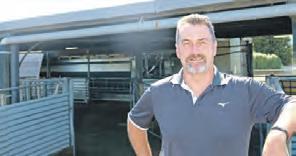
16 minute read
Schuler Sheep Waikato
by Sun Media
Farm overseer Keith Arnold. Grant Coburn, from GEA Farm Technologies, checking out the high-tech goat milking/ research system. FIL Te Awamutu and Otorohanga area manager Colin Ranby looking over the teat care system his company provided. Happy in his work: Josh Kane from King Electrical in Matamata.
Milk ‘n’ Water Services – Matamata milking machine technician Peter Taylor with the new clusters.
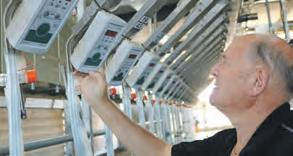

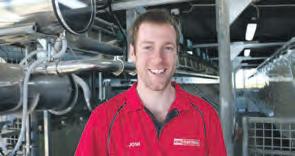
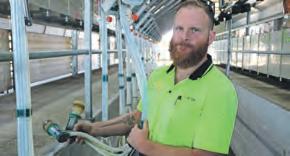
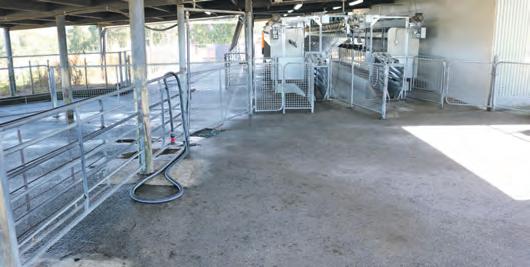
installed new clusters and cup removers, milk metering and pulsators.
Peter says the company also assisted GEA Farm Technologies in the animal identification system, with the yard upgraded to suit. This included RFID reader in-bail entry, he says.
Peter says Milk ‘n’ Water Services Matamata installed a sanitary trap in the Pukeatua shed, hooked up the compressed air for the bail system and plumbed in the teat-wash.
The company also plumbed-up the secondary milk vat.
Keith says stairs were changed to extend the pit length and better accommodate the new clusters. The milk-room basically remained the same, with the addition of a new air compressor.
A new IntelliBlend teat spray system was provided by GEA FIL.
FIL area manager for Te Awamutu and Otorohanga, Colin Ranby, says the system involves automatic mixing and delivery of an iodine-based teat spray and emollient. Teat spray
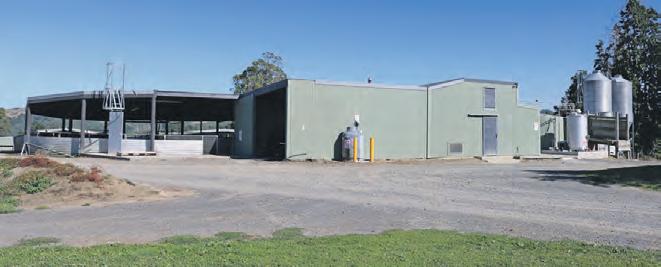
The ratio is computer-controlled, with material pumped directly to the pit from three drums – 200L Iodoshield Active, 100L Active Teat Conditioner and a water reservoir.
Colin says a drag hose in the pit is used to convey the spray after each goat has been milked.
An audible alarm notifies farm staff when drum contents are running low, he says.
Colin says the system is easily programmed to add more emollient as required through seasonal changes or when a deterioration in teat condition is detected.
Matamata-based King Electrical ‘gutted’ the existing goat milking operation’s Feeding time in the goat barn.
electrical system in order to upgrade it.
Electrician Josh Kane says in the bails this involved all power requirements, including control boxes, relating to the advanced milk sampling/metering technology used.
“This is the main brain of the system,” says Josh.
King Electrical also upgraded lighting in the milking shed and wired up the new in-bail feeding system.
Their work in the yard also included electrical requirements for water reticulation and associated washdown controls.
In the plant room, Josh says King Electrical was responsible for powering the new teat-spray operation, air compressor and vacuum pump.
The company also changed electrical controls for the water pump and vat wash system, while recommissioning the ice bank and refrigeration system. Goats have plenty of space in the “scaled back” operation.
Josh says King Electrical wired the chiller unit and vat wash pump for the secondary milk vat, along with providing power to the farm office computer.
Keith says physical work on the existing shed centred on lifting the roof to accommodate the rapid exit and in-bail feeding systems.
Existing barns, with associated feeding systems, are used in the Arapuni Rd operation.
The first milking in the revamped facility was undertaken on August 15, 2020.
Keith says the Saanen herd is milked twice a day, with three staff engaged.
Originating from the Saanen Valley in Switzerland, this breed is acclaimed as the most popular and highest producing milking goat in New Zealand.
Processed at the DGC’s Hamilton factory, milk from the Pukeatua property is destined to become infant formula.
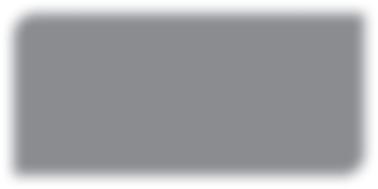
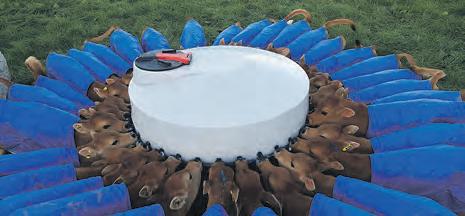
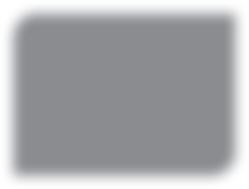

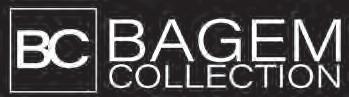
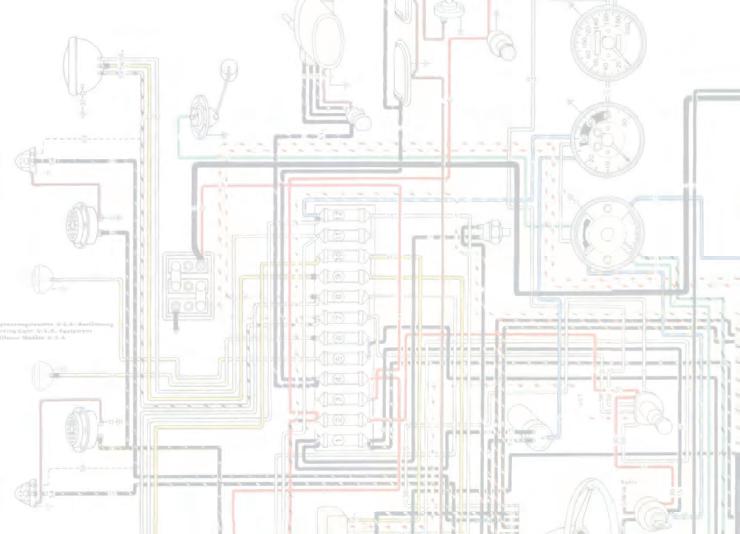



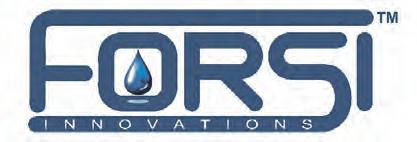
Clare Bayly

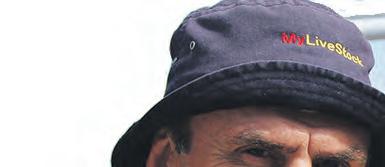
Kevin Schuler has cause to smile after a successful first season milking sheep
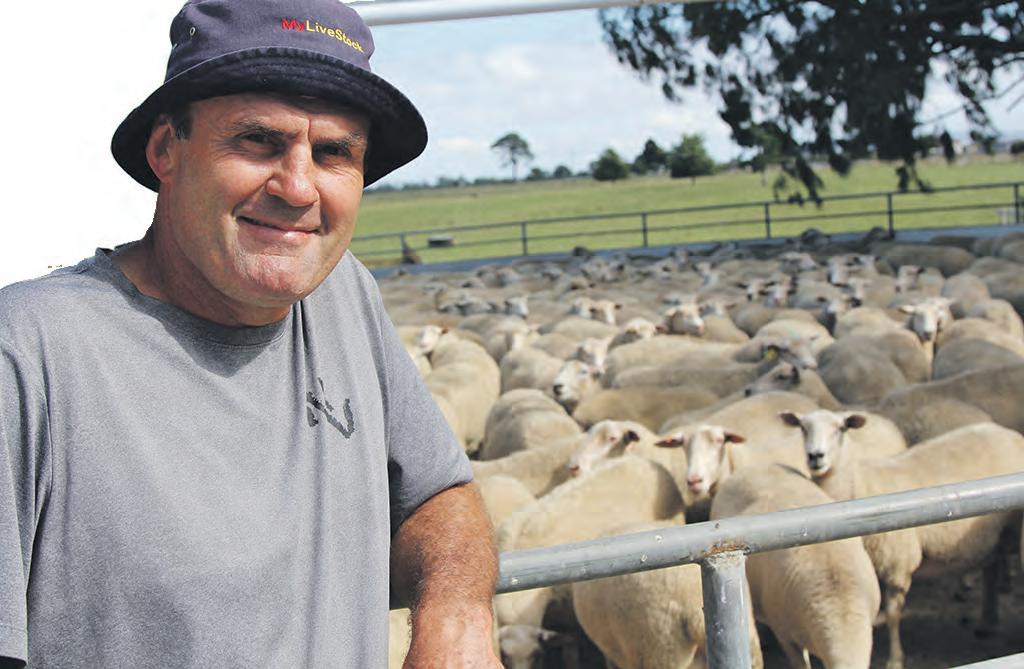
Schuler Brothers’ dairy farms at Te Aroha West showcase dairy diversity, with the brothers milking three animal species across the 234ha farm property which has grown around the family farm purchased by their grandfather in the early 1900s.
“The original farm was 40ha,” Kevin Schuler recalls, “and over time the family acquired neighbouring farms as they came on the market to make up the current 234 (215 effective) hectare property.”
The increased scale of the farm has provided the ability to diversify. Once all bovine dairy, today Kevin and Paul Schuler and their team of nine full-time staff now milk 350 cows on 105ha, 1,400 goats on 70ha and, in 2020, 650 sheep. In addition, 45ha of lease land supports the platform.
Kevin admits he and Paul have always enjoyed being on the cusp of change.
“We could see the potential for goat milk when we got into that industry around 2012 and similarly for sheep now. The working side of the refurbished sheep dairy showing the entrance yards leading to the 600 sheep collection yard.
“Diversifying our income stream and creating strong cashflow has always been important to avoid the volatility which accompanies prettymuch every sector of agriculture.
“Being early adopters carries risk, but also reward and hopefully our learnings will benefit other farmers who join later.”
Cut back
Developing a sheep unit saw the brothers retire 40ha which had been used as cut and carry for the goat farm.
“We have cut back on cow numbers over the years. From 850 we cut back to 500 when the goat farm started and then reduced to 350 in the 2020 season to accommodate the sheep. Next season we will increase sheep numbers to 1,000 and pull back goat numbers to peak milk around 1,250 which is more in line with our quota.”
Kevin Schuler said the three farming businesses are separate but, thanks to contiguous land boundaries and supportive management, the farms work collaboratively “cutting and pasting” people from one team to another as required to meet seasonal demand. “The units are great at helping each other out and enjoy the variety and opportunity to gain unique multi-species experience.
“One fundamental to achieving efficient use of resources across all three farming businesses was avoiding the pinch-point of three species calving, kidding or lambing at the same time. We moved the cows from spring calving to autumn to qualify for the winter milk premium. It’s been a popular move with the team, who are revelling in calving during late summer as opposed to early spring. We don’t rear replacements to be brought into the herd, instead buying in spring empties from high BW herds.
“Originally, on the goat farms, we kidded in late June but, with the sheep lambing in late July, we will this year bring kidding forward to the start of June.
Kevin and Paul Schuler supply Maui Milk, which supplied the herd of 650 milking sheep, a mix of hoggets and mixed age ewes.
Locked down
Planning for the dairy sheep conversion began at the start of 2020. Within weeks of Kevin and Paul meeting with Qubik’s Nick Heffer and builder Matt Walker, New Zealand went into lockdown to prevent the Covid pandemic and the project halted.
“Site development was effectively delayed until we were out of lockdown, meaning the shed was not fully operational until the end of September and milk collection only commenced in October.
“We decided to recommission an old cowshed rather than start from scratch. There were several old sheds on the farm to choose from and the one we selected was well-situated on the area allocated for sheep. Although it hadn’t been used for a number of decades it was structurally sound (apart from the derelect dairy) and the yards were in good condition,” says Kevin.
Milking Systems
Effluent Management
Refrigeration + Water Reticulation
Milk with confidence
Oubik are proud to have supplied and installed the new sheep milking system, water reticulation, effluent system, refrigeration and pre-cooling system for Schuler Brothers Ltd.
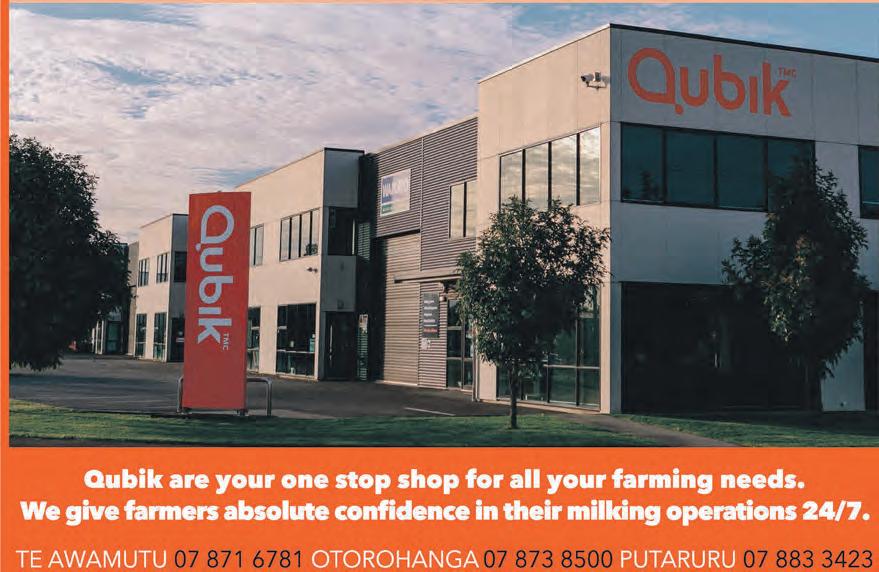
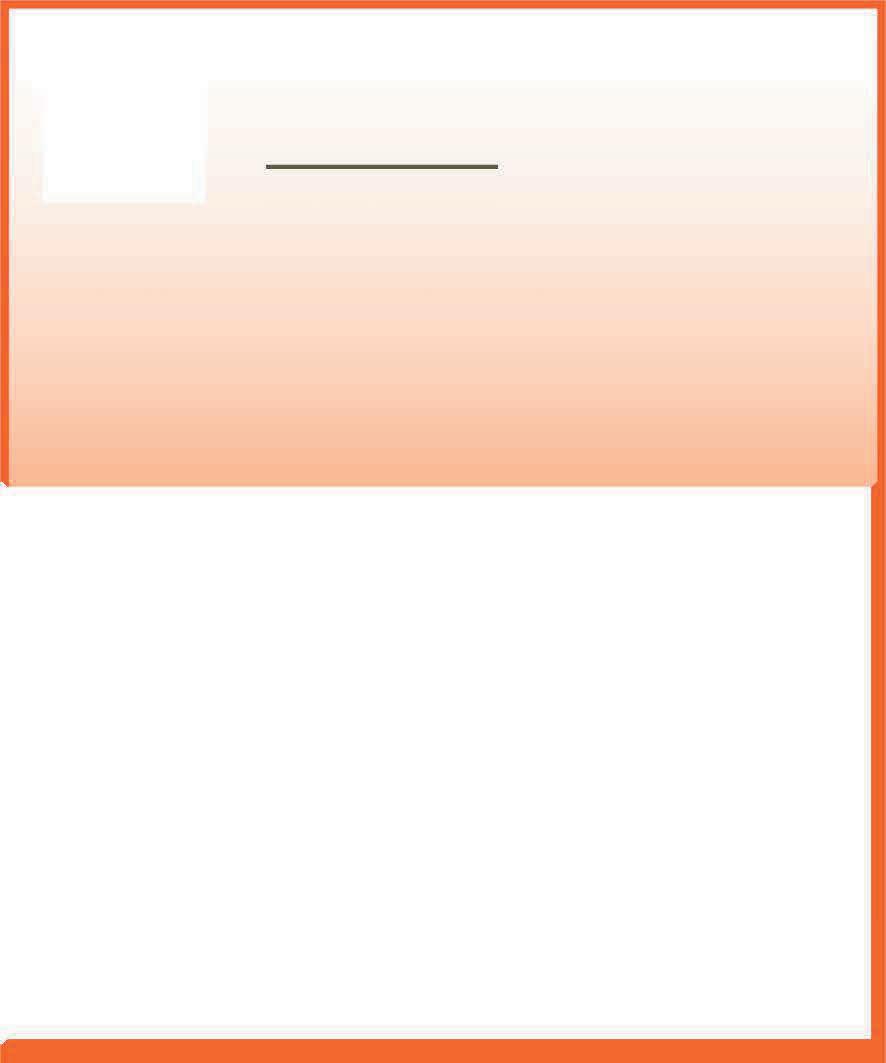

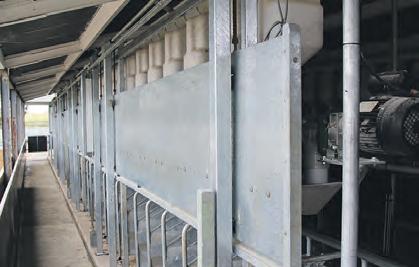
The Waikato Milking Systems AGILI Sheep Rapid Exit Milking Solution has been customised so the Rapid Exit Gate can be used in two sections, providing split-row release to maximise sheep flow. Looking down one of the rows with the bails and feed dispensers to the left, and clusters to the right. The 1.1m wide pit means that milker Sami White is in touch with sheep on both sides of the herringbone.
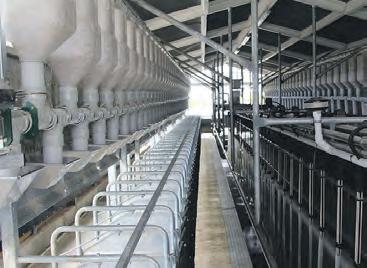
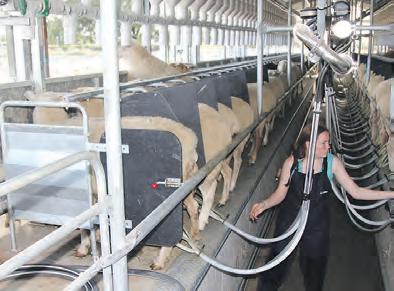
Kevin Schuler attaching clusters in the refurbished dairy.
Builder Matt Walker recalls the initial plan was to convert the herringbone to a 32-aside sheep dairy based on the length of the old pit. “But we subsequently extended the roof by two bays allowing the pit to be extended to 40-aside to shorten milking time and future-proof the shed for planned growth.
Cows to sheep
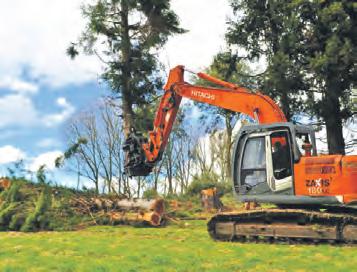
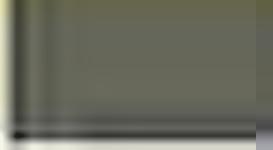
“Modifying a herringbone from cows to sheep calls for an adjustment to the floor of the pit to position the milker at the optimum position for cluster attachment. The roof was in good condition and the ideal height for the rapid exit system so we didn’t want to raise the level of the bails, instead opting to lower and, at the same time, narrow the pit to 1.1metres so that milkers could simply turn to attach clusters on the other side,” says Matt.
Matt’s team developed a new dairy comprising a kitchen/staff room, bathroom complete with shower and toilet, office and milk room. The new section features poly panel exterior cladding. The interior of the original shed was concrete block which was continued Specialising in • in the extension. Removal / chipping of whole trees • On site chipping for stand off pads • Wood chip for sale • Orchard shelter removal • Stump removal • Woodlot marketing of all tree species

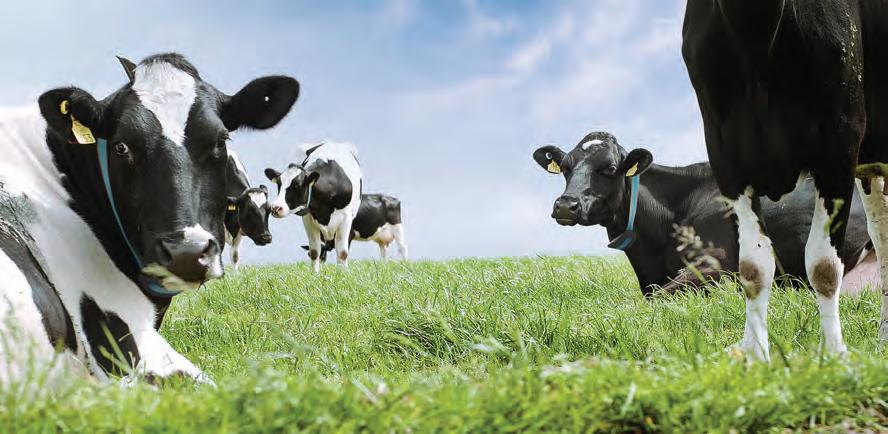
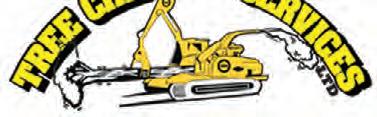
Some of the team behind the conversion of a 40-year-old herringbone to a modern, efficient sheep milking dairy. From left BCL’s Jamie Haupapa, builder Matt Walker, Waikato Milking Systems Dave Cassells, BCL’s Bill King, farmer Kevin Schuler, Qubik’s Morgan Keighley, Andrew McAllister and Nick Heffer.
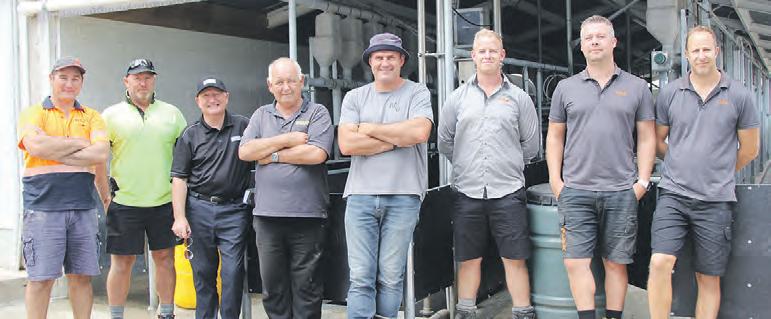
The existing yards were in good condition but needed sheep proofing with the rails modified to take sheeting. This was undertaken by Waihou-based Rural Engineering which specialises in welding and general engineering maintenance, modification and new construction for the wider agricultural sector. The Rural Engineering team also constructed and installed new entry and exit rails and erected the herringbone frames to take the milk lines in the dairy.
Kevin and Paul decided on a 40-aside Waikato Milking Systems AGILI Rapid Exit Sheep Milking system with a self-indexing gate that automatically allocates sheep into individual stalls.
The Rapid Exit features a split-row release which optimises sheep flow through the parlour.
The 40-aside system runs smoothly and efficiently, enabling two people to milk 600plus sheep in about one hour.
Milking
A BP200 Blower vacuum pump with a Variable Speed Drive supplies and controls the vacuum level during milking.
The milking machine includes Waikato Milking Systems sheep clusters with auto shut-off and the company’s electronic pulsators adjusted specifically for milking sheep.
A feature of the Rapid Exit is the milk recovery system. When activated, it ensures most of the milk is recovered from the delivery line and moved through into the bulk storage tank at the end of each milking.
Qubik installed the Rapid Exit parlour and supplied a Fristam rotary Lobe milk pump which adds real value to the milking operation. It’s simple, reliable and its design ensures milk is transferred from the plant to the vat efficiently, providing a premium product every milking.
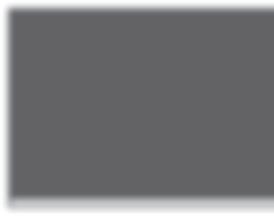
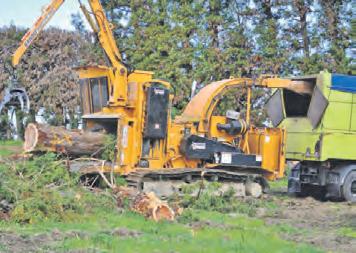

Specialising in

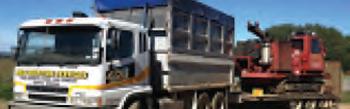
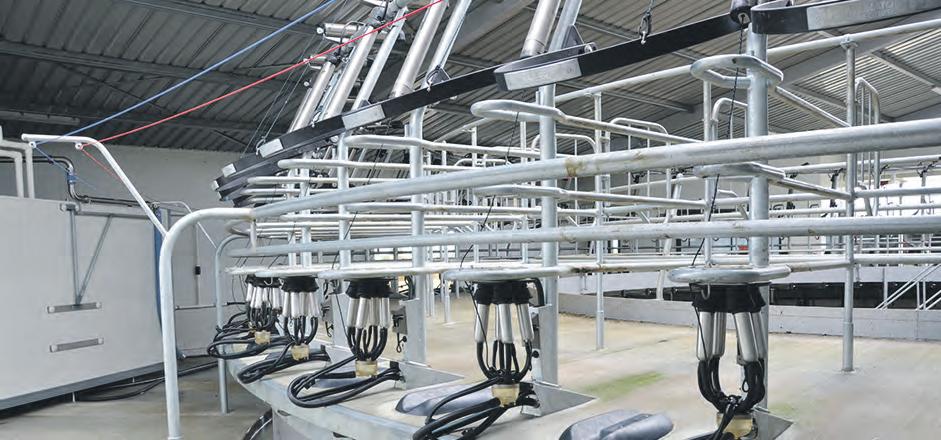
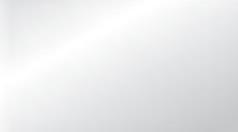

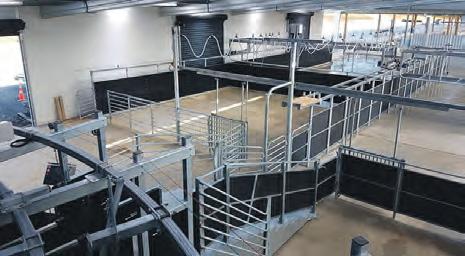

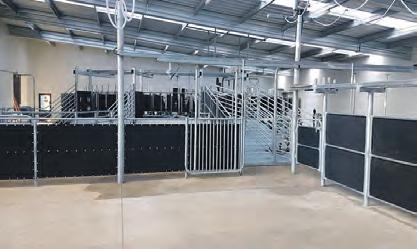
Rural Engineering Ltd Rural Engineering Ltd
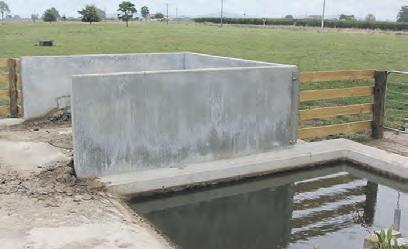


Proximity to the Rail Trail supported installation of a Flexi Tank bladder to store effluent over a pond.
BCL’s shed fitter/installer Jamie Haupapa, checks the dairy’s new feed dispensers.
Qubik also laid 750m of new water line to enable connection to Te Aroha’s town water supply.
Doing this was important to ensure the best quality water was available for plant wash and dairy hygiene.
Ben Collins Electrical upgraded and installed the new electrical circuitry for the renovated dairy. Based in Hamilton and Te Aroha, the company provides electrical support and services across the greater Waikato area, delivering continuity of supply with a 24 hour call-out service.
Specific treatment
The quantities and viscosity of sheep effluent requires specific treatment and Qubik designed and supplied a system which features a stone trap and effluent holding tank. Effluent is separated using the stone trap, before gravity feeding to a 25,000L sump tank. The Mono
Effluent Pump 2-Stage 7.5kW and Kelco pressure guard pumps the effluent to the holding Flexi Tank bladder or straight to pasture depending on the season.
A Flexi Tank was obviously the best solution for the Schuler Brothers’ situation that suited all aspects of their farming operation, says Flexi Tanks NZ owner Jacky van der Poel.
“The beauty of the Flexi Tank System is that the Schulers have been able to add to the system as they have grown, using one 500m3 tank initially for both dairy and goat and then adding the second 300m3 tank in for the goat operation,” says Jacky.
“Being an enclosed system, they have been able to keep the rainwater out of the system and will enjoy the benefits of a 25 per cent depreciation rate, making it a very sensible infrastructure investment.”
Paeroa Farm Services installed a washdown system with PVC mains water lines, primary
The spacious new milk room. The sheep are eager to go into the shed for milking. The BCL 16 tonne silo.
Industrial Plate Cooler water system, dairy water supply system with new water pump, and hot water for the plant wash. The bore/ well system was linked to water reservoirs and a sheep farm reticulation system is being developed to futureproof the farm’s stock and dairy water needs.
Sheep milk needs to be maintained at four degrees or less, entering the vat at a lower temperature than cows due to smaller volumes and required quality. Qubik supplied and installed a new 10kW Glycol system that snapchills the milk before entering the milk vat. Once the milk has entered the vat, the milk temperature is maintained by a 8hp vat chiller unit. This system meets MPI and Maui Milk regulations but is also future-proofed should there be regulatory changes in the future.
Buster Cover (BCL) designed, manufactured and installed the feed dispensers and trickle feed system in the new dairy. The dropdown bins, which hold up to 4kg of feed, are powered by compressed air and are identical to those used for cows and goats with the exception that – in sheep and goat dairies – they are mounted more closely together. When the rapid exit lifts, the feed system refills the feed bins for the next row of sheep. Feed is stored in a 16 tonne silo, augers delivering it to the dairy with secondary auger lines delivering the feed into the individual bins.
The unknown
Looking back at the first season supplying milk to Maui Milk, Kevin recalls it was a bit like stepping into the unknown milking sheep.
“We didn’t have direct experience with sheep but a lot of the concerns we had never came to fruition – and when issues have arisen, we’ve had great support. We are producing quality milk and milking through the shed is nice and quick and low stress for staff and animals.
“You go into this business to secure your financial future and do well with a business that is sustainable, has good cash flow and profit. We’re excited to partner with Maui Milk and want to be part of their ongoing success story.
“We are happy with year one. The next big thing will be seeing what we can get out of each sheep and if it goes anywhere near the levels anticipated by Maui Milk, we’ll be pretty happy farmers.”


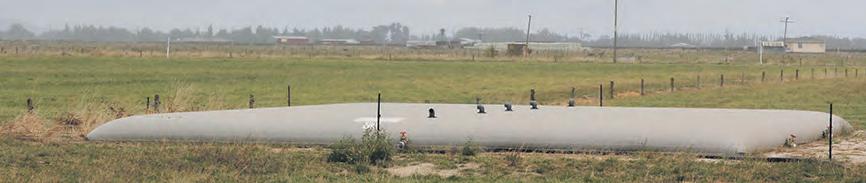

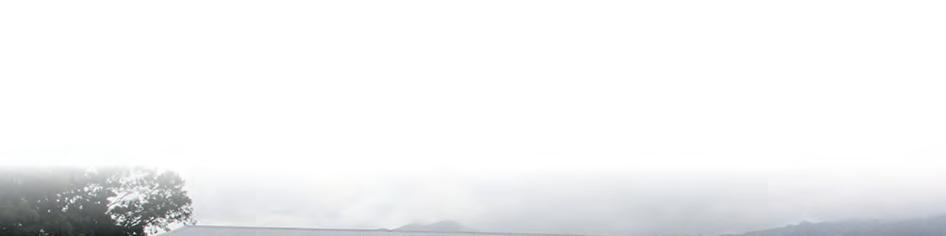


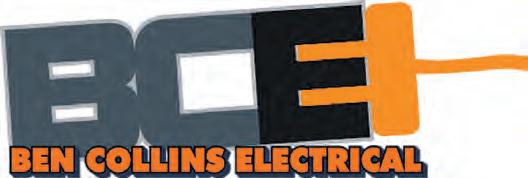
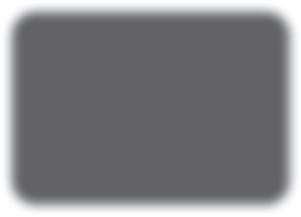
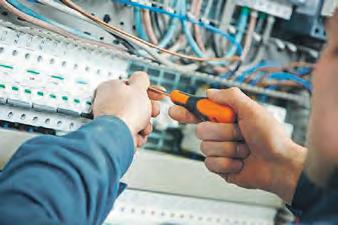
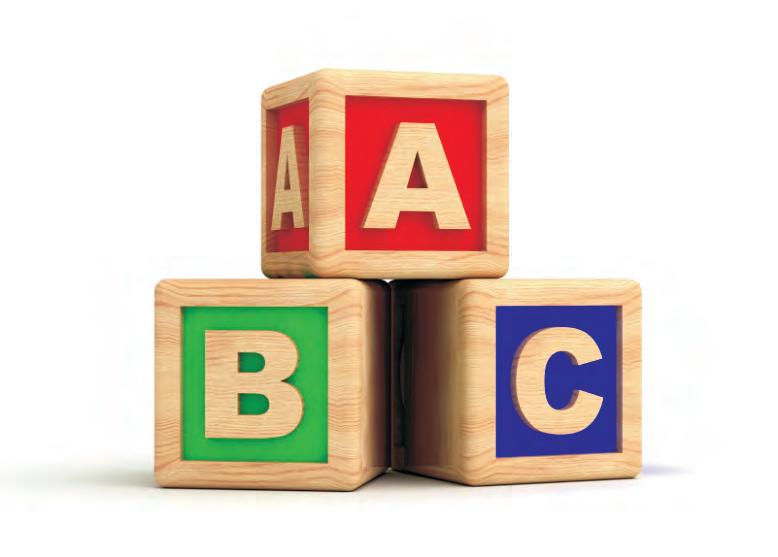