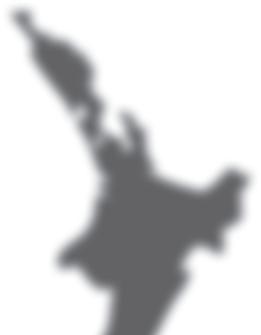
10 minute read
Lepper Taranaki
by Sun Media
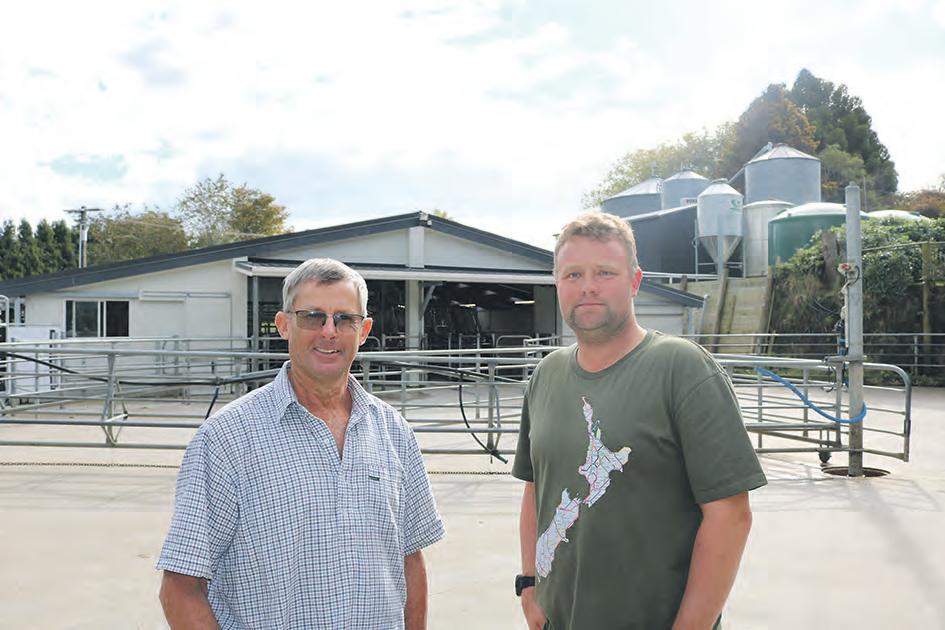


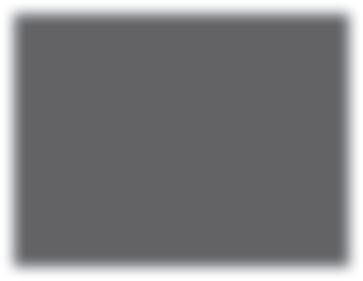
Steve Edwards
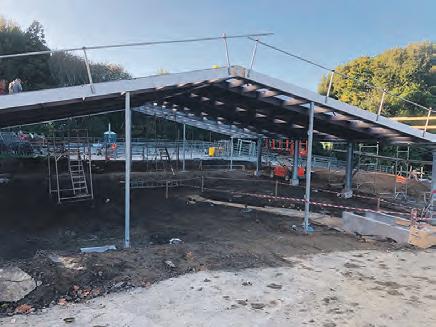
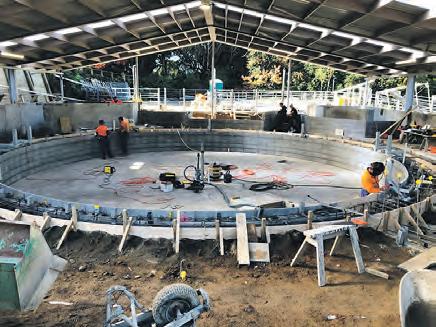
Shed construction underway.
Graeme Lepper, left, with co-farm owner and son-in-law Andrew Pritchard. The new rotary taking form.

Another chapter has been written in the long history of the Lepper family farming operation in Taranaki.
Graeme Lepper has connections to Manutahi Road, near New Plymouth, stretching back more than 160 years.
His family’s place in history in the area is marked by the naming of the local town.
Lepperton was established as a military settlement in the 1860s and given its title in recognition of Lieutenant Colonel Maxwell Lepper, commander of the 14th Regiment in the Taranaki Militia during the Land Wars.
After his retirement the Colonel was allocated a block of land in the settlement.
He died about four years later, but the family name remains strong in the area.
Married to Robyn, Graeme Lepper is the Colonel’s great-great-great-grandson.
Graeme says Lepperton was originally called Manutahi, “but they had one in South Taranaki as well so this one got changed”.
Historic Homestead
The 120-year-old Lepper family homestead remains at the centre of a renowned garden on the Manutahi Rd property.
An older home on the property was destroyed by fi re.
Graeme says the area has grown hugely in recent decades, with former farmland cut up into lifestyle blocks and a subdivision created in Lepperton.
“It’s a privilege to still be in an area named after your family,” he says. “There are only a handful of settler families left.”
Graeme’s father Dennis started a genealogy book detailing the family history in the area since the days of Colonel Lepper.
Through the generations, the Leppers built on their Manutahi Rd farm holding.
While Graeme and Robyn still live in the homestead, ownership is now in the hands of son-in-law Andrew Pritchard and daughter Sarah who were married in her parents’ renowned garden.
A former builder, Andrew did a couple of seasons on a dairy farm at Midhurst before coming to Lepperton seven years ago and graduating from manager to sharemilker and more recently leasee.
“Graeme is a world of knowledge, but has never told us what to do,” says Andrew. “He is an incredible mentor.”
Taking on ownership and the new milking shed was just the way it evolved, he says.
With two primary-age children, Andrew and Sarah are conscious of the farm’s future as well as its rich past.
“We are guardians of the land for this generation,” says Andrew.
He says he and Graeme have both always added more infrastructure than immediately required on Manutahi Rd to cater for future generations.
“It’s been an amazing journey so far.”
Farm linkage
In 1971 Graeme’s father bought 97ha directly across the road from the 155ha home farm, with an underpass linking the two properties.
His father built a pioneering 36-bail rotary shed for the home farm and a 12-aside herringbone, since demolished, on the other side of the road.
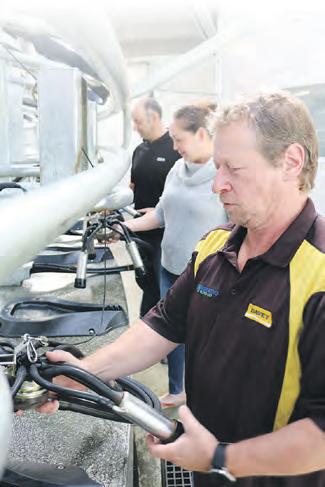

DAIRY WALL COATING SYSTEMS
HARDWEARING AND DURABLE
Acraflex Dairy Wall Coating Systems save hours in cleaning, seal against bacterial build up and create a bright, hygienic working environment.
10 YEAR GUARANTEE ON ALL NEW SHED APPLICATIONS
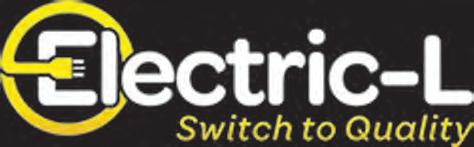
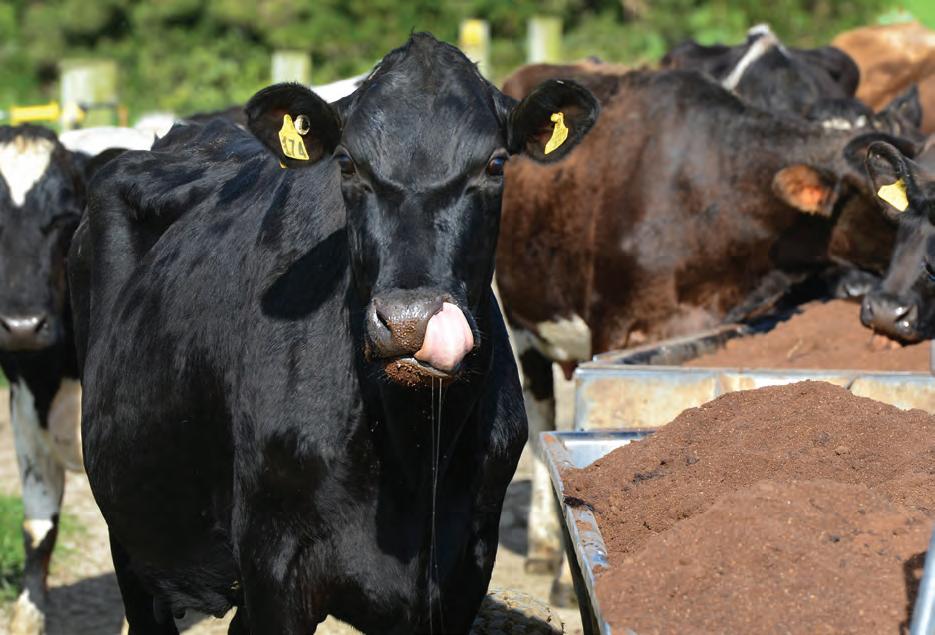


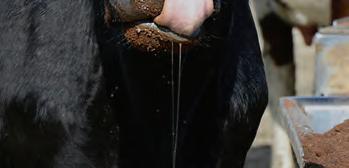
LIQ
MOLASSES MINS
COW
35
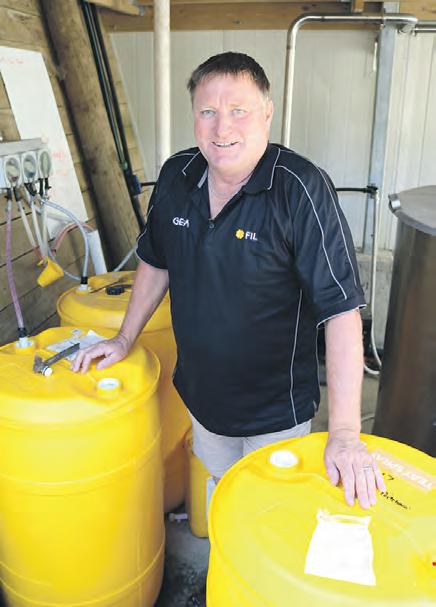
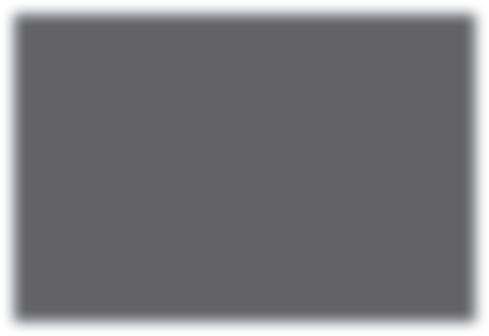
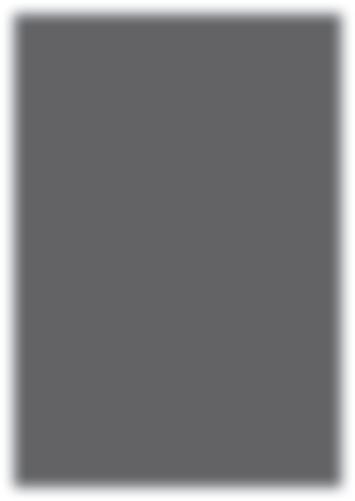

Greg Sampson, area manager for FIL in King Country/North & Coastal Taranaki, with detergents his company supplied to the Lepper shed.
BHL Feeds’ North Taranaki sales manager Rob Topless with some of the tasty treats enjoyed in-bail. Dairypro directors Alexis Stevens, back left, and Glen Stevens, centre, with GEA Taranaki area sales manager Steve Nolly.
Electric-L director Kerry Larsen at the control panel.

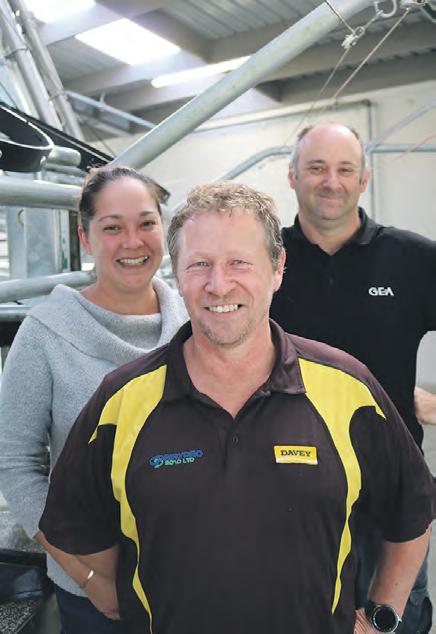

The new 50-bail rotary milks two herds of about 230 cows apiece.
Five staff are employed, with 2IC Toni Feaver.
Graeme and Robyn have been at the helm since the mid-70s, with the yard in the rotary shed replaced nine years ago and technology upgraded over the years including clusters, vacuum pump controller and plate cooler.
He says they have been thinking about a new shed since 1980.
The 50-bail design features auto plant wash, teat spray and drafting system.
Construction was undertaken by Okato-based Brian Hill Building.
Director Brian Hill says the project involved demolition of the original rotary shed, replaced by a 50-bail rotary, including the existing yard.
Brian says the yard was already big enough to accommodate the new milking shed and 500cow herd.
The new rectangular shed and milking platform was built on the cleared site after the removal of the existing facility.
Design features
Brian says the design features an underpass into the middle of the milking platform, separate rooms for the milking plant/hot water cylinders, vacuum pump/switchboard, offi ce, toilet and vat-stand.
Skylights in the milking area complement LED lighting.
Brian says the walls are made of double-sided, coloured, insulated panels, with ColourSteel used on the roof.
Mitre 10 Trade New Plymouth was involved in the Lepper cowshed project through its close supplier relationship to Brian Hill Builders, says marketing & customer experience manager Nicole Attrill.
“We have a long-standing supplier relationship with Brian Hill, so know him and his team well,” she says.
Nicole says this was a large-scale project, with Mitre 10 Trade New Plymouth supplying varying aspects for the build.
This included solid timber beams, hyspan (laminated) beams, paint, paint accessories, reinforcing steel, mesh, bar chairs, tie wire, various sizes of timber (some machined to profi le), sealants, hardware (bolts, nuts, nails, framing brackets), various sizes of plywood, PEF backing rod, steel cut and bend, polythene, aluminium gate, fence panels, posts, drainage channel, Marley spouting (Typhoon and Magnum), door stops and timber mouldings.
Joint e ort
A combined effort saw the milking plant supplied by GEA Farm Technologies and installed by Dairypro 2010.
GEA Taranaki area sales manager Steve Nolly says this involved both new and recycled equipment from the old shed.
Steve worked closely with Dairypro directors Alexis and Glen Stevens on platform technology and automation including cup removers, clusters, teat-spray and in-bail feeding.
Both companies also supplied and installed the plant wash, vat wash and vacuum systems.
Detergents for shed hygiene and teat spray were provided by FIL.
Greg Sampson, area manager for King Country/North & Coastal Taranaki, says the washdown system – milk plant and vat – involves acids, alkalis and chlorine.
The chemicals are automatically measured, mixed and pumped through the milk lines every day and the vat after each collection.
Greg says the acid and alkali is stored in 200L drums, and the chlorine in a 60L container.

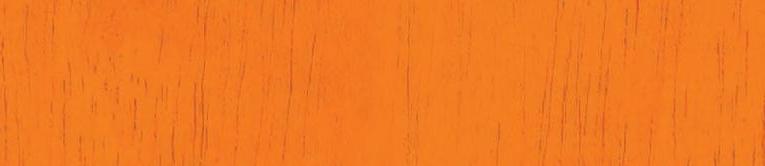

NEW PLYMOUTHNEW PLYMOUTH NEW PLYMOUTH

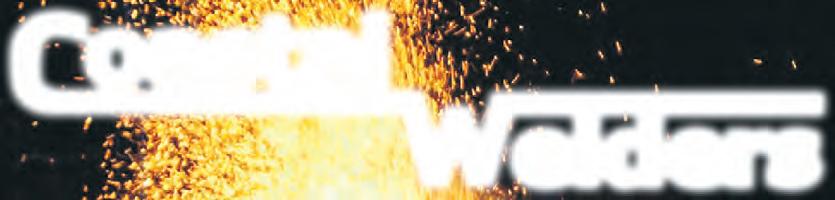
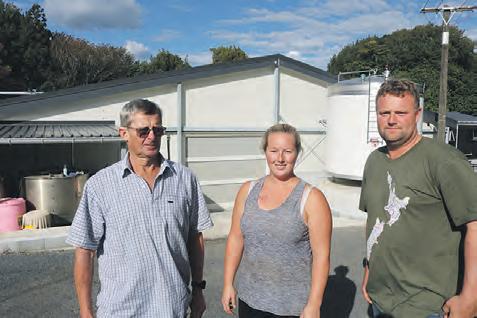
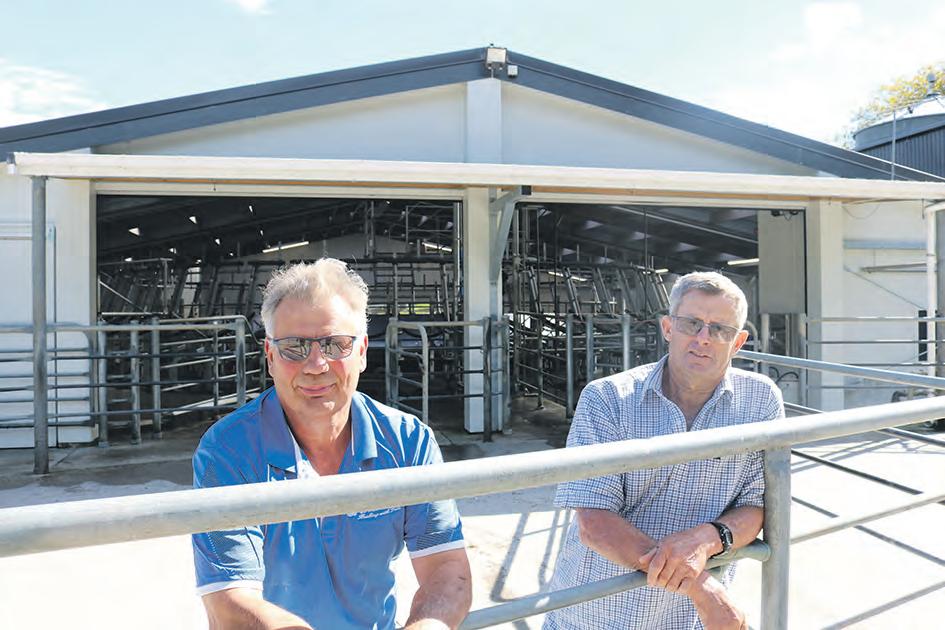

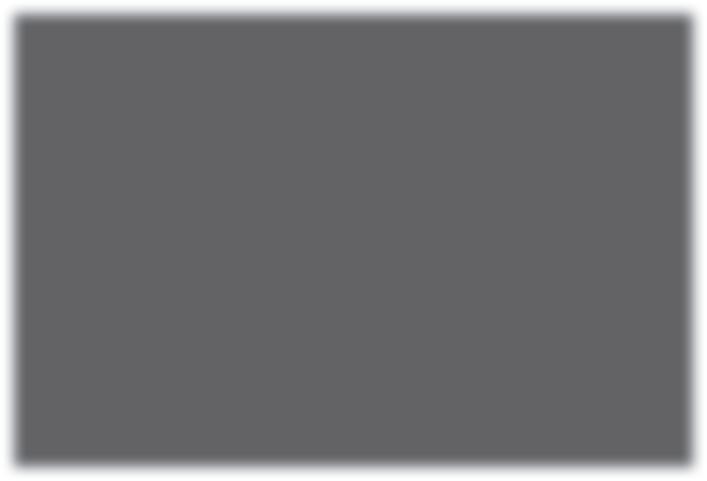
Brian Hill Building director Brian Hill, left, with Graeme Lepper. Graeme Lepper, left, with 2IC Toni Feaver and co-owner Andrew Pritchard. A view across the yard which combined old and new in the 50-bail rotary project. The shed is buffered by established trees and plants.

For hygiene and cow care, FIL’s automated IntelliBlend system includes teat spray and emollient, which is pumped from holding drums and delivered to each bail.
“It gets sprayed on (for 2.5 seconds) three seconds after the cups are off,” says Greg.
In-bail feed for the Lepper herd comes from BHL Feeds at nearby Bell Block.
Feed blend
North Taranaki sales manager Rob Topless says the feed is a harvest blend with ingredients including palm kernel, barley and molasses.
Rob says the meal is stored in two 12 tonne silos from an existing feed operation changed two years ago – the manual mixing system is now automated – in anticipation of the shed renovation.
Two augers and a molasses line move the material from the silos into the pit area, with associated dispensers and bins.
Rob says the feed mix can be changed, with additives such as zinc included, as cows enjoy a seasonal diet.
He says a cow, fed at both morning and afternoon milkings, will consume about half-atonne of meal per year.
Andrew says they place a particular emphasis on cow condition and know the importance of diet in the milking herd.
This extends to a similar mix of supplements fed in-paddock, says Andrew.
All electrical requirements, from the power pole to distribution board with MCC (motor control centre), were designed and built by Electric-L in New Plymouth.
Director Kerry Larsen says the electrical system at the Lepper shed was purposedesigned, and included a central MCC, VSD platform drive system and an automated in-bail feeding system.
A previously designed and installed backing gate control system by Electric-L was relocated into the new cowshed. “It is all site-specifi c,” says Kerry.
Electric-L’s work also included wiring up the VSD milk plant vacuum pump, milk lift pump, milk plant power supplies, vat refrigeration and milk cooling system.
Future-proofi ng
They also installed water pumps, LED cowshed and area lighting, digital temperature control of hot water cylinders, offi ce and ablutions and all other site power and data with future-proofi ng in mind for years to come.
Painting in and around the platform was conducted by Surfatex from Foxton.
Director Glen Sinclair says the company painted concrete walls all around the milking platform, plus the pit and underpass.
Surfatex used its specialist Acrafl ex dairy wall coating throughout. Glen says this hardwearing coating is specially designed for shed hygiene and easy cleaning in the dairy industry.
He says walls are prepped with hydrochloric acid, with a grinder then used to smooth off rough edges.
The paint is sprayed on using a seven-coat system, fi nished with a solvent glaze.
Earthworks on the Lepper project were undertaken by Busby Contracting.
Graeme Lepper says this included demolition work on the old shed.
A year earlier Busby Contracting cut a bank away on-site in preparation for the enlarged shed. Graeme says preparation of the new site included digging out for the platform, along with some drainage work.
“They moved quite a bit of material over a few days.”
Coastal Welders from Okato were engaged to help in the project by Brian Hill Builders.
Graeme Lepper says this contribution included all the trusses for the new building, including supports and beams.
Coastal Welders made the required elements at their workshop, then assembled them onsite, says Graeme.
John Wilson - 3rd GEA iFLOW 60 bail rotary.
At Bluemont Dairies, John’s latest conversion project, he is set to milk 900 cows through the new 60 bail iFLOW rotary with just one milker – doubling what they milked last year, in the old shed.
Looking for a system that would support a one-person operation, was reliable and produced a quality product, John thinks he’s ticked the boxes with the iFLOW.



Need all-round milking efficiency like John? Call us to book your on-farm consult today.
0800 GEA FARM.
Driving dairy efficiencies? We can help.