
9 minute read
Alexandra Road Farms Waikato
by Sun Media
Steve Edwards
The milking goats are fed pasture cut from the home farm.
A trans-Tasman chicken company has spread its wings into dairy goat farming in the Waikato.
Agright GP, almost 50 per cent owned by managing director Daniel Bryant and 15 per cent by his father Max, last year established a 3000-goat milking operation near Matamata.
The 164ha property on Alexandra Rd, previously used for dairying and latterly commercial potato cropping, also features a large-scale chicken-growing facility.
Daniel Bryant, who bought the property in May 2019 for chickens primarily on 21ha, says he looked at a range of projects for the surplus land.
The goat milk – up to 10 million litres a year – is processed at the Waikato Innovation Park dryer in Hamilton and sold directly to the open market.
Daniel says the goat business has created 15 full-time jobs and another 20 part-time roles during kidding.
By hand
Baby goats are hand-reared and hand-fed.
The Bryants debuted in dairy goat farming via a deal with New Zealand Dairy Goats, founded and chaired by Duncan Milne.
NZDG is also a new company and headed by Milne’s son Robert.
Agright acquired a nearly 24 per cent stake in NZDG, set to rise to just over 30 per cent by mid-2022 once the second goat barn is operating.
Daniel says Agright sold NZDG land in exchange for 23 per cent, or 3.7 million shares, and cash. NZDG has the option to acquire more land in exchange for further shares and cash, which should happen by June 2022.
On-site earthworks at Alexandra Rd started in March 2020 but were interrupted by Covid.
However, Daniel says a real drive by the respective contractors saw the first milking in mid-October.
The build
The building project was led by Te Awamutubased Gibson Construction.
Director Blair Atkinson says his team went on-site after lockdown lifted, erecting an 80-bail rotary milking shed.
This included entry and exit bridges, along with a plant room, office and staffroom.
Blair says the milking facility covers 960 square metres, with the first of the adjacent goat barns creating a footprint of 14,000 square metres. Gibson Construction provided design and build for the project, says Blair, including piping, railing and roofing work. The design was undertaken in conjunction with Daniel Bryant and project manager Shaun Murray. Blair says the brief was to provide a nice, open shed.
This was the biggest farm job the company had ever undertaken.
Shaun Murray says the initial 3000 milking goats was split into six herds. This will double, with another barn built and separate milking parlour planned.
“We will be a commercial operator in our own right.”
Shaun says the key to the milking shed design is low labour input.
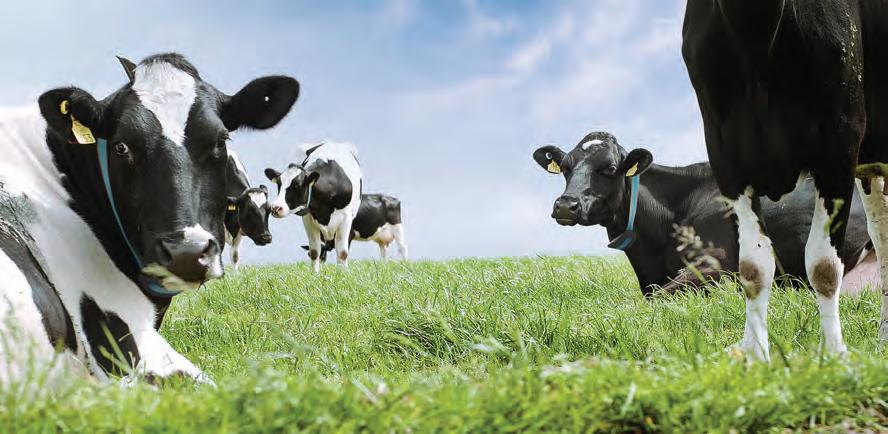

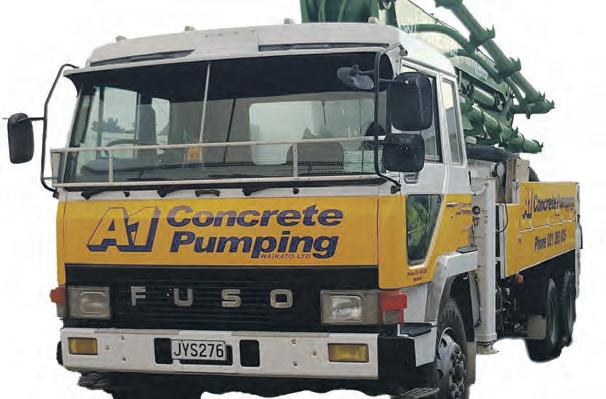
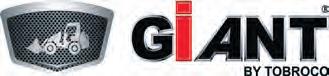

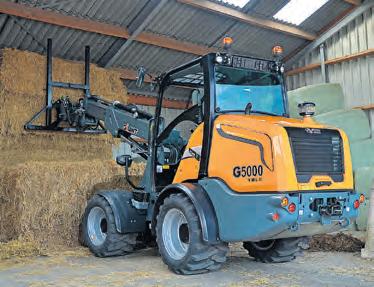
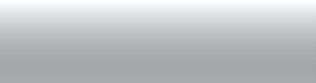
Three entrance points were created onto the milking platform, giving better flow to the bails. Blair says he had seen this in other goat milking sheds.
Indoor lifestyle
The goats are kept indoors all year round, with 130ha of the property devoted to growing pasture for feed.
Blair says the barns allow for three square metres per goat, as per industry standards. “Animal welfare is our top priority.”
There is a 10-hour split between milkings and Blair says the goats, all yearlings, produce between 90kg and 160kg of milk a year.
Matamata-based Mark Wilcox Builders laid the concrete – about 3500 cubic metres in total.
This included the milking shed and tractor lanes – 3 x 186m long – in the barn. Director Mark Wilcox says his team also laid the pad – 70m x 15m – for a tractor turnaround area associated with the barn.
Concrete pumping was undertaken by Hamiltonbased A1 Concrete.
Director Quin Abraham says he worked with Mark Wilcox and liaised with the concrete supplier.
A1 used a boom with a 42m reach on the concrete pump.
Quin says staff were often on-site from 1am to 10pm the following night.
The operation was powered up by King Electrical from Matamata.
Director Jeremy Kidd says they worked on the barn first, including milk mixing equipment and lighting.
Wired up
In the milking shed, King Electrical wired the rotary platform and plantroom, including vacuum and hot water systems, plus chilling systems for the vats.
Completing their part in the project, Jeremy says staff completed wiring for the farm’s effluent management and irrigation systems.
The milking plant, plus water and effluent systems, were supplied and installed by Qubik.
Operations Manager Jeremy Collett says this included milking machines, pulsators, milk pumps and lines on the platform and in the plant room.
Outside the milking shed, the company had a hand in the refrigeration systems for the two 21,000L vats, which feature automatic washers.
Jeremy says the feed system Qubik supplied and installed included three 16 tonne silos, with an auger system carrying meal to dispensers on the milking platform.
Qubik Water Technician Karl Hart says three pumps are used to provide drinking water and washdown water to the operation.
He says Qubik also supplied and installed effluent management and disposal equipment for the barn and milking shed.
A screw-press separator removes solids, with material ultimately irrigated onto pasture after passing through a series of sumps, stone traps and a mixing trap.
The in-shed milk monitoring system was provided by Hamiltonbased Halo Systems using Tag IT technology.
Halo sales executive Sean McChlery says the system tracks milk from the udder to the vat.
If a problem develops, a text and email alert is sent to farm staff.
“This eliminates human error and equipment failure,” says Sean.
With a central control box in the shed, he says the system monitors milk flow and volume, plus water (drinking and washdown).
The kitset milking platform was erected on site by Matamata-based Moa Rotary Platforms.

Milking cluster technology supplied by Waikato Milking Systems.
Milking time at the Alexandra Rd operation.
Entry/exit ramps make for a smooth flow in the milking shed. Looking out over the yard at the Alexandra Rd complex.
Te Aroha Tractors & Machinery sales manager Steve Workman with some of the freshly cut pasture used to feed the milking goats.
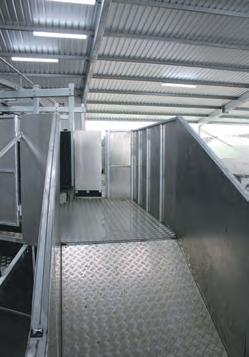
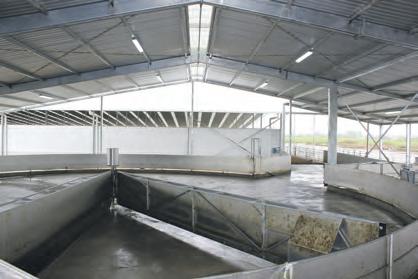
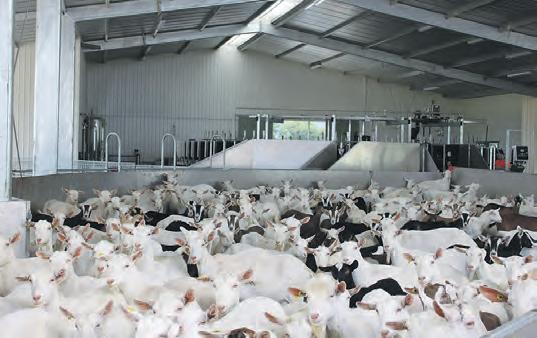
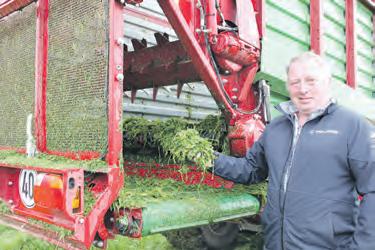
Feeding time at Alexandra Rd.

Milking Systems
Effluent Management
Refrigeration + Water Reticulation
Milk with confidence
Oubik are proud to have supplied and installed the new goat milking system, water reticulation, effluent system, refrigeration and pre-cooling system for New Zealand Dairy Goats.
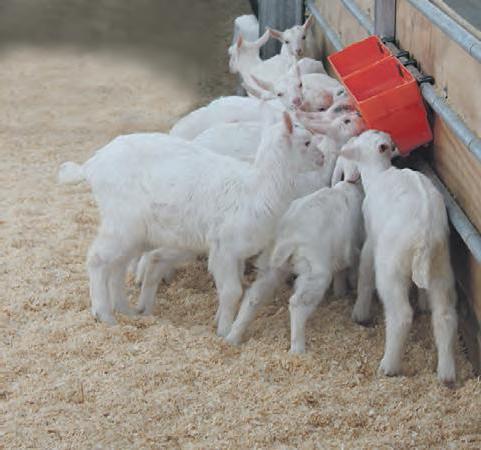



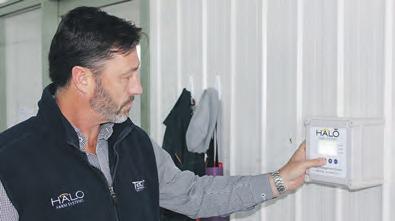
Halo sales executive Sean McChlery checks out the milk monitoring system. Carl Jeffries, from King Electrical, in front of the new switchboard.
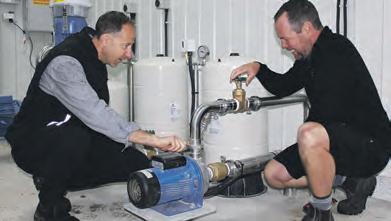
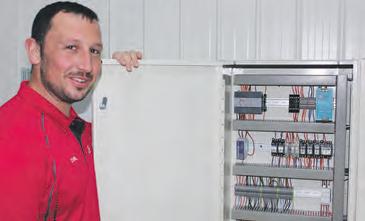
Qubik water technician Karl Hart, left, on site with operations manager Jeremy Collett. Moa Rotary Platforms director Shane Arthur, left, and Waikato Milking Systems’ general manager of sales and operations Grant Wisnewski.
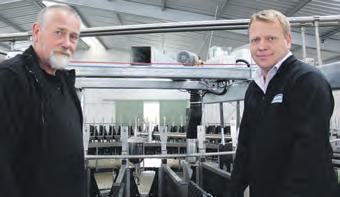
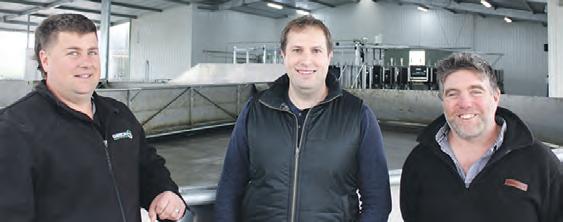

Mark Wilcox on the yard his team laid.
Gibson Construction director Blair Atkinson, left, with New Zealand Dairy Goats CEO Rob Milne and farm operations manager Shaun Murray.
Director Shane Arthur says his company’s part in the project came after the concreting was completed and roof in place.
Working with Waikato Milking Systems, Shane says they put together a steel frame and deck, with four-bail sections, plus entry and exits from the platform.
“The goats walk on the platform and back off when finished,” says Shane.
He says the 80-bail rotary can get through 500 goats in 45 minutes. Milking technology
Grant Wisnewski, general manager of sales and operations for Waikato Milking Systems, says his company also supplied the milking cluster technology, including automatic cup removers, teat-spray and auto wash.
Goats are identified, and milk volume recorded, during milking via an electronic eartag system.
Grant says the system has a central control box overseen by staff near the milking platform.
Information is stored electronically in the farm’s computer system.
The milking goats are fed a mixture of grass from the home farm, plus pellets and hay in troughs at the front of their enclosure, with concrete tractor lanes developed for delivery.
Associated vehicles were supplied by Te Aroha Tractors & Machinery.
Sales manager Steve Workman says a “cut and carry” system is used, with his company supplying a front mower (for a tractor) and feed-out wagon.
Te Aroha Tractors & Machinery also provided Polaris electric 4 x 4 vehicles used by staff in the barn to deliver pellets and hay to the goats.
Steve says the vehicles are quiet and environmentally-friendly.
Northpower was also involved in works associated with the new goat milking operation on Alexandra Rd.
Pat Watson, project delivery manager for Northpower, says works related to installation of new poles, lines and a transformer to supply power to the goat farm.
Actual works that were included were installation of 12 x 11m concrete poles (this incorporated crossarms, insulators and new power line or conductor) to a shiny new transformer situated on the property. Kilometre span
Pat says the pole and line installation spanned one entire kilometre of overhead line works as well as a 500kVA transformer with two circuits.
One circuit supplied the feed to the new goat sheds and the other circuit supply was to feed a submersible pump (enabling water to be pumped around the site location/farm including the chicken sheds).
Pat says a 500kVA transformer installation provided the supply necessary for the goat farm and pump connections.
He says King Electrical supported Northpower’s field resources by installing the site metering and service mains.
Daniel Bryant says goat milk, like sheep product, is naturally A2 and is pitched at lactose-intolerant consumers as well as the infant formula market.
Agright started life as ProTen, a small chicken business founded by Max Bryant in Feilding 20 years ago.
ProTen went on to become a major player in the chicken business in Australia.
Proceeds from its later sale have been ploughed back into the Alexandra Rd operation via Agright.
Daniel says the goat opportunity came up as the company was looking outside the realms of dairy farming.
“We looked around and settled on the Waikato. It has expertise in the area, with staff, vets and builders,” he says.
“We found the money and found the right people,” says Daniel. “Twelve months later – including Covid – we were milking.”
He says the Alexandra Road project has “certainly been some journey”.
“The stars aligned.”
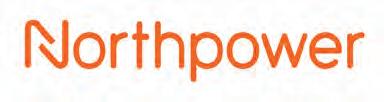
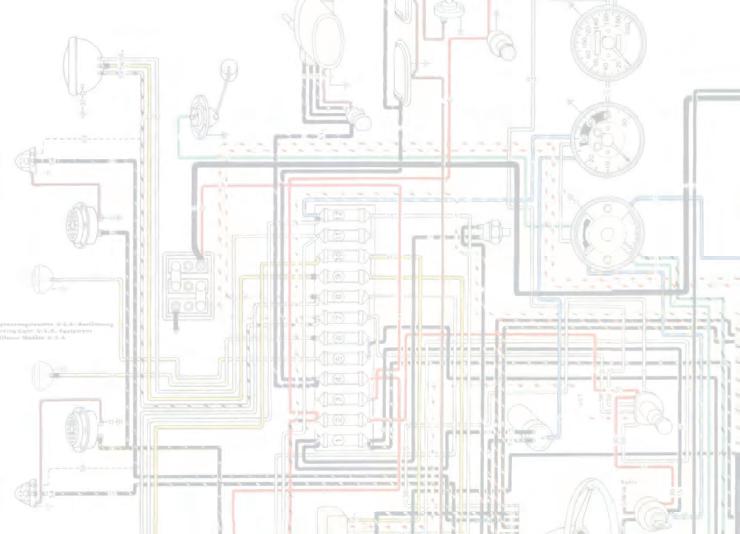
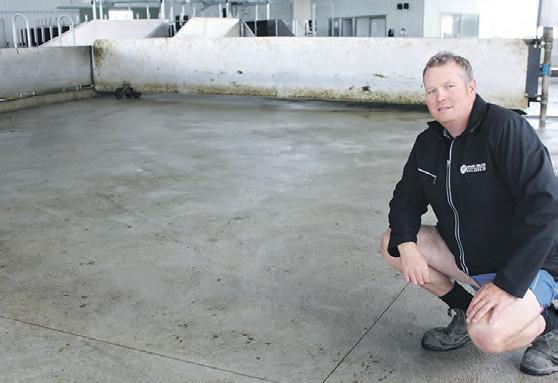
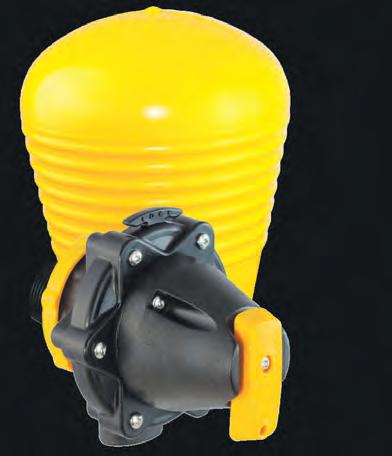