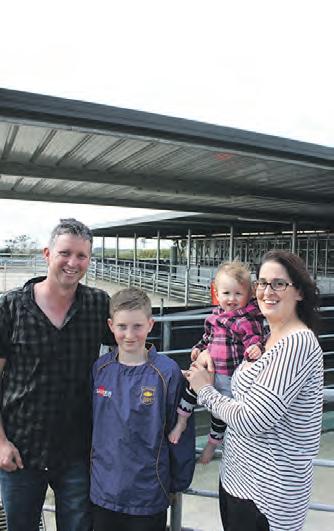
16 minute read
Twin Creek Dairy South Auckland
by Sun Media
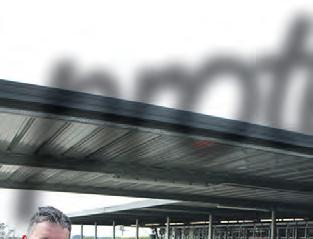

Steve Edwards
James and Stacey Wallace with children Ashton and Emilia. Absent is daughter Karley. A side-on aerial view of the sheep milking facility. Photo: Don Chapman Waikato.
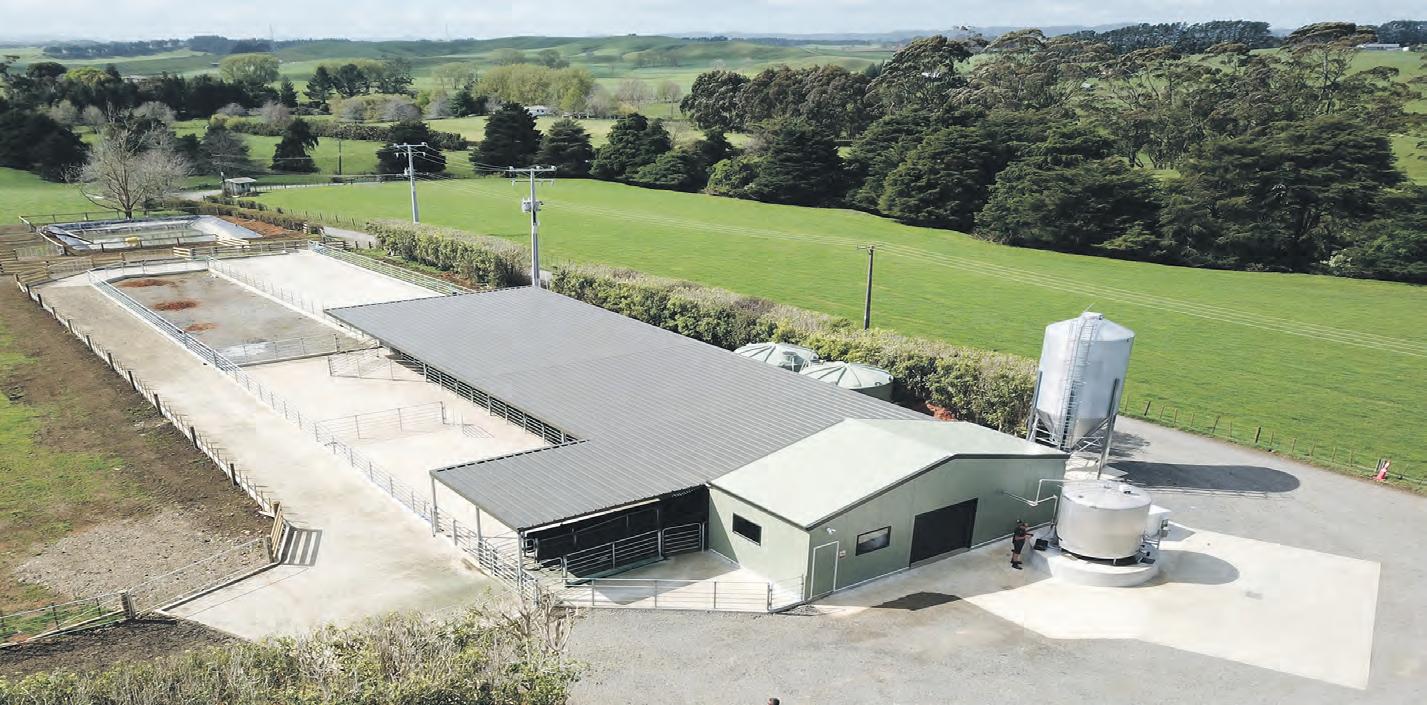
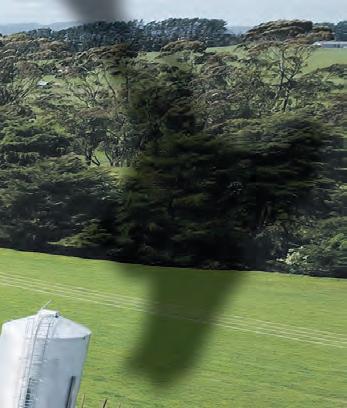
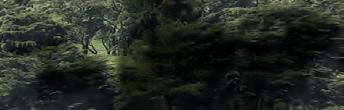
A Pukekohe property has gone from high-fashion to highprotein production.
The Wallace family now milk 750 sheep on a 90ha farm along the aptly named Ostrich Farm Road.
In the late 1880s it was part of a 1400ha block – Helvetia – which stretched from Whitford to Pukekohe and ran 500 ostriches to fulfi l the fashion needs of the women of the day.
Today, James and Stacey Wallace supply Spring Sheep New Zealand, based at Innovation Park in Hamilton.
The family’s connection with the property goes back 50 years when James’ father Barrie worked for a calf-rearing operation run by what is now Wilson Hellaby.
In 1987 Barrie and his wife Sandra took over a 30ha block, continuing to rear calves while also entering into commercial vegetable growing.
Trial and error
After some trial and error with various crops including buttercup squash, beans, peas and onions, Barrie says they started to specialise in courgettes about 20 years ago.
The holding grew, including some leased land, to cater for the courgettes, calf-rearing and sheep (grazing/fattening).
James had been leasing a property at Karaka, milking sheep, bringing that operation home to Twin Creek Dairy in 2018.
The romney-cross sheep were replaced with his milkers – East Friesian sheep.
James and Stacey use about 90 per cent of the property for their sheep milking operation, with his parents continuing to use the balance for calf-rearing and courgettes (sold commercially).
Plans to start building a milking shed in February 2020 were halted by Covid, but eventually completed in April.
Bails for the 30-aside operation came from James’ previous operation at Karaka, with the milking shed designed to fi t around this by Morrinsville-based Chapman Dairy.
Safe future
James says the pit has been future-proofed to accommodate a 40-aside system.
A 40-aside herringbone system was tried out initially on the farm, but James says the sheep hated it and a replacement straight bail design has proved highly successful.
A milking time of six hours involving three to four staff has been cut to two-and-a-half hours and two people.
James asked Morrinsville-based Chapman Dairy to design a shed that would be modern, effi cient, and future-proofed so it can easily have add ons at a later date when needed.
“They succeeded on all accounts,” he says. “The fl ow of the shed is incredible. The sheep run to the shed and fl ow through with ease, hence the reason we did not purchase a backing gate. It is not needed.”
The roof was extended slightly over the yard so it can hold fi ve rows under cover.
James says this ensures that no animals are left out in the weather on the yard for any more than 20 minutes, eliminating the need for a covered yard.
“They also exit quickly either through the drafting race or through the foot-bath, making animal health an easy chore.”
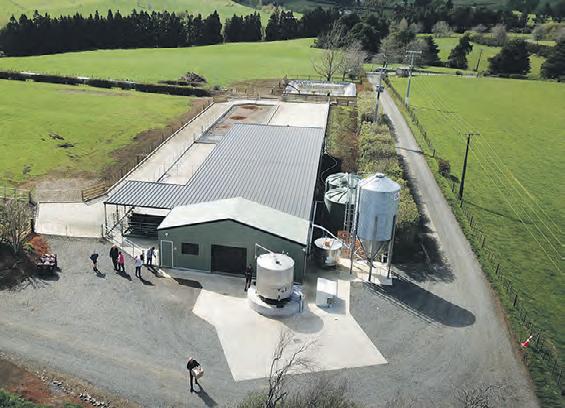

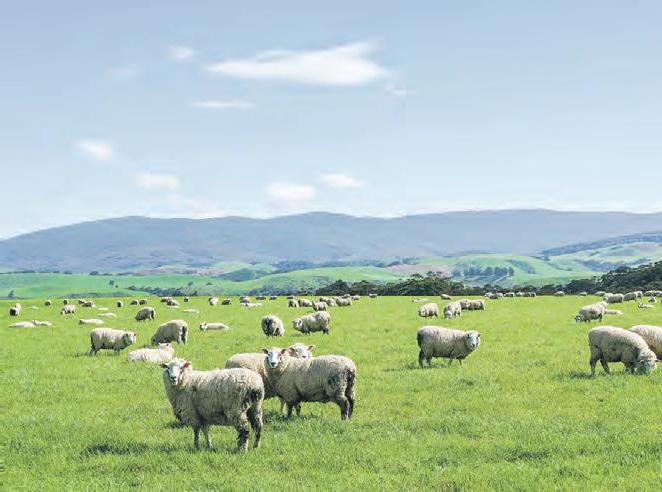

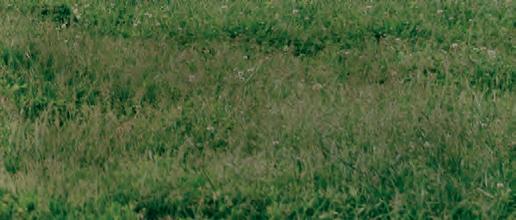
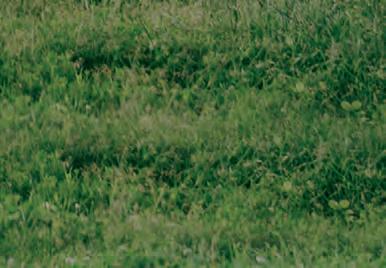
norwood.co.nz
KUBOTA. BE READY.
Talk to your local Norwood dealer today.
SPECIALISED COATINGS LTD


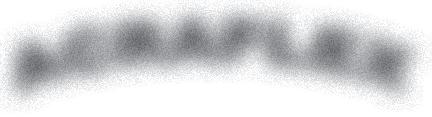

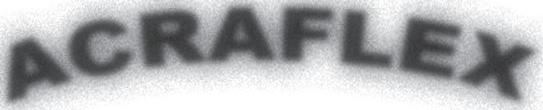


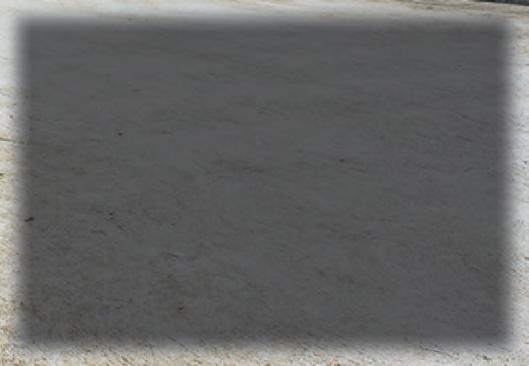

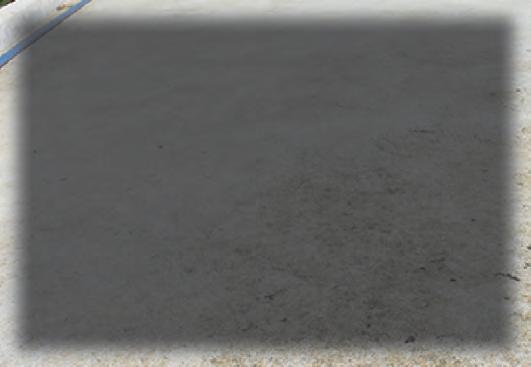
The Wallace family – Sandra, left, Ashton, Barrie, James and Stacey, holding Emilia.

Flocking into the milking shed at Twin Creek Dairy. The youngest members of the fl ock.
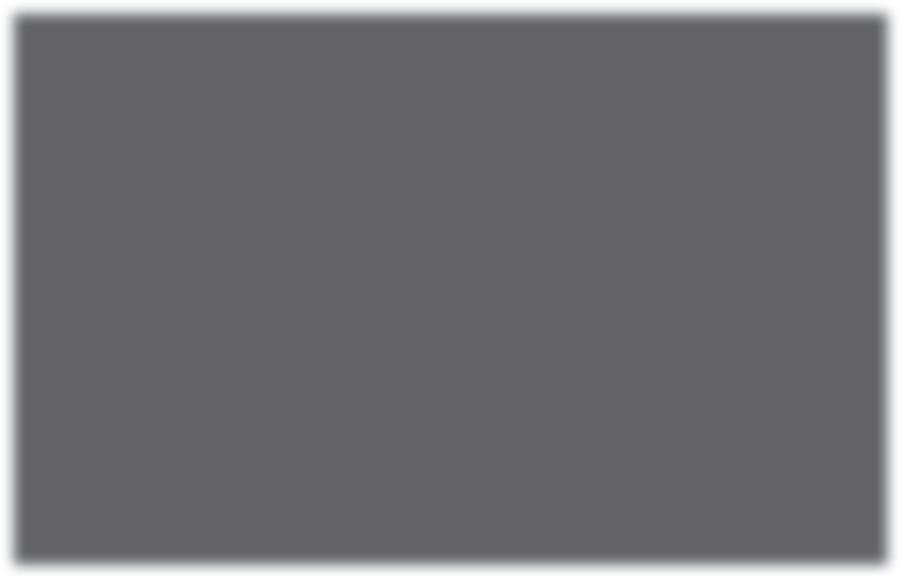
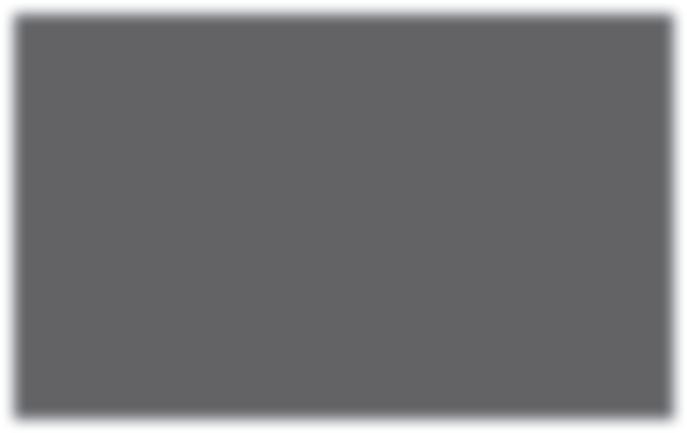
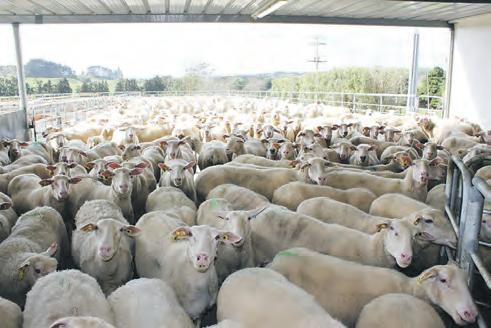
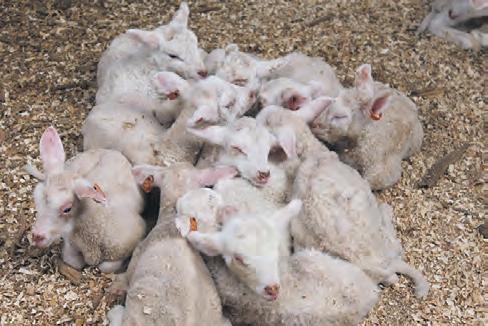
Chapman Dairy director Don Chapman says he worked around using the existing bails – a parallel stall system – from Karaka in his design at Twin Creek Dairy.
This included the roof extension, while he says it was also made higher than the usual cow dairy design to allow for rapid exit by the sheep. Built with purpose
The pit is lower to cater for the lower udder of the sheep compared to cows.
Don designed the milk room and offi ce to fi t the client’s requirements.
Built on a green-fi eld site by Don Chapman Waikato, the shed links with new and existing races.
A new transformer was required to power the facility, while water comes from an existing bore.
James adopted a “keep it simple” approach to milking and washdown equipment – manual cup removal and teat wash.
“We decided not to install an automatic wash system and we feel our decision has been justifi ed. It only takes two people 15 minutes to put the wash through and hose out due to the low mess the sheep make and the Waikato Milking System’s equipment we installed.”
Washdown of the yard is via a good oldfashioned high-pressure hose, however, to meet industry and council compliance requirements, an effl uent disposal system was built, including a gravel pit and holding pond.
The building project included a milk-room, with capacity for future expansion, and an offi ce.
James opted for multiple variable-drive pumps to keep electricity costs down, including the vacuum pump, washdown and shed water pumps.
In the yard there is a gas-powered sheep cradle used to inspect and treat and animals’ feet.
Covers have been placed on rails at the entrance and exit to the milking area to help with sheep focus and fl ow.
James says the sheep have also learnt quickly that a meal dispenser lies at the head of each of the bails.
Nutritional diet
With help from a nutritionist to establish the best type of feed, the system James installed provides each sheep with 800g per day over two milkings.
Two staff handle the twice-a-day milking – with James on call – plus another to help out during lambing.
Milk is collected twice a week by Spring Sheep, with the season running from mid-July to the end of April.
In the future James is looking at installing a Halo milk monitoring system; “mainly to measure milk volumes so we can instantly gauge how the sheep are performing without having to wait for the tanker pick-up.”
Associated with the milking facility is a 820 square metre lambing shed, where youngsters are fed and raised from birth to fi ve-weeks-old.
Bedded on wood chips, they are separated into groups according to age and enjoy a diet of powdered milk and solids.
James says the shed can hold up to 600 lambs.
Effl uent from the milking shed is managed via a system designed and built by AgFirst Engineering from Te Awamutu.
Director and engineering consultant Davieth Verheij says the company initially looked at the farm’s layout, fl ock size and soil structure to help in the pond calculation and irrigation design.
A 600 cubic metre polyethylene-lined pond was built, along with an associated sand-trap.
This receives effl uent from the milking shed, via a 50mm PVC pipe, in a gravity-fed system.

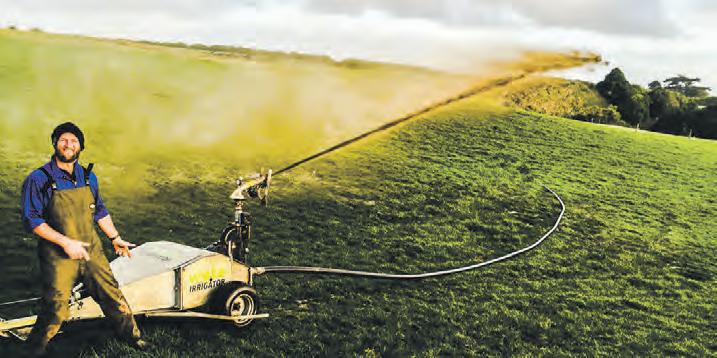
DAIRY
EFFLUENT WOF’’
WARRANT OF
FITNESS
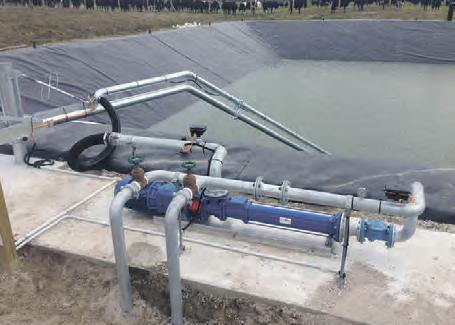
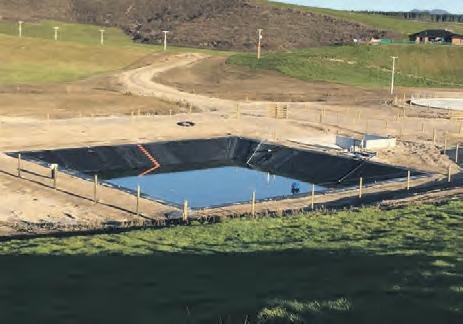
Cost Effective performance in water & waste applications
• Dairy Effluent Ponds • Irrigation Dams • Canal Liners • Frost Protection • Dry Beds & Weeping Walls • Underpass Encapsulation


AgFirst Engineering director and engineering consultant Davieth Verheij in front of the sandtrap associated with the farm effl uent system.

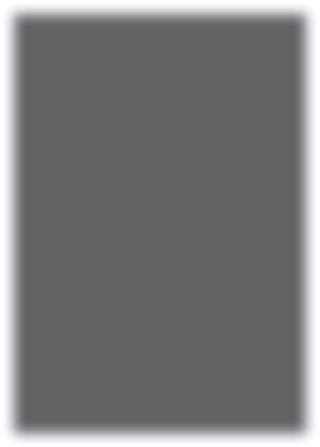
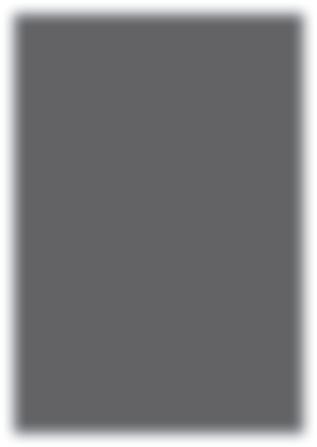
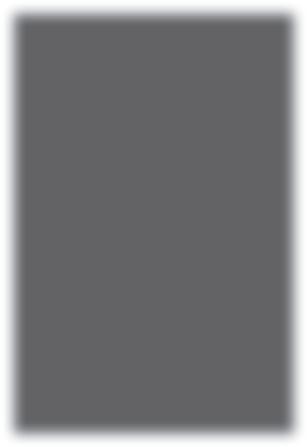
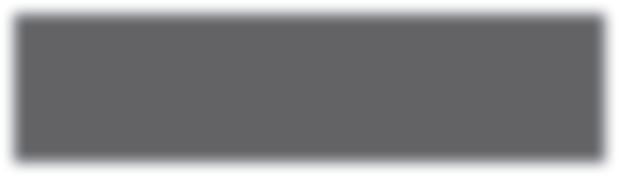

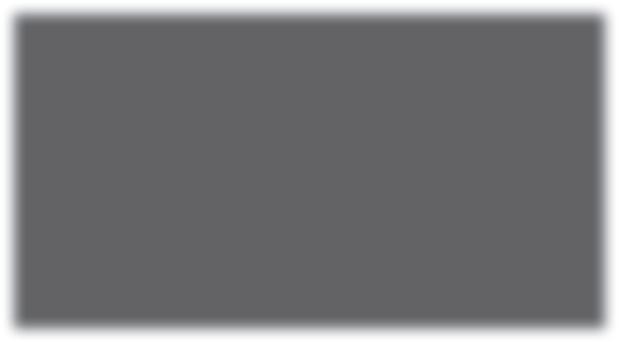
The 600 cubic metre polyethylene-lined effl uent pond designed and built by AgFirst Engineering. Easy entry at Twin Creek Dairy. Landmore Agri project manager Matt King in front of the 16-tonne feed silo which supplies meal to dispensers in the sheep milking shed.
Takanini Feeds’ business development manager Clare Burndred with some tasty treats on offer for the Twin Creek Dairy fl ock.
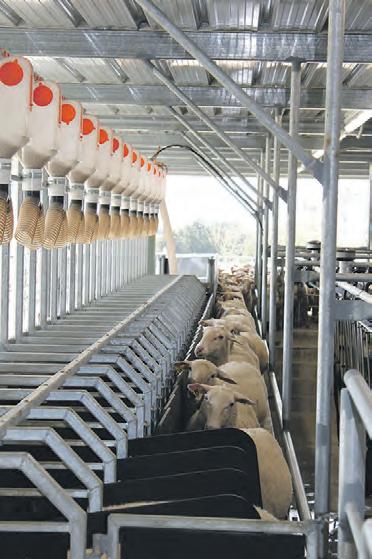

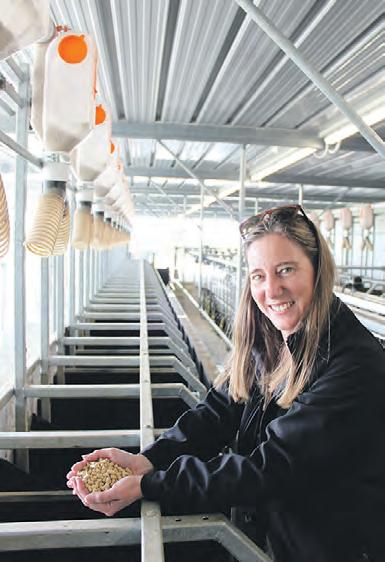
Davieth says the pond provides a month’s storage, with irrigation to pasture from it undertaken on one day a month.
A high-capacity PTO pump feeds a travelling rain gun with 35 cubic metres of material an hour.
Pond setup
The pond liner was provided and installed by Auckland-based Viking Containment.
Brent Whitehead, head of company sales and installation, says the liner required 1000 square metres of high-density polyethylene.
Made in Malaysia, the material comes in 1.7 tonne rolls, with the Twin Creek Dairy project using just under a full roll, says Brent.
Eight-metre-wide strips were welded together by a self-propelled machine which he says heats the material to 400 degree C and covers three metres a minute.
Jeff says the liner was laid on a geotechtile cushion layer covering the earth pond and anchored around its perimeter.
A team of four from Viking Containment completed the job in a day.
The feed system at Twin Creek Dairy was provided by Landmore Agri from nearby Pukekohe.
Project manager Matt King says this included a 16-tonne zinc-coated silo which supplies meal to dispensers – two per bail – in the milking shed.
The feed is transported through PVC piping by way of an auger, powered by a threephase motor.
Matt says the amount of feed is regulated by a slide control on each of the clear plastic dispensers in the bails.
As each row of sheep walk out after milking the dispensers are re-fi lled for the next row.
The tasty treats enjoyed by the milking fl ock at Twin Creek Dairy comes courtesy of Takanini Feeds.
Business development manager Clare Burndred says grain-based pellets were made specifi cally for the farm.
“In different seasons a different mix may be required, so we can change it to suit.”
Sweet treat
A 12-tonne load of the feed is sent out to the Pukekohe property every 2-3 weeks, says Clare.
Takanini Feeds also provides the Wallaces with bagged feed for the lambs – a type of muesli with molasses.
With the added sweetener, Clare says the youngsters do not require a lot of training to tuck in.
She says the amount and type of feed prescribed for the milking fl ock is based on aspects including the amount of pasture available and the season of the year.
“You have a base pellet, which can be adjusted with different ingredients,” says Clare.
The milking shed at Twin Creek Dairy was built by Morrinsville-based Don Chapman Waikato.
Director Shanan White says his team developed the facility on the greenfi eld site around the existing bails brought across from Karaka by James Wallace.
“The shed specs were to accommodate the bails,” he says.
The shape
A rectangular yard was built, linking with new and existing farm races, to provide a good fl ow to and from the milking area.
Shanan says the pit has an overhanging lip to cover water and cabling systems, also catering for any future expansion/changes in technology.
With four staff on site, his company’s role also included construction of the new milk-room and offi ce at Twin Creek Dairy.
Milking equipment was provided by Waikato Milking Systems.
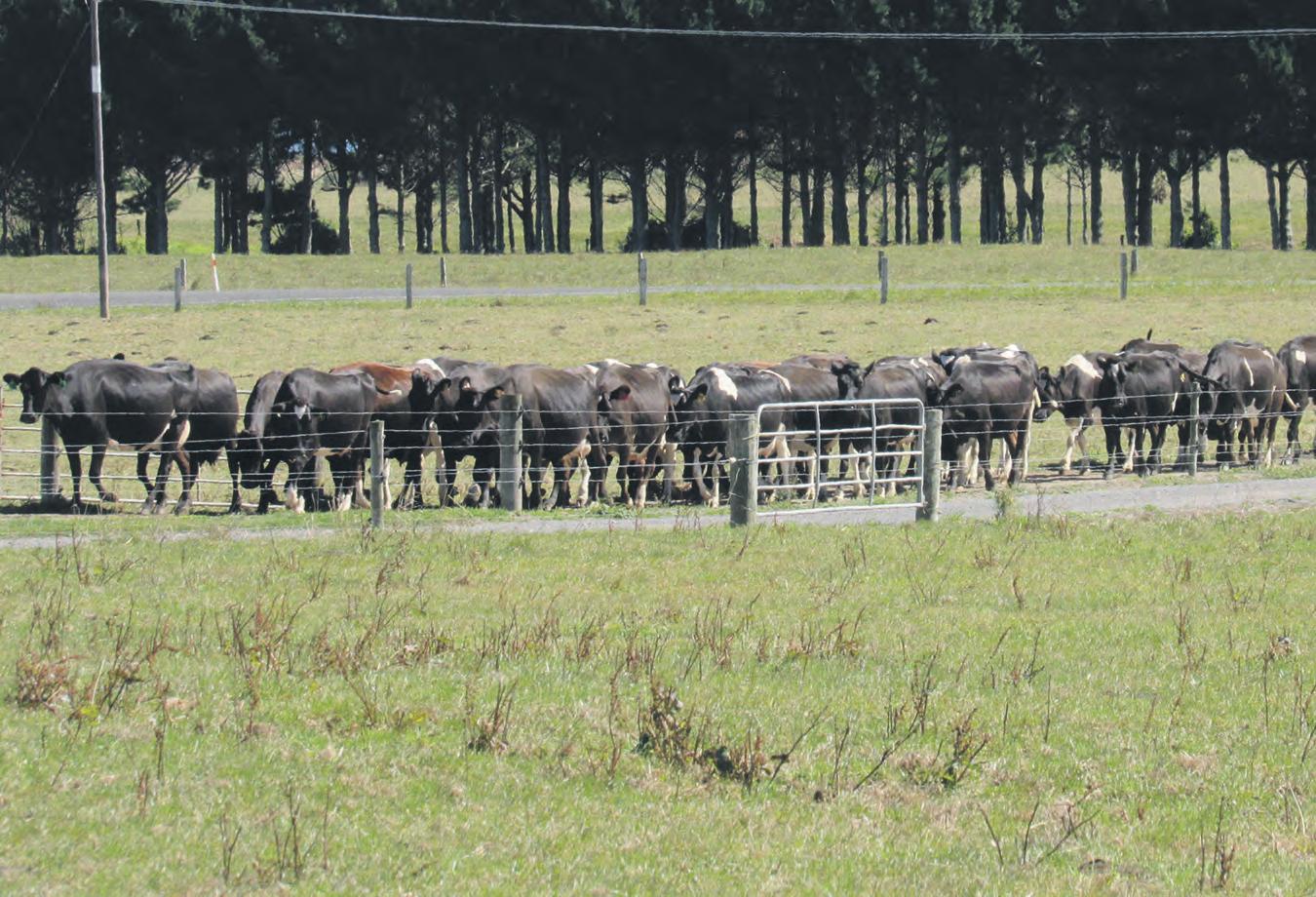
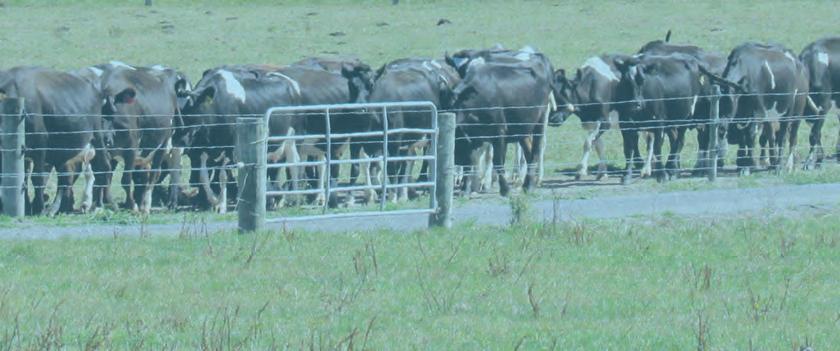
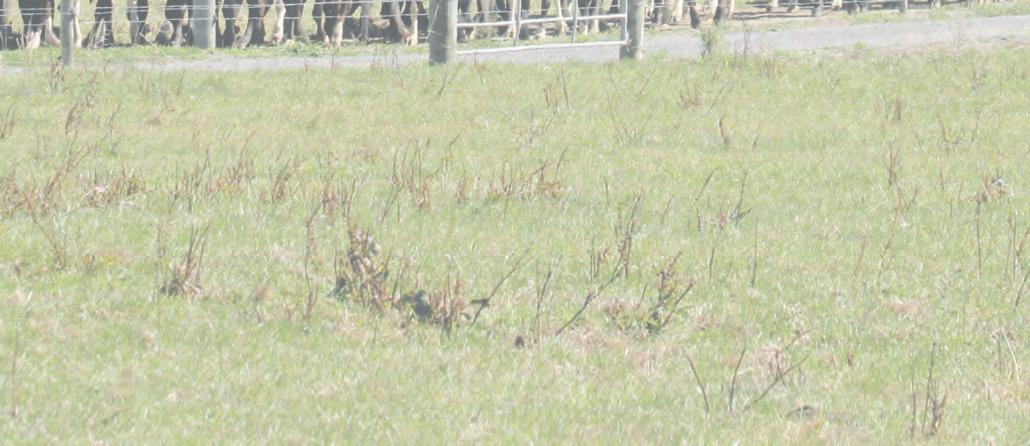

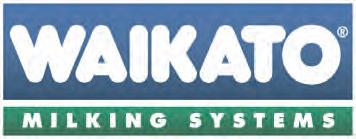
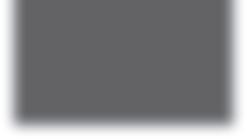
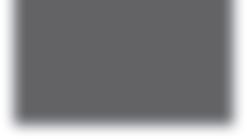


The lambing shed can hold up to 600 lambs. Milking time with staff member Fiona Libeau. Staff member Abbie concentrating on the job at hand.
Don Chapman Waikato director Shanan White in front of the Wallace shed.
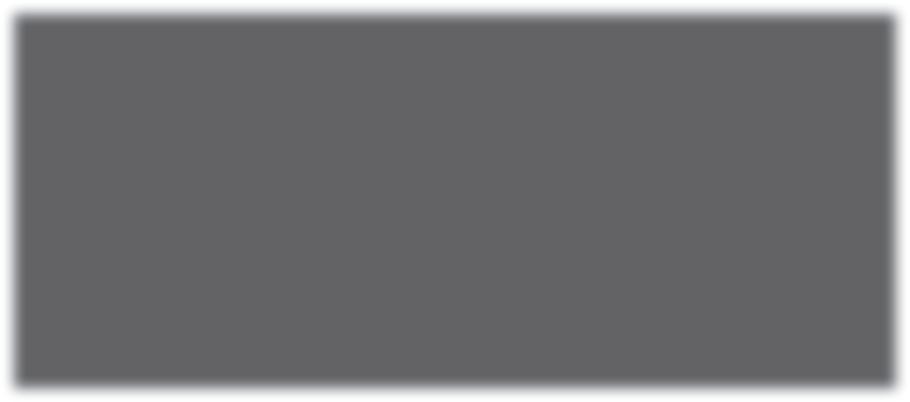
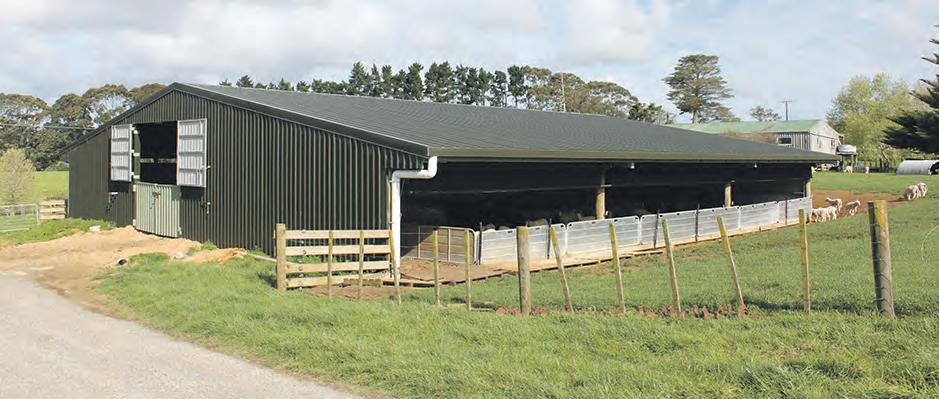


Waikato/Northland sales manager Gary Feeney says it was during Covid lockdown when WMS was asked to price a basic swingover milking system for James Wallace.
He says the milking machine is a standard 30 swing-over with ITP sheep clusters and a 76mm milk line.
“We included a blank section of milk line, enabling James to increase to 40 sets in the future.”
Gary says the pulsator airline is 63mm, with WMS pulsation running at 180ppm at a 50:50 ratio.
The receiving can and sanitary trap are a 90L/60L combination, while the main air line is 76mm.
He says James requested a fl exible impellor milk pump controlled by a 2.2kW variable speed drive.
Milk fi ltration is via a WMS Maxi fi lter and cooling via a 7000L Sondex double bank PHE.
The vacuum system is a BP400 blower type vacuum pump controlled by a 15kW variablespeed drive, says Gary.
“A point of difference with WMS is the use of stainless steel for all milk and air lines. The standard option for fi ltered air is PVC (as this is atmospheric pressure) however this can be stainless steel if requested.
Covid impact
“Covid did produce some challenges, as I’m sure other service providers have experienced,” says Gary. “It did necessitate having a ‘Plan B’ and in some cases a ‘Plan C’ and a lot of afterhours organising.”
“The end result is a simplistic, easy-to-use mono slope sheep herringbone.”
All electrical work was undertaken by Pukekohe-based EW Electrical.
Director Eamonn Wallbutton says this included a new switchboard linked to a PTOdriven generator, which acts as a back up in case of power failure on the property.
EW handled all electrical requirements in the pit, plant room and offi ce.
Out in the milking area, EW fi tted the general power and lighting systems required.
Eamonn says his team also worked on the control panel and associated wiring for the vat and chiller units.
Refrigeration and compressor units were brought over from the Karaka property and wired-in by EW.
Eamonn says 2-5 staff worked on site for about 260 hours from mid-May to mid-August.
Blank canvas
This was the fi rst sheep dairy operation EW has tackled and he pretty much started with a blank canva” at the Wallace property.
James Wallace says EW Electrical was always one step ahead of the rest and completed a tidy, effi cient job ahead of schedule.
The 45kVA generator was supplied by Norwood Pukekohe.
Dealership manager Andrew Jameson says the Italian-made device is powered by a tractor PTO, with 1500rpm producing 50Hz.
“You power up the tractor and lights are green,” says Andrew. “It is pretty fool-proof.”
He says the generator is a sound back-up to the regular power supply on the Wallace property.
“It’s something farmers should be thinking about.”
Pit walls were fi nished courtesy of Acrafl ex Specialised Coatings from Waiuku.
Director and franchise-holder Bruce Cameron says the long-lasting, easy clean coating is acrylic-based with a special glaze.
It is also resistant to alkalis and acids, he says.
Bruce says the material is sprayed on then rolled and sprayed again.
“It’s equivalent to about 10 coats of paint.”
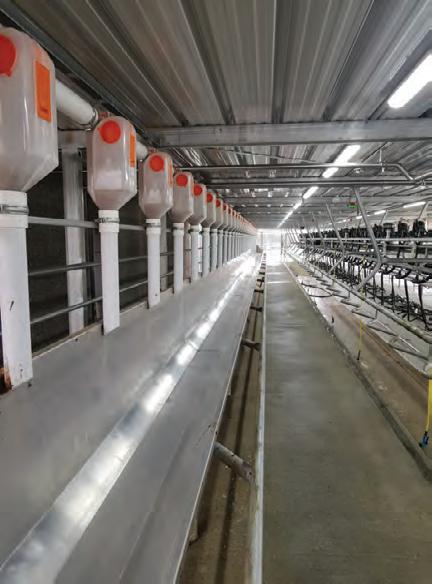
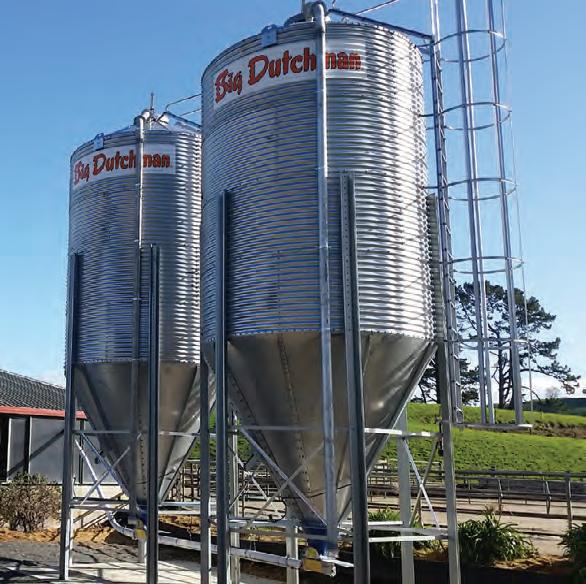
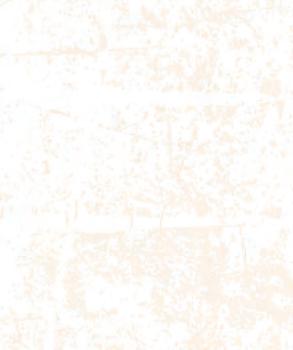
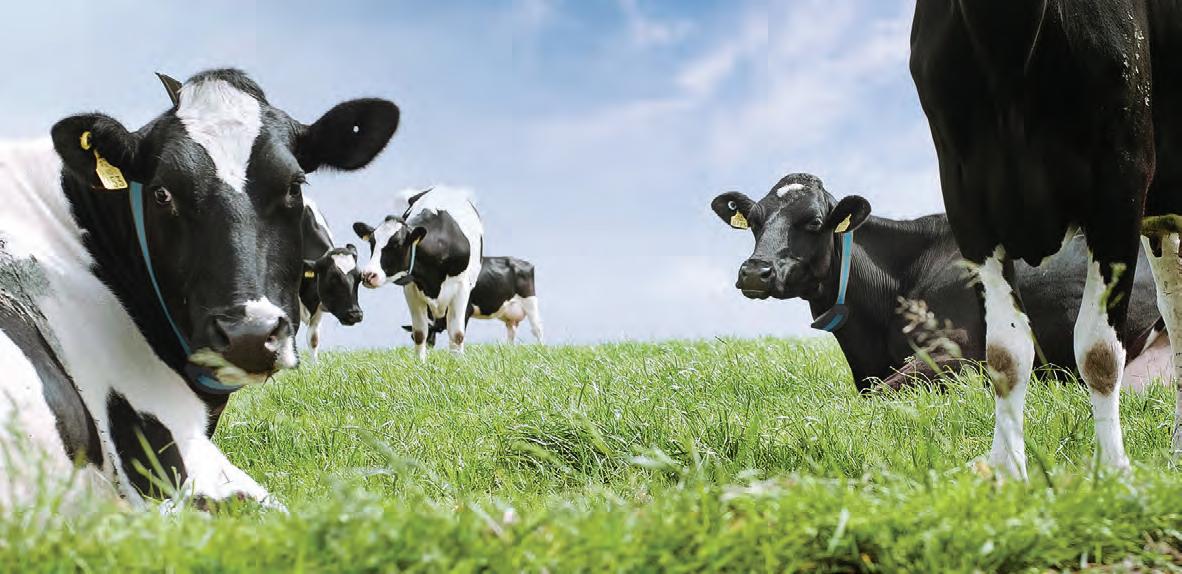

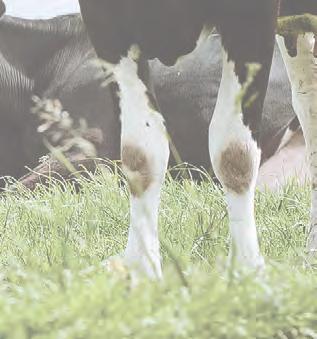
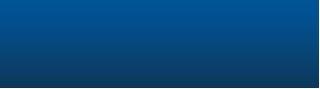


THINKING OF INSTALLING A DAIRY MEAL FEEDING SYSTEM?
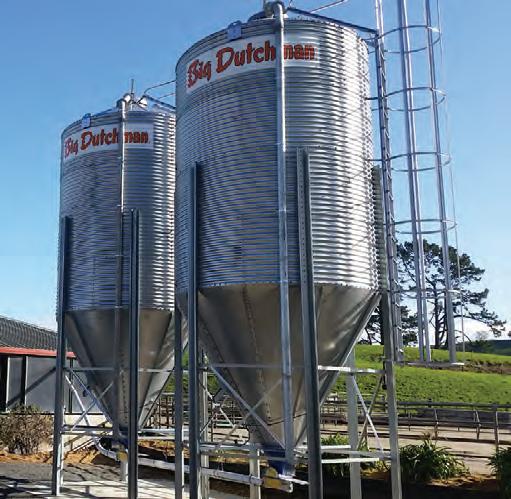

FREE • Ability to manage feed intake per cow with individual dispensers • Improved shed flow • Strong reliable system MEASURE & QUOTE • Labour efficient feeding • Ability to add minerals to feed For more information phone
• Ability to manage feed intake per cow with individual dispensers FREE • Improved shed flow • Strong reliable system MEASURE • Labour efficient feeding • Ability to add minerals to feed & QUOTE For more information phone
FREE MEASURE & QUOTE
For more information phone 07 873 8900 www.landmore.co.nz 07 873 8900 www.landmore.co.nz 4 Ranfurly St, Otorohanga For more information phone 07 873 8900 www.landmore.co.nz 4 Ranfurly St, Otorohanga For more information phone 07 873 8900 www.landmore.co.nz 4 Ranfurly St, Otorohanga 07 873 8900 www.landmore.co.nz 4 Ranfurly St, Otorohanga For more information phone 07 873 8900 www.landmore.co.nz 4 Ranfurly St, Otorohanga 4 Ranfurly St, Otorohanga
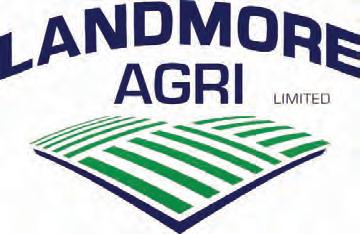