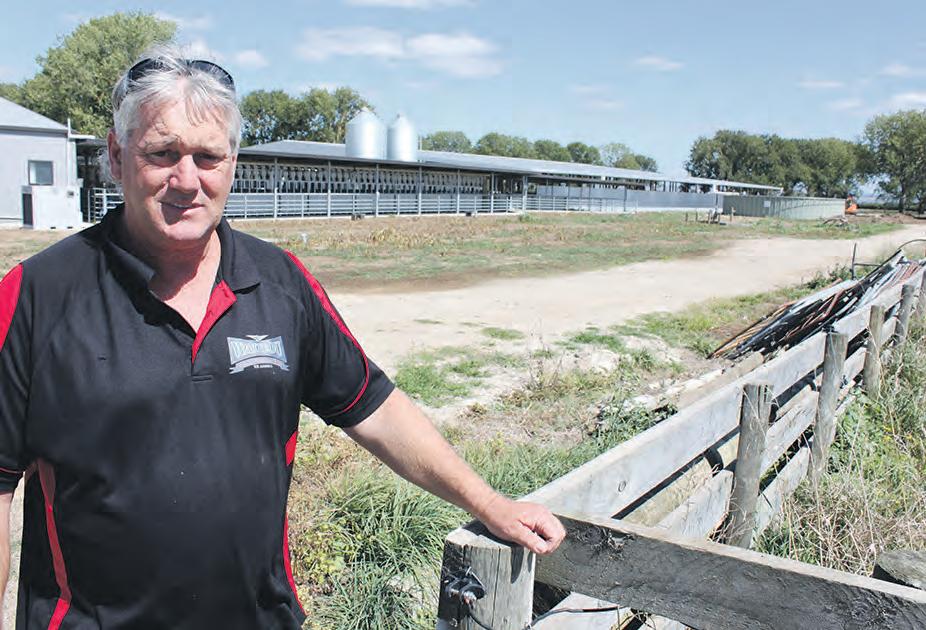
Waihou Excavation owner/operator Frank Teague.
GEA Farm Technologies’ area sales manager Paul Convery in the pneumatic bails. Buster Cover director Talya Raumati with feed enjoyed by the goats during milking. FIL area manager Mark Mohring checks out the dairy detergents.
Ang and Sharon Finnerty in the Baby Barn.
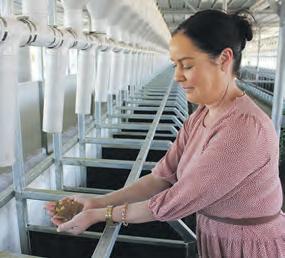
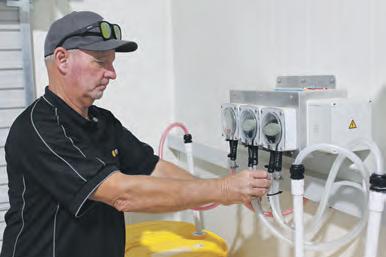
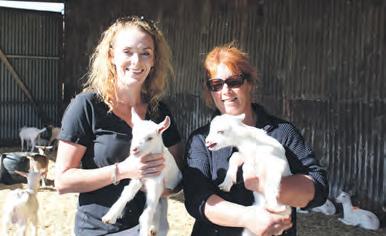
Bill says the equipment was all built in the company’s workshop and erected on-site.
Dual purpose
A 350,000L tank, supplied and installed by Tauranga-based Kliptank, serves a dual purpose in the Toa Rd operation.
Kliptank business development manager Fiona Birchall says the tank catches roof water from the barn and also stores effluent when irrigation onto farmland is not possible due to wet weather.
Built on site on a sand base, the 13.75m diameter tank was tailored to suit the Toa Rd operation, says Fiona.
The structure is made of high-density polyethylene (HDPE), bound by galvanised wire ropes, on an aluminium base.
Fiona says a top ring holds the liner in place and stabilises the tank while allowing it to move in relation to any seismic activity.
The one millimetre thick liner is made of flexible polypropylene (FPP), and Fiona says Kliptank also supplied associated piping and taps.
Getting the entire area ready for the new milking shed and parlour was undertaken by Waihou Excavation.
Owner/operator Frank Teague says the site of the former cowshed was excavated, with 900 millimetre of soil removed, and backfilled with sand from the farm. Generator power
The goat barn was built on a green-field site stripped out by Waihou Excavation, with the company also completing earthworks required for the surrounding yard/vehicle turnaround area.
Frank says the footprint of the Toa Rd facility covers about 1ha.
The site – milking shed and barn – was initially powered by a generator, while the regular supply was being connected, and this remains on site as a back-up.
Company director Barry Hayes says the capacity of the generator was dictated by the size of operation and hours of use.
Cowpower supplied a Fawde F56 model, made in China.
Barry says a flick of a switch will have the Toa Rd operation, including the milking system, up and running again within a minute of a power outage.
With waterproof sockets and a baked enamel coating, the generator can be sited outdoors and is portable.
Ang Finnerty says while the generator was only used for about a month while the regular power supply was connected, it remains a back-up for the Toa Rd operation and can be transported to the other family farms if required.
Connecting
All on-site electrical work was undertaken by Te Aroha-based business, Ben Collins Electrical.
Ben says providing a connection for a generator to a milking shed is required to meet compliance standards in all new-build projects.
Involved in the Toa Rd project from the outset, he initially jacked up the builders’ lights, then the generator and finally the regular power source as construction progressed.
This included from the road-side power pole to the farm milk/plant room and pit/bail area, plus the associated vat and barn.


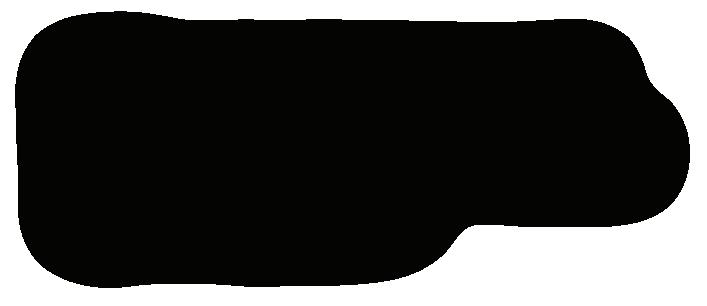
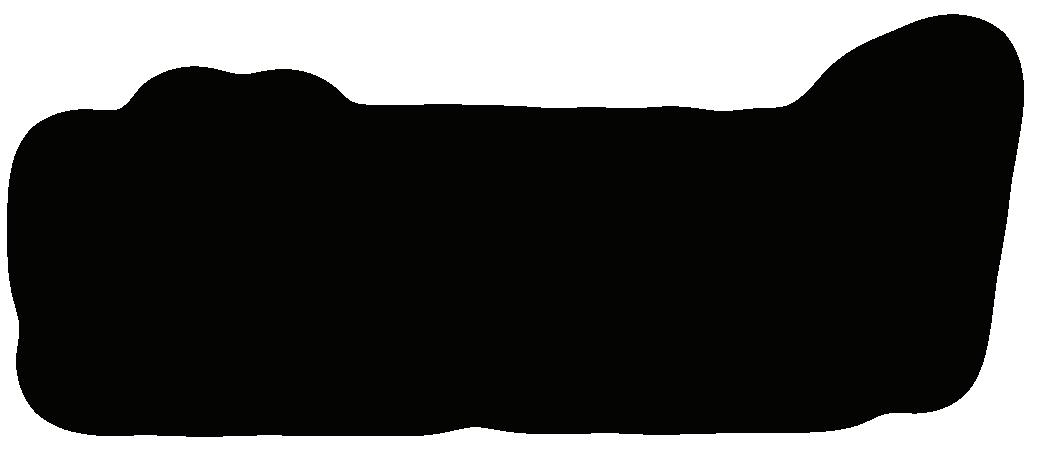
CAN YOUR BUSINESS SURVIVE WITHOUT POWER?
Ready to go on delivery Any size of generators (1kw - 400kw) anywhere Cowpower Generators have 100’s of happy customer Be one of them!