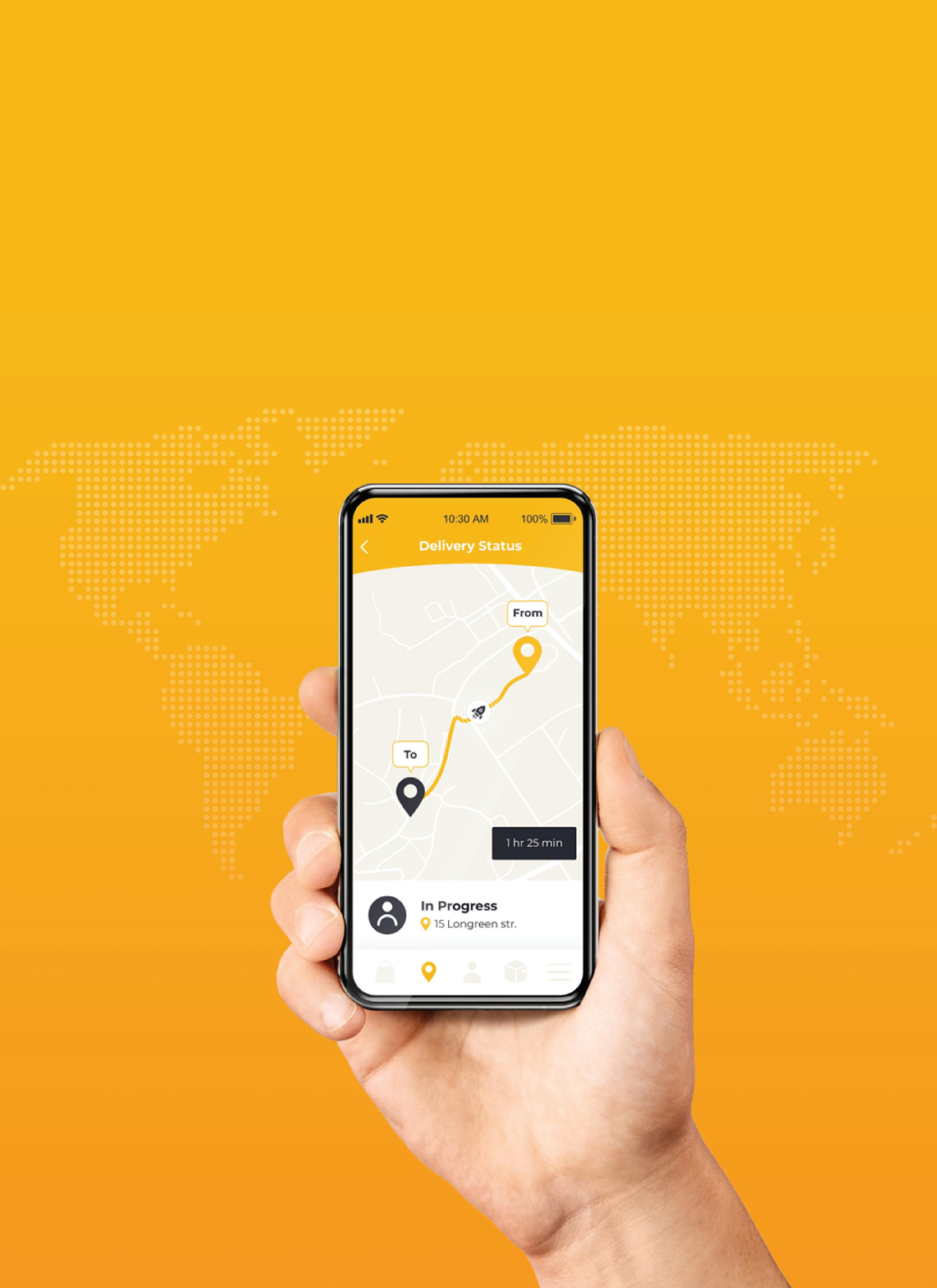

Tania Walters Publisher tania@reviewmags.com
Coperational efficiencies and meet environmental responsibilities. Innovations, such as AI, blockchain, and renewable energy sources, are making it easier to manage the complexities of cold chain shipping while reducing waste and ensuring product quality. Tech breakthroughs like
AI and data analytics are reshaping cold chain logistics, providing operators with real-time monitoring and predictive insights. This shift allows companies to proactively address issues before they escalate, enhancing supply chain visibility and improving the reliability of transporting perishable goods.
Sustainability is integral to cold chain operations, and there has been a notable shift towards renewable energy, sustainable packaging, and electric transportation.
Consumer demand for sustainably sourced and packaged products is influencing industry practices, prompting companies to adopt green technologies in transport and warehousing. In this issue, we look at the sector's challenges, customer demands and what's ahead in 2025.
old chain logistics is a key pillar of global supply chains as brands depend on these systems to deliver temperature-sensitive goods like fresh food. In 2024, the sector has seen tech advancements and sustainability initiatives introduced to enhance 11 8 14 25
PUBLISHER Tania Walters
GENERAL MANAGER Kieran Mitchell
BRAND MANAGER Sarah Mitchell
EDITOR-IN-CHIEF Caitlan Mitchell
EDITORIAL ASSOCIATES Jenelle Sequeira, Sam Francks
ADVERTISING SALES info@reviewmags.com
SENIOR DESIGNER Raymund Sarmiento
GRAPHIC DESIGNER Raymund Santos
Total sales of veterinary and horticultural antibiotics in New Zealand have been down for a sixth year, and the number of antibiotics considered critical for human health has almost halved in the past year.
"Antibiotics are essential for treating bacterial infections in humans, animals, and plants. But they must be used responsibly to prevent antimicrobial resistance (AMR)," said New Zealand Food Safety acting deputydirector general Jenny Bishop.
"AMR happens when germs develop the ability to resist the medicines designed to kill them.
The World Health Organization has identified AMR as one of the top ten global health threats facing humanity. So, it’s vital we ensure our current antibiotics can continue to be used.”
These results, released in the latest Antibiotic Agricultural Compound Sales Analysis, are clear signs that antibiotics have been used more carefully.
"They are a direct result of the concerted effort by veterinarians, farmers, industry and New Zealand Food Safety to ensure these life-saving medicines are used appropriately so they stay effective."
Read more here
Wine science researchers from the University of Adelaide have found that a tailor-made polymer developed in New Zealand could be key to removing smoke taint in wine.
Wildfires have been a billion-dollar problem and an ongoing threat to vineyards. Wines made from grapes exposed to smoke result in an acrid, ashy aroma, taste, and mouthfeel that compromises quality and reduces the value to the point that they are often unsaleable.
Ideally, to remediate smoke-tainted wine, the molecules responsible need to be reduced without removing desirable elements that contribute to the wine’s composition, colour, and flavour.
Professor of Oenology Kerry Wilkinson and her colleagues have successfully tested a method to lessen smoke taint in wine. The method was validated using molecularly imprinted polymers (MIPs) to target removing the volatile phenols responsible for the smoke taint.
Read more here
New Zealand’s largest contestable science fund has invested in 72 new projects to address challenges, develop new technology, and support communities.
“This Endeavour Fund round being funded is focused on economic growth and commercial outputs. It involves funding more than $236 million for a range of ambitious ideas and research programmes during the next five years,” said Science, Innovation, and Technology Minister Judith Collins.
“It is crucial that this investment is targeted to deliver value for New Zealand and that is why this investment round focuses on economic outcomes.”
Collins said that scientists in New Zealand have been conducting exciting research. They are devising new ways of approaching and combatting problems in areas of critical need for New Zealand, such as making technology more efficient, improving resilience, and responding to global weather changes.
Read more here
Regulation Minister David Seymour, Environment Minister Penny Simmonds, and Food Safety Minister Andrew Hoggard have welcomed interest in the regulatory review of agricultural and horticultural products.
The Ministry for Regulation's review looks at how to speed up the process of gaining farmers' and growers' access to the safe, innovative products they need to remain competitive.
The Ministry has received 80 comprehensive written submissions and has met with more than 50 representative groups and companies representing agricultural and
horticultural primary producers, major exporters, product producers, and other interested parties.
There are too many delays, and the process is too complex. It stops farmers and growers from accessing products approved by other OECD countries.
“One business I visited described the current process to me as like being in the ice cream queue behind a family of 13 because all applications –changes and new products – are in the same line. It all just takes too long,” said Seymour. Read more here
Science, Innovation, and Technology Minister Judith Collins announced a programme to drive the uptake of Artificial Intelligence (AI) among New Zealand businesses.
The AI Activator will unlock AI's potential for New Zealand businesses through a range of support, including access to AI research experts, technical assistance, AI tools and resources, and funding and grant options.
AI will contribute $76 billion to New Zealand’s GDP by 2038. As the rest of the world rapidly adopts this technology, it is crucial to support businesses in improving their awareness and uptake of AI to capitalise on its benefits.
Read more here
Synlait has completed the strategic review of its North Island assets, including its manufacturing facility in Pōkeno and its blending and canning facility in Auckland.
The review was undertaken as part of Synlait’s business recovery plan. It explored a wide range of factors, including potential ownership structures, mothballing the Pōkeno plant, and how to balance its capability to process both dairy and plantbased proteins.
“The review has been detailed and thorough. It’s given us the insight needed to lift the financial performance of these
world-class assets. We now have a pathway to ensure our North Island operations will be profitable in the future," commented Synlait CEO Grant Watson.
One of the review’s findings was that switching between processing dairy and nondairy hybrid nutrition products hinders the Pōkeno’s plant’s operational efficiency.
In addition, it found that transportation and a number of manufacturing costs mean it’s not financially viable for Synlait to keep processing milk at Pōkeno.
Read more here
DHL unveiled its 7th edition of the DHL Logistics Trend Radar as the logistics landscape has evolved rapidly.
Since its inception in 2012, the report has provided an in-depth analysis of logistics trends, their impact, progression, and associated challenges and opportunities. For each of the 40 trends, 17 social and business and 23 technological, the radar outlined the predicted time to adoption and their impact on logistics.
While trend clusters like robotics, the Internet of Things, and digital backbone have continued to affect logistics significantly, it has been evident that the emerging field of AI
has been making an increasingly substantial contribution and that sustainability has remained a top priority.
“The DHL Logistics Trend Radar is an invaluable strategic resource for our customers and logistics community,” said Katja Busch, CCO and Head of DHL Customer Solutions & Innovation.
“It consolidates key logistics trends, with AI and sustainability taking the lead in this edition, driving the evolution of businesses, consumers, and technologies over the next decade. This empowers our customers and us to stay competitive in a demanding landscape.”
Read more here
Costa Coffee stores across the UK will provide free coffee pod drop-off points and Podback recycling bags for a five-month trial.
Costa Coffee has announced a new trial collaboration with Podback, a UK-wide coffee pod recycling service, to offer coffee pod recycling in 142 Costa Coffee stores across the UK.
During the trial, customers
can pick up free Podback recycling bags in-store and return them once full for Podback to collect and recycle.
Customers will be able to pick up free Podback bags from baristas in all Costa Coffee stores located within Tesco stores across the UK, then take back their full bags for recycling.
Read more here
The Infinigate Group, the leading technology platform and trusted advisor in cybersecurity, cloud and network infrastructure, has made a strategic investment in Wavelink, a fast-growing IT distributor specialising in cybersecurity and mobility, with strong credentials in the Australian market. The investment provides Infinigate with a solid entry into the Australia and New Zealand (ANZ) market, as part of the company’s global expansion.
The partnership between Infinigate and Wavelink is designed to fuel both organisations’ growth plans. Infinigate gains a majority stake in Wavelink, who will continue to operate autonomously with the existing management team, retaining a significant share of the business. The agreement was sealed on 4 July, with immediate effect.
Read more here
In February 2025, Maersk A/S (Maersk), an entity under A.P. Moller–Maersk, and HapagLloyd AG (Hapag-Lloyd) will launch their operational collaboration, Gemini Cooperation.
Once fully phased in, the ambition is to deliver a flexible and interconnected ocean network with industry-leading schedule reliability above 90 percent.
Since the two companies unveiled the new long-term collaboration in January 2024, they have been working on
finalising the details of the operational collaboration, which covered a joint ocean freight network on East-West trades.
With around five months to launch, Maersk and HapagLloyd have shared an update covering finalised service maps and how the network has evolved since the announcement in January 2024. The companies also presented an alternative Cape of Good Hope network due to the on-going disruptions in the Red Sea.
Read more here
HIFOOD has been recognised at the Global Food Industry award at the 22nd World Congress of Food Science and Technology, held in Rimini, Italy.
At the 22nd World Congress of Food Science and Technology, held in Rimini from September 8th to 12th, HIFOOD, a company part of the CSM Ingredients group that specialises in the research, development, and production of natural-origin ingredients, won the Global Food Industry Award in the “Most Innovative Process” category thanks to Micro Protein, a new range of micronized plant-based, allergen-free, and clean-label proteins. This solution also ranked as a finalist in the “Most Innovative Ingredient” category.
Read more here
Further strengthening its international senior leadership team, Alto-Shaam has welcomed two industry leaders as it navigates the future.
Alto-Shaam, a global leader and innovator in the foodservice equipment industry, has further strengthened its international team across the Asia Pacific (APAC) region with two senior appointments.
Adil Parkar has been appointed as India Subcontinent Commercial Leader. In his new role, Parkar will lead, oversee and drive the sales function, implementing effective sales strategies to capture market share and achieve revenue targets in the region. He will also cultivate and maintain relationships with key clients,
stakeholders, and partners to further enhance market presence across the APAC region.
Parkar has joined Alto-Shaam with more than 20 years of experience within the hospitality and foodservice equipment industry. Prior to joining Alto-Shaam, he was the Key Accounts Manager for Unox India, and then Unox Arabia.
Reporting directly into Parkar, Alto-Shaam has appointed Dipali Shevate as Alto-Shaam's new Senior Business and Customer Service Specialist. Shevate will bring over 10 years of experience in order management and fulfilment in sales coordination, customer service, supply chain, manufacturing and the commercial industry.
Read more here
Refrigerated cargo logistics is a field where precision, reliability, and efficiency are not just advantages but necessities.
The stakes are high when transporting perishable goods like protein, dairy, seafood, and fresh produce. These products require exacting care to ensure they arrive in perfect condition. For over 30 years, Urgent Couriers has been a leader in this space, offering solutions that meet and exceed industry expectations, delivering tangible benefits to our clients.
When you choose Urgent Couriers for your refrigerated logistics needs, you’re choosing peace of mind. Our advanced live tracking system provides real-time updates on the status of your shipments, so you’re never left in the dark. No more guessing where your goods are or worrying about potential delays. You can see exactly where your cargo is at every stage of its journey, allowing you to manage your operations more effectively and ensure that your products reach their destination on time.
SAVE TIME AND REDUCE
Managing the logistics of perishable goods can be time-consuming and stressful. With Urgent Couriers, we take that burden off your shoulders. Our worldleading error rates mean you can trust that
your shipments will be handled carefully, reducing the risk of costly mistakes and delays. This reliability level saves you time and minimises the stress associated with managing complex supply chains. You can focus on growing your business, confident that your logistics are safe.
Your customers expect the best; with Urgent Couriers, that’s precisely what they’ll get. Our commitment to excellence ensures that your products arrive fresh, safe, and on time, contributing to higher customer satisfaction. Happy customers mean repeat business, and with our proven track record, you can be sure that your reputation is in good hands.
Choosing Urgent Couriers also means choosing a partner committed to sustainability. As the first carbon-neutral transport company in New Zealand, we help you meet your environmental goals without compromising service quality. In today’s market, sustainability is not just a nice-to-have—it’s a critical factor that can enhance your brand’s reputation and appeal to eco-conscious consumers.
At Urgent Couriers, we’re more than just a logistics provider—we’re your partner in success. Whether you’re a small distributor or a large exporter, our tailored solutions are designed to meet your specific needs. With our expertise, technology, and dedication, we ensure that your refrigerated goods are transported efficiently, safely, and sustainably. When you choose Urgent Couriers, you’re choosing more than just a delivery service. You’re choosing a partner to help you save time, reduce stress, satisfy your customers, and protect your brand. Let us take care of your logistics so you can focus on what you do best—growing your business. Join us and experience the difference that over 30 years of industry leadership can make.
With a sustainable and energy-efficient future in mind, AoFrio has introduced AoFrio INSIDE, an eco-focused solution for refrigeration systems.
The refrigeration sector has been responsible for ten percent of global carbon emissions and consumes 17 percent of the world's electricity. This, combined with releasing harmful greenhouse gases, has made the refrigeration sector a significant contributor to climate change.
AoFrio INSIDE helps reduce fleet energy consumption and carbon emissions. Externally validated by independent refrigeration testing specialists Re/GenT against standard refrigeration systems, the high-efficiency hardware and software package has contributed to overall energy reductions.
It also gives customers a dashboard view of their assets’ real-time energy usage,
enabling fast and accurate fleet-wide reporting.
“AoFrio INSIDE is a game-changer. It contributes to potential energy savings of up to 64 percent, significantly reduces carbon emissions, and provides real-time reporting and actionable insights on further improvements,” said Greg Balla, CEO of AoFrio.
“This solution empowers our customers to reduce their environmental impact and enhance their profitability. Refrigeration is much more than keeping food and drinks at the optimal serving temperature; it's about driving a more sustainable industry for generations.
Last year, the environmentally safe technology earned global acclaim by
winning the ‘Incremental Change in Energy Efficiency’ award at The Cool Challenge, an initiative led by the Beverage Industry Environmental Roundtable.
As a hardware-enabled SaaS company, AoFrio’s mission has been to lead the charge towards a more sustainable and efficient food and beverage industry.
With over 2.7 million coolers connected to the AoFrio cloud and over eight years of actionable data acquired, AoFrio has provided solutions to its customers to keep food and drinks fresh and safe at the point of sale.
Global beverage brands such as CocaCola, Pepsi, and Heineken already use its technology to manage their fleets of commercial bottle coolers.
Sunswap, a UK clean-tech startup decarbonising cold chain logistics, has secured £17.3 million through a funding round led by investment company BGF to accelerate the rollout of its zero-emission transport refrigeration technology across the UK and Europe.
Sunswap’s pioneering combined solar and battery technology has fitted the trailer units of articulated lorries carrying chilled consumer goods throughout the European road transport network, providing a low-carbon alternative to diesel-powered refrigeration.
The £17.3m invested by Shell Ventures, Dutch venture capital fund Move Energy, and existing backers Barclays and Clean Growth Fund will accelerate Sunswap’s zero-emission Transport Refrigeration Units (TRUs) development and production.
“We are thrilled to have BGF and Shell Ventures support our mission to decarbonise cold chain logistics. Their investment, alongside the continued backing of our existing investors, is a real validation of Sunswap’s journey to date. This funding will accelerate our growth and expand our presence in the UK and European markets,” said Michael Lowe, cofounder and CEO of Sunswap.
“It will enable us to ramp up production,
support further customer trials, and invest in developing our zero-emission technology. Together, we will work towards a cleaner, greener future for cold chain logistics, helping businesses meet their sustainability targets.”
Sunswap’s “Endurance” TRU has been a breakthrough fully electric solution that eliminated tailpipe carbon emissions while providing a viable, cost-effective alternative to traditional diesel units.
Endurance has seamlessly enabled fleet operators to transition to zero-emission refrigeration without compromise by combining advanced battery technology, solar power, and rapid charging.
Operators can monitor and control units by installing solar panels on the trailer roof and a cloud-based telematics system, delivering high performance and significant operational savings.
Sunswap’s technology has undergone rigorous commercial trials with industry leaders such as Tesco and Muller, demonstrating superior performance and
lower total ownership cost than traditional diesel units.
The business has a growing customer book, including equipment services provider TIP Group, shipping and logistics giant DFDS, and leading UK operators. Funding will be used to expand production to meet growing customer interest, increase a nationwide service network, and further advance technological development as the business capitalises on significant market opportunities in the UK and Europe for cleaner, more sustainable transport solutions.
Rowan Bird, investor at BGF, said Sunswap’s TRU technology stood out as a leading solution for fleet operators seeking to reduce their carbon footprint and operational costs as the logistics industry moved towards more sustainable practices. With this investment, Sunswap will accelerate the decarbonisation of cold chain logistics and rapidly transition the industry away from highly polluting legacy technology.
The Korea Institute of Energy Research (KIER) has developed a refrigeration technology that uses air instead of Freon gas, hydrofluorocarbons (HFCs), and other refrigerants that cause global warming.
The European Union’s revised regulation on fluorinated greenhouse gases (F-gases) took effect in March this year. Starting in 2025, the sales of products containing F-gases will be gradually phased out, and regulations on processes using F-gases are expected to be strengthened.
Since F-gases have been used in critical Korean export products such as air conditioners, automobiles, and semiconductor processes, alternative technologies must be developed urgently.
The research team successfully developed an integrated ultra-high-speed compander used in air refrigeration to create an air cooling system. This system has enabled a temperature environment of -60 degrees Celsius using air as a refrigerant.
Traditional refrigeration and cooling systems have primarily used the vapour compression cycle, which achieves cooling as the liquid refrigerant evaporates and absorbs heat.
Due to its simple structure and design, it has been widely used across various fields. However, a key drawback has been its dependence on fluorinated greenhouse gases as coolants, leading to the impact of global warming.
In response, the research team focused on implementing a cooling system based on the reverse-Brayton cycle, which uses air as the refrigerant. Unlike the traditional liquid evaporating method, this system compresses a gas. Then, it goes through heat exchange and expansion to produce a low-temperature gas, enabling cooling
without needing liquid refrigerants.
However, the complexity of designing and building such a system has been a significant challenge, preventing its application in refrigeration systems until now. The compander must be designed with extreme precision due to the ultra-highspeed rotation during the cooling process. For instance, the gaps between components and shaft displacement require a tolerance within 0.1 millimetres.
To implement the reverse-Brayton cycle system, the research team devised a compander system that connected the compressor, expander, and motor on a single shaft. Although the compressor and expander have been connected to a single shaft, each device must operate at its maximum efficiency.
The shaft system design ensured stable operation even at ultra-high rotational speeds, further enhancing the system's reliability and performance. The cooling system utilising the developed compander successfully cooled air to below -60 degrees Celsius within one hour.
Notably, the system demonstrated higher refrigeration efficiency when generating cold temperatures below -50 degrees Celsius than traditional vapour compression systems.
Theoretically, it can cool down to -100 degrees Celsius; at that temperature, the refrigeration efficiency is expected to improve by more than 50 percent compared to vapour compression systems.
"Due to environmental regulations, refrigeration systems that primarily use
refrigerants with a high global warming potential are rapidly transitioning to ecofriendly refrigerants,” said Dr. Beom Joon Lee, lead researcher.
"We are currently working on improving the system's performance to enable the production of cold temperatures below -100 degrees Celsius. We anticipate this technology will be applied in fields requiring ultra-low temperatures, such as semiconductor processes, pharmaceuticals, and biotechnology."
This research was conducted with support from the Ministry of Science and ICT's "Climate Change Response Technology Development Project" (led by Dr. Beom Joon Lee) and the Korea Institute of Energy Research's basic research program (led by Dr. Hyung-ki Shin).
IFCO, a leading provider of reusable packaging containers (RPCs), launched Marina, the smart reusable IFCO Fish Crate. Designed closely with the fishing industry, Marina has brought protection, efficiency and sustainability to the fresh fish and seafood supply chain.
Featuring track-and-trace Bluetooth
Low Energy tags and QR codes, the Marina Fish Crate has enabled real-time data collection, improving the cold chain management of fresh and chilled products along the entire fish and seafood supply chain, from shipping to all points of sale (POS).
Single-use expanded polystyrene (EPS) boxes can break down into microplastic pollution and contaminate the marine food chain and human health, so governments worldwide have been increasingly tightening regulations and introducing EPS bans. As a result, many in the fishing industry have prioritised eliminating EPS boxes and switching to sustainable packaging.
To secure long-term higher logistics efficiency and sustainability gains for the fishing industry, wholesalers and retailers, Marina is available exclusively through the IFCO SmartCycle circular pooling system. This means that the IFCO Fish Crates are efficiently reused up to 120 times and that the empty crates are quickly returned, reused and, once they can no longer be used, sustainably recycled. IFCO ensures that the reusable fish crates are washed
according to international standards of food safety and hygiene and efficiently pooled for sharing and reuse. As required in the fishing industry, IFCO ensures a response time and delivery within 24 hours.
DESIGNED FOR AUTOMATED LOGISTICS AND THE FISHING INDUSTRY
Nestable when empty, securely stackable when full, the Marina Fish Crate saves space on ships and on shore, cutting carbon emissions in transport and improving handling conditions. Its uniform dimensions are compatible with existing supply chains, automated logistics systems and the IFCO Plastic Pallet Dora.
IFCO FISH CRATE
Francesca Amadei, Vice President Southern Europe at IFCO, highlights the unique advantages of the Marina Fish Crate: "Marina is the result of intense collaboration across the fishing industry. We’ve taken on board the unique demands of every step of the fresh fish and seafood supply chain in our R&D efforts."
“ I’m excited that we’ve succeeded in
developing a smarter, more protective and sustainable fish crate for the Mediterranean cross-border market.” - Francesca Amadei Vice President Southern Europe at IFCO
INNOVATIVE FEATURES FOR SUPERIOR PROTECTION
• IFCO optimal temperature regulation
• Double-wall isothermal construction for superior insulation at controlled temperatures, keeping products fresh for longer
IFCO ICON DIGITALISATION
• Tight-fitting lid, interlocking surfaces and easy-to-use strapping system ensures secure packing and stacking for transportation
IFCO LOCATIONS
• Track-and-trace Bluetooth Low Energy tags enable real-time data collection and analysis
RECYCLING PROCESS
• All-round sustainable packaging solution — robust, reusable, 100% recyclable — replaces single-use expanded polystyrene (EPS) boxes that can easily break down and pollute the marine environment
PRODUCT DAMAGE
• Smooth surfaces offer increased protection from damage and spoilage, cutting down on food loss and waste
CIRCULAR MODEL FOR REUSABLE, 100% RECYCLABLE FISH CRATE
The Marina Fish Crate offers a sustainable and efficient complete packaging solution. Like all IFCO Reusable Packaging Containers (RPCs) Marina uses fewer natural resources throughout its life cycle compared to single-use packaging. And, unlike conventional fish boxes made from expanded polystyrene (EPS) that
are typically sent to landfills or end up as marine pollution, Marina is 100% recycled at the end of a long service life into new products.
Inigo Canalejo, Vice President ESG and Strategic Marketing at IFCO, highlights the long-term benefits of Marina for the fishing industry and the planet:
"We see it as our responsibility to improve the environmental sustainability of every category of the fresh grocery supply chain. Our Marina Fish Crate is a smart, innovative packaging solution that will have a lasting positive impact on the fresh fish and seafood supply chain. We’re proud to have designed a sustainable and more efficient alternative to harmful expanded polystyrene containers."
With three million ice cream freezer cabinets strategically placed worldwide, Unilever has effectively leveraged AI technology to meet consumer demand.
“To win those impulse sales, our brands need to be available at the right place and time,” said Sarosh Hussain, Ice Cream’s Head of Digital Selling Systems.
“For example, if a customer breaks their journey at a petrol station to buy a Magnum and the freezer is out of stock, there’s no second chance; the sale’s lost.”
Most of Unilever’s ice cream brands have been sold by distributors, who have significant numbers of retailers to serve. Ensuring the retailers who host these freezers always have these bestsellers in stock was a key driver in equipping ice cream cabinets with AI.
Work is underway to add the tech to 30 percent of Unilever's top-selling ice cream cabinets for priority markets. To date, 100,000 freezers have been fitted with the technology to reach 350,000 in the next two years.
The software in each freezer unit has been carefully positioned to take photos only of the stock inside the freezer rather than general images of the shop. These images are taken periodically and automatically sent to the cloud, where they’re analysed by AI trained to identify only Unilever ice cream brands, analyse their depth in the cabinet, and use an algorithm to generate an order for the distributor.
“It’s like two eyes are looking at our stock
every day. It also means whenever a retail outlet asks for stock, the distributor knows from the data exactly what their freezer needs.”
Data from the AI-enabled freezers show that the uptick in retail orders and sales has been significant.
“There is no one size fits all. It varies from country to country, but we have seen incremental growth that ranges from 8 percent in Turkey to 12 percent in the US and up to 30 percent in Denmark.”
In Hungary, where almost ten percent of its freezer fleet has been AI-enabled, work has also been done to integrate the freezer’s system with those used by distributors. In addition to seeing the retailer’s regular ice cream order, distributors receive an order recommendation based on images and AI analysis of the cabinet's stock levels.
The response from distributors and retailers to these ‘recommendations’ has been positive, and close to five percent of orders have been generated from the AI system’s input during this ice cream season.
The data has also helped upskill sales teams by providing insights that allow them to understand their businesses better, cross or upsell, and make their calls more productive and proactive.
“Knowing what stock needs to be replenished before going into an outlet means the time usually taken up by the
The data has also helped upskill sales teams by providing insights that allow them to understand their businesses better, cross or upsell, and make their calls more productive and proactive.
order process can be used on tasks like new business development and merchandising. If you understand more accurately what customers want, distributors can plan their tertiary route and distribute to the outlets efficiently and cost-effectively.”
To win impulse sales, Unilever brands must be available at the right place and time. Big data from this freezer fleet has also given the company clearer insights into the performance of new product launches and marketing campaigns.
Analysing this data has provided an
understanding of whether the ice cream brand’s above-the-line campaigns have positively correlated with freezer sales and stock.
Ensuring availability and sharing of shelves is just the start of what these AIenabled freezers can do.
“If 350,000 of our freezer fleet are AIenabled, we’ll have a large enough data set to provide analytics on product visibility and supply chain strategy. And we’ll be able to grow our ice cream sales by serving our shoppers better than ever before.”
The cold chain industry is undergoing significant transformation across Oceania as businesses respond to technological advancements, environmental pressures, and a growing demand for cold storage and efficiency.
There are three key areas of change – the shift from -18°C to -15°C for frozen storage, the increased pressure to respond to the food waste crisis and the availability and use of Internet of Things (IoT) technology. Together, these trends are a glimpse into a future where accountability, sustainability, and improved processes will define the cold chain.
There is increasing interest from food manufacturers within the region, particularly in Australia, to shift frozen food transport and warehouse temperatures from -18°C to -15°C. Their expectation is that this change would deliver about ten percent energy improvement along with significant CO2 emission reductions.
This shift also supports corporate social
responsibility obligations by lowering environmental emissions. By reducing frozen storage temperatures, businesses are helping to meet global climate goals, but any such change must be carefully managed as the removal of the 3°C risk blanket has the potential to expose the industry to risks that up until now have been more apparent in the refrigerated, rather than frozen goods category. The tyranny of distance, harsh climate, variable equipment capability and other variables that influence the temperature of refrigerated goods in transit expose the fine line between safe and unsafe products. While interest in the change is increasing, a formal platform to explore the opportunity is yet to be established. The use of IoT technology in cold chain
While Australian industry and government have increased their focus on this issue, there is a lack of genuine engagement to improve the cold chain. This inertia has so set in that the Australian Food Cold Chain Council has recently announced it is closing its doors due to a continuing lack of interest and genuine engagement by key players in the sector.
logistics is helping to transform industry capability by enabling real-time temperature monitoring of products from source to destination. While the capability has existed for many years, the increasing food safety and vaccine handling requirements have seen it be deployed more expansively.
In practice, the technology provides businesses with live real-time data on conditions to which product is being exposed, serving to validate the service provided and establishing confidence in the quality of goods delivered and ultimately sold to the consumer.
The technology, when accompanying a product from farm to destination, realises what is often referred to as a cold chain of accountability, where each constituent in the chain can validate the conditions to which the product was exposed while under their control. Its use reduces the likelihood of diverting products to landfills if
temperature breaches occur. It also facilitates the identification of the true root cause of any failure and subsequent identification of required corrective action.
Well-considered procurement of IOT technology has the potential to stepchange a business's quality capability. In addition to monitoring temperatures, it affords businesses the ability to validate and improve processes and proactively manage operations, making it a key component of the food safety management plan. With this capability, it has a vital role to play in supporting a reduction in food waste and the potential transition to -15°C.
The news is not all good. Food waste across the oceanic region is considerable, both within the supply chain and at the consumer level. It’s exacerbated by a lack of cold storage, seasonal demand shortfalls, and the distance between source, storage, and distribution points.
Waste data covering the entire region is hard to come by, but in Australia alone, the government's National Food Waste Strategy of 2020 revealed that it costs the economy an estimated $36.6 billion annually, with around 7.6 million tonnes of food wasted each year. That's equivalent in weight to more than 140 Sydney Harbour bridges or enough food to feed more than a quarter of Australia's population on an annual basis. Of this, approximately 70 percent occurs before the food reaches consumers, during production, processing, and distribution. This equates to 5.32 million tonnes of wasted food, valued at $25.6 billion, highlighting the need for improvement across the industry.
While Australian industry and government have increased their focus
on this issue, there is a lack of genuine engagement to improve the cold chain.
This inertia has so set in that the Australian Food Cold Chain Council has recently announced it is closing its doors due to a continuing lack of interest and genuine engagement by key players in the sector. Reform is urgently needed but is considered a low priority by most of the industry because of the lack of government mandates covering the safety standards of cold and frozen foods.
The author, Adam Wade, is a cold chain logistics specialist, having worked at senior levels in the refrigerated consumable goods industry for more than two decades. He was a foundation director of the Australian Food Cold Chain Council. His company, Keep It Cool Consulting, applies its training, auditing, benchmarking and advisory services to help businesses across Australia and Oceania improve their cold chain processes and reach profitable compliance.
TerraCycle, an international leader in innovative sustainability solutions, creating and operating firstof-their-kind platforms, was formed to eliminate the idea of waste and move the world from a linear economy to a circular one.
With the core purpose of combating the global waste crisis, TerraCycle has tackled the issue from many angles, such as recycling the hard-to-recycle, integrating recycled materials into new products and transforming packaging from disposable to reusable.
“We provide comprehensive recycling and reuse solutions that seamlessly fit into everyday lives. We do this through partnerships with brands, retailers, manufacturers and government organisations to offer free and paid recycling solutions for hard-to-recycle waste in easy-to-access locations,” said JeanneVida Douglas, Head of Marketing and Communications at TerraCycle ANZ.
“Overconsumption and a throwaway culture have led to a global waste crisis. While even complex trash is technically recyclable, most materials are not profitable. As a result, waste piles up in landfills and pollutes our
planet while virgin materials are extracted from the earth to create new products.”
The organisation also offers free national recycling programmes sponsored by brands, manufacturers and retailers. Some examples in New Zealand include GLAD, Finish, Fairy, NESCAFÉ Dolce Gusto, Gillette, Maybelline, Schwarzkopf and Colgate, among others, to offer free recycling for everyday household packaging and products.
New Zealanders can easily access these free programs by signing up online and mailing back waste such as coffee capsules, plastic food care packaging, beauty and cosmetics packaging, and oral healthcare using a free shipping label to be recycled.
Another innovative offering from TerraCycle has been the Zero Waste Box, a comprehensive recycling solution for all waste that is not recycled through kerbside recycling services.
Zero Waste Box is ideal for the TerraCycle community and others looking to keep
Additionally, we work with retailers and supermarkets to adopt in-store recycling solutions, such as public drop-off locations for used products and packaging, right through to "Community Recycling Hubs", which enable customers to recycle multiple waste streams.
waste out of landfills and incinerators. The boxes are easy to set up, and when full, they are returned to TerraCycle for recycling using the prepaid shipping label.
As with all free and paid recycling solutions, TerraCycle guarantees that all compliant waste will be recycled into raw materials that can be used to make new products.
“TerraCycle is different. We recycle the unrecyclable–items not accepted by kerbside services because we work with brands, retailers, and other stakeholders who fund the recycling process, enabling us to offer free and paid recycling solutions.”
Douglas said it boiled down to economics and that sustainability needed to become a business's commercial priority.
“This can be achieved through legislation or by consumers showing their preference in their purchasing decisions. Every time consumers choose sustainably packaged products, they message corporations that endof-life solutions for products are essential.”
TerraCycle strictly controls the movement of materials through each part of the recycling process so that it can track and confirm where materials were sent and for what purpose. Bureau Veritas, a world leader in testing, inspection, and certification services, annually audits the collection and recycling supply chains.
The global reuse platform Loop also activates a circular economy by collaborating with brands, retailers, and manufacturers to make reuse convenient
and accessible. It enables consumers to responsibly consume various products in customised, brand-specific, durable packaging that is collected, cleaned, refilled, and reused.
This approach has encouraged packaging to be treated as an asset rather than a cost of goods to be minimised, enabling new materials, features, and consumer experiences.
“Additionally, we work with retailers and supermarkets to adopt in-store recycling solutions, such as public drop-off locations for used products and packaging, right through to “Community Recycling Hubs”, which enable customers to recycle multiple waste streams.”
TerraCycle has previously worked with The Warehouse in New Zealand to offer recycling collection hubs, Carrefour and Monoprix in Europe, Aldi and Superdrug in the UK, Aeon in Japan, and Walmart in the US.
Nowadays, demand from consumers and businesses seeking “better” products designed for reuse, repair and recyclability has grown, and legislation requires producers to contribute to the costs associated with recycling the products and packaging.
“What we expect to happen and is already happening is extended producer responsibility (EPR) legislation being introduced in more countries worldwide. EPR is a sustainability approach that holds manufacturers/suppliers responsible for their products' lifecycle.”
Some manufacturers have also taken
voluntary responsibility for their products and packaging, known as voluntary producer responsibility (VPR), such as product stewardship schemes. Douglas said that TerraCycle was proud of its partner brands for taking voluntary action against waste by investing in recycling solutions for their hardto-recycle products and packaging.
However, Douglas acknowledged that buying less was the only silver bullet solution to the global waste crisis.
“Recycling, upcycling, and reuse are essential, but they still leave a carbon footprint. Reducing our environmental impact is the best way to reduce our consumption. Consumers should always look for sustainably packaged items where possible, but ultimately, we need to consume less.”
You’ve probably heard the term “succession planning” mentioned before, and if you’re like many business owners, you might have thought, “I’ll deal with that later.” It's natural, considering succession planning is challenging on many fronts and presents a conflagration of sticky issues.
Initially, there is the realisation that you may not want or be able to own and run the business forever. Confronting the idea of stepping back, either through retirement or simply seeking a different path. This often leads to questions about what you truly want for yourself and what life might look like if you are no longer running your business. What would you do next? Would anyone else be able to take on the enormous responsibility of managing your business? And even if they could, would they actually want to? You might also begin to wonder whether selling the business would be the best course of action, or if it would be better to have someone else take on part ownership or management.
The majority of these questions are fairly confronting and big existential-type questions. Unsurprisingly, it's tempting to act like the proverbial ostrich and stick your head in the sand.
However, when done well, succession planning meets the single value shared by humanity - freedom. When achieved, it will allow you to pursue something other than running your business - the freedom to design the life you want to live. This freedom may involve still spending time in your business or fulfilling functions that bring you joy.I have always believed that a business should serve the needs and desires of its owners. You are in control, and your business will evolve in the direction you choose. However, many founders reach a point where the business takes more from them than it gives. It’s important to remember that if you feel overworked, unhappy, or stressed, you can change things.
It just requires intention and a plan.
One method I often recommend is the ICIGAI framework, which is inspired by ancient Japanese wisdom. This approach encourages you to reflect on four key areas. First, ask yourself what you excel at professionally. Consider what you genuinely love doing and what aspects of your work bring you the most fulfilment. Next, think about what the market and the world need, and how your skills or business can provide a solution. Finally, reflect on what you can be paid for. These are remarkably simple questions that, when answered, will provide you with clarity on your personal place in your business. Combining this with your business plan will allow you to map out your business's future needs, and it's an exercise that will pay huge personal dividends. Not having a succession plan in place (or one mid-way through execution) is similar to building your dream home and then neglecting its upkeep. Imagine moving into a beautiful house only to let the garden grow wild, the paint peel, and the windows gather mould. That sounds ludicrous. What about your business? You have built something meaningful and valuable; a business is a complex organism, so why wouldn't you maintain it?
If you have reached the point of considering what life is all about and what it all means for you, you represent a small percentage of business owners who even consider succession planning. Succession planning isn’t always a loud, urgent matter—it often starts as a quiet whisper. You might begin to feel a growing dissatisfaction with how you’re spending your time in the business. Perhaps you’ve found yourself looking at other industries with a sense of curiosity or even envy. Maybe you’ve started longing for something more, a different way to spend your days. When it comes to succession, there are four main types of exit: strategic, acquihire, economic, and succession. In terms of succession, you typically have three main options. First, you could sell the business to your employees, executives, or management team in what’s known as a management buy-out. Another option would be to sell your share to your partners. Finally, you could pass the business on to a family member, whether that’s a sibling or your children. Succession doesn’t always
mean a complete exit—you may choose to retain some ownership while passing the responsibility of running the business to someone else. Each of these options offers the opportunity to create distance between yourself and the business, allowing you to experience more freedom in your personal and professional life.
In his book The E-Myth, Michael Gerber highlights the importance of building systems that ensure both the success of your business and your own peace of mind. Gerber suggests that most entrepreneurs feel like entrepreneurs for only a brief moment before they’re pulled back into their core roles— whether as a manager, a salesperson, or a technician. This may help you understand the area you need to build skills in.
As you begin your succession planning journey, it’s important to consider key questions. First, think about what your life will look like after you’ve made your exit. Where will you spend your time, and what will your days involve? Reflect on what kind of involvement, if any, you’d like to have with the business once you step back. And finally, consider the practicalities: when is the right time to start planning, and if it’s not going to be you, then who will take over? Should you hire, sell, or promote someone from within?
Succession planning can feel like a daunting task, but it’s a necessary one if you want to secure both the future of your business and your own personal fulfilment.
For more in-depth guidance, my e-book The Exit Factor breaks down the various types of business exits—strategic, acquisition, economic, and succession—into clear, actionable steps.
JOSH COMRIE josh@joshcomrie.com www.joshcomrie.com
Consumer preference for convenience in food and drink in Australia and New Zealand is significantly influenced by technology and the desire for time-saving solutions. Mintel’s 2024 Food and Drink Trend ‘Eating, Optimised’ notes that a new era of convenience is dawning as technology streamlines meal planning, shopping and cooking.
Here are some key insights and opportunities for brands based on the 'Eating Optimised' trend:
TECHNOLOGICAL INTEGRATION:
Consumers in Australia and New Zealand are increasingly trusting and interested in emerging technologies to help them optimise their meal planning, shopping, and cooking. For instance, 48 percent of Australians and 46 percent of New Zealanders believe that artificial intelligence will make daily chores easier, such as time-saving tips for cooking and cleaning, according to Mintel Global Consumer research. This indicates a strong opportunity for brands to integrate AI and other hightech tools to streamline these processes.
Retailers can enhance the shopping experience by offering real-time shopping assistance through push notifications, personalised alerts, and AI to help consumers find ingredients or products they would like while in stores, in transit, or shopping online. This can help consumers navigate their shopping more efficiently and make informed decisions.
CONVENIENCE IN MEAL
A significant portion of consumers find meal planning and preparation challenging. For example, Mintel data shows that 35 percent of Australian consumers agree that it is hard to decide what to make for meals, and 21 percent of New Zealand consumers consider preparing meals a chore they dread. Brands can address this by offering products that simplify meal choices and preparation, such as pre-prepared meal kits or easy-tofollow recipe suggestions.
Convenience is also a key value indicator for consumers. In New Zealand, 27 percent of consumers agree that being easier to
prepare than other products is a value indicator in food and drink. This suggests that products that save time and effort in the kitchen are increasingly valued.
There is a strong interest in personalised product recommendations based on shopping history, particularly among younger generations. For instance, 40 percent of New Zealand consumers aged 25-34 have either tired or are interested in food and drink innovations tailored to their specific needs (based on diet or activity data they share). Brands can leverage data analytics and AI to provide personalised shopping experiences.
Overall, Mintel 2024 Food and Drink Trend 'Eating Optimised' highlights the importance of convenience and the role of technology in enhancing consumer
experiences in food and drink. Brands that can effectively integrate AI and other technologies to offer seamless, time-saving, and personalised solutions are likely to resonate well with consumers in Australia and New Zealand.
*All consumer data mentioned above are from Mintel Global Consumer research.
Epson has launched its newest on-demand colour inkjet label printer –the ColorWorks C8010.
Purpose-built for mid- to highvolume batch runs in on-demand environments, the 4-inch ColorWorks C8010 has been engineered for exceptional print quality, reliable performance, and high-speed printing with advanced connectivity and cloud printing, allowing businesses to print almost any label.
Colour labelling has been used across various applications to improve efficiency, quality, and customisation. The new ColorWorks C8010 helps companies eliminate multi-step printing processes and stockpile pre-printed colour label rolls to print state-of-the-art, high-quality labels in real-time.
The ColorWorks C8010 has been designed to meet the high-volume label
production needs of businesses in several markets, including prime and boutique, product ID, warehousing, and logistics.
The powerful printer features advanced PrecisionCore Heat-Free technology, combining exceptional image quality and sharp precision at incredible speeds. It can print multiple labels with variable data at speeds up to 30.48 cm per second.
The PrecisionCore permanent printhead requires fewer interventions and has low maintenance costs, making it ideal for busy, on-demand environments.
Durable, high-performance UltraChrome DL pigment inks provide high-quality, long-lasting labels that resist smudging, smearing and fading. Customers can choose between Gloss and Matte Black ink to fit labelling needs.
New high-capacity ink packs are ideal for high-volume batch runs. They allow for fewer interventions and offer low cost per millilitre and low consumable waste.
Advanced connectivity, such as cloud printing and optional Wi-Fi, helps to maximise workflow. Epson Cloud Solution PORT2 offers remote management for powerful fleet productivity to improve efficiency and optimise printer workflow, including viewing printer status, ink consumption, and operation history.
Epson ColorWorks on-demand label printers have been designed to help businesses print as many labels as possible.
The ColorWorks C8010 colour inkjet label printer is now available through Epson's authorised partners in Australia and New Zealand.
Concept Solutions offers a comprehensive range of flat belt and plastic modular belt conveyors and equipment. These can be specified to suit virtually any configuration, environment or conveyed product.
• Versatile, reliable and economic conveying solutions
• 3D design for realistic product visualisation
• Hygienic design for ease of sanitation
• Plant layout and flow optimisation
• Safety standard compliant design
• Food grade plastic machining and supply
Vacpack is a leading provider of innovative machinery and cardboard base food packaging products to New Zealand, Australia and the Pacific.
Are you looking for eco-friendly packaging that improves the shelf life of your fresh and frozen items? Then, Vacpack’s market leading cardboard base technology is the solution for
you. The systems help reduce plastic by up to 80%, is 100% biodegradable or recyclable and creates an appealing and safe end-product. Call us now to find out more.
or
www.conceptsolutions.co.nz
At DTS, we specialise in stainless steel engineering solutions for the food, beverage and pharmaceutical industries. Our tank design philosophy is to minimise waste and maximise profit, not only during tank fabrication, but also throughout the tank’s operational life and production. • Food & beverage tanks
• Insulated hazardous pressure vessels
• Hot water recovery / 2205 duplex
• Laser-welded dimple pads / thermal control
• Clean in place and agitation
• Walkways, ladders and handrails
In the food industry, temperature measurements are part of the daily routine. The quality of food products can only be tested and guaranteed by precise measurements. The Testo range of measuring instruments, available from NZ authorized distributor Eurotec Ltd, a member of Carel Group, can carry out spot-check measurements in seconds.
Whether in the transport and storage of foods, in restaurants or in large kitchens, wherever temperature needs to be recorded, Testo measures up and helps you keep compliant. Testo enables you to guarantee optimal performance in key areas of your business.
Food industry instrumentation for incoming goods: Every item that enters your premises should undergo rigorous checks in order to ensure its quality and safety. Whether that be your weekly delivery of fresh fish, or the daily top up of your fruit and vegetable stocks, food can spend a long time in transit from the wholesaler before it arrives at your door. The testo 831 infrared thermometer is perfect for
dealing with incoming goods, as it allows you to carry out quick and precise temperature measurements of whole pallets of food and smaller individual products from a distance.
Monitor the cold chain and ensure food safety Perishable foods are sensitive to changes in temperature. While fruit and vegetables ripen quickly and barely make it to the supermarket if they are stored and transported in conditions that are too warm, bacteria can multiply in meat and dairy products when heated. These, in turn, can cause serious illnesses. Therefore there must never be any gaps in the cold chain, but this can only be ensured through continuous monitoring. The testo 184 series
of Cool Chain Temperature Loggers can measure the temperature and humidity of your goods while in transit. With up to 150 days of battery life, you’ll be able to keep track of goods over long stretches, measure and analyse temperature and humidity data - arming you with information to implement changes when needed backed by data.
info@easirecycling.co.nz www.easirecycling.co.nz
Freephone: 0800 342 3177
Protect your brand solutions that enhance food safety and weight compliance for processing lines.
LEARN MORE ABOUT OUR EQUIPMENT ONLINE
EXBERRY® Colours are the ideal and future-proof solution for food and drink applications matching the recent plant-based, vegan and vegetarian trends.
HRS Heat Exchangers operates at the forefront of thermal technology,
Pasteurisation
Sterilisation
Aseptic Filling
Direct Steam Injection
Evaporation
CIP Kitchens
Process Skids
Juice Crushing and Remelting
NZMS Scientific offers specialised solutions to help ensure your products meet the standards you and your customers expect.
Give us a call today to talk about:
• Pathogen testing
• Allergen testing
• Hygiene testing
• Sterility testing
SCANZ is a multi-discipline supply company and manufacturers agent, specialising in technology and equipment for the food industry. It’s primary focus is within three market segments, namely fish (including aquaculture), meat and the dairy industry. High Pressure Processing takes Scanz into other areas, as does a recent involvement in industrial waste water treatment.
SCANZ
a Custom Blends
a Flavours: Sweet, Savoury, Smoke
a Caramel Colours
a Yeast Extracts
a Proteins: Plant & Animal
a Starches: Native & Modified
a Minerals
a Dehydrated Vegetables
a Carrageenan & Gums
a Preservatives
a Clean Label Ingredients
For 125 years we’ve been a trusted ingredient partner for iconic vanilla. With a range of bulk and customised solutions for industrial, along with deep manufacturing experience, we can help you find your next flavour solution. Our food industry passion, dedicated technical team and global commitments to sustainable and ethical sourcing can help you achieve your business goals.
BULK FORMATS & CUSTOMISED SOLUTIONS:
Extracts
Pastes
Dried vanilla derivatives
CUSTOMISABLE CLAIMS:
Certified organic
Certified vanilla provenance
Urgent Couriers are specialists in temperature -controlled deliveries of chilled small goods.
Fast, reliable, guaranteed sameday services live tracked from despatch all the way to your customer’s door. We provide techforward and innovative solutions to make your life easier.
With over 40 years operating experience in New Zealand, TC Transcontinental Packaging New Zealand (TC NZ) is a leading manufacturer of flexible packaging to the FMCG, horticulture, retail and manufacturing markets
TC NZ is both a reputable manufacturer and trader, supplying all forms of flexible packaging made from traditional plastic films recycled blended films, laminated barrier substrates. TC NZ employs over 90 people in New Zealand with centres in Auckland and Christchurch, home to an ultra-modern food grade packaging manufacturing plant, and supported by our global TC Transcontinental research and technology platform from North America.
TC Transcontinental Packaging brings a distinctive blend of science, technology, and art together to create flexible packaging that preserves our customers’ products and accentuates their brands on the store shelf. Our expertise, resources and conversion technology helps us create packaging that gives our customers a competitive advantage. We utilise a widevariety of printing techniques, laminations and converting styles including pouches that help enhance your brand.
We invest in state of the art technology to offer and invest in a sustainable future and are delighted to be recognised for our high quality packaging that we supply to our customers. Globally TC Transcontinental Packaging is committed to a circular approach to plastic. As global signatories to the Ellen MacArthur Foundation, we are working towards our 2025 goal where 100% of our plastic packaging will be reusable, recyclable or compostable, and 10% of our plastic output to be made from recycled plastic waste.
At the 2022 Pride in Print Awards, TC NZ were awarded Gold Sustainability Award in the Flexible Packaging Category for our significant volumes used into industrial, refuse and hygiene packaging. TC NZ are meeting customer requirements by extruding and converting recycled resins of in-house, postindustrial waste, and post-consumer recycled content , Green PE (PE derived from renewable resources such as waste sugar cane), and has the ability to manufacture flexible packaging with other