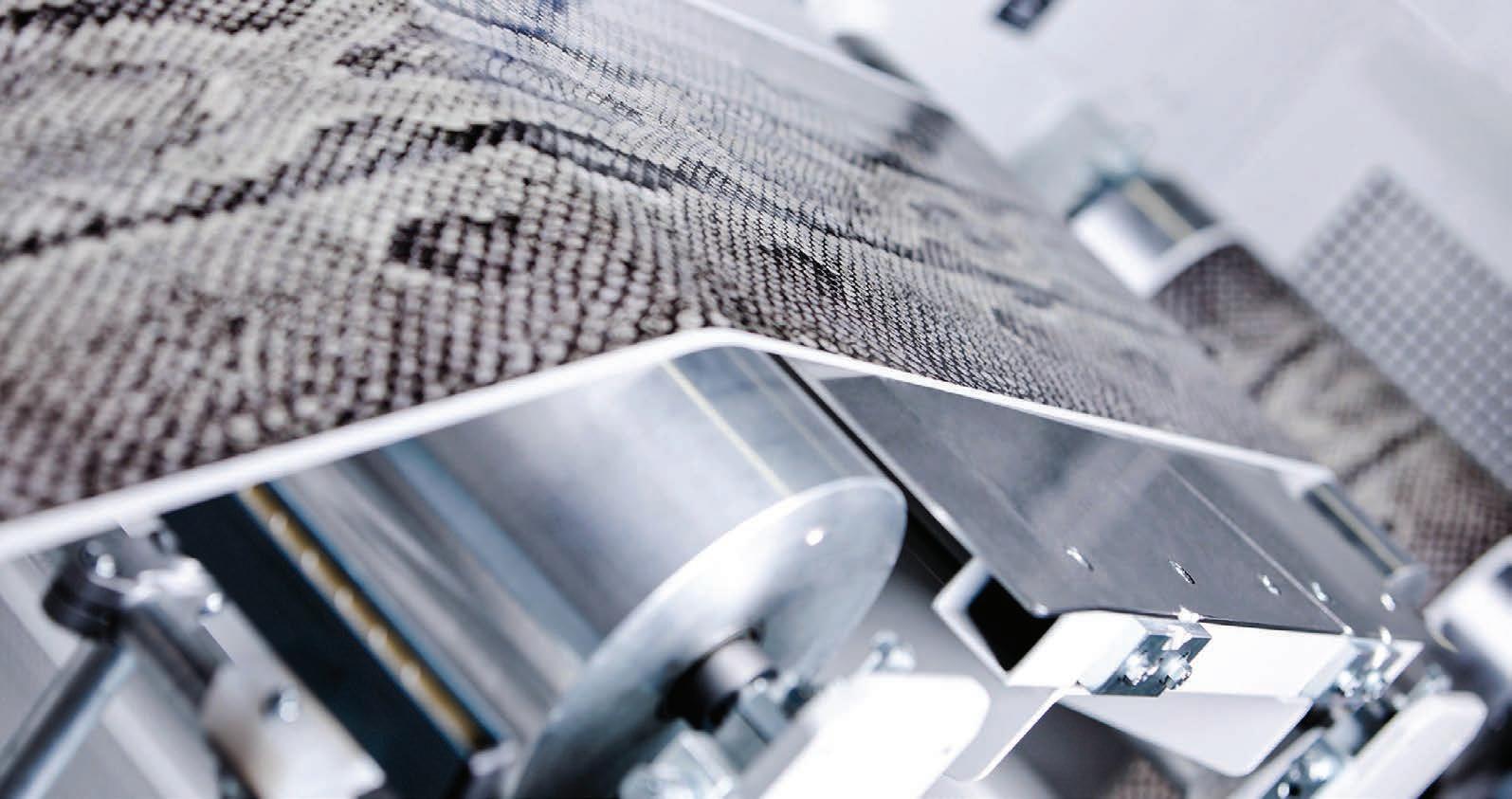
4 minute read
Not Your Mother’s Laminate
New Technologies And Machinery Are Taking Laminate Production And Design To The Next Level
Laminate products are widely used in various industries and applications. With their durability, versatility and affordability, they have become increasingly popular in the surfaced panel industry.
And with new technology and techniques in laminate machinery and materials, these highly customizable product possibilities suit a wide variety of tastes and preferences, limited only by the imagination.
Laminate products traditionally are made by stacking decorative sheets atop layers of structural materials such as plastic, resin, fiberboard, and particleboard. The decorative and structural layers are joined together using heat and compression, and protective top layers are often added to help protect the final product from wear from water, wear and weather.
To produce high-quality laminate products, manufacturers are using advanced laminate machinery and equipment that can handle various types of adhesives, films, and substrates — along with machines that make the whole process just a little (or a lot) easier.
One helpful machine is the Flipper, a machine designed by Diffenbacher to automate manual labor. It separates laminates from a stack with random orientation and flips them on demand to build a new stack of laminates in a selected orientation. The fully automated process includes separation of the laminates, detection of their orientation, transfer of the laminate directly to the new stack or flipping it if required and finally building up an aligned stack. Visit dieffenbacher.com/en/ for more information.
Take It Up A Notch
A major recent advancement in creating truly customized laminate panels is printing custom designs onto the overlay to replicate everything from wood and natural materials to a favorite cartoon character or pattern—not only in looks but also in texture.
Hymmen showed off its award-winning Digital Lacquer Embossing (DLE) Technology at the recent LIGNA 2023 show in Hannover, showcasing how they are delivering highly realistic optics and haptics by printing a transparent liquid medium into a layer of structure lacquer.
This technology grants all commercial and technical benefits of digital single pass printing like flexibility, faster set-up times and individualization, and company officials say its most important feature is the creation of structures that are embossed-in-register
(EIR) to the decor of the surface – regardless whether they are printed digitally or with an analog method. This also allows for more rapid responses to market demands and trends while reducing material waste.
Dr. René Pankoke, managing partner of Hymmen, says he is certain that digital printing will increasingly replace analog printing in the industry as well. "[It is a] trend that can no longer be reversed," he says.
Increased automation and the emergence of cloud-based monitoring and analysis to optimize production is the wave of the future, says Pankoke. "The positive feedback from our customers and the market's demand for significantly higher automation and efficiency has now prompted us to expand our commitment in this market area," he adds. Visit hymmen.com for more information.
MULTI-TASKING MACHINES
Manufacturers today are also looking to commercial and industrial laminating equipment that can perform various laminating processes with speed and precision. These “all-in-one” machines offer features such as double belt presses, heated platen, high/ low pressure vacuum press, roller/nip roll, multiple workstations, durometer capabilities, top/bottom temperature adjustments, heated shoe laminators, radiant heat laminators, no touch lamination systems, and specialty adhesives. These machines can handle different materials and thicknesses and produce consistent and uniform results.

Union Tool offers a Veneer/Vinyl Laminating System which contains a Union Hot Melt Roller Coater, Union Powered Lay-up Conveyor and Union Rotary Laminator to laminate several different core materials to a variety of different veneers and vinyl materials. The laminating system is designed to boost productivity and product quality, producing a panel with a maximum size of 60 inches wide x 120 inches long and a maximum thickness up to four inches. Visit uniontoolcorp.com for more information.
And the Panel Express Laminating System from Black Bros. is designed to produce 240 ready-tocut panels in an eight-hour shift, combining a heatassisted rotary press designed to laminate all types of HPL to particleboard or MDF panels with fast-tack PVA adhesive. This in-line Panel Express Laminating System requires no additional curing or press time. Visit www.blackbros.com for more information.
Laminate By Design
Laminate product design software that can help designers and customers create custom laminate products that match their vision and needs. These software programs allow users to choose from a variety of colors, patterns, textures, and finishes for their laminate products. They also enable users to preview how their laminate products will look in different settings and lighting conditions. These software programs can help users create unique and personalized laminate products that suit their style and budget.
VectorLam 3.0, the latest edition of Vectorply’s proprietary laminate analysis software, provides a cloud-based, multiplatform compatible approach to classical laminate theory and provides a suite of services across diversified market segments.
VectorLam helps achieve goals of stiffness, strength, weight and cost by allowing users to design the perfect laminate for their application. Whether it is comparing materials, resin, or even manufacturing processes, VectorLam offers the best solution and reports it in clear, concise language. It has never been easier for users to build, review, and adjust their laminates to meet their specific requirements. Visit vectorply.com for more information.
TOP LEFT: THE FLIPPER, A MACHINE DESIGNED BY DIFFENBACHER, SEPARATES LAMINATES FROM A STACK WITH RANDOM ORIENTATION AND FLIPS THEM ON DEMAND TO BUILD A NEW STACK OF LAMINATES IN A SELECTED ORIENTATION.
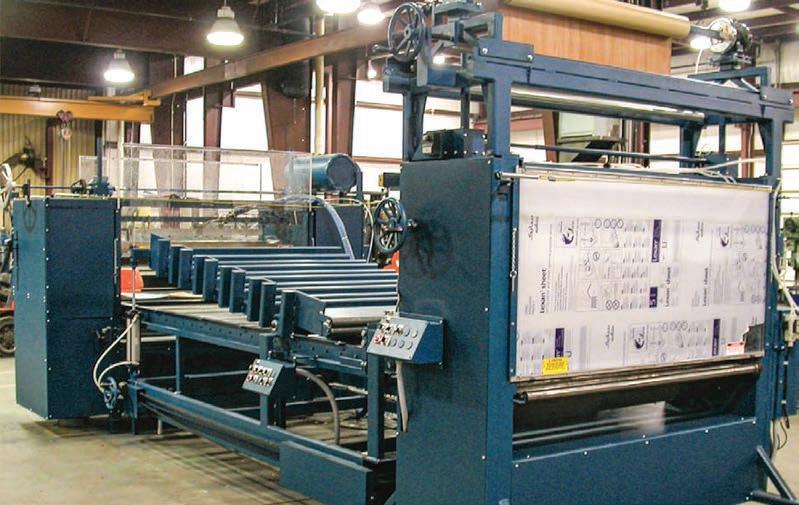
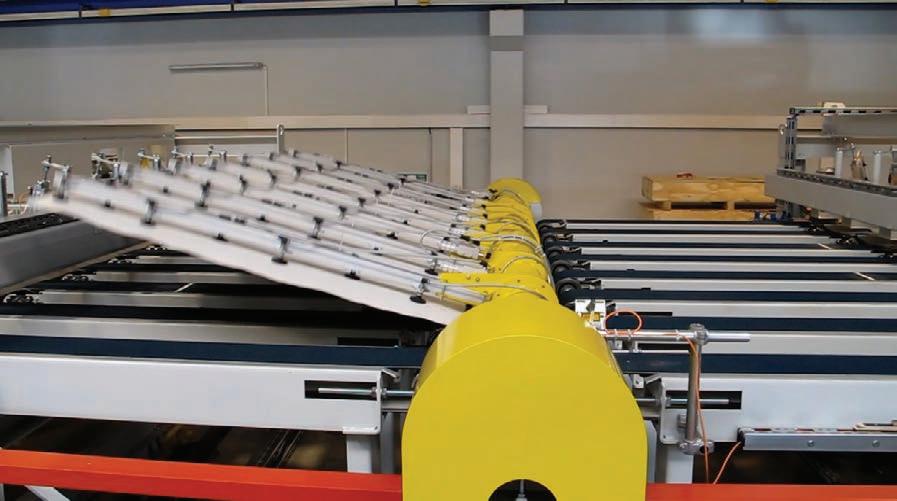
TOP RIGHT: BOOST PRODUCTIVITY AND PRODUCT QUALITY WITH THE UNION VENEER/VINYL LAMINATING SYSTEM.
BOTTOM: THE PANEL EXPRESS LAMINATING SYSTEM FROM BLACK BROS. IS DESIGNED TO PRODUCE 240 READY-TO-CUT PANELS IN AN EIGHTHOUR SHIFT, COMBINING A HEAT-ASSISTED ROTARY PRESS DESIGNED TO LAMINATE ALL TYPES OF HPL TO PARTICLEBOARD OR MDF PANELS WITH FAST-TACK PVA ADHESIVE.
Laminate machinery and materials are constantly evolving to meet the changing demands and expectations of customers and markets. By using the latest in these materials, software and machines, manufacturers can continue to produce highquality laminate products that are durable, versatile, affordable, and attractive while keeping up with industry trends. S P
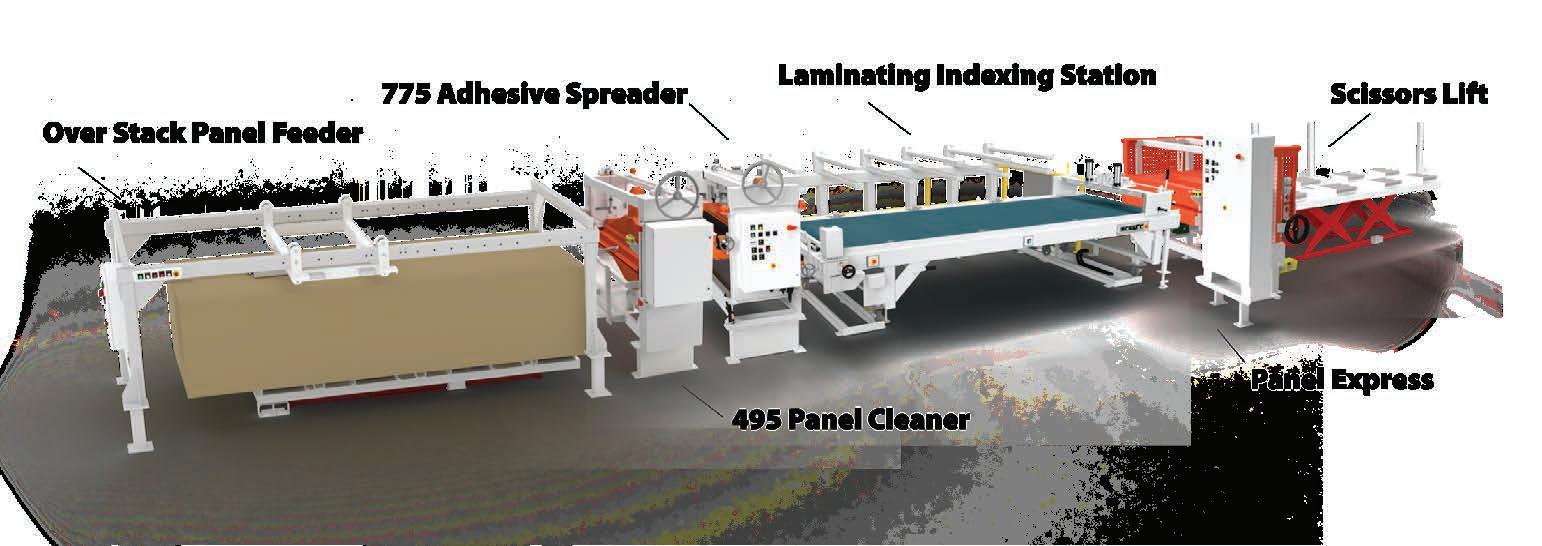
