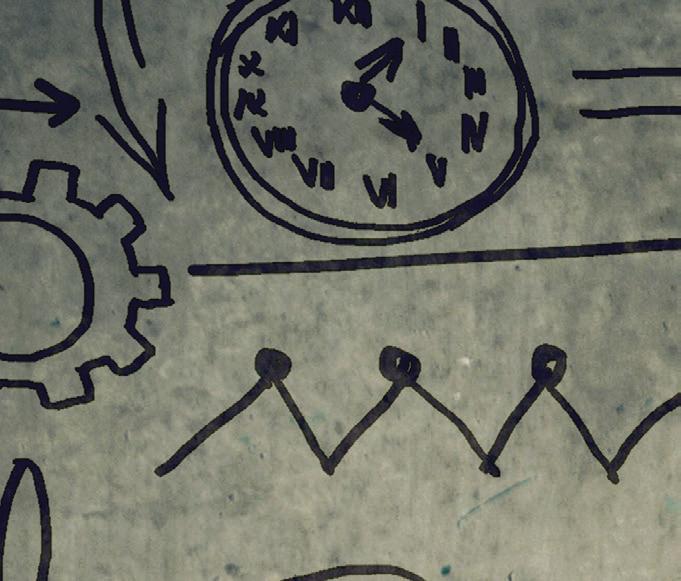
8 minute read
3PL Compliance: If You Fail to Plan, Then Plan to Fail


While recall problems typically arise from the source, they directly impact 3PLs in major ways.
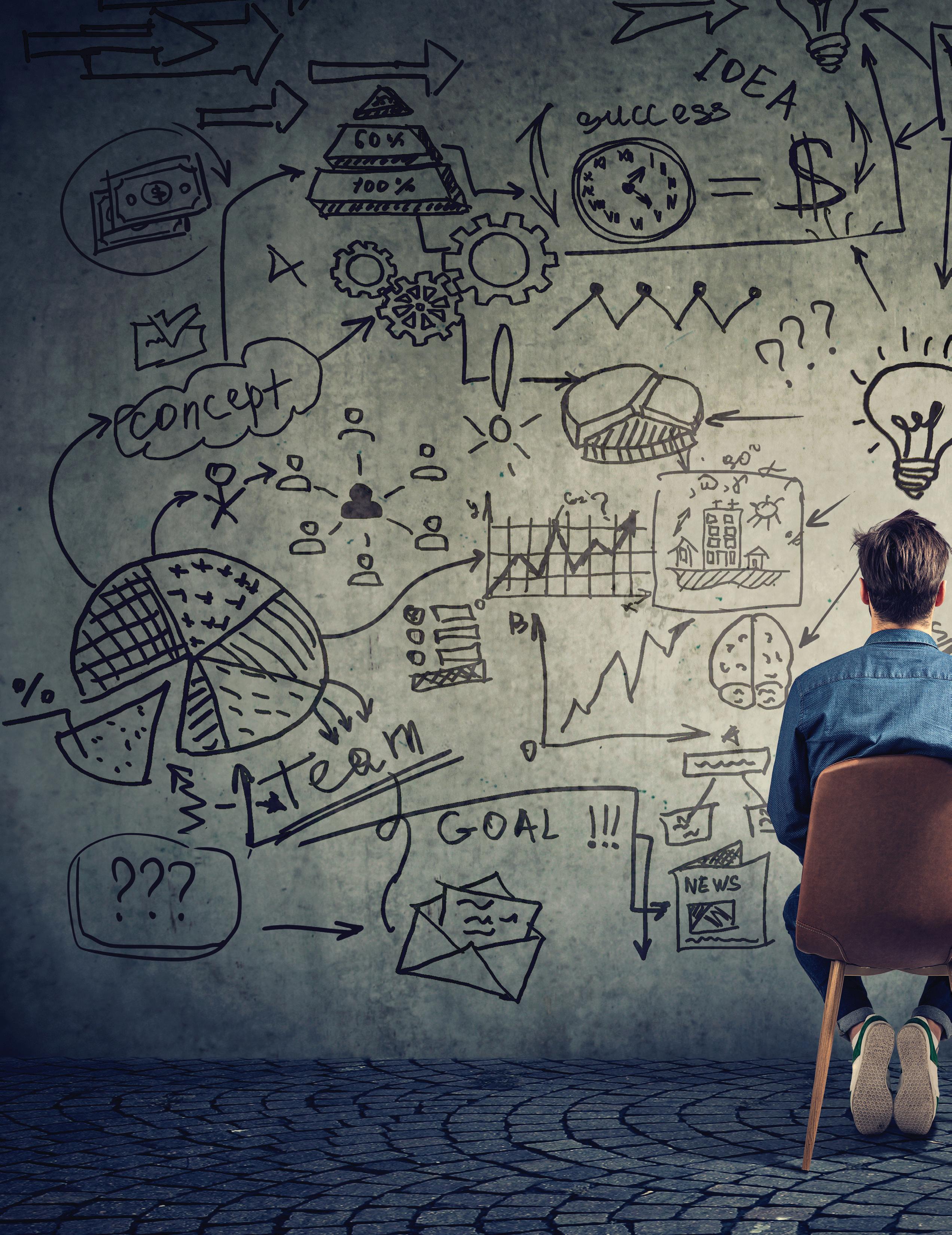
@pathdoc - adobestock.com
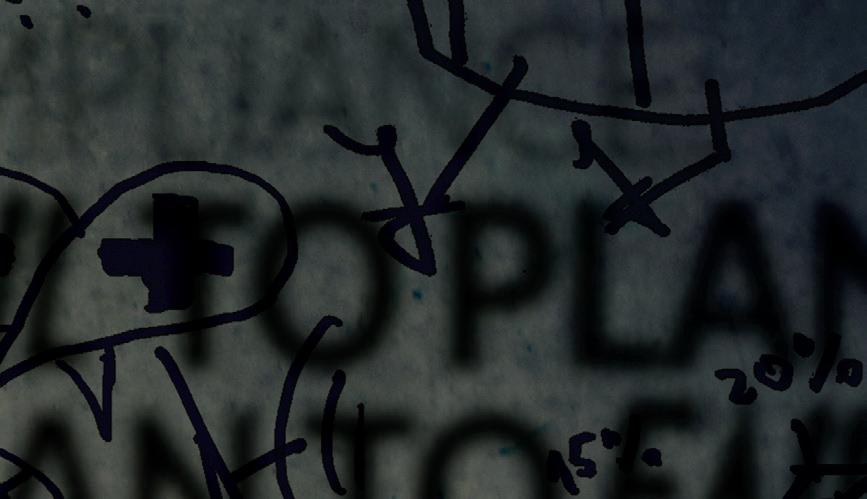
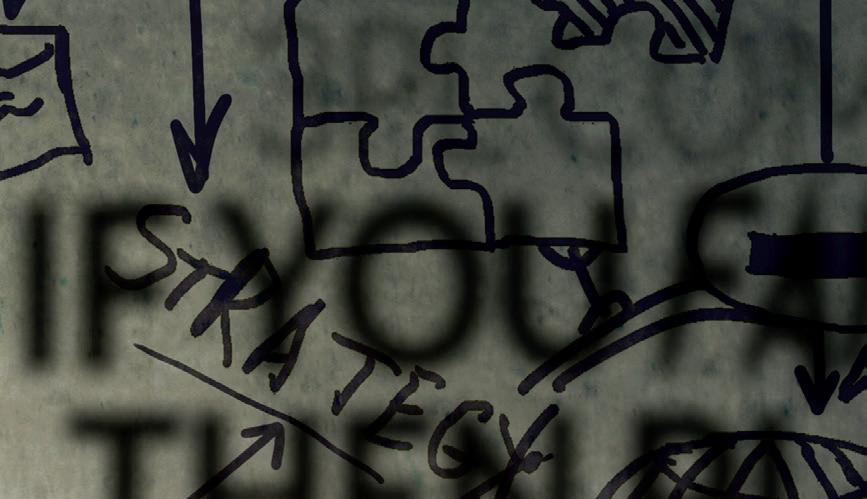
@ pathdoc - adobestock.com
In just this quarter alone, Kraft Heinz, Kenosha Beef International, Mars Foods, Sabra Dipping Co. and Giant Food all experienced recalls, and weren’t the only ones. Unfortunately, this comes with the territory in selling food, and for the cold chain and perishable goods, it only heightens recalls and monitoring.
“Temperature-controlled products are prime categories for potential recalls, often attributable to ‘lotspecifi c issues’ from the manufacturer/grower or expiration dates compliance while in storage,” says Brien L. Downie, president of Holman Logistics. While recall problems typically arise from the source, they directly impact third-party logistics (3PLs) companies in major ways, as 3PLs must immediately deal with the repercussions. Throughout the past few years, recalls became even more complicated as politics and the pandemic dramatically shifted food production and transportation, causing incredible shifts in processes as well as demand. “Two major challenges over the past two years have been geopolitical politics and COVID-19,” says Jim Hardeman, chief product offi cer and director of marketing at CMX. “Both have been incredibly disruptive to supply chains. With tariffs, shifts in manufacturing, many cycles of closing and reopening of businesses, shifts in consumer demands, increased e-commerce and manufacturing facilities opening and closing or scaling back for worker safety or shortages, 3PLs have had to fl ex to accommodate all these changes. With increased complexity comes increased risk.
“While 2020 saw a dip in FDA inspections, citations and recalls due to COVID-19, the trends over the last 10 years show an increase in recalls,” he continues. “And, while there is much debate about whether that is because there is more risky food out there, or there are better detection methods, or there is more public awareness and pressure on brands to voluntarily withdraw products faster or face the reputational damage, the need for better traceability and tools to manage recalls has never been greater.
“When it comes to the food supply chain, 3PLs play an important role between the supplier and the end retail food establishment. Because they are regulated facilities by the FDA due to holding product/or have product in transit, they need to be able to quickly identify, isolate and remove/ dispose of product per manufacturer’s instructions before quality and food safety issues become widespread crises,” says Hardeman.
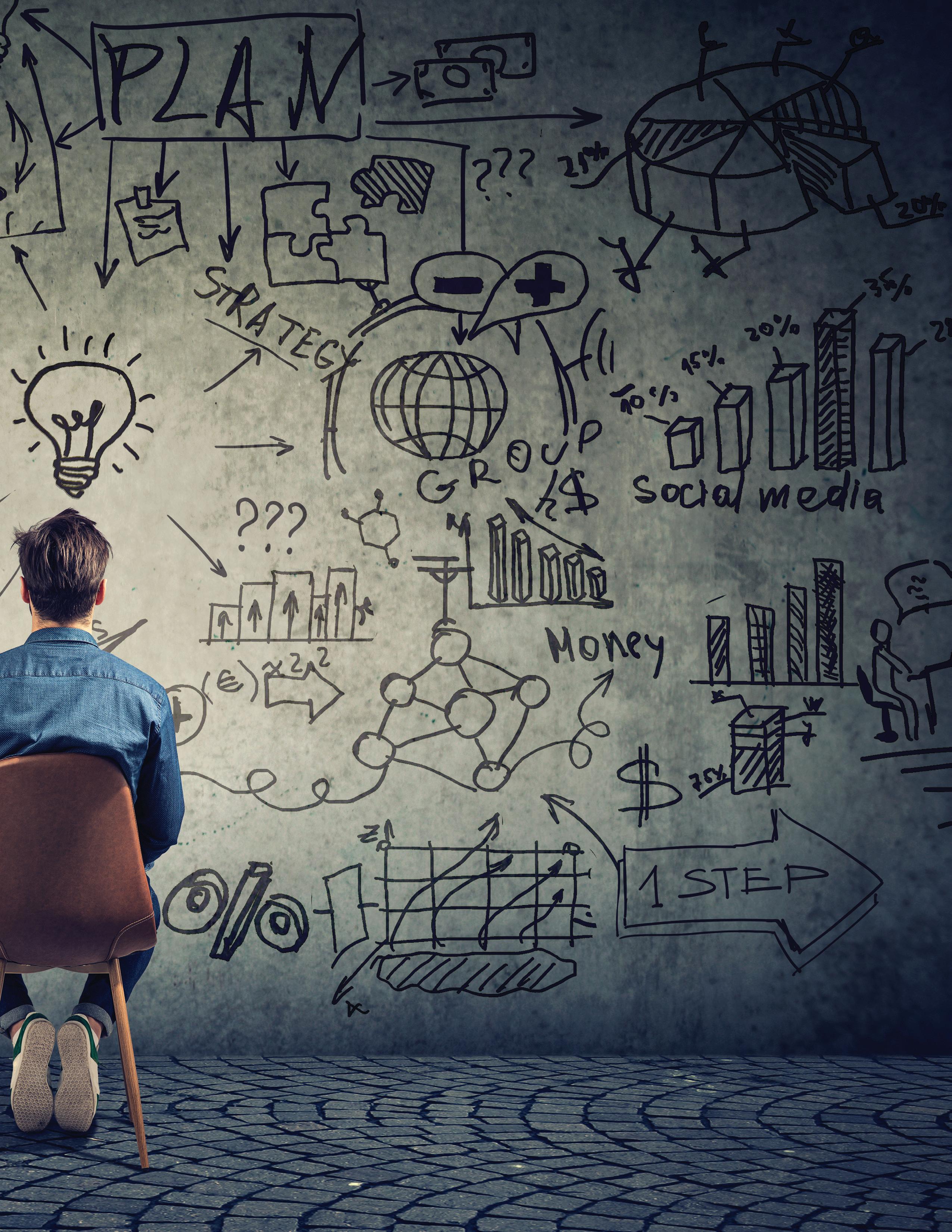
Technology can help
Recalls are imperative for health and safety, but also dramatically impact multiple companies’ bottom lines. Despite gross fl uctuations in the industry, 3PLs need to focus on preparedness as well as the ability to be fl exible. Having procedures in place, as well as tapping into tracking and data are just a few best practices to help keep a stable
The major disruption right now might help for long-term resiliency.
zimmytws
more complicated,” Hardeman continues. “This is further compounded by the lack of data standards and system interoperability among trading partners. “The FDA’s New Era of bottom line and reduce outbreaks or safety Smarter Food Safety Blueprint aims to hazards. address these challenges, but will require
“Recalls and regulatory compliance in cooperation in data standards and any area require discipline procedures, innovative technology-driven solutions product/lot-code tracking and for compliance. As a result, we’ll see an communication systems that ensure accelerated movement toward creating any product at risk can be identified and data standards for exchanging critical handled in the most time-sensitive manner,” tracking events and key data elements, Downie continues. “Having an existing which are required for record-keeping, preparedness plan for traceability and executing handling recalls and recalls.” regulatory compliance is fundamental—if you fail to plan, then you’re “Implementation However, the concept of technology in the 3PL world and regarding planning to fail.” and adherence to recalls is more than data
Hardeman explains and tracking. The 3PL that in addition to rigorous COVID and supply chain industry tracking, data and other has its own set of specific technology needs to be protocols are not technologies. included so that 3PLs can take definitive action and act quickly. optional.” “In our world, we have three critical technologies—warehouse
“As products have management systems become more complex and supply chains (WMS), electronic data interchange (EDI) have grown longer, the ability to track and Internet of Things (IoT) sensors, all of and trace and monitor the journey of the which help us maintain tight control over ingredients in our food has become what goes in and out of our facilities and keep customer product within specified customer conditions,” Downie adds. “Having a solid WMS that is capable of lot-code or expiry date tracking is essential in the modern logistics game, as is a WMS that can export that data in a usable format that can be easily ingested into Excel, Tableau or some other analysis tool. Fortunately, Holman recently invested in a highly capable WMS, ensuring that not only are we able to properly rotate product according to customer specifications, but also that we can export the data in a user-friendly format, helping us live up to our promise of extraordinary service. It’s one thing to have the data locked away in SQL tables of the WMS; it’s another to have it ready to go at a moment’s notice, as responding to a recall request is an incredibly time-sensitive issue.
“EDI capabilities are critical to enabling the supply chain participants to better view products throughout the supply chain, ensuring that communication is efficient and direct, and not prone to human error,” he says. “The more information is ‘touched’ (e.g. ‘and-keyed’ into a system from an email or phone call), the more opportunity for corruption of that information. EDI offers direct, system-to-system communication to reduce human error opportunities.
“There’s no substitute for living Gemba (i.e. going to the work and seeing it firsthand), but a close second can be IoT sensors that allow for 24/7/365 monitoring of a situation. Holman has custom built several digitally calibrated temperature sensors that are connected to our information management system. These IoT sensors automatically alert our team to potential issues, ensuring quick response times when temperatures approach specified thresholds.”
In a recent study, Quantzig found that smart sensors and predictive analytics, similar to what Hardeman explained, can track temperatures of food throughout the entire transportation process, beyond the in-house warehouse. Sensors will be able to tell when food enters a dangerous temperature on the road and possibly be contaminated. Sensors notifiy the transportation company or processor, so they can check for any damaged goods and prevent a recall from happening before reaching consumers. Predictive analytics
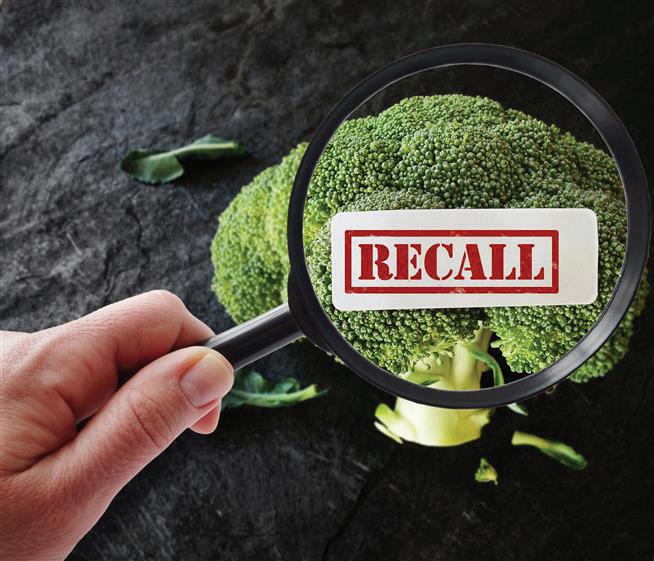
may be also able to tell when food is about to go bad.
COVID-19 could lead to a better future
Recalls and food safety are always an important issue in 3PLs, but last year, safety and hygiene heightened dramatically after the Coronavirus disease (COVID-19) outbreak began. Once the disease became widespread and shutdowns occurred, new protocols were put into place to help stop the spread in every industry, especially in the food and cold chain sectors. While the FDA took a step back in on-site auditing, companies had to ensure they were transporting food safely yet still socially distance for themselves.
“Implementation and adherence to rigorous COVID protocols are not optional,” Downie says. “It is critical to the ongoing operation of any storage or warehousing facility handling with or without a product recall event. However, people make the difference in successfully managing a recall or regulatory response issue. Keeping our people and the facilities we operate ‘COVID free’ will continue to be a ‘best practice’ requirement.
“Holman has thrived in the COVID environment, with our masking, distancing and cleanliness initiatives working well thus far,” he adds. “In many ways, it’s been business-as-usual with a whole lot of hand sanitizer. The most critical aspect to ensuring our facilities remain ‘COVID free’ is engaging directly with our people, helping them to believe in the program so they want to follow along; not just do it as a result of being forced.”
Beyond regulations though, COVID-19 continues to disrupt the supply chain, which puts massive pressure on 3PLs dealing with recalls, and can even cause more recalls due to changes in demand. But, this major disruption might help for long-term resiliency.
“COVID has shown that supply chains can be easily disrupted and that we have an over-reliance on people and manual processes to keep them functioning properly (especially for food),” Hardeman says. “We’ve also seen that in many ways, we have too much information and data and not enough of the right information and data in a format that provides trading partners the visibility and interoperability across channels and systems.
“President Biden signed an executive order that calls for a 100-day review to assess vulnerabilities and areas of improvement in four major supply chain areas,” he adds. “The order also called for the review of six broader supply chains, including transportation and food production. And, while the primary goal may be to reduce our dependence on foreign suppliers and avoid shortages, it is also aimed at minimizing disruptions. This coupled with FSMA and the FDA’s New Era of Smarter Food Safety all lead to increased regulations and the need for advances in data, technology and collaboration to overcome these challenges.”
Hopefully the safety challenges brought about throughout the pandemic will help build a future more resilient for recalls.
Despite gross fluctuations in the industry, 3PLs need to focus on preparedness and the ability to be flexible.
@Trueffelpix - adobestock.com