
1 minute read
RHI Magnesita’s pandemic problems: a catalyst for change
WRITTEN BY: SEAN ASHCROFT
PRODUCED BY: CRAIG KILLINGBACK
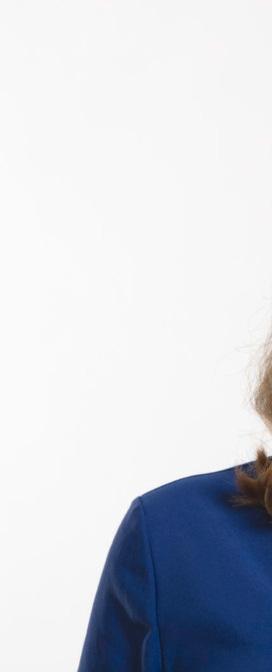
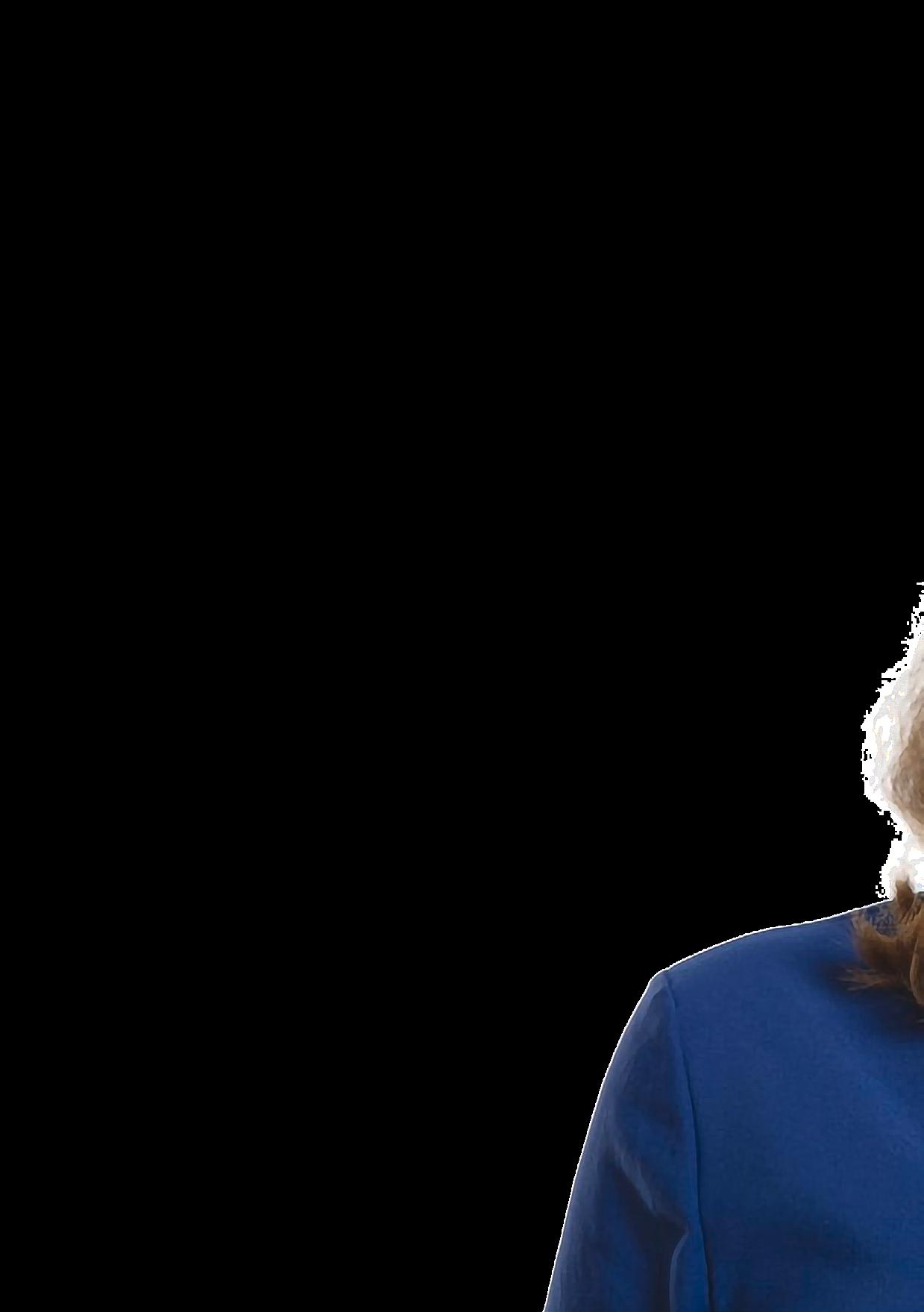

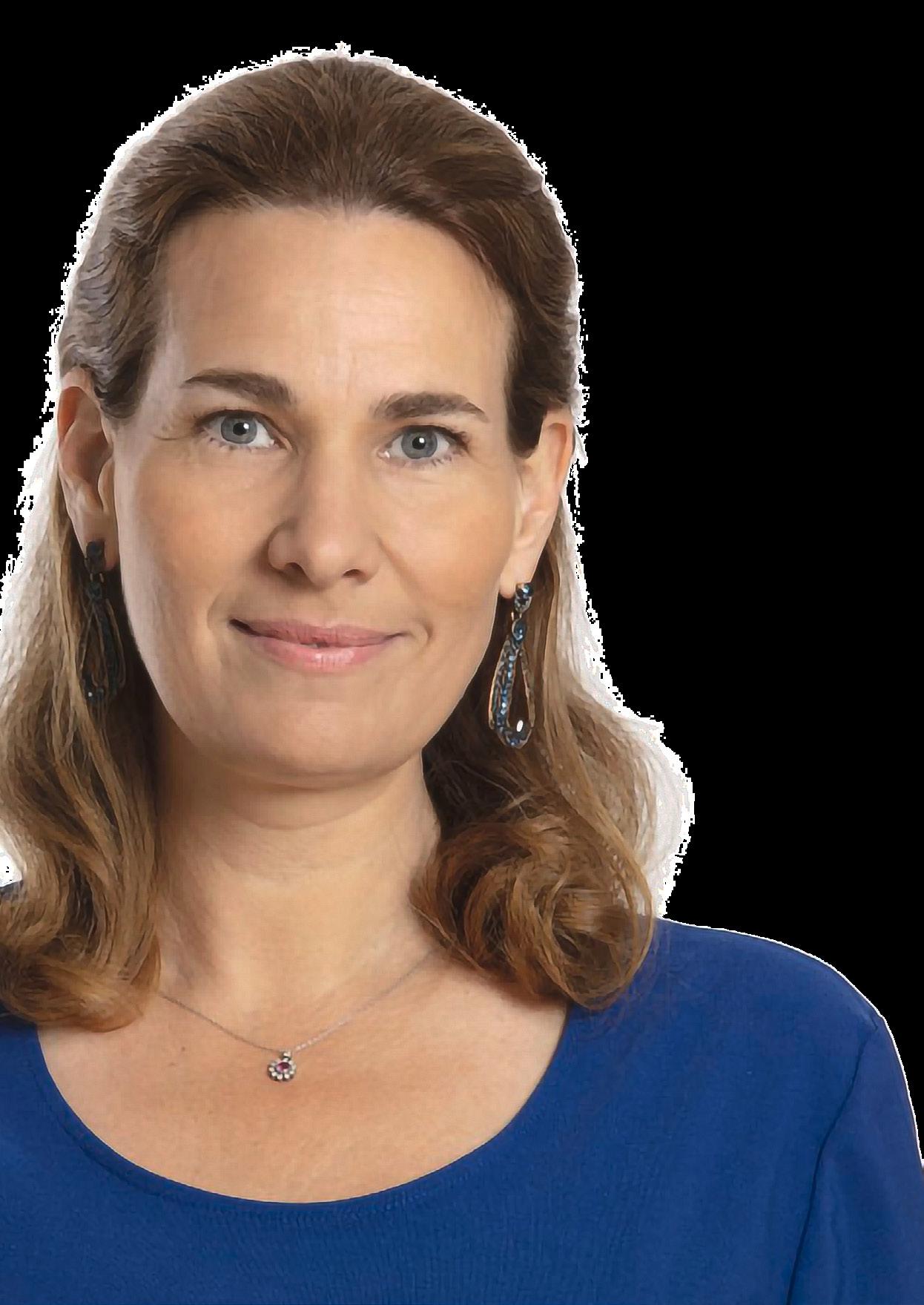
SIMONE OREMOVIC EXECUTIVE VP PEOPLE, PROJECTS & SCM, RHI MAGNESITA
33 Main production sites (incl. raw material sites)
100+ Countries shipped to worldwide
5 R&D hubs and centres
Overseeing RHI Magnesita’s supply chain – and much else besides – is Simone Oremovic, whose three-pillared title is EVP, People & Culture, Supply Chain Projects, and Integrations.
“Ours are not well-known products most of the time but are essential for our modern lives,” says Oremovic. “They’re needed in the production of steel, cement and glass. So the construction industry needs us. The car industry needs us. In mobile phones, there are components that couldn’t be produced without refractory.”
“If we stopped production,” she says, with a serious look, “we would stop steel-making production worldwide within a few weeks.”
Dolomite and magnesite are the core product the company uses, and these are extracted via mining activities.
“We have some mines ourselves,” says Oremovic, “but sometimes we need to buy raw material on the market.
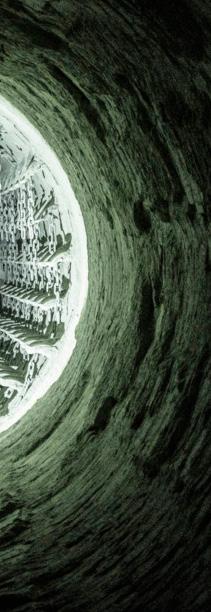
The company’s biggest mine is in Brazil, and it also has mines in the US, China, Turkey and smaller ones in Europe, including Austria. “We obviously also try to match our production footprint to the existence of the raw materials,” she explains.

The pandemic was a huge challenge, and was the catalyst for RHI Magnesita to transform its supply chain, particularly around logistics.
The company has shifted from a very centralised global model to a much more regionalised model.