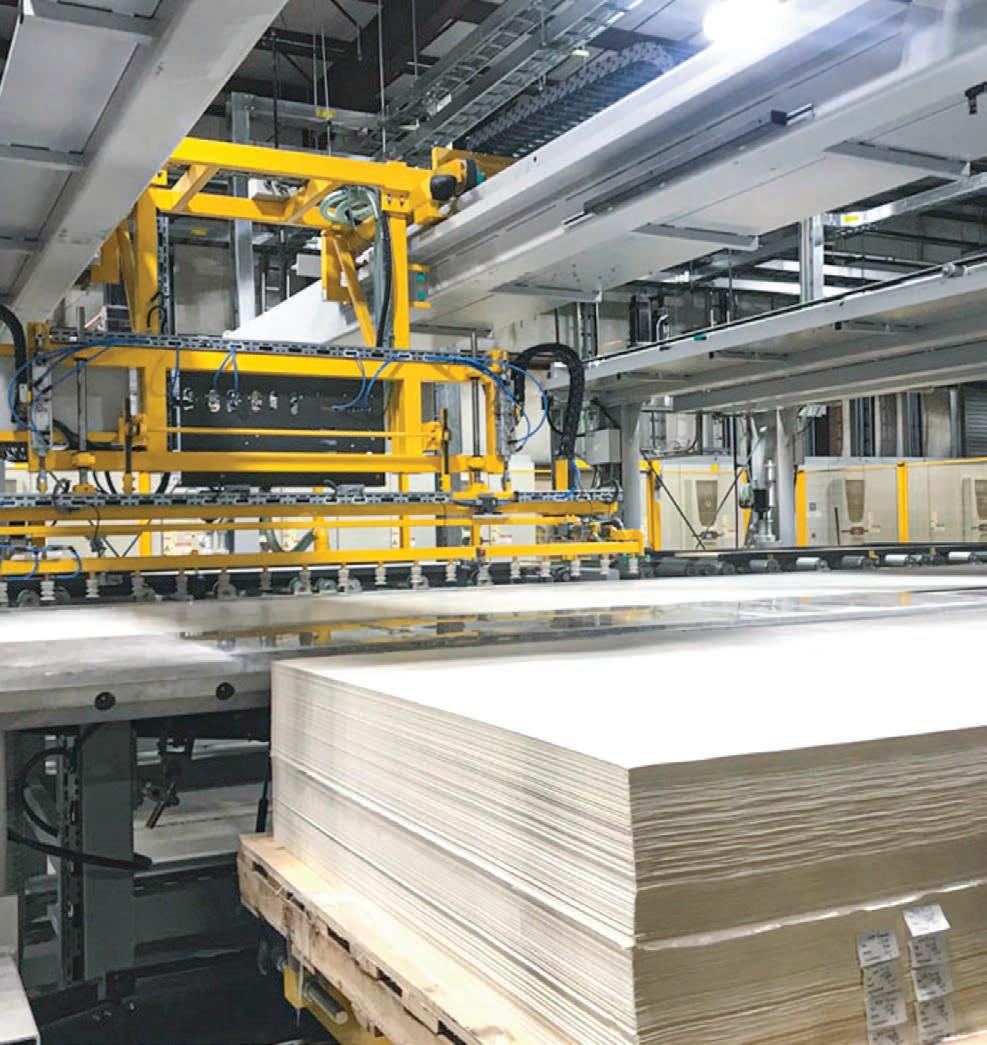
2 minute read
Making it Work
FROM TACKLING THE SUPPLY CHAIN TO ADDRESSING LABOR SHORTAGES, MANUFACTURERS TODAY
FACE A MYRIAD OF CHALLENGES, BUT ARE FINDING SOLUTIONS TO SUCCEED
BY JENNIFER WILLIAMS
you can use instead. You do have to be careful, though, and know what you’re getting.”
Identifying alternatives and maintaining a good relationship with vendors is key, agrees Jonathan Thompson, sales manager for E.B. Bradley Co & West Coast Laminating.
“Product knowledge is really important,” he says. “A few years back, we found we were under promising and trying to overdeliver when demand exceeded what we realistically could provide.”
Being transparent with their team, vendors and customers helped bridge the gap, says Thompson. “Just-in-time can still work,” he adds. “But it needs to be more flexible. We learned a tough lesson that we’re not in control of certain variables.”
And fabricators need to also be more flexible in what they offer over the next few years, says Thompson. “Supply chain issues will not affect the market as much as the lack of highly skilled workers will — especially as it relates to JIT.”
Wilmes agrees that the labor issues are here to stay “for a very, very, very long time,” but says they are key to helping alleviate that shortage can be found in automation and robotic machinery. “There’s no question that the only way American industries can compete to be leaders is through robotic integration in our manufacturing facilities,” he says. “Our industry usually lags, but we have to be looking at making these changes…things like sorting, stacking, palletizing, robotic forklifts…these things that we can’t hire for anymore.”
Finding people who want to work has been our biggest challenge, says Bob Brown, who serves as executive vice president of Royal Plywood Co. and is on the AWFS board of directors. “We need more education for our workforce…getting wood shops back in schools.”
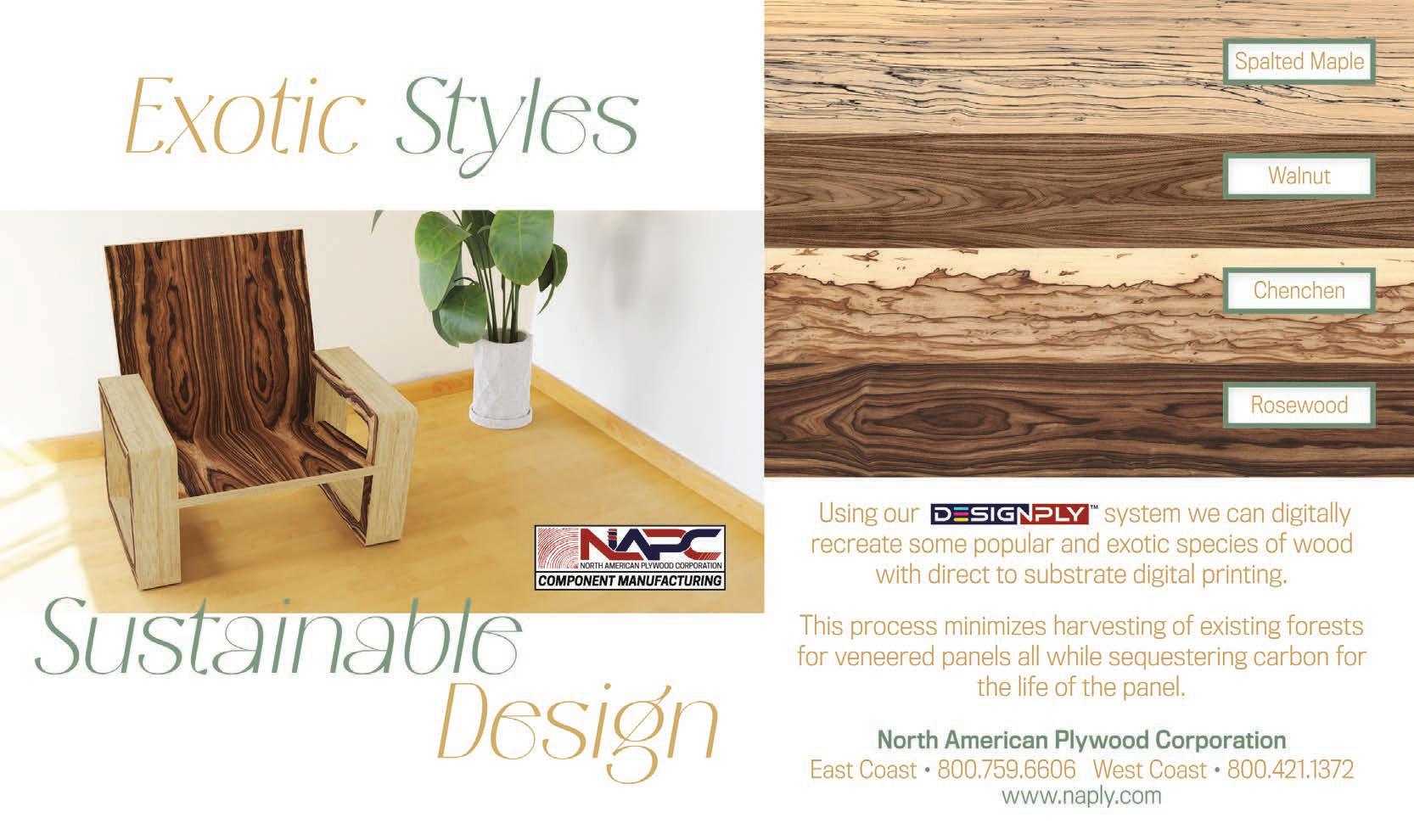
As for retaining current employees, he says, the key is engagement and being generous with not only wages but things including time off and flexibility as needed.
“It’s so important to take care of your people,” Brown says. “They are what make us.”
And while onshore manufacturing has captured recent headlines, Thompson says it’s impossible to onshore everything, especially with labor shortages. “I do foresee China imploding soon, though, and we will have more opportunities for onshoring,” he says.
Shipping and distribution also remains an issue for many manufacturers, adds Thompson. “We import most of our products from Europe and have had different issues at different times,” he says. “But the bigger challenge has been getting the containers out of Europe — the war in Ukraine has really affected that aspect of our business.”
“Fifty percent of the cost of goods has to do with shipping and import costs,” he says. “Amazon has pretty much taken over small parcel shipments, so there are additional challenges and opportunities for small businesses to step up.”
Brown says that the trucking industry today is a nightmare that affects every level of manufacturing. “Today it can take 12-18 months to get a new truck — and then it may be missing parts. And on the West Coast — California, Oregon, Washington — the electric vehicle agenda doesn’t work. Electric trucks are VERY expensive and they just don’t work…not to mention that we just don’t have the power grid to handle these mandates. And all of these significant costs would have to be passed down to the consumer.”
But it’s not all bad, says Thompson. “Stop watching the news — it’s never as good or bad as they say,” he stresses. “Focus on your people. The businesses that are growing are the ones who are willing to change and try new things.” s p