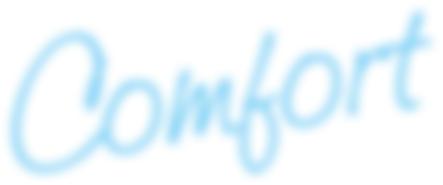
11 minute read
Niaruo Farms Taranaki
by Sun Media

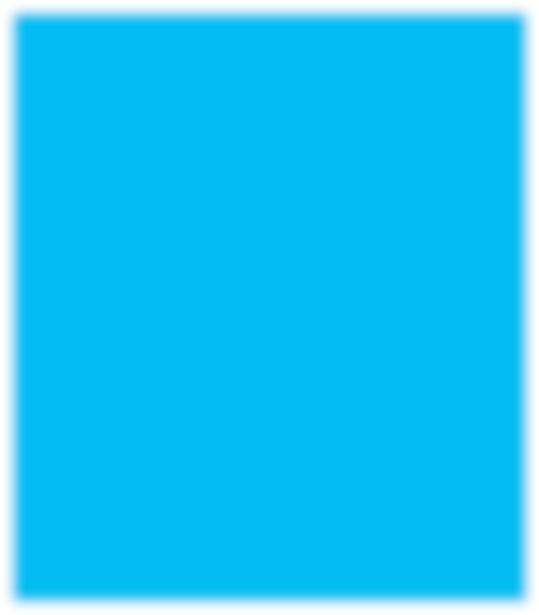

Steve Edwards
Matting on the pit fl oor aids staff comfort.
Hayden and Alecia Lawrence with children Fletcher and Emelia.
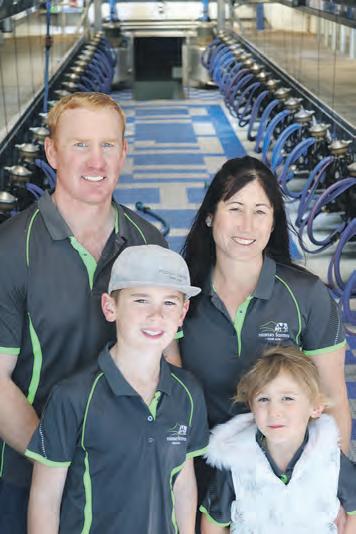
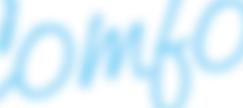
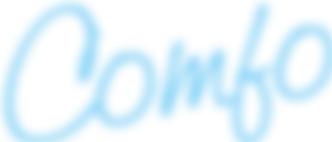
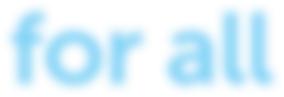
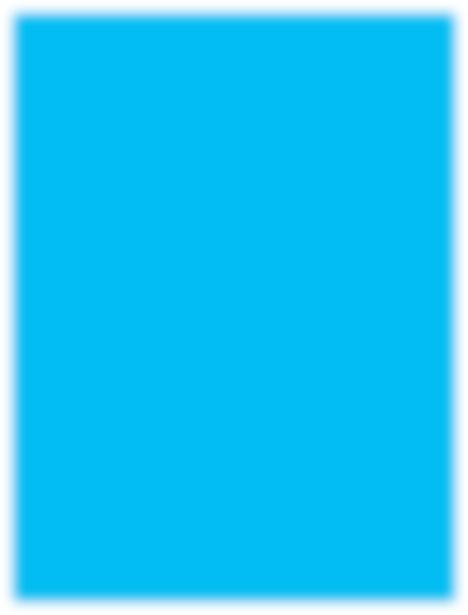
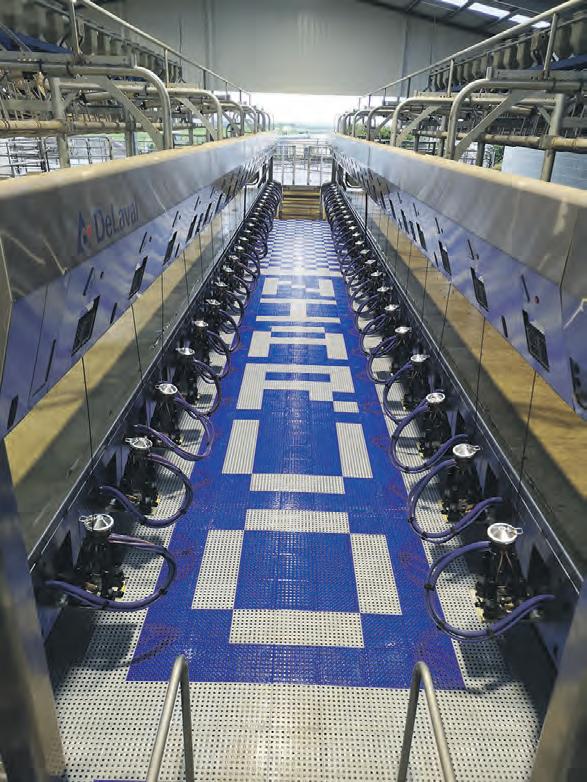
A centralised milking operation has changed lives at the Lawrence farm in Taranaki.
With three young children, Hayden and Alecia Lawrence didn’t relish long hours milking and cleaning up in an expanded 400 cow operation near Eltham.
Their new 24-aside ‘double-up’ herringbone shed, with 48 sets of cups, means a milking time of less than two hours for the 400-cow herd.
The Lawrences milk on 153ha after combining the home farm with a neighbour’s property fi ve years ago.
He says they decided immediately to opt for a single, larger milking shed rather than run with the time-consuming two – a 22-aside herringbone on the home farm and 12-aside on the neighbouring block.
After researching designs on both sides of the Tasman, he says they decided on the rapid exit/ parallel parlour herringbone, as a rotary would have been double the cost.
“Tidiness got it over the line,” says Hayden. “It is very comfortable.”
The new shed was built around the old one and, as the Lawrences winter milk, cows literally went from one to the other on the same day.
Roof raising
Hayden says the same yard was used, with the roof for the new shed built in the adjacent paddock as the existing facility continued to operate.
The original home farm has been in the family for 40 years, with Hayden and Alecia now milking a combined 80 per cent Friesian and 20 per cent Friesian-cross herd.
Hayden says the farm name – Niaruo – is spelt out in the pit matting and comes from his ancestors’ stud farm in Scotland, which had a herd of 30 cows.
He says staff and cow comfort are key in the new shed, with matting on the pit fl oor and bail size increased.
Features include individual milk metering, drafting and in-bail feeding, with an underpass to the pit included in the design.
An upstairs offi ce provides a view over the yard.
The milking plant was installed by Hawerabased Better Dairy Solutions.
Director Gary Wallace says in the milking area this included feed-heads for the in-bail feeding system, plus associated dispensers and bins.
Better Dairy Solutions also installed automatic milk metering systems, cup removers, clusters, milk and air lines. The Lawrence property offers a panoramic view of Mt Taranaki.

Cow Identifi cation
Eartag ID technology provided by DeLaval sees a cow’s details read as it comes into the bails.
Gary says the DelPro system means farmers can manage each cow individually, even with a large herd.
As well as recording milk production, he says the system has the ability to cut-off milking immediately if a health care issue is identifi ed.
It also assists with drafting and calving data.
Hayden says DelPro is a valuable tool in monitoring cow health as well as milk production, with an interactive screen at the end of the pit and a remote station in the shed underpass.
Gateway Finance Brokers Limited
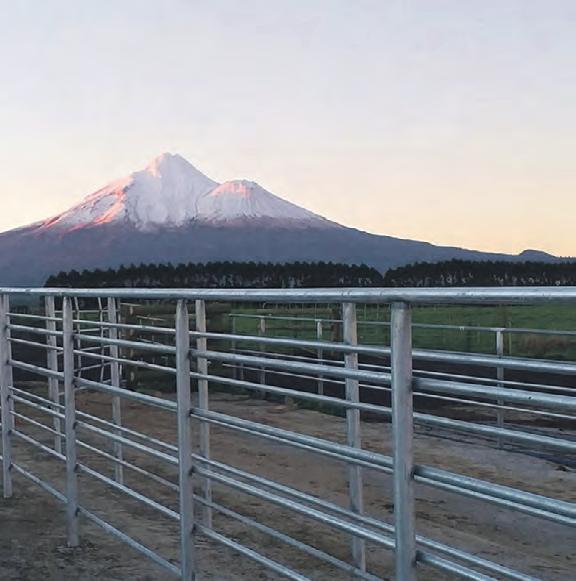
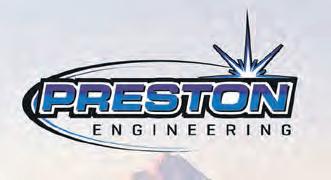
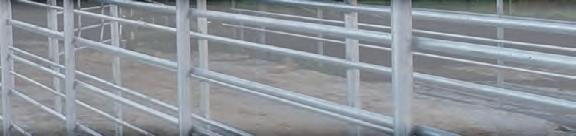

NZ Owned & NZ Owned & OperatedOperated Dairy Hygiene Dairy Hygiene ChemicalsChemicals Minerals Minerals MolassesMolasses
FREE ON-FARM DELIVERY FREE ON-FARM DELIVERY FREE ON-FARM SERVICE FREE ON-FARM SERVICE Calf Meal & Feed Calf Meal & Feed
Manufacturers of Quality Chemicals
Phone: (03) 341 8490 Manufacturers of Quality Chemicals Fax: (03) 341 8491 Phone: (03) 341 8490 12 Wigram Close, Fax: (03) 341 8491PO Box 323, Sockburn 12 Wigram Close, PO Box 323, Sockburn
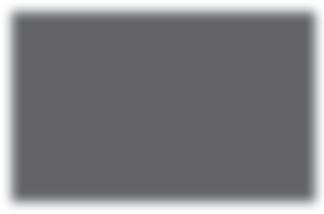

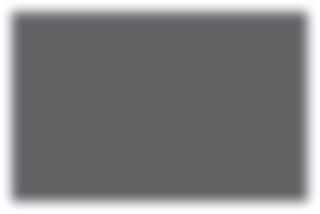
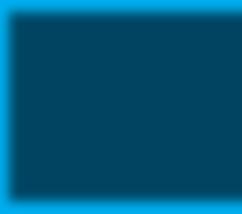

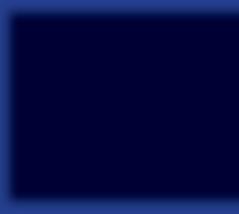

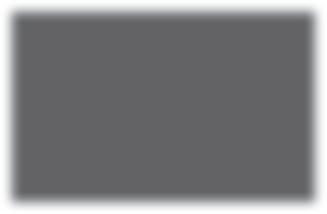

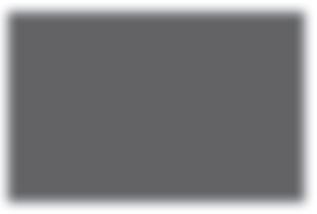
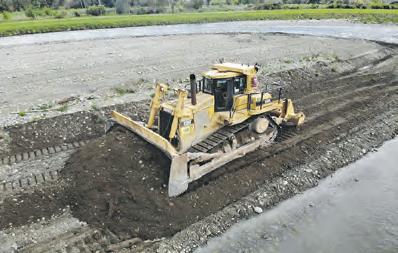

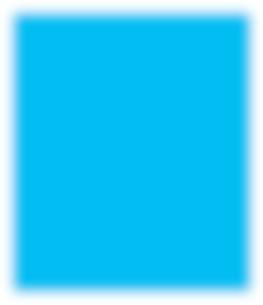
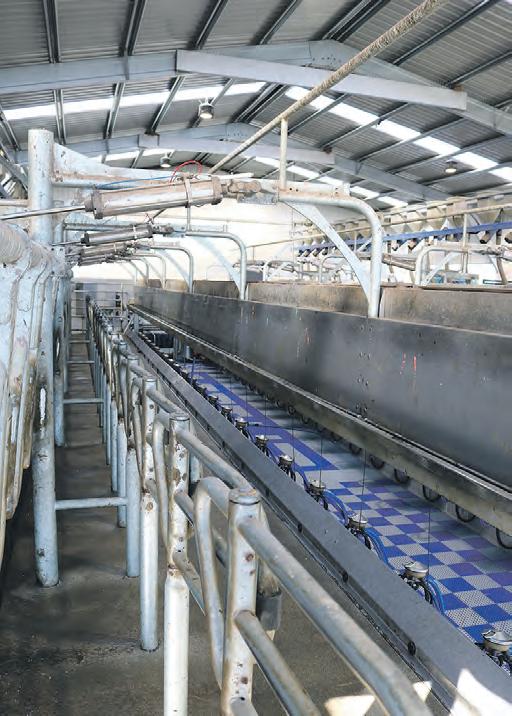

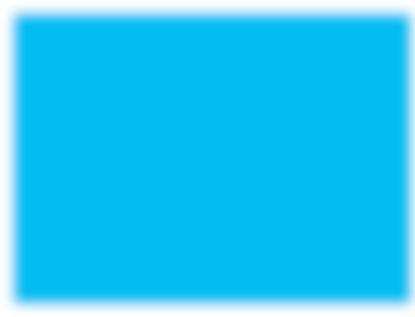
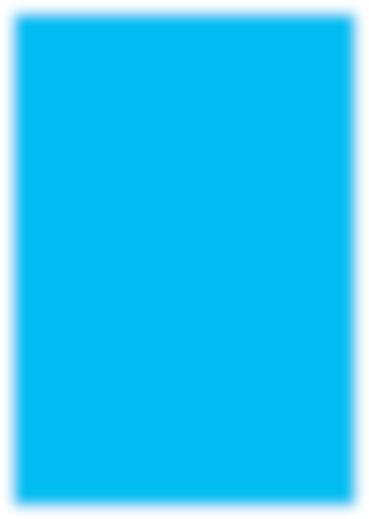
Data is stored on the main PC in the farm offi ce.
Gary says Better Dairy Solutions worked closely with DeLaval, in association with Hayden and Alecia, from the outset of the project.
DeLaval supplied “everything bright and shiny” for a complete working shed, he says.
This included clusters, automatic cup removers, in-bail feed system, milk cooling system and vacuum pump.
Better Dairy Solutions installed the walkover teat spray system, along with the rub rail, which features water jets to keep the internal shed walls clean.
Gary says in the plant room the company was responsible for the milk, cooling and wash down systems for the shed and vat.
The vacuum plant installed by Better Dairy Solutions included compressors, dryers and chillers.
Pipes are covered to give the area an uncluttered look, he says. “It’s a good space to work in.”
Gary says the Lawrence shed is -edge with its level of automation and technology.
Teat spray and conditioner in the milking shed was supplied by FIL.
Central and South Taranaki area manager Craig Allen says an iodinebased teat spray is used, along with an emollient conditioner.
The product is stored in 200L drums connected to a mixing system.

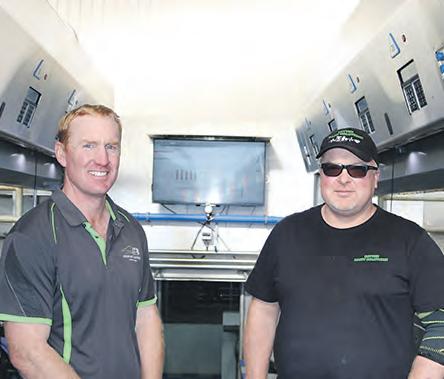
Hayden Lawrence, left, with Better Dairy Solutions director Gary Wallace. Hayden Lawrence, left, with FIL Central and South Taranaki area manager Craig Allen.
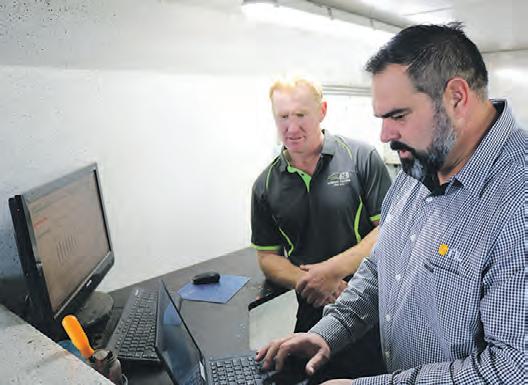
The Lawrences opted for a double-up herringbone shed in preference to a more expensive rotary version. The big screen data monitor. Chris Perrett Electrical Solutions’ director Chris Perrett.
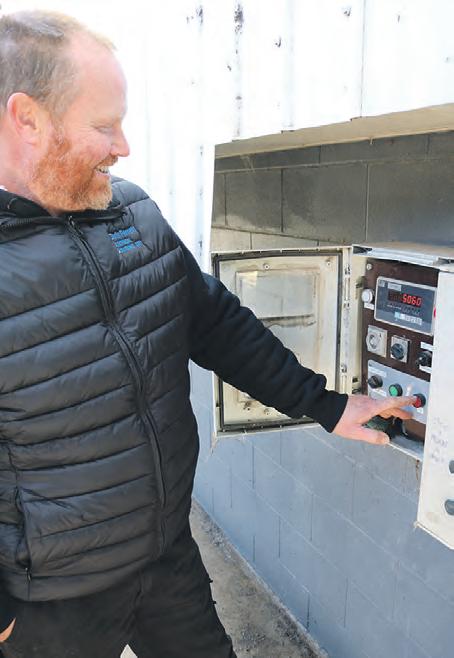
Spray system
It is pumped out at pressure to an automated walk-over spray system, activated by a sensor when the cows exit the milking area, says Craig.
He says the system maintains good teat condition in the cows. The teat spray includes manuka honey.
Craig says the mixing system is calibrated so it can be changed according to the season, such as calving when there is heavier risk of teat damage. Electrical work was undertaken by Hawera-based Chris Perrett Electrical Solutions. Director Chris Perrett says his company bonded all the DeLaval tecnnology and equipment together. “It was a good project,” says Chris. “Something a bit different.” A tidy fi nish was also important, he says.
Chris Perrett Electrical Solutions was also responsible for electrical work associated with the vat, milk plant, hot water cylinders and feed system, plus the vacuum system and compressors.
The company installed the big screen data monitor in the pit and LED lighting throughout the facility.
In-bail feeding
Ingredients for the in-bail feeding system were supplied by Eltham-based Wonder Minerals.
Sales consultant Wayne Trethewey says Hayden Lawrence consulted an animal nutritionist to get the right mix for his herd.
This can be adapted according to the respective season, such as the addition of zinc when the herd could be prone to eczema, says Wayne.
Regular ingredients include magnesium oxide, lime fl ower and calcium phosphate.
Wayne says the mineral mix is stored in a silo on-site and combined with meal before entering the in-bail feeding system.
Wonder Minerals also provides calf meal for the Lawrence property.
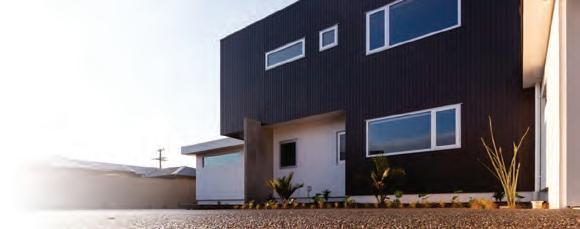
admin.hawera@graypainters.co.nz the proven health system.
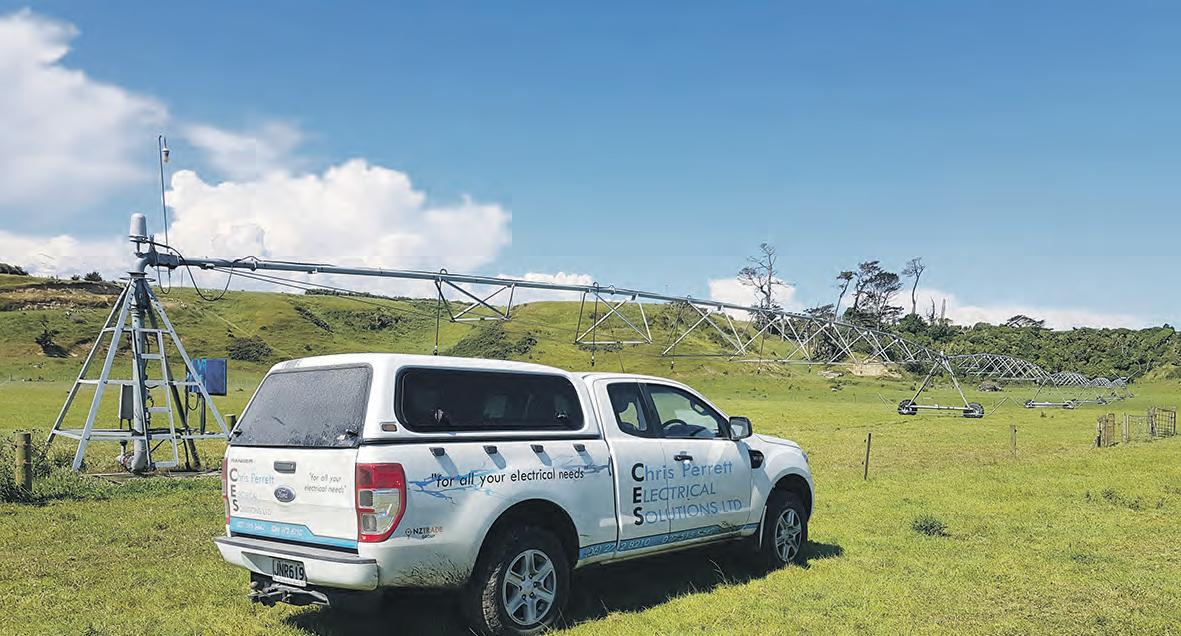
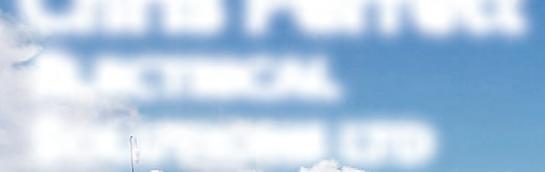

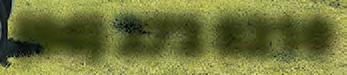
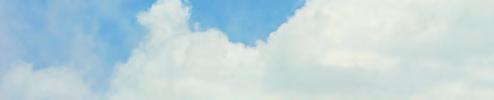

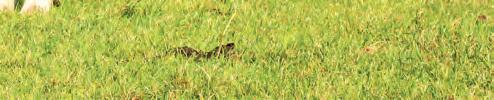
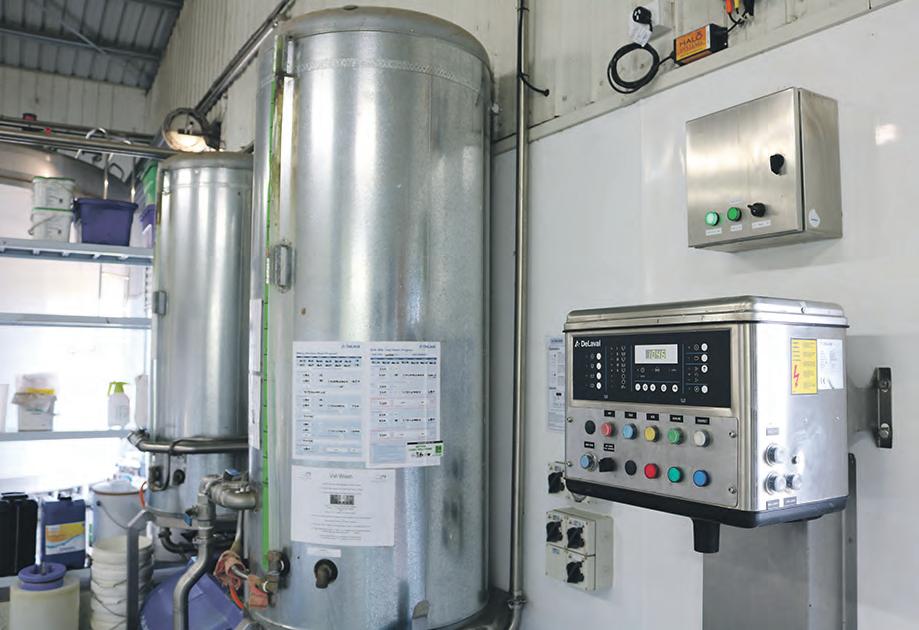

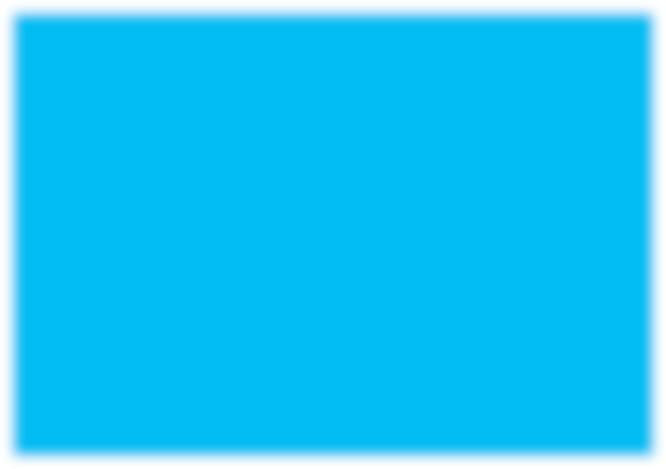
The nerve centre of the plant room. The roof for the new shed was built in an adjacent paddock as the existing facility continued to operate. Photo: supplied.

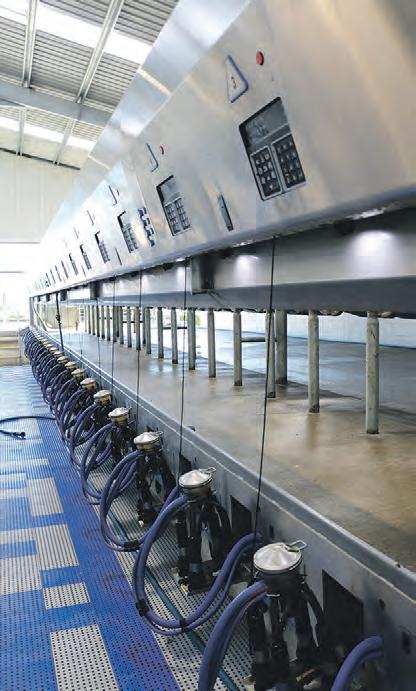
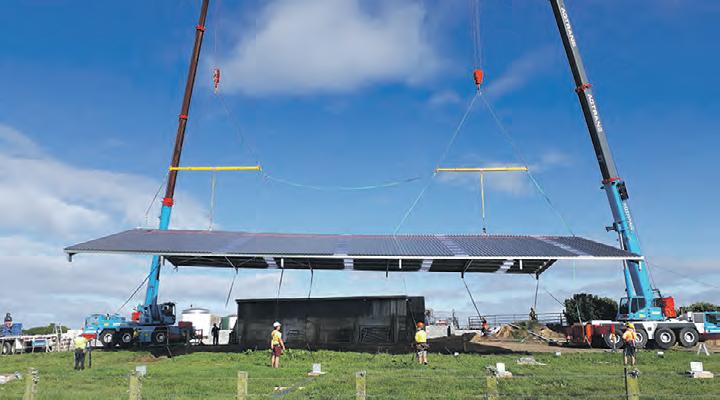
While cutting edge in technology, Hayden Lawrence says the shed is very comfortable for staff and cattle.
Hayden and Alecia use a high-tech monitoring system that collects and analyses physical data for each cow.
Clint Brereton, Southern Hemisphere country manager for Austrian-based developers SmaXtec, says sensors in a bolus placed in the cows provide live data on animal health, heat and calving.
“It monitors core productivity and rumination activity,” says Clint.
Each cow has a unique code relating to its ear-tag number.
High-tech detection
Clint says information on a cow’s inner body temperature is invaluable for early disease detection including feverish conditions and metabolic diseases.
The system also acts as a heat detector, helping to identify the ideal insemination time for each cow.
Clint says SmaXtec detects calving early through measuring change in a cow’s body temperature.
The wireless system transfers data to readers around the farm which ultimately lands in owner’s/staff’s personal computers or mobile phones.
Clint says the system can also be designed to provide farm data to vets/farm advisors on a read-only basis.
“It gives an insight into the engine of a cow,” says Clint.
Cow comfort in the yard was enhanced by Hamilton-based NZ Cowshed Groovers.
Founder Neil Taylor says, as the name suggests, the company cut grooves in the concrete to prevent cows slipping over.
A former concrete cutter, he invented the ride-on machine which saws cross-cut grooves into the concrete.
Neil says the three-wheeler he used at the Lawrence shed is powered by a four-cylinder diesel motor and has 11 blades cutting grooves 8mm deep.
Grooving of the Lawrence yard was completed in two parts.
“I did half about three years ago, and the other half when the new shed was built, says Neil.
Depending on the size and shape of yard, Neil can also use a smaller machine, with seven blades.
He says his service can cover 1000 square metres of concrete in two days.
Engineering expertise
Preston Engineering, from nearby Kaponga, put together the AI and vet race set-up, plus all the gates and pipes in the yard.
Hayden says the old shed had AI facilities, but this just catered for the 150-cow herd.
The new, larger set-up is in design and under one-roof, he says.
Hawera-based DR Gray completed all painting required for block-work inside and out, says Hayden.
This included the pit walls, milking area and plant room.
Hayden says the painting project covered about 120 square metres.
“It is easy to clean, and we selected the colour to blend in with the roof.”
Hayden says the painting team worked around the building project.
“It was quite a challenge as we were still milking every day,” he says.
On the farm, Hayden has adopted a comprehensive plan for fertiliser application.
Rather than a uniform approach across the property, in 2009/2010 all paddocks were soil sampled and fertiliser applied differentially.
Hayden says there is less cost involved in altering the amounts and types of nutrients for each paddock compared to the traditional blanket ‘one rate fi ts all’ approach.
“This was achieved without compromising pasture production and hence milk production on the farm.”
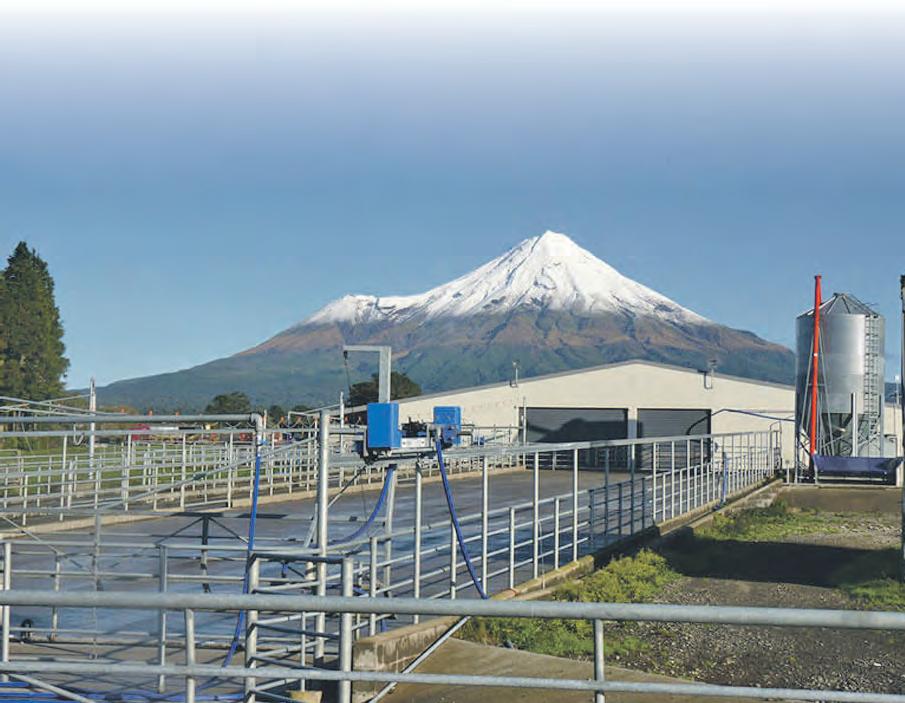
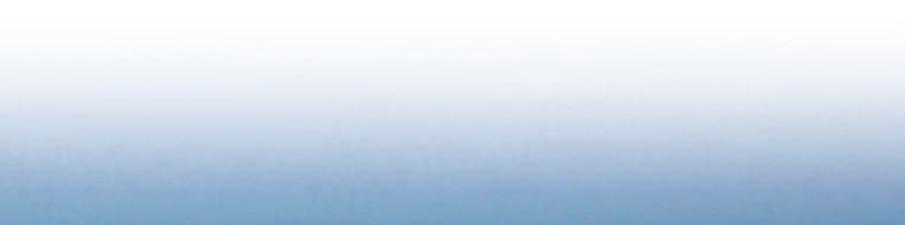
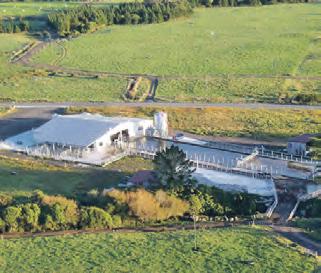
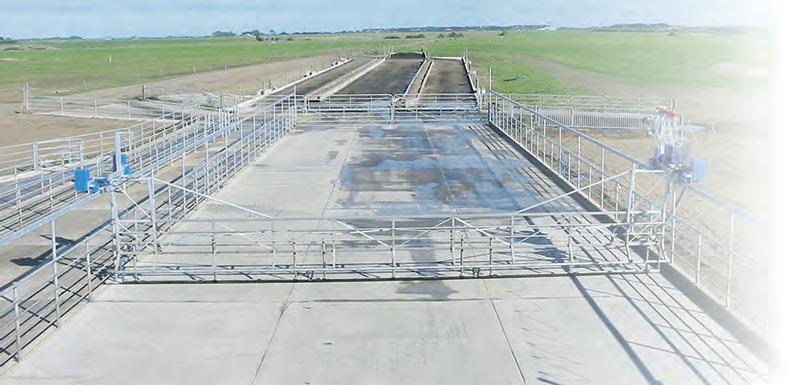

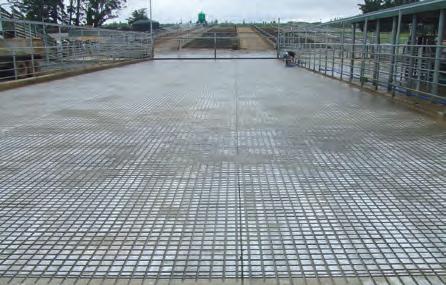
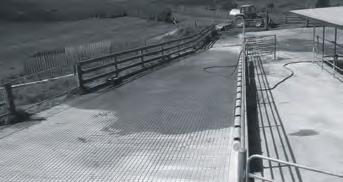